Key Takeaways:
- Asset tags support centralized inventory by improving tracking and workflows.
- Organized storage helps minimize inefficiencies and security risks.
- Geofence-enabled GPS trackers are the best tagging option for high-value machinery.
- Effective tracking relies on employee adoption and continuous improvement.
Equipment tracking takes the spotlight every time a major case of tool theft comes to light.
However, construction businesses are often less affected by brazen thieves than by inadequate tracking practices which lead to huge replacement costs, inefficiencies, and project delays.
Strengthening your tracking practices is essential, and this article will show you how—step by step.
In this article...
Step 1: Create a Centralized Equipment Inventory
You can’t keep track of all your tools and equipment without a centralized inventory.
A comprehensive list of construction equipment ensures no tool is overlooked or unaccounted for, making it easier to allocate assets when and where they’re needed most.
So, create an equipment inventory.
Include as many details as possible, starting with basic information such as the equipment’s:
- Name
- Model
- Serial number
- Purchase date
- General condition
The next step is deciding how to organize this information—whether through spreadsheets or a dedicated software solution.
Many construction businesses still favor spreadsheets because they’re affordable and versatile, with many different templates and tutorials, like this one by Fleetio, available for free.
Source: Fleetio on Youtube
A spreadsheet inventory is a solid start, especially for smaller businesses, but it becomes inefficient at scale.
As your inventory grows, it will take more time to create or remove tool entries and update service information.
Not to mention the increasing risk of errors.
These challenges are precisely the reason why James Vowles, Team Principal of Williams Racing, criticized the F1 team’s long-time use of an Excel spreadsheet listing over 20,000 parts.
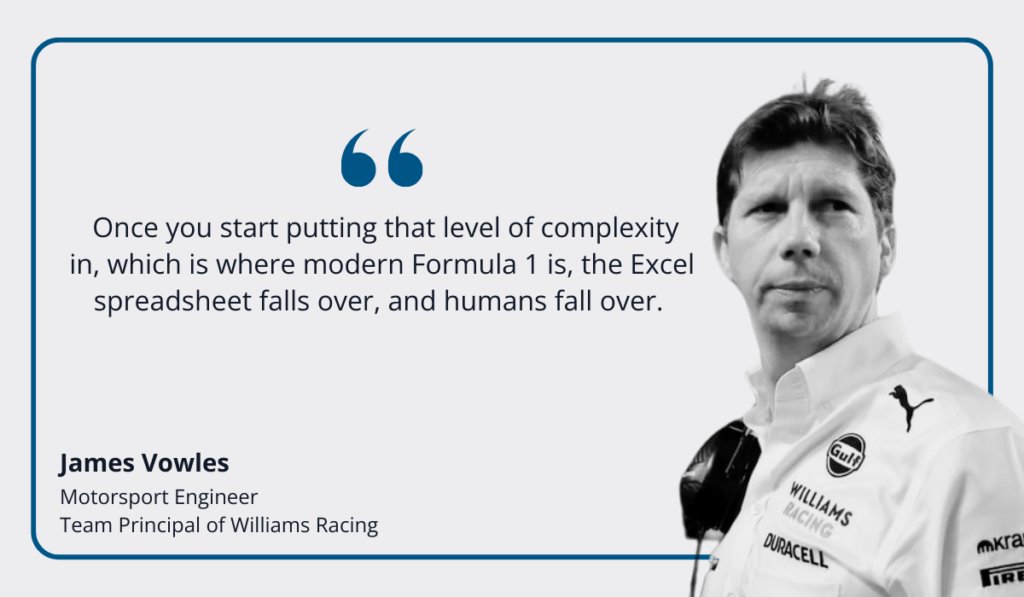
Illustration: GoCodes Asset Tracking / Quote: Ars Technica
Moving tools and equipment between multiple job sites is a different, yet equally complex task—but advanced inventory tracking solutions can simplify both.
They offer plenty of possibilities, such as increased visibility and smooth navigation.
The dashboard below shows a fraction of the information you can access and update from any device by using a comprehensive asset management solution like our GoCodes Asset Tracking.
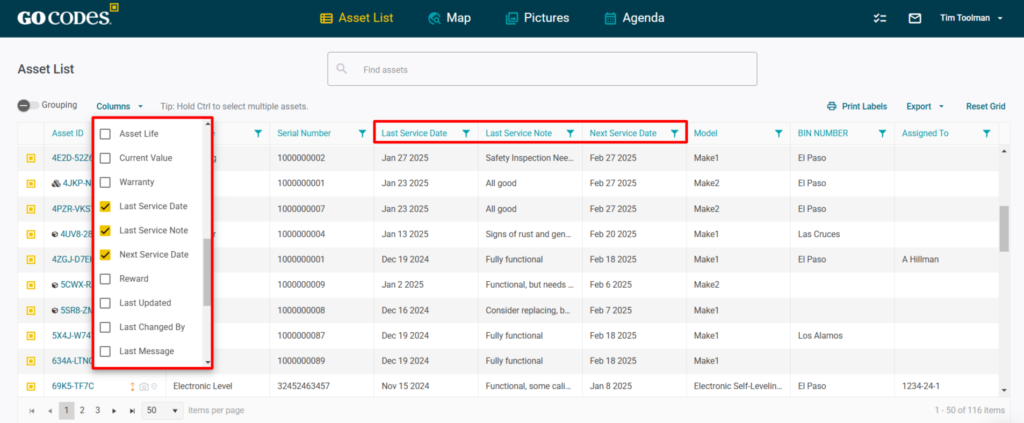
Source: GoCodes Asset Tracking
All in all, both spreadsheets and more advanced inventory tracking solutions can support your inventory management efforts.
The key is to strike the right balance between your current needs and future growth.
Step 2: Label Each Tool for Easy Identification
Managing countless tools requires easy identification and traceability.
Asset tagging enables both.
Labeling your equipment and assigning a unique ID number to each piece allows you to differentiate between several sets of the same tools while establishing ownership.
