The global asset tracking market will reach a staggering $36.3 billion in four years, which reflects its importance to many industries, including construction.
This shows that businesses clearly need ways to track their belongings easily and accurately, so chances are you’re probably already tracking your equipment and tools in some way. The real question is whether it’s time for you to automate this task.
This article will explain how you can benefit from switching to automated asset tracking so you can make an informed decision to help your business prosper.
In this article...
You Can Track More Information
Choose to automate your asset tracking, and you’ll be able to keep up with more information about your tools and equipment at once.
Here are some details you can easily track with an automated system:
- Asset description
- Images of the asset
- Current and past users
- The condition of the asset
- Past maintenance records
- Maintenance schedule
Any of your workers who need to find specific information can get it in a couple of clicks instead of contacting other team members for help or going to the office to gain access to the data.
This level of insight will make everyone more productive, as automation eliminates the need to enter all the relevant data manually. Otherwise, you’d have to track this data manually for each piece of data you’re looking into, which would take time.
PlanGrid’s extensive construction industry report notes that 17% of people who spent more time than expected on a particular task did so because they had trouble locating the information they needed about it.
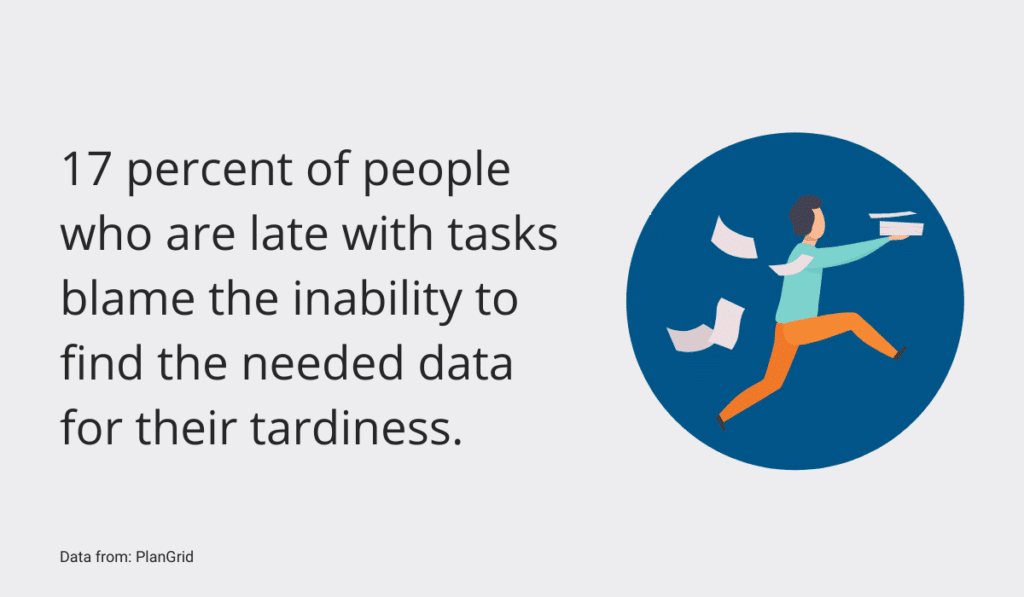
The search took a lot of time and delayed their work. Something like this can’t happen if you use software to store all the asset data.
Besides storing the information, asset tracking software also ensures the information gets updated in a couple of clicks, so it saves you even more time.
The best part of using such a solution is that you can share access with your entire team.
Let’s say one of your machines malfunctions at the worksite. With asset tracking software, a field worker can update the equipment’s condition in a matter of minutes.
Your maintenance team will then see the change in real time and react to it as soon as possible, minimizing downtime and, therefore, increasing your overall productivity.
Automation Eliminates Human Error and Inaccuracies
A great benefit of automation is that it minimizes human error.
If you use spreadsheets to track your assets, you risk not being able to keep up with all of the changes to your tools and equipment, and being overwhelmed leads to mistakes.
That’s why it’s no surprise that almost 90% of spreadsheets contain at least one error.
