If you’re a construction company owner or manager, it’s highly likely you’re already familiar with a construction phase plan, albeit maybe under a different name.
In essence, this key document serves as the cornerstone of construction safety, ensuring a secure work environment for your team.
In this article, we’ll unravel the intricacies of what this plan truly entails—why it’s indispensable, who shoulders its preparation and implementation, and the crucial elements it should encompass.
Let’s dive in.
In this article...
What is a Construction Phase Plan
Before we explain what a construction phase plan is, let’s deal with varying terminologies (names) you can encounter depending on where your business or your construction project is located.
For instance, the terms “Construction Phase Plan (CPP)” or “Construction Phase Health and Safety Plan (CPHSP)” are predominantly used in the U.K.
These terms are less used in the U.S., where you may come across names such as:
- Construction Safety and Health Plan (CSHP),
- Site-Specific Safety Plan (SSSP),
- Construction Safety and Phasing Plan (CSPP),
- Health and Safety Plan (HASP), etc.
Other countries may have their own distinct names for similar plans, often aligning with local regulations and industry practices.
To illustrate, here’s an example from Australia.
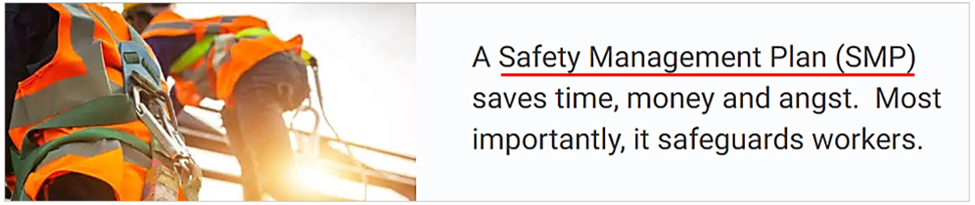
While terminologies vary, these documents essentially share the same purpose as a CPP.
As the above image reveals, their primary focus is on safeguarding workers and maintaining a secure work environment.
Specifically, a CPP serves as a comprehensive framework for systematically addressing health and safety concerns throughout the construction process.
Therefore, a CPP is designed to anticipate and mitigate construction site risks, ensure the well-being of workers, and prevent project delays that could arise if one or more of those potential risks become a reality, like in the case below.
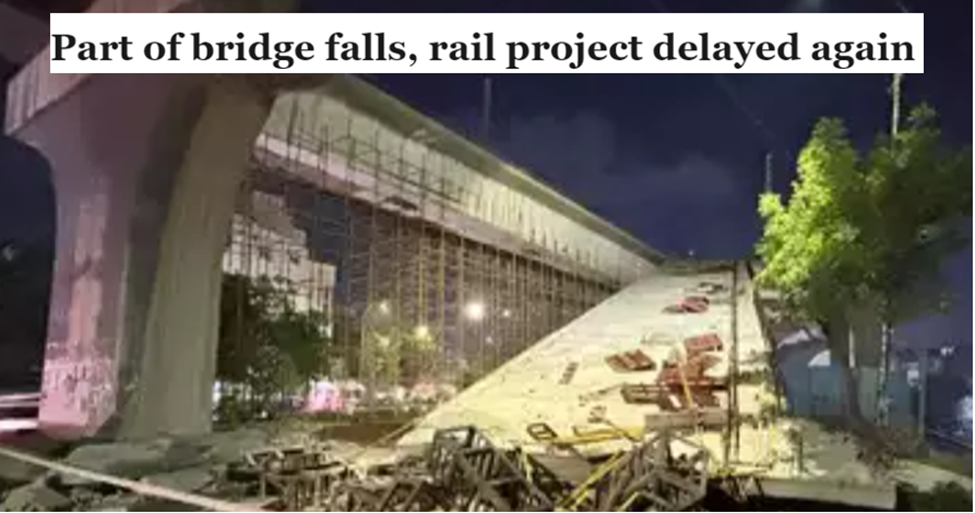
As we’ll see later, CPPs outline key project stakeholders, construction site hazards, safety measures, and emergency protocols, thereby contributing to the prevention of accidents and saving both time and resources.
As such, CPPs are always prepared in the preconstruction phase, and then reviewed and updated as the project progresses.
Additionally, CPPs play a crucial role in regulatory compliance, as we’ll discuss in the next section.
