Are you feeling overwhelmed by all the tool-tracking solutions on the market?
You’re not alone.
There are so many choices available, it can be hard to know where to start.
That’s exactly why we put together this ultimate guide for choosing the right tool-tracking software.
In it, we’ll walk you through all the must-haves and deal-breakers, so you can easily navigate the sea of software options and make a confident choice.
Let’s begin.
In this article...
What to Look For in a Tool Tracking Software
First, let’s get into some must-have features of efficient tool-tracking solutions.
Without these, put bluntly, you won’t get much out of your software.
Real-Time Tool Tracking
If you want to boost productivity across your job sites, choose a tool-tracking software with real-time monitoring capabilities.
Knowing where every tool is at any given moment is incredibly valuable as it can help cut down on asset loss and even theft.
As a result, operational disruptions are kept to a minimum and projects get finished right on schedule.
Not convinced real-time tracking could make a real difference in your operational efficiency?
Just ask Michael McGowan, Region Head and CEO of Hilti North America, a provider of construction technology, who knows exactly how much time is wasted each month searching for missing tools.
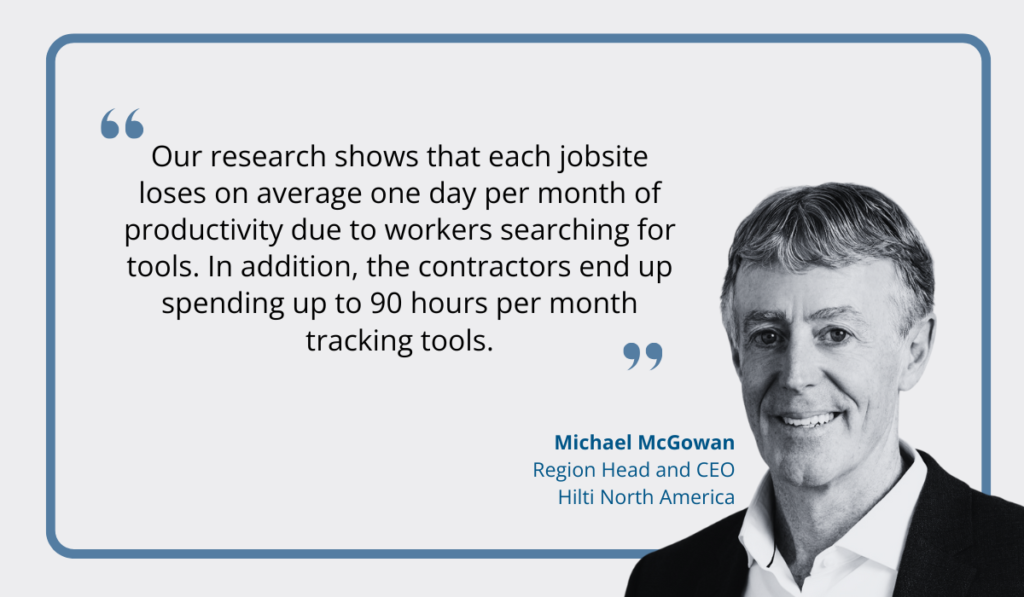
Real-time monitoring drastically reduces such inefficiencies, allowing workers to quickly locate the assets they need, whenever they need them.
And here’s the best part: many tool-tracking solutions offer more than just location data.
Take our own GoCodes software, for example.
It doesn’t only tell you where your tools are but also shows who’s using them, their condition, as well as their expected return date.
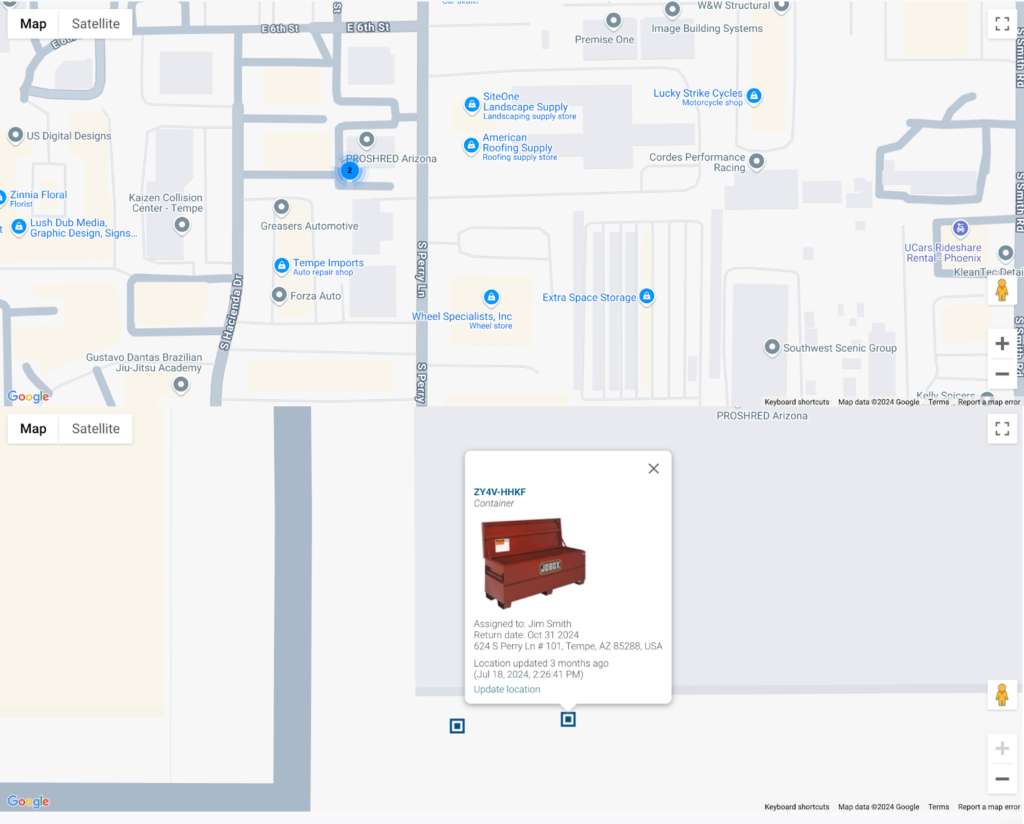
No confusion, no uncertainty—all the relevant information about your assets is right there in the system.
