Delays have long plagued the construction industry. Reasons for this are as varied and complex as the construction process itself.
Regardless of possible categorizations, some causes of project delays are more common than others and can affect construction projects of any type and size.
Without further ado, here are the six usual suspects.
In this article...
Changes In Project Scope
According to a meta-analysis of causes of project delays, changes in project scope are among the most prevalent reasons for delays in construction projects.
That’s not surprising since the scope covers project objectives and deliverables, i.e., everything that should be done to consider a construction project completed.
Here’s an example of a project scope for constructing a new home with a tentative total project cost and a more defined timeline.
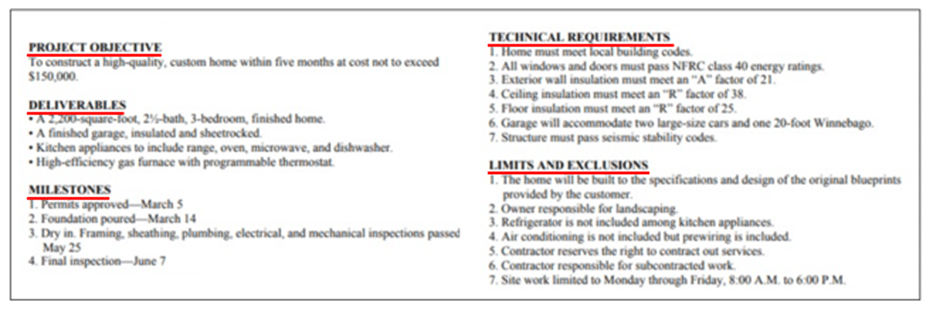
As you can see, a project scope will define at least the following:
- overall project objective (e.g., constructing a home)
- project deliverables (i.e., what the contractor should deliver)
- project milestones (significant project phases to be reached during construction)
- other specific requirements and limitations
Hence, anything that necessitates a scope change, such as a design error or omission, the investor changing their mind about materials, unexpected site conditions, etc., can throw the project schedule off course and cause delays.
Let’s say that the client decided to add another roof window to their home just before the project reached that stage of construction.
This would require a design change that would delay that project activity until the change gets approved and the design updated.
That process is well visualized in the design change management workflow below.
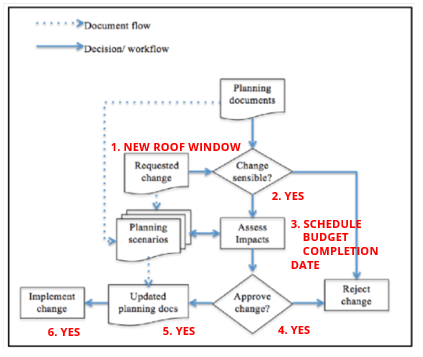
Naturally, the question remains whether the roof window in question would affect the final project completion date or not.
However, scope changes in larger construction projects can cause a cascade of interconnected delays.
The key to avoiding significant scope changes is rooted in good planning with some buffer time and float accounted for, design (using different software tools), excellent team communication during the project planning stage, and efficient change order management during construction.
Budget Inaccuracies
The saying “time is money” is particularly true in construction, where project delays (time) are directly linked to budget overruns (money).
However, this is a two-way street. In other words, budget inaccuracies (money) can also cause project delays (time).
For instance, let’s say somebody, while drafting an initial budget, seriously underestimated the quantity of a particular construction material required for a specific task.
This budgeting miscalculation can have less or more serious consequences. For example, if the material is available in storage, a few hours delay is probable.
However, suppose the material needs to be ordered and delivered.
