Key Takeaways
- Design-related rework can be curbed by using BIM technology and developing a comprehensive review process before construction begins.
- Most project delays result from poor initial scheduling, but realistic, data-driven timelines and detailed contingency plans successfully mitigate this risk.
- Safety issues are unavoidable, but reducing their impact is possible through regular site and equipment audits, along with additional procedures outlined in safety programs.
- Technology is essential for preventing construction theft and unauthorized access, and leveraging comprehensive solutions delivers the best outcomes.
Seasoned construction professionals know that, no matter how smoothly the job seems to be going, they’re bound to encounter risks at some point.
Indeed, construction risks are a never-ending battle.
But the truth is, there are effective practices to anticipate and handle every obstacle that comes your way.
Today, we’ll explore ways to mitigate common construction risks and equip you with the knowledge that every construction company needs to succeed.
Ready to make your company safer from all lurking risks?
Then join us for a deep dive!
In this article...
Design Risks
Incorrect or incomplete design documentation often leads to rework, especially if the issues become clear only once the project is well underway.
Here’s how to mitigate them.
Conduct Design Reviews
Reviewing project designs thoroughly reduces the chances of having to make expensive changes down the road.
The design process, and preconstruction phase as a whole, involves multiple stakeholders, and all parts of the design rely on each other, meaning that one small mistake creates a ripple effect.
The error in design causes low-quality work, which calls for rework, and causes project delays.
And we already know that quality issues and rework are major causes of construction delays.
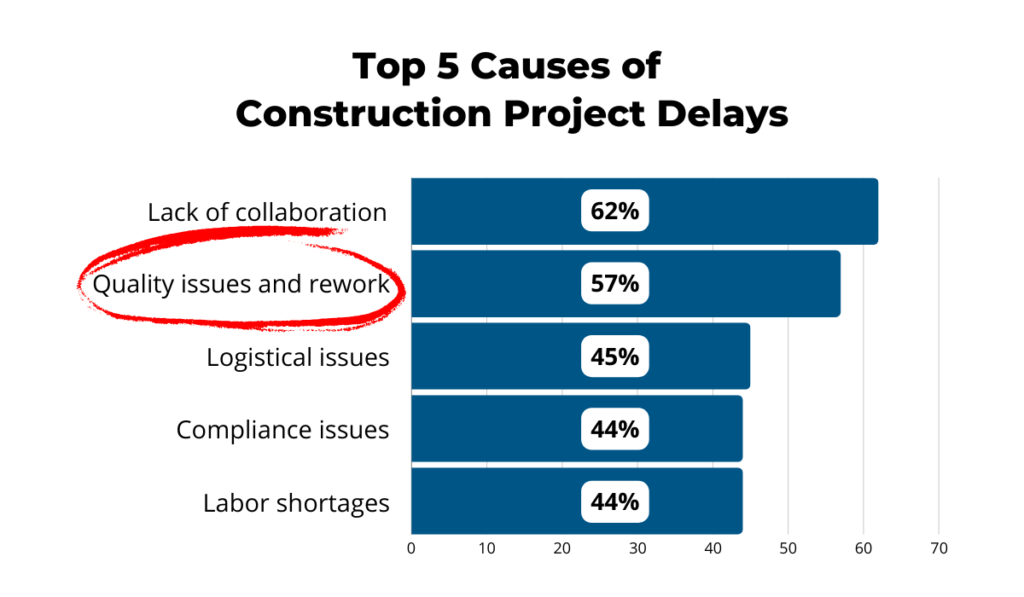
While root causes of rework vary, many issues go back to the design phase errors or miscommunication.
The solution? Introducing several design review stages.
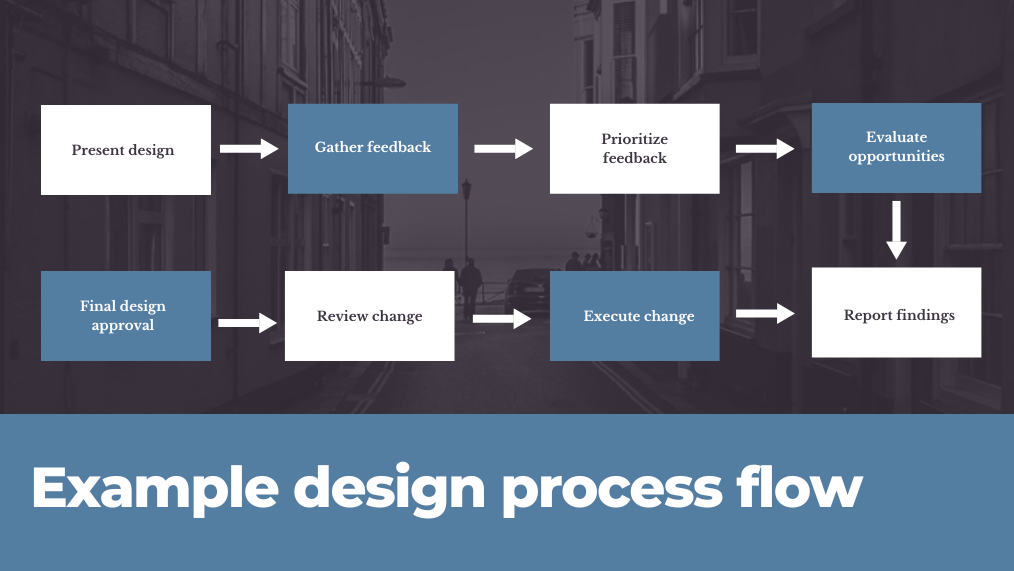
By making sure all relevant stakeholders are giving input throughout the project lifecycle, you’ll be able to catch errors before they become problems.
Your first step is to map critical milestones for conducting reviews and define the scope, methods, and tools to be used in the process.
Your choice of reviewers matters too.
They need to have expertise and experience, as well as sufficient time to conduct design reviews.
Furthermore, reviewers should make note of all things learned during the process so that changes can be implemented in the future.
Senior Projects & Development Manager, Rami Kaibni, advises companies to actively ask for feedback, and always aim for improvement down the line.
