This is the reality in the construction industry nowadays: two-thirds of contractors are experiencing delays on one of their projects.
And the problem is expected to continue in the following year, with almost 81% of them predicting further delays in the upcoming 12 months.
Most of these delays were caused by the pandemic and the challenges that came with it.
Yet, contractors continue making some common mistakes that further negatively affect their project deadlines.
Let’s look at some of them and find solutions so you can have better control of your project’s schedule.
In this article...
Unrealistic Resource Projections
Every company has limited resources in the form of labor, materials, and equipment, so miscalculations can have an adverse effect on your results.
In other words, if you don’t assess your inventory levels adequately or schedule 10 people to do a job that requires 20 workers, you’re inevitably creating project delays.
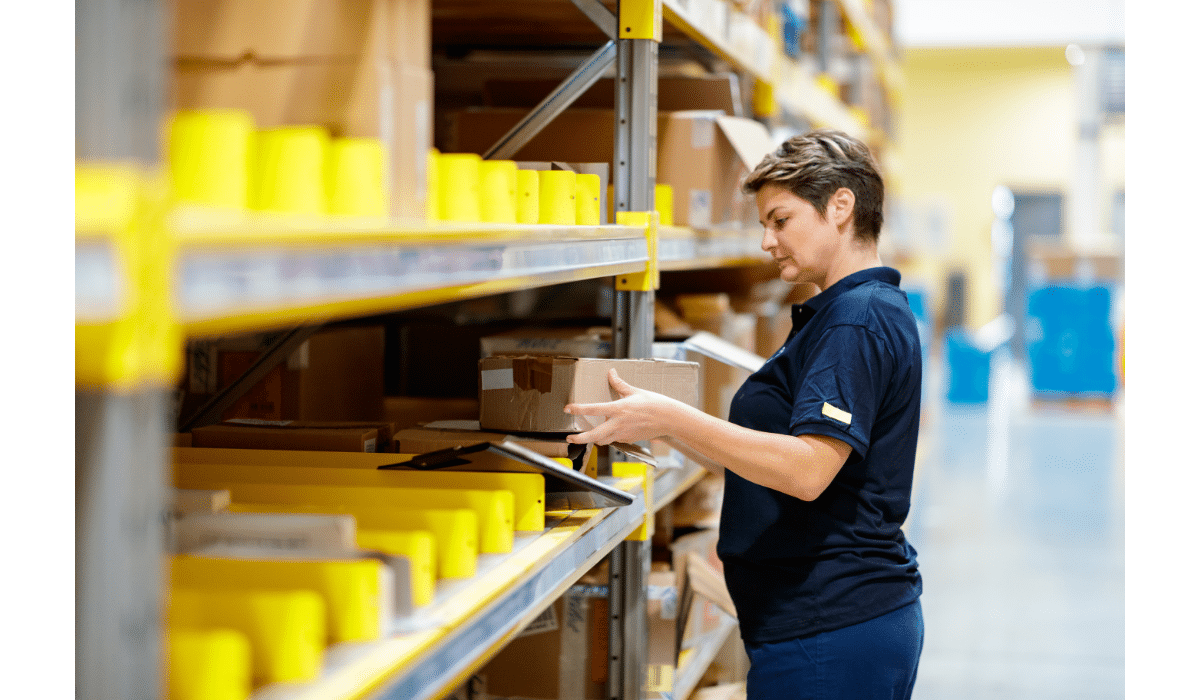
On the one hand, failing to procure enough materials can lead to waiting times with both equipment and labor necessary to install them into the building.
Obviously, waiting means you can’t do other tasks until the material arrives, so the question is not whether you’ll break the project timeline but by how much.
On the other hand, you have to be realistic about how many people can bring a project to a successful and timely completion.
Sometimes, labor shortages require field workers to work overtime, but that should be an exception, not the norm.
Regularly overworking your employees will not create a more productive and happy workforce.
In fact, it will inevitably lower their motivation, put pressure on their health and wellbeing, and even ruin their personal relationships.
That is exactly what happened to this construction worker.