Construction companies typically do this using one of these three tagging options, but they can also combine them to maximize benefits:
Barcodes | Very affordable and widely used. |
RFID tags | Enable quick, multi-item scanning. |
QR codes | Cost-effective and store extensive information. |
You can see all three options below:
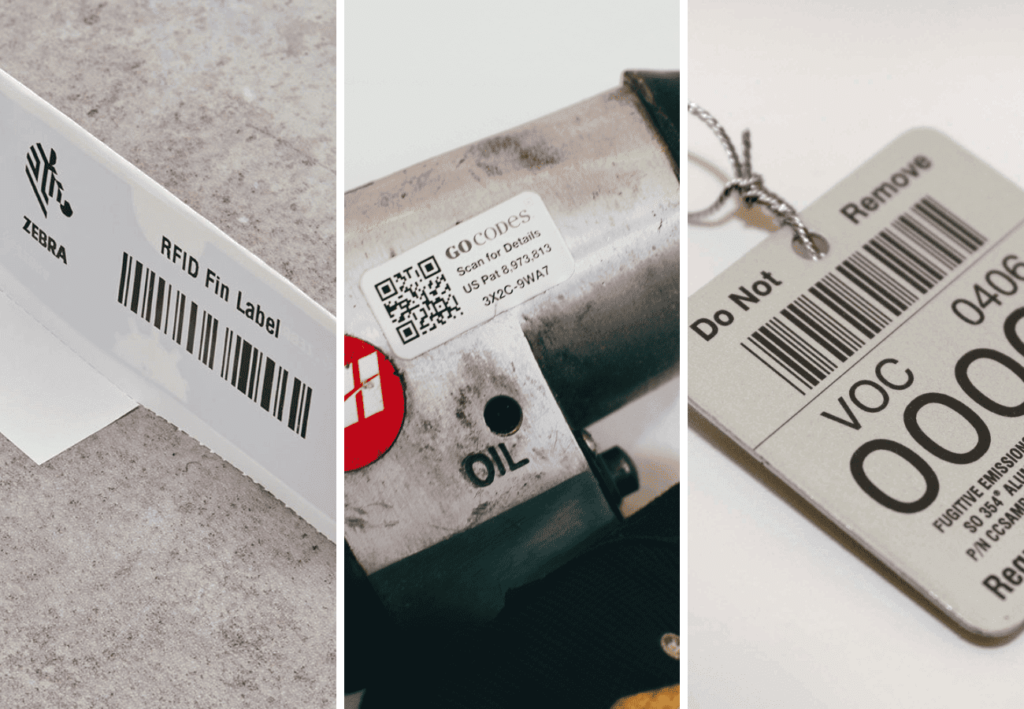
Source: GoCodes Asset Tracking
Each tagging method has its own strengths, and choosing the right one depends on factors such as ease of use, cost, and the tracking environment.
For example, barcodes and QR codes are inexpensive and simple to set up, while RFID systems require specialized readers and have higher upfront costs.
Moreover, harsh outdoor environments require durable, anodized labels that have increased resistance to chemicals, abrasion, and high temperatures.
For best results when applying labels, choose a visible, easy-to-scan area and clean the surface beforehand.
Step 3: Implement a Check-In/Check-Out System
Implementing a check-in/check-out system is the next step towards boosting efficiency and ensuring accountability.
The main aim of these systems is to optimize tool allocation across multiple jobsites and reduce the number of misplaced or stolen tools.
Construction companies don’t file claims to a reporting agency when tools and equipment vanish from job sites, so it’s difficult to establish the magnitude of this problem.
Nevertheless, CIOB’s findings shed some light on this issue.
In 43.4% of cases, tool theft was attributed to either directly employed or subcontracted staff.
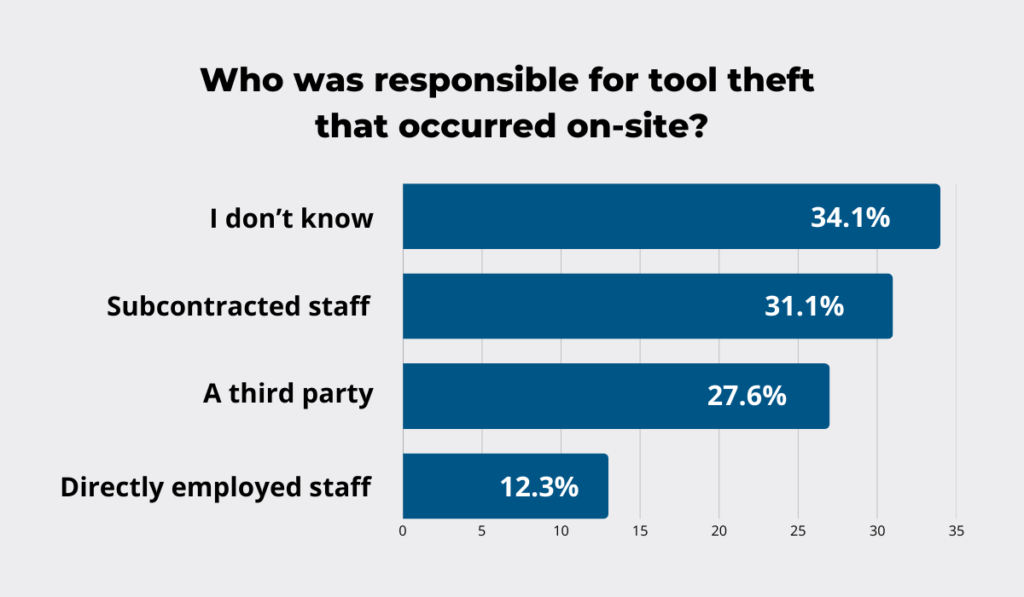
Illustration: GoCodes Asset Tracking / Data: CIOB
However, in 34.1% of incidents, the responsible party remained unknown.
Founder of SJ Construction Consulting, Scott Jennings, explains that in many cases businesses simply can’t hold their staff accountable even when tools go missing.