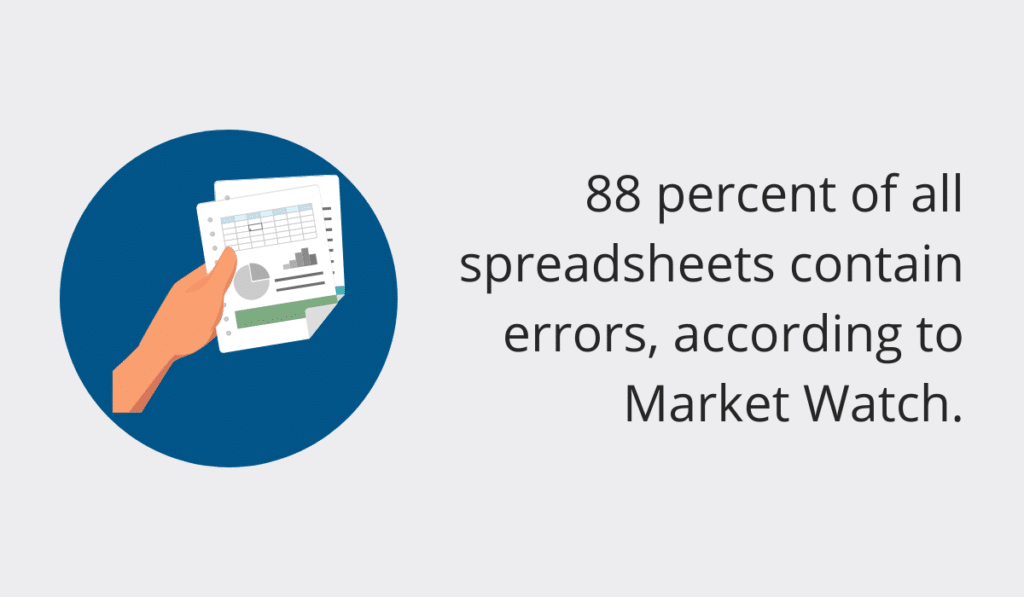
That’s because whenever something changes, you have to adjust the information in the spreadsheet manually.
If you forget to save your work, it will be lost, your information will be inaccurate, and it will be super difficult to track down the source of the error.
Besides, it’s relatively easy to override someone else’s changes or create a copy of the spreadsheet, creating two files that contain different information, which will result in even more confusion.
PlanGrid’s report touched on this topic as well, noting that 19% of employees who finished a task late blamed the delay on the lack of confidence in the accuracy of the available information.
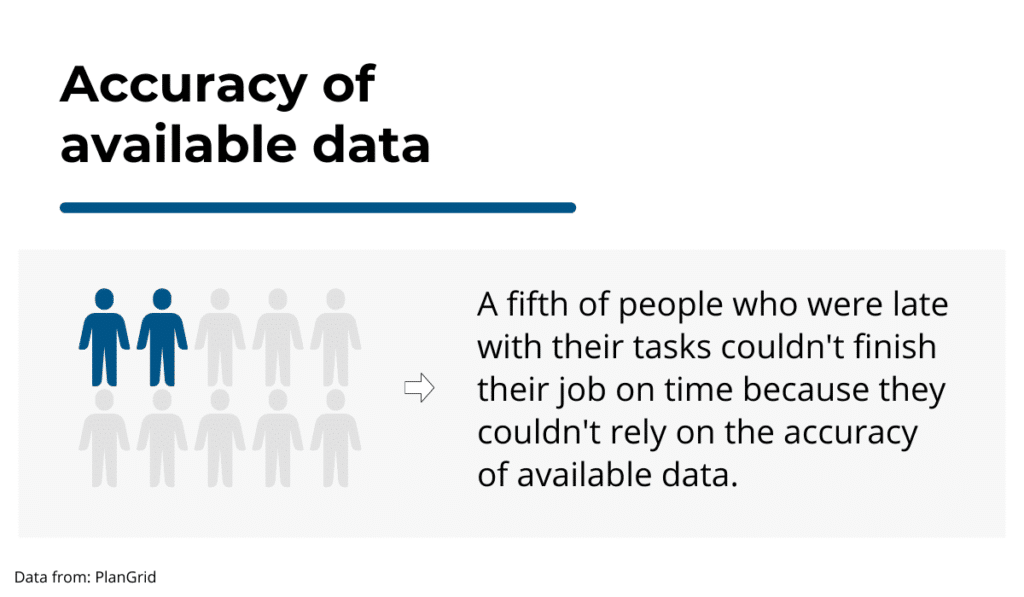
All these workers simply don’t trust that the data they have access to is accurate. However, this is something you can change if you choose to automate your asset tracking.
