Key Takeaways:
- Equipment management software can be paired with hardware.
- It tracks and optimizes equipment use to reduce costs.
- It also simplifies maintenance scheduling.
- Real-time GPS and geofencing prevent equipment loss and theft.
Managing construction equipment efficiently takes careful planning, but also the right tools.
With rising demands and tight project schedules, even the most skilled teams need a boost to optimize equipment utilization, minimize downtime, and keep operations on track.
That’s where equipment management software comes in handy.
In this deep dive, we’ll take a look at the key benefits and functionalities of equipment management software.
If you are thinking of adopting it, or you are already searching for the best fit, this is the article for you.
Let’s jump right in!
In this article...
What Is Equipment Management Software?
Equipment management software enables construction businesses to log, track, maintain, and use all assets as efficiently as possible.
It combines asset tracking and equipment maintenance functions, helping you pinpoint where everything is at all times while ensuring it’s utilized to its fullest potential.
In other words, with such software, you can more easily address common equipment management challenges, meet project-specific demands, and unlock long-term benefits.
Given all this, it’s not surprising that the equipment management software market is expected to grow to $18.9 billion by 2032, reflecting its growing importance in construction.
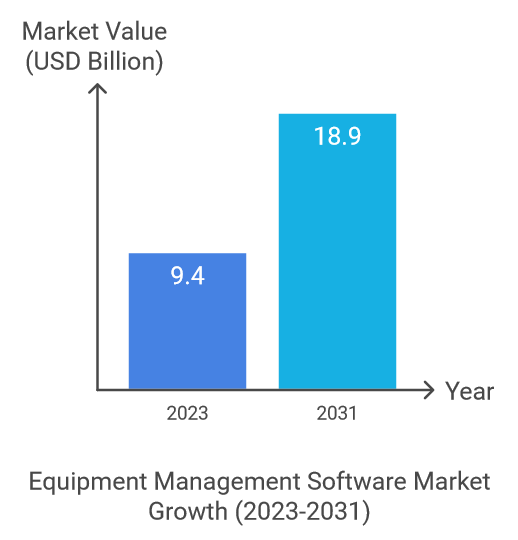
Now, how can equipment management software do all that?
Well, because it streamlines and improves various processes, including:
- Job scheduling
- Inventory tracking
- Usage monitoring
- Lifecycle management
To be able to do that, equipment management software needs a centralized database with all of your asset information that’s easy to access and update in real time, using any device.
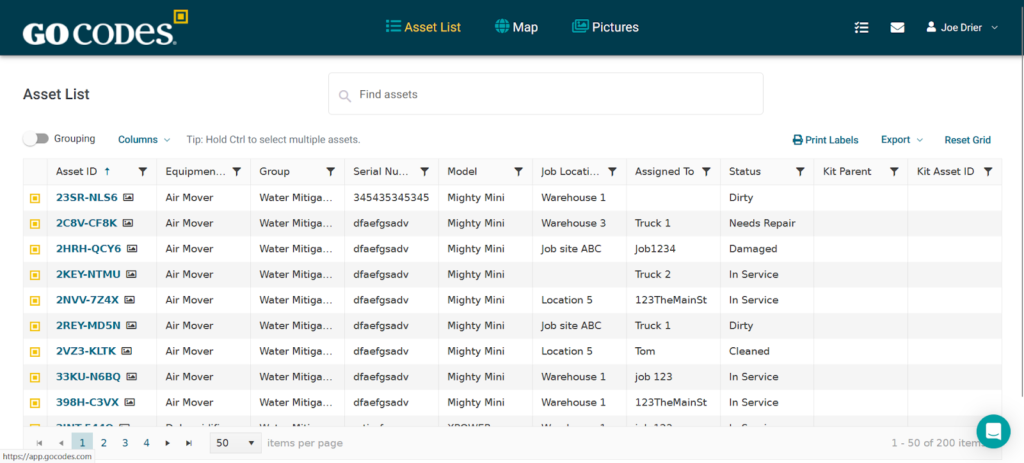
Another essential thing is the ability to assign unique identifiers to each asset or inventory item.
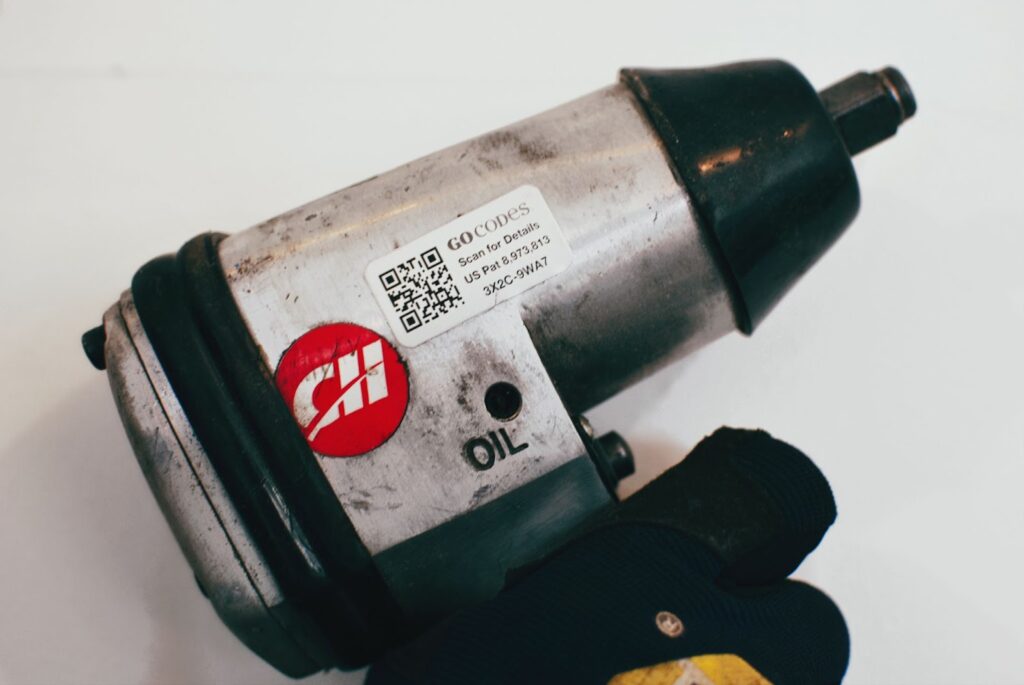
This eliminates the chance of any mix-ups, if, let’s say, your company owns three excavators of the same make, model, and age, or identical sets of power tools.
The equipment management system charts each piece of equipment separately, making it easier to monitor its condition and usage and maximize uptime and productivity.
Depending on your priorities and scale of operations, you can opt for all-around solutions like Procore’s construction management suite or more specialized asset management software like our GoCodes.
No matter your preferences, these systems enable you to reap several benefits which we’ll dive into next.
Benefits of Using Equipment Management Software
Using equipment management software has several advantages over manual tracking methods, leading to huge cost savings and an efficiency boost.
In this section, we’ll explore three key benefits, starting with improved equipment utilization.
Improves Equipment Utilization
Equipment management software provides construction businesses with real-time data on equipment utilization.
How?
It’s simple.
