If you manage the fleet of a construction company, you know that doing so efficiently is crucial for staying competitive.
Luckily, technological advancements like fleet telematics can provide invaluable insights into your fleet operations, leading to improved safety, productivity, and cost-effectiveness.
If you’re thinking about using a telematics system for tracking your fleet, you’re in the right spot!
This article will take you through the process of implementing it. So keep reading!
In this article...
Choose the Right Solution
You’ll find many fleet telematics systems on offer, so the first and most important step is to choose the right solution.
This process starts with determining the goals your company wants to achieve with the help of fleet telematics, such as:
- improving fleet efficiency,
- reducing fuel and maintenance costs,
- enhancing driver/operator safety and accountability,
- strengthening vehicle/equipment security,
- optimizing route planning.
Naturally, you might conclude that you want all these goals to be achieved, but you should still get your priorities straight by analyzing the key problem areas in your current fleet management.
From there, you can evaluate different fleet telematics solutions based on the following criteria:
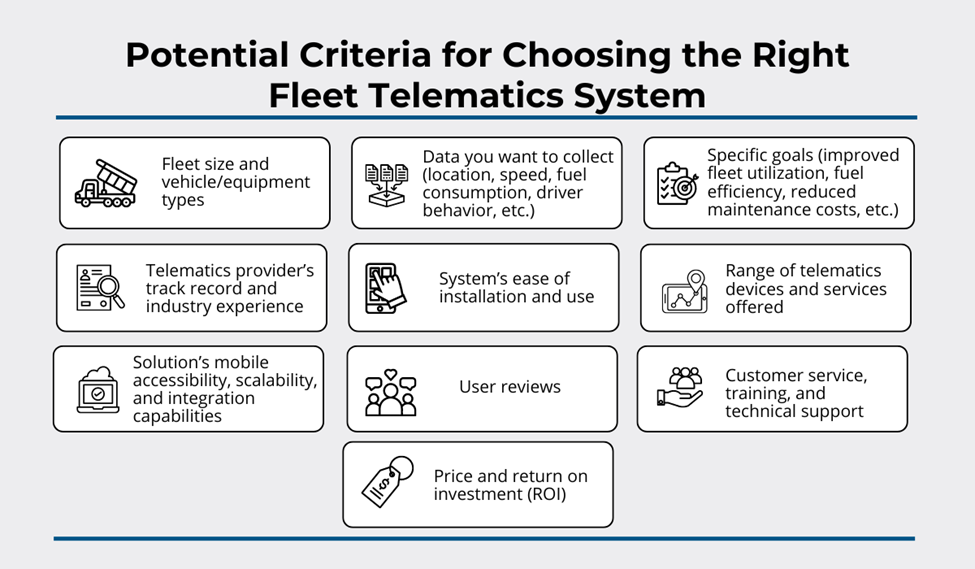
As you can see, there’s a lot to consider, which underlines the importance of defining your fleet management needs (together with key stakeholders) and setting a tentative budget.
This is relevant because the market offers a wide range of fleet telematics solutions, from basic GPS tracking of vehicle/equipment locations to full-blown enterprise systems that include a range of internal/external sensors and dashcams.
So unless you want to pay for features you won’t use, determine which software qualities are crucial for improving your fleet management.
For instance, you might be fine with GPS trackers with basic telematics sensors (speed, harsh braking, sudden accelerations, engine hours, etc.) that provide essential insights into vehicle whereabouts and driver behavior parameters.
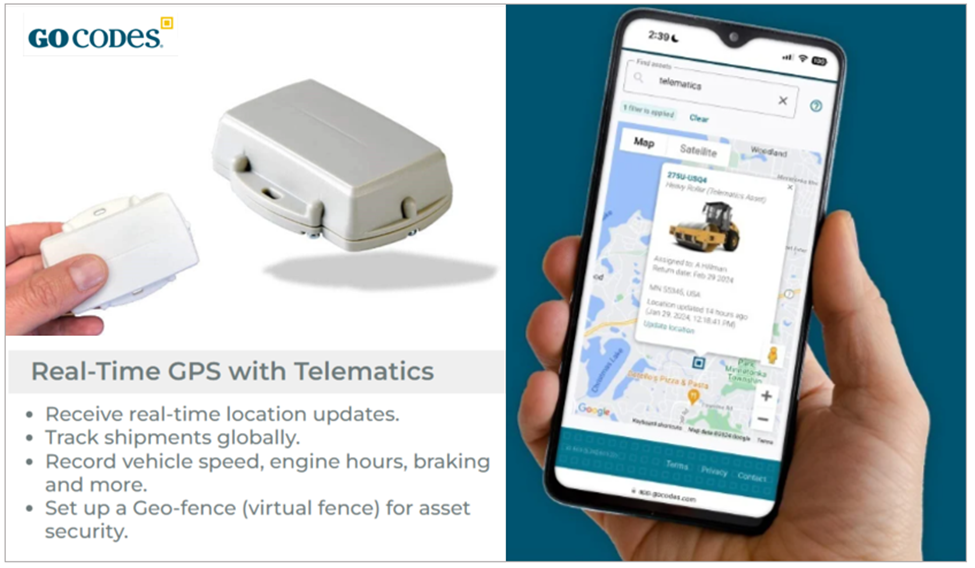
A GPS tracking system with some telematics is often sufficient for businesses aiming to enhance fleet efficiency and monitor basic fleet metrics without investing in more advanced devices and features.