Using software to track your assets will help you minimize human error, consequently increasing data accuracy.
The Reliability of Scheduling Asset Maintenance Increases
With automated asset tracking, it’s also easy to set up and follow an equipment maintenance schedule.
An automated solution lets you schedule a servicing session in advance, based on factors like the item’s age and current condition.
Then, your maintenance team performs a detailed check of the equipment and fixes any issue they find. The only downside is that you have to invest in regular inspections, which some find burdensome.
In fact, a fifth of respondents of the aforementioned Plant Engineering survey said that their current maintenance program suffered because of poor scheduling, so they rarely ended up following through with it.
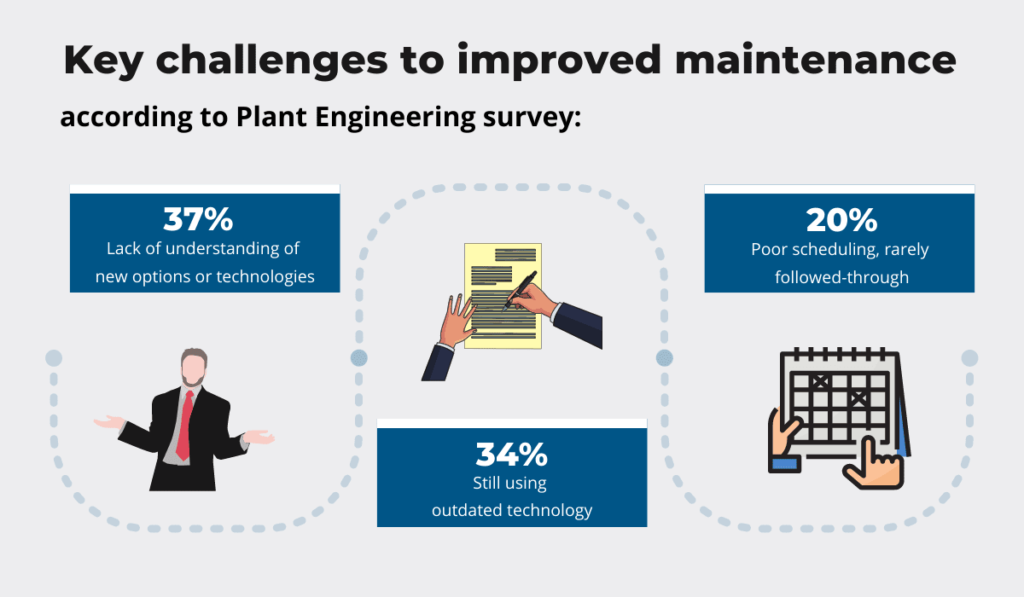
Another 34% reported still relying on old technology, which slowed them down. In comparison, 37% of respondents said their servicing suffered due to the lack of understanding of the new options and technologies.
Here’s the good news: asset tracking software is mobile-friendly and straightforward, which helps with all these issues. Because of this, most of the people on your team will have no trouble understanding and using such software.
The maintenance scheduling feature will make it impossible for you to miss a maintenance date since your administrators will get a notification when it’s time for doing upkeep, and the system will show the equipment as unavailable during service hours.
Inventory Audits Become Easier
Inventory audits are another thing that becomes less challenging when you use an automated asset tracking system.
We know that audits compel you to stay compliant while also helping you discover ghost assets. In that sense, audits also help you save money, so you need to conduct them regularly.
Since ghost assets are items that you no longer own but are still on your inventory, if you fail to eliminate them on time, you essentially end up wasting money on them.
Such items may have been lost, misplaced, or thrown away, but you’re still depreciating them, paying insurance, and investing in them, thinking they are an active part of your inventory.
Everyone thinks ghost assets don’t happen to them, but statistics show otherwise.
A survey has found that 65% of all asset data is incomplete, has errors, or is missing altogether. At the same time, 10-30% of fixed assets are ghost assets.
