Key Takeaways:
- Telematics allows construction companies to plan and optimize driving routes and monitor driver behavior.
- It helps with streamlining resource allocation and improves project planning.
- Telematics makes it easy to conduct preventive maintenance and minimize the risk of breakdowns.
If you’re a construction company owner or fleet manager, you know that some of the biggest fleet management challenges are the visibility of vehicles and equipment, fuel consumption, and maintenance.
Luckily, that is where telematics comes in.
By harnessing the power of data and connectivity, telematics offers a comprehensive solution to these longstanding issues, empowering fleet managers with real-time insights and actionable intelligence.
In this article, we’ll explore specific benefits of telematics, and how together they can help you transform fleet management in your company by providing unparalleled visibility, enhanced planning capabilities, and substantial cost savings.
In this article...
Provides More Visibility
To make clear how telematics devices provide more visibility into the location and status of your construction fleet, let’s first explain what telematics is.
In essence, telematics consists of GPS trackers that, by either using their own sensors or connecting to the vehicle’s internal sensors, track a range of engine, vehicle, and driver performance data in real time.
Among those data, the most important element for improving overall fleet visibility is the telematics system’s ability to provide fleet managers with an accurate, real-time GPS location of each vehicle in their fleet.
Here’s a simplified view of how GPS tracking enables fleet managers to track the location of fleet vehicles and equipment.
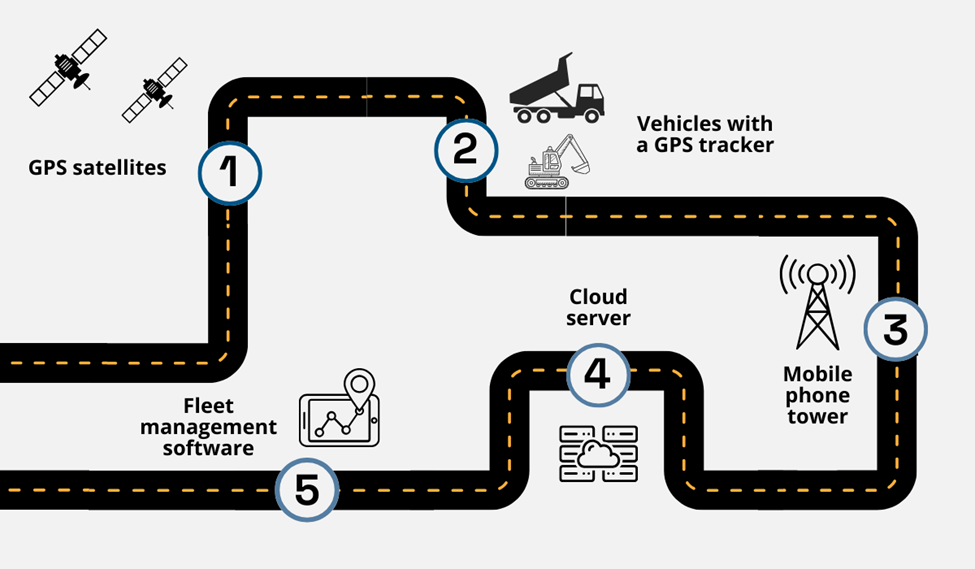
As a vehicle travels, its GPS tracker uses satellites to pinpoint its position anywhere in the world.
It then transmits that data via cellular, satellite, or wireless connections to the cloud server (database) and finally to fleet management software, which is a crucial component tasked with interpreting and analyzing telematics data.
In terms of fleet visibility, this enables managers to know, at minimum, exactly where each vehicle or heavy equipment is, whether it’s stationary or moving, and in what direction is it going when on the move.