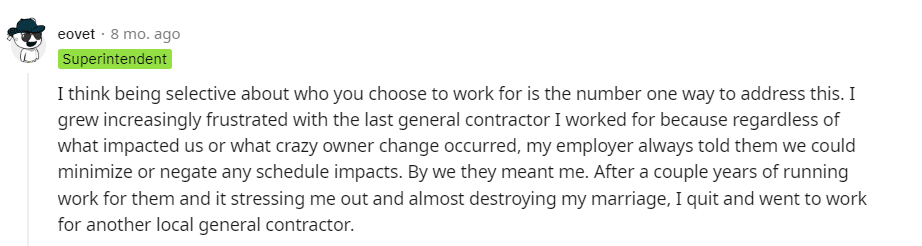
Their boss thought he could cover up his own scheduling mistakes by pushing his employees to work overtime.
After several years of these working conditions, the worker finally decided to quit.
So, what can you do?
Even with limited resources, you can still create realistic schedules and finish work on time.
The most important thing is to have a realistic view of what’s at your disposal at the beginning of the project planning process and work around that.
If you notice missing resources (labor shortage, not enough key materials, etc.), you need to address those shortages early and don’t overcommit existing ones.
Remember to be realistic about what you have and don’t have so you don’t wait for vital resources and extend your project timeline.
Disregarding Project Dependencies
The dictionary definition for dependencies describes them as “relationships between products or tasks”, or to put it simply, each task requires another one to be completed so the following one can start.
Basically, construction activities need to be completed in a logical order so the project can progress successfully.
This means you can’t start painting over drywall until you actually put it in. Yet, many contractors still don’t consider the logical order of dependencies.
What’s more, in an attempt to finish projects early, contractors even try to schedule different workers to complete tasks in the same area simultaneously.
In some cases, you can find carpet installers scheduled to work at the same time as painters.
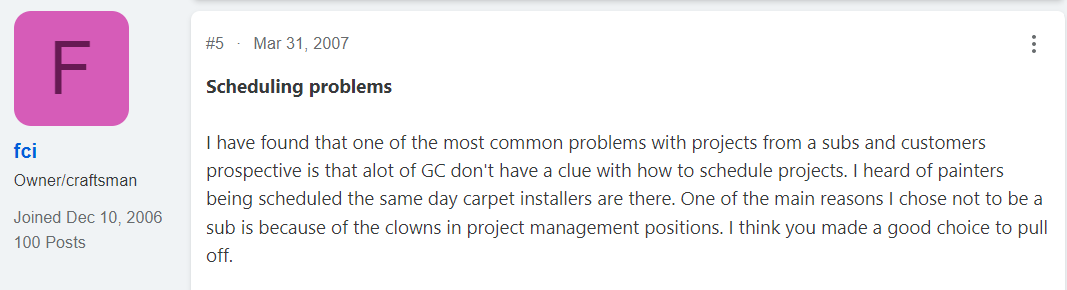
It goes without saying that this will not lead to faster project completion. Either carpets need to be installed first, or the room needs to be painted first.
Working on top of each other will only slow down each subcontractor, create additional waiting times or produce damage to finished work.
The end result is always breaking the project timeline and additional (re)work.
Now, no matter the complexity of your project, construction dependencies are a necessary part of every project.
The best way to address them is to create a detailed schedule for the entire project, considering tasks that depend on each other or overlap.
Here’s how to do it:
- Lay out crucial tasks that link to each other.
- Calculate how long each task will take to complete.
- Identify necessary resources.
- Analyze potential scheduling issues.
- Manage tasks and monitor task completion.
Keep in mind that a proper construction schedule that lists and inserts logical project dependencies is more likely to be completed on time.
Failing to Include Buffer Time in the Project Schedule
In a perfect world, project schedules would be estimated accurately, and tasks would be finished in the timeframe we predicted. Unfortunately, that’s rarely the case.
According to a recent Autodesk survey, 66% of contractors have added costs due to inaccurate schedules, with almost 50% needing to extend the project completion dates.
