Ensuring that your machinery functions at its best requires more than just periodic check-ups; it demands a comprehensive maintenance tracking system.
From heavy machinery to safety equipment, each of your assets needs your full attention in order to prevent breakdowns, minimize downtime, and extend their lifespans.
That’s why, in this article, we delve into the topic of equipment maintenance tracking, exploring the best practices that you can adopt to streamline your maintenance processes and, in turn, enhance your equipment’s longevity.
Let’s dive in.
In this article...
Establish a Centralized Maintenance Log
The first step towards successful maintenance tracking involves setting up a centralized log that consolidates maintenance data for all your equipment in one, easily accessible place.
Instead of having to sort through numerous Excel sheets or paperwork to determine when a particular machine was last inspected, this gives you a complete view of your assets’ upkeep history with just a few clicks of the mouse (or taps on the phone screen).
Details concerning past servicing, inspections, OEM manuals, current conditions, warranty information, and more, become much more readily available, accessible, and most importantly, accurate.
No more duplicate records. No more missing data. No more errors.
But this isn’t only about convenience. Data centralization also helps with faster problem detection.
With all this information in front of you, you become much better equipped to identify patterns and trends, which, in turn, allows you to intervene on time and address existing or potential issues before they escalate.
It’s also about accountability, says George MacIntyre, product manager at CNH Industrial:
“[Record-keeping] helps ensure that all preventive maintenance activities are done in the timeframe they are meant to be done and that the machine will continue to work as intended.”
Having such complete data visibility allows you to verify whether or not your team is on top of their maintenance responsibilities.
To centralize the data, you can use either specialized maintenance tracking software or more comprehensive equipment management solutions like our GoCodes Asset Tracking.
GoCodes Asset Tracking, a QR code-based system equipped with GPS location monitoring and a host of other useful features, provides a consolidated database containing all relevant machine information, including previous repairs, status, condition, user, and more.
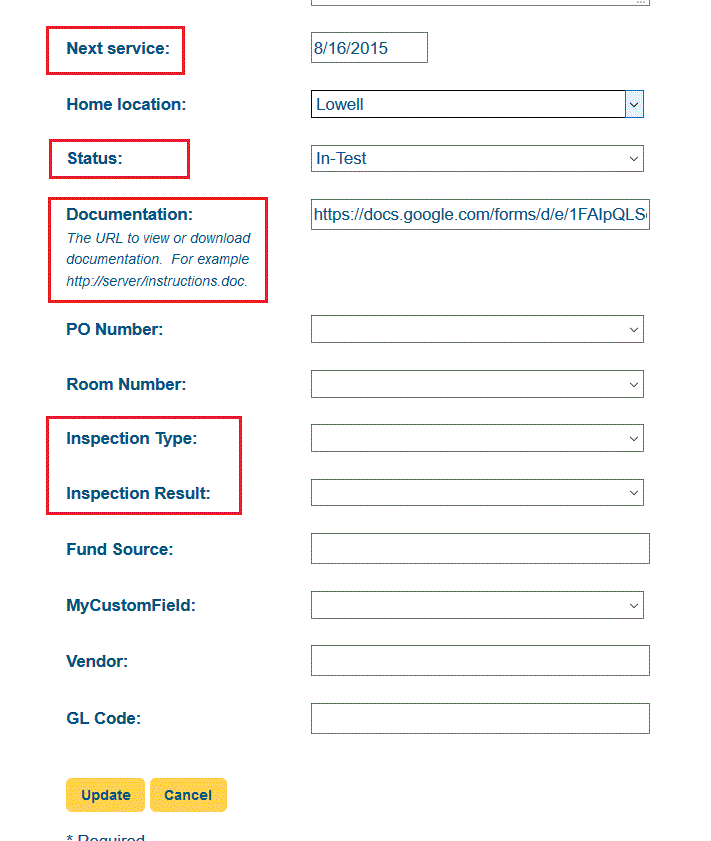
Updating and accessing this data with our system is remarkably easy—simply use the GoCodes Asset Tracking scanner app to scan the QR code label affixed to your equipment, and you’ll instantly have a thorough overview of the asset’s service history and other important details.