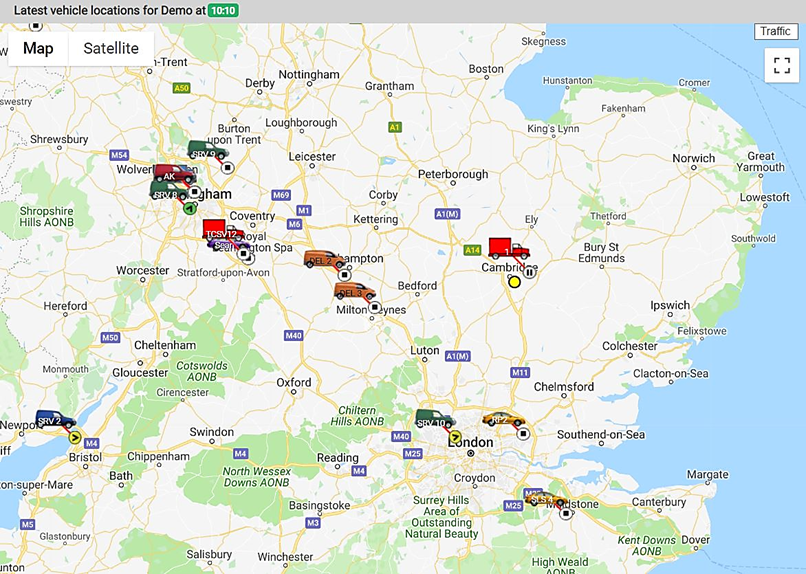
This unprecedented, real-time visibility allows fleet managers to:
- locate vehicles in case they’re stolen or used without authorization
- plan and optimize driving routes
- monitor driver behavior (speeding, sudden accelerations, hard braking, etc.) to identify unsafe and/or fuel-wasting driving practices
- allocate vehicles and heavy equipment more efficiently
Moreover, they can set geofences around areas where specific vehicles are operating or along the routes they’re taking.
These invisible, digital fences ensure that, if a vehicle leaves the designated area or departs from its geofenced route, the fleet manager will be immediately notified.
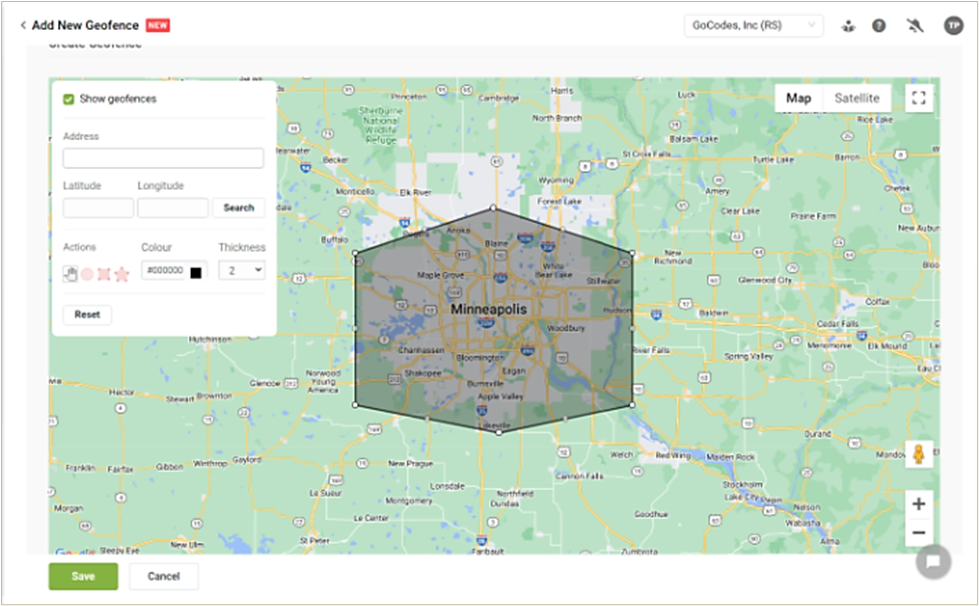
Therefore, geofencing can be efficiently used to enhance jobsite security and increase driver/operator accountability.
It should be noted that the location of other smaller, less expensive equipment and tools can also be tracked via GPS trackers, shorter-range Bluetooth beacons, or GPS-enabled QR code tags.
For example, our fleet/asset tracking software package, GoCodes, offers all three of these GPS tracking options, so contractors can choose the technology that best fits their needs and budget without using different solutions and software providers.