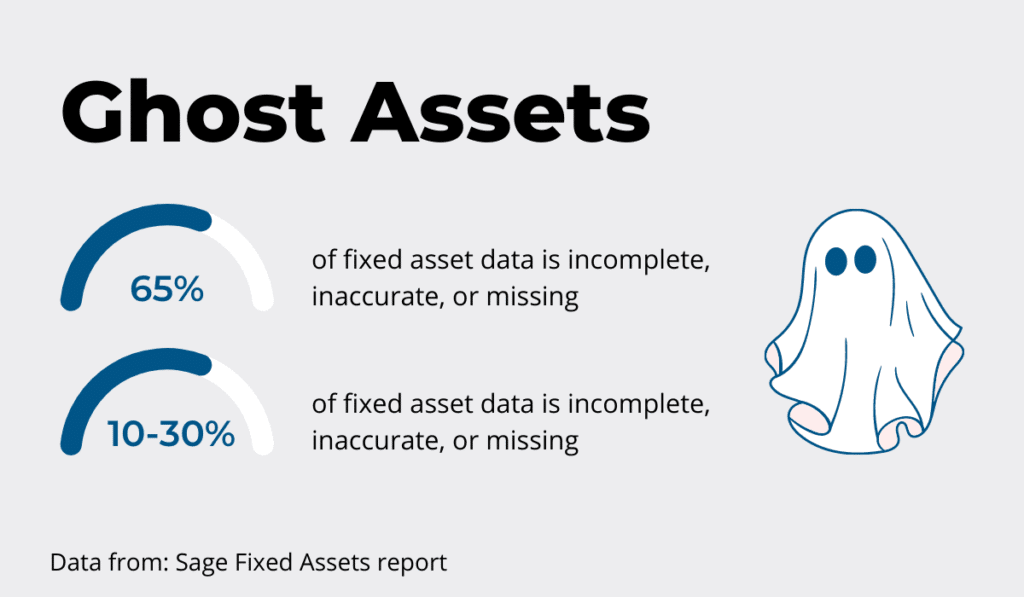
If you use automated software to track your assets, you can update your inventory in real time, avoiding all the manual work that could take hours. The same thing happens with your audits: you’re a lot quicker because most of the data is digital.
Adding new information or deleting an asset from your database is fairly easy when you can do it through an app, which updates everything promptly.
On top of all that, software like GoCodes Asset Tracking allows you to see your entire audit history, ensuring that you’re always up to date and have a clear overview of your business.
Consistency Is Easier to Achieve
If your goal is to have consistent and uniform processes, you should automate your asset tracking.
Think of it like this: workers come and go. Whenever a new person is hired and takes over a task, there is a chance they will change the way of doing things.
For example, when checking in and out the equipment on paper, each employee might use different wording for the same thing. Then, you might have different, confusing statuses like “in use”, “field use” or “taken” indicating the same thing.
Luckily, using software for asset management and tracking eliminates such discrepancies and creates uniformity and consistency across the company.
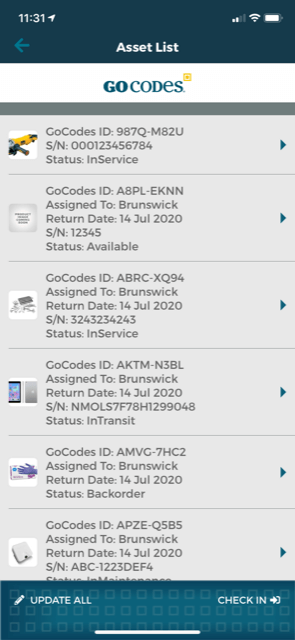
It often happens that when one detail changes, the whole process does too, along with the end results. However, when you automate an inventory management process, you ensure consistency no matter who is handling the procedure.
Real-time updates also play a part in information uniformity.
When a user updates information on the asset, you can rest assured that the data in the app always matches the current state of your fleet and that everyone has access to the same information.
Let’s take maintenance as an example.
Each maintenance specialist can place their focus on a different aspect of the equipment they are inspecting. If some fail to check a part of two, they are greatly risking the consistency but also the safety of your employees.
