While the advantages of streamlined equipment management are widely acknowledged, it’s also crucial to understand the intricacies of its implementation.
What does it truly mean to manage equipment effectively?
To answer this question, it’s essential to dissect each element of the process and devise optimal strategies for handling them.
Only by doing so can you ensure you’re maximizing the potential of your assets.
This article, therefore, aims to delve a bit deeper into the nuances of equipment management, providing insights into how each facet contributes to overall efficiency.
Let’s get started.
In this article...
Capturing Relevant Equipment Data
In the age of big data, the key to propelling businesses forward lies in having access to relevant asset information.
Consequently, we see an increasing number of construction companies integrating some form of equipment tracking technology into their management strategies.
These systems enable users to extract vital insights about their machinery, influencing and optimizing their decision-making processes.
For instance, Jason Threewitts, the site innovation manager at Carter Machinery, highlights that monitoring engine overspeed rates can help predict a machine’s maintenance needs as well as aid in understanding job sites and their challenges.
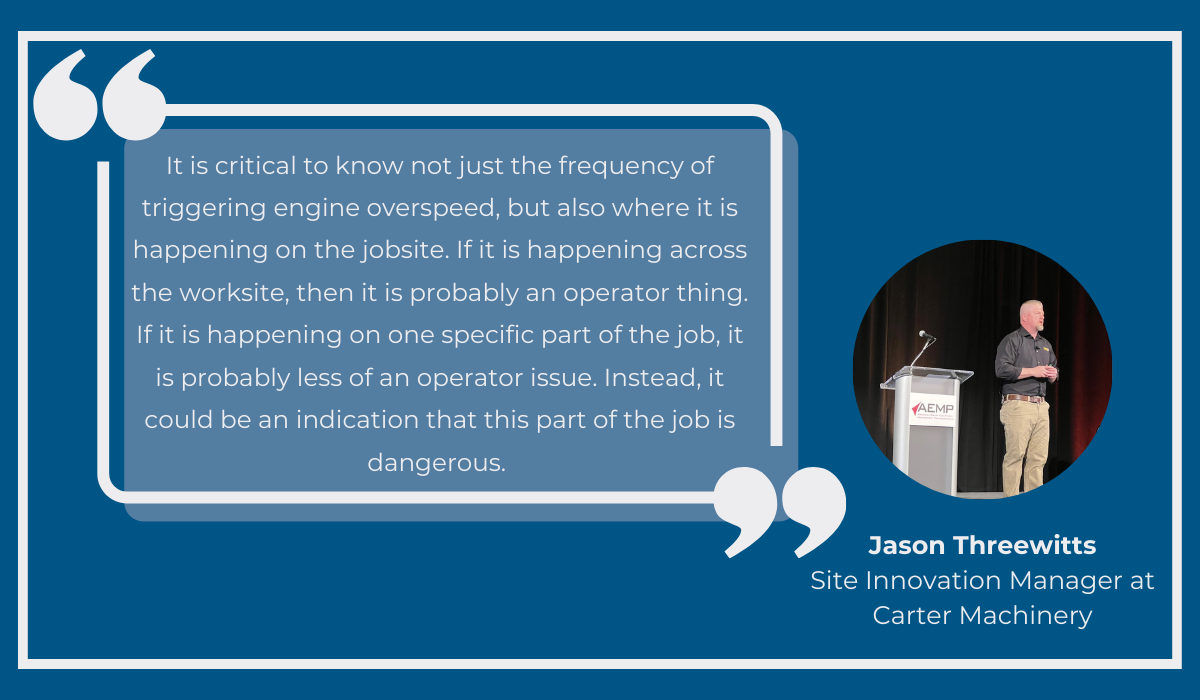
Your equipment holds a surprisingly large amount of information—you just need to know where to look.
However, while high-quality data is crucial, not all data can be considered relevant.
In fact, Autodesk’s research reveals that a significant portion of the information collected on job sites could be categorized as “bad”—either incorrect, incomplete, or untimely.
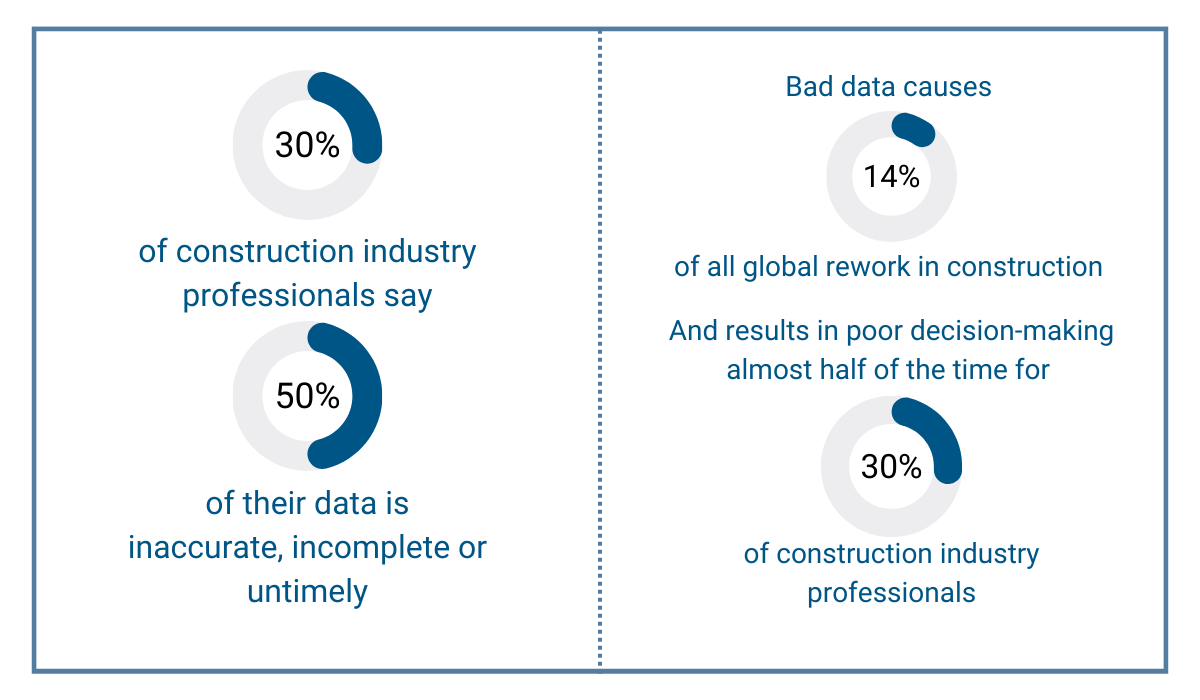
This erroneous data can be quite harmful to companies, leading to poor decision-making and sometimes even costly rework.
