Heavy equipment, vehicles, and tools are both high-value investments and essential resources for any construction company.
Therefore, efficient management ensures that construction equipment is optimally used and allocated, well-maintained, and safeguarded from theft, meaning that projects are completed on time, workers are safe, and investments are protected.
Against this backdrop, this guide will explain what equipment management is, why it’s important, cover the pitfalls of neglecting it, and provide practical tips to harness the full potential of your construction equipment.
In this article...
What Is Equipment Management
As an umbrella term, equipment management encompasses the strategic coordination and oversight of all activities related to the construction equipment, vehicles, and tools within a company’s operations.
As such, it includes everything from the moment a piece of equipment is purchased by the company, put into operation, used, maintained, repaired, and, finally, disposed of.
To visualize all the processes that equipment management entails, here is an overview of a typical equipment lifecycle:
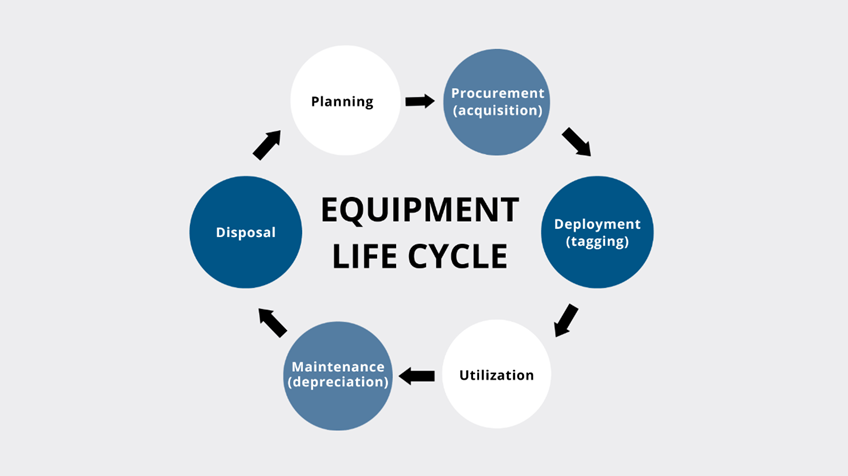
In a nutshell, after a company acquires the planned equipment, that machine will be prepared for operation (deployment) and tagged for identification and tracking purposes (tagging).
Until its disposal, that equipment will be utilized and maintained, gradually losing value over time (depreciation) in both operational and financial reporting terms.
Keep in mind, though, that some of these equipment lifecycle management stages won’t apply if you’re renting equipment instead of buying it.
Those implications aside, let’s further delve into why efficient management of construction equipment, vehicles, tools, and other assets is crucial for any company’s productivity and profitability.
Why Is Equipment Management Important
Obviously, no construction project can be done without the right tools and equipment, and buying or renting them costs money.
Similarly, old or poorly maintained equipment will cost even more because it will underperform and break down more frequently, causing employee downtime, potential project delays, and necessary equipment repairs or replacement.
Therefore, construction companies implement equipment management strategies to ensure equipment is running smoothly and make better-informed purchasing and project scheduling decisions.
Let’s look more closely at these three benefits.
Allows for Informed Purchasing Decisions
By tracking equipment throughout its lifecycle, construction companies collect key data to gain valuable insights into each asset’s performance, maintenance history, and overall lifespan.
This thorough understanding of these and other considerations empowers them to make informed purchasing decisions, such as when new equipment should be bought or whether it’s better to repair or replace a machine if it breaks down.
In a nutshell, it’s easier to make such decisions (and understand their budgeting implications) when the following equipment management data is consistently tracked and kept up to date:
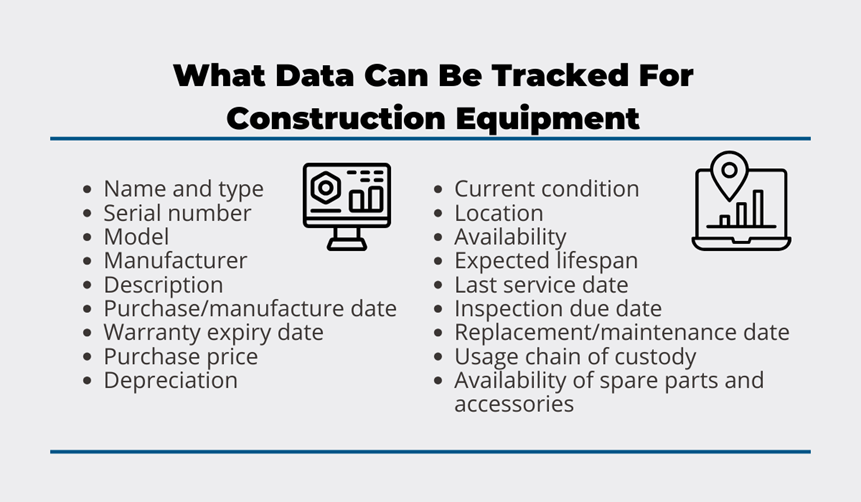
For example, when you know that a machine is nearing the end of its expected lifespan, you can budget for its replacement.