But if you create a maintenance checklist, upload it into your software, and append it to a piece of equipment, you can ask each service employee to follow it whenever they perform their regular checks.
That way, you’ll ensure that the quality of their work—as well as yours—remains consistent.
Staff Accountability Improves
With asset tracking software, you have an easy way to improve accountability: the check-in/check-out system.
Whenever a team member needs to borrow equipment or a tool, they use the app to change the asset’s status to in service. That way, the borrower’s name is linked to the asset until they return it.
Then, if one of your workers is late with returning the equipment, the software can send you a reminder so you can check in with them and see where the problem is. This way, nobody will fly under your radar.
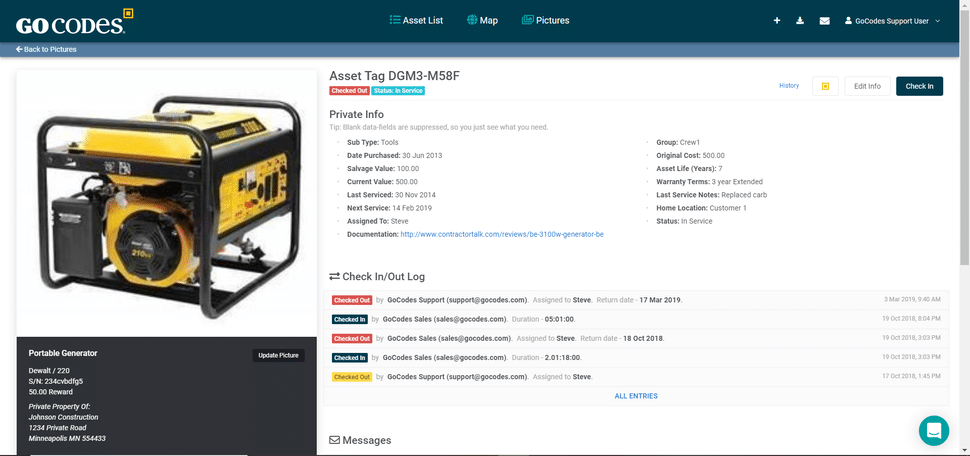
This level of transparency will also significantly reduce the chances of equipment theft.
Moreover, by checking the equipment out, the borrower lets everyone else know that the asset in question is unavailable, improving operational efficiency.
And why does that matter?
Well, when people are accountable for their work, they go above and beyond to achieve the desired results. However, this becomes possible only if you explain your expectations and how to achieve them.
Even workers themselves agree that accountability is a priority at work. According to a Partners in Leadership study, most people believe it’s important to hold others accountable.
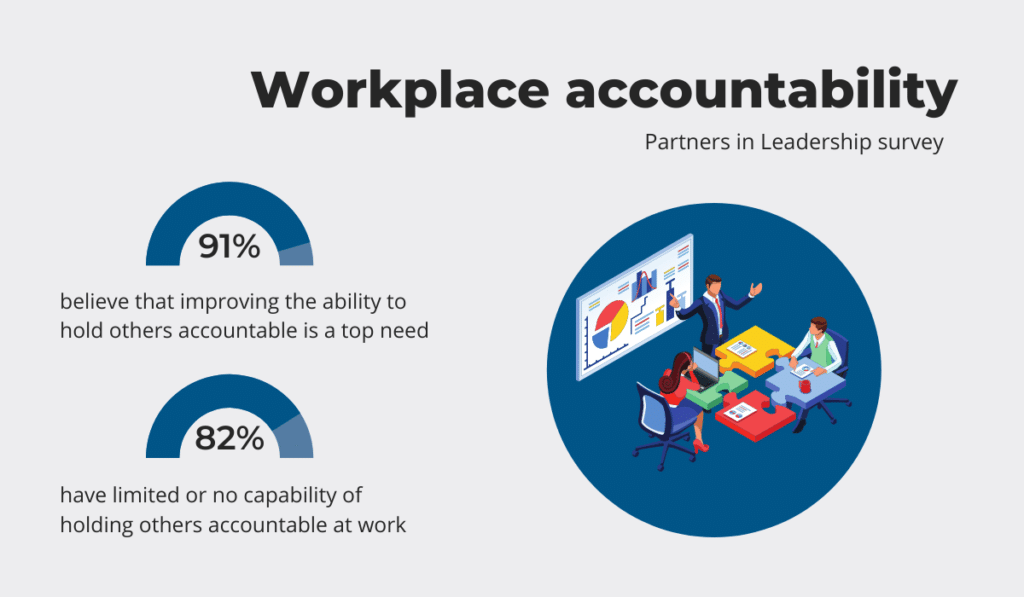
Interestingly, they also think this is something their company lacks and should prioritize.