However, if you want additional functionalities, such as real-time video monitoring of road conditions and/or driver behavior, you should explore more comprehensive telematics solutions that offer integrated dashcams and advanced sensor capabilities.
Such advanced telematics systems can provide deeper insights into fleet operations and driver performance, but they typically come with a higher cost and more extensive installation requirements.
Overall, choosing the right fleet telematics solution starts with determining what you want to achieve, researching different telematics providers, evaluating their offerings, and selecting the one that best meets your fleet management needs.
Define the Key Performance Indicators
After you have a sense of what you want to improve first, the next step is defining the Key Performance Indicators (KPIs).
They will serve as your compass and help you gauge the success of your fleet management, enabling you to track improvements over time and make informed decisions.
This typically requires establishing initial benchmarks for various fleet management metrics, such as your fleet’s current fuel consumption, maintenance costs, and utilization rate.
Such benchmarks will serve as starting reference points, enabling you to measure how your fleet is performing with a telematics system versus without it.
So, what KPIs can you define?
Here are just a few (out of many) fleet management KPIs to consider:
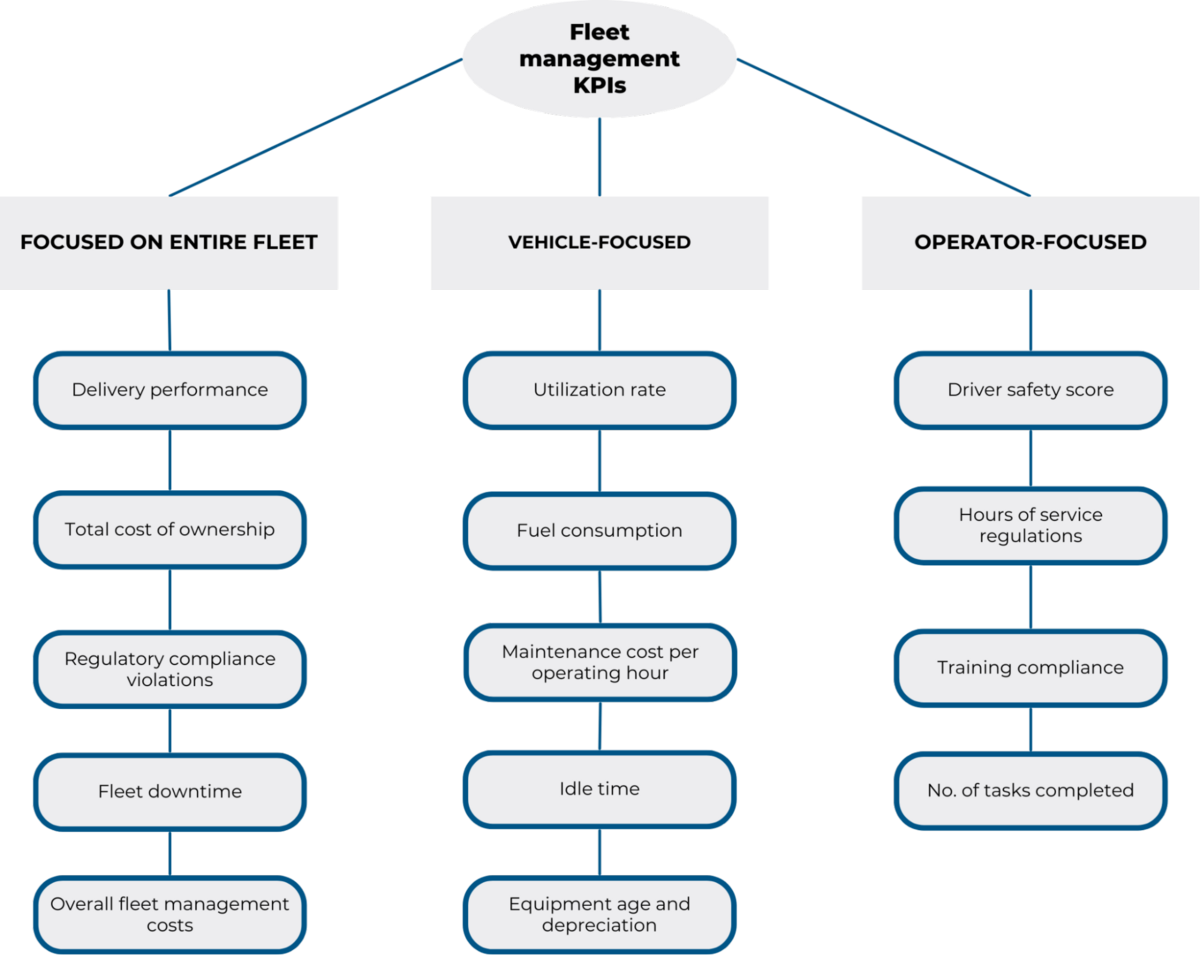
For instance, the KPI “Utilization Rate” measures how effectively your vehicles and equipment are being used.