Equipment management software usually comes with an easy–to–use barcode scanning checkout system, so you can clearly see who used which tool, and for how long.
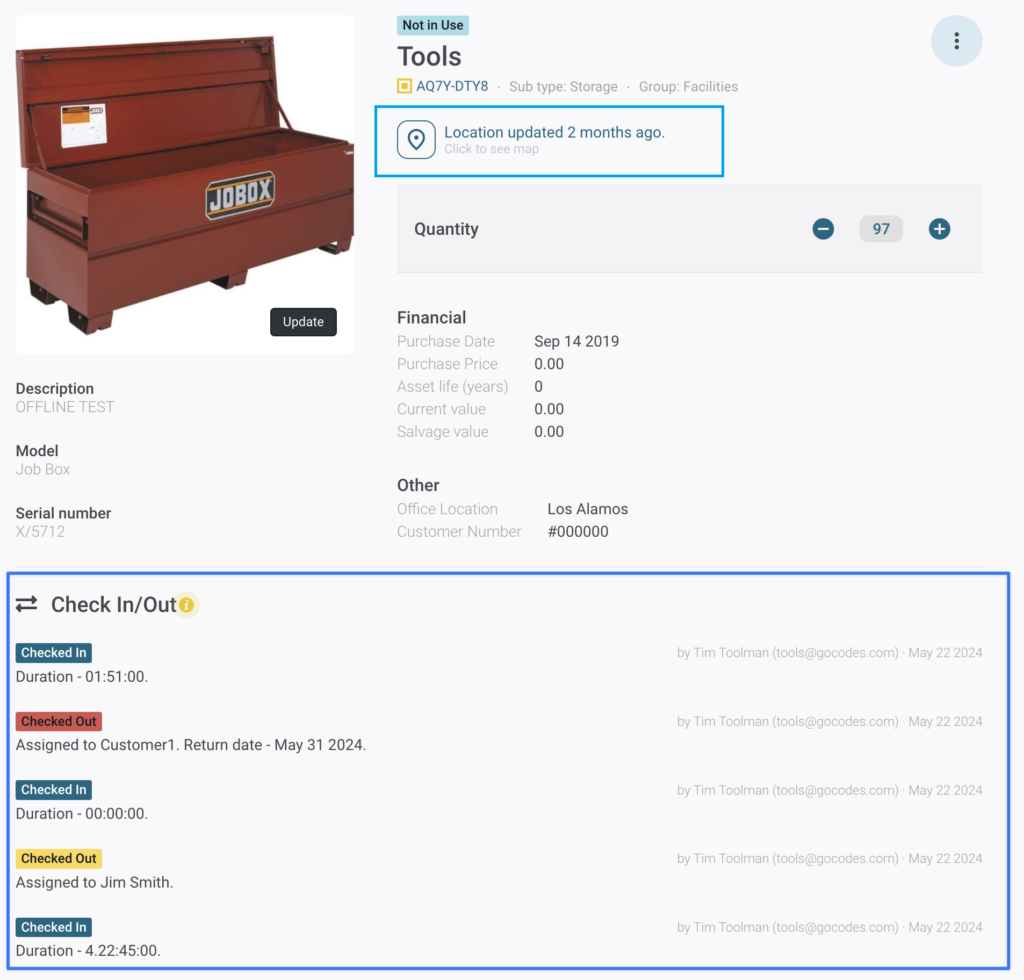
With this information for each piece of equipment, you can make better decisions on where to allocate your assets to be fully utilized.
Maximizing equipment utilization also means you’ll be less reliant on rentals or new acquisitions, helping you save money in the long run.
Equipment management software that has built-in telematics features takes this one step further.
According to Teletrac Navman’s recent survey, it can help you maximize equipment utilization in a bunch of different ways by tracking various data, which you can see below:
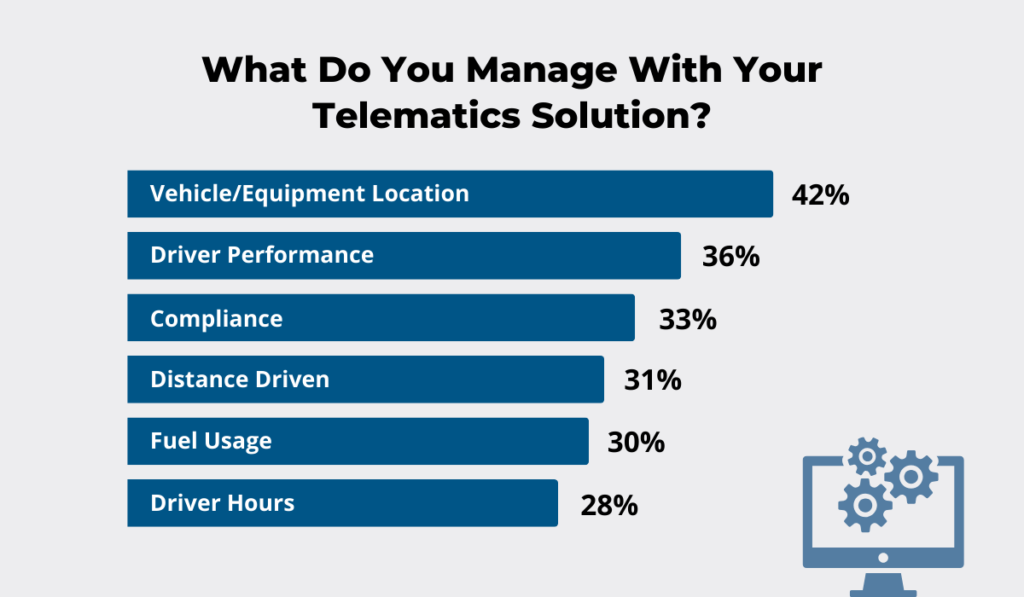
Equipment management software uses telematics to track key equipment utilization metrics, such as operating hours, location, and utilization rate.
Collecting data on fuel usage and mileage of your larger machines is especially important, explains Kevin Aries, Director of Product Marketing for Verizon Connect:
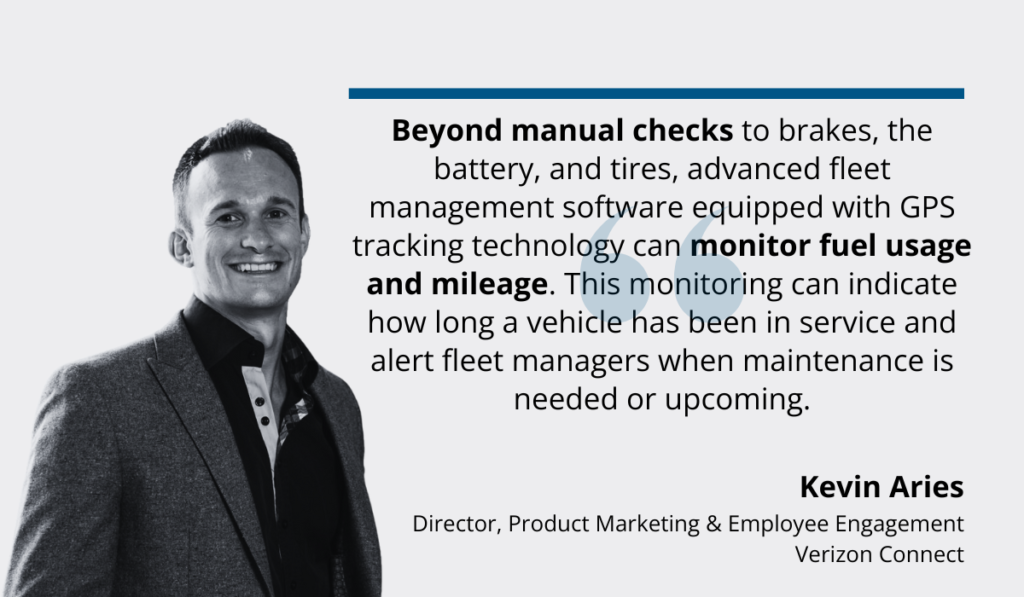
While this information guides maintenance efforts, it also leads to notable operational improvements and additional benefits.