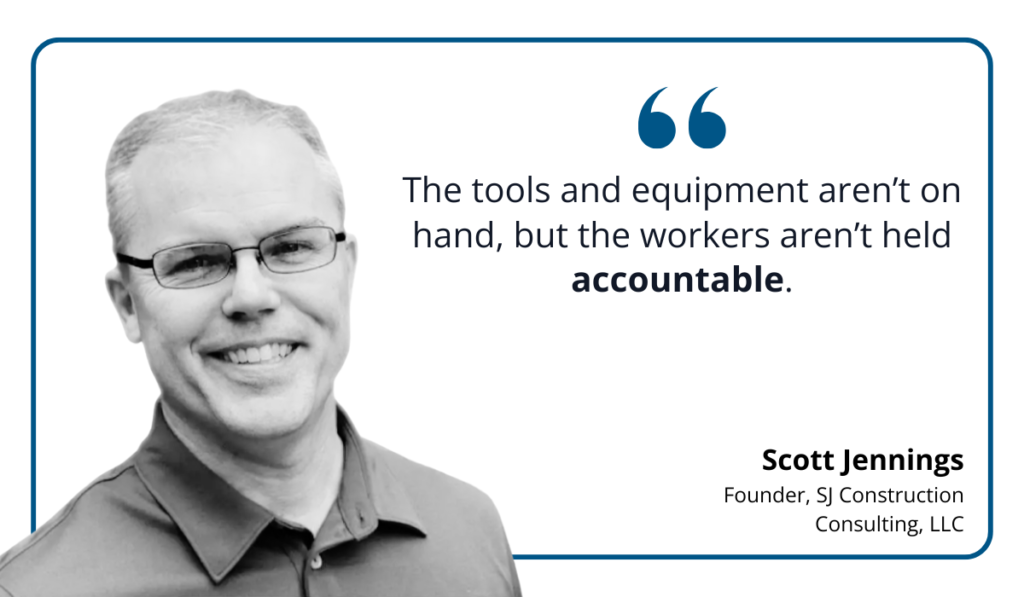
Illustration: GoCodes Asset Tracking / Quote: Construction Dive
Check-in/check-out systems help eliminate the uncertainty.
Since every tool is scanned before use, there’s an additional incentive and responsibility to return items.
The system automatically captures check-out timestamps, and stores notes on all items.
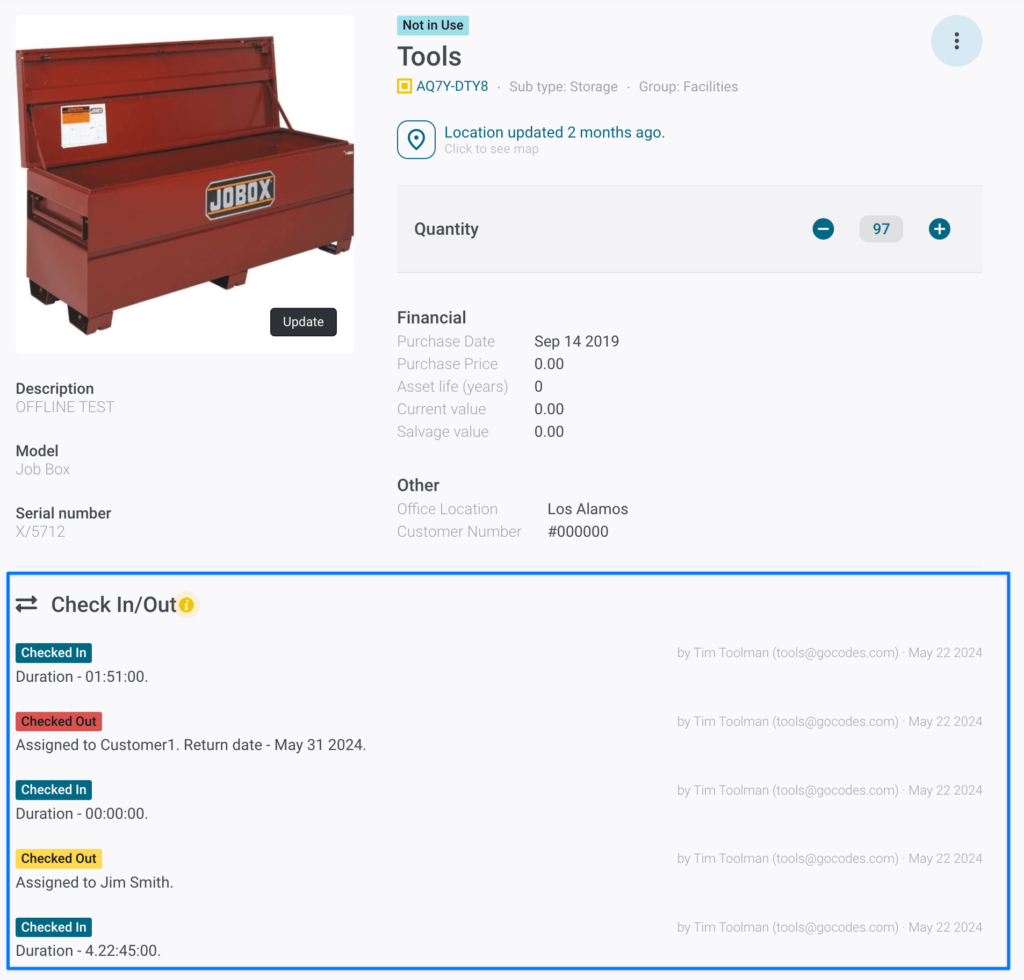
Source: GoCodes Asset Tracking
Given the fast-paced construction environment, it may take time for all workers to consistently use the system.
To encourage compliance, consider introducing a simple backup log like the one shown below.
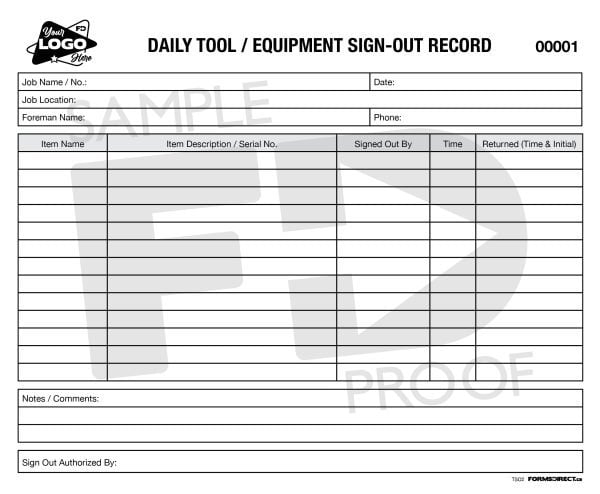
Source: Forms Direct
While this printable sheet captures only basic information, it serves as a helpful reminder for less tech-savvy crew members to sign out equipment, thereby reinforcing good tracking habits.
