A company’s flow of work orders is much more efficient when managed with asset tracking and dedicated software.
To take full advantage of the many benefits of utilizing work orders in this way, however, decision makers and workforce members should understand what they are, how they operate, and the ways an organization might manage them.
This post will define what work orders are and how they might affect fieldwork.
You will then learn what a work order process looks like, as well as the best way to fill one out.
After discussing why work orders are important, this post will explore various ways to manage work orders.
In this article...
What Is a Work Order?
It’s important to know what a work order is, as well as the purpose it serves.
Work orders are formal requests for business or maintenance action. They might function as technical or maintenance actions or have a purpose in other areas.
While each work order format is different for every organization, they tend to contain similar information.
Usually, work orders contain:
- the names of workforce members involved in the action
- any tools needed
- which departments of the company the work order affects
- the date of the action and projected completion time
- optional relevant details about the situation leading to the work order
Furthermore, work orders can serve many functions.
They provide precise information for technicians and acquaint third-party contractors with company processes.
Additionally, they create and build a paper trail proving when actions took place, building a history of the item and its life cycle.
A work order can affect software and technology, as well as human resource actions.
It can determine shipping and scheduling, and the movement of vehicles and materials.
Moreover, it might contain checklists, instructions, and warnings against danger.
Depending on what the work order requires, it could contain information about public relations, current events, or suggestions of others to contact.
These details are important not only for members of the workforce who will participate in the work order but also for decision makers who must have pertinent information to understand the situation that prompted the work order.
Types of Work Orders
Work orders can vary according to company, industry, and compliance rules. For the purposes of this post, let’s focus on those applicable to fieldwork.
Installation of Heating/Ventilation/Air Conditioning (HVAC)
A great deal of information is necessary to successfully install an HVAC system.
HVAC involves equipment that weighs a great deal and work that takes place behind walls.
It also takes into account air quality or filtration.
The systems must work together to provide air quality monitoring, heat in cold weather, cold air in hot weather, and sometimes humidity removal.
Boilers might play a role, as well as pipes, linked air conditioning units, ventilation equipment, and avoidance of carbon monoxide buildup.
Preventive Maintenance
This important, ongoing process is key to keeping assets in good working condition and making the most of their purchase price. It’s also vital to ensuring that they will operate as safely as possible.
Therefore, preventive maintenance is any action, mechanical or otherwise, dedicated to keeping assets in operation.
Safety Inspection
The Occupational Safety and Health Administration (OSHA) stipulates certain regulations dedicated to maintaining a clean, healthy, and danger-adverse work environment.
Work orders for safety inspections might include tending to signage, adding railings, or clearing out hazardous items and waste.
Property Inspection
Local laws and company regulations might address lighting, electrical systems, sewage pipes, yard features, roof repair, or plumbing updates.
Property inspections are often a major aspect of real estate transactions or construction endeavors.
Work orders might also refer to social media updates, software installation, or requests for proposals.
Sometimes a work order might even be to create another work order or trigger the separation of a large project into many smaller items.
What Does a Work Order Process Look Like?
Each organization must decide for itself how a work order’s flow takes place. In general, however, the process of filing, acting upon, and completing a work order looks as follows.
Work Request Is Submitted
A client, tenant, employee, or project manager generates a request for a specific action.
The filer must include all pertinent information to ensure that employees complete the action efficiently.
It’s important for the employees tending to the task to have accurate and current details about the job that needs to be done.
Work Request Undergoes Review
Depending on the company or nature of the work order, the request might reach a manager or decision maker, who will add it to a daily, weekly, or monthly manifest.
In the case of a smaller company or department, a single employee might both review and undertake the task.
