“Boss, we have a problem.”
This phrase strikes a chord with every construction equipment manager, signifying an unwelcome disruption in their operations.
Yet, the challenges within construction are many, ranging from lost or stolen equipment to project delays resulting from unexpected delivery delays.
The silver lining is this: there are now technological solutions that specifically target these common yet persistent issues.
In this article, we shed some light on one of these solutions: equipment management software.
So read on to find out how this piece of technology can help you address some of the common problems in the industry and contribute to the optimization of various workflows within your company.
In this article...
Costly Project Delays
Project delays in construction are more than just inconveniences; they represent a major threat to a business’s success.
The ramifications of this serious problem include financial losses but also potential damage to a company’s reputation, possibly leading to the loss of future clients.
So, how does equipment management software help in this regard?
By improving your equipment maintenance strategy.
After all, well-maintained assets are reliable assets. They won’t unexpectedly break down, even in those critical moments.
In fact, research consistently demonstrates that businesses adhering to proactive maintenance strategies encounter considerably fewer defects and experience minimal equipment downtime.
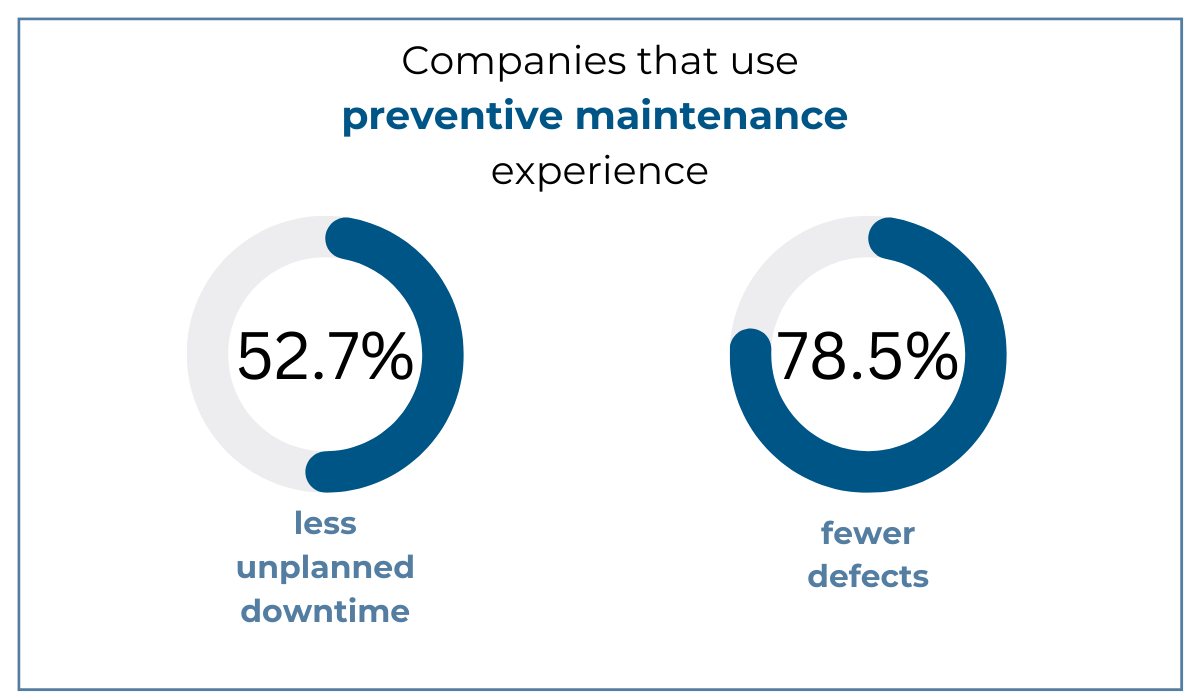
This is because regular inspections and servicing allow for the detection and resolution of smaller problems with equipment before they escalate.