For instance, using the telematics data can help you spot any fuel-related inefficiencies, and determine alternative, quicker routes for your heavy machinery.
In this way, you’re maximizing the utilization rate of your key pieces, but also preventing engine idling which quickly leads to excess fuel costs.
Ultimately, the software gives you a bird’s-eye view of all your equipment, and the utilization insights provide the basis for better productivity and fewer unnecessary costs.
Reduces Equipment Downtime
Unplanned downtime is a major productivity killer, easily driving up costs and leading to project delays.
Remember the last time a piece of your equipment broke down suddenly?
The chances are that you scrambled to find replacements or arrange emergency repairs, had to halt work or even push back project timelines.
Shawn Beinhower, CIO at E.K. Services Inc., illustrates just how disruptive, costly, and time-consuming equipment downtime can be:
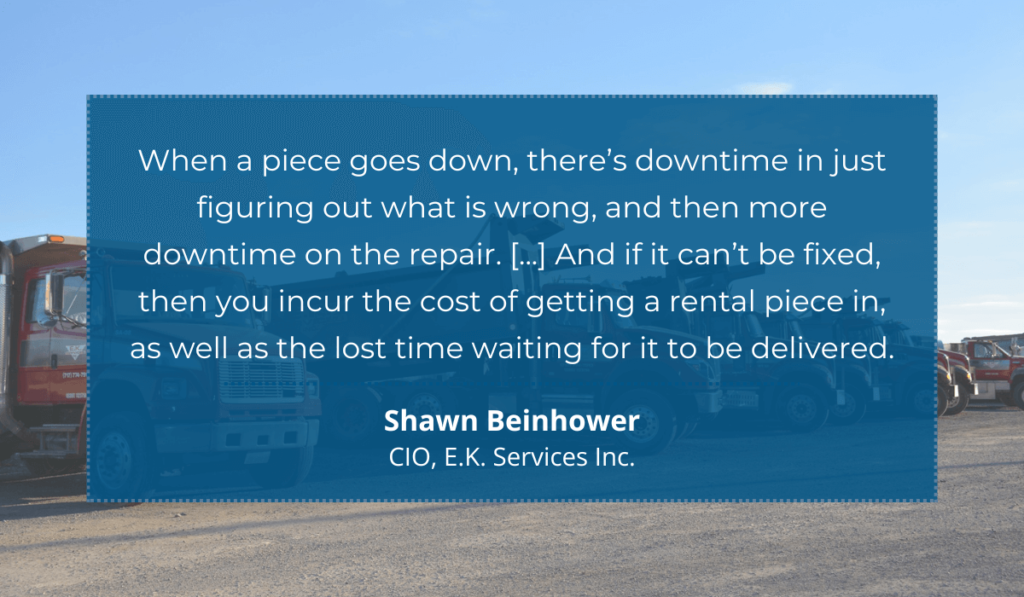
Truly, unexpected downtime eats up both time and money, impacting timelines and eroding your profit margins.
However, with equipment management software, you can have all your equipment maintenance data in one place.
From equipment manuals and maintenance instructions to previous maintenance history—you can have it all written down in one database, and you can even attach documents to each piece of equipment:
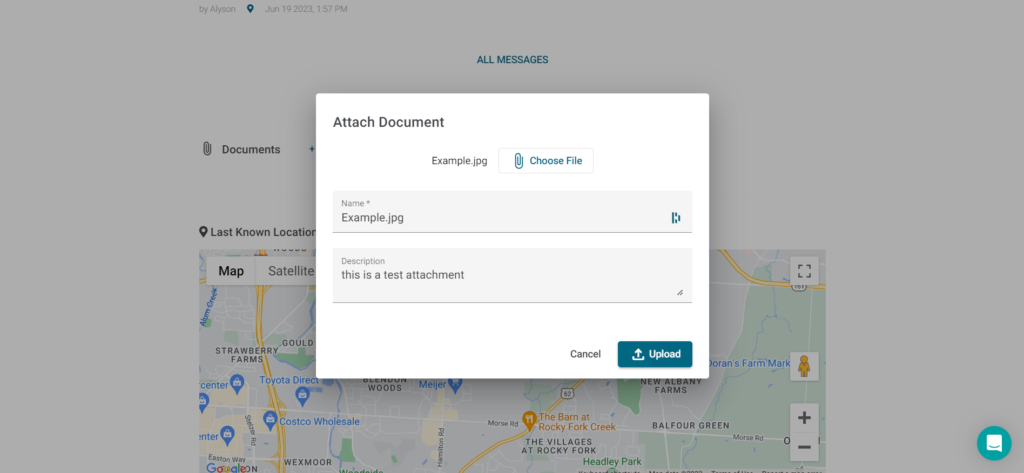
With that information, you can improve equipment maintenance scheduling.
In fact, with some equipment management software, you can even schedule maintenance directly from the system, and assign maintenance tasks to your staff.
This, then, helps you minimize unexpected equipment breakdowns and downtime.
Plus, you’re making sure your equipment is readily available and as healthy as it can be.
And there are additional perks to this.
According to ABB’s recent study on industrial businesses, equipment reliability has a positive impact on several fronts, including the company’s reputation and financial performance.