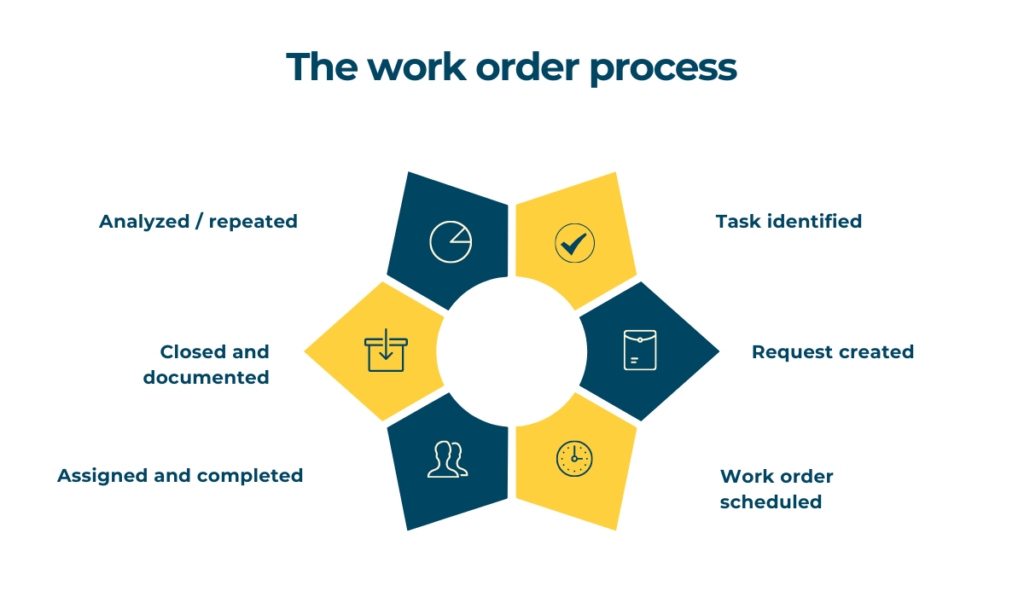
The work order might require multiple actions or involve contracting with a third company.
In some cases, the system or a manager assigns the order to one of a large number of employees.
Work Order Is Approved/Disapproved
The work order may undergo an approval/denial process by a manager or team.
If the order is approved, the work undergoes distribution, and labor begins.
Sometimes, the work order might not undergo approval, perhaps because of budgetary constraints or due to the limitations of regulations.
In this case, the company should notify the requestor that the work order will not go forward so that he or she can make other arrangements.
Work Order Creation
This is the formal process of filling in the details of the work order and undertaking the actions required to address and complete the task.
We shall describe how to fill out a work order in more depth later in this post.
Work Order Completion
Some organizations separate this final portion into two separate steps.
In the case of a simple task, the employee can affirm the work order is complete. Sometimes, a manager or outside inspector must verify that the action is satisfactory and closed.
Depending on the complexity of the work request and the work order that follows, some employers might assign several employees to a single work order.
Completing it could require just a few minutes or several days.
How to Fill Out a Work Order
Work orders are only effective if they are consistent and follow a specific format. Otherwise, confusion, misunderstandings, or even dangerous conditions could result.
Here are a few details your company’s work orders should contain.
Specification of Asset
The work order must contain information about the asset that requires repair or preventive maintenance, if any such action is necessary.
A strong asset tracking system can aid in ensuring that the correct asset is included on the request.
Description of Issue
This section should detail what the work order calls for, such as which repairs an asset needs, what a client has requested, or a reminder that preventive maintenance is in order.
Work Action
If the work order requires a specific action, this should appear so that employees are clear on what is necessary.
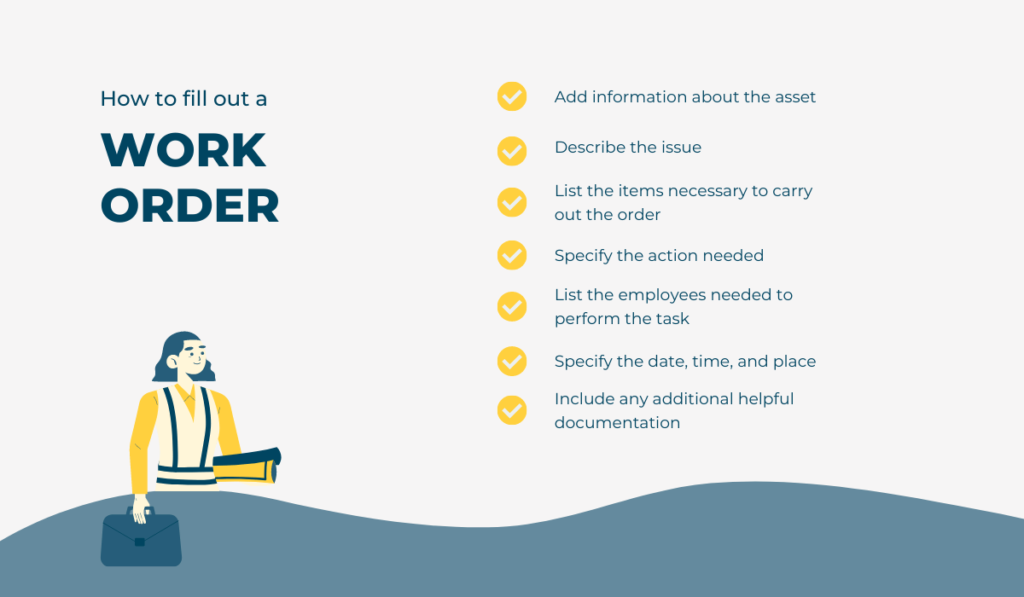
If not, the symptoms of the problem, history of complaint, or details of the client’s questions must be part of the work order.