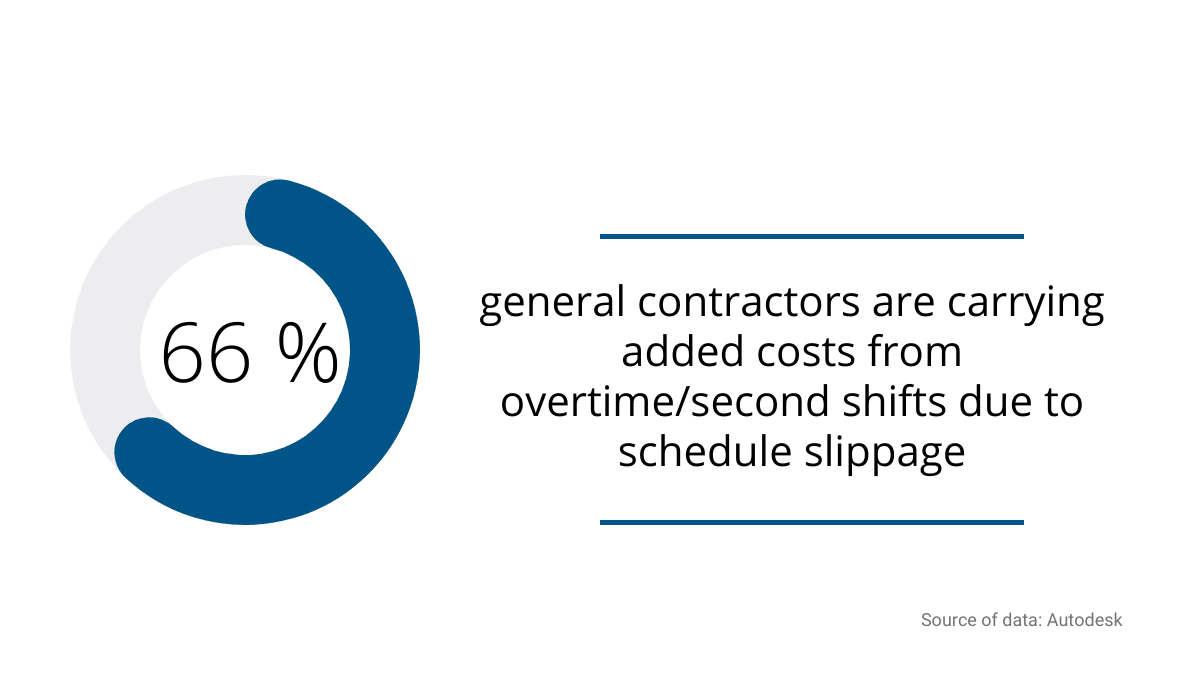
But this is just one side of the coin. In fact, people always make inaccurate time estimates, but this is not due to laziness or lack of information.
A psychological phenomenon called planning fallacy is the main culprit.
It was first described in 1979 by Daniel Kahneman and Amos Tversky, and the main premise is that people look optimistically at the time needed to complete a task and often provide shorter estimates than what the task requires in reality.
Interestingly, in their study,even when they repeated the task, people still gave much shorter estimates than the actual ones.
So, what does this mean for construction projects? Are you doomed to break schedules repeatedly?
Well, not really. Good project managers will know that different things impact project schedules and deadlines, so they’ll include buffers or floats into their time estimations.
Buffer or float time is spare time for a construction activity that doesn’t impact the final project timeline or other connecting activities.
For example, let’s say you have tasks A, B, and C with time estimations of 4, 7, and 5 days, where tasks A and B can be completed simultaneously, but task C can start after task B is finished.