Overall, a construction phase plan (or whatever else it might be called) is a key document that serves as a strategic roadmap for contractors, ensuring the safety of workers and all other on-site personnel during construction.
Why Construction Companies Need It
Considering the inherently dangerous nature of construction, contractors need a CPP to ensure worker safety and comply with related laws, regulations, and guidelines.
Naturally, these two goals are closely related since the primary reason for regulating construction health and safety is to prevent accidents and injuries on worksites.
In the United States, construction site safety is primarily regulated through a combination of federal and state-level agencies.
The Occupational Safety and Health Administration (OSHA), a federal agency under the Department of Labor, plays a central role in establishing and enforcing safety standards for the construction industry.
The highlighted text in the image below nicely sums up the main reason behind OSHA’s regulations and standards and underscores why construction companies need a CPP.
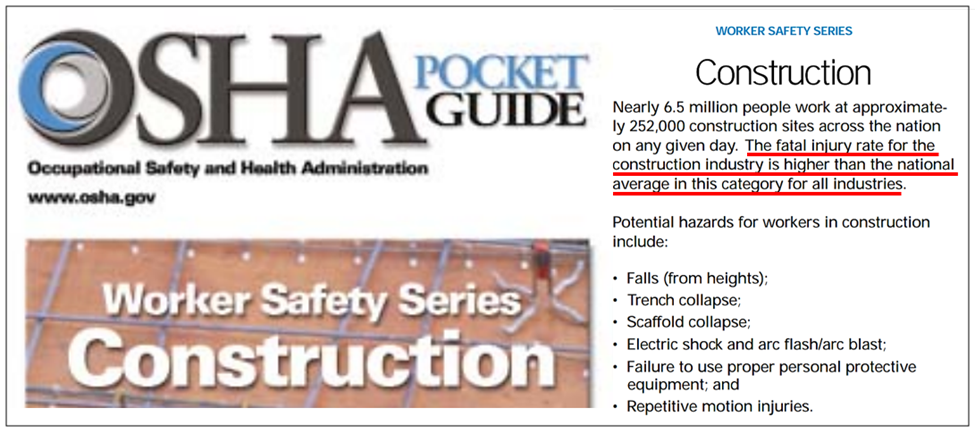
OSHA standards cover a wide range of topics, such as fall protection, hazard communication, electrical safety, and more.
They also include guidelines for scaffolding, excavation, and trenching, personal protective equipment (PPE), and other critical safety aspects.
All these elements are typically covered in project-specific CPPs.
Furthermore, some U.S. states operate their own OSHA-approved safety and health plans, which may include additional regulations or standards, such as the example from Minnesota below.
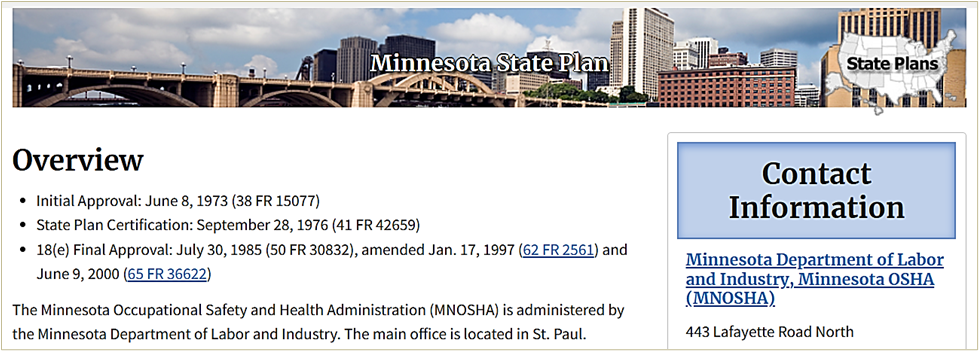
These state plans must be at least as effective as federal OSHA standards, and they often address specific regional needs.
Although CPPs are not explicitly mentioned, OSHA’s “Recommended Practices for Safety and Health Programs in Construction” state that:
“Employers in construction work must have a program that includes measures to detect and correct workplace hazards.”
This underscores the imperative for construction employers to have a comprehensive safety program, effectively indicating the necessity of drafting a CPP or an equivalent plan serving the same purpose (e.g., a Site-Specific Safety Plan (SSSP)).
For comparison, CPPs in the U.K. are legally mandated under the Construction (Design and Management) Regulations of 2015 (CDM 2015 regulations).