To understand how exactly equipment management systems contribute to this regime, it’s essential to explore their features.
Task management, for example, empowers users to manage service tasks, assign them to specific employees, and then monitor their progress, which makes maintenance planning and scheduling a breeze.
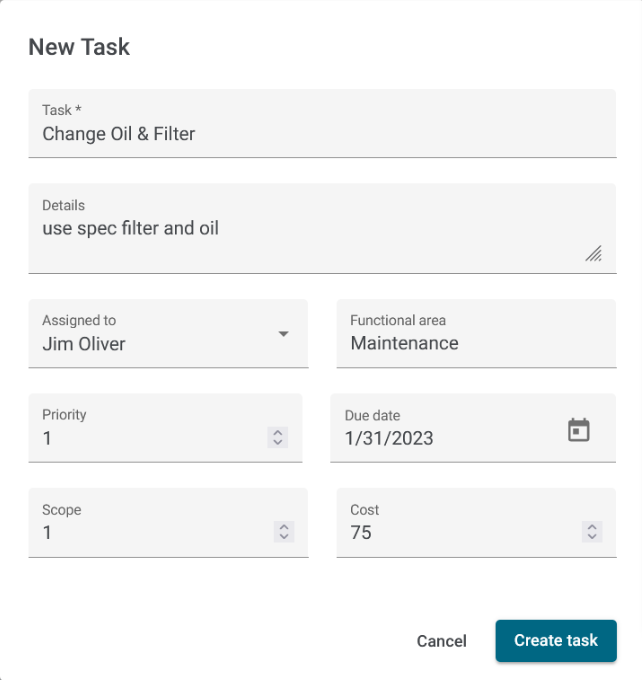
This functionality also proves invaluable in ensuring your team stays on top of their responsibilities.
No more arguments about who was responsible for that filter change—all information is documented in the system and everyone knows their role.
Automated field service requests are yet another key feature that elevates your maintenance strategy and prevents project delays.
Imagine your workers identify a potential issue with a machine on a job site.
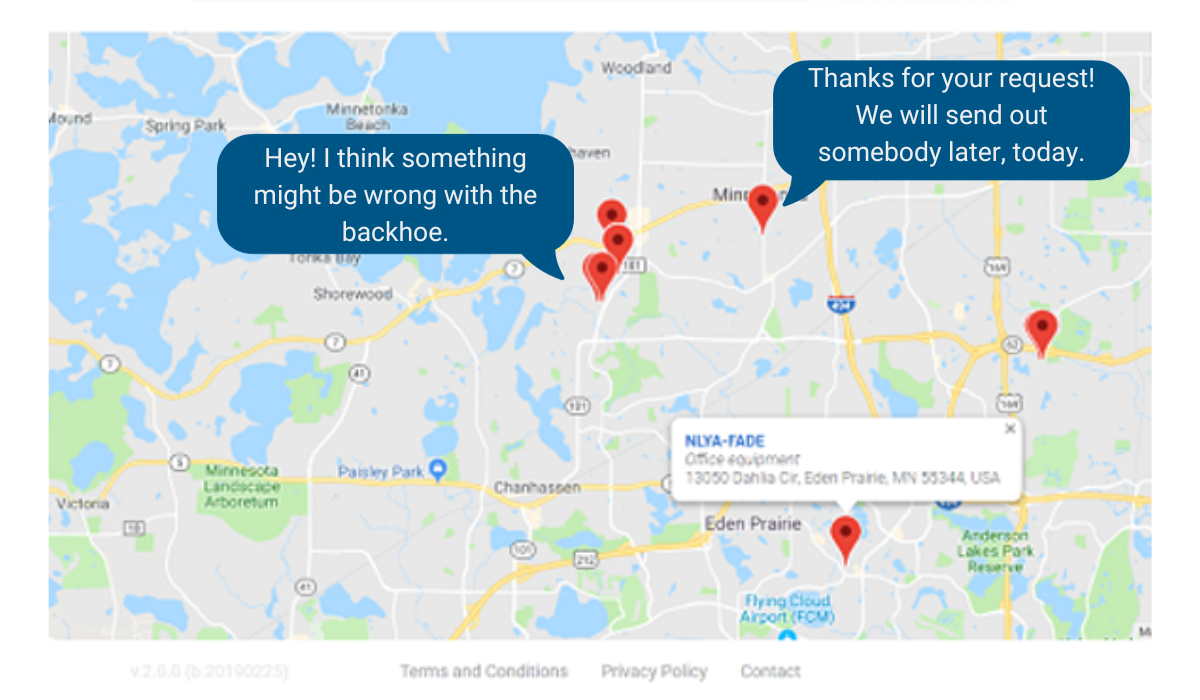
Instead of engaging in time-consuming calls until they finally reach someone who can help, they can use the app to send a message with a detailed description of the issue, location, and the machine involved to the maintenance team.