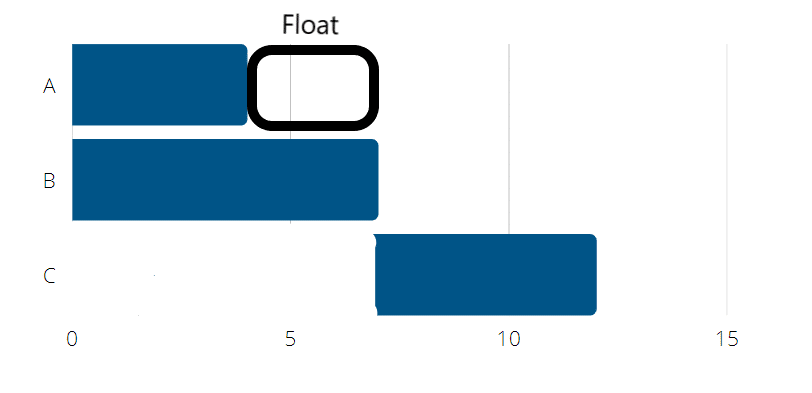
In this scenario, task A can be completed in 4 days, which is less than the 7 days it takes to do task B. Therefore, task A can be delayed by three days and not affect task C or B.
Then, we can say that task A has a float of three days.
Now, the main question is, how much buffer do you add to the project timeline or each activity?
Eli Goldratt presented a solution in his book Critical Chain (1997). According to him, you’ll need a 200% buffer period for every task with a specific time constraint.
Or in other words, if a task demands one week for completion, add two more weeks to that estimate.
The key thing is to cut that buffer in half, where you’ll allocate a week and a half to the original task.
Then the rest is shifted to the end of the project to account for any major problems and delays.
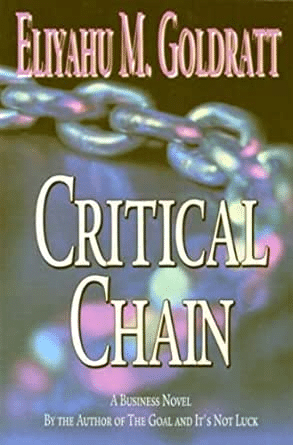
In the end, you get enough time to complete the task on time (or even faster) and allow for additional time to sustain unexpected problems at the end.
Remember that overseeing construction schedules isn’t easy, so you need to account for additional time to complete tasks so your project can progress according to schedule.
Neglecting to Document the Project
Another mistake contractors often make is not documenting their project schedules.
Of course, you’ll create the initial schedule, but if you’re not documenting changes throughout the project life cycle, you’ll inevitably break the project deadline.
Luckily, taking notes and tracking schedule changes can be done faster, more efficiently, and accurately.
You can shift all of your project-related documents and reports to a cloud-based system that will keep everyone in the loop.
What’s more, accurately documenting delays and problems will help you prove what actually happened and the core cause of project delays during disputes.
So, a great asset in keeping careful documentation for the construction project is construction software.
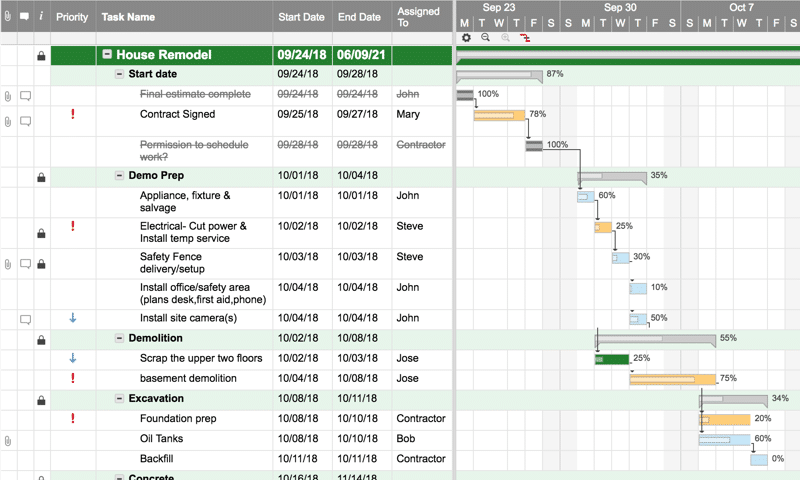
A well-organized and integrated system will follow you in all stages of the construction project, so you’ll have consistent references to fall back on to make important decisions and prevent delays.
Maintaining proper paperwork is necessary to organize a successful project, but most importantly, it can severely impact timely project completion.