And it’s as fresh as it can possibly be.
Tool Check-In and Check-Out
A check-in/check-out system lets you see exactly who is using which tool for what project, and when they returned it, as shown in the example below.
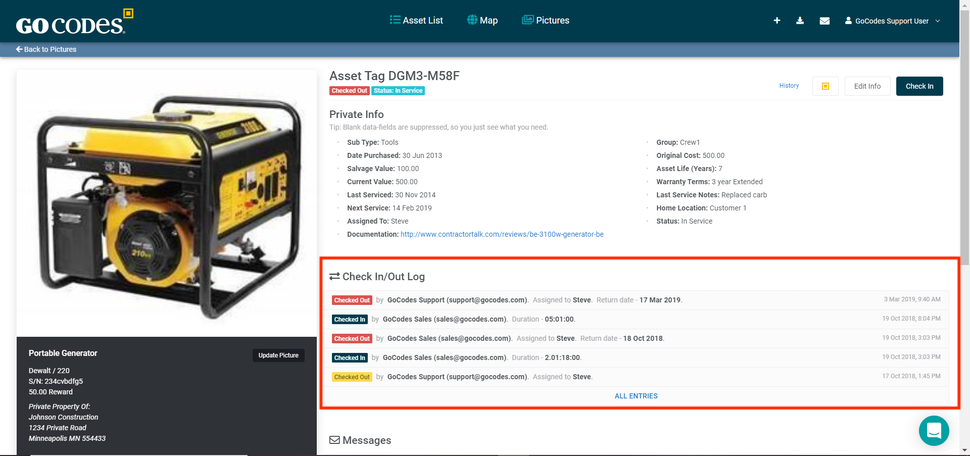
Such a feature is bound to add more transparency to everyone’s behavior, encouraging employees to take ownership of how they handle the equipment.
This means tools get returned on time, right where they belong, instead of being left scattered across the job site.
It also means the workers will be less likely to damage the assets during use.
Let’s be honest: sometimes employees get too relaxed with construction equipment when they think nobody’s watching.
But a check-out system brings accountability into play, motivating everybody to stay on top of their asset use.
That’s why, at GoCodes, we’ve made sure our check-in/check-out process is as available and simple to use.
All you need to do is attach our QR code asset labels (shown below) to your tools, enter their details into a database, and install the GoCodes app on workers’ smartphones—and the checkout process can begin.
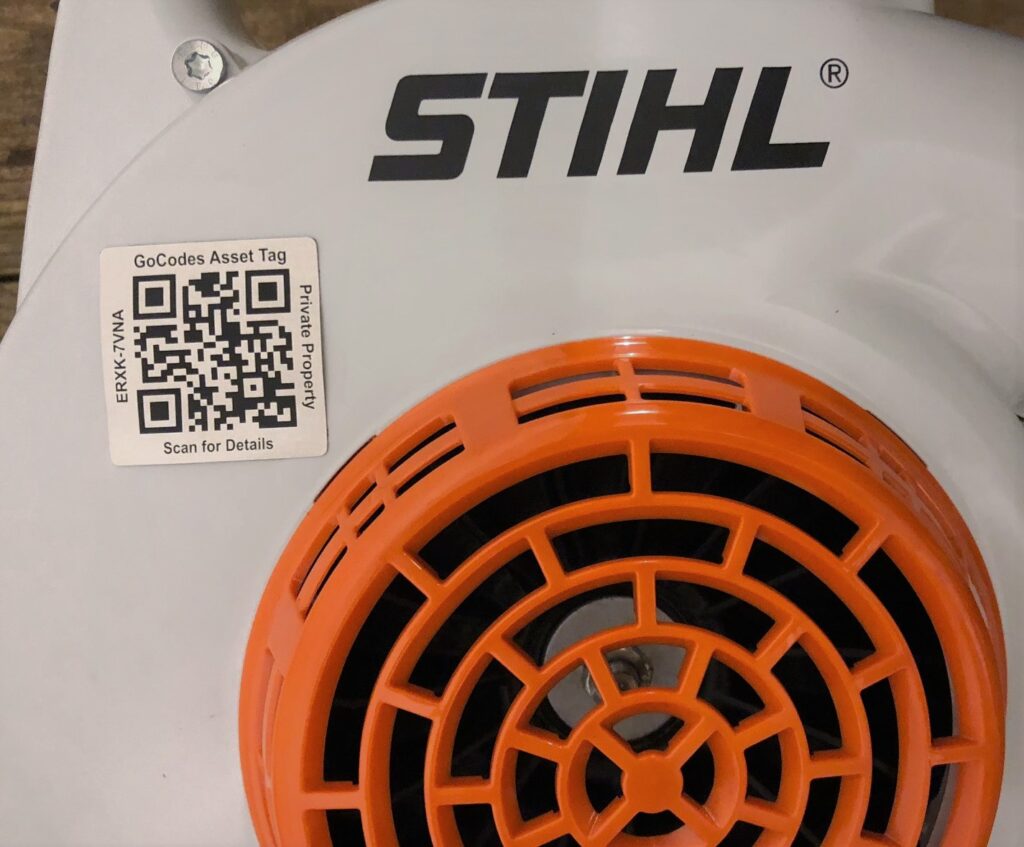
The process itself takes about five seconds.