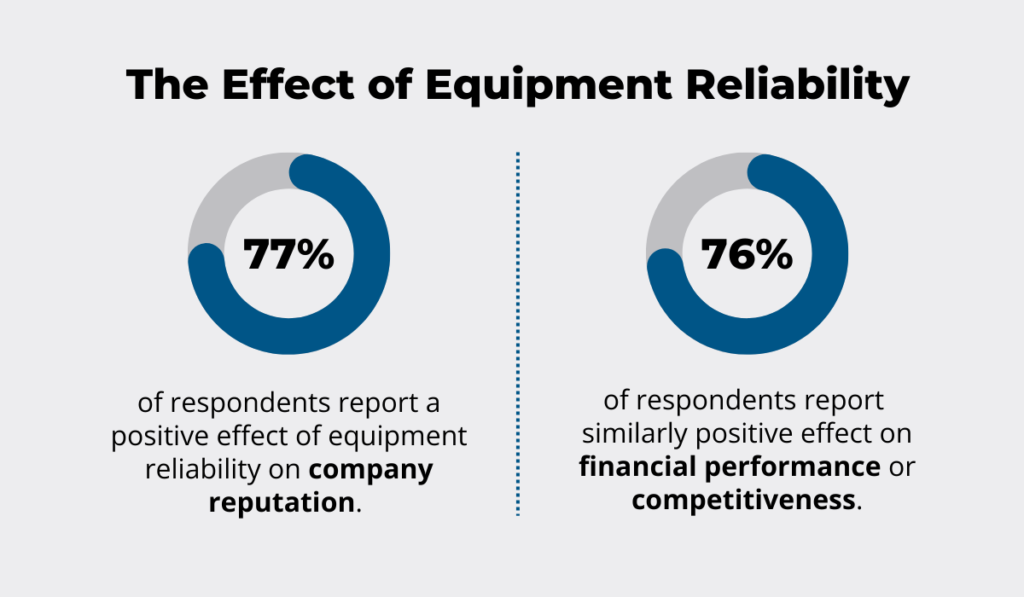
Given construction’s heavy reliance on equipment, it’s easy to picture similar benefits in this industry too.
All things said, equipment management software’s impact on reducing equipment downtime, and saving you both time and money, is undeniable.
Helps Control Equipment Loss
Key software features like real-time tracking and asset monitoring minimize equipment loss or theft.
Controlling equipment loss is essential for ensuring that essential tools and machinery are available when needed.
That way, you’re preventing potential delays, but also the financial impact of having to find replacement equipment on short notice.
It’s no secret that construction companies are very exposed to theft, and recent studies show that things are getting worse.
One interesting statistic from BauWatch reveals that 27% of on-site thefts are carried out by insiders.
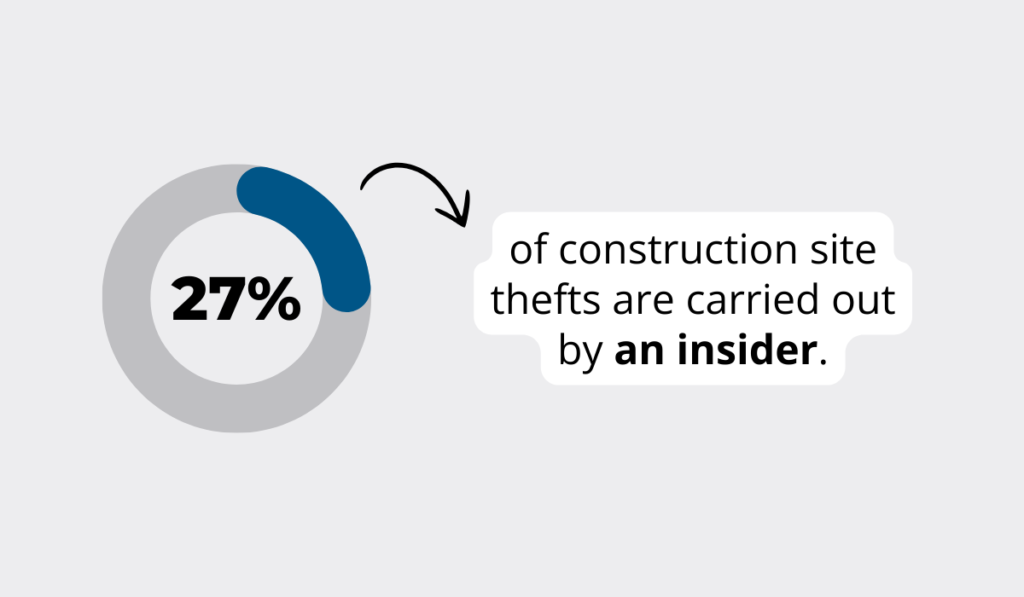
Small tools are the most frequent targets, but even this security risk can be handled effectively when you’re using the right software.
Good equipment management tools come with a variety of asset tagging options that increase employee accountability by:
- providing hard-to-remove proof of ownership, and
- increasing transparency through custody-chain tracking.
Even the simple knowledge that an item is being tracked acts as a theft deterrent.
However, brazen thieves may still attempt or even succeed in stealing your equipment.
Fortunately, according to an exhaustive study of over 15,000 construction crime incidents, half of all recoveries happen within 24 hours.
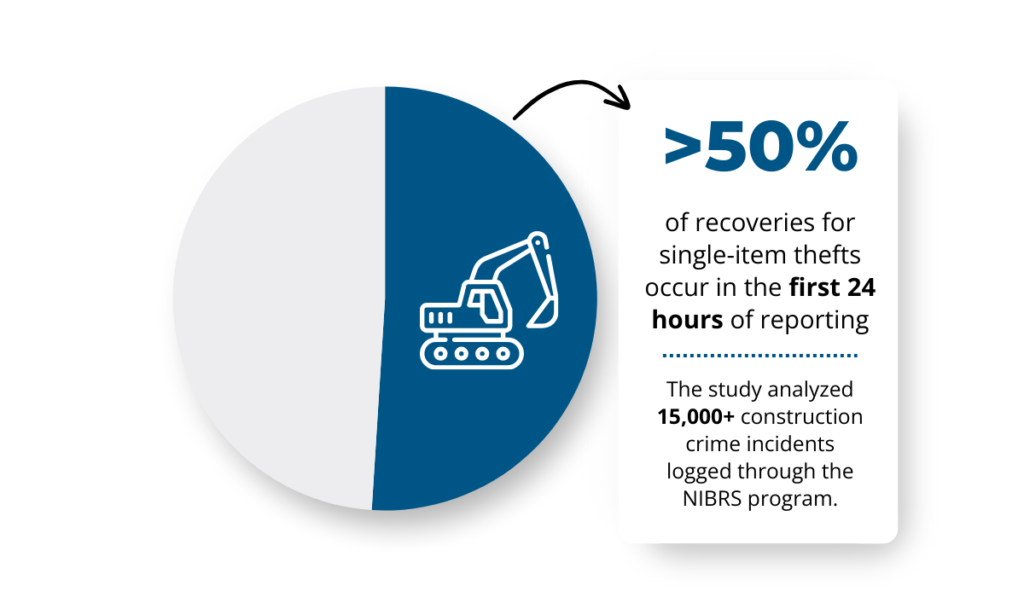
But—successful asset retrieval depends on your ability to detect and instantly react to any suspicious activity on site.
With GPS trackers embedded in your equipment management software, you can do that!
Namely, you can monitor equipment location in real-time, and be promptly alerted of any issues.
In the end, having this level of control over your machinery and tools is sure to curb equipment loss and resulting impact.
What to Look for in Equipment Management Software
Now that we’ve established what would be the benefits of adopting equipment management software, let’s zoom in on the key features you should look for.
Mobile Access
This is a must-have equipment management feature because it connects the field and the office, improving responsiveness and decision-making.
Mobile asset-tracking enables on-site workers to:
- update equipment status,
- report issues, and
- access data on the go.
In our GoCodes, managing equipment information is as simple as scanning a QR code label!