So, your best solution is to invest in construction software that will update and manage project documentation.
Not Accounting for Weather Constraints
The weather is one of the key factors that impact a project’s schedule and timely delivery.
One rainy day often means the postponement of critical tasks, which can snowball into other jobs not being done on time.
Or in other words, cranes will not operate in windy conditions, nor can exterior painters do their job if it’s snowing.
But even when you’re working in areas with more sunny days than average, like Las Vegas, Nevada (294 sunny days per year), you’ll have to consider other elements such as temperatures that can reach 41°C in the summer months.
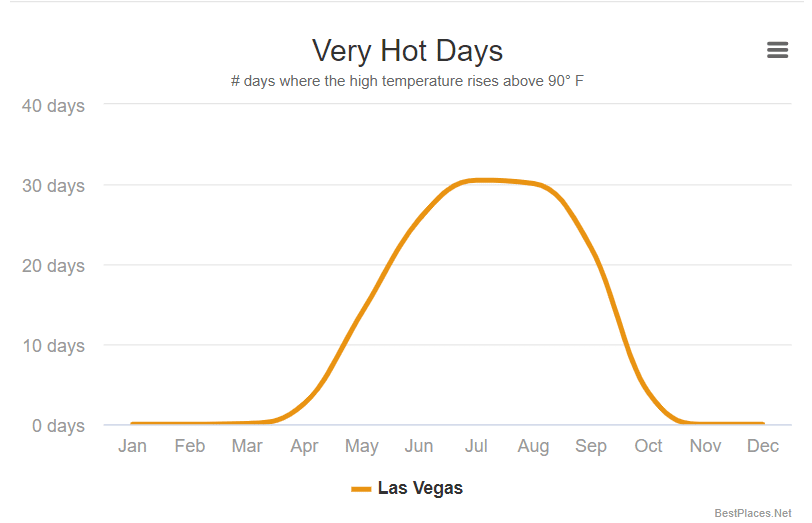
Obviously, you can’t predict extreme weather conditions like hurricanes, tornadoes, or snowstorms, but average seasonal weather is more predictable.
Each region has its normal precipitation, humidity, and temperature averages you can work around and plan your project.
Monitoring weather conditions daily is necessary once the construction begins, but planning for weather conditions has to begin before the shovel hits the ground.
But if you think that you can’t plan several months ahead for the weather, the latest research will make you change your mind.
Researchers at University of Reading (UOR) have looked into historical data for 102 weather stations across the UK.
Their main goal was to collect weather data in various regions and develop a sine wave model to calculate workable days for particular construction activity in those regions.
So, for example, here is a sine wave model for painting outdoors in Brize Norton over the course of a year.
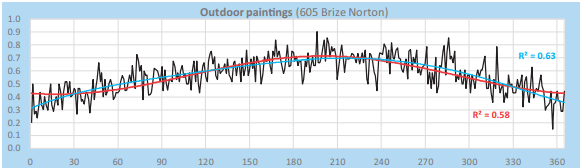
From this model, you can see that there are more productive days in the middle of the year, approximately from April to September.
At this time of year, there is less precipitation and higher temperatures which are ideal conditions for outdoor painting.
So, based on this data, you can coordinate and schedule construction activities that can be finished faster due to more ideal weather conditions.
This means you can have a quicker turnaround on projects and squeeze in more jobs, thus gaining more profits while staying on schedule on multiple projects.
