Key Takeaways:
- Efficient construction fleet tracking starts with selecting a fleet tracking system that is easily installed, user-friendly, and covers all fleet management needs.
- Setting up geofences can deter theft and unauthorized use.
- Installing fleet tracking devices in concealed locations within vehicles will minimize the risk of detection.
- Data provided by the fleet tracking system needs to be continuously monitored and analyzed.
As the number of your company’s construction vehicles and heavy equipment grows, ensuring that all of them are efficiently managed becomes essential.
In addition to preventing theft and aiding in locating stolen assets, fleet tracking can ensure that your construction operations are running smoothly while lowering maintenance and fuel costs and increasing equipment utilization.
However, to reap these benefits, construction companies should, other than selecting the right technology, leverage some best practices when tracking their fleets.
In this article, we’ll cover five best practices for construction fleet tracking and provide actionable insights for construction company owners and managers.
In this article...
Select the Right System
The initial best practice or first step on your journey to efficient construction fleet tracking involves selecting a tracking system that cost-effectively meets your specific fleet management needs.
In other words, with so many fleet tracking solutions out there, you should ensure that the tracking system you opt for helps you improve operational efficiency while not putting you out of pocket by providing features you’ll never use.
On that note, here are the key features you should prioritize when searching for potential fleet-tracking solutions:
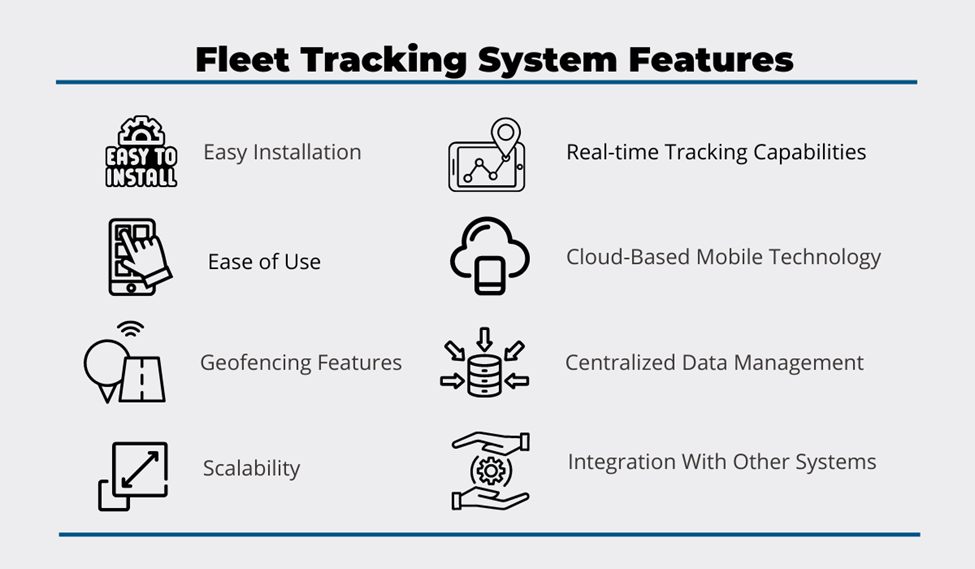
For instance, easy installation is paramount for minimizing downtime and ensuring swift deployment of the tracking system across the fleet.
More precisely, the installation of GPS trackers in your vehicles and heavy equipment should be quick and easy, allowing you to avoid extensive disruptions to ongoing operations.
Likewise, a user-friendly interface and intuitive functionalities are vital for ensuring that fleet managers and other personnel can easily navigate and utilize the tracking system without extensive training.
Of course, you also want your solution to provide real-time tracking and geofencing, as well as to be cloud-based, i.e., available on any internet-connected device.