All in all, cultivating a culture of responsibility across teams takes time, but digital check-in/check-out systems and supplementary manual logs can speed this up substantially!
Step 4: Store Tools in Designated Locations
Even the best tracking systems lose their effectiveness if tools are scattered across the job site or warehouse.
Tools and equipment need designated storage locations.
It’s the fastest way to quickly locate specific tools and maintain an accurate inventory.
Plus, you’re doing a lot to bolster security.
According to a former operations manager, Mike Stokes, you can effectively organize your tools by following three simple rules.
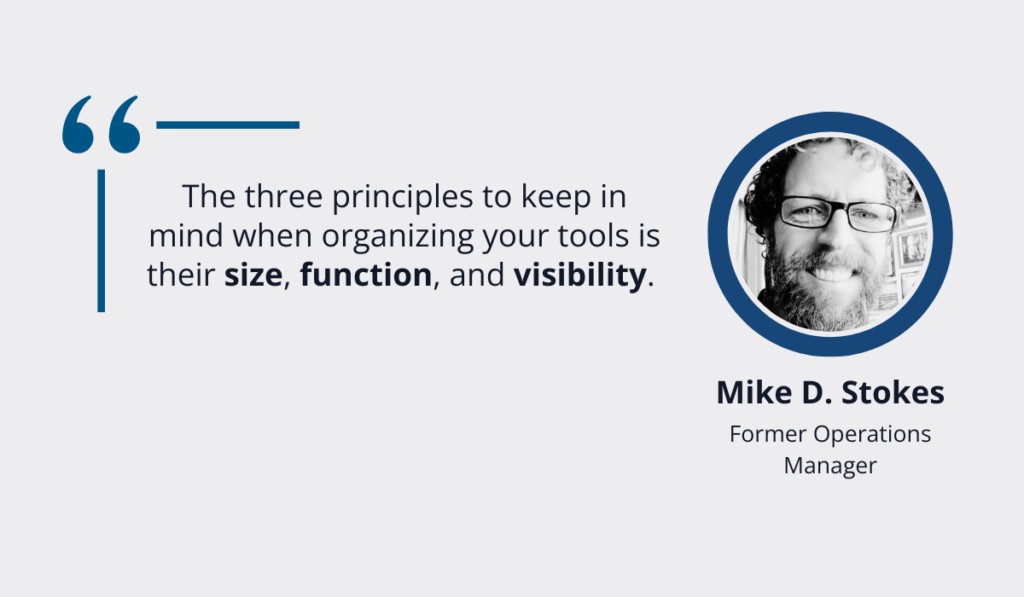
Illustration: GoCodes Asset Tracking / Quote: The Regenerative Home on Youtube
Although Stokes focuses on hand tools, the same applies to power tools and other types of equipment.
The point is to keep it intuitive and make use of different storage options, such as labeled shelves, stackable bins, and tool cribs.
Using labels or color-coding systems, for example, helps with tool visibility, saving you time spent looking for tools and also reducing losses.
Or take shadow boards.
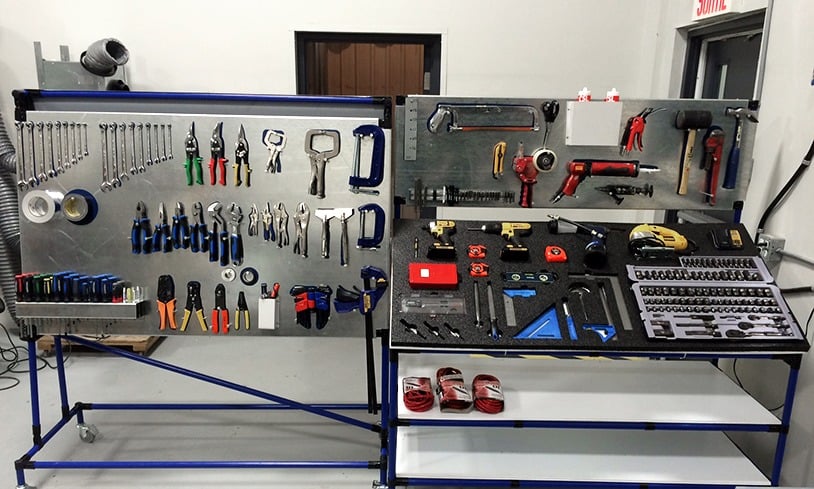
Source: Flexpipe
The outlines on the board remind employees where specific tools should be placed when they’re not in use while improving retrieval time.
Here’s a quick comparison between unorganized tooling and shadow boards.
Source: Peak Visual Management on Youtube
The tools stacked on the shadow board were retrieved nearly 10 times faster on average, which translates to potential savings of three working days a year.
Besides efficiency, there are also security considerations.
Assets should be stored indoors whenever possible, with high-value equipment placed in designated areas with restricted access.
Tool cribs are ideal for smaller tools and handheld power equipment while on-site shipping containers can even hold smaller machinery overnight or during non-working hours.
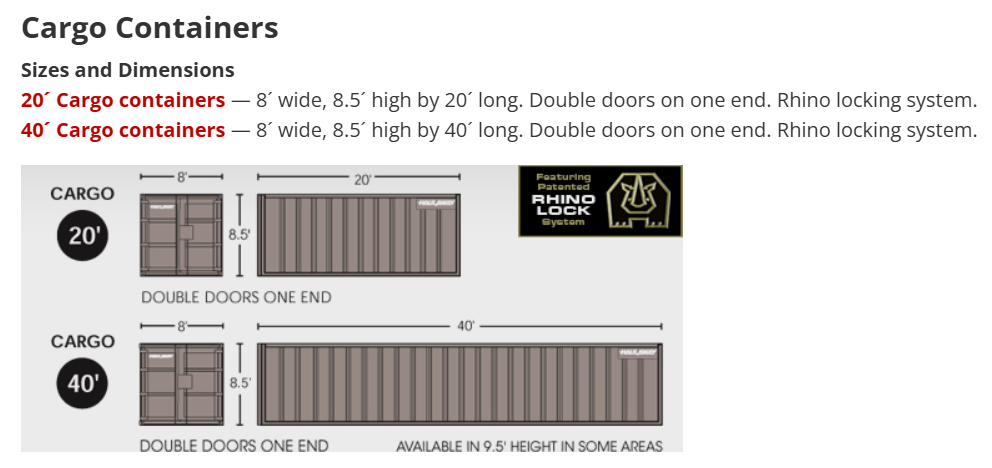
Source: Haulaway
Ultimately, combining different storage options while investing in a tracking system is the surest way to promote efficiency and prevent loss.
