To do their job and deliver construction projects on time and within the planned budget, contractors typically use a lot of equipment and tools.
Naturally, all construction equipment, from big cranes and excavators to small power tools and measuring instruments, will necessarily experience wear and tear over time, eventually reaching the end of its life cycle.
However, the duration of that life cycle depends on many different factors.
Therefore, construction company owners or managers who want to improve the durability and reliability of their equipment need to understand how those factors affect their equipment’s life cycle.
So, this article will share four essential tips on how companies should approach equipment life cycle management to maximize the lifespan of their equipment and avoid unnecessary costs.
In this article...
Start by Creating a Plan
To enhance your practices and ensure improvements across your equipment life cycle, you should start by creating an equipment management plan.
And to do that, you should reflect on what you did well and what you did wrong with your equipment in the past, evaluate your present resources, and consider your future equipment-related needs.
Doing so will enable you to establish a plan geared towards prolonging the equipment’s lifespan.
In fact, planning is the first stage of a typical equipment life cycle, which is shown here.
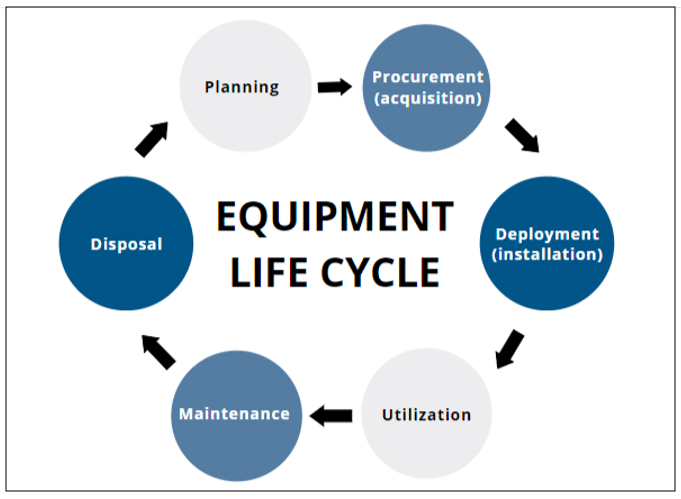
As you can see, good planning lies at the root of all other life cycle stages, from purchasing the right equipment to considering disposal options.
Therefore, you should analyze your equipment’s past usage, reliability, maintenance needs, and lifespan, which can provide some valuable insights.
For example, in the case of power tools, it can show that one model generally lasts longer than other ones, which you can then use to inform your future purchasing decisions.
Likewise, this reflection on previous usage can reveal inadequate maintenance practices that shorten the equipment’s useful life, such as not regularly cleaning and lubricating equipment.
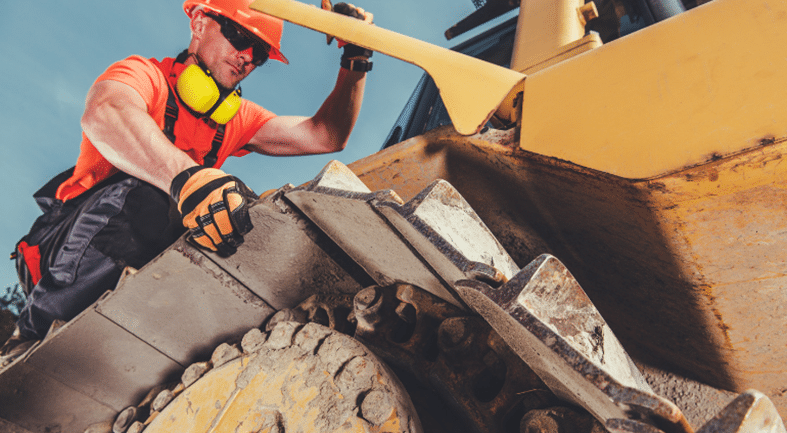
Naturally, these shortcomings can then be addressed, thus improving future maintenance practices.