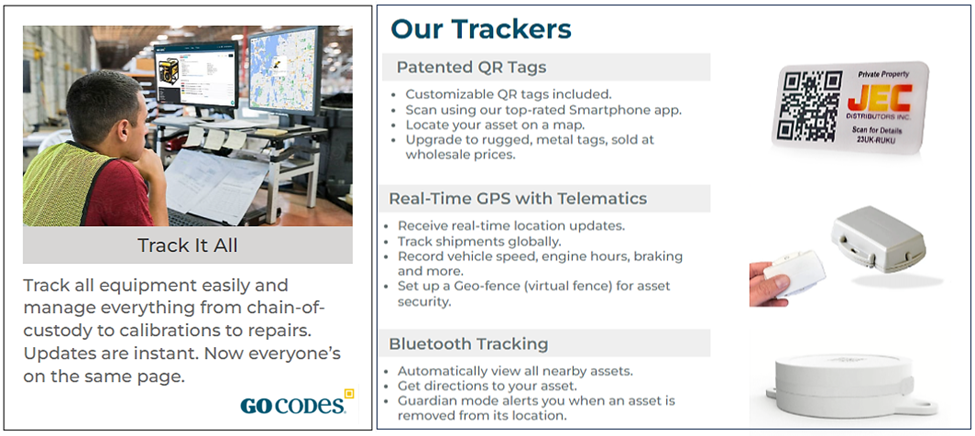
By combining these tracking devices, you can get a full, all-encompassing view of not only your fleet but also the remaining arsenal of your equipment and tools.
To recap, GPS tracking, as an essential part of telematics, provides managers with comprehensive, real-time fleet visibility, enabling them to enhance the safety and security of their assets, optimize routes, and monitor driver performance.
Helps Improve Project Planning
Effective planning is crucial for the success of construction projects, and telematics-powered fleet management software can play an important role in enhancing this process.
More precisely, managers can use valuable insights into fleet utilization and performance metrics derived from telematics data to make informed decisions that streamline resource allocation and improve project planning.
For example, telematics (sensors and GPS tracking) provides more precise and detailed data on fuel consumption, vehicle usage, and maintenance costs than non-telematics fleet management solutions.
By analyzing historical fleet utilization data, project planners and managers can more accurately estimate equipment costs, including operating hours, fuel expenses, and maintenance.
These insights help ensure that the proposed project budget is realistic, ultimately allowing for better financial planning and more accurate billing.
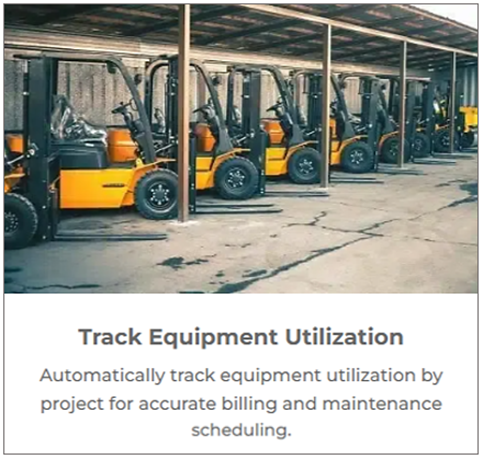
Furthermore, having real-time visibility of vehicle locations, utilization rates, maintenance status, and availability enables managers to efficiently cross-reference this information with specific project requirements.
They can access fleet management software directly to check whether their construction company has the appropriate equipment on hand or if it needs to be rented.
For instance, let’s say that a project calls for a bulldozer with specific horsepower and blade width requirements.
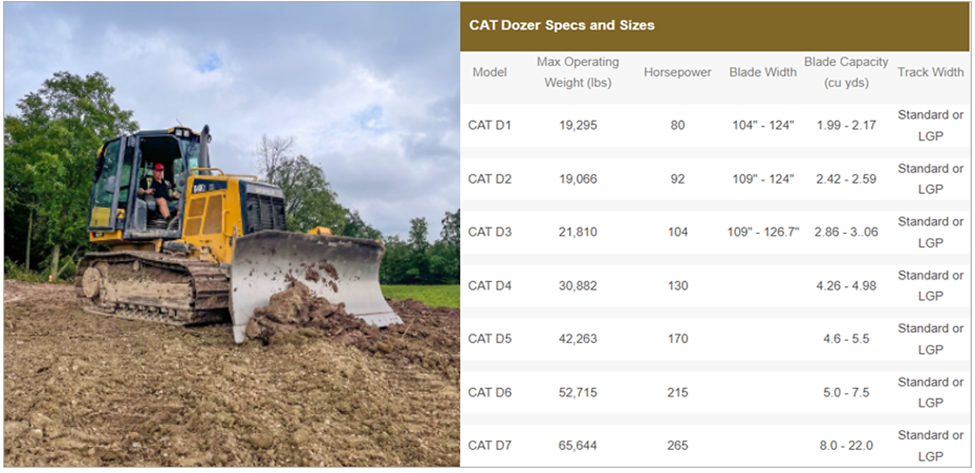
In such cases, managers can quickly check whether one of the company’s dozers fits those specific parameters by accessing the list of tracked assets on their phone, tablet, laptop, or desktop.