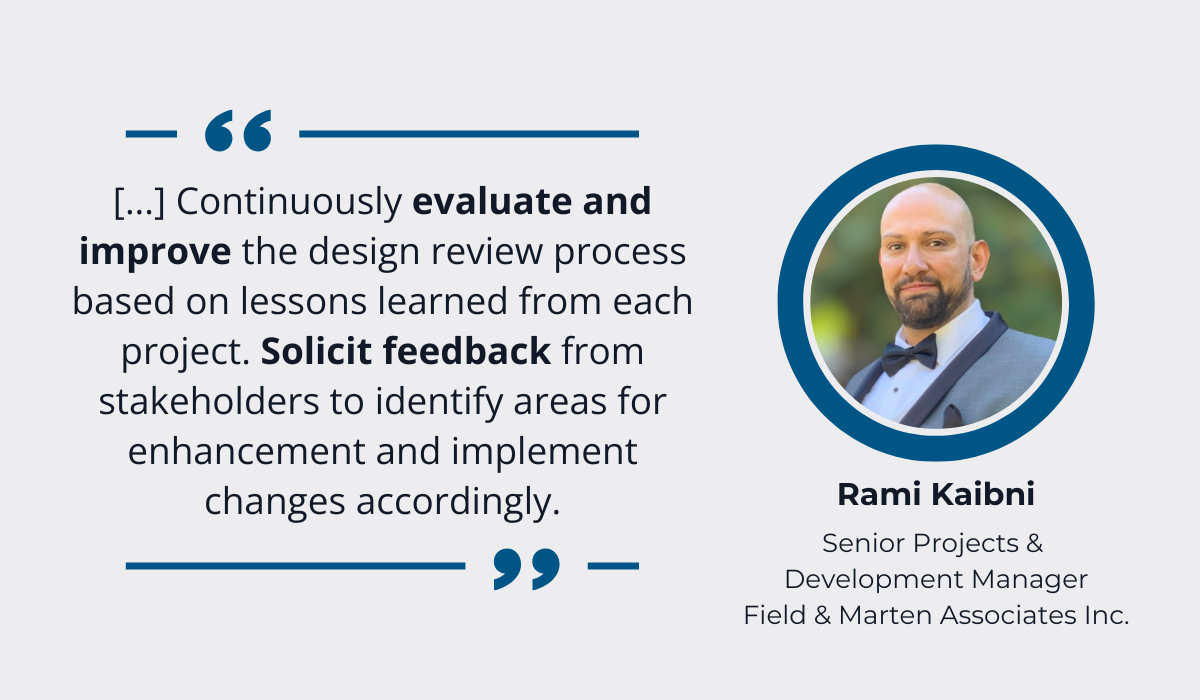
Even with multiple review stages and collected feedback, integrating the final design can be challenging.
The trick is to keep everyone in the loop at all times, but more on that in the next section.
Help Yourself with Technology
Want to collaborate effectively to minimize mistakes and enhance your design process? Help yourself with technology.
Nowadays, construction companies can rely on different collaboration tools, CAD software, augmented reality (AR), and virtual reality (VR), to ensure precision and bring designs to life.
Building information modeling or BIM software is a particularly significant and widespread form of virtual design, enabling users to visualize the structure in 3D and keep track of all edits.
Ultimately, this technology leads to:
- efficient design process,
- reduced risk of rework, and
- better final product.
As shown below, BIM tools help capture and show construction projects from all angles.
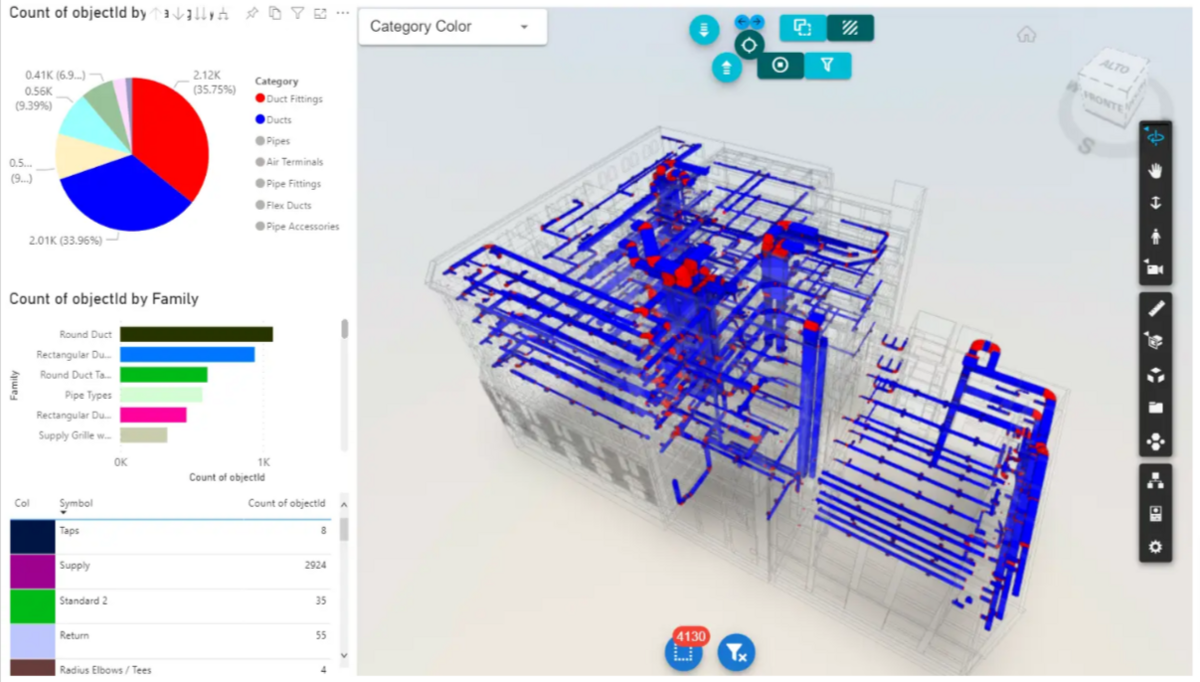
What’s more, VCAD’s solution integrates with Microsoft’s Power BI, which excels at turning complex data into actionable insights.
With that, users aren’t just able to visualize the project but get data from its design.
Which types of pipes will be used? How many?
Everything is automatically calculated.
Extracting and reinterpreting data like this supports agile project management, improves decision-making, and reduces risks.
BIM technology is widely used in construction, but its degree of accuracy and transparency is proving especially important for delicate projects, such as the preservation and digitization of Brazil’s Ipiranga Museum.
Autodesk combined Geographic Information System (GIS) and BIM to recreate the historical building’s interior and exterior, and produce digital replicas of the Ipiranga Museum’s invaluable collections.
What’s more, the precise BIM models enable the safeguarding of this unique world heritage while supporting the Museum’s further expansion and modernization.
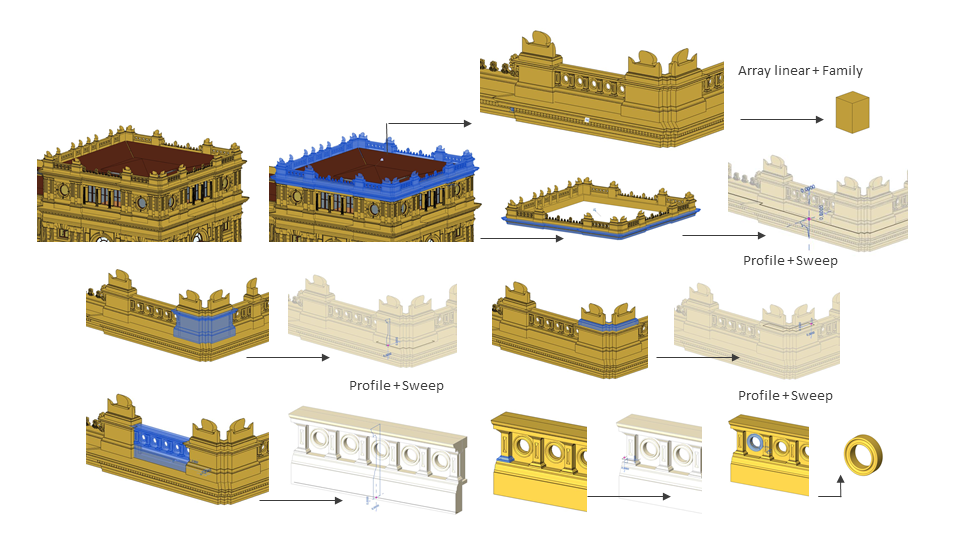
No matter the delicacy of the job, you don’t want to rely on manual, costly, and error-prone processes if you can use technology that captures reality at minimal risk.