The responsible person can then swoop in, inspect the asset, and nip the problem in the bud before it turns into a disaster.
All in all, the importance of a proactive maintenance approach in keeping your machinery operable and your projects on track cannot be overstated.
By integrating equipment management software into your operations, you can streamline the complexities of maintenance planning and organization, resulting in a more efficient and effective overall process.
Inefficient Equipment Use
Are you losing sleep over the thought that your company’s valuable assets might not be used to their full potential?
Is there a machine hoarding issue within your company?
The truth is, without proper equipment management software, you just can’t know for sure whether you’re making the most out of your assets, and that’s a problem because idle machines at a job site mean you’re bleeding money instead of raking in profits.
This issue can be particularly critical for those renting their equipment.
Their money gets tied up in the rental fees for this underutilized machinery when it could be better used elsewhere in the project or business.
As Lonnie Fritz, senior market professional at Caterpillar, emphasizes, knowing that a machine is in the field is simply not enough.
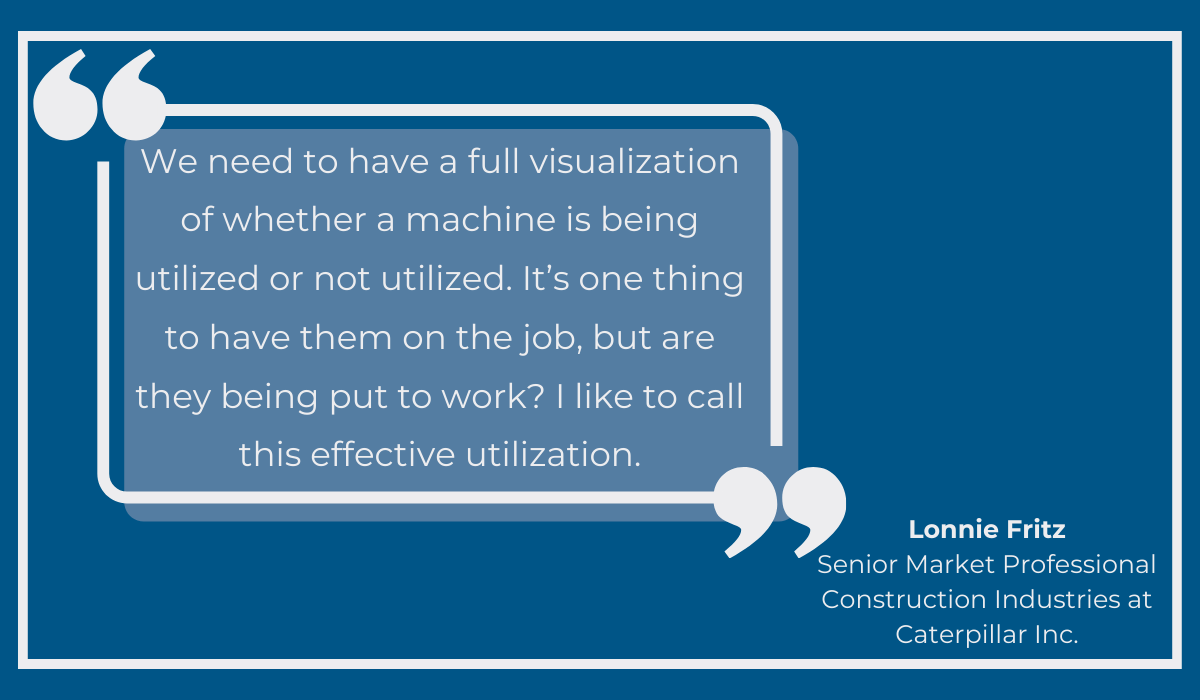
You also need to understand if and how it’s being used.