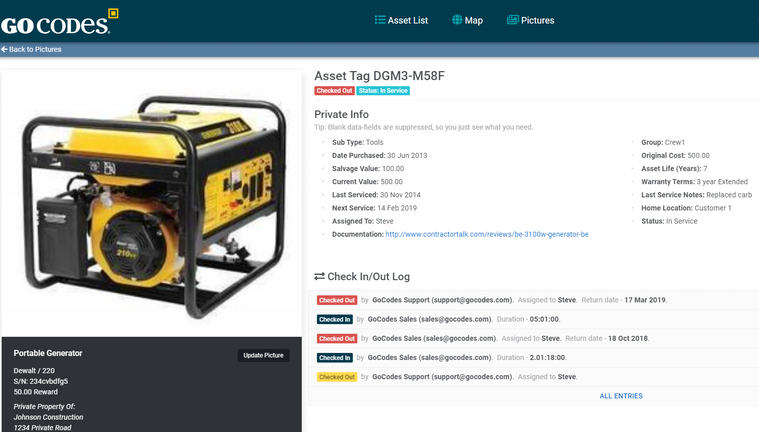
Ultimately, you can’t really properly track your maintenance activities without a unified record-keeping system.
It ensures your data is accurate, reliable, and available when needed, thus helping you take your maintenance planning to the next level.
Use Unique Equipment Identification
Each piece of equipment has its own distinct maintenance history and requirements, so it’s vital to differentiate between them within your system, especially if you have multiple instances of the same item.
Now, while serial numbers commonly serve as tracking IDs in equipment management, you should know that they aren’t completely unique.
Sure, they may be exclusive to assets of a specific type from a particular manufacturer, but there’s no guarantee of uniqueness among assets of different types from various manufacturers.
Not to mention that serial number uniqueness is even further compromised when machinery is exchanged among suppliers or business partners.
Using a self-assigned tracking ID proves to be a much more effective solution in this case.
Remember, without these unique identifiers, the quality of your maintenance data becomes significantly jeopardized.
For example, having two machines with identical serial numbers could lead the system to recognize them as a single item, resulting in updates for each asset being recorded under one entry.
Needless to say, this would be a serious problem in the long run, causing poor maintenance for both assets and potentially shortening their lifespan down the line.
When you use dedicated asset management software, such problems are typically taken care of by the system.
For instance, QR code-based systems come with asset labels already linked with a globally unique, randomized code specific to each piece of equipment.
That way, the possibility of duplicate IDs is entirely eliminated, even when managing thousands of machines.
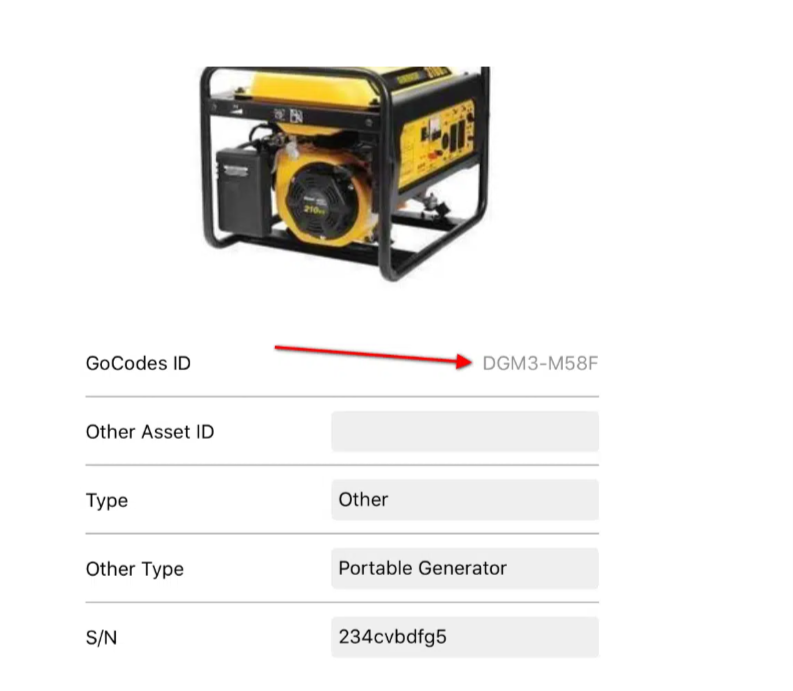
All in all, when it comes to ensuring the accuracy of your maintenance records, it’s best to steer clear of serial numbers.