In that case, supply chain issues involving various materials like the ones below can extend the delay, as indicated in a 2020 survey on materials shortage:
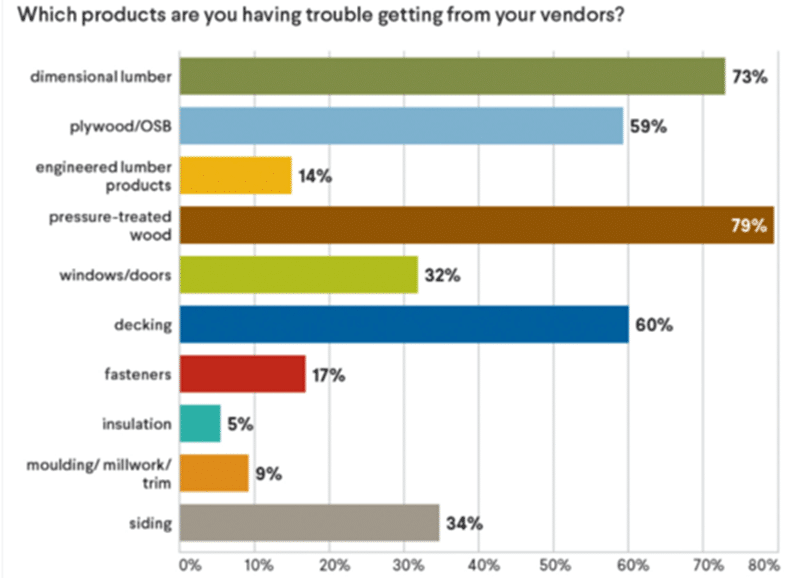
Such situations could cause a delay of a few days, weeks, or even months while the missing material is supplied or a viable alternative is found.
In some cases, initial budgeting miscalculations can delay a project even before it starts.
Like in this recent example where new cost estimates for the Soo Locks reconstruction project ended up being 2-3 times higher than the initially authorized amount.
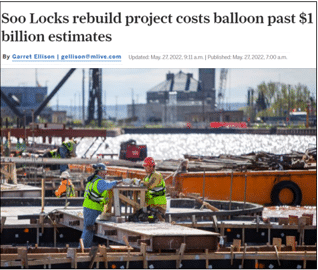
That could delay the project as Congress may need to reauthorize the new cost.
In his statement, U.S. Rep. Jack Bergman summed up why the initial project price could triple and potentially affect the schedule:
“In addition to inflation and the rising costs of everything from tools and equipment to personnel, the Army Corps made miscalculations in the original cost estimates—making the total cost of the project far higher than originally thought.”
Bergman also mentioned “inflation,” which alone can cause project delays if, for example, the project was agreed as a fixed-price job.
In such cases, rising prices can jeopardize the contractor’s cash flow, sometimes leaving them unable to pay their workers and forcing them to suspend construction works, which results not only in further delays but also in potential disputes.
In the current situation, accounting for inflation when you’re budgeting a project or including an inflation adjustment clause in your construction contract is a wise course of action.
So, yes. Budget inaccuracies do cause project delays. Especially those made when project costs are being estimated.
Problems With Available Labor
The skilled labor shortage is a long-standing problem in the construction industry. Naturally, this has only been exacerbated by the pandemic.
In 2020, 61% of contractors reported that workforce shortages caused project delays.
Faced with such problems, contractors may resort to hiring less skilled staff.
However, that can cause other issues like equipment breakdown due to improper operation, site safety concerns, and substandard work quality that requires rework, all of which can pull the project away from its original schedule.
Another labor issue causing delays is the age structure of construction workers.
For example, the 2018 Current Population Survey (CPS) revealed that 21.7% of workers in this industry were aged 55 or over, meaning that about one-fifth of workers will retire in the near future.
The map below supports these numbers.
This map from the National Association of Home Builders (NAHB) shows the median age in all states. Basically, the darker color indicates an older workforce.
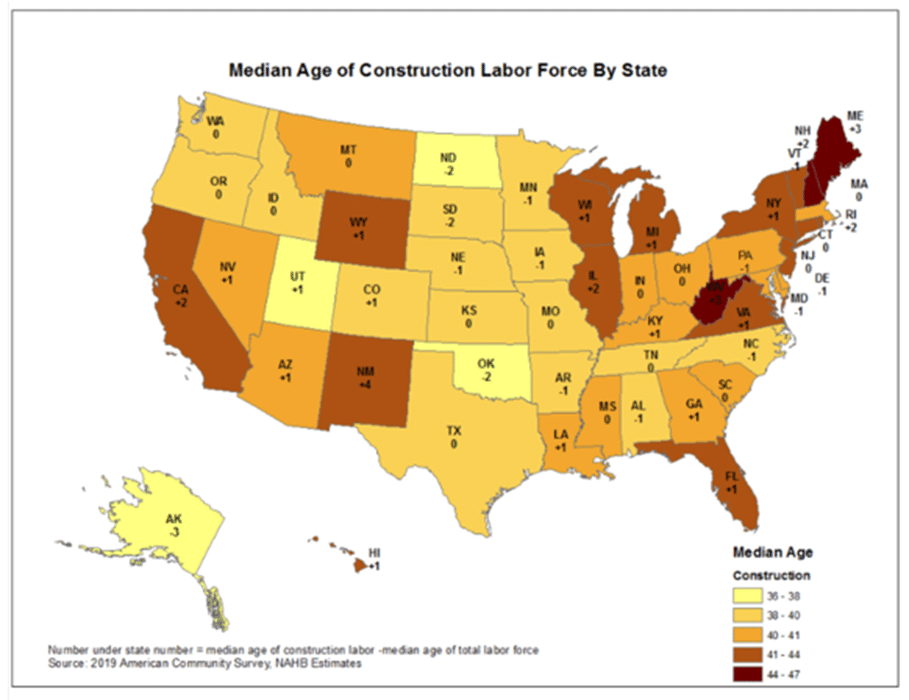
An aging workforce is not problematic just because it retires soon.