At the end of the day, your equipment is too big of an investment for it to gather dust on a job site.
Equipment management software addresses the problem of underutilized assets by providing complete transparency into various aspects of their usage, such as:
- Equipment check-in/check-out
- GPS location
- Machine part action
- Ignition running time
- Miles
- Fuel use
- Engine hours
Armed with this comprehensive data, you gain the ability to swiftly assess whether your equipment is where you need it to be productivity-wise, and allocate your assets accordingly.
If, for example, some equipment at one job site is not being used, relocating it to another, more strategic location or returning rented machinery can help decrease unnecessary expenses.
The last thing any business owner wants is for their resources to be wasted or used ineffectively.
Luckily, equipment management solutions give you total visibility and control over your assets so you can make sure they are performing at their best every single day.
Reliance on Manual Record-Keeping
Record-keeping is one aspect of construction operations that could arguably benefit the most from a technological upgrade.
But, what’s wrong with keeping track of your asset inventory via pen and paper or Excel?
Sure, those may be a viable solution for small businesses with a limited number of assets, but their efficacy diminishes as the company and the asset portfolio expand, which then leads to the primary issue with manual record-keeping: its vulnerability to human error.
This problem is further underscored by a survey from Acuity Training, revealing that users often lack proper training in tools like Excel, resulting in mistakes that cost companies both time and money.
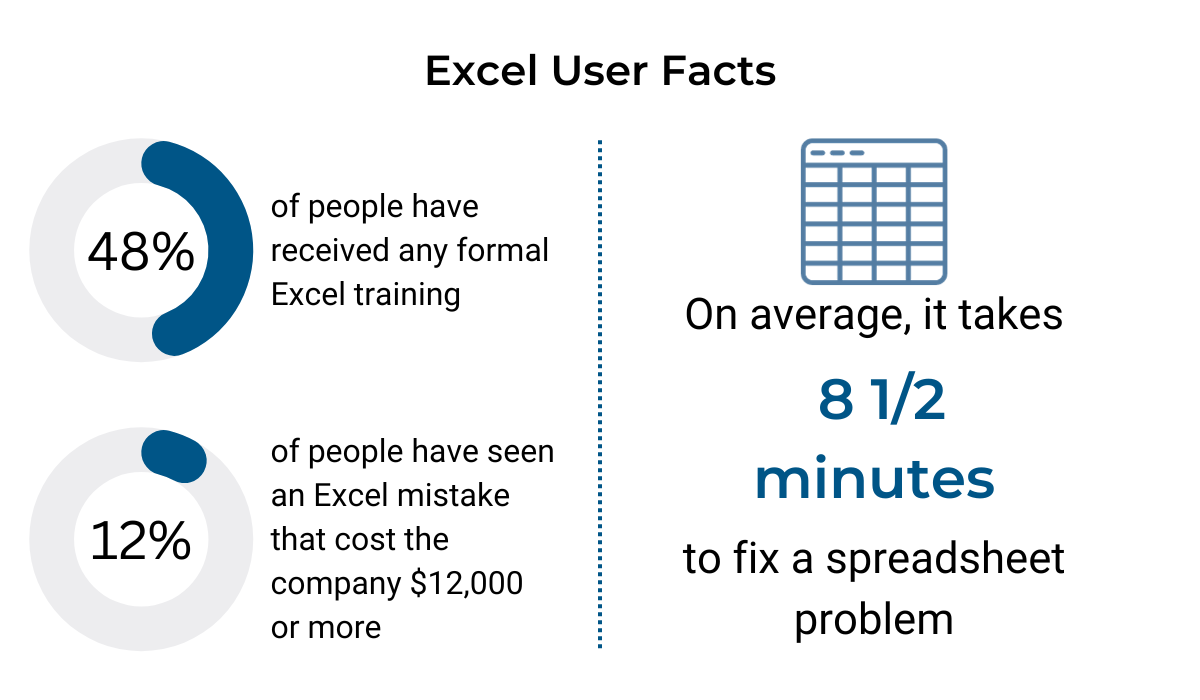
Think about it.