You just scan the label using the app, and you’re immediately greeted with a screen like this:
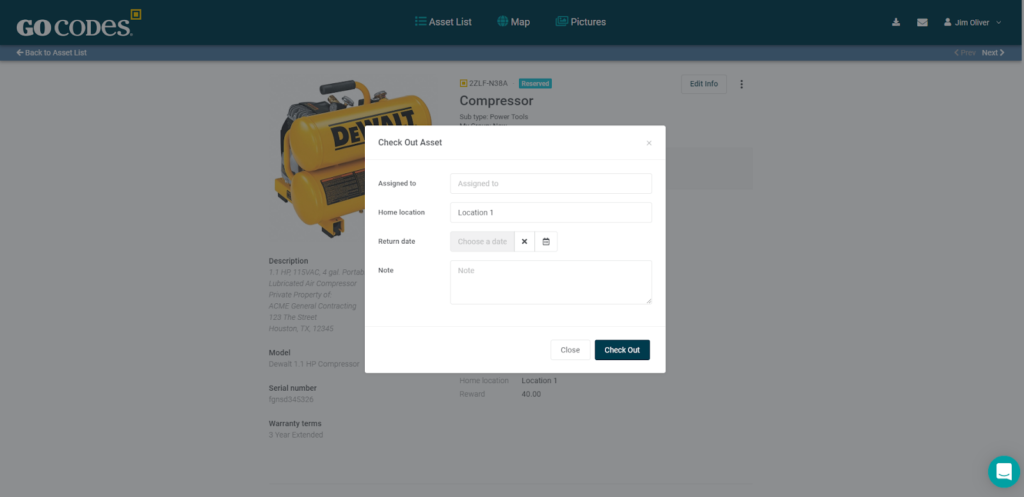
Here, you can either view an asset’s information or, of course, check it in or out.
You can also assign tools to specific employees, set return dates, and add extra details, all following the same steps.
And in case a piece of equipment isn’t returned by the due date, you’ll receive an instant notification.
Having an intuitive check-out system like this is truly the easiest, most effective way to ensure your assets are handled responsibly and with care.
Mobile Accessibility
A tool-tracking solution needs to work wherever the employees do.
And since, in construction, the real action happens on job sites—not in offices—you should ensure your new software is mobile-friendly.
This allows your team to access vital information on the go, instead of having to go back to the office to get on a computer and look up where the tool they need is.
And after all, what good is that real-time monitoring if you can’t access the data from anywhere, anytime?
A 2023 KPMG survey proves that mobile accessibility is becoming increasingly important in the construction industry.
As it turns out, 81% of E&C companies are currently either using or planning to use mobile platforms—up from 69% in 2017.
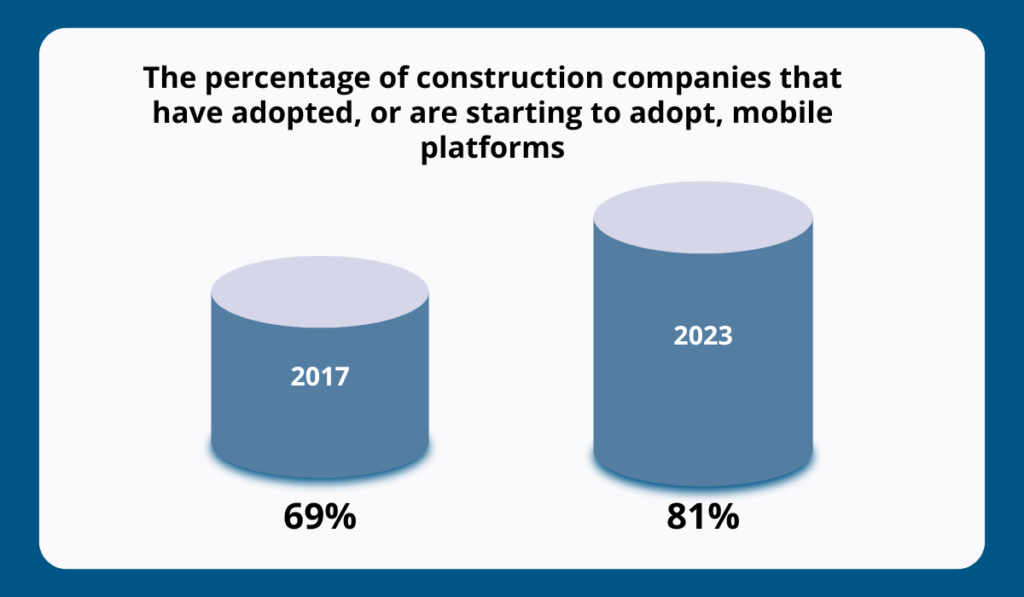
The tool-tracking software you use should keep pace with this trend.
So, when evaluating your options, check if they offer an intuitive mobile app with all the features of the desktop version.
For example, below, you can see GPS location tracking and asset list displayed in the GoCodes app when you’re using a mobile phone.