It’s precisely these problems that underscore the importance of using advanced technology for meaningful data collection and analysis.
Traditional tools like spreadsheets and pen-and-paper methods just don’t cut it anymore.
Asset tracking solutions, on the other hand, are a much more popular choice nowadays, as they automatically monitor and store all important information, including equipment’s location, utilization, and status in one place and make it accessible on the go.
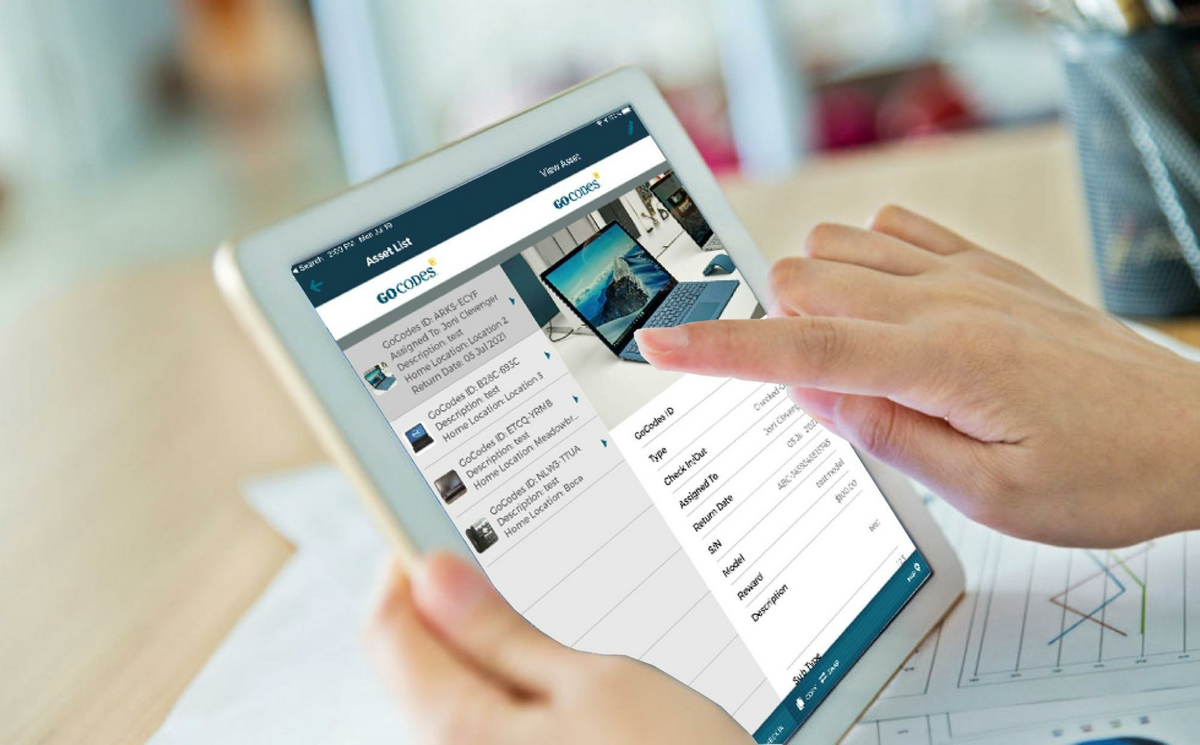
Curious about where your excavator is and when it’ll be available for use again?
With an asset tracking solution, all you need to do is take a quick look at your phone.
All in all, as the cornerstone of efficient equipment management, precise data empowers businesses to make informed and sound business decisions throughout the entire asset’s life cycle, whether it’s acquisition, operation, disposal, or, of course, maintenance.
Managing Equipment Maintenance
Anyone who has ever been responsible for the management of construction equipment will tell you that the importance of proper maintenance cannot be overstated.
After all, the success of your projects hinges on the reliable performance of these machines; the last thing you want is for them to unexpectedly fail in the middle of a job.
Justin Steger, solutions marketing manager at John Deere Construction & Forestry, underscores that ensuring sufficient care for your machinery and tools not only contributes to a higher resale value, but it’s also crucial for their longevity.