This can be determined by, among other things, tracking the percentage of time each vehicle spends actively engaged in productive work versus its downtime while it’s stored or serviced.
Fuel consumption stands as another vital KPI, offering insights into the efficiency of your fleet’s fuel usage.
More precisely, monitoring fuel consumption trends over time enables you to identify areas for optimization, such as reducing unnecessary idling or implementing more fuel-efficient driving practices.
Likewise, tracking maintenance costs allows you to identify issues, such as increasing maintenance expenses for certain vehicles or equipment, and take proactive measures to address underlying causes.
To recap, the second step in implementing a fleet telematics system is to define relevant fleet metrics (KPIs), benchmark them, and track improvements over time.
Provide Comprehensive Training
After choosing, installing, and deploying a fleet telematics system, comprehensive training becomes essential for both fleet managers and drivers/operators to maximize the system’s benefits and ensure smooth integration into daily operations.
Depending on how simple and easy-to-use your telematics system is, the training requirements may vary.
For instance, if the system has a user-friendly interface and intuitive features, training might be minimal and you could begin using the software within a few hours.
However, if the system is complex or includes advanced functionalities, more extensive training may be necessary to ensure all users are proficient in using it.
Of course, this training may be provided in many forms:
- free training courses offered by the telematics system provider
- live support (demos, phone, chat, email)
- online self-service tools (video tutorials, Q&A, and help centers)
Here’s an example of the latter:
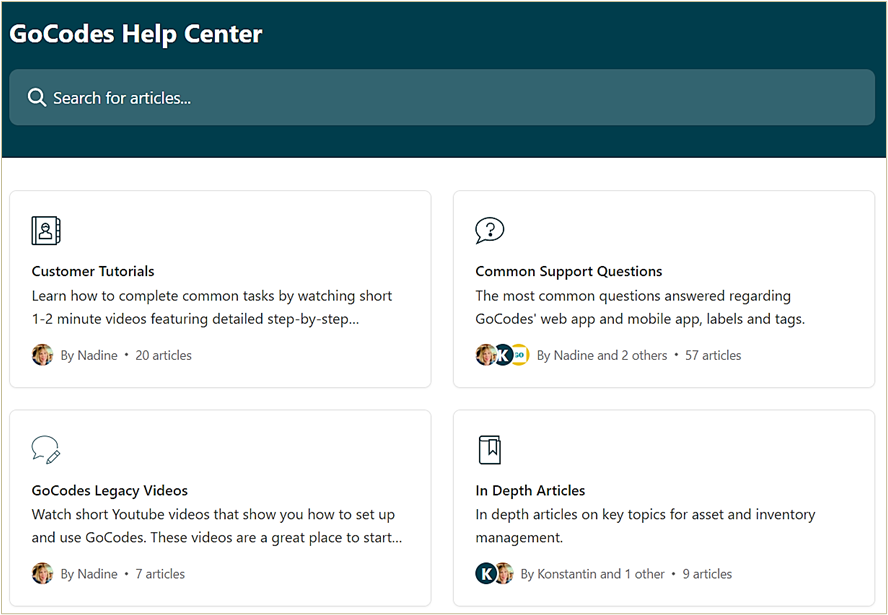
Regardless of its format, training for fleet managers should focus on system administration, data interpretation, and utilization of its features.