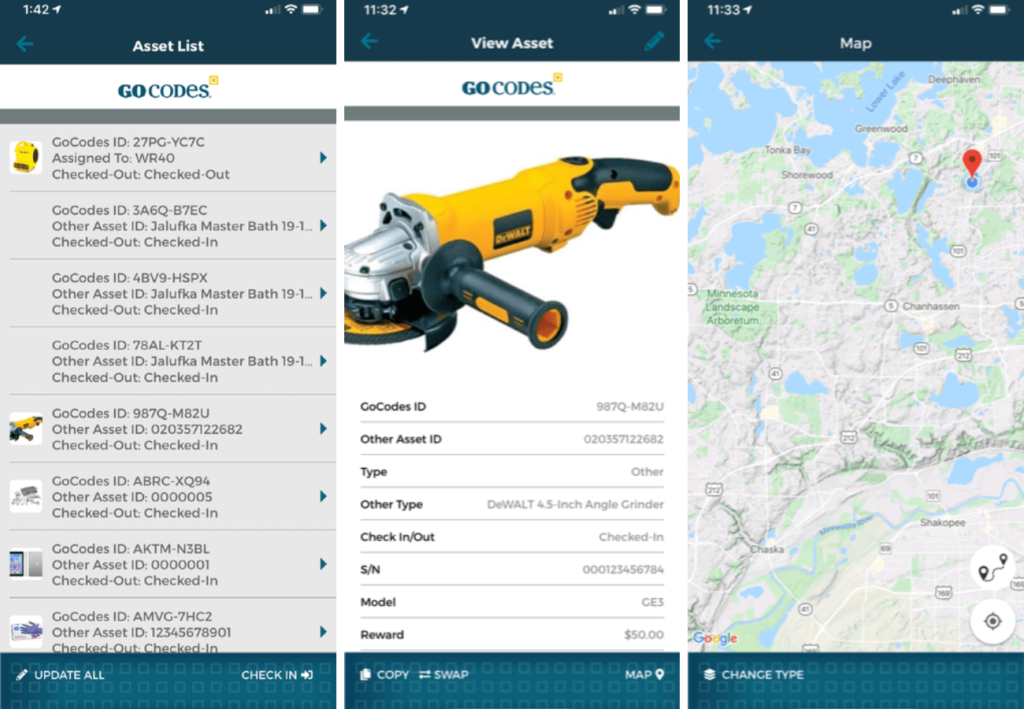
It offers everything the desktop version does.
Overall, having access to asset data in real-time isn’t just a nice-to-have anymore—it’s a must.
Mobile accessibility makes that possible, putting everything you need in the palm of your hand.
Automated Tool Maintenance and Calibration Alerts
Planning and scheduling asset upkeep can be quite complex, especially as the number of tools and equipment you own increases.
So why not let your tool tracking software lighten the load with maintenance and calibration alerts?
These notifications are sent automatically when a service task is due, ensuring everything gets done on time and no tool goes overlooked.
This is crucial for proper asset maintenance.
Shawn Beinhower, CIO of E.K. Services, Inc.—a full-service utility, excavating, and paving construction contractor—shares that missed tasks were a major issue in their company.
“Prior to [asset management software], I know there were times when preventive maintenance on a piece of machinery might have been missed—especially during our busy season. If you miss more than one of those in a row, you can end up with a problem.”
As a result, equipment would get seriously damaged, leading to increased repair costs as well as unplanned downtime, he explains:
“When a piece goes down, there’s downtime in just figuring out what is wrong, and then more downtime on the repair. If it’s an excavator on a pipe crew, then your whole crew’s just sitting there waiting to be fixed. And if it can’t be fixed, then, you incur the cost of getting a rental piece in, as well as the lost time waiting for it to be delivered.”
But when they finally implemented asset management software, that all changed, in part thanks precisely to automated maintenance alerts.
If you also want to keep your assets in top shape at all times, look for a solution that offers such notifications, like GoCodes.
When you assign service tasks to specific workers with GoCodes, you get to set deadlines for their completion and enable email maintenance alerts.
As you can see in the video below, it’s all done in just a couple of clicks.
Simple, hassle-free, and, most importantly, effective.
With automated notifications, there’s simply no excuse for missing equipment upkeep.
Robust Reporting Capabilities
A good tool-tracking solution needs to facilitate informed, data-driven decision-making. It shouldn’t just gather raw data but transform it into actionable insights.
That’s where reporting capabilities come in, giving you a clear, data-rich picture of your assets, including their upkeep histories, usage patterns, and costs.
This, in turn, can significantly improve your asset management and budgeting.
Just like it did for an award-winning commercial contractor, White Construction.
Their former Project Manager, Cristian Sebastian Fernandez, explains how monitoring and analyzing asset costs has had a major role in keeping the business profitable.
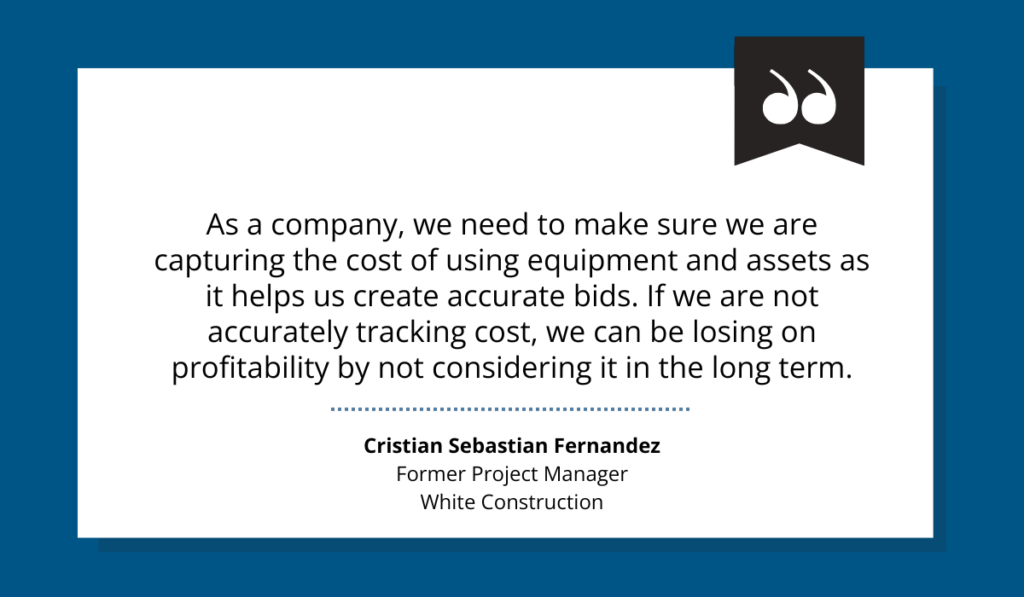
But trying to keep up with all that information manually would be next to impossible.