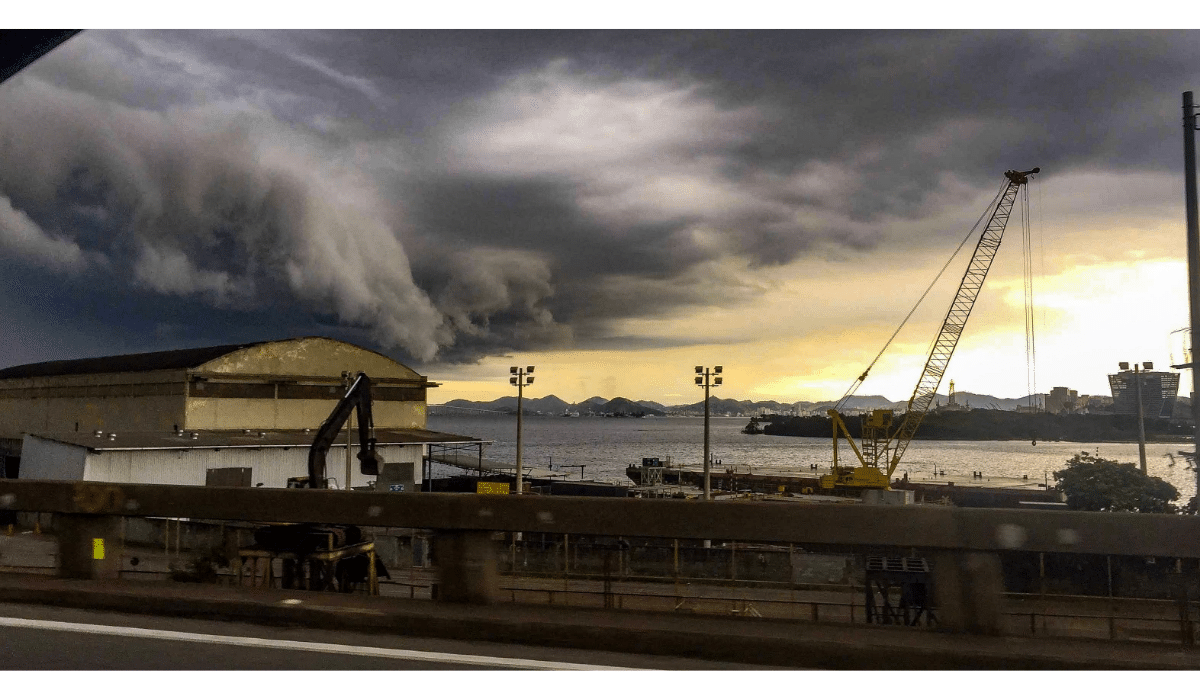
Furthermore, the findings in the UOR study showed that weather delays extended projects by 21%, but with proper planning and taking into account these delays, construction companies can reduce the average project timeline by 16%.
It is true that the weather conditions and patterns are somewhat skewed because of climate change, but you should still keep those trends in mind if you want to finish your projects on time.
Overpromising Due to Client Pressure
Everyone loves happy clients. Actually, every business strives to create happy clients because they can bring more work to the company.
So, it’s not uncommon that construction companies often promise their clients things they can’t do to keep their loyalty.
Construction lawyer Bill Barton, Director of Barton Legal, often sees the problem of overpromising and underdelivering in handling disputes in construction.
According to him, everything is perfect at the beginning, but poor communication with clients brings up unexpected problems, and expectations aren’t met.
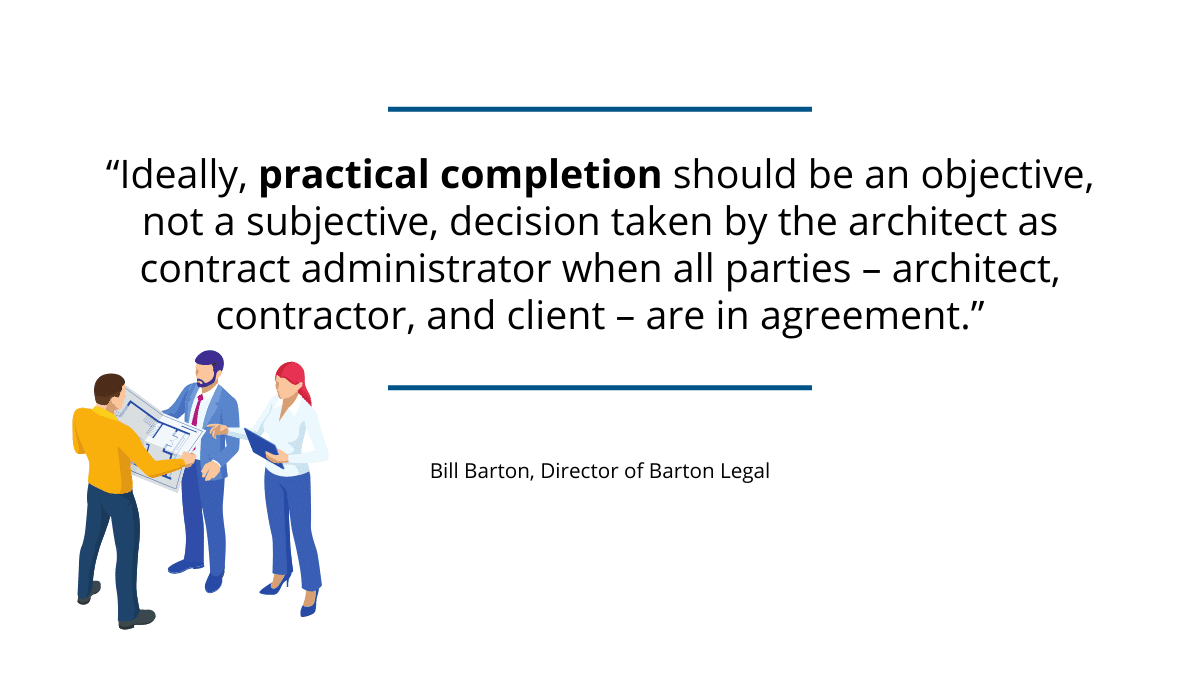
His advice is to talk to the clients from the very beginning and discuss practical completion.
If a client wants to push for early completion, but the contractor can’t deliver on it, it needs to be communicated at the start.
That way, you manage expectations and mitigate problems that might arise from additional pressure to finish a project when the client wants it.