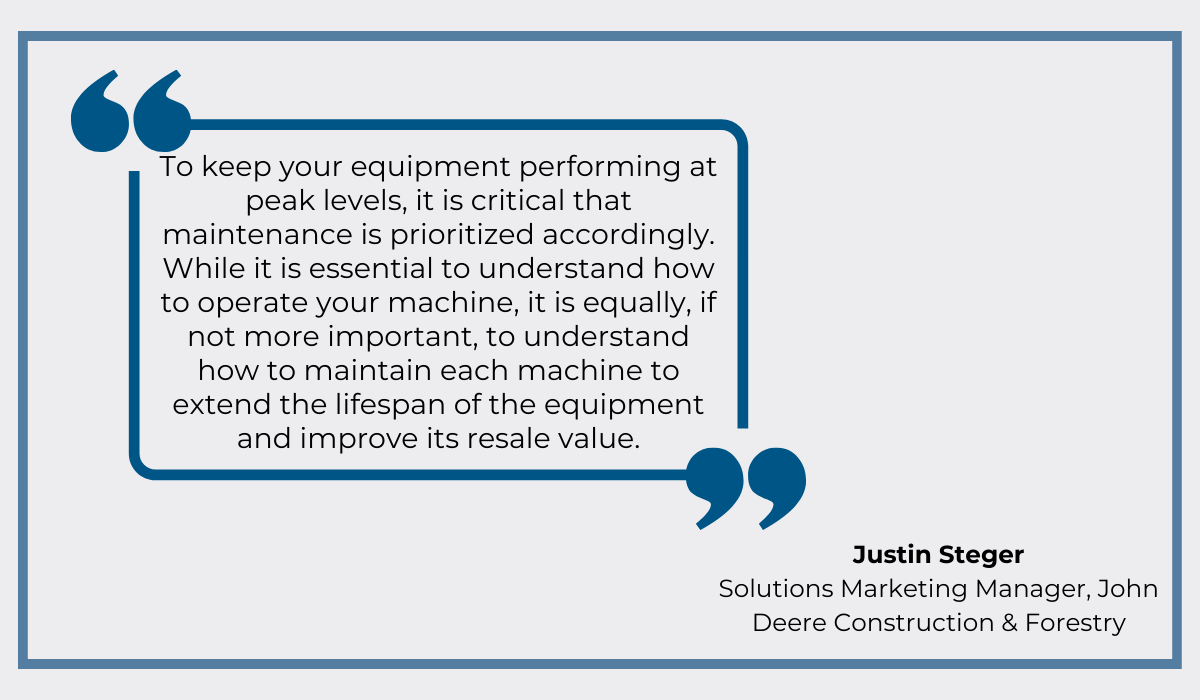
It’s imperative for your assets to remain dependable for as long as possible, and effective maintenance management is the key to achieving this.
Without adequate servicing, on the other hand, you expose yourself to a multitude of serious consequences.
For instance, a study conducted by ATS revealed that equipment breakdowns resulting from inadequate upkeep ranked as the primary culprit behind decreased productivity in manufacturing industries and other asset-intensive sectors.
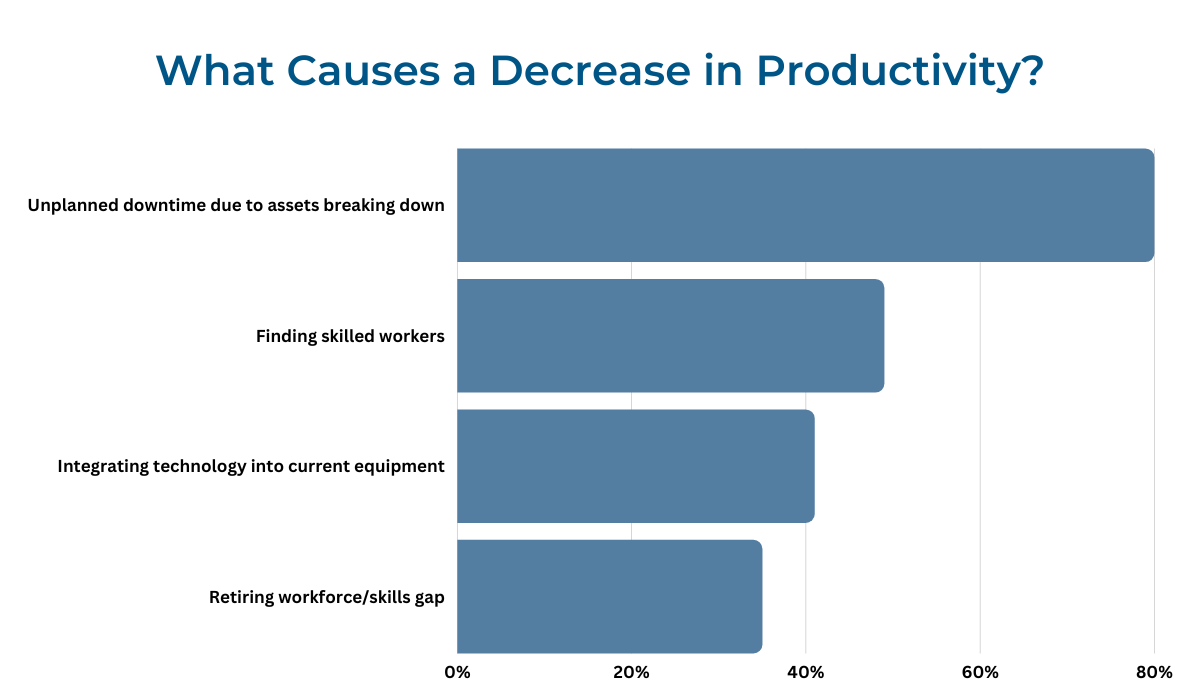
People working in construction, which is inherently asset-heavy as well, would agree that lack of proper care not only affects the machinery itself, but whole project teams and their ability to meet deadlines.
This is where that relevant, high-quality data steps in.
By monitoring your assets and gathering information on their usage, you empower yourself to forecast potential failures in specific machine parts.
