Whether you’re a construction company owner or manager, the fact you’re here means you’re considering using equipment management software to track and manage your construction equipment, tools, and other assets.
If that’s the case, you’re probably wondering what software solution would best fit your company’s needs and budget and which essential features such software should have.
In this article, we’ll cover nine important features of construction equipment software, describe how they work and how you can use them to minimize equipment theft and loss, extend its lifespan, reduce equipment maintenance and purchasing costs, and much more.
In this article...
Life Cycle Management
Equipment life cycle management allows you to monitor the life cycle of your construction equipment from acquisition to disposal, calculate its depreciation, and make informed decisions about when it should be serviced or replaced.
The ability to do all that is actually the combined result of all the other features described here, which reflects the all-encompassing nature of equipment life cycle management.
In practical terms, once you select and implement the equipment management software, the system will collect a range of valuable data that can be used to improve life cycle management.
For example, the purchase date and the price are typical starting points for life cycle management, and they can be easily viewed in the software’s database for each piece of equipment, like in this example.

Of course, the date and value also help you calculate the equipment’s loss of value over time (depreciation) for accounting, tax-saving, and financial reporting purposes.
Depreciation calculation is a standard equipment management feature that, in terms of life cycle management, allows construction companies to:
- determine the ideal time to replace equipment based on its remaining value and projected lifespan, ensuring the optimal utilization of resources
- make better-informed maintenance, repair-or-replace, and buy-or-rent decisions to minimize equipment downtime and maximize efficiency
- improve budgeting and capital planning of equipment-related expenses
Aside from depreciation, your equipment management software will store a lot of data, which will facilitate more efficient life cycle management, such as the equipment’s maintenance and usage history.
To summarize, this overarching but essential feature enables you to monitor the life cycle of your equipment and, based on the data collected by your software, make informed servicing and repair-or-replace decisions and efficiently manage equipment from acquisition to disposal.
Barcode Scanning
One of the primary features that physically enables automated equipment management is barcode scanning.
In other words, for your construction tools and equipment to be managed, you need to know who is using them and at what locations, meaning you need to track them.
Barcodes and QR codes are the most cost-efficient and widely used tracking method involving labels affixed to construction assets you want to be tracked, which can be anything from a screwdriver to an excavator.

Furthermore, if you select a software solution with a built-in barcode scanner (instead of more expensive special handheld scanners), this tracking solution becomes even simpler and cheaper to implement.
In other words, your selected software should come with an in-app scanner that turns your company’s and/or workers’ smartphones and tablets into barcode-scanning devices.

This feature enables workers to scan the equipment’s barcode to access the equipment’s info (unique identifier, purchase date, maintenance history, etc.), view relevant information, make updates, leave comments, and add pictures.
As for managers, they can access the barcode-based system’s database and filter their search to find what they need, such as a particular piece of equipment, its availability in a specific period, or all equipment currently in use (checked-out).
One such software solution that comes with a built-in scanner for QR-code scanning is GoCodes Asset Tracking.

As you can see, the GoCodes Asset Tracking package includes cloud software with an in-app scanner that enables smartphones and tablets to scan rugged, customizable QR code tags/labels (delivered to you).
Again, this barcode-scanning feature can be enhanced using other tracking methods like Bluetooth beacons or active GPS trackers.
Still, barcodes/QR codes are usually kept in such cases precisely for equipment management purposes.
Overall, barcode scanning lies at the core of any efficient equipment management software, and an in-app scanner as part of an all-in-one tracking package makes the system’s implementation and use even more practical and affordable.
GPS Tracking
In addition to tracking equipment usage and maintenance, you should be able to know where exactly your equipment is, meaning your equipment management software should have GPS tracking capabilities.
Of course, active GPS trackers installed on heavy equipment and construction vehicles, which offer “dot-moving-on-screen” real-time tracking, represent the most advanced option.
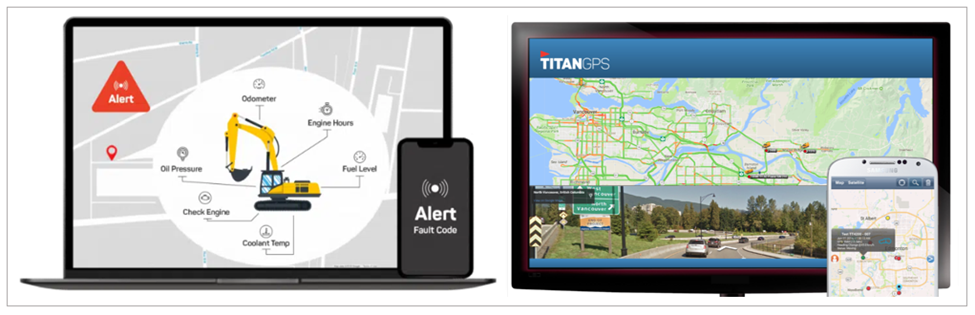
However, such trackers are often too pricey and/or too large to track countless smaller equipment, tools, and other valuable construction assets.
And that’s also why other location tracking solutions that did not rely on GPS emerged, like RFID (radio-frequency identification) and Bluetooth technologies that track equipment movements within a limited range of their respective remote readers and other signal-boosting infrastructure.
One GPS-based tracking method, both innovative and cost-effective, involves using patented GPS-enabled QR code tags that, when scanned, prompt the tracking software to automatically record the equipment’s location.
The software updates the GPS location using the GPS function of the device that scans a tagged piece of equipment and shows it on a Google map.