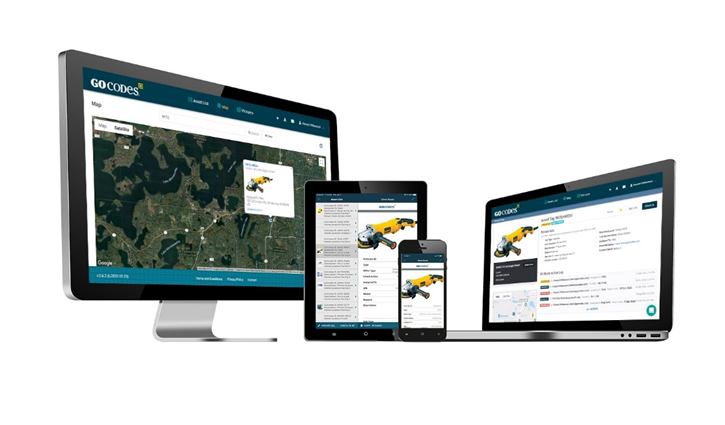
Additionally, the right system should be scalable, meaning you can easily add new tracked assets as your fleet grows.
This also implies that the system should provide centralized data management, i.e., allow you to use it as the central inventory database for all your assets beyond fleet vehicles and yellow iron, such as smaller equipment, tools, and spare parts.
Lastly, you want to ensure that the system can be easily connected to your other software systems, such as construction project management software or payroll and accounting solutions.
By enhancing data flow and interoperability, easy integrations can help you further streamline operations and decision-making processes.
With this quick rundown behind us, it’s time to suggest a tracking system that has all the above features (and more) and is considered one of the simplest and most affordable solutions on the market—our asset tracking solution, GoCodes.
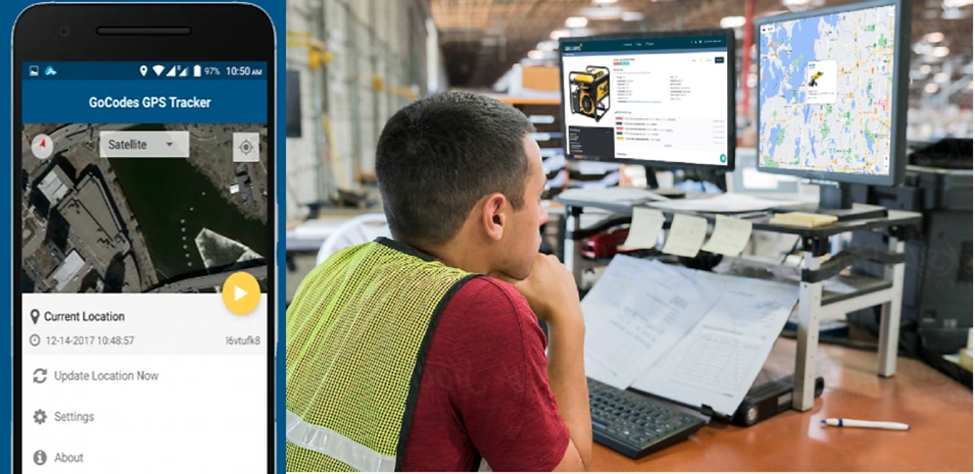
Our real-time GPS trackers use cell phone or Wi-Fi signals to provide minute-by-minute updates of your fleet’s location, showing you where your vehicles and heavy equipment are at all times.
They operate automatically, meaning all you need is GPS trackers and a mobile phone with the GoCodes app installed.
Our trackers are battery-powered and utilize ordinary AA batteries that should be replaced about every three years.
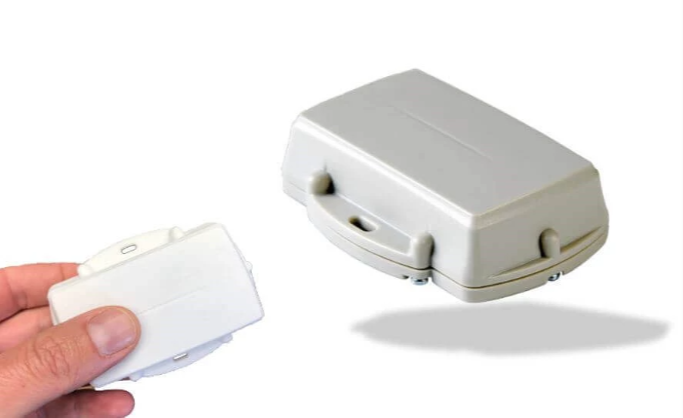
These small and easily installable devices will ensure your fleet is efficiently tracked in real-time, allowing you to monitor where your valuable equipment is and, if they’re stolen, track their location and alert the authorities.