As for evaluating the company’s present resources, this involves compiling or updating the inventory of tools and equipment your company already owns, along with info like:
- date of manufacture
- utilization data
- maintenance and repair history
After auditing the equipment your company currently has, you may realize that some of your assets are overworked—which shortens their lifespan—and you can adjust their maintenance schedules or plan their replacement.
Finally, you should consider your future equipment needs, i.e., determine which equipment is near the end of its useful life and should be replaced, as well as what new equipment, such as drones for surveying and jobsite inspections, you need to get to stay competitive.
When the past practices, present resources, and future needs are reviewed and insights combined together, this will enable companies to create a comprehensive equipment management plan optimized to extend the life cycle of their equipment.
Perform a Life Cycle Cost Analysis
The next step when your construction company is determining how to improve the equipment life cycle is to perform a life cycle cost analysis (LCCA).
Simply put, LCCA aims to determine the total cost of equipment throughout its lifecycle, starting from the price a company pays for a piece of equipment, followed by how much its operation, maintenance, repairs, and disposal will cost.
Here are the main components of LCCA, courtesy of the Corporate Finance Institute (CFI):
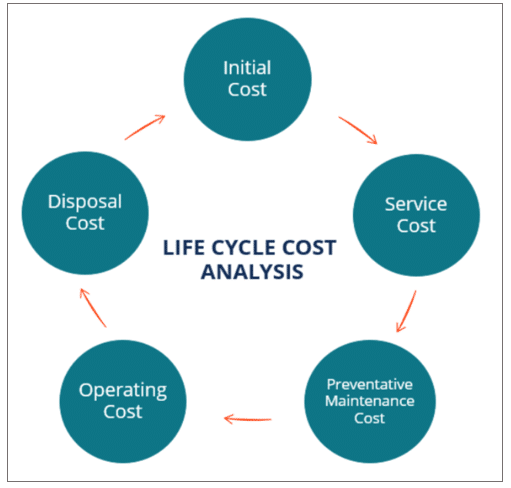
As you can see, the analysis considers the initial cost, which can, other than the price of equipment, include taxes, transport costs, and even operator training and licensing costs (if required).
As for service costs, they generally refer to unplanned expenses associated with repairs and maintenance in case of equipment failure, so they can be harder to estimate.
However, you can use historical data on similar equipment or work with the equipment dealer/manufacturer to better assess potential service costs associated with a specific piece of equipment.
Preventive maintenance costs, on the other hand, are easier to estimate.
They include activities such as oil changes, filter replacements, and regular inspections, which can help reduce unexpected service costs, as cited by the MacAllister Company.
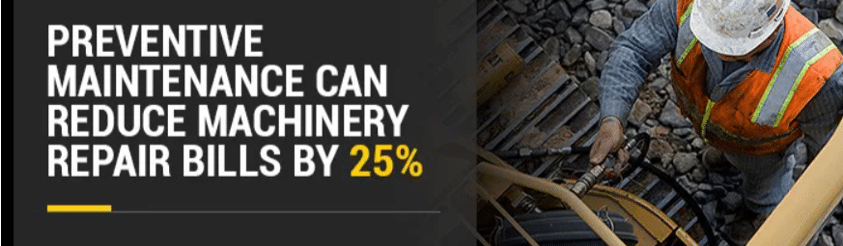
Operating costs, which typically include fuel, lubricants, tires, and other consumables spent when using equipment on a day-to-day basis, are also easier to determine.
Finally, the disposal cost can be harder to predict as it depends on factors like the type and condition of end-of-life equipment, the disposal method, and government regulations.
After these costs are estimated and aggregated, you will be able to compare the total estimated life cycle costs for different equipment.
For example, when you’re deciding between two models of backhoe loaders, one can be more expensive to acquire, but other life cycle costs, such as lower fuel consumption, make it a better investment.
Overall, a life cycle cost analysis is a great way to estimate all the costs associated with the equipment’s useful life and make better-informed purchasing and maintenance decisions.
Centralize Your Equipment Information
Our third tip is that construction companies should centralize their equipment information, which provides them with improved visibility, efficiency, and control over their equipment life cycle.
In other words, the more information you have about your company’s equipment, the better your life cycle management will be, including the first two tips—planning and analysis.