Step 5: Use GPS for High-Value Equipment
Critical assets and high-value equipment require real-time tracking for an extra layer of security.
Even the most secure shipping container can be broken into, and when costly pieces of machinery go missing, construction companies have to deal with replacement costs and delays.
Fortunately, when you attach real-time GPS trackers to your expensive tools and machinery, you can monitor their location in real time and be alerted of any suspicious activity.
Moreover, it’s the only kind of tracker that makes it possible to locate and retrieve your assets even if they’ve been stolen.
This case from 2024 testifies to it: one GPS tracker ended up leading law enforcement to a large stash of stolen construction equipment.
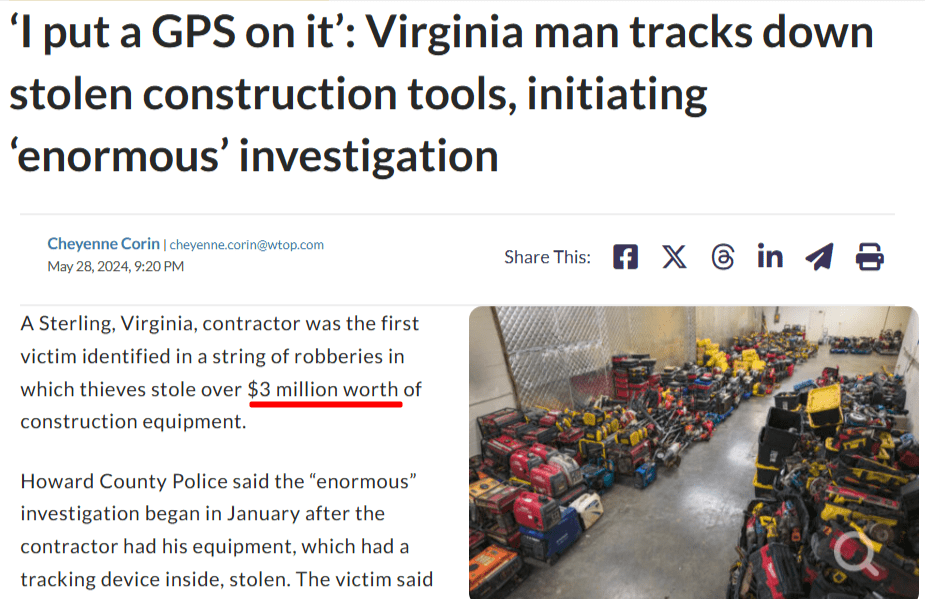
Source: WTop
Most of the victims in this case had long since given up on their stolen tools and replaced them, but this is not always an option with critical pieces of equipment.
That’s why it’s important to invest in powerful GPS tracking devices that enable real-time tracking, which increases operational efficiency and supports asset retrieval.
GPS trackers are generally hard to remove or deactivate, making it difficult for thieves to disable tracking. Even when they are not completely hidden, their presence alone can discourage theft.
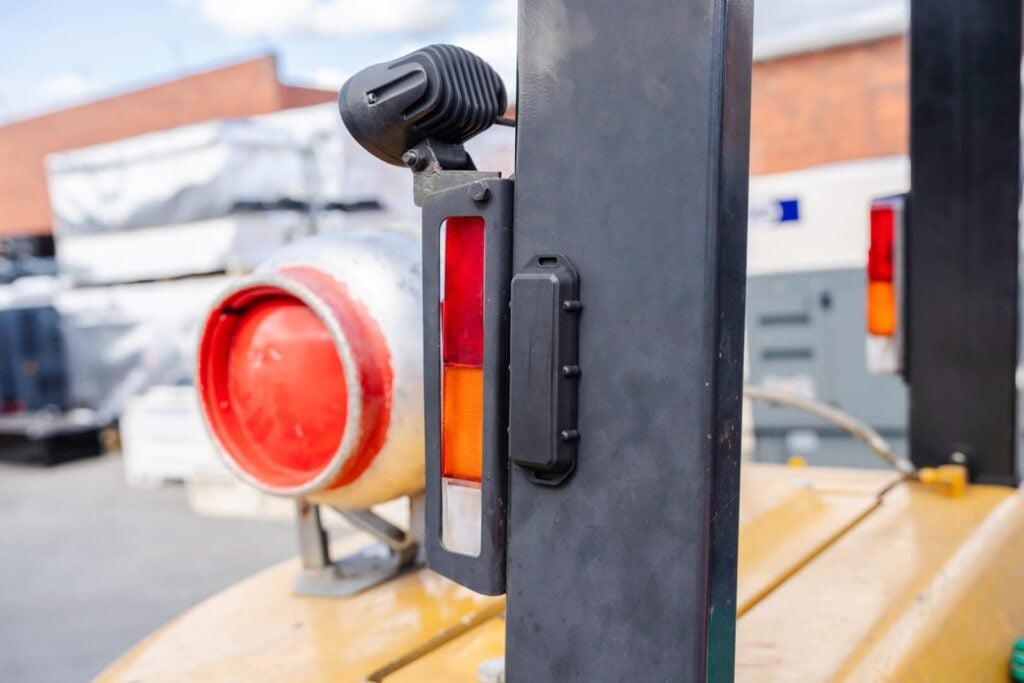
Source: GoCodes Asset Tracking
Moreover, more advanced devices have integrated geofencing capabilities, which makes things even more difficult for brazen thieves.
Geofences are invisible, monitored perimeters that can be set up around the whole construction site or designated areas, as pictured below.