Project Delay Risks
Late deliveries, shortages of key materials, equipment, and workforce, and weather-related interruptions can push back project completion.
But, there are some things you can do to prevent them.
Set Realistic Project Timelines
If your project timelines accurately capture the job ahead, you can enjoy relative peace of mind and not worry about delays.
However, the reality is usually quite the opposite.
A 2022 survey by UK-based firm Cornerstone Projects delved into the reasons behind construction delays, and their findings were telling: the biggest impact on construction delays was poorly planned project timelines.
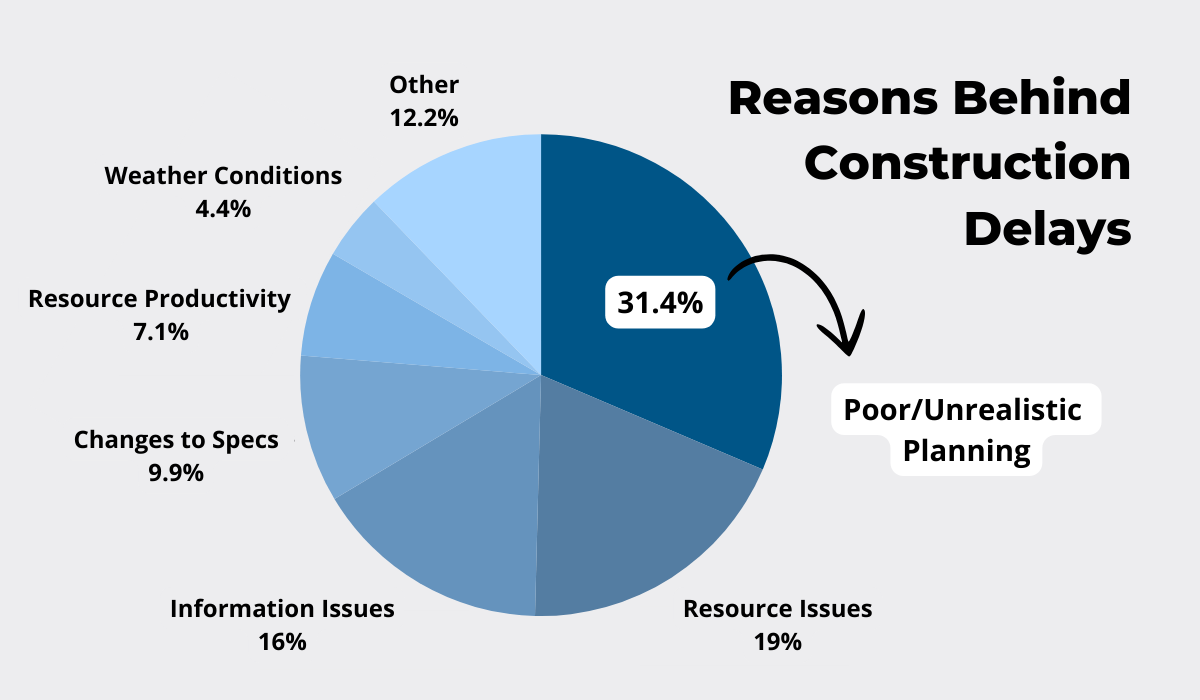
If you establish timelines that are difficult or near impossible to achieve, you’re sure to encounter bottlenecks and inefficiencies.
Moreover, if you try to speed up things and put pressure on workers to meet unrealistic deadlines, you’ll impact the quality of work.
You won’t be just multiplying errors, but the project costs and safety risks.
So, how do you set a realistic, achievable timeline?
Breaking down the project into phases helps you account for all the tasks and dependencies, make precise time estimates, and avoid common scheduling pitfalls.
In creating your project schedule, you need to pinpoint key deadlines and add a buffer period for each phase to account for different construction risks like:
- supply chain issues,
- contractor availability, and
- episodes of inclement weather.
And remember: data helps you make accurate predictions.
In the words of Procore’s first Global Technology Evangelist, Kristopher Lengieza, each construction project may be unique, but most risks remain universal.
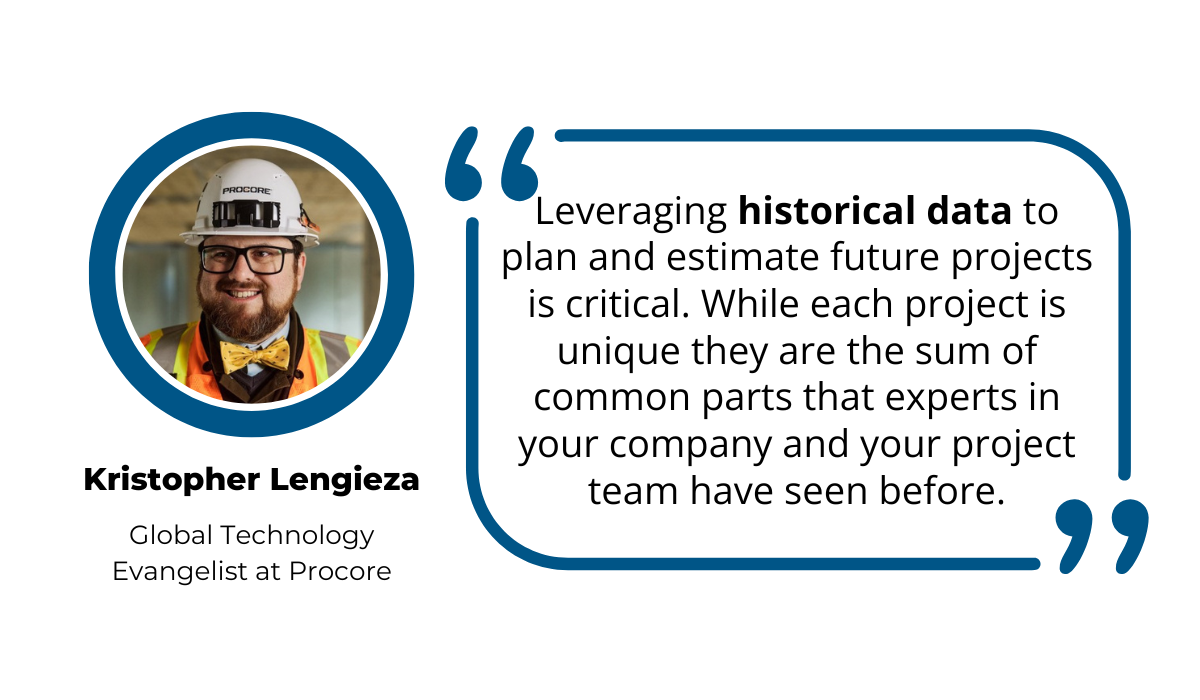
Therefore, by combining historical data with insights collected during ongoing projects, you can build more resilience and ensure you can adjust swiftly in case of schedule changes.
Have Contingency Plans In Place
Contingency plans are another safety measure.
They enable you to take common construction risks in stride and lessen the impact of unexpected disruptions.