As expected, older workers have often climbed up the corporate ladder, and hold positions of construction managers, supervisors, or inspectors, which adds to the delay problem due to not having enough adequately skilled and experienced workers to do the job.
Of course, older workers, especially “irreplaceable” ones, can cause a project delay by themselves.
For example, if your master carpenter keeps missing work due to their bad back, and you didn’t plan for or already trained their replacement, there’s often not much to do but wait for them to get back.
Otherwise, you’re risking subsequent rework that would cause even more delays.
As suggested, training your younger personnel, providing mentorship and key skills transfer, and having backups are just some measures that can alleviate problems with available labor and help keep your project on schedule.
Inefficient Material and Equipment Management
If the proper materials, tools, and equipment are not available at the right time, delays follow.
Studies show that materials account for around 60% of the total project cost and that about 80% of the project schedule depends on their procurement, timely delivery, and quality.
Thus, efficient material management can prevent many project delays that could otherwise spring up.
Equipment management is focused on securing, maintaining, and scheduling construction equipment—ranging from cranes to screwdrivers—to ensure smooth jobsite operations.
Here’s what equipment management practices should involve when aiming to improve on-site productivity and minimize equipment-related delays.
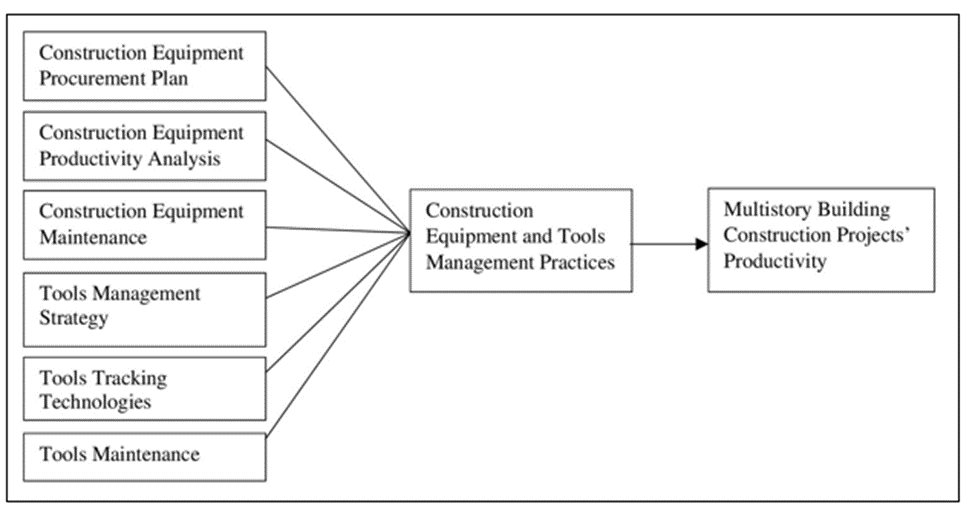
As shown, effective equipment management practices include a procurement plan, productivity analysis, maintenance, and tracking of tools and equipment.
When these practices are not properly applied, reasons for delays multiply.
For example, if the location of a piece of equipment that moves from site to site is not tracked, this might result in a transport mix-up, breakdown due to poor maintenance, misplacement, or even theft going undetected for a while.
In all these instances, one of the consequences of missing a key piece of equipment will be a delay.
Again, whether this delay will postpone the final project delivery date or the schedule has some float to compensate for it depends on good project planning and efficient construction project management, which is nowadays best achieved by using various software tools.