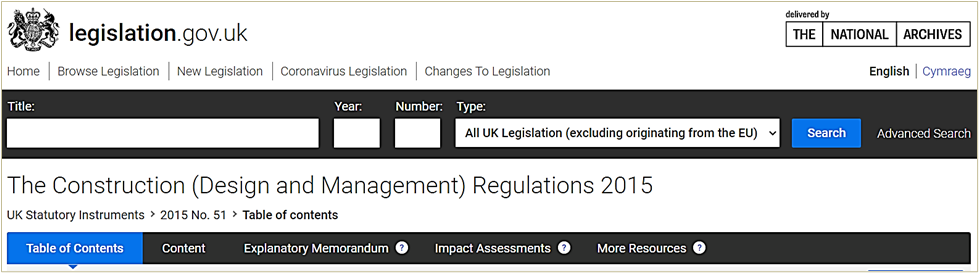
Under these regulations, all projects need to have a CPP.
Of course, the scope and level of detail of such plans will depend on project size, complexity, and the number of people working on it.
Regardless of the country, state, or plan’s name, the CPP serves as a proactive tool that establishes a structured approach to identifying, assessing, and mitigating construction site risks throughout the construction process.
As such, these plans assist contractors in fostering a culture of safety and adherence to regulations on their projects.
In summary, construction companies need a CPP to help them ensure worker safety and regulatory compliance and to build a reputation as a safety-conscious business.
Who’s Responsible for Making Construction Phase Plans
The primary responsibility for drafting a CPP rests with the principal (main) contractor managing the project, typically embodied by the project manager.
However, if the project manager is engaged by the project owner before the selection of the general contractor and continues to oversee the project in that capacity, they are likely to delegate this responsibility.
In such scenarios, the CPP is usually prepared by the main contractor upon their selection (either through the bidding process or by direct appointment).
This ensures that the CPP aligns with the overall project plan, the appointed contractor’s proposed construction methods, and the agreed schedule.
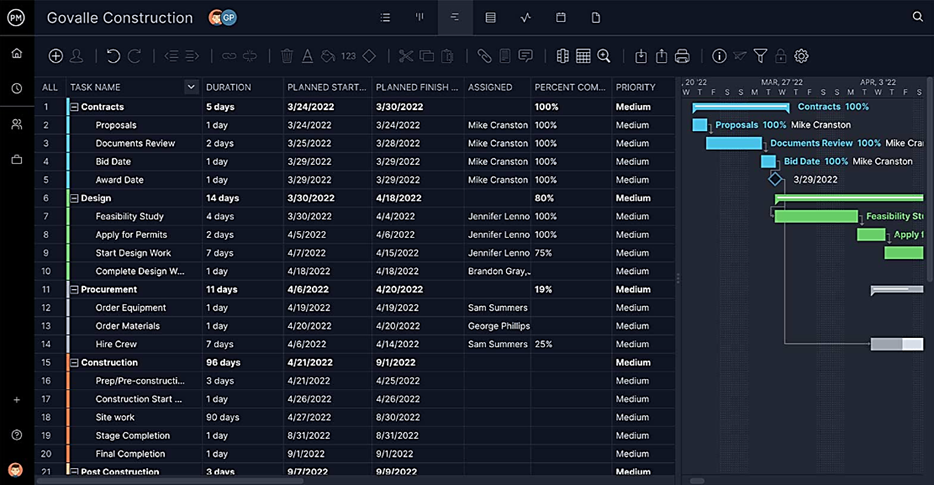
For instance, the project schedule can influence the timing of specific safety measures, ensuring that critical precautions are implemented in tandem with key construction milestones and activities.
That’s why the principal contractor’s hands-on experience is crucial for ensuring that the CPP is tailored to meet project-specific requirements and adheres to relevant safety regulations.
The contractor will typically collaborate with construction safety officers or health and safety managers who are proficient in identifying potential hazards and recommending suitable mitigation measures.
Likewise, the collaborative nature of construction projects means that CPP preparation often requires input from various stakeholders, including architects, engineers, and subcontractors.
Their input can help identify risks and determine safety measures related to their specific trade or scope of work.
The involvement of all these professionals is crucial for enhancing the overall effectiveness of the CPP.
To recap, the primary responsibility for CPP creation rests with the main contractor/project manager.
However, this process extends beyond a single role, involving a collaborative effort to address the diverse aspects of construction safety.
