Considering the importance of tools, equipment, and other assets that construction companies use in everyday operations to effectively do their job, it’s not surprising that keeping them in good condition is one of the top priorities for company owners or managers.
For this purpose, they typically establish maintenance management procedures which—despite possible differences depending on company size and setup— involve creating work orders for equipment maintenance.
Efficiently tracking these work orders can generate a host of benefits, such as increased employee productivity, minimized equipment downtime, improved safety compliance, and lower maintenance costs.
So, let’s look at the five best practices that can help your company do just that.
In this article...
Centralizing All Work Orders
The first best practice is to keep track of maintenance work orders through a centralized database that can be accessed and updated in real time from any place and any device with an internet connection.
In fact, all the other practices we describe in this article stem from this one.
In other words, your company should go paperless and replace manual pen-and-paper and spreadsheet-based work order tracking processes with a cloud-based software system.
This system will automate work order tracking and give your service technicians real-time access to crucial information about the specific piece of equipment their work order refers to, as well as provide your managers with a birds-eye view of all past, present, and scheduled work orders.
To illustrate, here’s an example of how an individual equipment info portal looks on a smartphone and how the central asset database—with filtering options—looks on a computer screen.

The convenience of having instant access to this information in the field and at the office simply outperforms any paper- and spreadsheet-based work order tracking methods.
For example, a technician performing equipment repairs on-site can use cloud-based tracking software to access the equipment’s maintenance history along with links to relevant documentation with a few clicks on their smartphone or tablet.
After carrying out their work order, the technician can use it to immediately enter their findings and other data, such as the date and time, location, and any parts used or replaced.
They can also add images and leave comments.
As for their future assignments, they will receive automated notifications, like the one shown below, of the next work order on their schedule.

On the management side, centralized tracking of work orders in one digital system enables managers to:
- have a clear overview of all ongoing and completed maintenance work orders
- schedule, update, and prioritize future work orders according to maintenance needs
- generate reports and analytics that help them identify any recurring equipment usage or maintenance issues and patterns
- make data-driven decisions about future maintenance plans and investments
And, again, they can do all this in real time from any device with internet access.

All things considered, we don’t need to describe how paper forms and spreadsheets are typically used to track and manage work orders, but we’ll just list some downsides:
- paper work orders can get lost, damaged, or misplaced—or can be illegibly written— leading to data loss and incomplete maintenance records
- manual data entry is time-consuming and error-prone, resulting in delayed and inaccurate information entered in spreadsheets or other digital tools
- no real-time updates or visibility, and no instant remote access, making it difficult to monitor progress and address issues on time
Overall, it’s clear that this best practice—digitizing, automating, and centralizing work order tracking processes—is the foundation for all other practices covered in this article.
Therefore, you should invest time and effort into finding and implementing the right cloud-based mobile software that meets your work order tracking needs and budget.
Documenting Every Work Order
Failure to properly document any equipment maintenance or repair action—even a minor one— in a work order can result in incomplete records about past work done, preventing the detection of larger issues and ultimately leading to costly breakdowns.
For example, let’s say a scissor lift operator, during their pre-operational inspection, notices that one of the bolts is loose.
In a misguided effort to save time—or because they hate paperwork—the operator tightens the bolt without documenting their action in a work order (or another official record).
If several different operators (or the same one) continue this practice and without recording the fact they tightened the same bolt, a technician tasked with routine maintenance will be missing what may be critical information needed to detect a larger underlying issue.
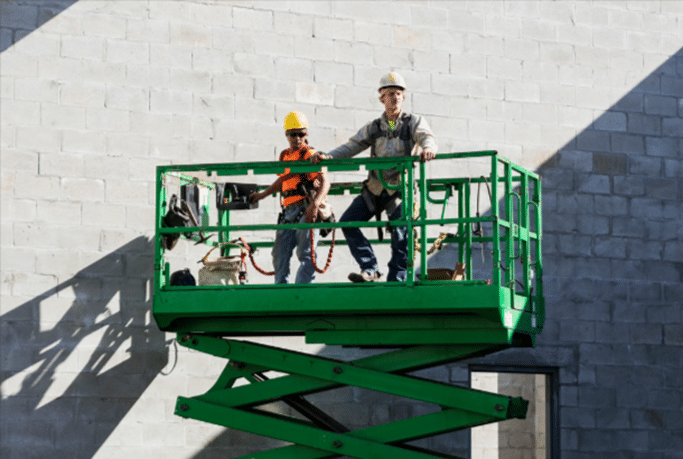
In the case of a scissor lift, this could be an incorrect alignment of machine components or their wear and tear, which leads to higher safety hazards, and can ultimately result in an accident or expensive equipment failure.
In other words, not properly documenting actions that any worker, equipment operator, or technician takes as a work order is a major obstacle to efficient work order tracking and effective maintenance management.
To avoid this, rules should be put in place to document each and every work order and enforced so that no work will be done without it first being documented as a work order.
Naturally, using the tracking software we covered above will streamline the documentation process and make the enforcement of those rules easier.
For example, instead of filling out a paper work order, an operator can use the tracking app to access the specific equipment’s profile, where they can document their maintenance actions on the spot.