Moreover, GoCodes is a one-stop solution that also takes care of other smaller and less costly equipment and tools by using GPS-enabled QR code tags attached to your assets.
Although this cost-efficient tracking method won’t provide automatic GPS location updates, it will help you keep tabs on your entire arsenal of equipment, tools, PPE, spare parts, and even construction materials.
Their location will be automatically updated every time workers use their smartphone or tablet to scan the QR code and access the list of all your tracked assets, regardless of whether they have real-time or scan-based GPS trackers.
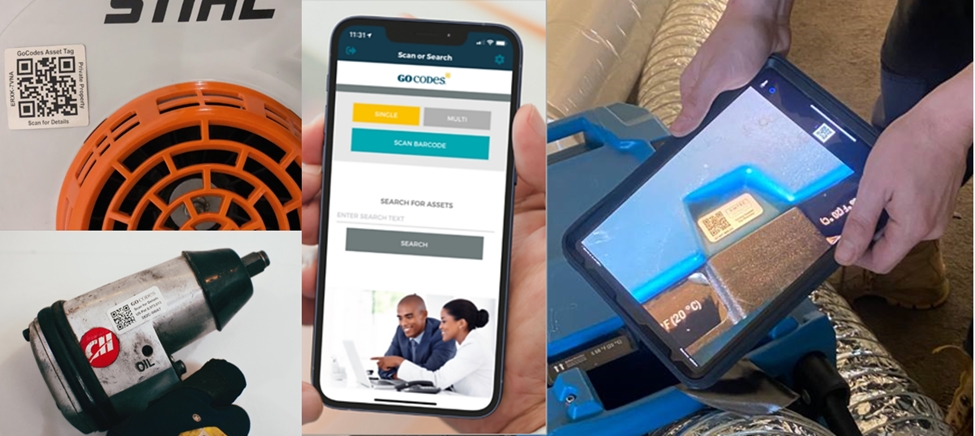
That way, you get to work with only one technology provider to track all your assets regardless of their value and size.
Since the cloud database is available on all devices and easily updated, this allows you to streamline many equipment management tasks, such as:
- tracking the location and usage of all your equipment and tools
- automating equipment check-in and check-out
- scheduling regular maintenance tasks
- monitoring equipment utilization
- generating various reports, from depreciation to inventory audits
As for our real-time trackers, they will record vehicle speed, engine operating hours, instances of hard braking or extensive engine idling, and more.
To recap, ensuring that your tracking system is easily installed, user-friendly, and covers all your asset tracking needs will set you on the right path to efficient construction fleet tracking.
Set Up Virtual Boundaries
One of the major benefits of utilizing a fleet tracking system is the ability to implement geofencing technology.
Geofencing allows you to create virtual boundaries around key locations such as jobsites, storage yards, and other critical areas.
By defining these geofences, fleet managers can receive real-time alerts when vehicles enter or exit designated zones, thereby enhancing security i.e., deterring theft and unauthorized use.
Dev Bhatia, former Chief Marketing Officer at Momentum IoT, explains:

Geofencing leverages your tracking system’s ability to correlate specific equipment with GPS trackers with a predefined geographical area to establish virtual perimeters around it, as illustrated.
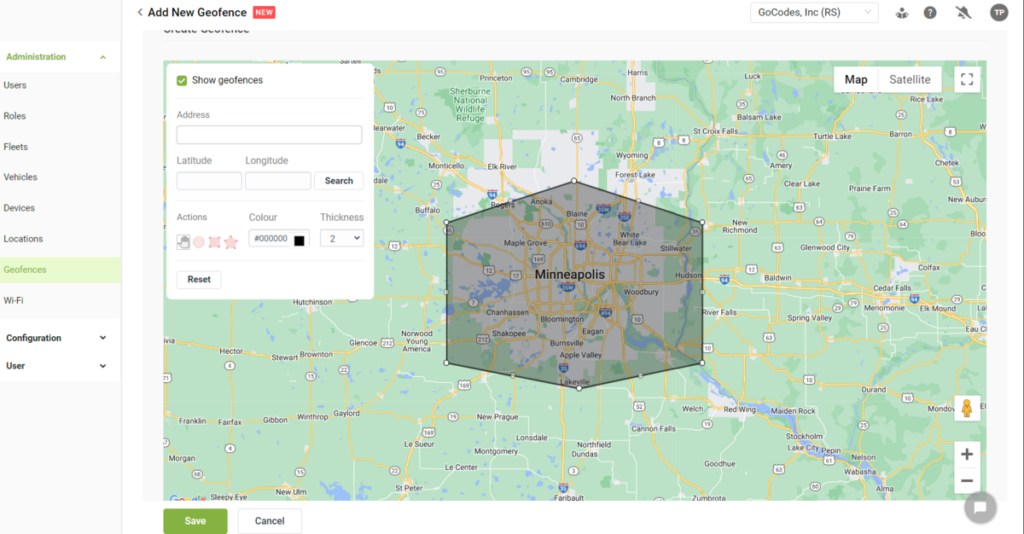
These invisible fences allow the system to automatically generate alerts to notify the fleet manager when your equipment enters or—more importantly for security purposes.—exits these boundaries.