What Should a CPP Contain
Having covered what a CPP is, why it’s important for construction companies to have it, and who’s responsible for its creation, let’s see what such a plan should contain.
Of course, every CPP will be specifically tailored to the construction project at hand, meaning its format and content can vary based on the unique health and safety requirements of each project.
That said, there are some essential components that a comprehensive CPP should include, which we listed below.
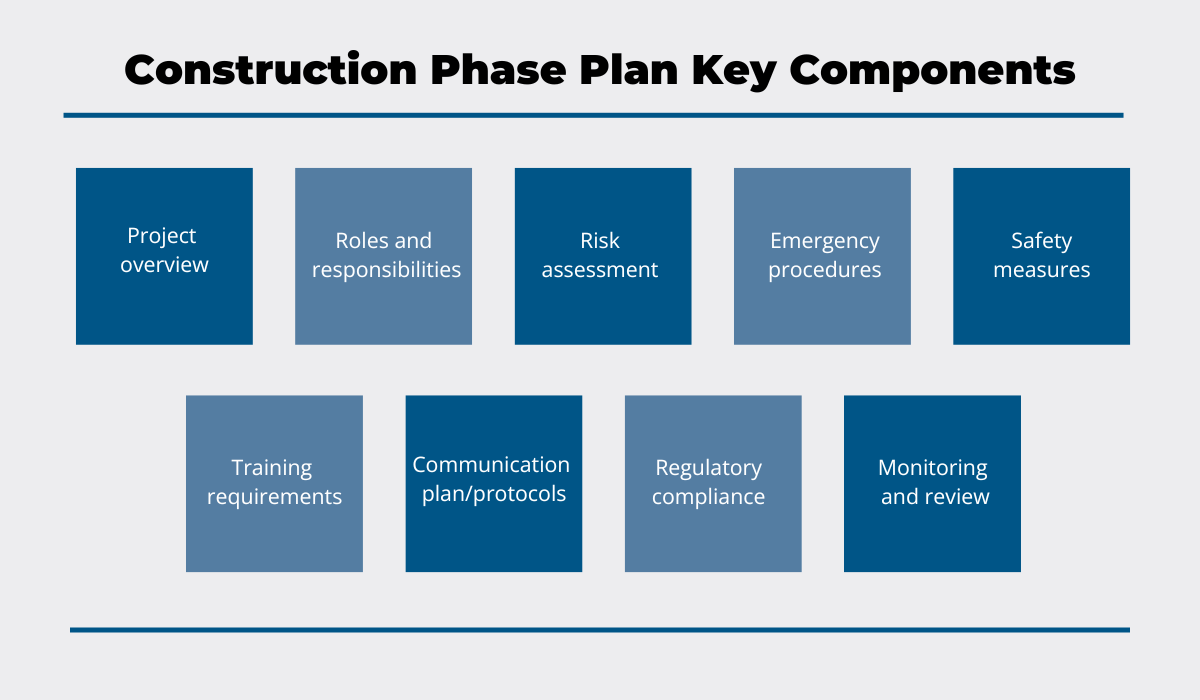
As you can see, many CPPs start with the project overview, which describes the construction project, its scope, location, and key stakeholders (with their contact info included).
This component typically continues by defining the roles and responsibilities of individuals involved in the project, outlining who’s accountable for specific safety measures.
The next critical element is risk assessment, which identifies potential hazards and provides strategies to mitigate them, ensuring a proactive approach to safety.
It’s important to note here that this risk assessment is distinct from the Risk Assessment Method Statement (RAMS).
The RAMS is more detailed and typically includes specific methods for carrying out high-risk activities.
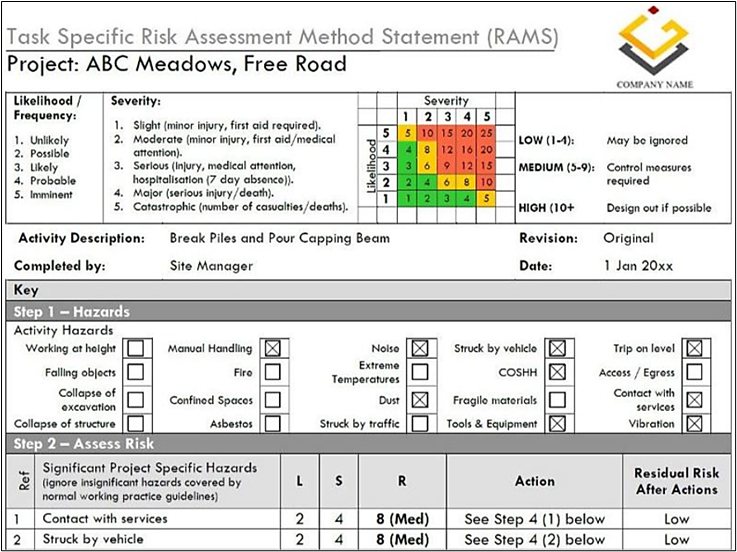
As illustrated, the RAMS focuses on the details of risk management for particular tasks while the CPP provides an overall framework for safety.