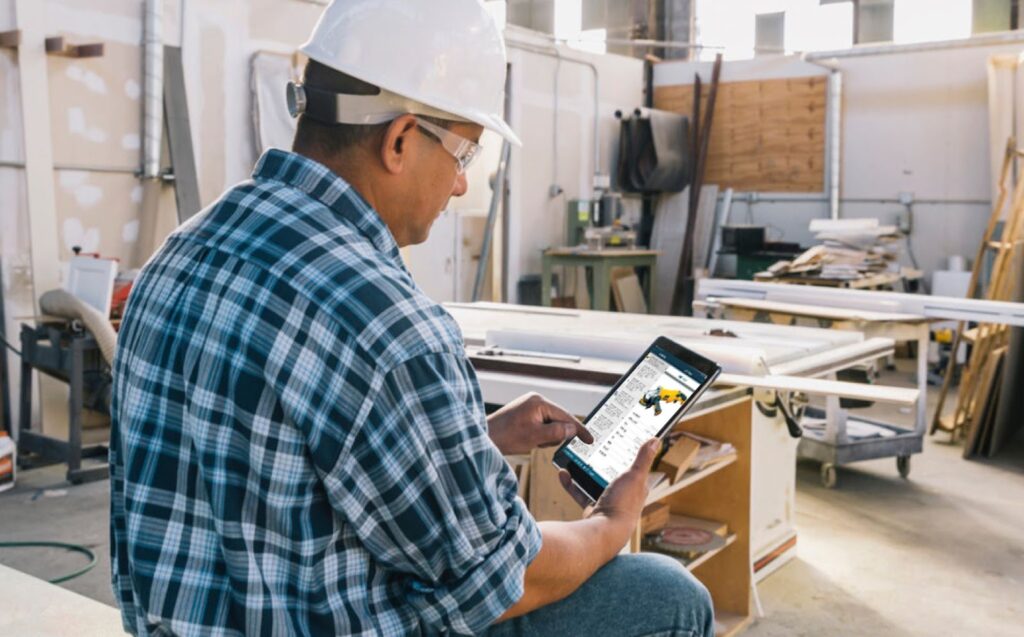
You can look up or update asset info using our app or any QR code scanner—all your data stays safely stored in the cloud and synced in real time.
Furthermore, using the GoCodes app brings the user experience to a whole new level, allowing you to access the telematics module, view asset locations on a map, and check out and update multiple asset information.

The GoCodes system is incredibly cost-effective and easy to use, especially since it requires no extra hardware.
As such, all training and work take place on devices that are already familiar to all employees, which is a huge advantage when introducing new technology.
Chris Malafa, the IT Director for a California-based constructor Griffith Company, reminds us why usability is so important in the construction industry:
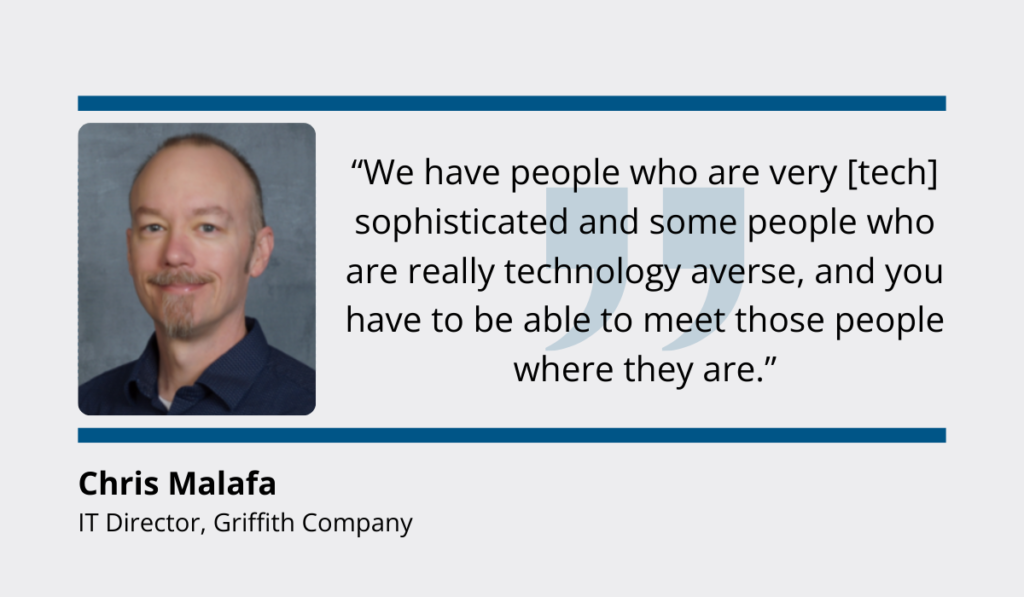
The bottom line is that mobile access enables everyone to stay in the loop while ensuring quick and cost-effective equipment management.
Real-Time Equipment Tracking
Real-time GPS tracking and telematics give you data on the location, usage, and operational status of equipment.
This is the key feature for preventing equipment loss, improving asset utilization, and helping you plan logistics more efficiently.
Real-time GPS trackers are at the very center of the GoCodes tracking system, and here’s what they deliver:
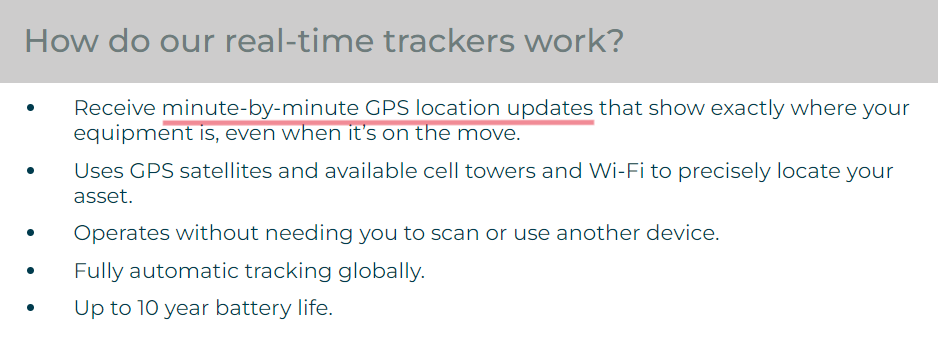
The technology is incredibly user-friendly and straightforward—you get real-time updates on the exact location and movement of your most valuable assets anywhere on the globe.
There’s only one thing you need to do first: mount one of our long-lasting, portable trackers on your key assets.