Due to their lack of complete uniqueness, they can introduce numerous issues with record-keeping, ultimately undermining the efficiency of the entire maintenance process within the company.
Make Equipment Issue Reporting Easy
If an issue with a machine arises, it’s only natural you’d want it to be reported as quickly as possible.
After all, the sooner a problem is identified, the quicker it can be resolved.
Besides, timely reporting ensures the team is promptly informed of the equipment’s unavailability, enabling them to find alternative solutions on time.
This helps bypass unnecessary, and often quite costly, downtime.
And if you’re curious about the potential financial impact of these inefficient processes that slow down operations, take a look at the research conducted by Siemens on downtime costs in the manufacturing industry.
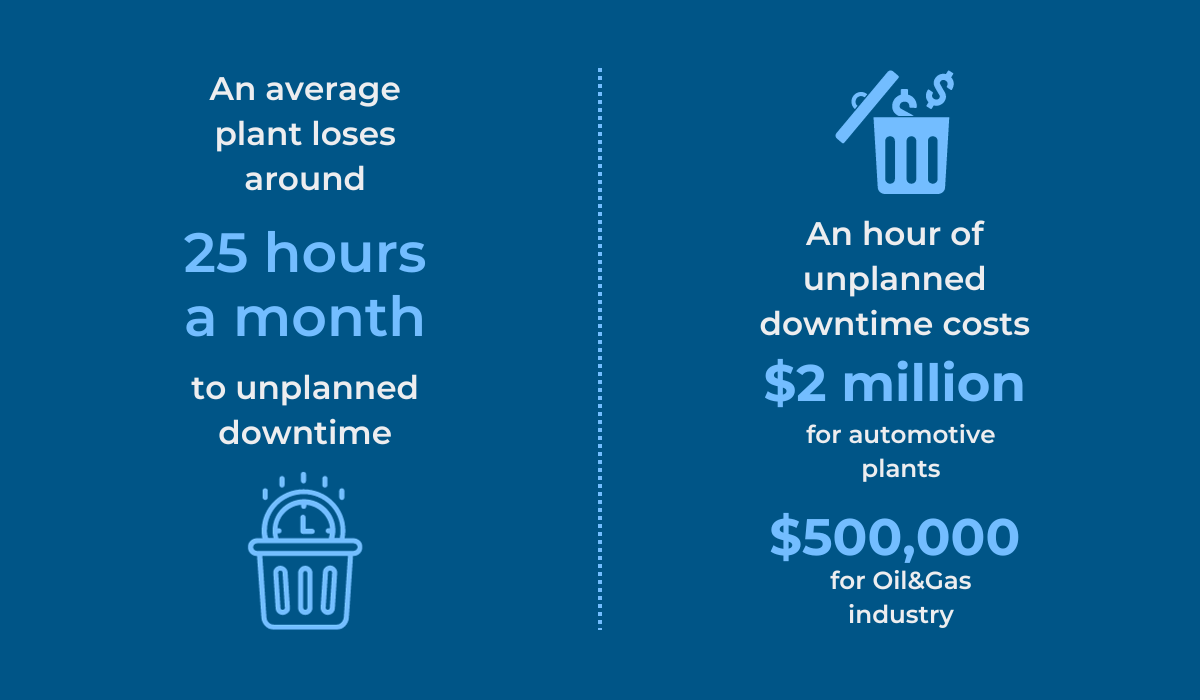
As you probably already know, construction faces similar risks, with a single machine failure potentially triggering a cascade of workflow disruptions, delays, and additional expenses.
That’s why it’s important to communicate issues promptly.
Maybe it won’t stop machine failure altogether, but it will definitely help resolve the problem much faster.
So, how do you step up your issue-reporting game?
The answer is, once again, technology.
Equipment management software is quite effective in facilitating communication between team members and thus makes it much easier to report any problems.
Take GoCodes Asset Tracking’ automated field service requests, for example.
This feature enables users to call for equipment service or inspection wherever they are, with minimal effort required.
All they need to do is scan the QR code asset label using our app, enter relevant data, and submit their request.