This proactive approach enables swift response to any unauthorized activities, thereby preventing potential theft and misuse of construction vehicles and equipment.
For example, you can set up a geofence around a storage yard or jobsite where your valuable equipment is kept overnight.
When the virtual perimeter is set, any attempt to move equipment outside of business hours will trigger an alert to the fleet manager’s mobile device.
This immediate notification allows the manager to investigate the situation promptly and take appropriate action, such as notifying security personnel or law enforcement.
Therefore, utilizing your fleet tracking system’s geofencing features is a best practice essential for safeguarding your assets.
By establishing virtual boundaries and leveraging real-time alerts, you can effectively prevent theft and unauthorized use, as well as enhance overall fleet security and efficiency.
Secure Your Tracking Devices
Since your tracking devices keep your equipment secure, it’s only logical they should be secured as well.
After all, you don’t want those with ill intentions to simply remove the device or tamper with it.
One key step in securing tracking devices is to install them in concealed locations within vehicles, as this will minimize the risk of detection.
Additionally, employing tamper-evident seals or enclosures can further enhance security by making any attempts at tampering immediately apparent.
Another effective measure is to use dummy trackers (conveniently placed in a not-so-hard-to-find location).
That’s exactly what contractor Ben Kasper did, reports CBS News.
When his $95,000 skid-street loader was stolen, the real tracker allowed him to locate his equipment and notify the police.

Upon retrieving his equipment, Kasper explained how he found the loader and what helped him do that:
“They ripped out the phony GPS tracker I put in it, but the real GPS tracker was in it – and that got me notified of this location.”
Moreover, when he got to the warehouse where his stolen equipment was kept, he also realized that all the other equipment in it was probably also stolen.
He was right, and a number of contractors whose equipment had been stolen also got it back thanks to Kasper.
This example nicely illustrates the importance of securing your tracking devices in a concealed location (and using a decoy to trick the tricksters).
Moreover, tamper-evident seals or enclosures and well-concealed trackers can also prevent less honest employees from turning them off when using equipment without authorization for private purposes.
This will not only protect your equipment from misuse but also maintain the reliability and accuracy of the tracking data collected.
Why this is important will become clear in our next section.
Analyze the Data
Other than safeguarding your equipment, a fleet tracking system provides a wealth of data that can be used to streamline and enhance your company’s operations.
Therefore, you should adopt a proactive approach to continuously monitor and analyze tracking data and uncover valuable insights and opportunities for improvement.
Historical data collected in your tracking system can be particularly valuable in this regard, allowing you to optimize routes, improve fuel efficiency, and enhance fleet allocation and maintenance.
For example, by analyzing past vehicle routes and utilization patterns, you can identify inefficiencies and adjust schedules or routes to minimize travel time and fuel consumption.
Additionally, you can detect when your equipment is unnecessarily idling.
According to the Alaska Department of Transportation and Public Facilities, idling increases fuel consumption and strains the engine.