Typically, defining a contingency plan results in several outputs, such as:
- Contingency funds
- Alternative sourcing strategies and inventory buffers,
- Defined communication protocols for crisis management, and
- Plans for delays, including critical path adjustments.
The main benefit of contingency plans is that they allow you to adapt to changing circumstances and successfully bounce back.
Although contingency plans address a broad range of issues, the initial steps are all about evaluating potential risks and pinpointing priority areas.
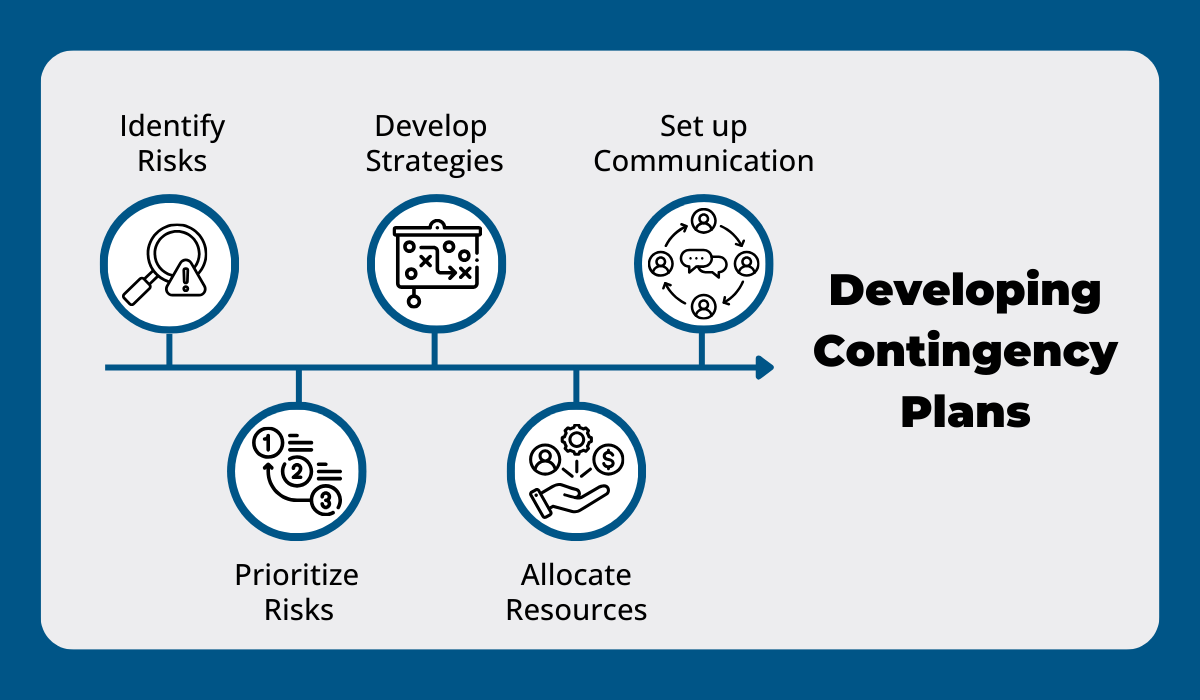
Priorities can be vastly different depending on the project in question, from natural disasters and labor shortages to equipment malfunctions.
Once you’ve outlined key risks, you’re ready to come up with the most effective action points and backup plans.
Still, you need to have enough resources to implement these strategies.
Contingency funds help you keep the costs in check and typically define a budget for different scenarios, such as construction project delays, finding replacement subcontractors, and such.
Finally, your contingency plan needs to have well-defined procedures for handling any unforeseen disruptions, and clear communication protocols to keep stakeholders up to speed.
If all these elements are in place, you can turn potential setbacks into competitive advantages.
Anthony Franco, a business strategist and the Founder of Launch Partners explains that contingency planning goes beyond ensuring safety in the moment.
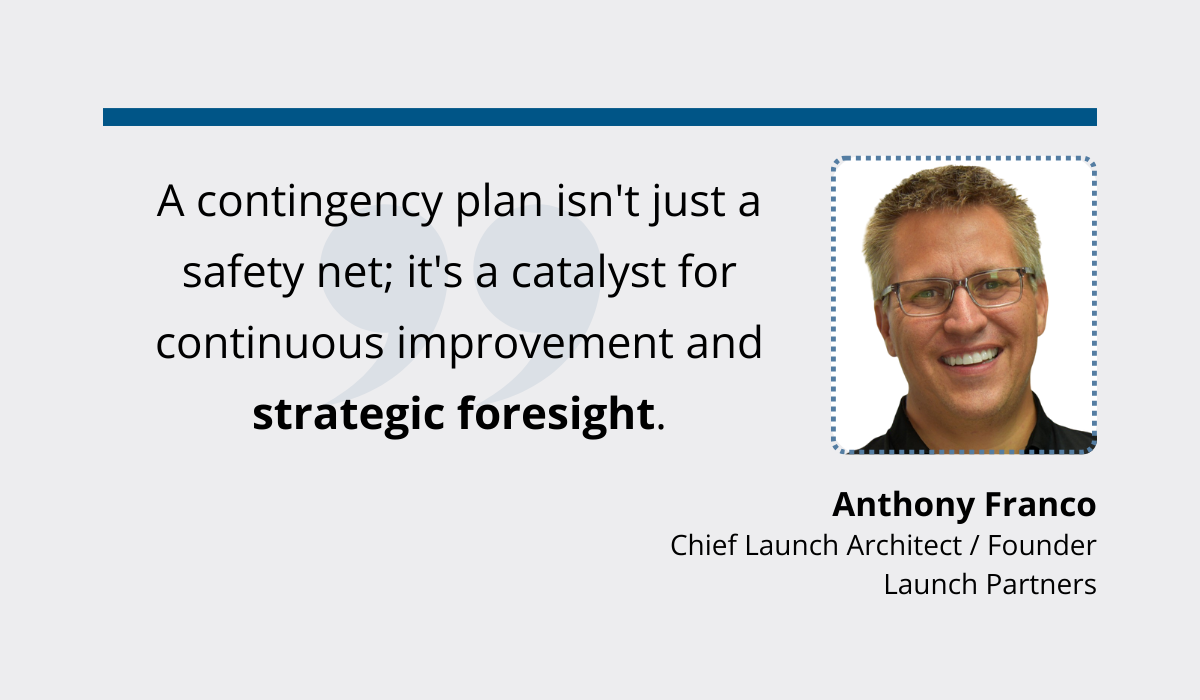
Coming up with risk mitigation strategies promotes overall adaptability and innovation within the construction firm, which in turn makes it easier to overcome both current and future obstacles.
Safety Risks
Construction sites are ripe with safety risks that can lead to injuries and deaths, followed by project shutdowns, investigations, and legal liabilities.
Not all accidents can be prevented, but there are a few best practices for mitigating these risks.
Implement a Comprehensive Safety Program
Having a safety program creates a powerful foundation for mitigating common safety-related risks.
Health and safety programs can incorporate a variety of practices, but their main aim is to ensure that workers are protected from injuries and accidents by:
- ensuring compliance with all laws and regulations,
- identifying hazards and implementing preventive measures, and
- providing relevant training and education on safety procedures, use of personal protective equipment (PPE), and more.