Can you really afford to base critical decisions on potentially flawed information?
Equipment management systems, on the other hand, automatically record every change in the asset inventory, whether it’s the purchase of new assets, disposal of old ones, or updates on current equipment usage status.
The software also centralizes crucial data for each machine and tool you own, including warranty details, salvage value, current location, user, and more.
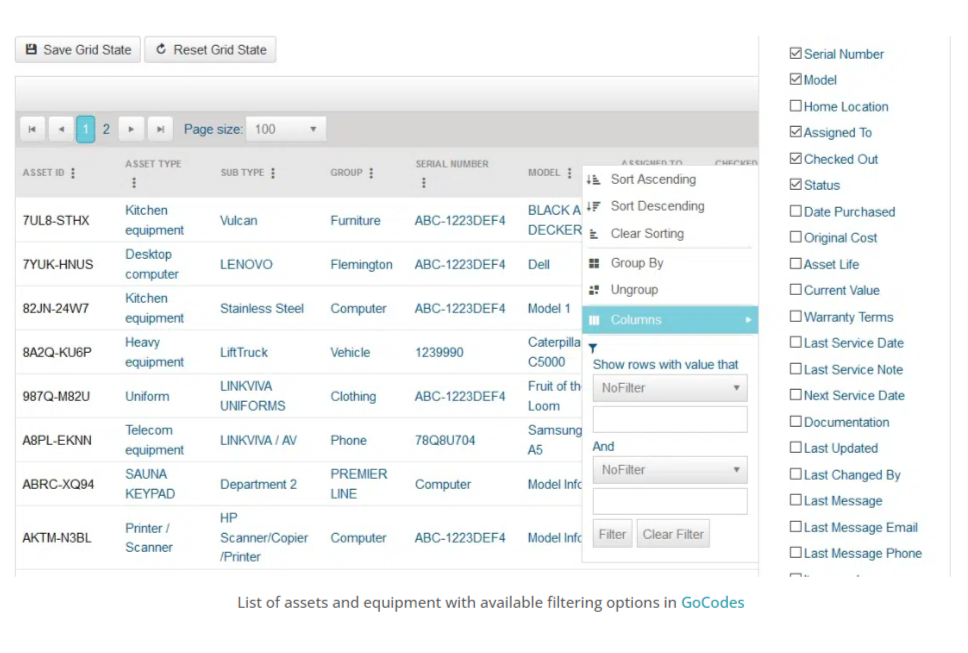
The outcome?
Detailed, up-to-date, and accurate records that can be accessed anytime, anywhere, and using any device with an internet connection.
Manual tracking methods simply cannot compete with this level of efficiency.
Remember, reliable information is vital for well-informed decision-making, whether it pertains to asset allocation, maintenance planning, or equipment acquisition, disposal, and upgrades.
Equipment management software eradicates errors from your records and equips you with dependable data, which you can then use to lead your business toward success with confidence, making decisions that propel you forward, not hold you back.