This includes learning how to:
- configure and customize the telematics platform to meet specific business needs,
- interpret data analytics to make informed decisions, and
- leverage advanced features such as predictive maintenance and route optimization.
For drivers and operators, training should cover system functionalities relevant to them, such as their reporting and logging requirements, proper use of the telematics system’s interface and features, and best practices for safe and efficient driving/operation.
Additionally, fleet managers may require training on regulatory compliance, privacy protection, and data security protocols to ensure adherence to industry standards and regulations.
Any privacy concerns drivers/operators might have regarding vehicles being tracked by GPS or them being monitored via driver-facing dash cams should be proactively addressed before deploying the system.
In summary, practical, hands-on training is invaluable for fleet managers and drivers/operators to gain proficiency with the telematics system and develop the necessary skills to leverage its full potential.
Monitor Your Fleet Performance
Once everything is in place, it’s time to put your fleet telematics system to use and monitor your fleet performance in real-time.
This gives fleet managers the data needed to immediately react to unexpected fleet-related issues, and—as discussed in the next section—gain longer-term insights into fleet efficiency and devise performance-boosting measures.
For example, when vehicles and heavy equipment are equipped with GPS trackers, this enables managers to use fleet management software to set up a virtual, invisible fence (geofence) around designated areas, such as specific job sites, storage yards, or driving routes.
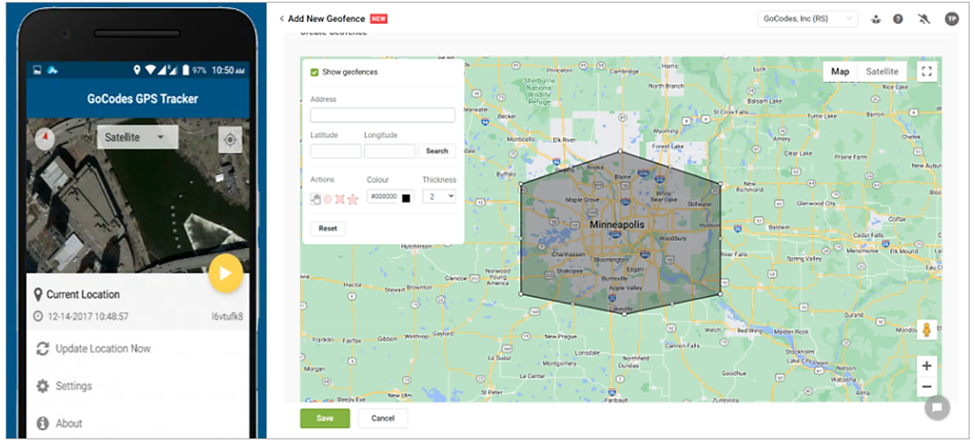
When a geofence is set up, the fleet manager will receive real-time alerts if any tracked vehicle or equipment leaves the designated zone.
This enables them to quickly react and investigate whether the driver/operator made a mistake or intends to use the vehicle/equipment without authorization, or that vehicle/equipment was stolen by somebody else.
In the case of theft, the manager can notify the authorities and, by tracking the vehicle/equipment, help them in recovering it.
In addition to geofencing, fleet telematics systems offer a range of other real-time alerts that empower fleet managers to react swiftly to unexpected situations.
For instance, managers can receive alerts for excessive speeding, harsh braking, or rapid acceleration when they occur, allowing them to address safety concerns immediately and provide timely feedback and/or coaching to drivers/operators.

Moreover, telematics systems can detect engine faults or maintenance issues as they happen, enabling managers to proactively schedule maintenance to minimize downtime and reduce repair costs.
Overall, the ability to track the location of vehicles and equipment along with a number of other parameters enables managers to monitor their fleet performance in real-time, receive timely alerts, and take swift action to address a range of fleet management issues.
Analyze the Obtained Data
In addition to enabling real-time reactions, a fleet telematics system collects and processes a wealth of fleet data.
When analyzed, that data provides managers with invaluable insights for improving fleet operations.
In other words, managers can use the telematics system’s historical data to analyze trends, identify areas for improvement, and take corrective actions as needed.
For example, after analyzing the collected data (e.g., mileage, engine hours), they can establish a preventive maintenance schedule, and set up automated scheduled maintenance alerts.