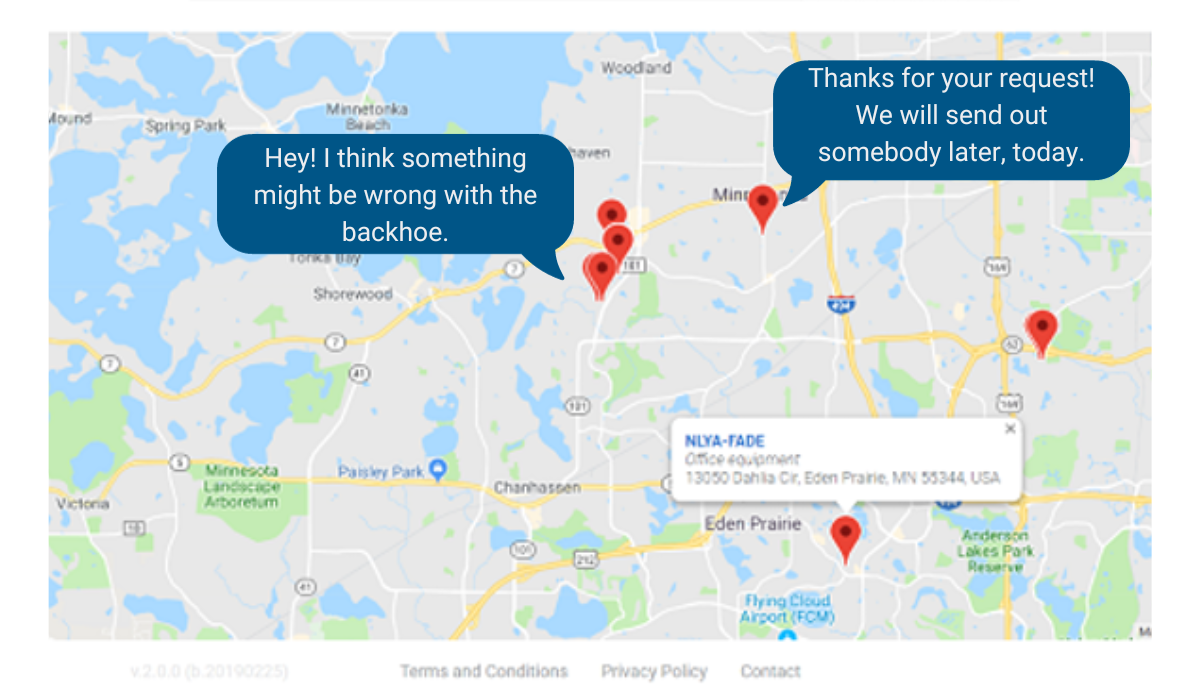
Maintenance personnel will immediately receive an email notification containing essential details, including the requester’s name, date, location, and problem description.
Moreover, through that very same scanning process, users can also update the status of a broken machine for all to see, keeping everybody well-informed about each asset’s availability.
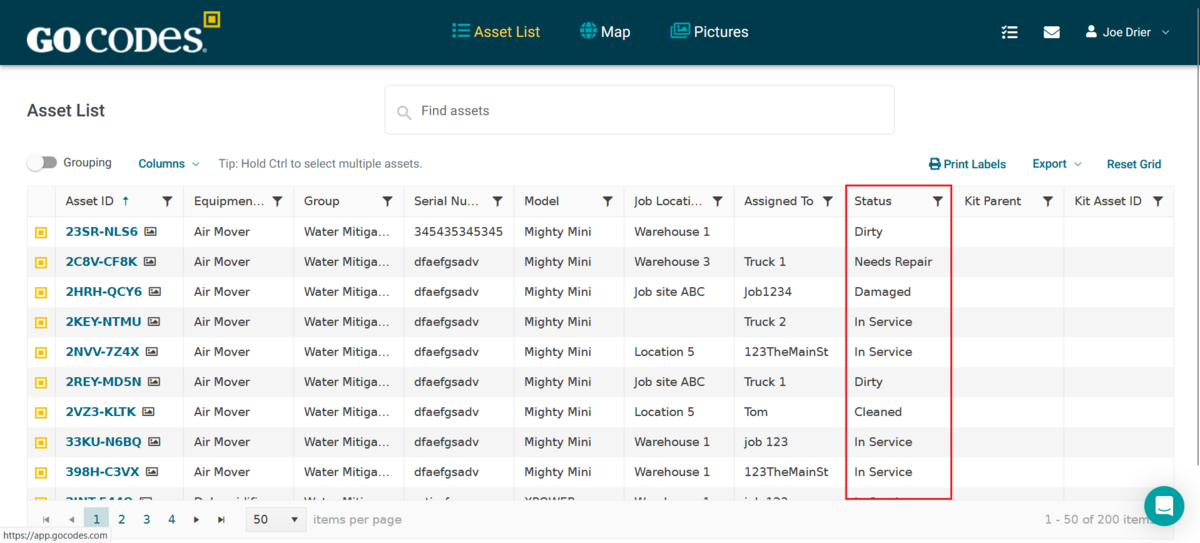
Let’s face it, cumbersome and disorganized issue-reporting processes only add unnecessary burden to everyone on the team.