Coordinating Equipment Availability
We’ve previously discussed the challenges that construction companies face with excess unused machinery on job sites, but what about the flip side—insufficient equipment availability?
Let’s be honest, such problems can greatly impact overall productivity.
Just picture this: your team, on a tight schedule, searching desperately for a crucial piece of equipment, only to discover it’s been relocated to another site or used by someone else.
The result?
Hours wasted, progress impeded, and project delays looming on the horizon.
It’s a scenario no construction manager wants to face.
That’s why we’ve developed GoCodes Asset Tracking, a QR code-based equipment management software that addresses these issues head-on.
The system helps you schedule equipment use and prevent conflicts by allowing you to pre-assign assets to team members and set a return date.
Should a machine or tool not be returned on time, the worker using it receives an email reminder prompting them to return it.
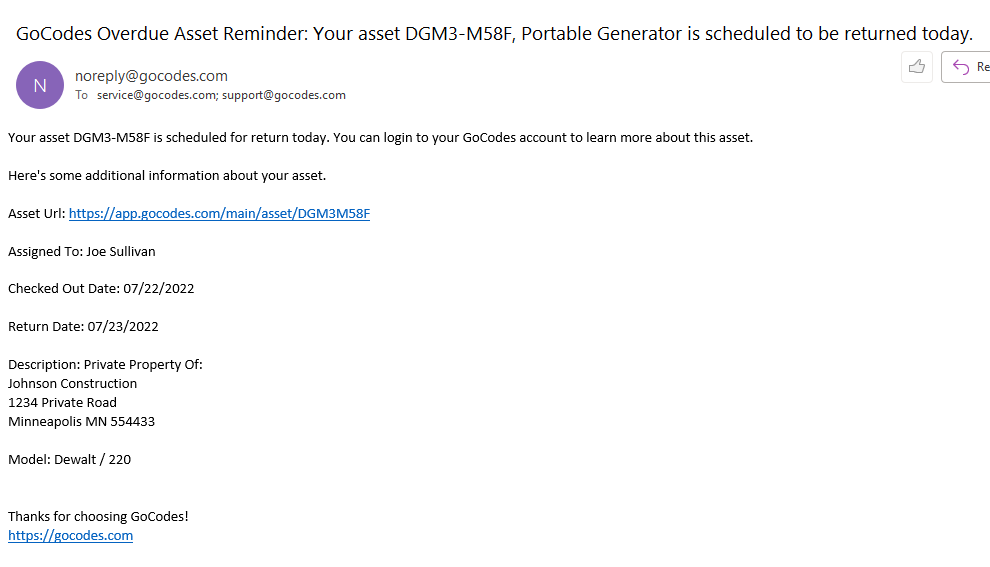
Our solution is elegantly simple: to get started, all you need are two things—QR code asset labels and the GoCodes Asset Tracking app.
Attach the labels to your equipment and then scan them via the app for a quick check-in or check-out.
Each time this is done, the location of the update is recorded, too.
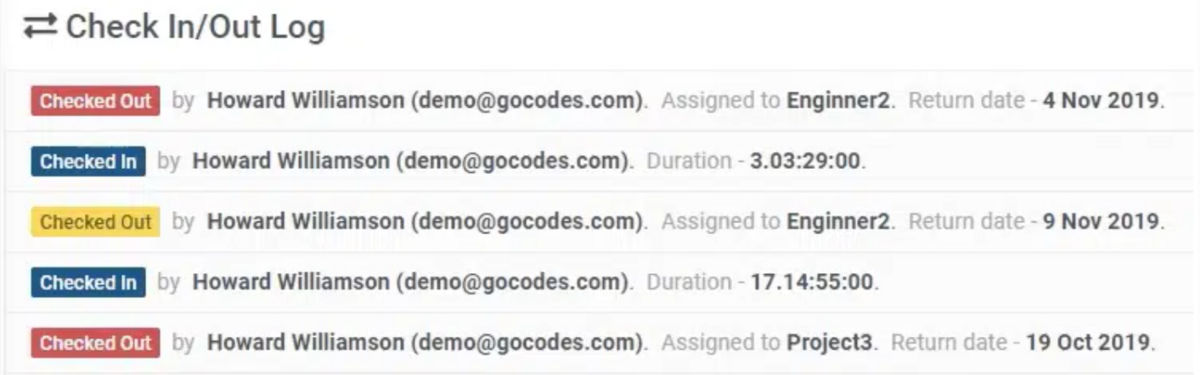
So, if you or your workers don’t know where a particular machine is, you can just take out your smartphone, and it’ll tell you not only where it is but also who’s using it, for what project, and when it’ll be ready for use again.