For example, to avoid delays stemming from inefficient material and equipment management, you can try our specialized equipment tracking software, GoCodes.
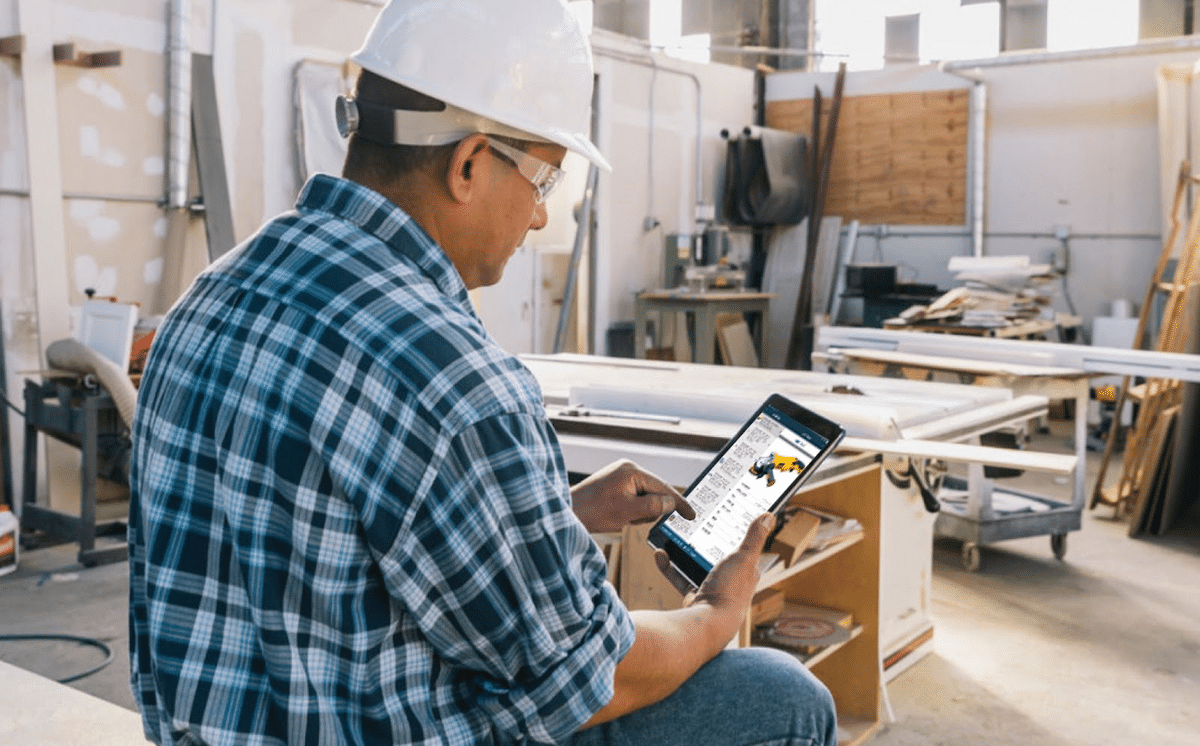
This simple and affordable solution harnesses the power of cloud software, patented QR code tags, and smartphones.
With new technological advances and the rapidly rising adoption of different construction management software tools, even small contractors can cost-effectively streamline their processes and prevent any delays associated with inefficient material and equipment management.
Poor Project Scheduling
A schedule is the backbone of any construction project. If scheduling is inadequate, that backbone can easily break and lead to delays.
Poor project scheduling may be the single biggest cause of delays in construction projects.
The reason for this usually comes down to the complexity of scheduling construction activities, accounting for their interdependencies, and integrating other scheduling elements into one detailed construction schedule.
In essence, a schedule arranges all project activities in a logical, sequential order, giving all stakeholders a roadmap of how the construction project should (ideally) play out from start to finish.
Of course, the market offers a plethora of software tools that can facilitate the organization and visualization of the project by automating many scheduling tasks.