That’s why reporting capabilities in tool tracking software are a vital part of it.
Take, for instance, GoCodes’ Enterprise Reporting.
It enables you to easily design custom reports, integrate them into dashboards, schedule automatic updates, and share these reports with your team via email or URL links.
Below, you’ll find the purchase cost by equipment type summary—one of many report types GoCodes offers.
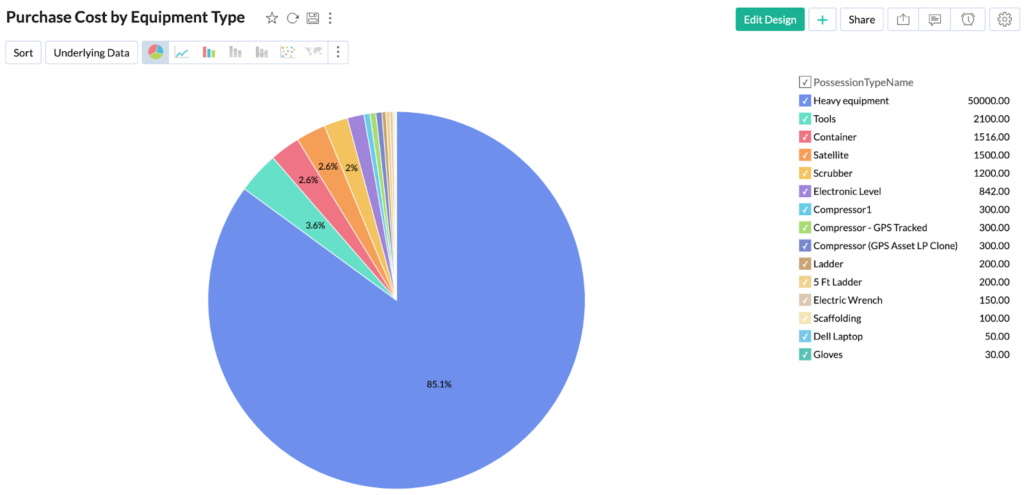
This reporting feature allows you to sort, filter, and present information in the format that best suits your organization’s needs.
Whether you need simple tabular reports or more advanced pivot tables with automatic total calculations, GoCodes has you covered.
Plus, GoCodes provides robust yet easy-to-use depreciation reports, too.
If you regularly input the purchase price and date for your assets, the system calculates depreciation based on common IRS MACRS methods.
Then, it generates a Microsoft Excel-compatible .csv file that details each asset’s depreciation, including annual, current-year, prior-year, and cumulative depreciation data, plus the remaining balance, as in the example below.
It’s time to stop basing your decisions on guesswork.
With the right tool-tracking solution, you can finally get access to the rich and reliable insights you need to take your asset management to the next level.
What to Avoid When Choosing a Tool Tracking Software
Since not every software is created equal, some tool tracking systems are far from ideal.
Here’s our recommendation on what to watch out for and avoid.
No Free Trial
Committing to a purchase without first trying the software out can be a risky gamble that you might soon regret.
Did you know that, according to a 2024 Capterra survey, 58% of U.S. businesses across various industries regret at least one software purchase?
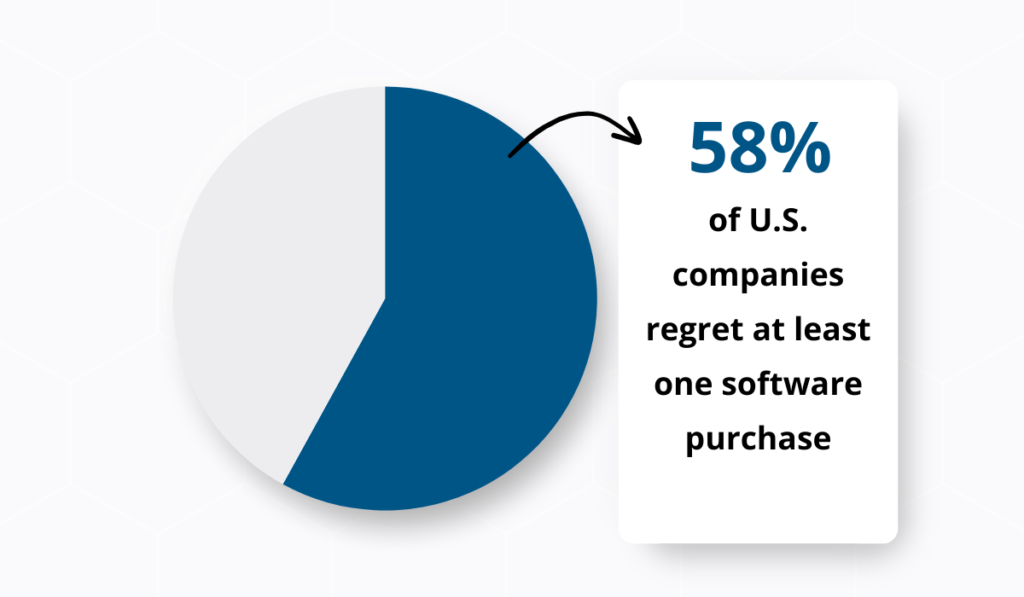
By skipping a free trial, you increase your chances of becoming part of that statistic.
Why?
Because that way, you forgo the opportunity to test all the features, assess compatibility with your workflows, and get feedback from your team.
Why take that chance?
Why risk investing in a system that doesn’t meet your operational needs?
A free trial is truly a great way to explore everything the solution has to offer without any financial commitment.
For instance, it was precisely GoCodes’ 15-day free trial that helped this user make up their mind about which system to buy.