At the same time, 82% of respondents admitted they have difficulty holding others accountable themselves and rated their ability to do so as limited or non-existent.
In sum, automating your equipment tracking promotes accountability among everyone handling it.
Workers Are Empowered
Easy access to information will empower your workforce, improving your company’s overall productivity.
Imagine you’re a field employee using a circular saw to finish today’s task when you realize there’s something wrong with the tool. There’s no supervisor around, and you can’t fix the machine yourself.
The only option you have is to drive back to the office to report the issue to the maintenance team, only to be informed that it will take a day or two to fix it, which means you’ll experience a two-day delay.
Think this scenario is an exaggeration? Think again.
PlanGrid’s survey that we’ve cited throughout this article has also touched on the topic of optimal and non-optimal activities. In other words, they have examined how much time your employees spend doing actual work.
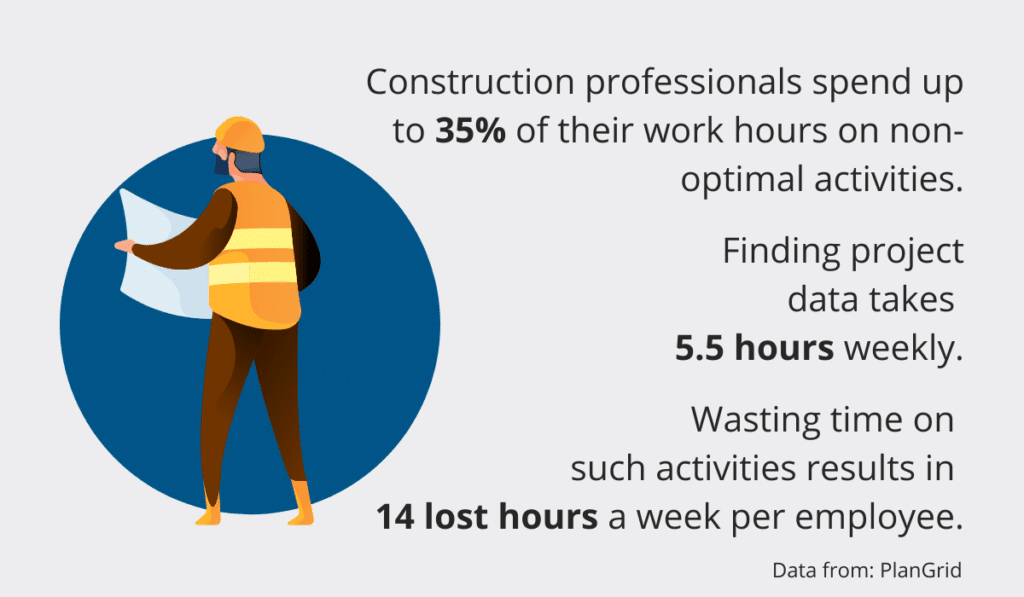
The results were surprising: people spend 35% of work hours or 14 hours a week on non-optimal activities. Out of these 14 hours, almost 40% are spent on locating project data.
Therefore, the scenario we’ve quoted at the beginning of this section is not as hypothetical as you may have thought.
However, the situation we’ve described could have gone differently had the employer given the worker access to tool tracking software.
This type of technology empowers employees through access to information as it lets your team be in the know at all times.
They can access maintenance records, user manuals, warranty and insurance information, or any other documents you choose to share in the app.
Nowadays, three-quarters of employers in the construction industry provide mobile devices to their managers and supervisors at the worksite to promote communication, according to PlanGrid.