Every construction company is required to respect regulations and standards defined by bodies like the Occupational Safety and Health Administration (OSHA).
Failure to do so often leads to loss of human life, but also fines, investigations, and a negative reputation, which motivates companies to draft and implement detailed safety programs.
Moreover, according to recent safety management data, creating health and safety plans brings palpable benefits, especially if the planning involves multiple stakeholders.
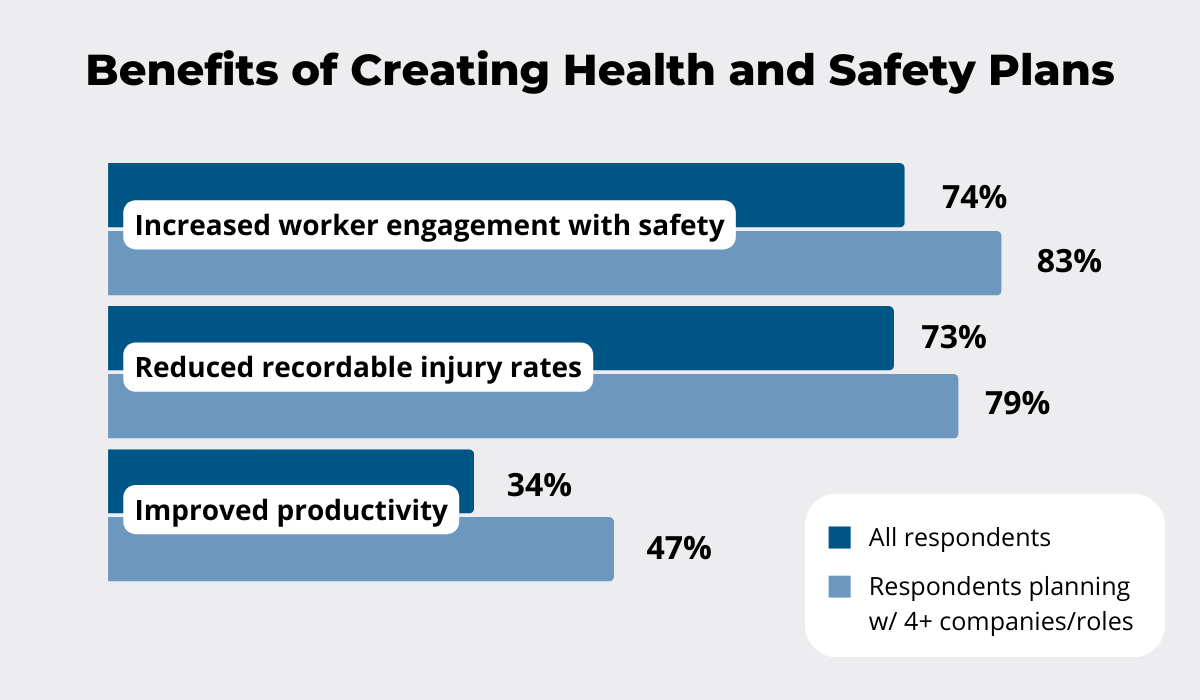
Although not presented in this research, investing in safety also helps you avoid indirect costs of safety accidents, which were estimated to multiply direct costs by at least 2.7.
A company can put in a lot of effort to create a safe environment that benefits workers’ well-being, but promoting and sustaining a safety-oriented culture depends on individuals.
Safety Tech at NexGen Contracting, Patricia Aquilar, explains that personal ownership starts with every worker being empowered to make safety-first decisions:
Everyone has a voice. Most importantly, we [can] reach out to our safety manager, and we have the Stop Work Authority as well.
Simply put, introducing sets of safety procedures has limited effect on mitigating risks compared to developing entire programs that empower workers to maintain a safety-first culture.
Perform Regular Equipment and Site Audits
Construction accidents happen even when employees are familiar with safety procedures and wear all the necessary gear.
It only takes one malfunctioning machine to wreak havoc.
Therefore, performing regular equipment checks and site audits helps you spot safety hazards and unsafe practices before they can endanger your workers and escalate into life-altering, costly incidents.
When it comes to equipment, conducting daily inspections prevents unexpected equipment failure and other common maintenance mistakes.
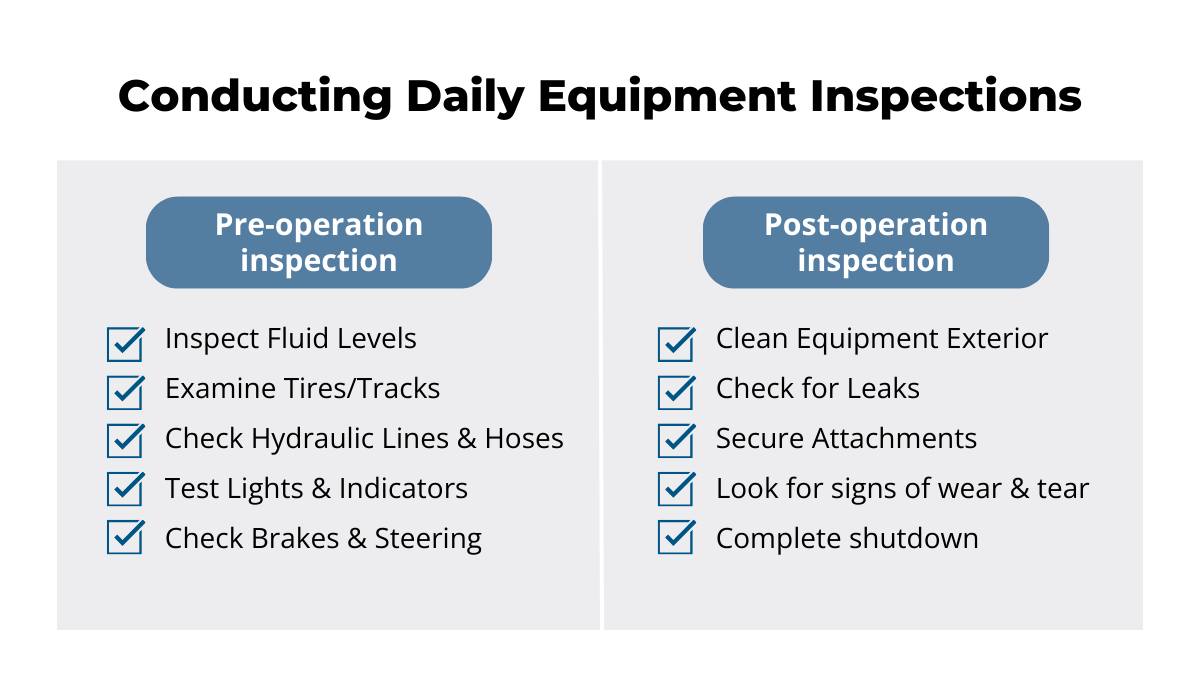
Even if the equipment isn’t used regularly, scheduling maintenance efforts is crucial for ensuring jobsite safety.
Failure to do so has its consequences.
UK-based law firm Leigh Day shared a recent case of a worker suffering an injury due to a defective piece of equipment.
Namely, a non-responsive pallet truck crushed the construction worker’s left foot against a wall—the injuries he sustained made it unlikely he’d return to work in this sector.