This way, you get to track equipment as it changes locations and persons using it, and—if a piece of equipment is misplaced or stolen—you can check the last recorded location and user in the software and start your search (or police investigation) from there.
Naturally, this can help prevent equipment loss and theft.
Additionally, the QR code tag serves as proof of ownership that can be scanned by any good Samaritan who wants to report they found your missing equipment.
Coupled with the check-in/check-out feature we cover below, this tracking method can significantly reduce the number of missing equipment, tools, and other assets your company must replace.
To recap, since active GPS tracking is often too expensive and impractical, and non-GPS solutions have limitations, your equipment management solution should provide automatic location updates using scannable GPS QR tags.
Check-in and Check-Out
The check-in/check-out feature enables workers to automatically record when they checked out a piece of equipment, tool, or another tagged asset and do the same when they return it.
As for managers, they can keep track of the current location, usage, and availability of equipment in real-time and can achieve various time and cost savings by using the data collected by this check-in/check-out feature.
Here are just some benefits of this essential equipment management software feature:
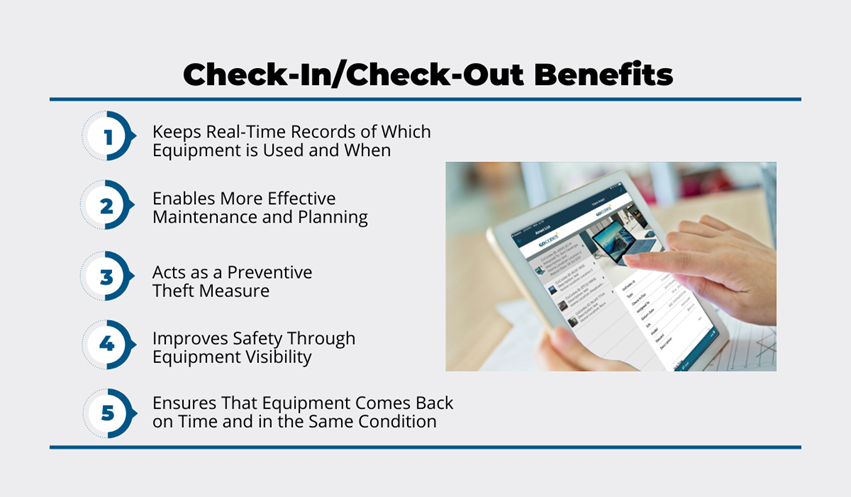
As you can see, most of the above benefits have to do with employee accountability.
In other words, once workers have the app on their smartphone, know how to use the automated equipment check-out system, and are willing to use it due to its practicality and ease of use, this brings forth many advantages.
More precisely, it instantly increases worker accountability and significantly reduces misplacement, theft, and negligent equipment operation.
In any case, when the system is up and running, workers can take and return equipment as self-service or under supervision and exchange equipment between themselves on-site while the tracking software records all these actions.
Since this key feature is highlighted by almost all equipment management software providers, it’s best to look for a simple, affordable, and user-friendly solution.
Maintenance Scheduling
Of course, your equipment management software should enable you to schedule future maintenance tasks and improve your company’s service-and-repair practices, making maintenance and, thus, life cycle management more efficient and less costly.
This maintenance scheduling feature ultimately helps keep equipment in good condition for longer, which minimizes unexpected breakdowns and safety-related incidents that could delay or even stop a construction project.
Naturally, scheduling service tasks should be as simple as possible, as shown in this short video.
Once you schedule planned maintenance tasks and assign them to service technicians, you can set up the system so any relevant staff members receive automatic scheduled service email notifications.
These reminders ensure that neither you nor the assigned staff will miss a scheduled maintenance task, thus increasing the quality of your preventive maintenance program.
All in all, maintenance scheduling is an important feature that allows equipment managers to plan, schedule, assign, and monitor the performance of regular maintenance tasks while ensuring responsible staff is automatically notified in advance.
Task Management
Other than scheduling and assigning maintenance tasks, your equipment management software should enable you to assign and manage various equipment-related tasks and work orders.
In other words, instant access to the equipment’s info page and the bird’s view of all equipment management operations allow managers to, for example, reserve specific equipment and tools (or kits) for particular project timelines and individual workers or jobsite crews.
This ensures all workers will have what they need when they need it.
Equally, other equipment-related tasks can be assigned to specific people, such as different equipment inspections, transport-to-jobsite orders, or maintenance work orders we mentioned.
Again, this feature—as all others covered here—should be simple and easy to use.
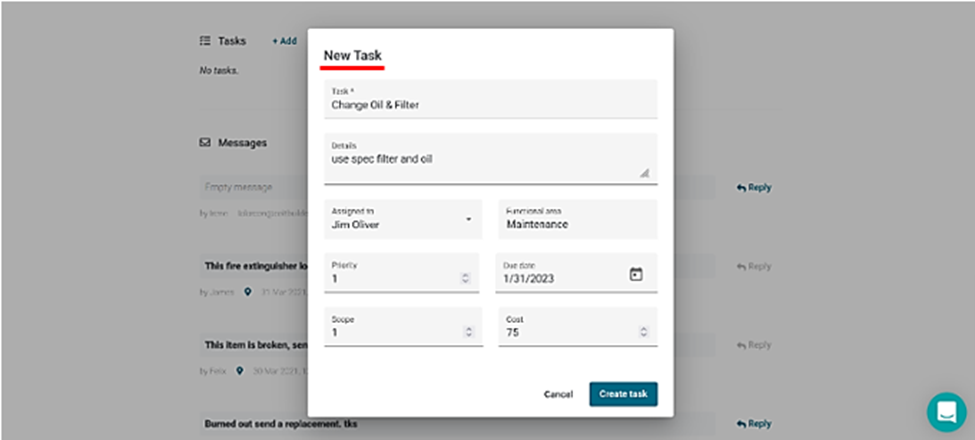
Task assignments clearly assign responsibility for performing specific equipment-related tasks and help avoid confusion, inaction, or, when things go south, blame-shifting.
In other words, it’s always clear who is responsible for what.
Finally, this task assignment feature enables managers to react in unexpected situations more quickly, reallocate equipment or reassign tasks and notify everybody involved using the software app on their phone or another internet-connected device.
Automated Alerts
As their name suggests, automated alerts allow you to configure your equipment management software to send different automatic notifications like the scheduled service alerts we mentioned under maintenance scheduling.
Another type of these software-generated and emailed notifications are overdue asset reminders sent when a worker is supposed to return the assigned equipment.