In such cases, you can easily send your team to intervene and rectify the issue before it escalates into a major disaster or poses a safety hazard.
This approach is commonly referred to as preventive maintenance.
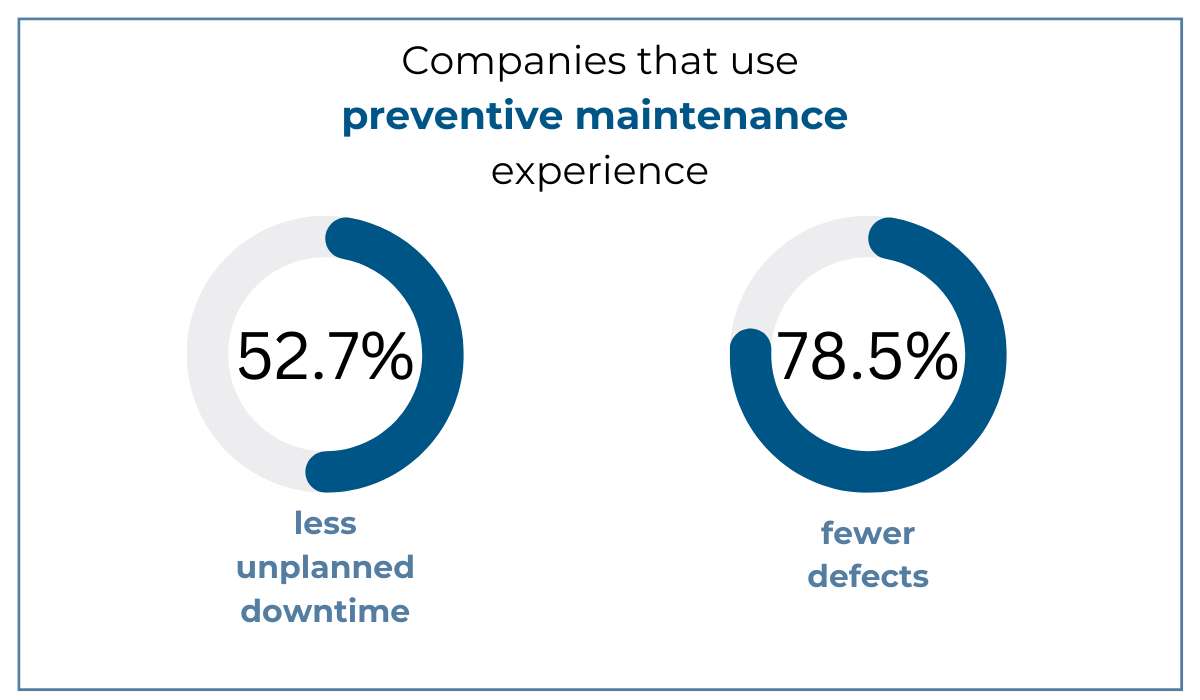
Proven time and time again to be superior to reactive maintenance, this proactive method stands out as one of the most efficient ways to ensure the prolonged operation of your valuable equipment.
Therefore, it’s well worth considering and integrating into any equipment management strategy that aims to maximize the utilization of company assets.
Ensuring Equipment Availability
Proper maintenance will increase your equipment’s longevity, sure, but it’ll also help ensure it’s available when you need it the most.
Although this may sound pretty obvious, we’ve already explained that heavy machinery suddenly breaking down can cause significant project delays and a decrease in productivity.
But what’s the true cost of this unplanned downtime?
Siemens attempted to answer this question in their 2022 report aptly titled “The True Cost of Downtime”, and the findings were staggering.
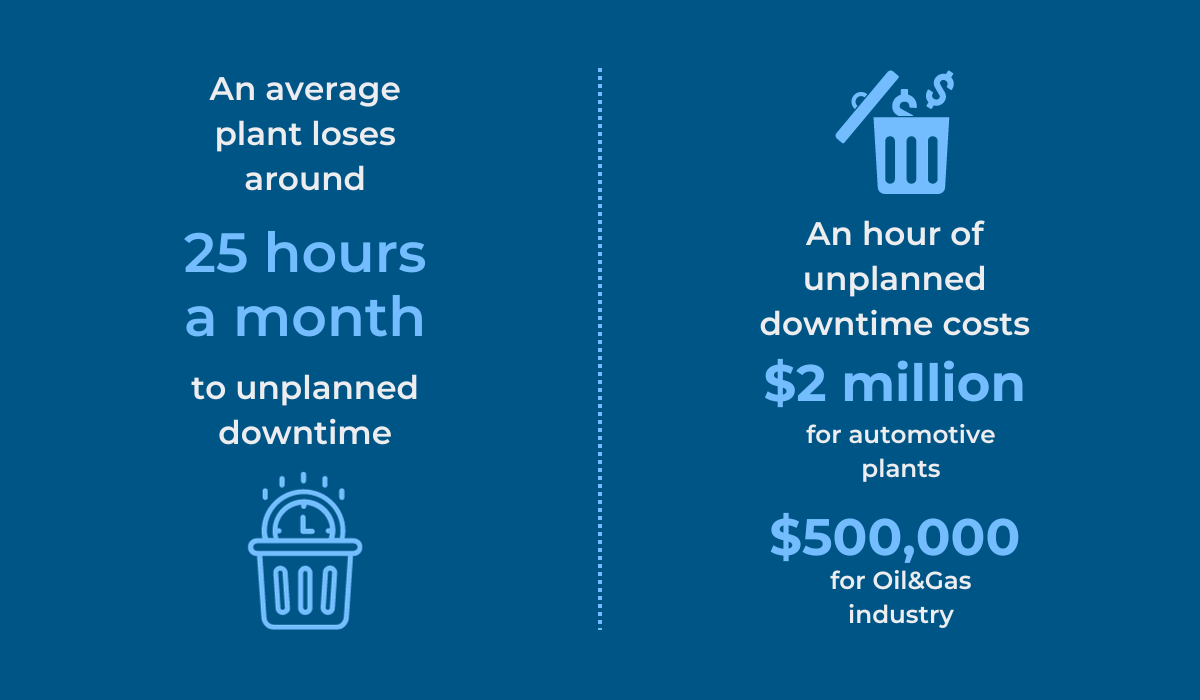
For instance, in automotive plants, one hour of unexpected downtime costs over $2 million, while the Oil and Gas companies lose approximately $500,000 for each unproductive hour.