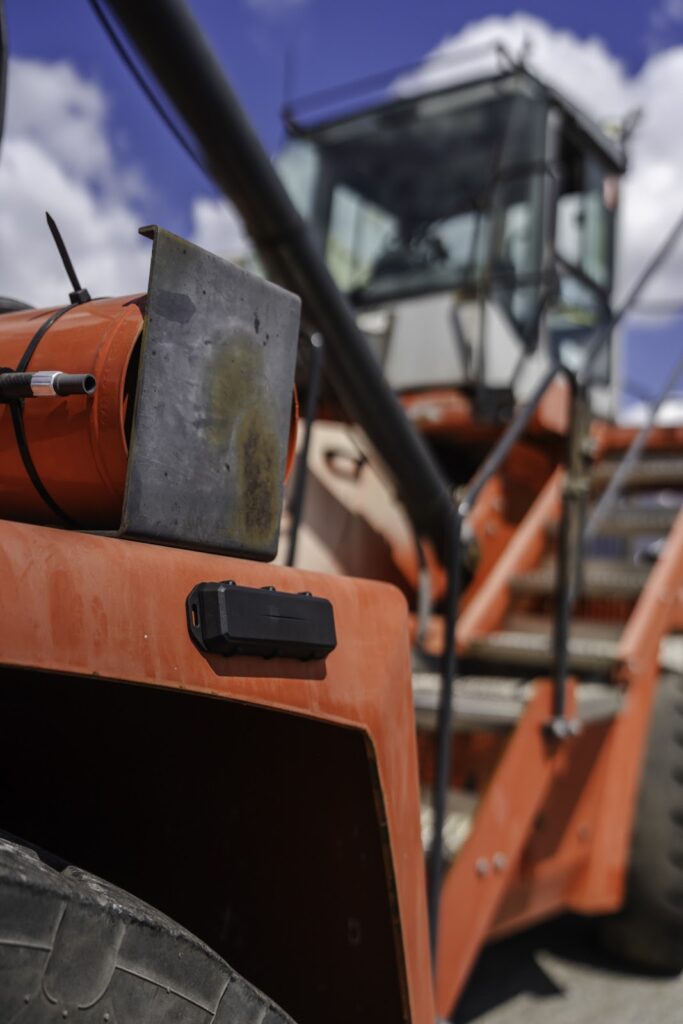
No matter the placement, the tracker enables insight into the asset’s current location and easy tracking on the map.
But that’s not the best part.
Even as your equipment moves across the jobsite or between different locations, you’re collecting precious data.
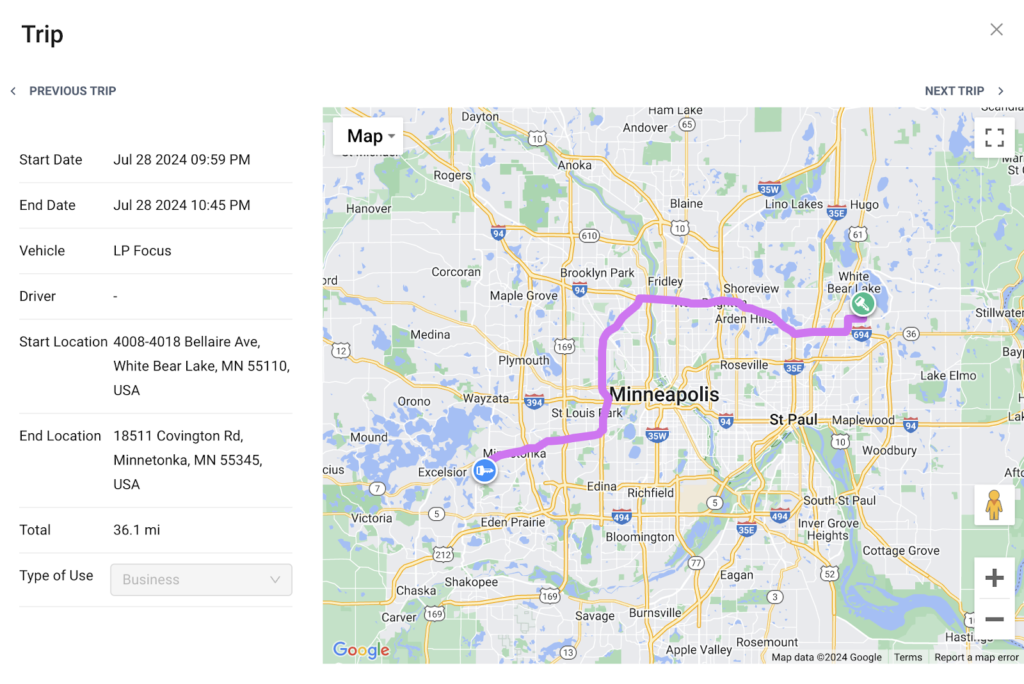
These updates can help you control mileage and fuel costs, while diagnostic trouble code alerts ensure you’re notified about specific issues and can react swiftly.
At the end of the day, you can pull up a daily vehicle inspection report (DVIR) to asses the asset’s overall health, look into potential problems in more detail, and adjust strategies where necessary.
To sum up, your equipment management software of choice needs to enable total visibility into each asset’s specific condition and circumstances, and that’s exactly what real-time tracking delivers.
Geofencing
Software with geofencing capabilities enables you to set up virtual boundaries around your construction site or yard.
This way, geofencing helps you counter theft, unauthorized usage, or other form of equipment misuse.
Geofencing has several applications in construction, but the main idea is that you can draw an invisible security perimeter around a specific area.
This enables you to keep a closer eye on your assets while collecting important data.
Here’s what that setup looks like with GoCodes:
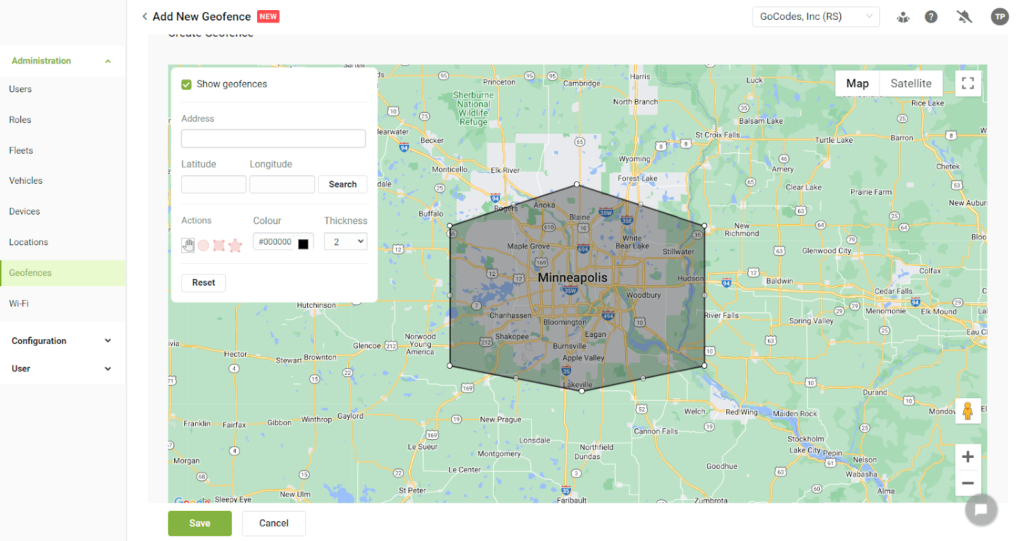
Once you’ve implemented geofencing, you can check when a machine started, when it got turned off, and whether there are any performance issues or unsafe driver behavior.
There are various types of geofencing, but the primary function remains the same: to receive geofence alerts whenever a set boundary is crossed.
Kirby-Smith Machinery’s Mark Tadlock, a Product Support Sales Representative, explains the significance of setting up real-time alerts:
”If that machine goes out of that area, we’ll set it up so I get alert, the service manager gets alert, and the customer will get alert [which is basically] saying: “Hey, that machine has gone outside that fence, you might want to check it out.”