They not only cost both time and money but also disrupt the maintenance workflow.
So, if you feel like this area needs some improvement within your company as well, look into equipment management systems with automated issue-reporting capabilities.
They can be a real game-changer for your overall operational efficiency.
Implement Regular Inspection Procedures
To ensure your valuable assets stay operable for as long as possible, you should make sure to inspect your equipment thoroughly and on a regular basis.
By doing so, you can proactively detect potential issues and fix them before they escalate into a major failure or become a significant safety risk.
In fact, did you know that research shows that such preventive measures can cut down equipment defects by up to almost 80%?
On top of that, they simultaneously reduce unplanned downtime by more than 50%.
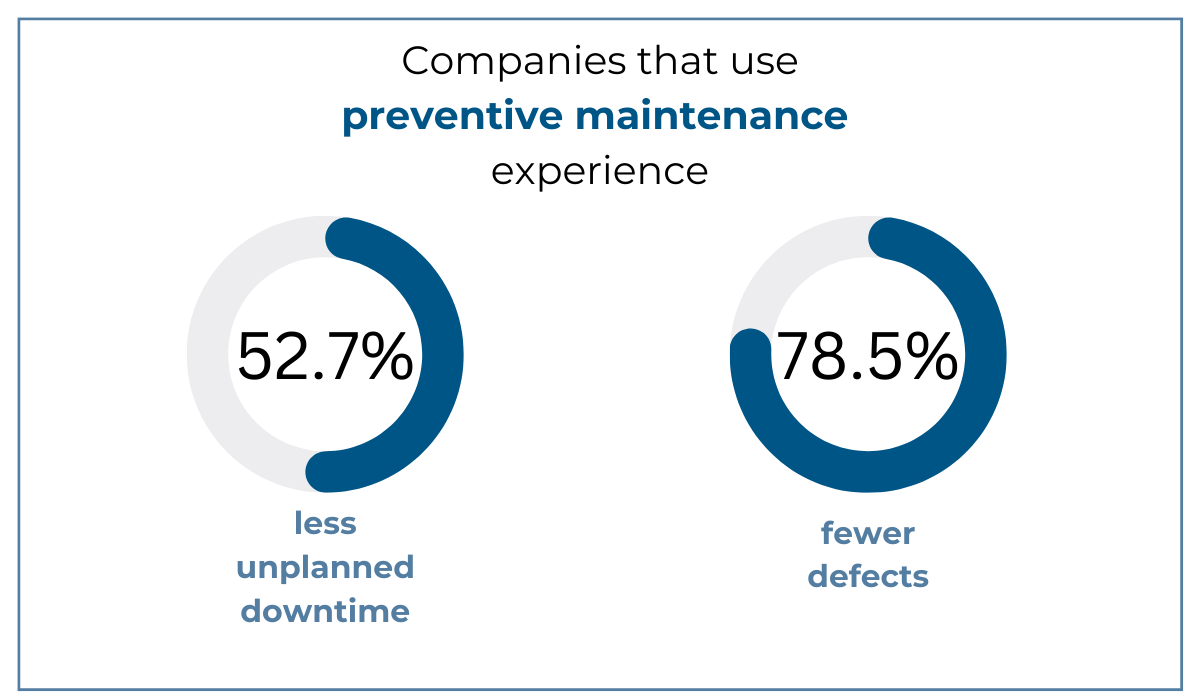
To make the most out of your inspections, be sure to establish a consistent, standardized routine to help everyone stay on track with their upkeep responsibilities.
How do you do that?
With maintenance checklists.
They give structure to the whole process, ensuring it’s done the same way every single time, by every employee, and that no detail goes overlooked.