These unanticipated disruptions aren’t a rare occurrence either; the average plant experiences around 25 hours of unplanned downtime each month, making those financial losses even more substantial.
Therefore, one of the key objectives of efficient asset management is to maintain equipment in tip-top shape to minimize, if not eliminate, unwanted downtime as well as the decrease in the overall operational efficiency that comes along with it.
Longevity, in this case, is certainly synonymous with dependability.
While preventive maintenance is widely recognized as effective for achieving this goal, one of its aspects sometimes goes overlooked: recordkeeping.
Tyler Smith, product manager at Volvo Construction Equipment, also emphasizes the importance of keeping maintenance records, likening them to a machine’s medical files.
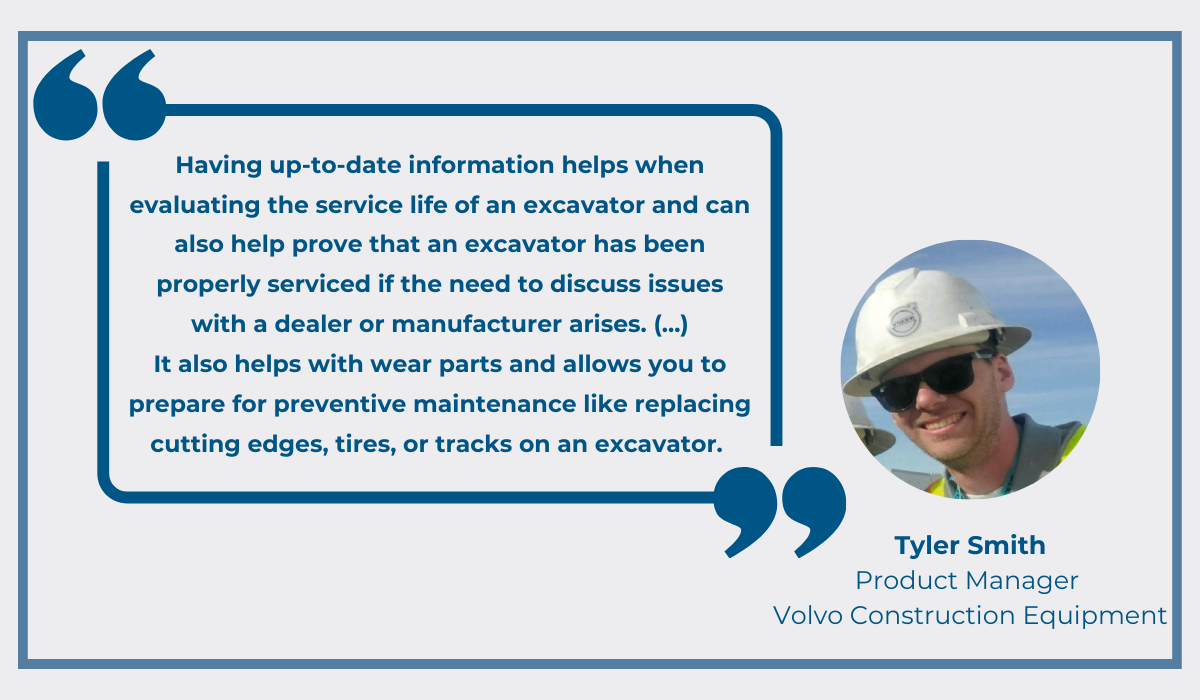
Merely conducting daily checkups is not enough if the details of observations made during those inspections and servicing are not properly documented.
Essentially, it’s like having a doctor’s appointment with no medical file.
This up-to-date, thorough information can then be reviewed and analyzed by multiple pairs of eyes, increasing the likelihood of identifying potential issues early on and serving as a basis for preventive maintenance.
Indeed, the power of comprehensive maintenance logs should never be underestimated.
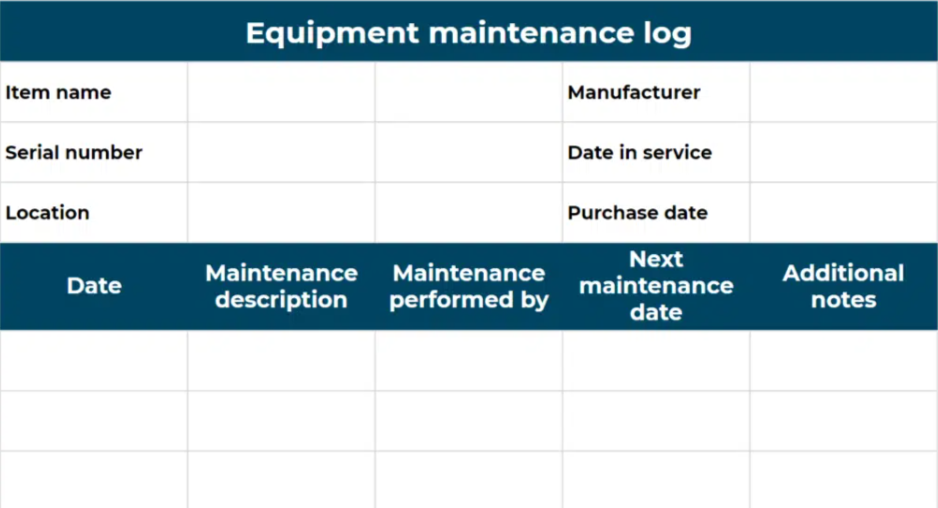
Detailing the type of service performed, the date, the responsible individual, and more, they serve as a valuable resource for tracking upkeep activities and planning for the future.