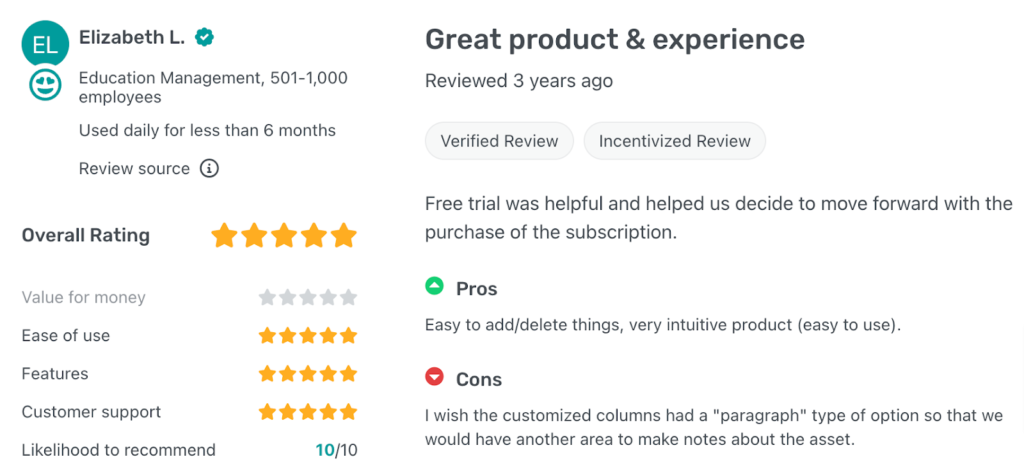
So don’t leave this important decision to chance and look for solutions that include a free trial.
Only by trying out the solution yourself can you purchase with confidence, knowing it will deliver exactly what you and your team need.
High Learning Curve
All the advanced features in the world mean nothing if the software is a pain to use.
In fact, if it’s too complicated to learn, your team might just abandon it.
Why would they have to deal with a confusing new system when they already have a lot on their plates?
The construction industry is already pretty reluctant to adopt new technologies.
Ibon Iribar, an Investment and Open Innovation Advisor at Cemex Ventures, a leading sustainable construction materials and solutions company, agrees with that notion.
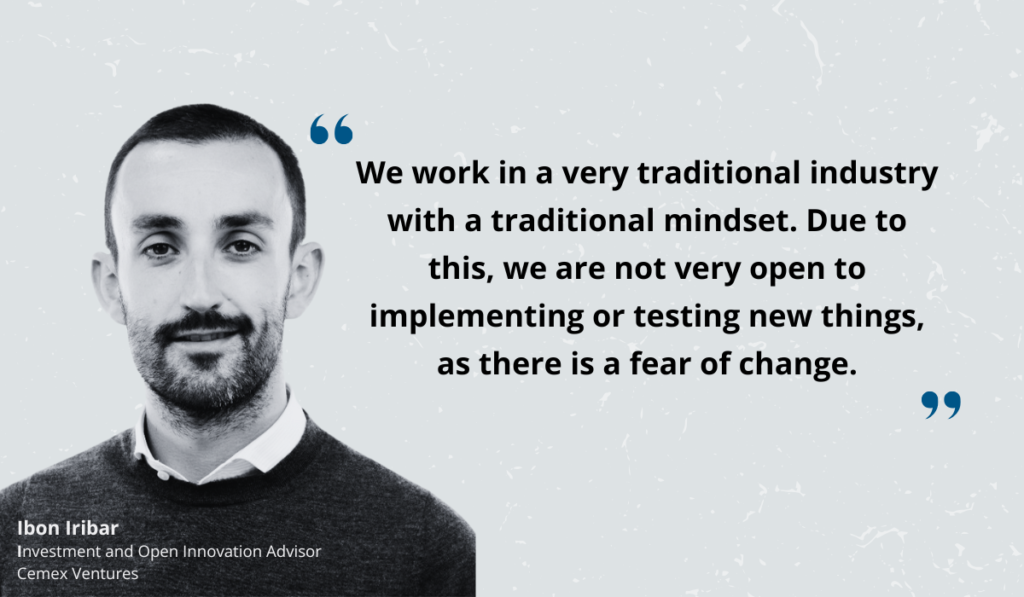
So the last thing you want to do is make work even more difficult by introducing an overly complex system into the mix.
Instead, prioritize finding a solution that’s intuitive and easy to navigate.
Spend some time browsing online reviews for insights into how the software performs in the real world.
Paired with free trials, these reviews are your best bet for understanding what you’re getting into.
If most reviews are positive—like the example below—you’ll know the software is worth exploring further.
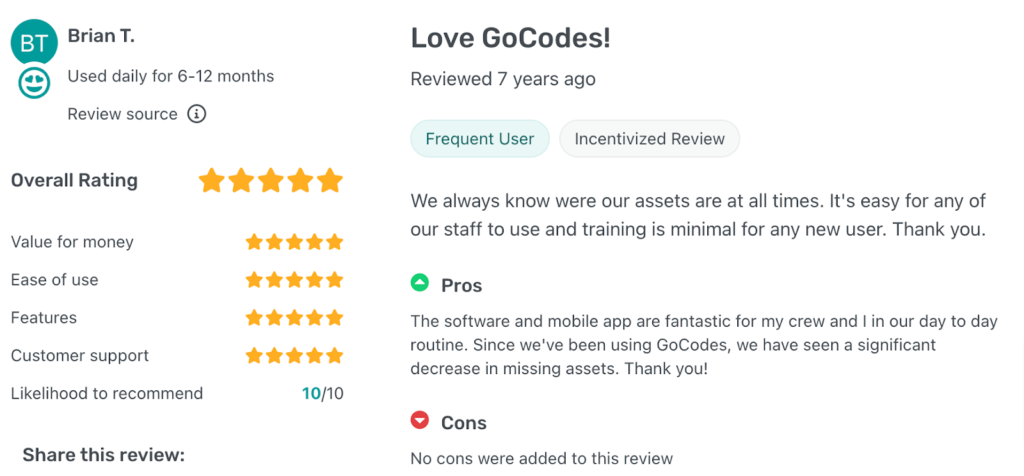
Remember, a truly effective tool-tracking solution should make your job easier—not harder.