Likewise, if it suffers any major breakdown, it’s clear that investing in repairs might not be the most cost-efficient decision.
Moreover, it’s easy to identify, for instance, which equipment models are more prone to failure or which equipment might experience increased wear and tear due to heavy usage.
From there, you can make appropriate maintenance and replacement decisions.
Overall, this data-based, proactive approach to equipment management ensures that purchasing decisions align with your company’s specific needs and budget, optimizing the overall cost-effectiveness and efficiency of its operations.
Helps You Stay On Top of Maintenance
When maintenance-related tasks are tracked and managed manually (typically on spreadsheets), it’s easy to miss or mix up regular maintenance tasks, which can lead to unexpected breakdowns and higher repair costs.
Conversely, when maintenance management processes are digitized and automated with the help of software, this helps companies stay on top of their maintenance by automating scheduling, tracking maintenance and repairs, and sending timely reminders.
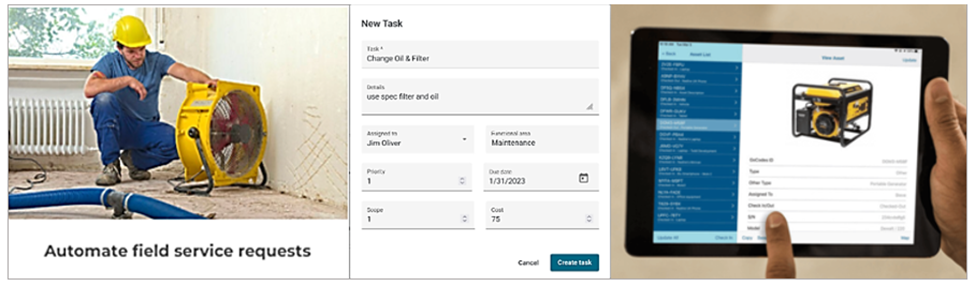
In essence, this ensures construction companies stay ahead in maintaining their equipment, preventing unexpected breakdowns, reducing downtime, and extending the lifespan of assets.
Now, let’s see how these and other features of equipment management software can help you improve project planning and scheduling.
Improves Project Schedule Planning
When you have real-time visibility into equipment availability, usage patterns, and maintenance schedules, this enables you to plan and schedule more precise project timelines.
With this information, you can avoid scheduling mistakes, optimize resource allocation, and ensure that equipment is deployed where and when needed.
Moreover, this not only helps you schedule equipment for future projects but allows for accurate billing and improved preventive maintenance planning.
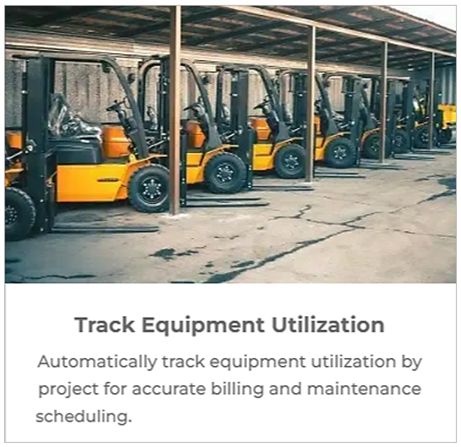
With streamlined project scheduling, construction companies can more confidently plan project schedules, meet deadlines, and deliver projects with increased precision and effectiveness.
Consequences of Ineffective Equipment Management
Having covered just some of the benefits of streamlined equipment management, it’s only fair to also highlight the biggest downsides caused by inadequate organization and ineffective management.
Whether it’s missed maintenance, workers sitting idle, or poor communication, the potential consequences of these and other equipment management mistakes can be boiled down to not taking full advantage of your equipment and experiencing costly project delays.
Poor Return on Investment
Regardless of how much construction equipment costs, you naturally want your investment to pay off during its useful life.
However, when equipment is not efficiently utilized or adequately maintained, its performance suffers and its lifespan decreases, leading to a poor return on investment (ROI).
In essence, ROI seeks to quantify the net profit (return) a piece of equipment will generate over its lifetime relative to the total investment cost.