And, when all equipment information is kept and updated in one place, that’s much easier to do.
Therefore, if your construction business is still keeping equipment management data in spreadsheets (or even paper), you should consider using equipment management software to centralize the data and track equipment throughout its life cycle.
More specifically, here is what such software does better than Excel or paper-based methods:
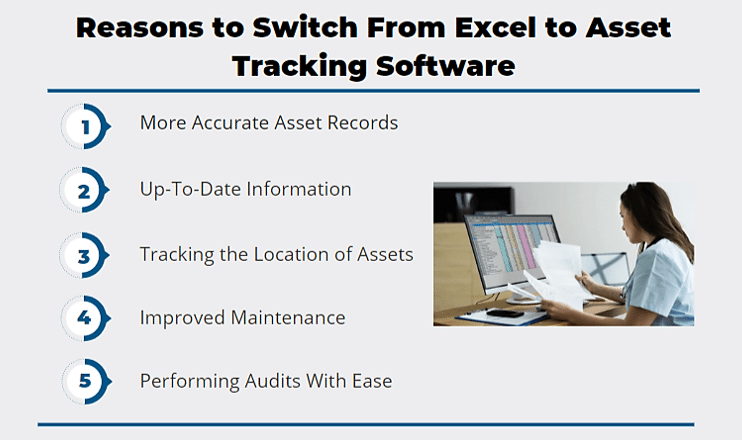
Basically, good equipment tracking software will enable you to create a centralized inventory of tools and equipment with accurate and up-to-date information, track their location, usage, and maintenance, and easily perform different equipment audits.
For example, our tools and equipment tracking software, GoCodes, combines cloud software and a scanner app (both available on your smartphone, tablet, or similar device) with patented QR code tags attached to your assets to cost-effectively provide the above-mentioned benefits.
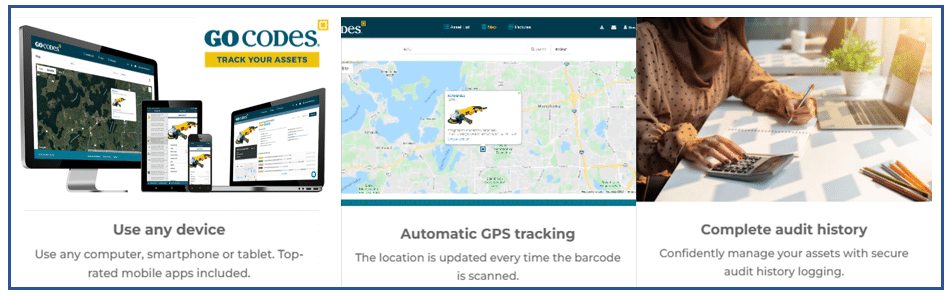
The steps required to set up the tracking system and centralize your equipment information essentially consist of the following:
- labeling equipment you want tracked with customized QR code tags
- entering or transferring the relevant equipment data into the system
- making sure everybody is committed to using the system
Once tracking is up and running, this enables you to establish a check-in/check-out system, where workers can simply scan a piece of equipment they will use and scan it again when they return it.
This feature, along with others, gives construction companies a comprehensive view of where their equipment is, who is using it, and when maintenance is due.
Naturally, this means that equipment allocation, maintenance, compliance, and safety are improved, which leads to better decision-making regarding life cycle management.
Therefore, construction companies that want to improve their equipment life cycle should consider using software to centralize all their equipment info and gain better visibility and control over their equipment life cycle.
Prioritize Your Maintenance Strategy
Of course, different construction equipment will have different life cycles and won’t require the same level of maintenance, so our final tip is that you should prioritize your maintenance strategy.
This prioritization means you should decide whether to establish a preventive or predictive maintenance strategy.
So, let’s first explain the difference between them.
Preventive maintenance simply means regularly inspecting, cleaning, and servicing equipment at predetermined intervals, regardless of the condition of the equipment.
Of course, the interval will differ according to the type, usage, and age of equipment.