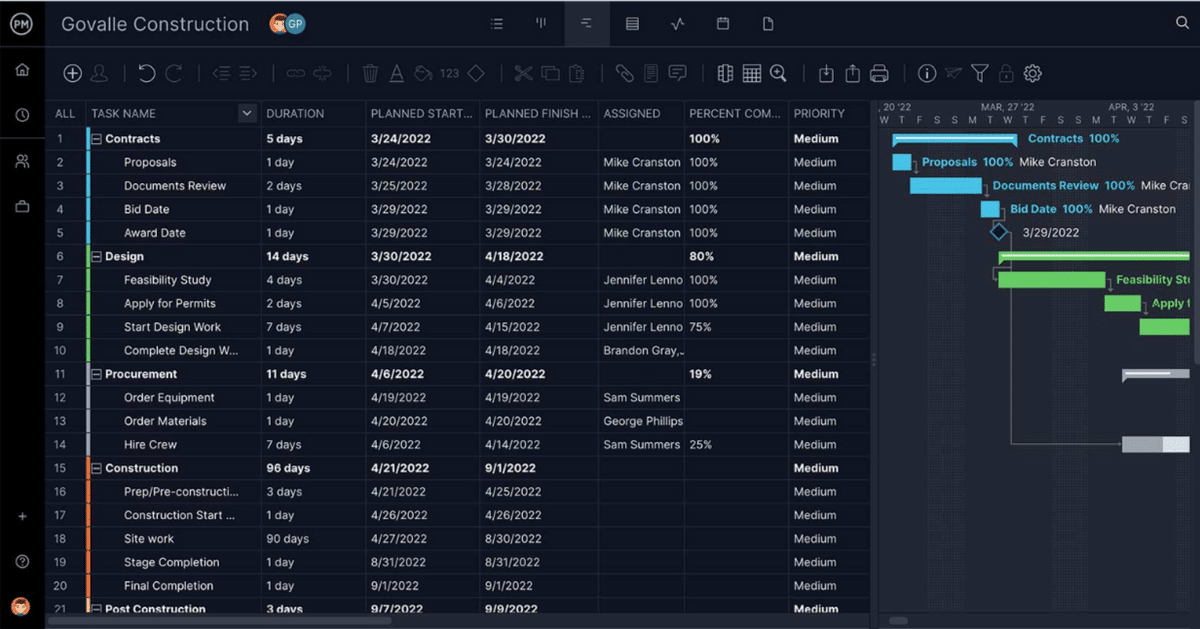
For example, a construction scheduling software will allow you to track project deliverables (tasks and phases), allocate and manage resources, monitor milestones, account for dependencies between tasks, and keep tabs on the project budget.
This will allow the project manager and other stakeholders to monitor the project’s progress.
However, even with the help of software, scheduling requires in-depth knowledge of construction activities, their sequential order, and different constraints and risks inherent to them.
Thus, to avoid creating a schedule that will cause more delays than it will prevent, the person making it (usually the project manager) should include safeguards and contingencies for various potential setbacks that may occur during construction.
For example, let’s say that excavation works are scheduled to be completed in one week, and you added a few extra days in anticipation of potential issues.
Suppose the crew encounters unforeseen adverse ground conditions (e.g., a large rock under the surface where foundations are excavated). In that case, the additional time will help keep the schedule on track or at least minimize the resulting delay.
If excavation works were completed as planned, you can keep that extra time as a backup and use it to avoid a delay in some other activity, thus keeping your project on schedule.
Bad Weather Conditions
Adverse weather conditions have long been one of the top reasons for delays in construction projects.
However, this has been exacerbated in recent times by the progressing climate change and a growing number of extreme weather events.
As you’ll see below, reducing the negative effects of weather on the schedule requires good planning and scheduling, which can be supported by climate data analysis and some innovative solutions.
Let’s start with a UK study revealing that bad weather extends the duration of construction projects by 21% on average.
In light of our previous section on project scheduling, this means that just the extra time allocated for bad weather would need to be at least 20% of the total project duration.
However, there are ways around this, and one of them can be reusable weather enclosure systems (RWES) like this one.
For example, this construction envelope protects workers, equipment, and materials from inclement weather, thus avoiding weather-related project delays.
Of course, even this system can’t provide protection from tornados or mega-storms.
That’s why such events are usually contracted as force majeure events, releasing the contractor from liability for delays.
The above-mentioned study also revealed that using historical climate data to plan the construction process better and predict possible setbacks due to bad weather can reduce the average project duration by 16%.
Thus, although weather can’t be controlled, you can take steps when contracting and scheduling the project that can prevent or minimize delays caused by adverse weather conditions.
Conclusion
To sum up, these six top reasons for project delays can be successfully minimized by good project planning, budgeting, and scheduling.
When this is coupled with strong change management, quality control, and continuous progress monitoring, delays can be efficiently managed throughout the project lifecycle.