The worker’s lack of training contributed to the accident, but it soon became clear that the company hadn’t completed inspections and maintenance while the vehicle was on site.
The pallet truck was operational when it was initially rented out, but the misuse and lack of on-site maintenance caused its condition to deteriorate, ultimately leading to the accident.
Such cases of equipment failure are common, but construction accidents happen for a variety of reasons, often due to the site conditions themselves.
Conducting regular safety audits ensures everyone’s well-being by assessing risks like structural stability and weather conditions that could endanger life and halt the project.
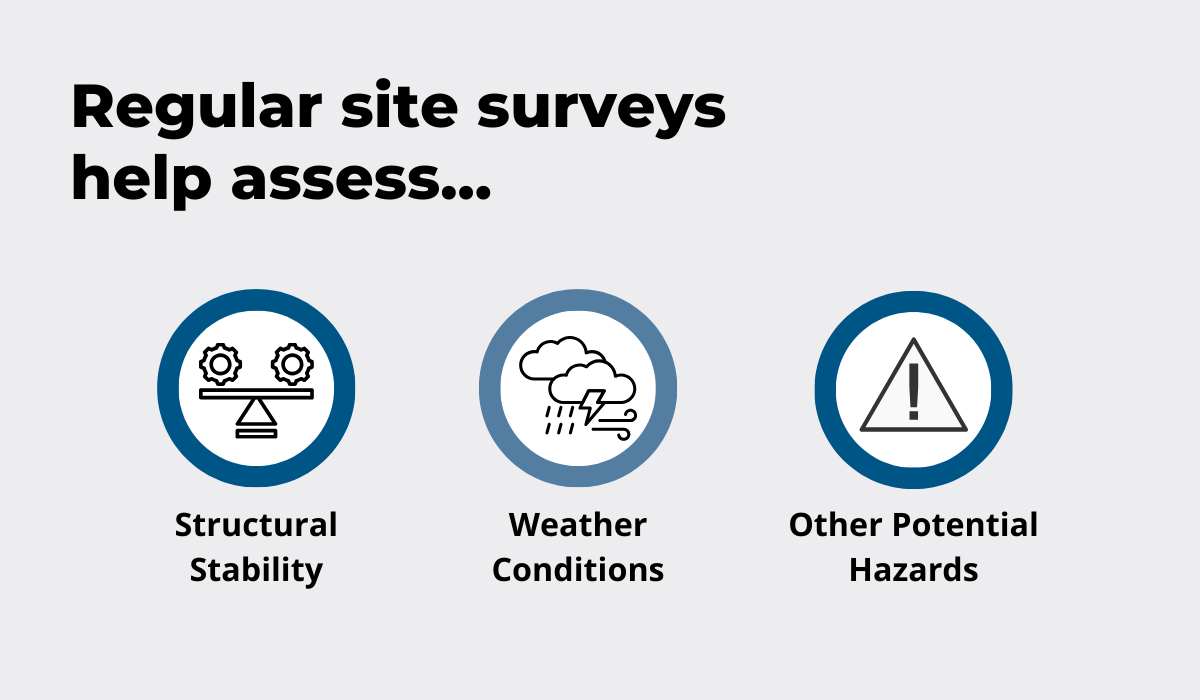
Risks related to terrain, weather, and other conditions, can be easily identified with aerial drone surveys.
Aerial inspections uncover hidden hazards and help map previously inaccessible areas, helping contractors save roughly $65,000 a year by improving accuracy and safety.
The drone technology is constantly evolving, as shown in the following video.
One thing’s certain: regular equipment inspections and site audits enhance safety while unlocking a wealth of other benefits.
Security Risks
Every construction company is also exposed to security risks. If unauthorized individuals can gain access to the construction site, you’re risking losing your equipment to theft and vandalism.
Here are two practices that can prevent that.
Track Your Assets
Keeping track of your assets at all times mitigates the risk of construction crime and loss of valuable assets.
There’s a reason why GPS-powered asset tracking emerged as the most implemented equipment technology in 2023 according to the IronPros report.
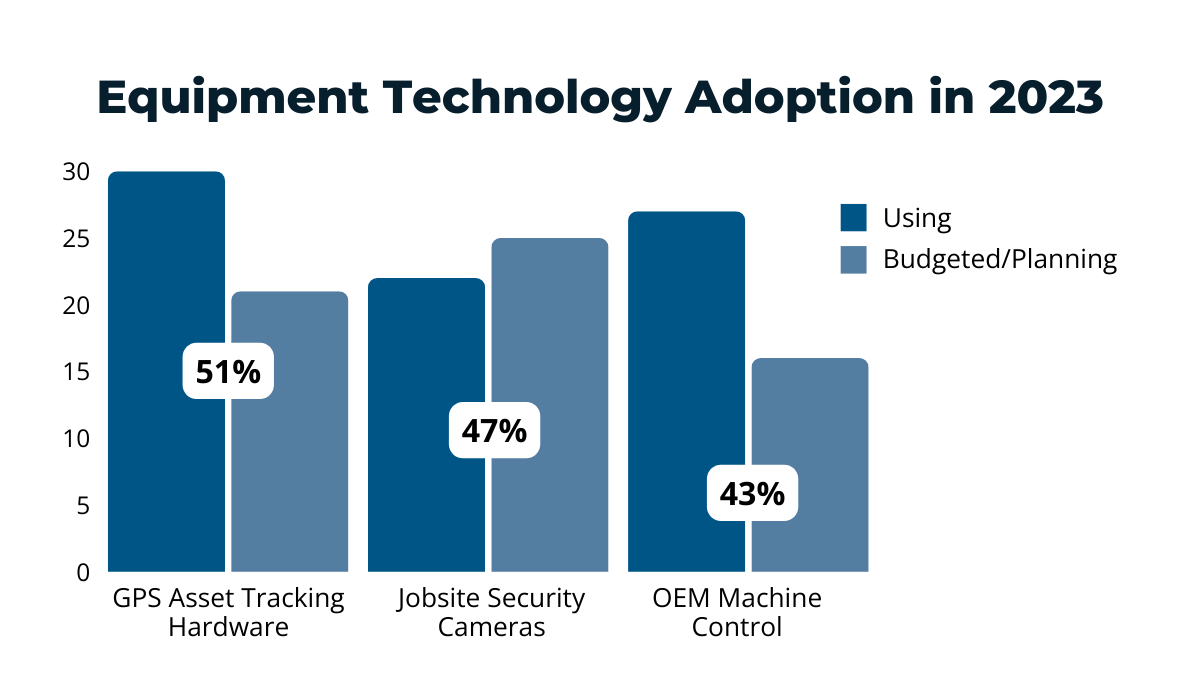
Technology like GPS tracking devices and QR code tags enables companies to monitor the location and status of their equipment, tools, and materials in real time.
Besides efficient resource management and improved accountability among the workforce, these solutions act as powerful theft deterrents.
Comprehensive asset management solutions combine different tracking devices with user-friendly cloud software to tell you when, where, and how your assets are being used.
One such solution is our GoCodes which helps you track and manage any type of asset, from large machinery to the smallest hand tools tagged with different GPS-enabled trackers.