Of course, if a worker doesn’t return the equipment assigned to them, the system can be set to send other reminders and/or notify the equipment manager.
Both upcoming maintenance and equipment return notifications are triggered by a specific date specified in your software.
Low-quantity notifications are another type of low-quantity notifications.
This add-on feature is very practical for monitoring the number of spare parts, cables, and other consumable construction inventory items in storage.

As you can see, a container can be barcode-labeled, and the quantity of spare parts inside it is set in advance.
When staff members take them out of the container, they record how many they’ve taken.
When the inventory level hits the preset low-quantity value, the system displays an alert and sends an email to designated persons.
In summary, automated alerts allow you to take full advantage of your software’s maintenance scheduling and task management features and improve your equipment management operations.
Report Generation
Report generation is a feature of your equipment management software that allows you and your management team to create custom reports using the data in the central database.
In other words, as data is collected by your software over time, this feature enables you to analyze different data aspects and generate accompanying reports to gain valuable insights into your equipment management practices.
Along with easy use, customization is vital for effective reporting.
With it, you should be able to filter different data points and analyze the information in a way that best fits your needs.
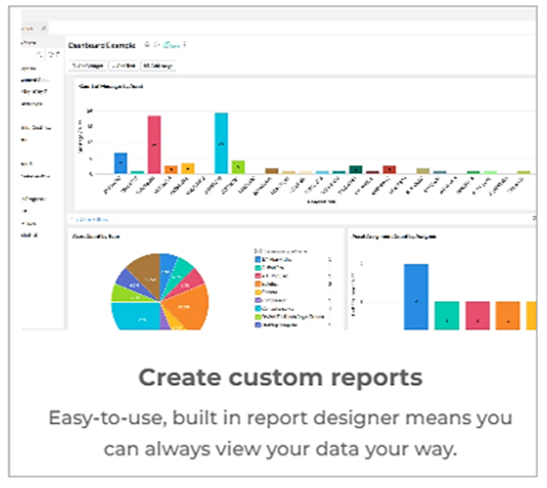
This important feature can be used to create reports about, for example, equipment usage across several jobsites, lost/stolen equipment per specific site, and so on.
Needless to say, this feature is crucial for identifying strong and weak points in your equipment management processes and improving them with the help of insights gained through analytics and reporting.
Cloud-Based Data Storage
Compared to on-premises software (which includes required hardware and related installation, maintenance, and data security costs), keeping your data in the cloud is more efficient and less costly.
Basically, cloud-based equipment management software has two main upsides.
First, anybody can access the software’s interface and database anytime from any internet-connected device in any location.

In addition to this instant real-time accessibility, you’re outsourcing a lot of IT, server, data storage, and online security issues to your software provider instead of your company having to deal with them on its own.
Overall, this software feature provides secure and unlimited cloud-based data storage and backups while providing your construction company real-time mobile access to information needed for efficient equipment management.
Conclusion
When combined, the described features of your construction equipment management software enable you to digitize, automate, and streamline how equipment, tools, and assets are managed throughout their life cycle.
At the same time, you’re enhancing the security (worker accountability), safety (improved maintenance), and utilization (better allocation) of all your equipment.
Ultimately, the right equipment management software enables your company to take advantage of data-driven insights to realize time and cost savings across your construction operations.