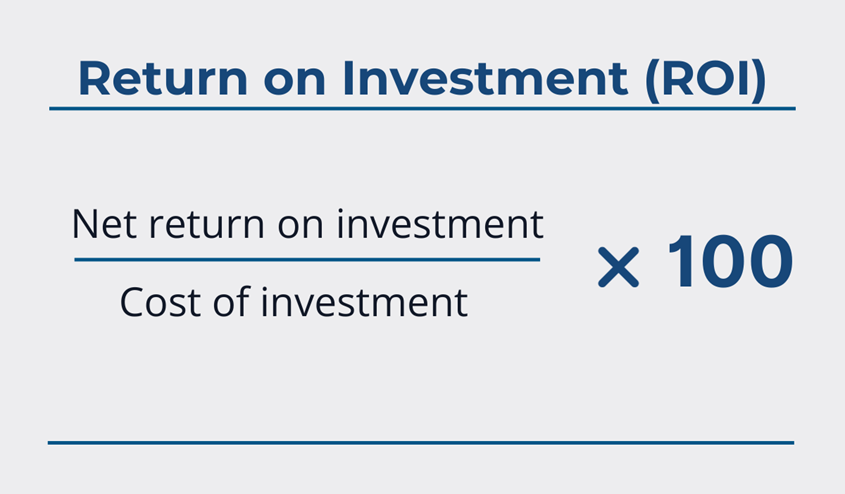
Although this formula seems simple, actual ROI calculations typically involve more detailed estimates (e.g., useful life, depreciation, utilization intensity) and projections (e.g., potential revenue generated, anticipated maintenance costs, inflation rates).
In essence, it boils down to how precise your estimates are (based on historical data and experience) and how well you’re tracking the equipment’s utilization and maintenance status throughout its lifecycle.
Moreover, a lack of centralized equipment management data collection can lead to inefficient utilization and insufficient maintenance, thus diminishing the ROI of all equipment and potentially resulting in project delays.
Costly Project Delays
Naturally, ineffective equipment management is often the culprit behind the construction industry’s major strife—project delays.
For instance, consider a scenario where essential equipment maintenance, like an oil change, is overlooked due to oversight during pre-operational inspections or a failure to schedule the next oil replacement.
In any case, this leads to an unexpected breakdown of a critical machine.
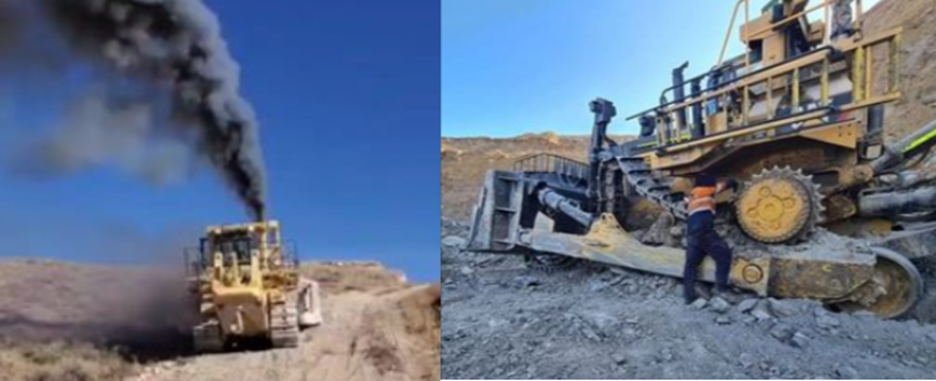
And that’s how a simple equipment management oversight can have complex and costly consequences, starting with disrupting the project timeline.
Therefore, such delays typically involve additional labor and material costs (employee downtime plus repairs), rental expenses for replacement equipment, and potential penalties for missing project deadlines.
Of course, this impacts the project’s overall profitability and potentially damages the company’s reputation for timely project delivery.
So, let’s see what you can do about preventing diminished returns on your equipment investment and avoiding costly project delays caused by inefficient equipment management.
Tips for Better Equipment Management
While there are many tips on improving equipment management, we’ll keep our focus on practical, tangible solutions that directly impact the productivity and security of your construction equipment.
Use Equipment Management Software
If we had to choose only one way to streamline construction equipment management, it would have to be software.
In other words, a single software system can digitize, organize, and automate a wide range of equipment management tasks, from maintenance scheduling to asset tracking.
This saves time, minimizes manual errors, and makes up-to-date information easily accessible to all users in one central database.