You can assess these intervals based on metered triggers like hours of operation or miles driven. For example, a dump truck may require servicing every time it passes another 10,000 miles.
The basic premise is that regularly performing maintenance will improve the equipment’s useful life and reduce the possibility of breakdown.
Here are the pros and cons of preventive maintenance, courtesy of Better Buys:
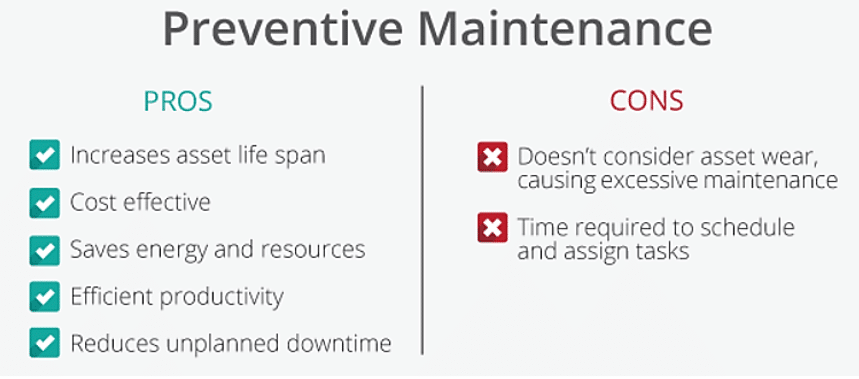
As you can see, although it can lead to unnecessary maintenance, the advantages of this strategy still far outweigh any potentially higher maintenance costs.
On the other hand, predictive maintenance takes a different, more technologically advanced approach where the equipment’s condition is monitored using various sensors (built-in or installed later), expert observations, and predictive algorithms to “foresee” when maintenance is required.
As such, predictive maintenance can minimize the machine’s downtime but does require sensors to monitor its condition, as well as skilled staff to observe the machine and interpret the data collected by sensors.
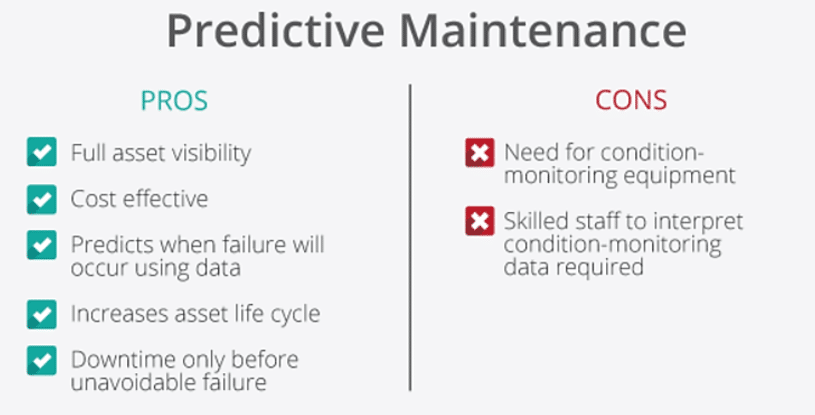
Of course, these two approaches can be combined, which will depend on an individual construction company’s specific needs and available funds.
Both of these strategies are classified as proactive maintenance—as opposed to reactive, “run to failure” maintenance—and both can improve the equipment life cycle, increase its efficiency, and minimize unplanned failures and the resulting downtime.
Therefore, to extend the lifespan of your equipment, you should prioritize equipment maintenance by deciding which strategy (or their combination) would best serve your needs and fit your company’s budget.
Conclusion
To summarize, improving the life cycle of your equipment should start with investigating past practices, current resources, and future needs to create an equipment management plan.
That plan should be further informed by performing a life cycle cost analysis, which will reveal the actual cost of a piece of equipment over its lifetime.
Both of these tips are much easier to implement when your equipment data is centralized and your assets are tracked in real-time, so that was our third tip.
Finally, as we just covered, your maintenance strategy should be set according to your priorities.
Overall, by implementing these four tips, you can improve your construction equipment’s lifespan, reduce downtime and unnecessary costs, and increase productivity.