When it comes to effective equipment management, after all, it’s all about thinking ahead and creating efficient strategies that will ensure seamless operations without any hiccups.
Knowing the Total Cost of Ownership
Managing your equipment efficiently throughout its entire lifecycle relies heavily on understanding its value and comparing it to the expenses it incurs.
Do your machinery’s expenses, such as repairs, outweigh the income it generates?
If so, it might be time to consider replacement.
In the simplest terms, tracking the total cost of ownership (TCO) is the most effective way to gauge the cost-effectiveness of your assets.
However, despite its importance, industry professionals, as noted by Troy Geisler from Talbert Manufacturing, often overlook TCO and fail to realize how big of an impact it can have on decision-making.
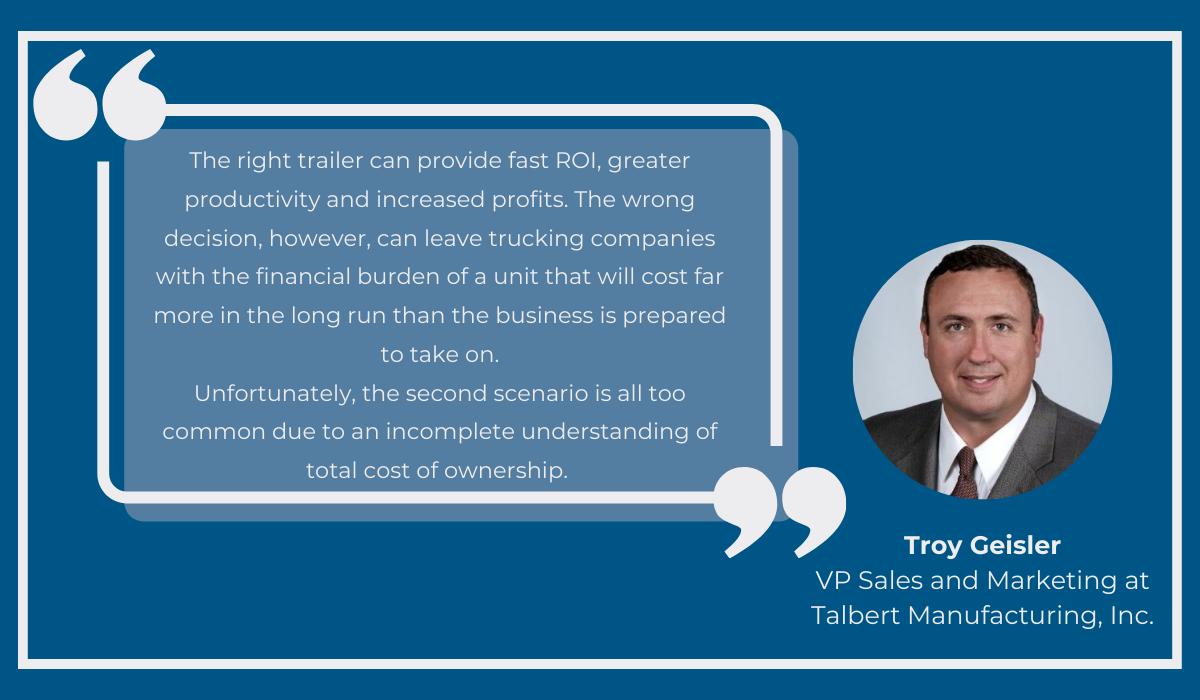
While Geisler specifically talks about heavy-haul trailers here, the same principle can be applied to any piece of equipment.
Many individuals focus solely on the initial expense a machine incurs, neglecting the bigger picture.
But beyond the purchase price, it’s crucial to take into consideration costs like:
- Maintenance costs
- Operating expenses
- Insurance
- Downtime costs
- Depreciation
- Taxes
- Storage
Figuring out all the ways in which your machines and tools cost you money is the only way to ascertain whether you are truly maximizing their potential, and to be better prepared for a new investment when the time comes.
Moreover, it’s essential to note that people sometimes misunderstand the term “initial equipment cost” itself.
It encompasses more than just the purchase price as many assume.