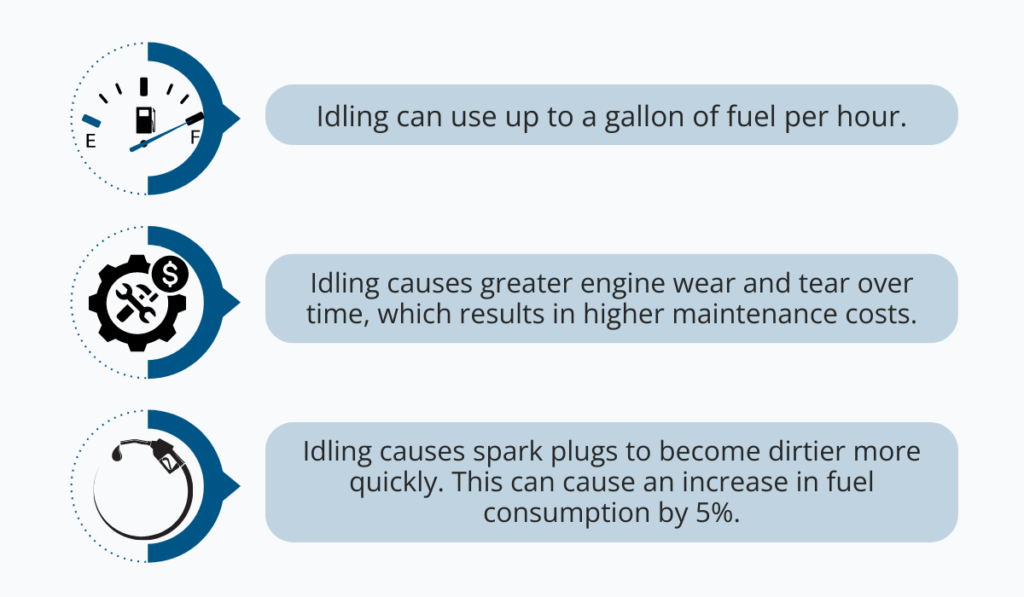
The above facts are even more concerning when you consider that construction equipment spends more than 30% of its lifetime idling.
Of course, not all idling is without reason, but there are a lot of fuel and maintenance costs that can be saved by leveraging your tracking system’s historical data to detect instances where operators do keep engines turned on when it’s not necessary.
Moreover, analyzing tracking data will enable your fleet manager to make better-informed, data-driven decisions across various aspects of construction operations.
For example, they can schedule maintenance based on operating engine hours, thus minimizing the possibility of breakdowns due to overworked engines.
As mentioned, you can also keep tabs on vehicle speed, rapid acceleration, and hard braking, all of which increase fuel consumption.
To recap, the best practice of regularly analyzing the data from your tracking system and leveraging the insights gained allows you to operate your fleet more efficiently and cost-effectively.
Encourage Open Communication
Effective fleet management extends beyond the technological aspects of tracking systems.
It also involves fostering open communication with employees, particularly drivers, regarding the purpose and benefits of fleet tracking.
This is crucial to alleviate concerns or misconceptions some employees might have about vehicles and heavy equipment being tracked, seeing it as an intrusion of their privacy.
Although tracking company-owned vehicles is generally legal, there are some differences between U.S. states, so it’s wise to check your state laws or consult legal professionals.
For example, as illustrated, construction companies in California should, as a best practice, get written consent from their drivers and operators.

In comparison, contractors in states like Kansas, Georgia, and Missouri won’t need their employees’ consent to track company-owned vehicles, but it’s still recommended to openly address the subject of fleet tracking.
In doing so, it’s essential to emphasize to operators the overarching goals of fleet tracking, such as enhancing safety, security, and operational efficiency.
By highlighting the role of tracking systems in promoting safer driving practices, preventing theft, and optimizing routes, managers can underscore the tangible benefits that tracking technology brings to both the company and its employees.
Some companies even establish incentives for drivers with the best driving behavior, thus turning GPS tracking into a prize contest, which helps improve the workers’ perception of fleet tracking.
Overall, by openly communicating with your employees and alleviating any concerns, you can ensure that your fleet tracking initiative is met with their understanding and support.
Conclusion
We’ll close this article by saying that prioritizing the fleet tracking practices outlined in this article can help you unlock new levels of productivity and profitability while safeguarding your valuable assets.
From selecting the right tracking system, leveraging geofencing and data analysis, and securing your trackers to fostering open communication with employees, each of these aspects plays a crucial role in enhancing efficiency, safety, and overall fleet management.