Simply put, they make the inspections much more efficient.
So, to create an effective checklist, consider adhering to the following steps:
- Identify equipment requiring maintenance to determine the checklist’s scope.
- Determine maintenance tasks for each equipment type based on manufacturer recommendations, industry standards, and operational requirements.
- Establish the frequency for each maintenance task.
- Assign tasks to specific employees or teams.
- Develop a clear, concise, and user-friendly checklist format.
- Pilot-test the checklist and ask for feedback to refine its effectiveness.
- Regularly review and update the checklist to accommodate your evolving needs and insights.
And if you’d like to delve even deeper into the world of efficient equipment inspections, check out our detailed guide on preventive maintenance checklists.
At the end of the day, there’s no denying that investing time and effort in equipment inspections directly translates to extended equipment lifespan, increased asset value, and enhanced operational efficiency.
That’s precisely why it’s so important to establish a system that’ll support this process by making it quicker, more structured, and simpler for everyone.
Document Maintenance History
A meticulous record of maintenance history provides a complete overview of the type of service conducted, the equipment involved, the responsible individuals, and the timing of each maintenance activity for every asset over time.
Having such a detailed maintenance log can be invaluable, as it empowers you to assess the current condition of your assets more accurately and to pinpoint any recurring issues with specific machines.
This, in turn, helps to:
- devise future maintenance strategies,
- optimize equipment lifecycle management, and
- determine whether an asset should be replaced or repaired.
Say your long-serving excavator suddenly breaks down.
Knowing you’ve had it for a while, you start wondering if it might be time to finally replace the machine.
With its maintenance history in front of you, you see that the excavator has been experiencing increasingly frequent breakdowns accompanied by escalating repair costs.
Adhering to the 50% rule, which stipulates replacement when repair costs exceed half the expense of a new machine, you opt to procure a new one.
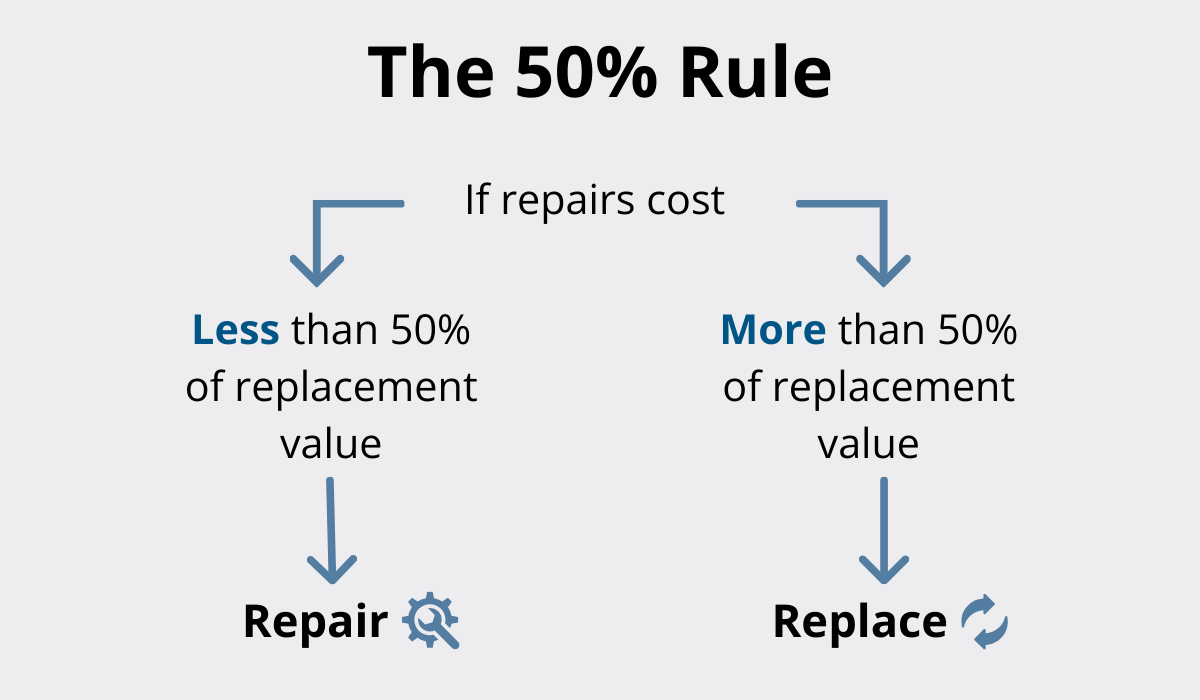
But, if you didn’t have access to this cold, hard, historical data, you might’ve been inclined to make decisions based on emotions, potentially prolonging the use of the machine.