Here’s an example of such an alert GoCodes Asset Tracking sends to its users:
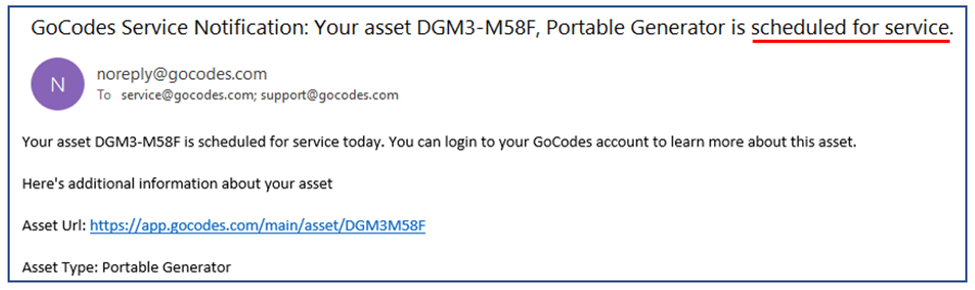
By scheduling preventive maintenance tasks based on usage patterns and equipment condition and automating alerts, you can ensure that vehicles and equipment are serviced on time, thereby minimizing downtime, extending their lifespan, and avoiding costly repairs.
Likewise, you can identify underutilized, overworked, and near end-of-life vehicles or equipment and make informed decisions regarding fleet size and allocation, as well as when it’s optimal to replace specific assets.
You can even use telematic-derived data to identify risky driving behaviors such as speeding, harsh braking, or rapid acceleration, and implement targeted coaching programs or incentive schemes to promote safer driving practices.
To illustrate, here’s an example of such a driver incentive program with metrics to be tracked, their tracking timeline, and potential rewards.
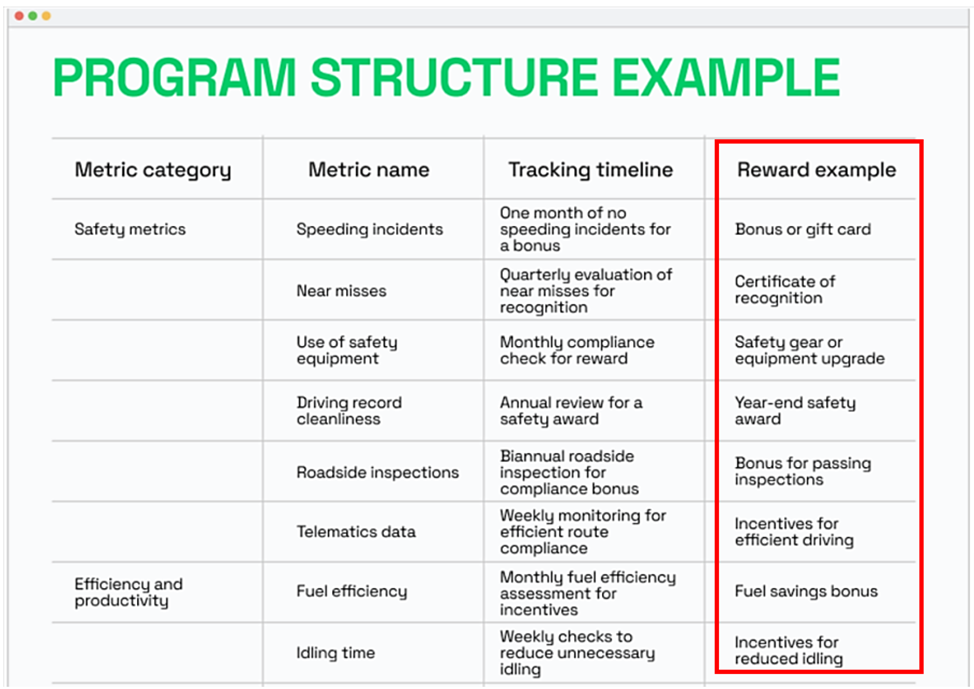
Of course, a fleet telematics system also allows managers to improve one of the biggest cost components in fleet management—fuel efficiency.
By tracking fuel consumption and identifying fuel-wasting behaviors such as excessive idling or inefficient driving, managers can implement targeted interventions (route optimization, driver training, and incentives) to achieve significant fuel savings.
To recap, the analysis of telematics data enabled by fleet management software empowers its users to make informed decisions that allow them to streamline operations, reduce costs, and enhance overall fleet performance.
Conclusion
Having covered the five stages of implementing a fleet telematics system, it’s evident there are many factors to consider, from defining your fleet management goals and KPIs to researching potential solutions and training requirements.
But once the telematics system is set up, managers can utilize its data to optimize their business operations.
Given all these advantages, embracing the right fleet telematics system can enable your company to improve its fleet productivity and safety, reduce fuel and maintenance costs, and become more profitable.