Naturally, such software should be easy to use and affordable, and offer a variety of features, among which the ones below are considered key for ensuring smoother operations and safeguarding your valuable assets.
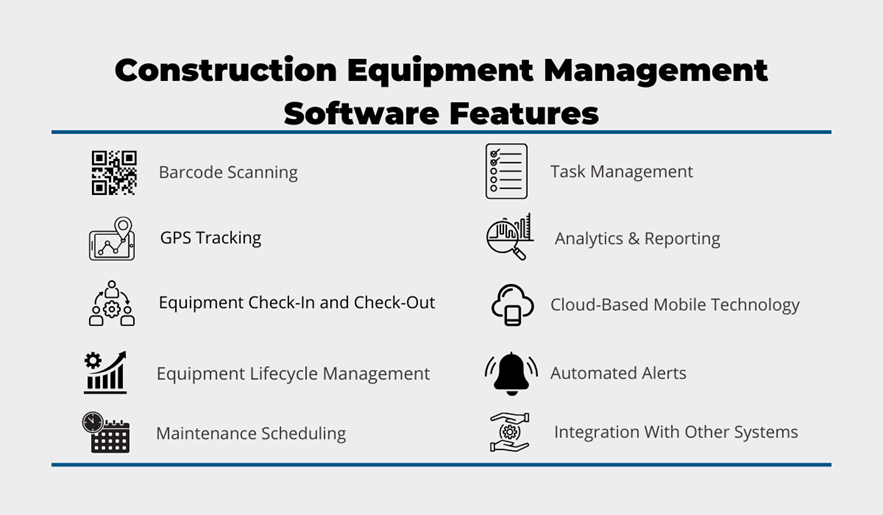
For instance, barcode scanning refers to barcodes or QR codes being attached to equipment so they can be scanned for identification and tracking purposes.
Although some systems may still rely on handheld, special barcode scanners, the majority of today’s software solutions come with a digital, in-app scanner.
This enables users to scan barcode/QR code labels with their phone or tablet to easily access and view or update the relevant equipment info.
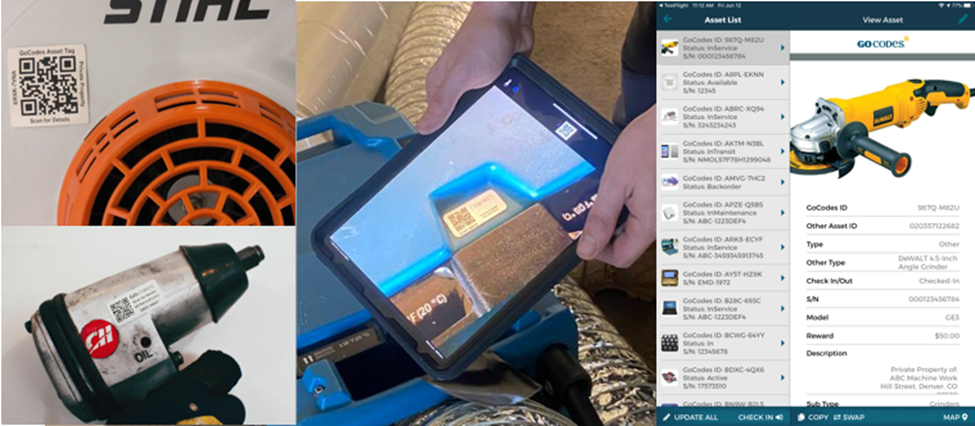
Moreover, such solutions should be cloud-based, meaning they can be accessed from any internet-connected device at any time.
When QR codes are affixed to equipment and linked with their unique data in the database, this gives rise to the other features shown above, such as maintenance scheduling, automated notifications, task management, and data analytics and reporting.
Best of all, the right equipment management software enables you to—as discussed below—track your equipment and prevent equipment theft or loss.
Track Your Equipment
Knowing where your equipment is located helps both maximize overall productivity and enhance equipment security.
Of course, tracking the location of equipment as it moves from site to site can involve active GPS trackers, which are usually reserved for construction vehicles and heavy machinery due to price and size considerations.
However, there’s a simpler and more cost-efficient solution, namely using GPS-enabled QR codes.
In other words, every time a worker or manager scans an asset’s QR code with their phone, the software will use the device’s GPS function to automatically capture the asset’s GPS location and show it on a map.