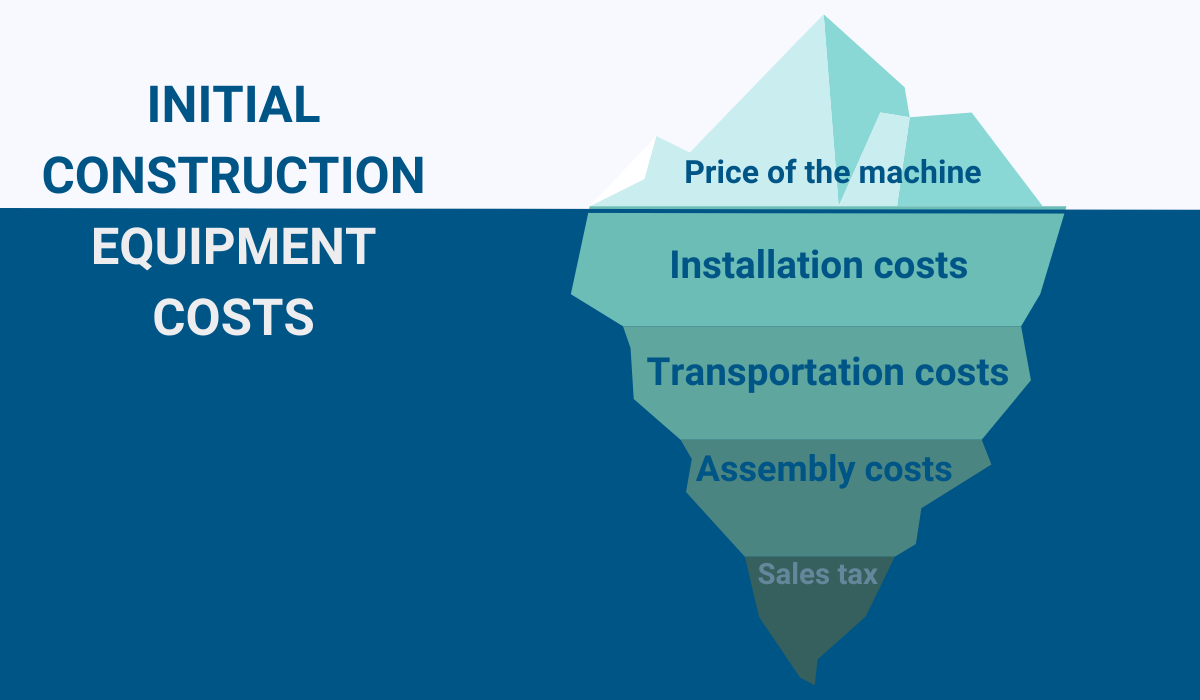
In fact, initial equipment costs also include all expenses related to making that asset operable, such as installation, transportation, assembly, and sales tax.
At the end of the day, every equipment manager should be aware of the total cost of ownership and understand its various components.
Those who do are better equipped to make informed decisions regarding the purchase, disposal, and replacement of machinery, as well as to minimize unnecessary asset-related expenditures in general.
Using Equipment Management Software
One common theme throughout all the previous sections of this article is the significance of trustworthy information as a crucial factor in efficient decision-making across all aspects of equipment management.
Whether you’re looking to properly allocate your assets, plan future maintenance tasks, or purchase a new machine, the solution is always the same—look at the data.
From equipment locations, users, and warranty details to salvage value estimates, maintenance records, and other important documentation, comprehensive asset information is essential when it comes to steering your business toward success.
Now, imagine managing all this data manually through spreadsheets.
One quick look at Acuity Training’s research on Excel user proficiency reveals why this isn’t such a good idea.
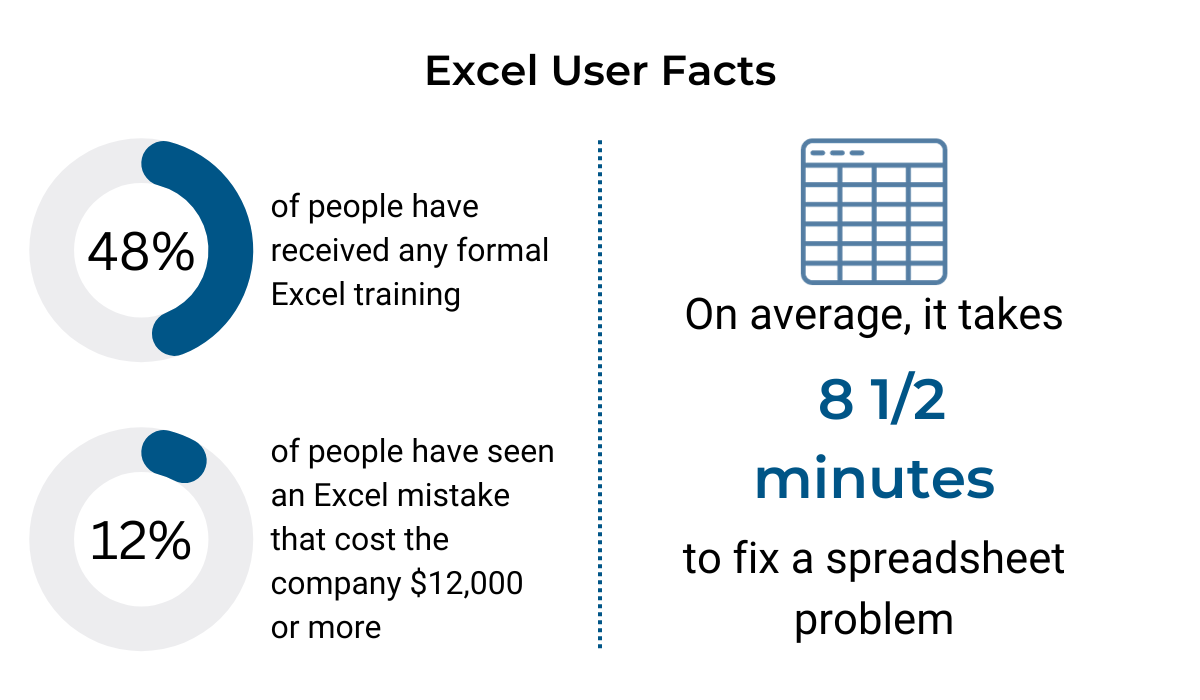
Not only is this method highly susceptible to human error, but it can also lead to significant time and financial wastage.