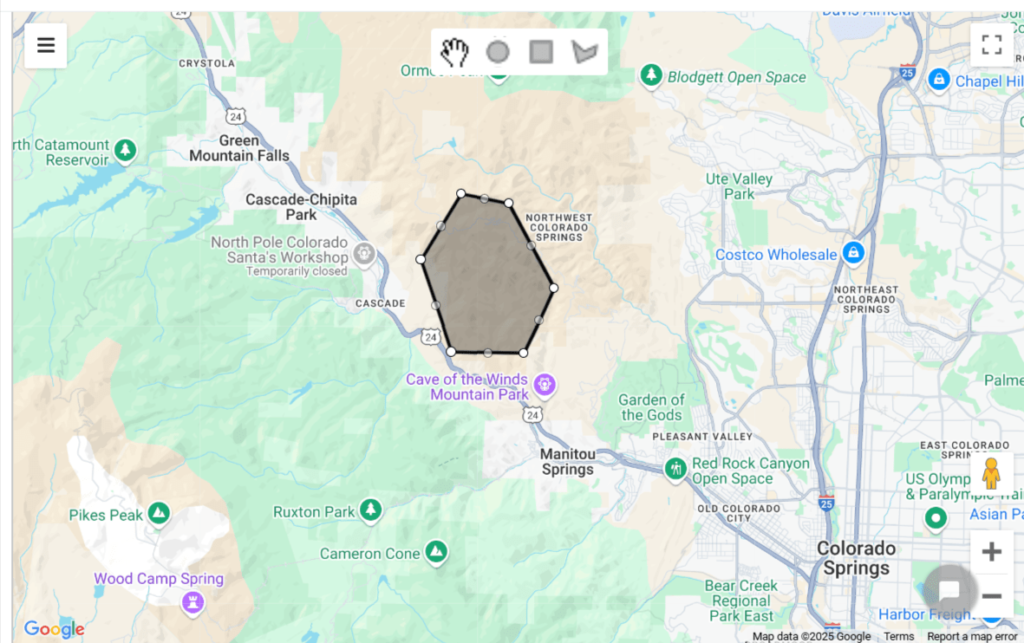
Source: GoCodes Asset Tracking
Once you’ve set up relevant geofence alerts, any unauthorized movement of assets or resources within or outside the geofenced zone triggers an instant loss alert.
Depending on the time and the circumstances of the event, the notified staff can easily reach out to law enforcement agencies and ensure swift action.
Step 6: Schedule Regular Inventory Audits
Even with different tracking systems, weekly or monthly inventory checks are the best way to ensure all tools are accounted for.
What’s more, with these checks you can stay on top of equipment maintenance, which helps you prevent unexpected breakdowns and maximize tool lifespan.
While inventory audits are generally time-consuming, the tracking technologies we presented speed things up considerably.
Scanning asset labels with a smartphone or a tablet automatically updates the asset’s location while logging the timestamp and the name of the user conducting the check.
Here’s how this looks like using GoCodes Asset Tracking’ audit mode.
Source: GoCodes Asset Tracking on Youtube
The verified assets are compared against the inventory records, flagging any discrepancies that can be further analyzed using GoCodes Asset Tracking’ comprehensive reporting capabilities.
Increased insight into each tool and piece of equipment also benefits maintenance efforts by enabling you to keep a detailed maintenance log.
With quick access to repair history and all the information in one spot, you have nearly everything you need to extend your equipment’s lifespan and maximize availability.
Still, the key is to be as proactive as possible.
Afrigrit’s Logistics Manager, Marius Pick, explains that proactive maintenance is his team’s key strategy for maximizing operational excellence and avoiding downtime.
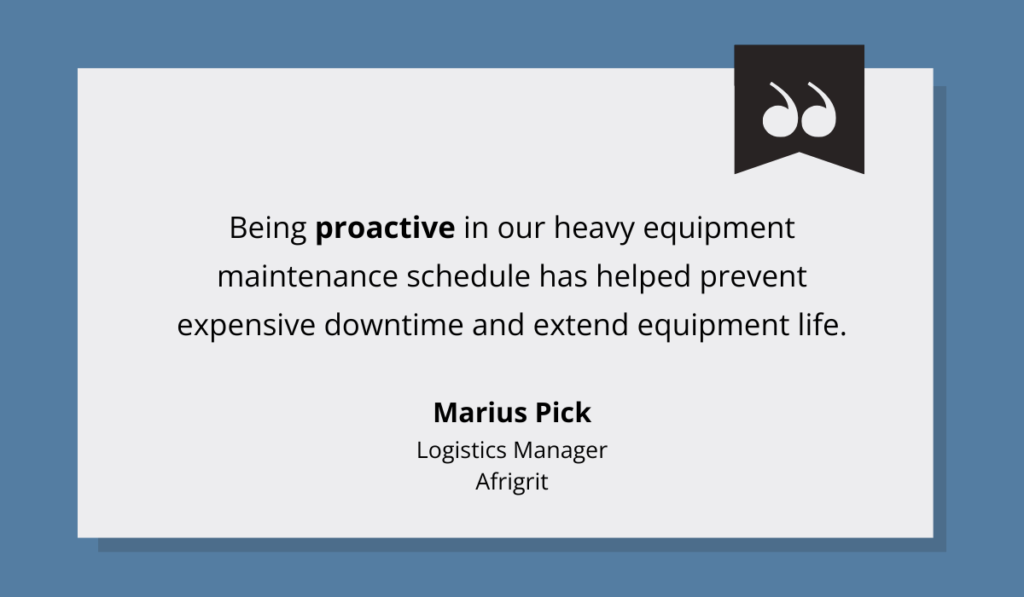
Illustration: GoCodes Asset Tracking / Quote: Aggregates Business
Despite its benefits, planned maintenance is often overlooked due to more pressing priorities and emergency service requests.
Luckily, you can easily automate scheduled service reminders to stay on course and prevent unexpected breakdowns.