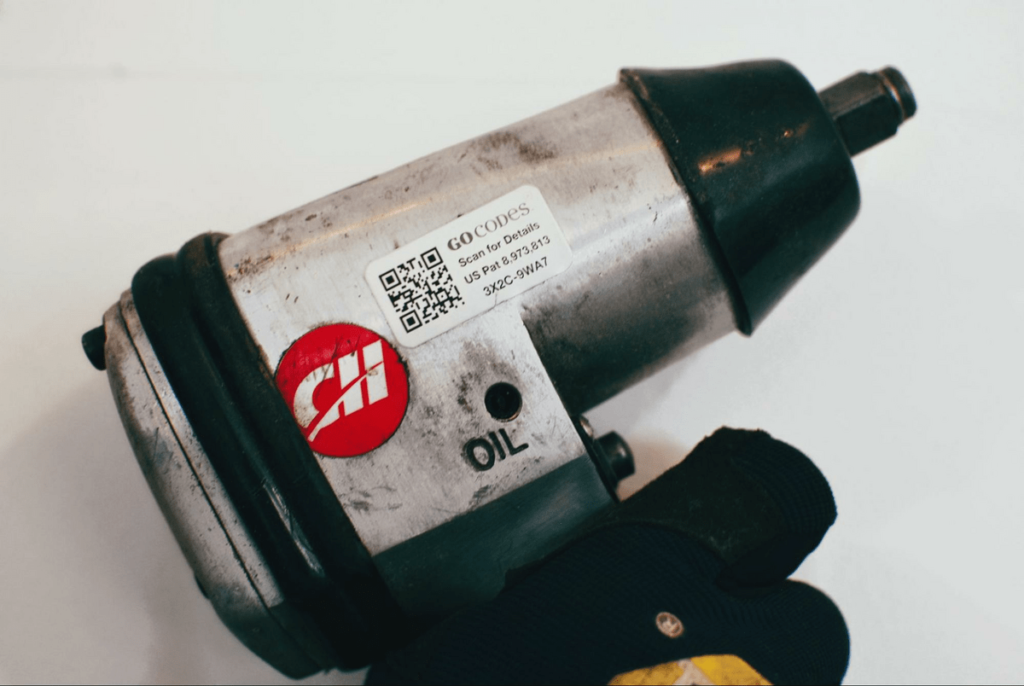
GoCodes QR-code tags protect even small tools which are the most common targets of theft.
Other real-time trackers mitigate risks concerning larger, more valuable assets by giving you minute-by-minute location updates, along with usage data.
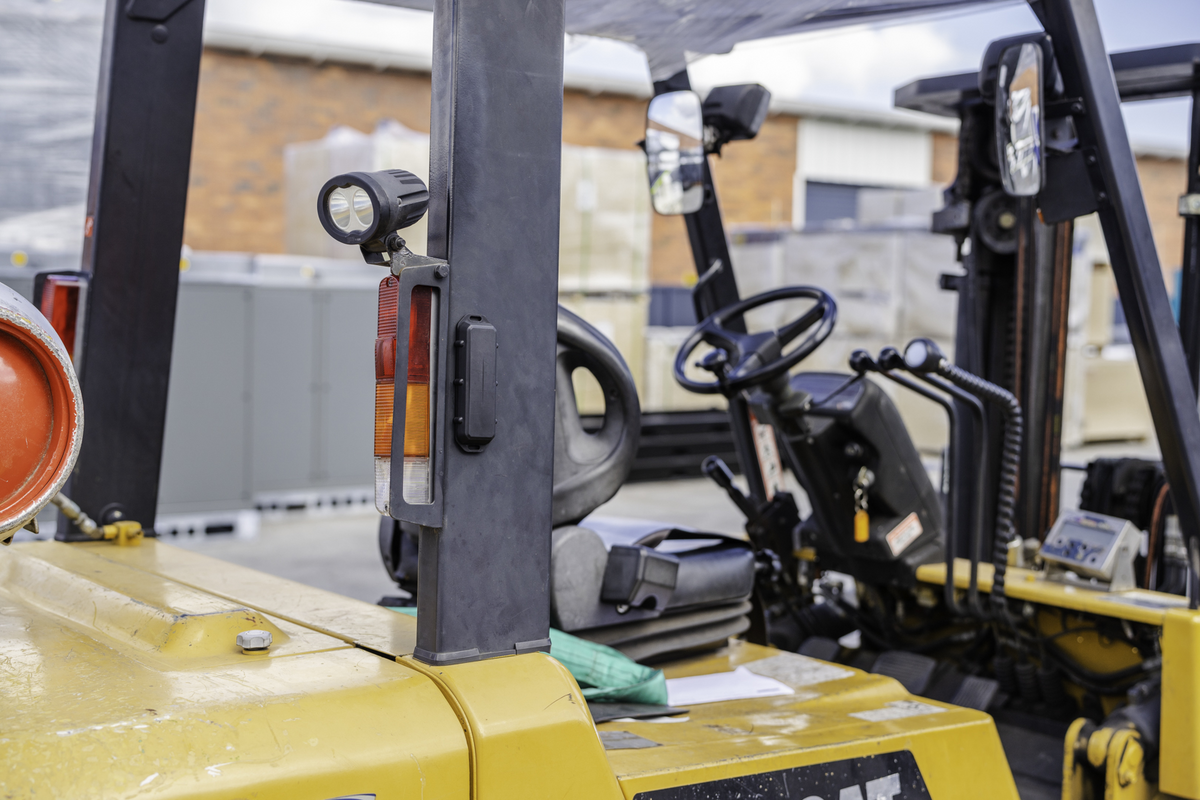
The GoCodes system is also equipped with geofencing capabilities, meaning that you can set up invisible perimeters around any area or asset and nip the theft issues in the bud.
The system will warn you of potential security breaches and unauthorized use.
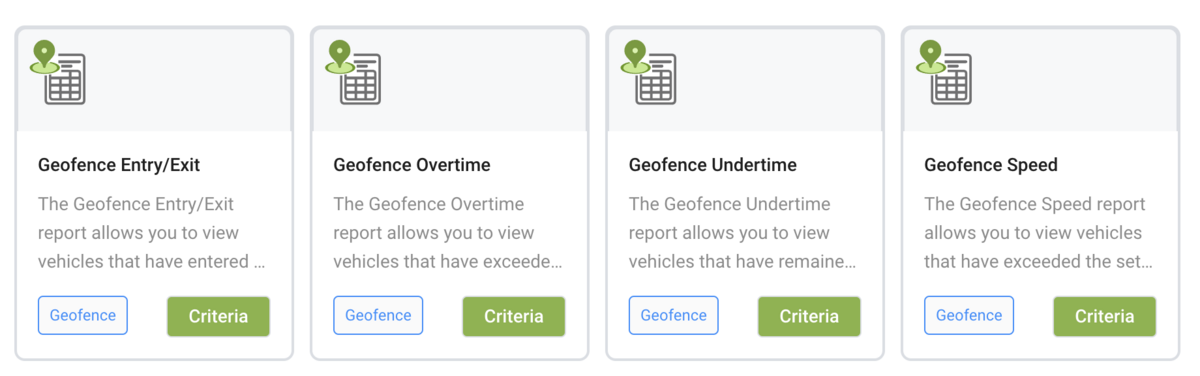
In conclusion, asset tracking is a powerful tool in your risk management arsenal, so be sure to utilize it to the fullest!
