Today, construction businesses are aware that manual processes and spreadsheets are not an efficient way to track assets used to complete construction projects, such as vehicles, heavy machinery, equipment, and tools.
Therefore, they’re turning to tech solutions that allow them to digitize and automate their asset management processes and enable them to track the location, usage, and maintenance of their construction assets at all times.
And that’s where an asset-tracking platform comes in.
Simply put, an asset tracking platform is any software solution that, combined with the dedicated tags attached to assets, can track heavy equipment, vehicles, tools, and other items to maximize your organization’s productivity and minimize costs.
However, if you’re responsible for streamlining asset tracking in your company, selecting a platform that will best fit your organization’s specific needs and budget can be challenging.
So, here are seven features that an effective asset-tracking platform should have.
In this article...
GPS Tracking
When your asset tracking platform can track the GPS location of assets in real time, you can easily monitor where your construction assets are at all times.
This has many benefits, including theft protection, reduced insurance costs and fuel consumption, and increased operational efficiency.
Naturally, using the Global Positioning System (GPS) is not the only way to track assets. Other technologies like Bluetooth or RFID can be used, particularly indoors.
However, when it comes to real-time tracking of construction assets circulating between several job sites and storage, GPS has no real competition.
Here’s how a GPS tracking system works:
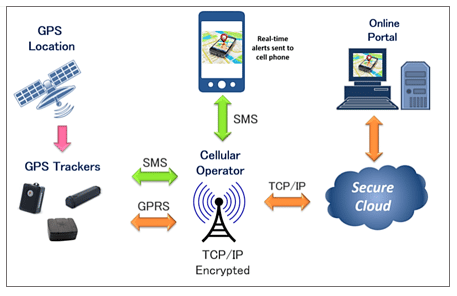
Satellites provide signals that are processed by active GPS trackers to determine their exact location and time, along with additional information such as the speed of a vehicle.
The GPS tracker sends this information to the cloud database, and users can access it via the tracking software and receive real-time location updates and alerts on their mobile devices.
It should be noted that GPS tracking can also be done without power-intensive and often expensive GPS trackers.
That passive, GPS-enabled asset tracking involves asset tags that, when scanned by a smartphone or other compatible devices, prompt the tracking software to use the device’s built-in GPS function to record the asset’s GPS location and show it on a map.
In any case, GPS tracking is one of the essential features that an asset tracking platform should have.
It provides numerous benefits for contractors, ranging from theft protection and reduced insurance costs to lower fuel consumption and increased overall productivity.
QR Code Generation and Scanning
As said above, construction assets can be tracked in many ways, and QR codes stand out as a quick, easy-to-use, and cost-effective way to do so.
For this reason, QR code generation and scanning is an important feature of an asset-tracking solution.
In other words, your asset tracking platform should enable you to generate custom Quick Response (QR) codes (or deliver them to you) that can be attached to different assets.
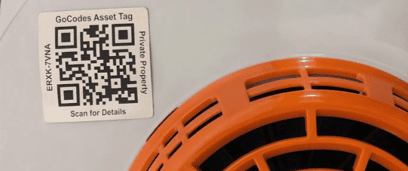
In addition, the tracking solution of your choice should enable users to scan QR codes with their smartphone or tablet to instantly access asset information via their tracking app.
So, when a user scans the QR code tag on an asset, the user can view that asset’s location, usage, maintenance history, and any other data your organization finds relevant, such as instructions or warranty information.

For instance, our asset tracking platform, GoCodes Asset Tracking, offers customizable QR code asset tags that you can either generate and print by yourself or have them delivered already printed on, for example, durable polyester or metal tags.
Once these patented QR code tags are affixed to assets and scanned by a smartphone or another device to establish the central inventory list, your asset tracking system is ready to go.
In other words, field workers can scan any tagged asset, and our mobile app will provide them with instant access to that asset’s information, as well as show the list of other assets in the inventory database.
Overall, QR codes are a simple and affordable way to track your assets, which makes QR code generation and scanning an essential feature of an effective asset-tracking solution.
Check-in and Check-Out
The check-in/check-out feature allows construction companies to track where assets are, who is using them, and for how long.
In addition, a well-designed check-in/check-out system will enable project/equipment managers to instantly see who the assets are issued to and when they are returned.