Next, emergency procedures list the proper sequence of actions required when responding to emergencies, including evacuation procedures, first aid measures, and initial response protocols.
This is followed by safety measures, which define specific safety protocols and measures to be implemented on the construction site.
These should address requirements related to, for example, fall protection, personal protective equipment (PPE), machinery safety (LOTO procedures), and jobsite warning signage.
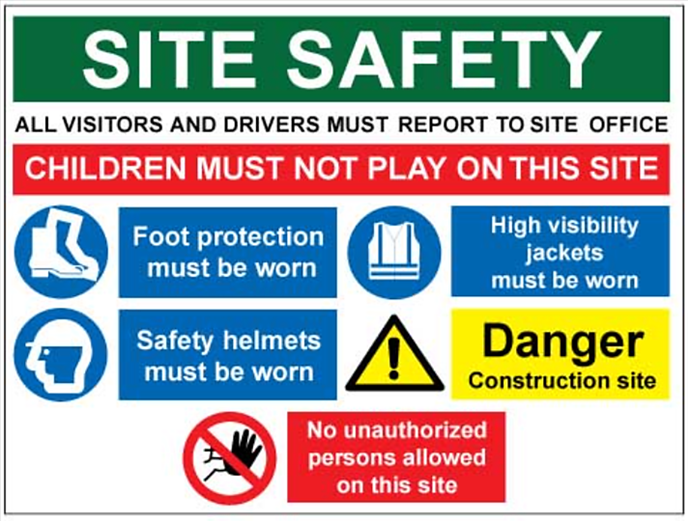
Next, training requirements identify training needs for on-site workers and equipment operators, ensuring that everyone is adequately trained to handle potential risks, as well as properly supervised.
The communication plan (protocols) establishes clear channels for information exchange, ensuring everyone (workers, subcontractors, regulatory authorities) is informed about safety procedures and project updates.
Regulatory compliance ensures that the CPP is aligned with local, state, and federal regulations governing construction safety.
This component can incorporate jobsite rules and regulations, as well as jobsite access and security measures, detailing procedures for controlling access to the construction site to manage both safety and security.
Lastly, monitoring and review procedures, including record-keeping and documentation requirements, are established for continuous monitoring and periodic review of the CPP to ensure its ongoing effectiveness.
Of course, the listed order of CPP components is illustrative, and the specific order may vary based on the unique requirements and priorities of each construction project.
As we explored the diverse elements within a CPP, let’s now delve into how these components can come together.
What Does a CPP Look Like
In this section, we’ll provide two examples illustrating what a CPP can look like.
For instance, here is the table of contents of a site-specific health and safety plan (HASP) for earthwork, excavation, and other construction project activities prepared by Stantec Consulting Services Inc.