Invest In Construction Site Surveillance
Tracking individual assets is important, but it’s still wise to invest in site-wide surveillance.
Robust construction site surveillance helps you monitor on-site activities around the clock and deter all unauthorized access.
Wondering how effective CCTV systems are?
In CIOB’s 2021 report, 63.9% of respondents rated installing security cameras as an “effective” or “very effective” construction crime deterrent.
Moreover, even if a crime occurs, surveillance footage can be used to investigate different security incidents and provide evidence in cases where legal action is necessary.
Your first step for introducing CCTV is to assess your current needs and primary risk areas, including:
- Entry points
- Equipment storage
- Material drop zones
Once you know where you need surveillance, consider cameras with motion sensors or thermal imaging, and speakers that enable security personnel to issue warnings to intruders.
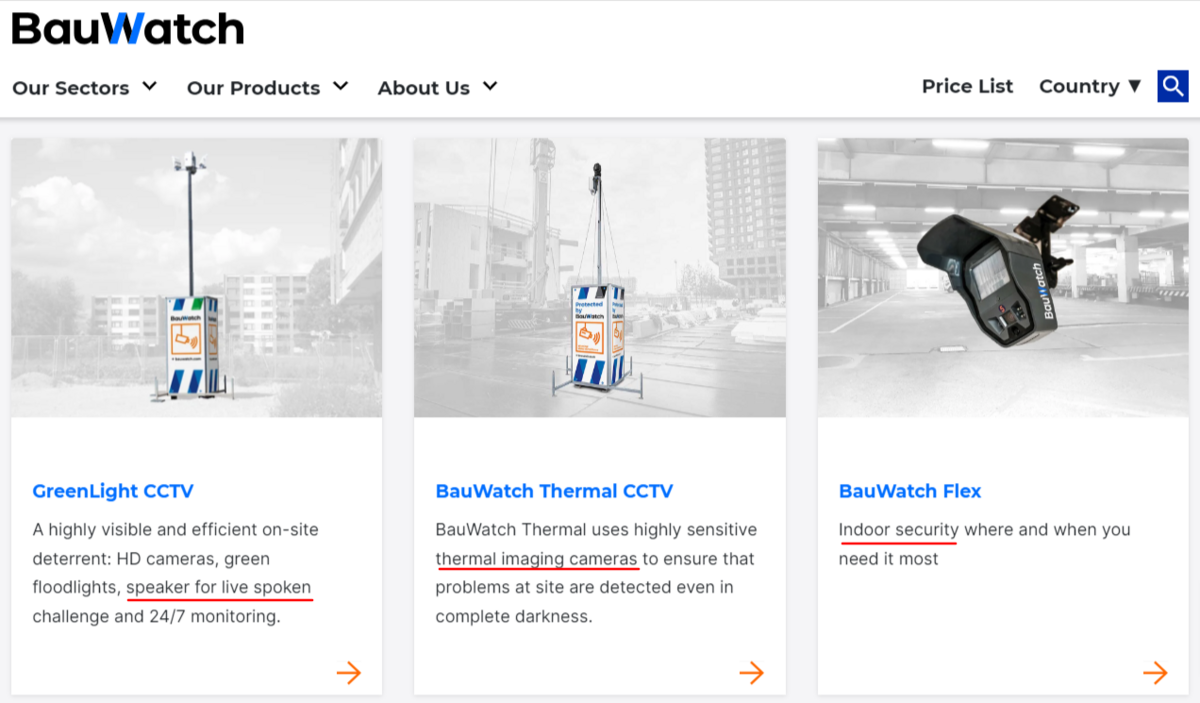
To make the best possible decision, re-evaluate past incidents to uncover the potential ROI of larger investments.
The advent of AI made surveillance systems more intelligent. Now, cameras can spot health and safety issues on site and bolster operational efficiency, alongside maintaining security.
Chandler McCormack, CEO of OxBlue, a company specializing in construction camera systems, spoke about new advancements that have enabled CCTV systems to collect a bulk of data.
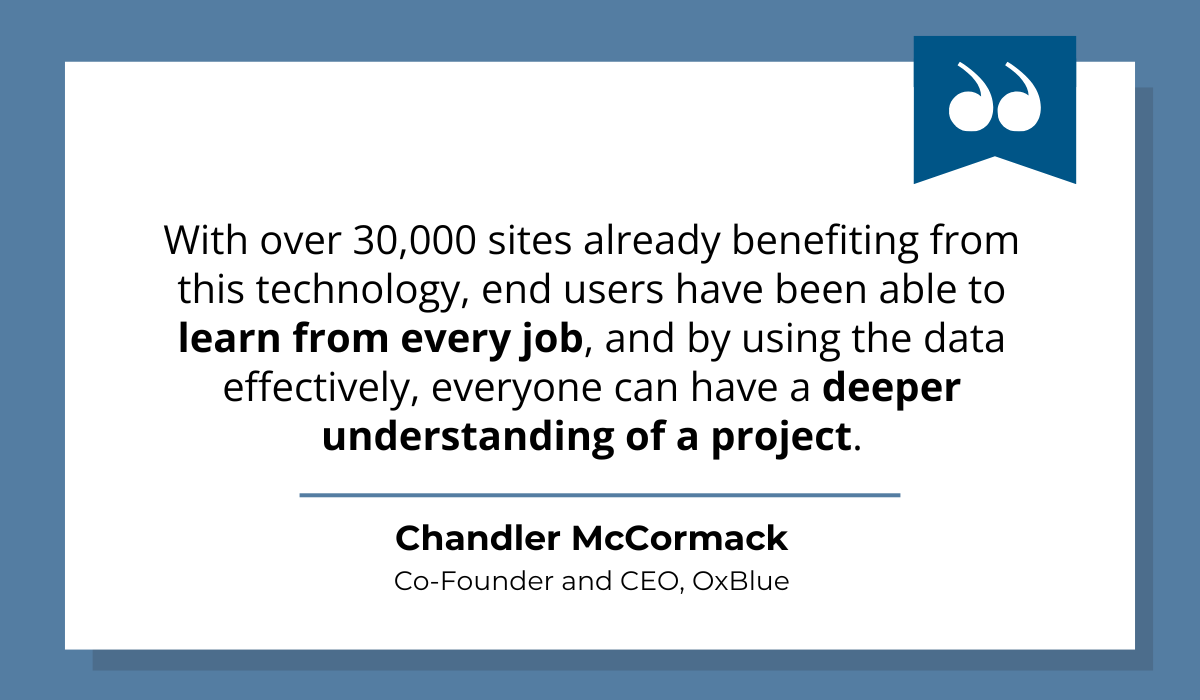
Creating a well-integrated and comprehensive system to prevent intrusions and theft is often a bigger, more immediate priority compared to collecting deeper project insights.
However, as risk mitigation is an ongoing effort, it remains an important strategic point to consider down the line.
Conclusion
The first step toward effective risk mitigation is to acknowledge the existence of construction risks and continuously seek effective ways to manage them.
Whether they relate to rework, delays, safety, or security, these risks can and should be addressed proactively.
The best practices we’ve shared with you are rooted in thorough planning and smart use of technology.
Take the time to integrate them into your work, and we guarantee you’ll start seeing amazing results.