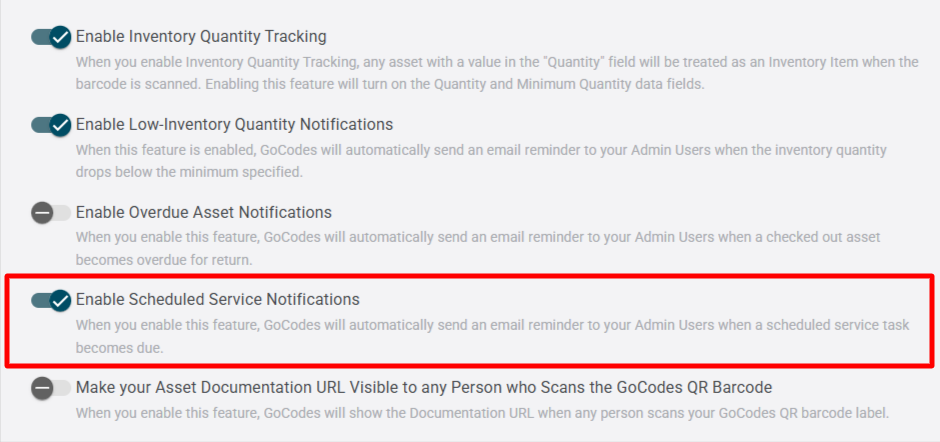
Source: GoCodes Asset Tracking
Regular audits and maintenance ensure your equipment is available and able to deliver peak performance.
Using the right tracking tools will help you stay on top of both, resulting in less downtime and huge cost savings.
Step 7: Train Employees on Proper Tool Management
Proper tool management requires well-trained employees.
Companies may adopt top-notch systems and methods, but the follow-through will depend on the whole construction crew.
Mike Griffin, President of Razr Logistics, argues that the human factor is pivotal in keeping track of the equipment and maintaining general order.
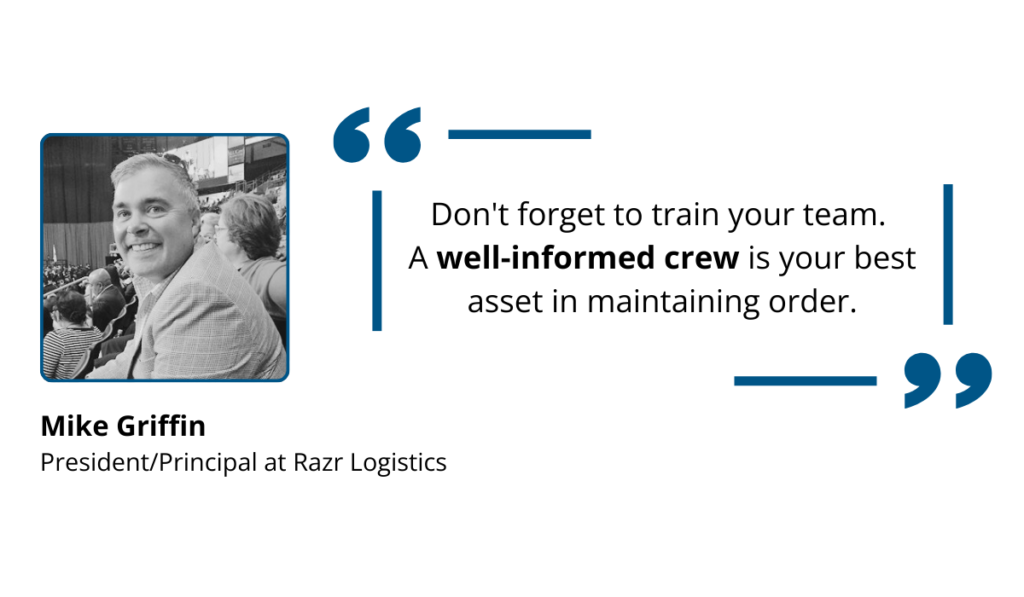
Illustration: GoCodes Asset Tracking / Quote: LinkedIn
In other words, ensuring comprehensive staff training is the only way to stay on track and achieve your objectives.
You should approach this on two levels:
- Give practical instructions on how to use tracking systems, and which procedures and methods to follow.
- Explain the importance of tool tracking and the crew’s role in it.
Before organizing training sessions, make sure to clearly outline key check-in/out procedures and storage methods.
Next, think about which resources you can use.
Tracking system providers typically prepare tutorials, webinars, and knowledgebases to support their customers and ensure everyone is quickly up to speed with the technology.
While structured, top-down training is essential, building a strong tool management culture requires more.
Bryan Furnace, a heavy equipment operator makes an excellent point about training construction workers, encouraging managers to find allies within the crew.
You don’t need to come up with this four-week-long training curriculum […] But I want to encourage you to go out of your way to find a couple of employees who do an exceptional job explaining and teaching.
Although this advice focuses on training in general, a few dedicated peer mentors can make learning more relatable and effective.
Plus, it reinforces the idea that everyone needs to be more responsible when handling tools.
To sum up, make sure to train your team properly on how—and why—to manage tools.
Step 8: Continuously Improve Your Tracking System
Once you have your tracking system in place, you need to monitor its effectiveness.
It’s more than just making minor efficiency tweaks.
Continuous monitoring ensures that the system actually supports your goals.
You can measure effectiveness by introducing several KPIs, but the quickest way is to collect employee feedback and observations.
Conducting anonymous surveys ensures that your team feels free to voice concerns, and they’re easy to create from scratch or by using existing templates.
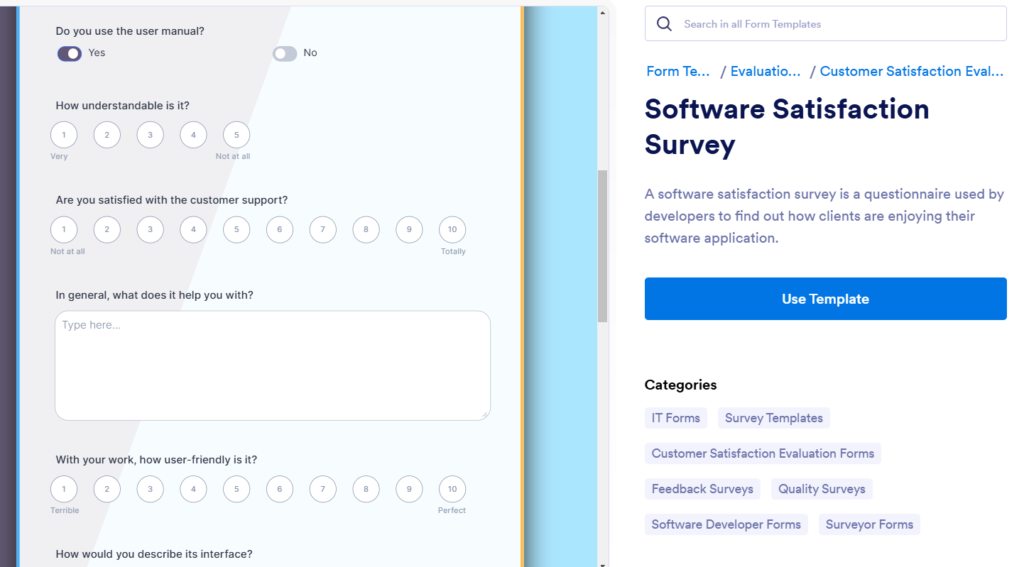
Source: Jotform
Analyzing the collected data helps adjust your procedures accordingly, enhancing employee satisfaction while bringing better overall results.