Needed Items
The work order should list which items are necessary for a particular required action.
This enables employees to check necessary tools or other items out of a tool crib or equipment cache ahead of time, thus ensuring that the work order is completed in a timely manner.
Personnel
The number of employees assigned to the work order, along with which ones, should be listed on it.
The work order should also include information about whether specific employees, such as a manager, must see to the matter.
Date, Time, and Place
These details are especially important where fieldwork is concerned, and may include the location of the filing as well as where the actions are necessary.
Documentation
Some work orders might require the inclusion of authorizations, parking passes, or permits.
Several other items might accompany a work order, depending on the task. For example, if the work order involves addressing a client’s question, the action will not require any specific tools.
Why Are Work Orders Important?
Work orders are important to everyone involved with their generation and execution.
These may include the client, employee or third-party contractor, manager, and even the government agency involved. Depending on the type of work order, these benefits vary.
One key benefit is building trust. Partners or contractors need to know that your company stands behind its work and products.
Since customers can quickly become impatient with mechanical issues or delays in completing their own work, having all important information listed in a work order which ensures transparency and accountability will improve client satisfaction.
Since a company can confirm that a work order was filed and completed, it also allows an organization to be more detail-oriented.
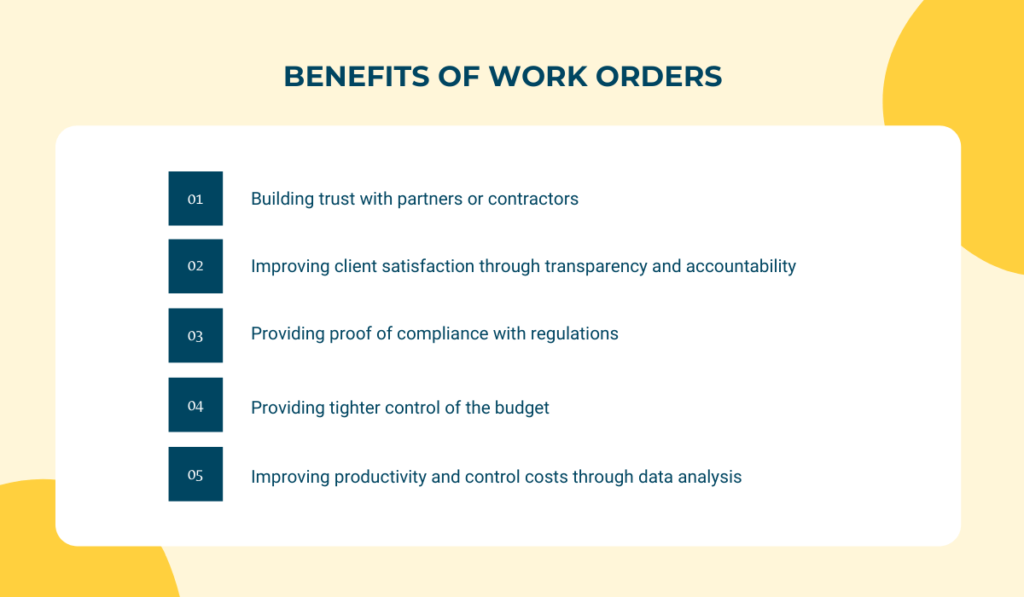
The ability to present a chain of action is also useful in the event of an audit, while the completion and closure of work orders can provide proof of compliance with regulations.
Additionally, implementing a work order system also enables analysis of cost overruns, thus providing tighter control of the budget.
It also provides benchmarks and indicators that measure productivity goals.