In essence, GoCodes Asset Tracking, by providing complete transparency of your assets’ whereabouts, liberates you and your employees from the worry about tool availability, allowing you to channel your efforts into more important tasks.
With this powerful tool in your arsenal, you can be confident that the right equipment will be in the right place at the right time, facilitating a smoother and more efficient workflow for your entire team.
Monitoring Equipment-Related Costs
Effectively monitoring and managing your equipment-related costs can be a daunting task without the support of equipment management software.
Without an adequate system in place, you lack precise insights into your costs, making it challenging to ensure adherence to your budget—a key responsibility for any equipment manager.
So, why is exactly tracking costs so crucial?
It allows you to compare actual expenses against budgeted costs, identify discrepancies, and implement corrective actions based on these insights, keeping your project within defined budget constraints.
In short, maintaining a vigilant focus on equipment-related costs is imperative for budget control.
Equipment management software acts as a reliable data repository, recording all pertinent expenses, including:
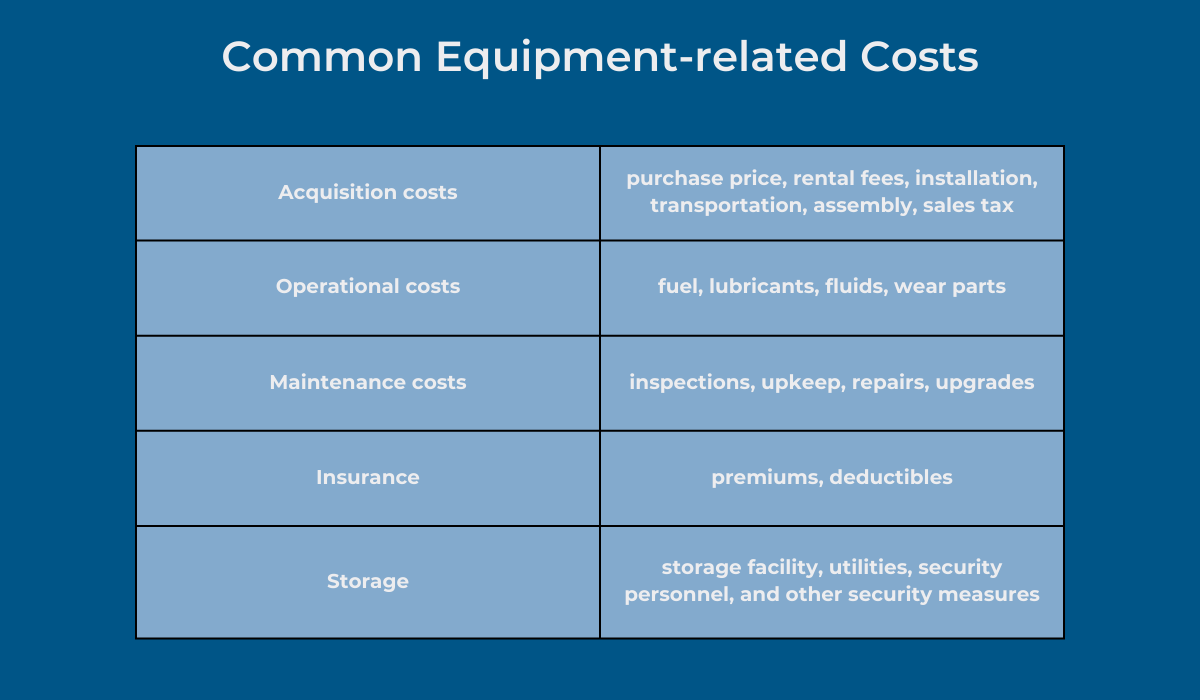
Trying to keep track of all of these expenses manually is downright impossible and could potentially result in costly mistakes, like budget overruns, decreased profitability, or cash flow problems.