Moreover, when all workers have the tracking app on their mobile device, tools and equipment do not have to go back to the central location, such as a tool crib, to be issued to another worker.
Instead, workers can do the check-in/check-out process amongst themselves directly on-site.
When established, such a system provides construction businesses with a range of benefits, some of which are listed here:
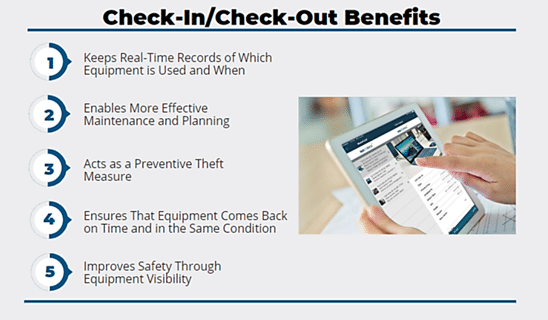
For instance, the check-in and check-out feature will increase worker accountability by providing a transparent chain of custody, leading to less misplacement and theft and enabling better asset allocation and maintenance practices, as discussed in the next section.
Naturally, this feature will enable all users, including construction crews, site supervisors in the field, and project and equipment managers in the office, to quickly view tool and equipment assignments, usage, and availability in real time.
In summary, considering the benefits it can create, the ability to establish a check-in/check-out system should be an essential feature of your asset-tracking platform.
Maintenance Scheduling and Tracking
Another vital feature your asset tracking solution should have is maintenance scheduling and tracking, which allows you to keep construction assets in good condition.
Maintenance scheduling and tracking can generate benefits such as fewer equipment breakdowns, longer useful life of equipment, and reduced maintenance costs.
Moreover, this feature enables you to schedule preventive maintenance, keep track of the schedule and receive maintenance alerts.
In other words, when equipment breakdowns, downtime, servicing, and repairs are tracked, this allows contractors to establish a preventive maintenance schedule that will ensure they can achieve their equipment maintenance goals, which usually include:
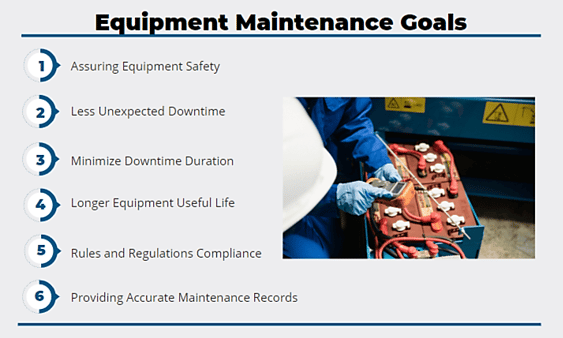
To meet these goals and reduce upkeep costs, contractors need to understand how their assets are performing over time so that they can make better informed repair-or-replace decisions.
As maintenance tracking provides accurate records, they can analyze the history of equipment and tool usage, breakdowns, and downtime to determine the maintenance required for each asset.
Furthermore, contractors can use the data collected by their asset tracking solution to create a preventive maintenance schedule, as well as set up alerts that will notify users of upcoming maintenance.
For example, when an asset has a future maintenance date, GoCodes Asset Tracking can be easily configured so users receive a scheduled service alert a day before or on the morning of the scheduled service date.
Overall, the maintenance scheduling and tracking feature allows you to streamline all asset maintenance practices, i.e., create a schedule, automate alerts, keep costs down, and make sure your equipment remains in good condition.
Depreciation Tracking
The next feature your asset tracking platform should have refers to tracking and calculating depreciation for your assets, allowing you to better align your organization’s financial statements, reduce taxes and increase yearly profits.
First, let’s quote Investopedia’s definition:
Depreciation refers to an accounting method used to allocate the cost of a tangible or physical asset over its useful life.
In other words, when a piece of equipment is purchased and put in use, it starts losing value through normal wear and tear, and depreciation is used to calculate precisely how much value it has lost over time.
By choosing a specific depreciation method, contractors can spread this reduction of an asset’s value in different ways.