If you get an alert during the daytime, it could mean that one of your drivers or operators made a mistake or someone intended to use the equipment without authorization.
However, the same alert in the middle of the night probably means attempted theft.
Since GoCodes uses geofence-enabled GPS trackers, rather than Bluetooth or RFID, you can continue tracking the stolen assets once they leave the geofence, which increases the chances of successful retrieval.
These and other geofence benefits make it worth investing in equipment management software with these capabilities.
Maintenance Scheduling and Alerts
Equipment maintenance tracking is a huge part of equipment management, which is why your software should come with robust scheduling features.
Proactive maintenance extends equipment lifespan and lowers repair costs, and it is done a lot more easier when you’re getting alerts for upcoming services, inspections, and repairs.
Here’s one example of what happens when regular maintenance is ignored.
Instead of CAN $50,000, a chemical plant in Canada ended up paying a total of CAN $300,000 due to the unexpected breakdown of its lime kiln, an essential production component.
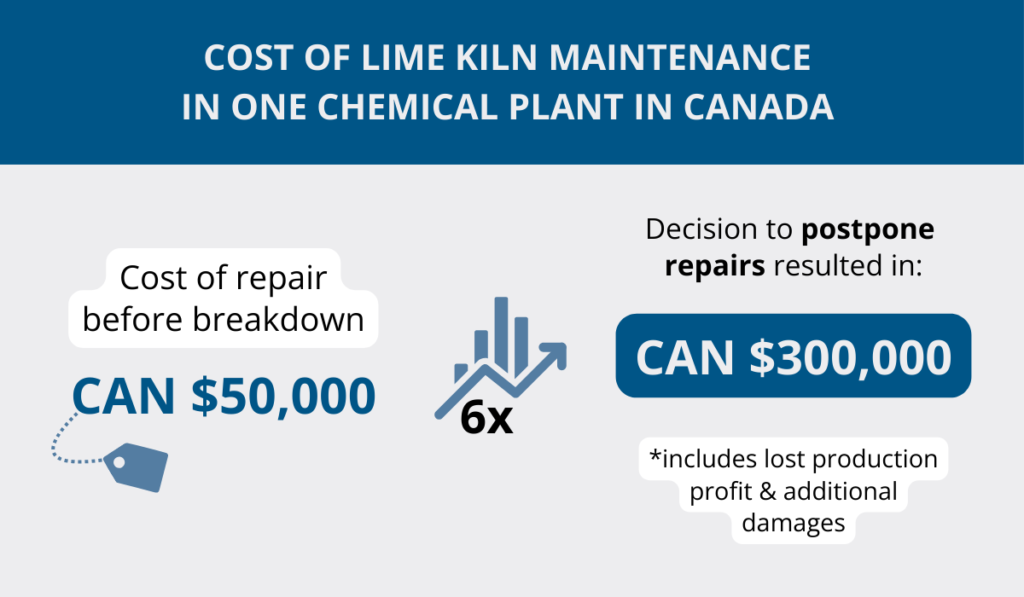
In this case, the management made a conscious decision to skip maintenance, which they ended up regretting.
However, these extra costs are just as likely if regular maintenance is simply forgotten.
And with everything happening on the construction site, you need reliable systems to keep track of equipment maintenance needs.
Luckily, equipment management software offers just that.
For example, the GoCodes database also functions as a central maintenance log.
In this way, the whole team can easily keep track of past and current maintenance needs, and report issues.
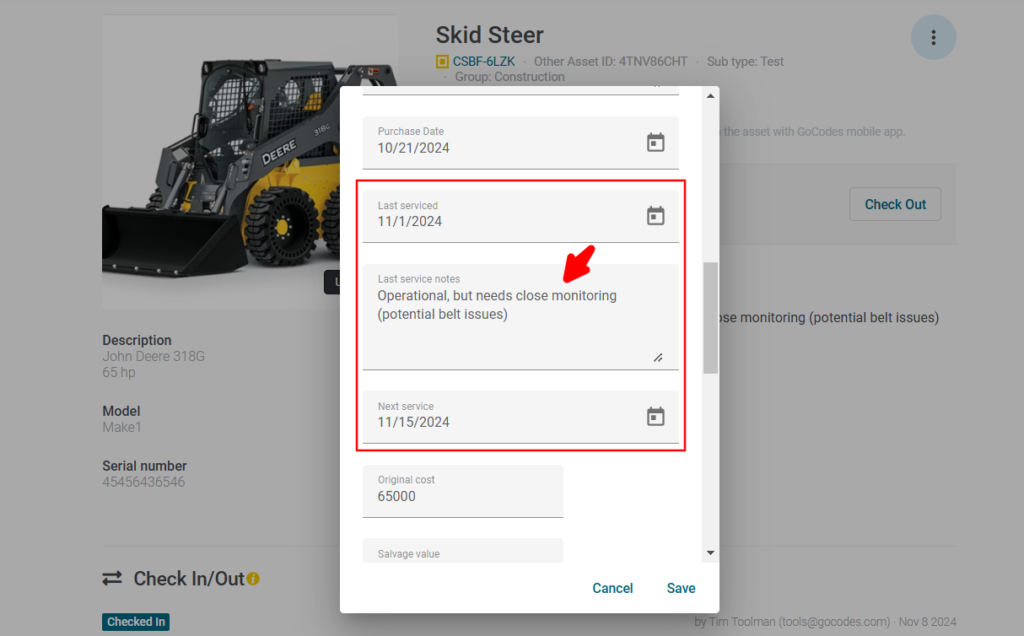
When it comes to scheduling future service tasks, the system enables you to set up notifications and be reminded of upcoming maintenance on time.
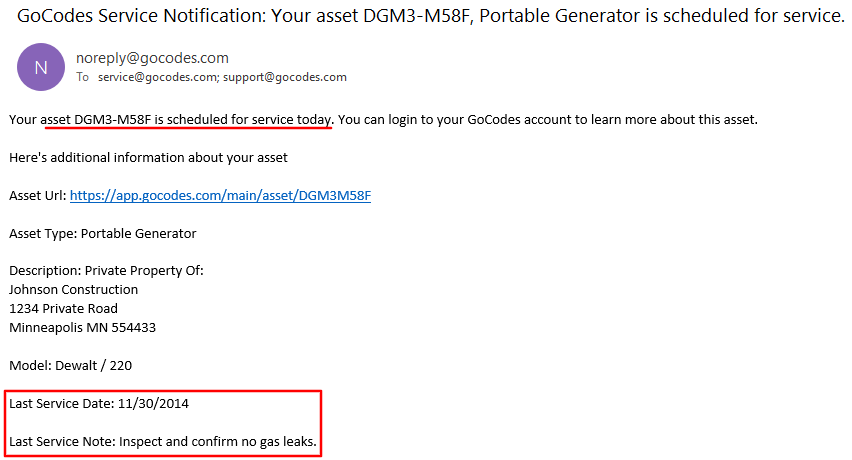
The email includes all the relevant asset information, alongside with last service notes.