However, equipment management systems go beyond mere data collection and storage and often incorporate reporting tools that help analyze the accumulated data.
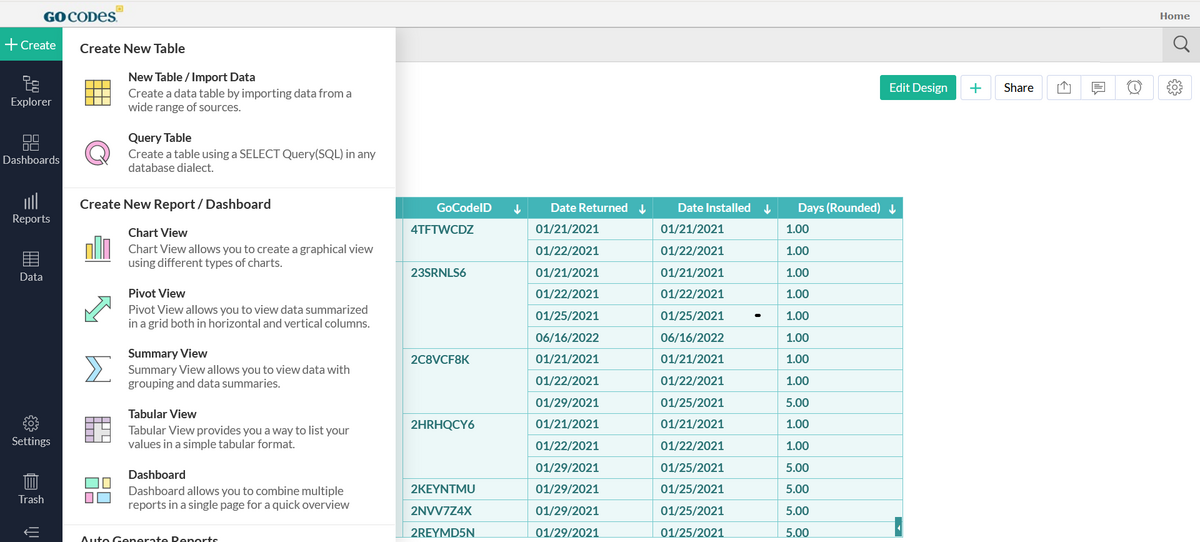
They generate reports that automatically consolidate the costs associated with each project, based on the expenses incurred by every piece of equipment used for that specific project, taking your budgeting game even further.
Keep in mind that these expenses are more than just bills to be paid.
Instead, they serve as a valuable tool for budget control and increased profitability.
In this context, equipment management software becomes your financial sidekick, assisting you in staying on track with all your equipment-related costs, and providing you with actionable insights that contribute to more informed decision-making.
Conclusion
Hopefully, we successfully demonstrated how technology isn’t a mysterious force to be feared but a reliable ally that helps tackle your everyday challenges.
However, the use of equipment management software extends beyond simply addressing common industry issues and establishes the groundwork for a more efficient, compliant, and resilient business.
Embracing this tool allows you to streamline operations, boost productivity, and, most importantly, maintain competitiveness in an ever-evolving market.