If the software’s database is correctly established (i.e., populated with relevant data), the machine’s specs should be easily available, thereby facilitating project planning and resource management processes.
Of course, one major advantage of having real-time information on your fleet’s whereabouts and status is that it vastly improves emergency planning, i.e., reacting to unplanned situations.
For example, if on-site equipment fails or site conditions unexpectedly require additional equipment, the fleet manager can quickly assess the availability of resources in the database and make necessary adjustments.
To sum up, telematics-enabled fleet management solutions allow construction companies to enhance project planning processes through more accurate cost estimation, improved scheduling and coordination, and dynamic equipment allocation.
Enables You to Conduct Preventive Maintenance
Another advantage of telematics is that it provides valuable data on vehicle diagnostics, including engine performance, fuel consumption, and maintenance needs.
This enables proactive maintenance scheduling, thus reducing the risk of unplanned downtime and costly repairs.
Since telematics devices are often connected to a vehicle’s network of internal sensors (i.e., onboard diagnostics unit), they’re able to continuously monitor vehicle health indicators.
In turn, this allows them to detect potential mechanical issues before they escalate into major problems.
For instance, if telematics detects a sudden drop in oil pressure or abnormal engine performance, the system can alert fleet managers to schedule maintenance inspections or address the issue promptly.
Moreover, some telematics solutions, like Volvo’s ActiveCare Direct, will decipher vehicle fault codes to help service technicians do their jobs more efficiently.
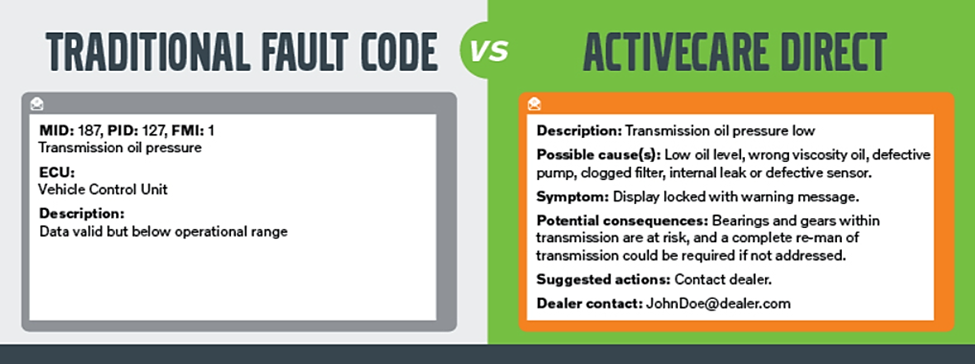
Regardless of the message format, such telematics-triggered alerts enable fleet managers to take immediate action and avoid further damage to the machine.
Without telematics, the drop in oil pressure would have to be detected by the operator either receiving a dashboard signal or doing a manual check.
Otherwise, the issue would remain undetected until machine failure or periodic inspections conducted during routine maintenance intervals.
Another example of how telematics helps in conducting preventive maintenance is the implementation of automated maintenance alerts and reminders.
More precisely, telematics devices can be configured to automatically generate alerts based on predefined criteria, such as engine hours or mileage.
When a vehicle or equipment in your fleet reaches a specified maintenance interval, the system sends notifications to the fleet manager, prompting them to schedule preventive maintenance tasks.