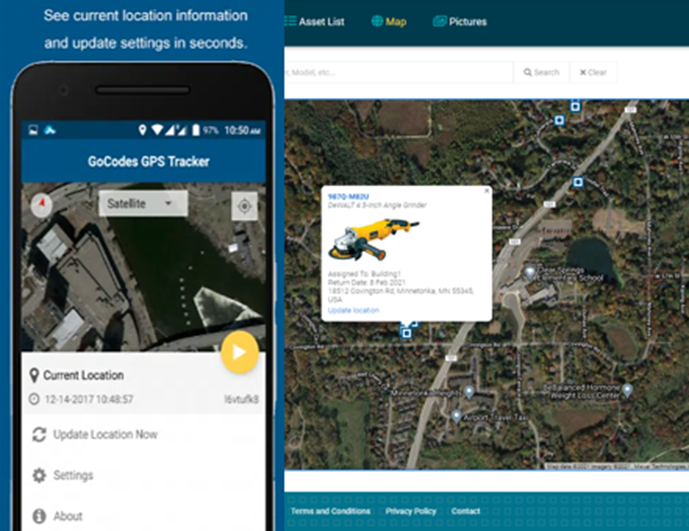
This is exactly how our equipment management software, GoCodes Asset Tracking, leverages QR codes for much more than just easy identification and quick data entry for lifecycle management purposes.
Using QR codes alone (or combining them with GPS trackers or Bluetooth beacons for added security) for location tracking will provide full visibility into where your assets are, thus increasing productivity while also—as you can see below—acting as a theft prevention measure.
Take Steps to Prevent Equipment Theft
As expected, efficient equipment management includes not only steps to keep them in good condition and optimize their performance but also measures to prevent their theft.
Similar to breakdowns, theft of a critical piece of equipment can disrupt operations and lead to project delays.
However, even theft or loss of many smaller tools and other assets will certainly affect your company’s bottom line, so it’s wise to take prevention steps on all levels.
For starters, this should include traditional security measures like fences, alarms, secure storage, and proper employee training.
One effective anti-theft feature enabled by QR code-based tracking systems we mentioned is that you can establish an automated equipment check-in/check-out system.
This means that workers are instructed to scan a tool or equipment when taking it from the toolroom or storage area and scan it back in when they return it, and the software will keep a detailed check-in/out log.
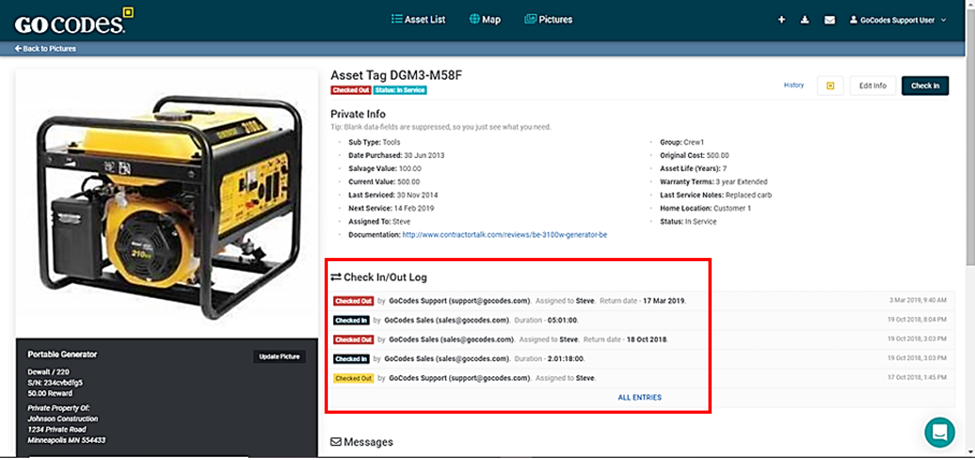
When properly implemented, this system will improve worker accountability, thus preventing internal theft and negligent operation.
At the same time, the scan-based location tracking feature may assist in cases of loss or external theft, while the rugged QR code labels make reselling stolen equipment harder and act as proof of ownership when the equipment is found.
Naturally, there are even more advanced anti-theft technologies that include geofences, thermal sensors, and high-precision cameras.
Overall, protecting your equipment from theft is always a good idea, and the combination of classic and modern theft prevention technologies will provide the best results.
Conclusion
So, we covered what equipment management is, and why it’s crucial for construction companies, allowing them to make informed procurement decisions, keep equipment well-maintained, and enhance project scheduling.
Then we explored how ineffective equipment management can affect a company, diminishing its return on equipment investments and causing costly project delays.
Finally, we covered some key tips for better equipment management, which can be operationalized by adopting the right software solution that also tracks equipment locations and users and helps prevent theft.
Ultimately, implementing these tips enables you to achieve efficient equipment management, bringing benefits like increased productivity, minimized costs, and maximized profitability.