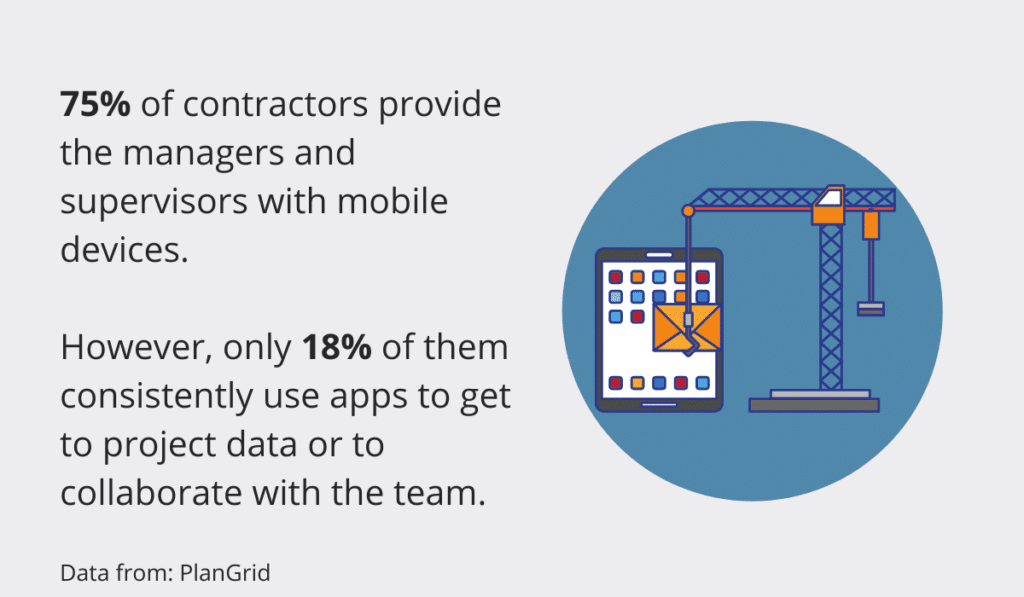
However, less than 20% of them consistently use these devices to find project data or communicate with the rest of the team. Therefore, a fifth of the people who have access to technology at the worksite aren’t using it to its full potential.
So, if you choose to use a tool tracking app, encourage your employees to install it on their phones and use it to quickly communicate with the rest of the team.
For example, equipped with a similar solution, the employee from the previous scenario could just scan the QR code on the saw and report the issue.
The maintenance team would see the change and add it to their schedule as soon as possible to minimize downtime.
Is It Time to Start Using an Asset Management System?
Most businesses nowadays track assets in some form or another, as only 11% of survey respondents claimed they don’t keep track of their assets at all.
However, 12% of these small businesses reported managing their assets manually, and 32% said they use spreadsheets for this task.
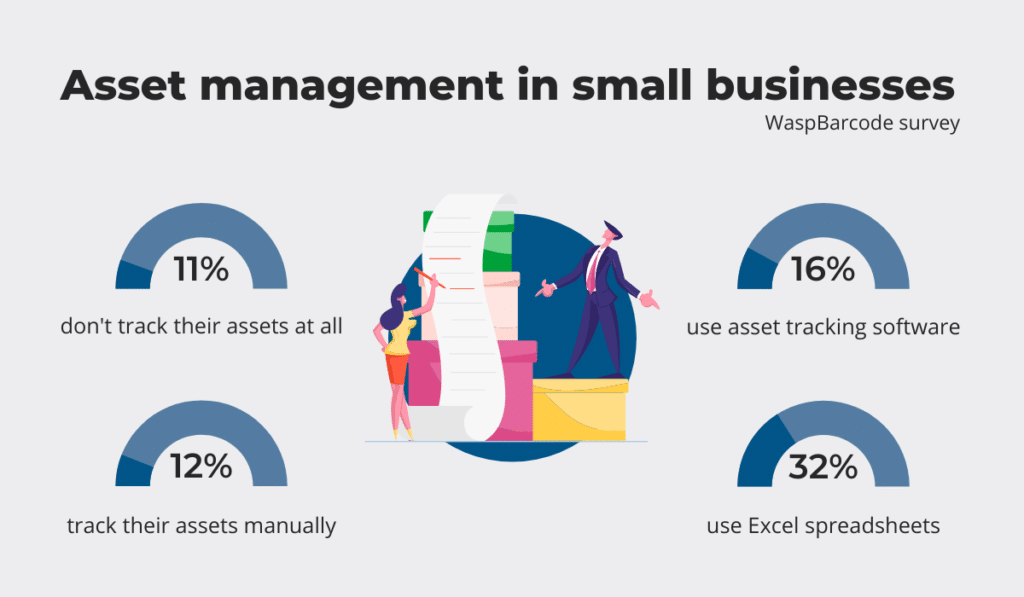
This means that more than half of small businesses don’t track their assets or do it manually.