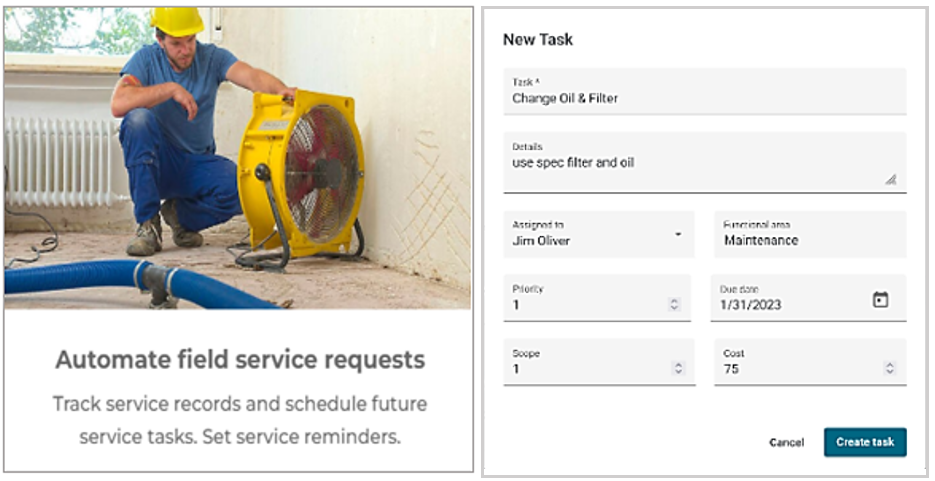
This proactive approach ensures that maintenance activities are conducted on time and according to manufacturer recommendations (warranty requirements), thereby prolonging the lifespan of equipment and reducing the risk of mechanical failures.
Overall, fleet managers can leverage telematics-derived real-time data and fleet management software’s automated alerts to proactively identify and address maintenance needs, minimizing the risk of unexpected breakdowns, operational disruptions, and costly repairs.
Helps Identify Cost-Saving Opportunities
We could argue that all the above benefits of telematics—full fleet visibility, accurate data for project planning, and automated preventive maintenance—already provide plenty of cost-saving opportunities.
However, one of the biggest advantages of telematics solutions is that they track fuel usage in real time, allowing fleet managers to monitor fuel consumption patterns and identify opportunities for fuel savings.
In view of recent fuel price hikes, geopolitical tensions, and increased environmental awareness, cutting fuel costs is among the top priorities of construction companies.
And, as highlighted by the U.S. Department of Energy, fuel-wasting driving habits can significantly reduce the mileage you get from each tank of gas.
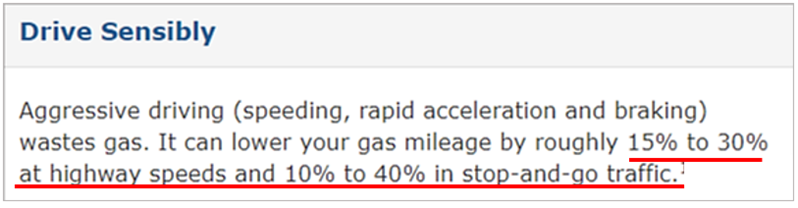
In light of this, the first area where fuel can be saved (and where telematics devices help) concerns promoting efficient driving practices.
More specifically, since every vehicle is tracked in real-time, telematics can reveal which drivers tend to engage in fuel-wasting driving behaviors, such as speeding, harsh braking, sudden accelerations, or excessive idling.
With these insights, fleet managers can devise coaching and incentive programs to encourage drivers to practice more mindful driving.
Here are just some fuel-saving driving suggestions:
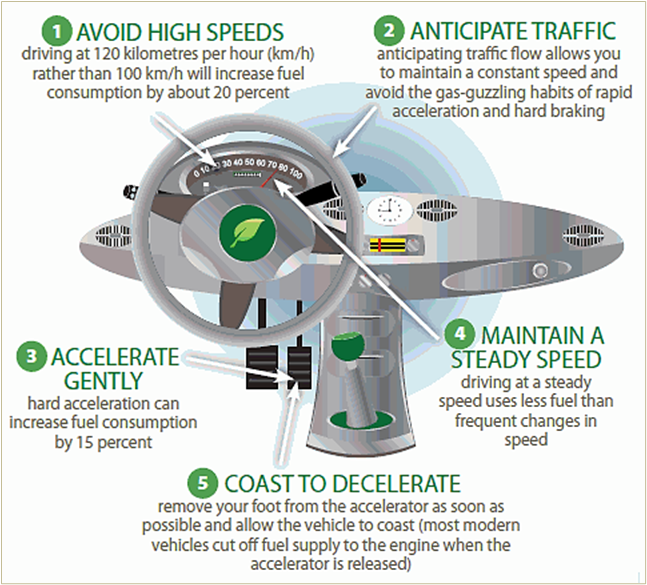
Another area where telematics helps is detecting when vehicles or equipment are left idling without any practical reason.