However, as your business grows, it’s best to be on the lookout for more advanced technology, as highlighted in this case study focusing on Plan Group Inc. and AlignOps partnership.
The construction engineering company stopped using their tool crib software after a data breach, and soon decided their business needs more than a replacement solution.
Plan Group pursued a more comprehensive asset management tool, ultimately improving their tracking accuracy and gaining more insights into tool usage.
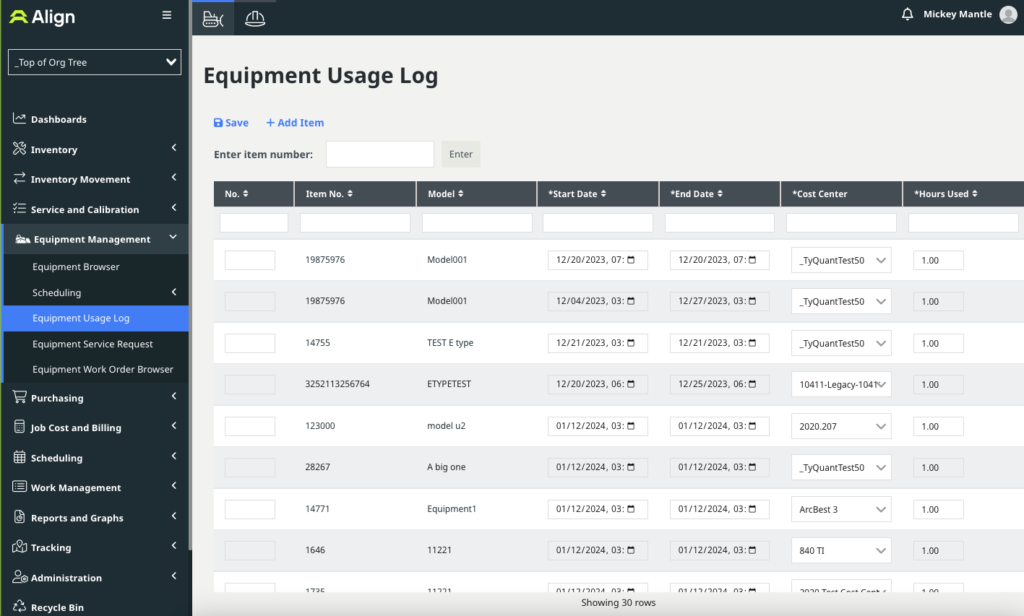
Source: AlignOps
With the ability to easily track equipment across job sites and reconcile tool-related expenses, Plan Group took the next step in strengthening financial responsibility and implemented a successful internal rental program.
Rochelle Groves, the company’s Equipment and Logistics Manager, points out that new technology saves time, and exploring it further just might deliver additional benefits.
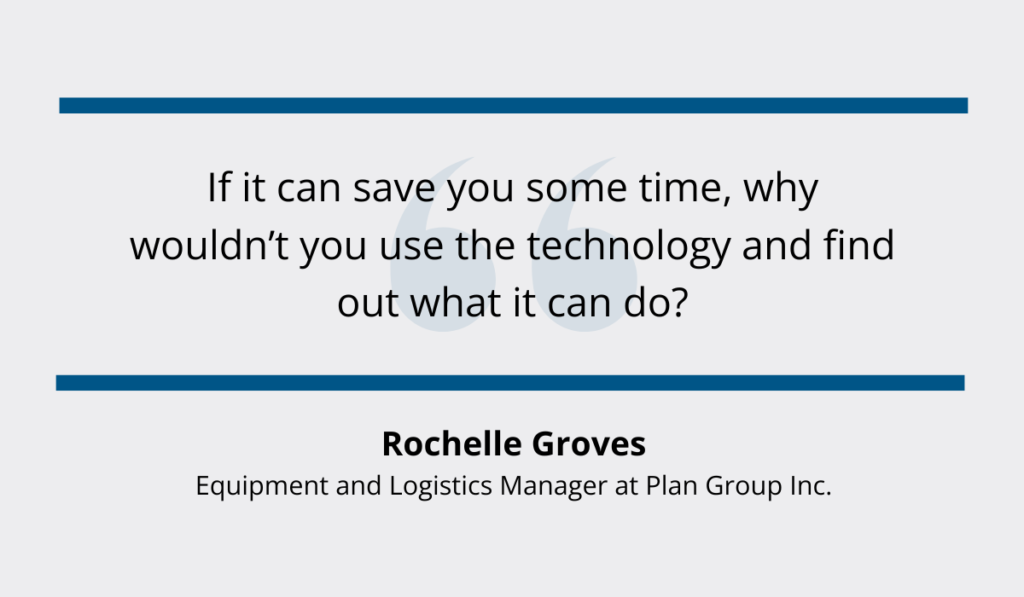
Illustration: GoCodes Asset Tracking / Quote: AlignOps
In conclusion, mapping areas for improvement helps you overcome short-term obstacles, but it also builds long-term competitive advantage.
The important thing is knowing when to take that leap of faith and change your system from the ground up.
Conclusion
Keeping track of tools and equipment isn’t just about preventing theft—it’s about maximizing efficiency and making the most of the assets you have.
A centralized inventory is a foundation that you can enhance with asset tags, GPS trackers, and a check-in/check-out system.
However, a comprehensive tracking system alone isn’t enough.
Successful implementation relies on an intuitive storage layout, well-trained employees, and a culture of responsibility.
So, don’t wait to lose tools or experience project delays to take action.
Instead, start optimizing your asset tracking today!