Lack of Scalability
Your tool-tracking software shouldn’t just meet today’s needs. It should meet the future ones too, and be able to grow with your company.
Otherwise, you could end up stuck in an endless loop of researching, switching, and purchasing new solutions every time you scale.
And that can quickly get costly, disruptive, and frustrating.
As Sagar Gandhi, Head of Strategy and Business Excellence at Shapoorji Pallonji E&C, explains, adaptability is a must-have feature for any software:
“The core philosophy of our technology implementation has been that it needs to be easily adaptable and scalable. We don’t believe in technology shopping because every now and then, a new technology comes on the block, and people run behind it.”
Therefore, if the solution you’re considering limits the number of assets, users, features, or locations, think twice.
Chances are, it won’t keep up with you down the road.
Instead, go for a system that will grow with you, like GoCodes.
With five flexible and affordable plans, GoCodes makes it easy to choose the right fit for today and upgrade smoothly when your requirements evolve.
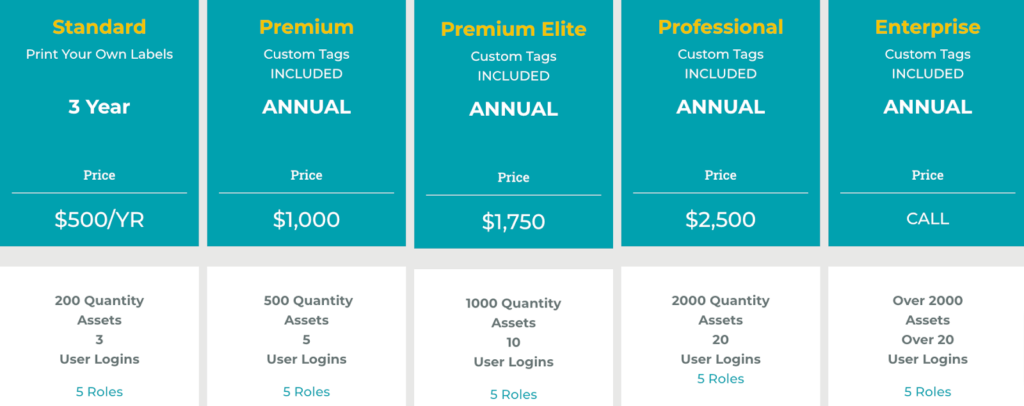
This way, you’re in control, tailoring the software to your organization, not the other way around.
No Asset Import Service
Even with the perfect software—loaded with all the right features, a good price point, and an intuitive user interface—switching from your current tool tracking method can feel daunting.
This is especially true if you’ve been tracking your assets manually.
The thought of copying all that information into a new system would make anyone hesitant to transition.
But did you know that you don’t have to do that?
Not if you pick a solution providing an asset import service.
GoCodes, for instance, offers a Data Upload service to make onboarding large sets of inventory data as easy and stress-free as possible.
Do you have your asset data in a spreadsheet or Google Sheets?
Great. We’ll send you a customized Excel template with simple data validations to guide you.
Once you paste in your data and send it back, our team takes over with a thorough Quality Assurance check, making sure your data is accurate and ready to go.
The upload itself typically takes just 1–2 business days, and voilà—you’ll get a clean, organized asset list, like the one below, no matter how many assets you’re currently managing.
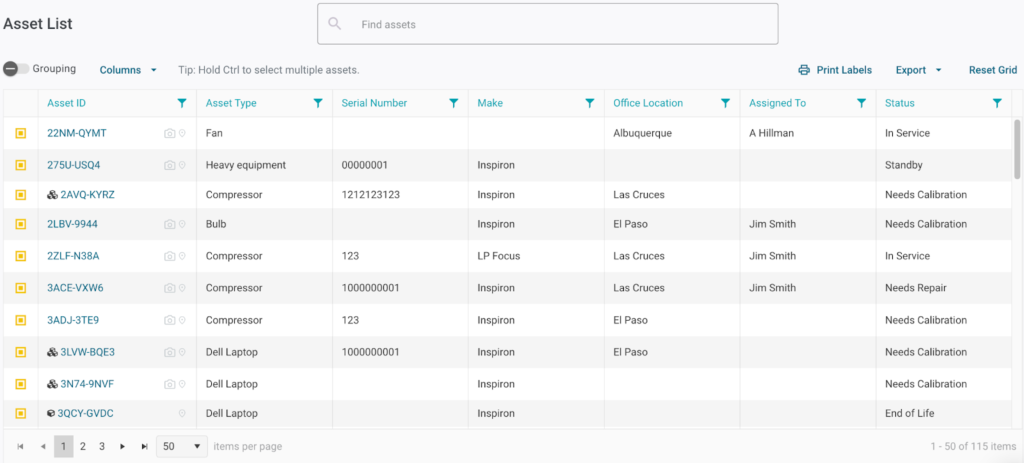
As you can see, switching to a tool-tracking solution doesn’t have to be challenging if you choose a vendor committed to making it easy for you.
Lack of User Roles
User roles allow you to assign varying levels of authority to users based on their job functions, ensuring each employee has access only to the features and data relevant to their roles.
But without user role customization, you can’t control who can view and interact with critical equipment information.
That means that all users—from site workers to admins—can see everything, which can lead to some serious issues.
For example, an employee might alter tool check-in/check-out data, hiding misuse or even theft.
And before you say that’s impossible, know that a 2024 BauWatch research revealed that 27% of construction site thefts are committed by insiders.