The telematics system can be set up to detect idling in different ways, such as monitoring engine activity, RPM, speed, ignition status, etc.
Regardless of the setup, fleet managers can gain valuable insights into extended idling events, with the level of detail varying depending on the sophistication of the telematics system configuration.
From there, they can take appropriate measures to reduce unnecessary idling.
Lastly, we already mentioned GPS-enabled route optimization, which can help further reduce fuel consumption by choosing the most fuel-efficient route (not always the shortest route).
To recap, telematics allows for easy detection of fuel-wasting driving practices, including idling, and helps optimize routes, thus enabling construction companies to lower fuel costs and minimize their environmental footprint.
Supports Data-Driven Decision-Making
Telematics systems play a crucial role in supporting data-driven decision-making in the field of construction fleet management.
As described, such systems are capable of aggregating a wealth of data related to vehicle performance, maintenance schedules, fuel consumption, driver behavior, and more.
By harnessing this data and integrating it into configurable reports, fleet managers can gain valuable insights into fleet operations and make informed, data-driven decisions.
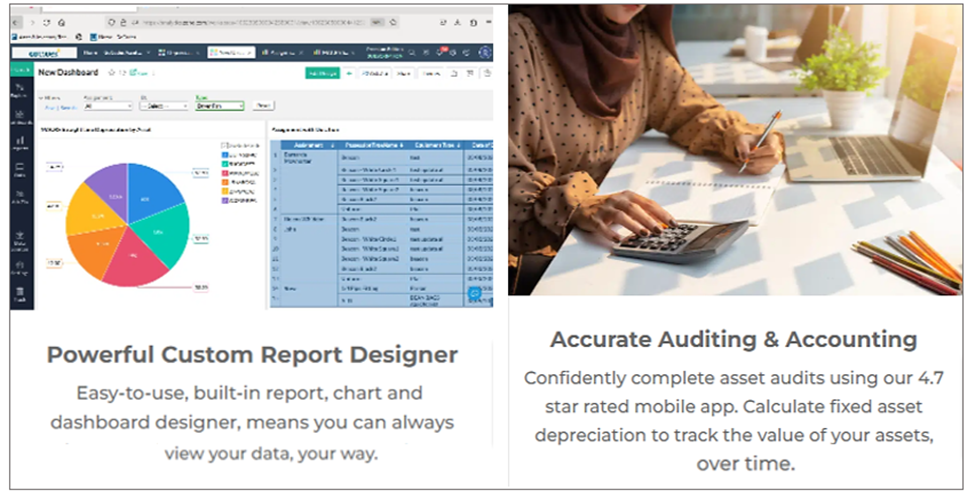
For example, the fleet manager can analyze telematics data on vehicle performance to identify patterns or trends, such as poor driving habits or inadequate maintenance intervals, that can lead to mechanical issues or breakdowns.
With these insights, the fleet manager can:
- promote mindful driving,
- adjust maintenance schedules for overworked or often-failing machines, and
- determine when it’s optimal to replace aging equipment.
Likewise, fleet managers can compare the performance of different equipment brands and models based on past usage, reliability, and maintenance requirements, thus providing decision-makers with valuable info when considering new equipment purchases.
At the same time, the fleet management software’s database and reporting functions allow other staff, like auditing officers and accountants, to access accurate, updated data in one place, enabling them to easily conduct equipment audits.
Overall, telematics-derived data, combined with the fleet management software’s analytical and reporting features, empower construction companies to make better-informed, data-driven decisions that enhance operational efficiency and reduce costs.
Conclusion
We hope all the benefits outlined in this article, along with examples of how telematics can improve fleet management, adequately demonstrate the transformative nature of this technology.
In conjunction with user-friendly fleet management software, telematics devices offer unparalleled fleet visibility, streamlined project planning, proactive maintenance, cost-saving opportunities, and data-driven decision-making.
Therefore, embracing a telematics-enabled fleet management solution that fits your company’s tracking needs and budget can help you optimize all aspects of fleet performance by maximizing operational efficiency and minimizing fuel and maintenance costs.