Yet, the construction companies are still trying to fit customers’ dates into unachievable schedules.
Over the years, some contractors have experienced the pressure to do three months’ work in under a month.
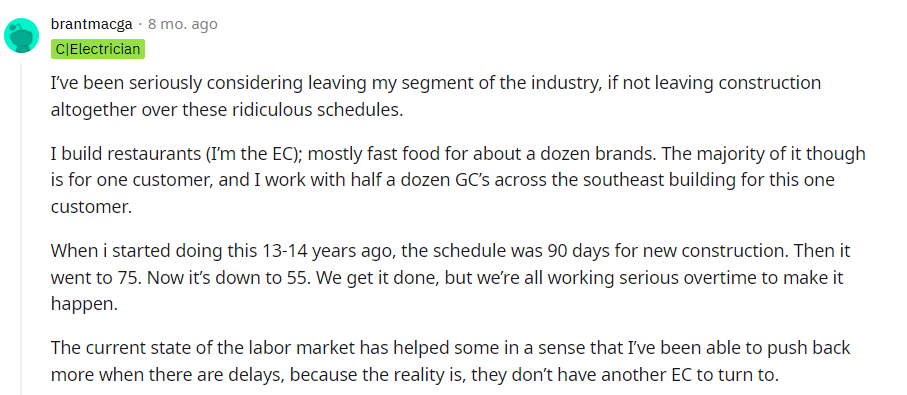
In the race to get the job, decision makers often promise clients results in unrealistic time frames.
But the additional work often falls on the shoulders of the field workers.
What happens next is that they end up cutting corners and rushing to satisfy the bosses and the client, which results in bad quality projects and damaged reputations (but it was finished on time!).
Still, if you continually try to please clients with unrealistic project completion dates, you’ll risk losing your workers, paying damages for a poor quality job, and ruining your reputation.
Clients hired you to do a good job, and if that means you’ll need two weeks instead of five days, you must tell them on time, so they don’t argue and refuse to pay once the deadline is ‘’extended’’.
Conclusion
The key to avoiding project scheduling mistakes is understanding the root problems and mitigating them before the project begins.
Sometimes delays are caused by unrealistic resource projections, additional waiting times, weather conditions, or too short project timelines.
The most important thing is setting a realistic timeline and accounting for external and internal factors that can cause extensions.
That way, you can set protocols to fix major issues and finish projects on time.