Using an in-house work order system with asset tracking also improves security, as it helps protect sensitive, financial, and proprietary information.
In time, work orders can provide an accurate picture of how to improve productivity and control costs through data analysis.
A data-driven asset tracking system allows decision makers and schedulers to plan for unavailable equipment.
Finally, automatically updated work orders quickly produce a more efficient workflow, because the overview they provide leads to automatic prioritization and organization.
In short, the applications of work orders are almost limitless. They provide immediate access to details, streamline documentation, and allow for performance monitoring.
Ways to Manage Work Orders
Depending on the field in which a company engages, as well as how quickly it adapts to new technology, the process of managing work orders might not have become entrenched in a particular era.
There are several ways of managing work orders; some are more traditional than others. Let’s take a look at a few.
Managing Work Orders With a Pen and Paper
This is the most traditional way to deal with work orders. It is inexpensive and requires no specialized equipment; only paper and a writing implement are necessary.
Some companies manage work orders with a whiteboard and markers.
Using pen and paper, however, limits the amount of information the record holds.
It is dependent on the ability to decipher handwriting. The paper might become lost, damaged, or destroyed.
Storing these records is expensive and insecure, and even then, paper records might become easily lost.
Organization is difficult, and manual updating is time-consuming and frustrating.
When a company relies on paper, it is time-consuming and difficult to see patterns, build reports, and mesh information.
Managing Work Orders With Spreadsheets
Many organizations consider using computer spreadsheets as an adequate solution. Computers are in play, and spreadsheets create a digital paper trail.
Additionally, spreadsheets are usually search-enabled and can provide automatic calculations.
While more efficient and modern than pen and paper, spreadsheet use still carries frustrations.
Hard drives might crash, and security and storage are dependent upon the location of the computer itself.
While data entry is more consistent and readable than handwriting, it is still error-prone. In addition, real-time updating is impossible, particularly across various devices.
Confusion is often the result, and communication can lapse. In addition, inventory-based scheduling is not available when a company depends upon spreadsheet-based work orders.
Managing Work Orders With Software
Managing work orders with software and asset scanning is the most modern and efficient format of organization.
For instance, GoCodes offers an all-inclusive solution to building and fulfilling work orders. From one single place, users can see where the equipment is, who used it last, and were there any messages related to it.
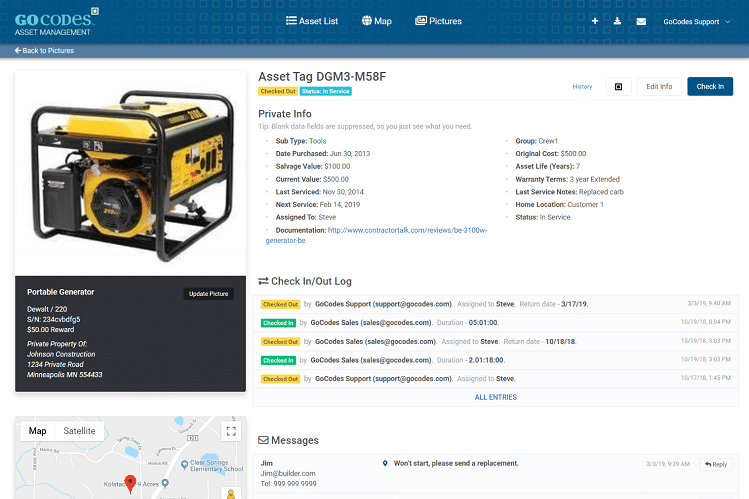
Here are just a few:
- QR codes provide simple one-step scanning using regular smartphones or tablets; no specialized equipment is necessary
- Updates are instantaneous
- Varying levels of access provide for need-to-know accounts and tight security
- Each asset receives a unique alphanumeric ID along with its QR code, which eliminates confusion and provides for positive identification of lost or stolen items
- Users can easily confirm the status of a work order or maintenance status
Life cycle management and planning are much faster and accurate with asset scanning and dedicated software.
Conclusion
When a company dedicates itself to using work orders, many benefits follow, such as more efficient task completion, a better-controlled budget, and improved communication.
The process of taking work requests, generating work orders, and fulfilling tasks is easily streamlined with the help of software and scanning.
GoCodes software can manage work orders and do so seamlessly and with a great deal of flexibility.