However, this would only lead to more unexpected failures, more workflow disruptions, and, naturally, more delays and stress for the entire team.
Tyler Smith, product manager at Volvo Construction Equipment, summarized the reason why maintenance history is so important:
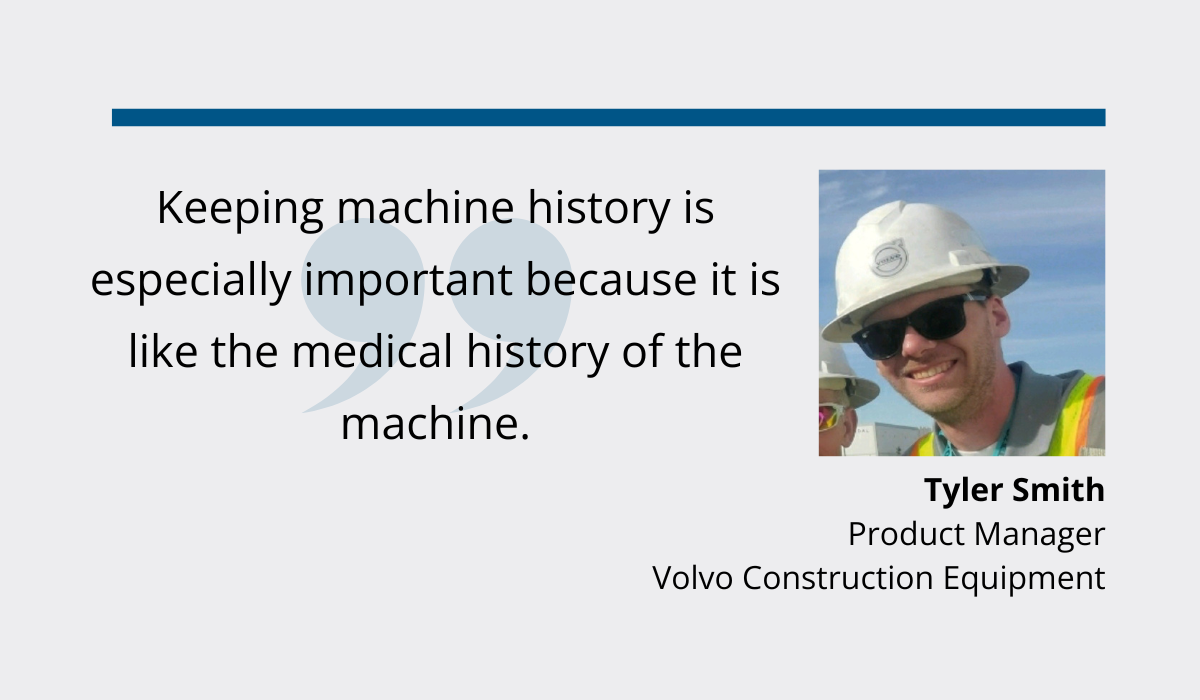
According to him, it’s the key to pinpointing—and therefore fixing—potential future problems with your machinery.
Now, to ensure the accuracy of your maintenance history log, it’s essential to conduct periodic records audits.
This involves verifying dates, times, and descriptions of performed work and cross-referencing this information with other relevant documents such as work orders, inspection reports, and equipment manuals.
By doing so, you guarantee the reliability, consistency, and regulatory compliance of the recorded data, thereby enhancing your decision-making concerning maintenance strategy optimization and asset lifecycle management.
Conclusion
There’s no doubt that efficient maintenance tracking can sometimes be quite challenging, especially if you have numerous assets to manage.
But the hard work pays off.
Remember, the goal here isn’t to monitor maintenance activities just for the sake of it.
Rather, the goal is to use that valuable data to make informed decisions, optimize maintenance processes, and ultimately increase the overall efficiency and profitability of the business.
So give some of these tips a chance.
They’re sure to help you ensure your equipment remains in peak condition, delivering reliable performance and maximizing return on investment for years to come.