On the other hand, only 16% of respondents use software, i.e., an automated tracking system for their assets.
Should you use it too? The answer is yes if any of the following apply to your business:
- You struggle to understand how many assets you own and where they are
- You have difficulty with staff accountability when it comes to your assets
- You skip or don’t even schedule maintenance sessions
- Your processes and tracking aren’t consistent
- Your audits last a long time, costing you time and money
- There’s no real communication between your teams
Asset tracking software like GoCodes Asset Tracking can help you solve all six issues at once. Here’s how!
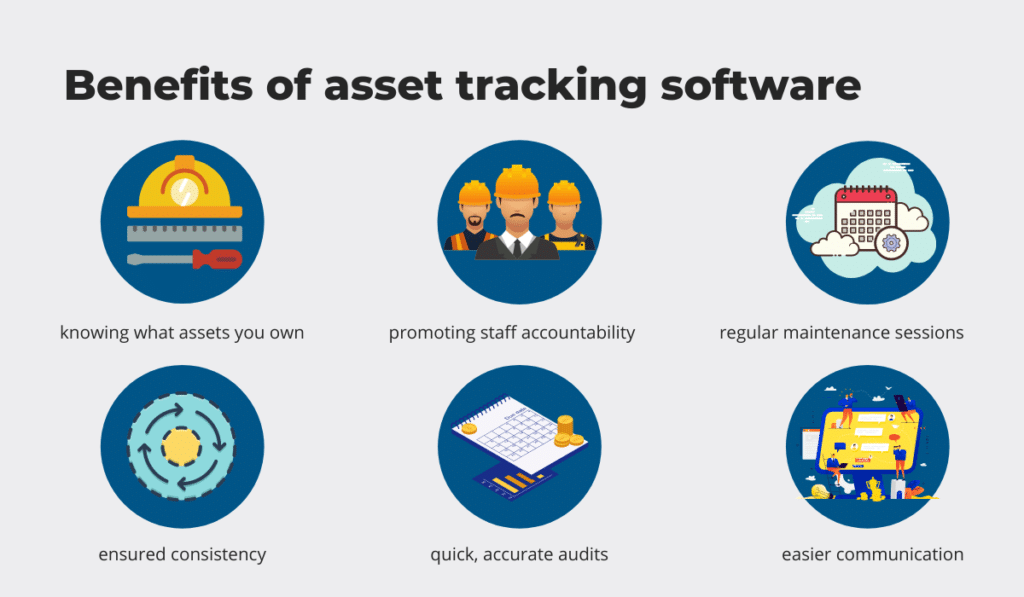
Firstly, to start using the software, you’ll have to create an inventory and add all your assets to the database. Whenever there’s a change in your inventory, you can mark it in the database in a couple of minutes, and so can your team.
You’ll ensure that you always know what you own and where it is, thanks to the check-in/-out feature, which, as mentioned earlier, promotes accountability among your staff as it directly connects them with the equipment or tools they are using.
The software also lets you schedule maintenance sessions and even sends you reminders, ensuring that you never skip a date.
Moreover, automation ensures that your processes can stay consistent. This is especially true for audits, where you strive to be quick but also accurate.
Finally, the option of leaving comments on the asset’s page or updating its status promotes communication between different teams which usually wouldn’t communicate, such as the field and maintenance staff.
Conclusion
Tracking your assets is crucial for any kind of business, no matter the industry. Still, it is particularly critical in construction, where companies own so many tools, equipment, and materials.
That’s why you should opt for automation. Instead of keeping track of all of your company belongings manually, let technology do it for you.
After all, choosing the right software can benefit you greatly and make your life a lot easier while saving you money and improving your productivity.
What are you waiting for?