With fewer emergency work orders to handle and less unplanned downtime, maintenance scheduling remains a core feature of equipment management software.
Customizable Reporting
Finally, no equipment management software is complete without robust reporting features that deliver insights into key performance metrics and equipment health.
The data you’re collecting is only valuable if you can organize it in the right way and make data-driven decisions.
Custom-tailored reports help construction companies zero in on exactly what they need, whether it’s a quick breakdown of asset performance or worrying usage trends.
So, here’s what you should be looking for in your solution:
- Flexible reporting options
- Custom report templates
- Exportable data formats
- Visual dashboards
GoCodes offers all that and more, from developing powerful custom data tables to creating custom reports in seconds by using our ‘drag and drop’ designer.
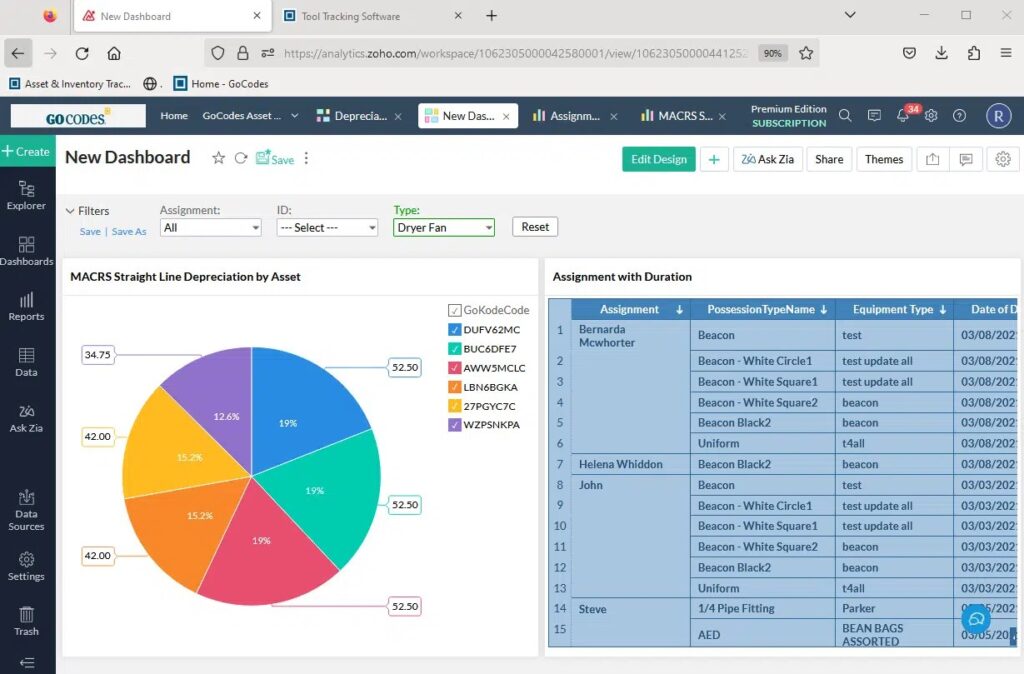
Once you get started with our enterprise reporting, you’ll see there are several valuable diagnostic reports you can use for tracking asset conditions.
For example, with the engine coolant report, you can quickly pinpoint which machines or vehicles exceeded a particular coolant temperature.
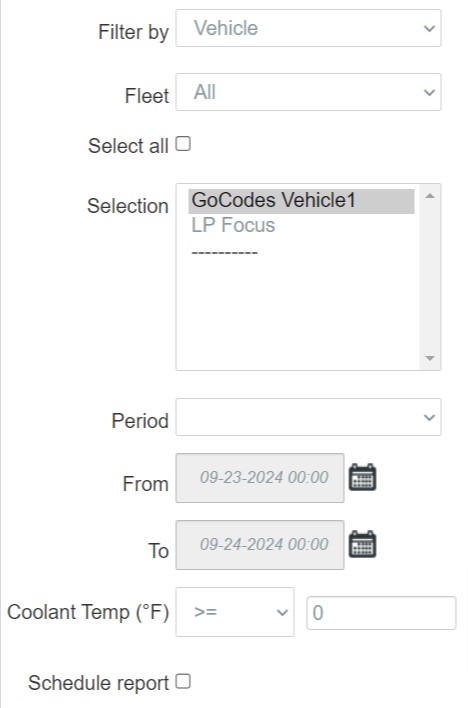
You also have telematics and geofencing custom reports that can help you map different trends related to safety, security, overall time utilization, and more.
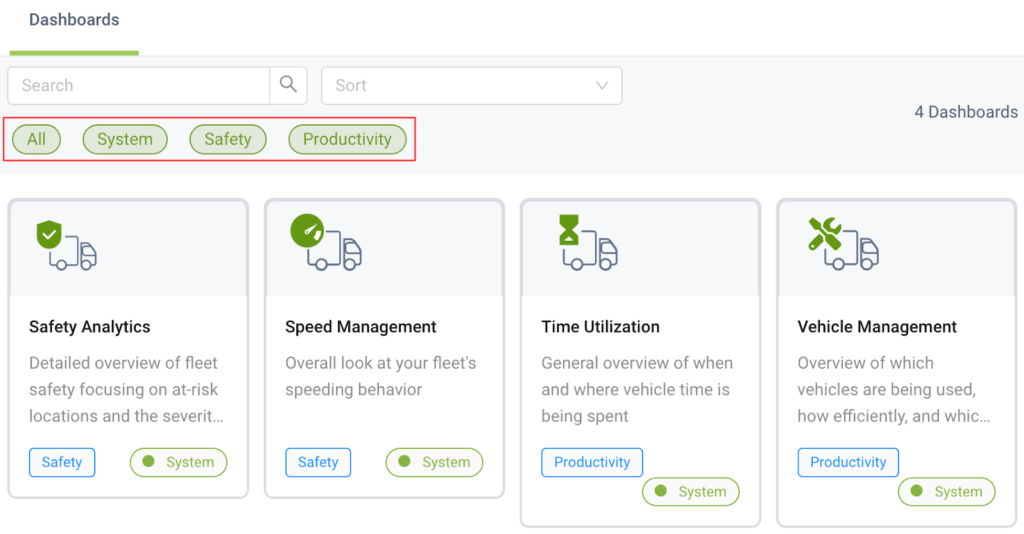
Each created report, chart, or dashboard can be shared in multiple formats like Excel, PDF, HTML & CSV.
Moreover, you can schedule them to be created and emailed to your team weekly, making it easier to involve all relevant parties in your equipment management processes.
Given the dynamic pace of the construction industry today, flexible reporting that can adapt to your emerging needs is a key feature of best-performing equipment management solutions.
Conclusion
Equipment management software ensures your equipment is always accounted for and in optimal condition.
So, if you want to streamline your operations, improve utilization, and reduce unnecessary expenses, using this software is a necessity.
Modern construction companies that are looking to stay competitive need to asses their specific needs and embrace the key software features we’ve discussed.
But regardless of the solution you choose, one thing is clear.
Investing in equipment management software sets you up for greater efficiency, a stronger bottom line, and long-term success.
So, what are you waiting for?
Take that leap!