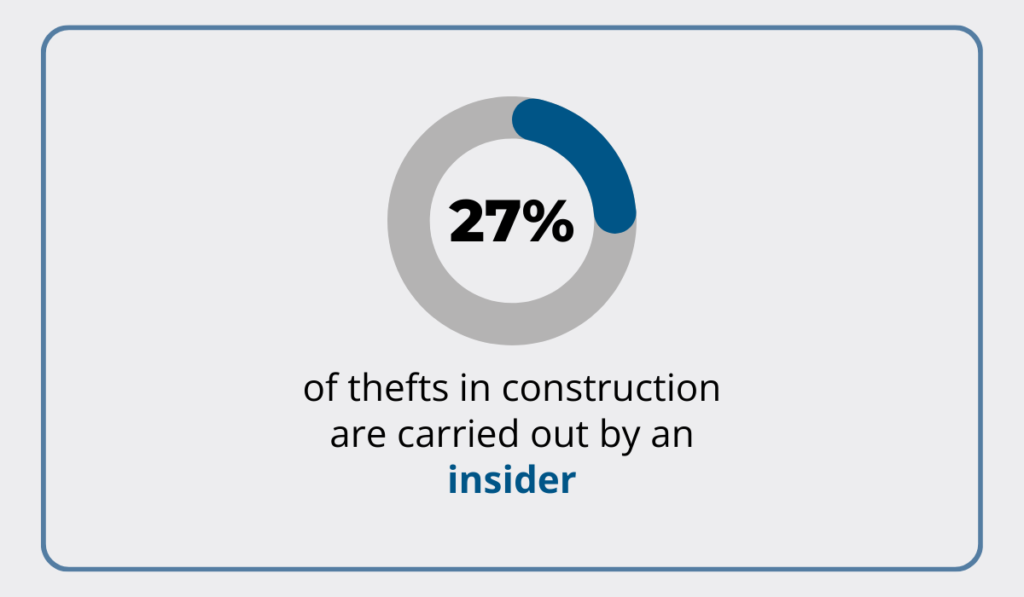
Luckily, with solutions like GoCodes, you can minimize such risks.
GoCodes gives you more control over who sees what, with its five distinct role-based levels: public, read-only, asset assigner, asset manager, and admin.
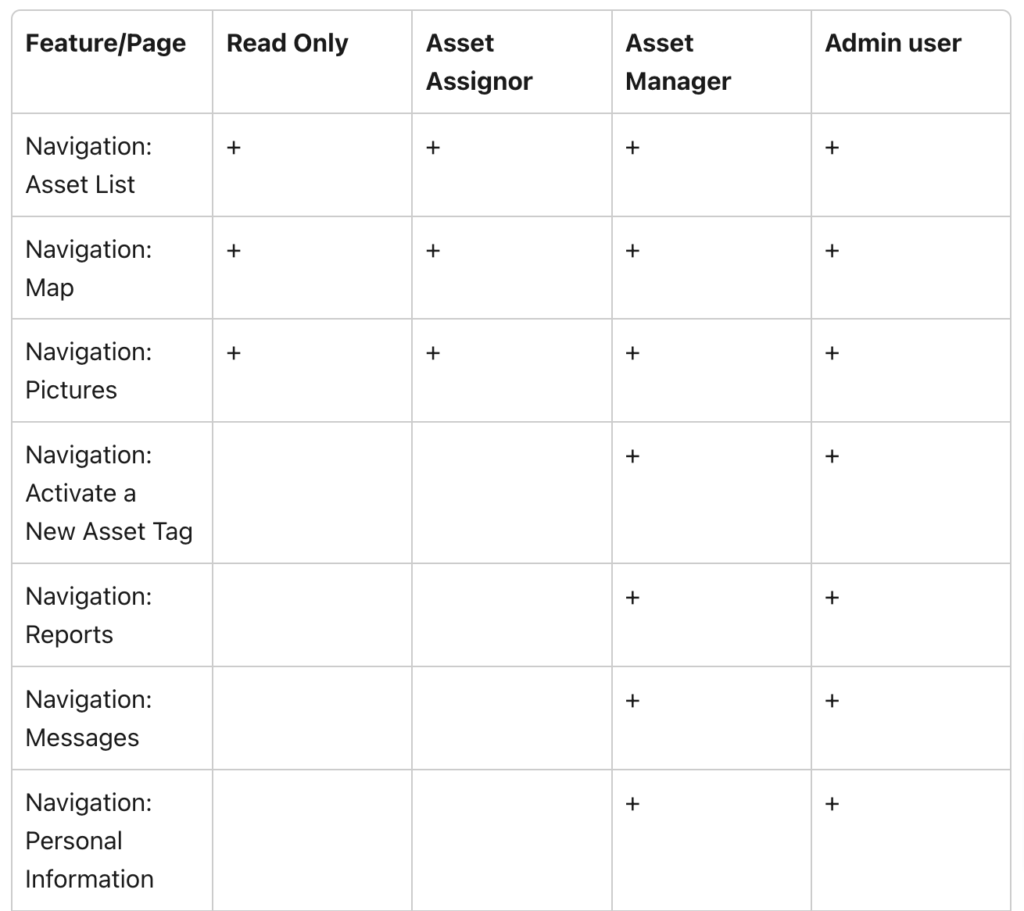
You can also easily add new users and change permissions as your team grows and your needs evolve.
This helps ensure that only the right people have access to sensitive information, allowing you to not only work smarter, but much safer too.
Conclusion
We hope that now, you’re feeling more confident in your search for the perfect tool-tracking software.
Sure, there’s still work ahead, but following this guide will make the process much easier.
And the effort you put in will pay off immensely.
Once you discover that ideal system, you’ll see a remarkable transformation in your tool management process.
Increased efficiency, reduced risk, and improved profitability—all of this is well within your reach.
Good luck!