Automated equipment management software is a far more reliable solution in this case.
Our own system, GoCodes Asset Tracking, excels in collecting this vital information but not at the expense of user-friendliness.
Even those who might feel less comfortable with technology will become expert GoCodes Asset Tracking users in no time.
Simply attach our QR code labels to your machines and use our app to scan them, instantly gaining access to, or updating, asset data.
Each time the labels are scanned, the location of the update is recorded, facilitating the establishment of a convenient check-in/check-out system—one scan for check-out, another for check-in.
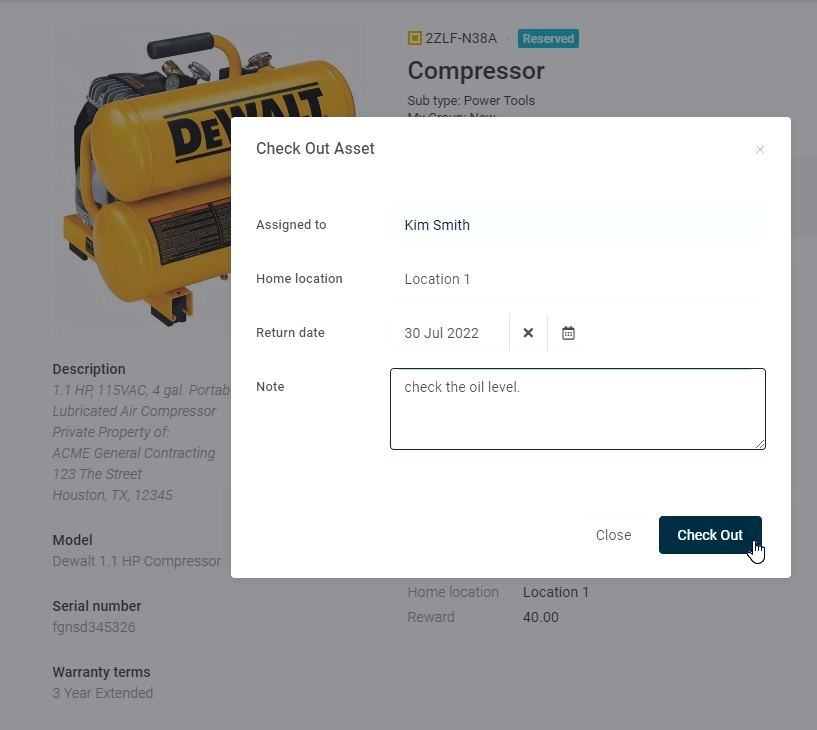
The information about where an asset is, and who has it, is then accessible to everyone, fostering better coordination among workers.
However, the system doesn’t merely assist in data collection; it also aids in making sense of it.
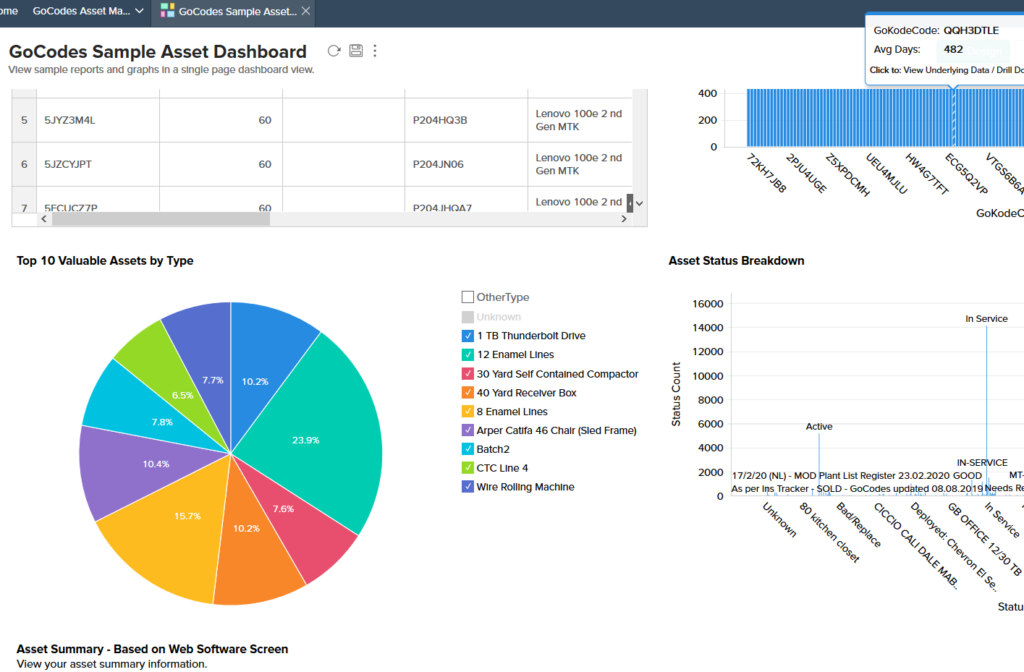
GoCodes Asset Tracking reporting feature enables you to visually represent and distill the compiled data, which allows you to use it more effectively.
This not only provides complete visibility of your assets but also ensures total control over them.
Conclusion
In wrapping up this article, we trust that you’ve gained valuable insights and feel better equipped to tackle your equipment management strategy.
By focusing on these five key elements, you can undoubtedly establish a solid foundation for operational excellence, with confidence.
Trust us; the benefits are well worth the effort.
This proactive approach not only minimizes downtime, prolongs equipment service life, and reduces repair costs but also fosters a culture of responsibility and efficiency within the company.
Ultimately, that’s what effective equipment management is all about.