Alternatively, they can use the app on their phone or tablet to access a standardized work order template and quickly fill it out.
In conclusion, documenting every work order is crucial for accurate records, detection of more significant issues and patterns, and effective preventive maintenance, while tracking software makes strict work order documentation rules much easier to enforce.
Tracking Work Order Assignments
We already highlighted that asset tracking software can be used to track work order assignments, which is essential for making informed maintenance decisions in real time.
This allows construction companies to reap the benefits like:
- increased productivity of maintenance staff and improved overall operational efficiency through better scheduling of work orders
- improved equipment performance and safety through timely maintenance and repair actions
- making real-time decisions on prioritizing and managing work orders through comprehensive record-keeping and analysis of maintenance data
In other words, an equipment manager or supervisor can use tracking software to assign work orders to specific maintenance team members, track the status of in-progress work orders, and have a detailed record of all completed and upcoming work orders.
Also, they’ll be able to reschedule work order assignments if their completion is running late or a higher-priority work order—such as critical equipment breaking down or worker safety being compromised—needs to be addressed first.
For example, our asset tracking solution, GoCodes Asset Tracking, allows managers to assign work orders, track their progress, and schedule future work order assignments.

As you can see, this mobile app also enables managers to set automated reminders about upcoming work orders.
Using GoCodes Asset Tracking’ task feature, they can assign tasks (i.e., work orders) to specific technicians, who can then view the list of their work assignments in the app under My Tasks.
At the same time, managers can view all work orders under All Tasks.
Mind you, this is only one of many GoCodes Asset Tracking functionalities that help streamline work order tracking and other equipment management processes.
Here are some other noteworthy features:
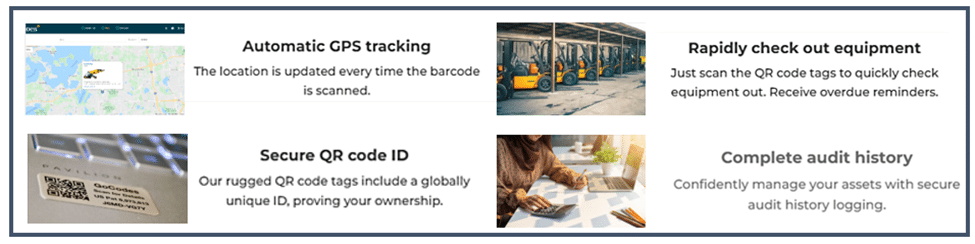
Each feature supports a different aspect of maintenance management; for example, the assigned technician can use GoCodes Asset Tracking to check the location of equipment they need to service.
We’ll discuss two additional features relevant to efficient work order management—inventory tracking and data analysis—in our next sections.
Overall, the ability to plan, schedule, track, and prioritize work orders in real-time with the help of tracking software enables construction companies to increase efficiency, improve equipment performance and safety, and make better-informed maintenance decisions.
Monitoring Inventory Quantities
Monitoring the inventory quantities of spare parts and other consumables used when performing maintenance work can support work order tracking and enable construction companies to improve maintenance scheduling and inventory management.
In other words, service technicians will use maintenance inventory—spare parts, oils and lubricants, filters, wires, and other supplies—to perform their work orders, so construction companies should monitor inventory quantities, which tracking software allows them to do.
That way, they will know when to order new inventory for future work orders to avoid the following situations:
- delayed completion of work orders due to a lack of necessary parts or supplies
- extended equipment downtime due to delays while obtaining required parts
- increased costs due to the rush ordering of parts and expedited shipping costs
When inventory levels of such consumables are monitored through tracking software, technicians can—upon receiving a work order—identify what parts and supplies they might need and check their availability using their smartphone or tablet.

For instance, GoCodes Asset Tracking uses patented QR code tags.
They are affixed to a container or pallet with spare parts, and enable technicians to access the app on their smartphone and record the inventory change, for instance, when taking a spare part to perform their work order.
Moreover, this inventory tracking system can send automated low-quantity alerts, so managers know when to order new inventory.
When replenishing the supplies, storage workers can repeat the QR code scanning process and update the number of spare parts in stock.
Therefore, by monitoring inventory quantities through tracking software, construction companies can ensure that work order scheduling is aligned with what parts and consumables are available.
As a result, they can then plan ahead and streamline their inventory management.
Analyzing Gathered Work Order Data
Of course, the last and probably the most valuable benefit of using tracking software for work order management is analyzing the collected work order data.
The ability to analyze all the data gathered by tracking work orders enables construction companies to make informed decisions on how to improve their work order management.
However, each company should first decide which key performance indicators (KPIs) should be tracked so that work order data can be used to evaluate the efficiency of specific maintenance management processes.
For instance, a construction company can track the percentage of preventive maintenance work orders completed on time, otherwise known as Preventive Maintenance Compliance (PMC).

This important metric indicates the effectiveness of your maintenance team, as well as the quality and efficiency of overall processes.
When the data concerning different types of work orders are recorded in tracking software, work order history can be easily analyzed to determine the current state of affairs and plan improvement measures.
PMC is only one of the key equipment maintenance metrics that can be measured using the gathered work order data and the tracking software’s analytics and reporting features.

Therefore, by tracking specific KPIs and analyzing work order data to evaluate them, construction companies can identify areas for improvement and make changes needed to maximize the efficiency of their work order management based on that analysis.
Conclusion
So, having covered five best practices for tracking work orders for equipment maintenance, it’s clear that centralizing and documenting all work orders in a single software system is highly recommended.
First, it allows construction companies to manage work order assignments, monitor inventory quantities, and analyze the collected work order data to improve their equipment management processes.
With an efficient work order tracking system in place, construction companies can reap the benefits like increased employee productivity, minimized equipment downtime, improved safety compliance, and lower maintenance costs.