The simplest method is straight-line depreciation, where the amount of depreciation stays the same every year, like in this example:
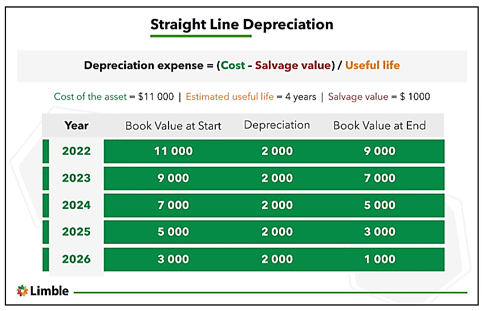
Other depreciation calculation methods use various factors to calculate the asset’s loss of value over its useful life, each having different effects on your organization’s cash flow, balance sheet, and equipment expenses in any given business year.
Aside from using it for accounting and tax purposes, the calculated depreciation can also be used for making better-informed decisions, such as whether to repair or replace a piece of equipment that has already lost much of its value.
Overall, your asset tracking solution should allow you to choose the depreciation method. It should also automatically calculate and track annual depreciation amounts.
Custom Reports
The ability of your asset tracking platform to generate in-depth, custom reports is a critical feature that allows you to analyze all the collected asset data and make informed, data-based decisions regarding asset management.
In other words, being able to generate comprehensive reports provides you with valuable insights into how to efficiently manage the lifecycle of construction assets, from planning and procurement to maintenance and disposal.
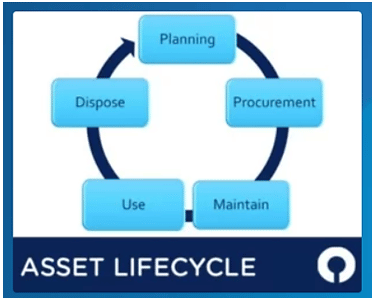
For example, you can analyze the usage of a particular type of asset, such as power tools, to plan the maintenance of existing tools, estimate their useful life, and ensure the timely procurement of new models.
Of course, this wouldn’t be possible without assets being tracked and data collected by the asset-tracking platform.
Tracking allows you to observe the performance of assets and learn how to maximize their use and extend their life span by scheduling preventive maintenance, avoiding overworking assets, and ensuring compliance with safety regulations.
For instance, GoCodes Asset Tracking offers an easy-to-use report generation feature that enables you to analyze and view tracking data according to your needs and preferences.

Overall, the ability to create custom reports allows you to use all the data collected by asset tracking, analyze it, and make informed, data-driven decisions to improve your organization’s asset management.
Mobile Compatibility
Similar to how asset tracking data couldn’t be analyzed without the reporting feature, your asset tracking solution wouldn’t be very effective without mobile compatibility.
This means that everyone involved, particularly field workers, can access the asset tracking platform anytime and from any place by using a mobile device, such as a smartphone, tablet, or laptop.
When that’s so, workers, managers, and even subcontractors (when allowed access) can quickly view, manage, and update relevant asset data from any location.
In other words, having a cloud-based and mobile-friendly asset-tracking solution will result in better collaboration, fewer errors, and increased efficiency.
Here are some additional benefits of mobile asset tracking:
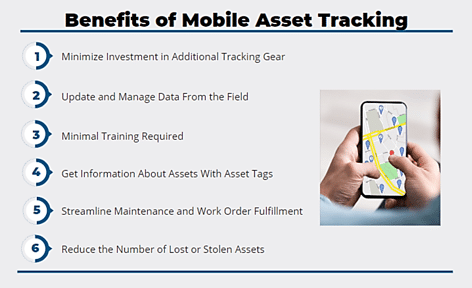
You can read more about each benefit in our article on this topic, and we’ll just give a few examples.
For instance, when workers can use mobile devices to scan asset tags and manage data from the field, this means you don’t need to purchase additional tracking gear, such as special scanners.
Likewise, since your workers are already familiar with devices like smartphones and tablets, they will require minimal training to operate the asset tracking system.
Overall, the mobile compatibility of your asset tracking solution allows workers to do their job more quickly and efficiently and gives managers relevant data to make well-informed decisions in real-time, thus helping them address unexpected situations and prevent project delays.
Conclusion
So, if you’re looking for an easy-to-use, efficient, and affordable asset-tracking platform, the seven features we described should be on top of your mind.
The efficiency gains and cost savings generated by adopting an effective asset-tracking solution are felt throughout the entire business, from equipment management, field-office communications, and maintenance scheduling to accounting, analytics and overall project management.
What are the results of all these improvements? Reduced costs, increased productivity, and higher profits.