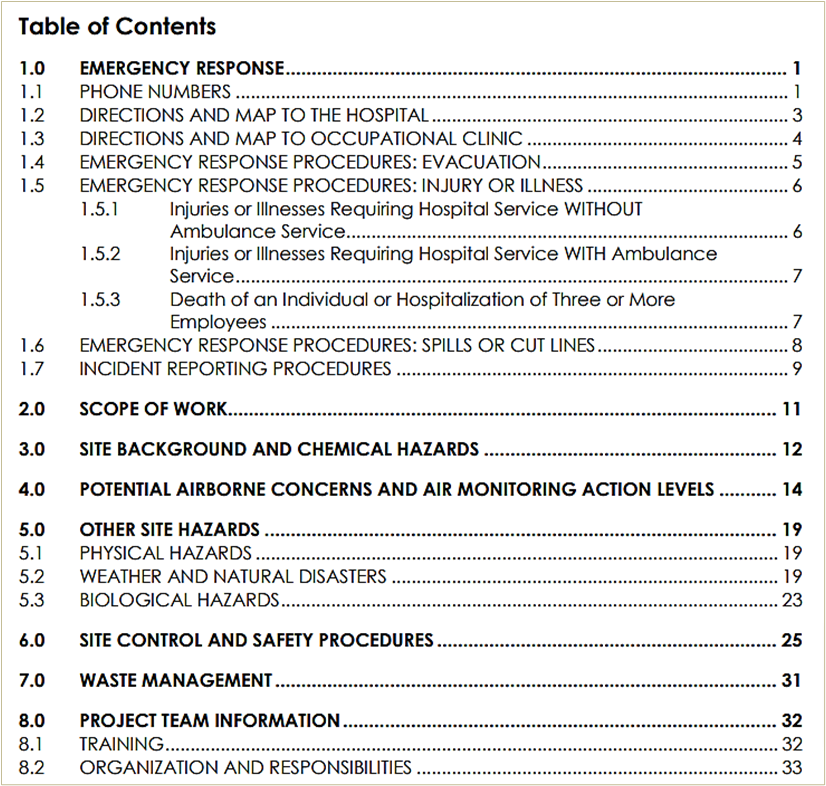
As you can see, this plan starts with the most critical info, such as phone numbers for emergency response and directions to the hospital.
It continues with emergency procedures, including incident reporting requirements.
Then, it moves to describe the project’s scope of work.
After that, different hazards are specified in order of their importance, highlighting chemical and potential airborne hazards, followed by other relevant risks.
Site control and safety procedures are described next, detailing specific safety measures.
It concludes by providing the project team info and listing training requirements, organizational setup, and responsibilities of key personnel in charge of construction safety.
For comparison, here is the table of contents of one simpler CPP template.
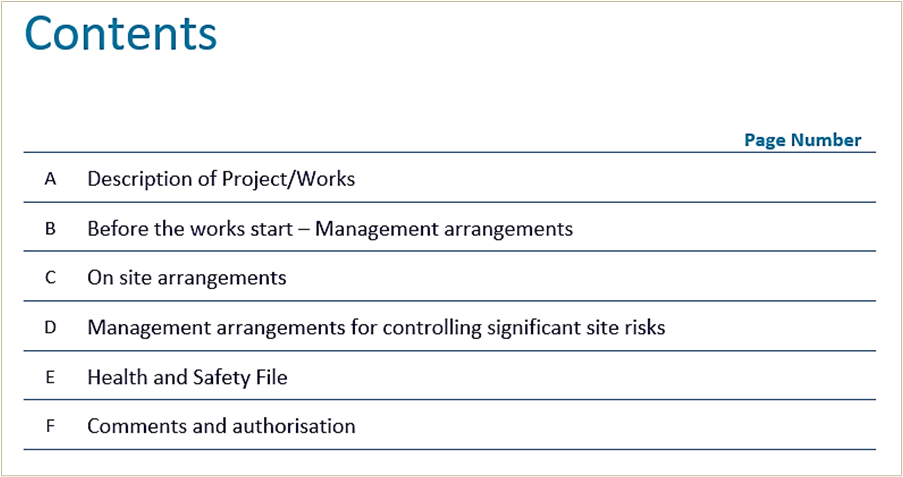
This template starts with the project description, including details on the project team, health and safety goals, and site rules.
Next, it covers the safety management structure and responsibilities followed by on-site arrangements, including items like site security, on-site training, and site induction.
Under item (D), it specifies management arrangements for controlling significant site risks, detailing how they should be addressed.
The template’s health and safety file includes details like:
- a brief description of the works performed,
- any non-eliminated hazards and how they’re addressed,
- any hazardous materials used.
The final item is left for comments and authorizations.
These two examples show that a CPP can be arranged in different ways while still containing all the key components we covered in the above section.
Conclusion
Finally, just a few key highlights.
A construction phase (health and safety) plan is a key document for ensuring on-site safety for both your workers and other personnel, allowing you to identify, eliminate, or proactively manage jobsite hazards.
When properly prepared, implemented, and monitored, a CPP enables you to prioritize safety, reduce the risk of worksite accidents and injuries, and ensure compliance with safety regulations.
Ultimately, this leads to enhanced operational efficiency, reduced costs, and improved reputation of your construction business.