Key Takeaways
- Construction workers spend about 10% of their workday looking for tools.
- Smaller equipment gets stolen more often than expensive heavy machinery.
- There are many different ways to track small assets and reduce the chances of them being stolen or misplaced.
Everyone knows that heavy construction machinery comes with a hefty price tag, which is why companies go to great lengths to protect these valuable assets.
But what about the smaller tools?
Unfortunately, they often fly under the radar, seen as less valuable or less impactful on daily operations.
But that’s a costly misconception.
Small equipment, if not properly managed, can lead to all sorts of problems that can impact entire project lifecycles.
In fact, it’s precisely because of their size that they are much easier to steal or misplace.
That’s why, in this article, we’re going to illustrate how crucial tracking your smaller assets is.
We’ll also show you how to do it properly so that you don’t have to worry about missing tools ever again.
In this article...
Losing Small Tools Adds Up
To demonstrate how important tracking small equipment and tools really is, let’s explore some of the consequences of neglecting this important task.
Effect on Productivity
Just imagine how much time is wasted on the construction site searching for misplaced tools and equipment, and how much that impedes a project’s progress.
Actually, you know what?
You don’t have to imagine because Soeren Brogaard, CEO of a SaaS-based IoT solution for the construction industry, Trackunit, has already done the math:
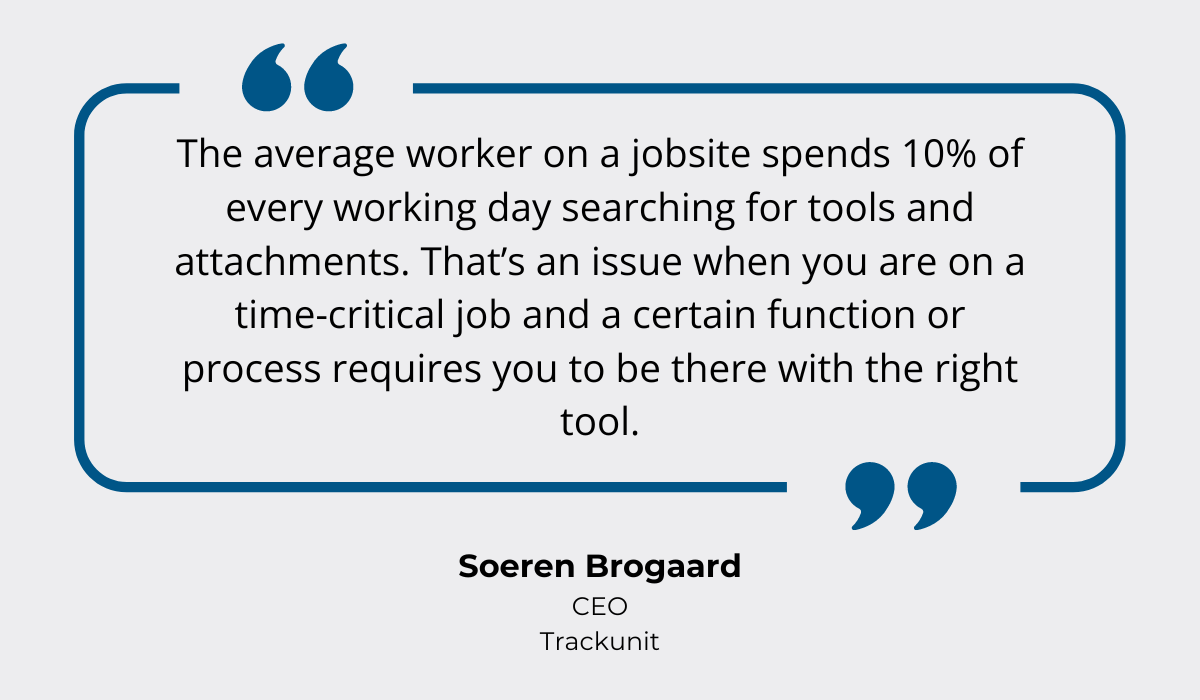
So, 10% per worker, per day—that adds up fairly quickly.
For someone working eight hours a day, five days a week, that amounts to four hours lost each week.
In other words, you’re paying that employee for four hours of looking around the job site rather than actual productive work.
But the problem goes even deeper than that.
Failing to implement a proper equipment monitoring system and constantly losing tools can lead to significant project delays.
Think about it: if you’re always hunting for critical assets, there will be less time to focus on the work that matters.
And this, yet again, adds another layer of unnecessary costs.
According to Cornerstone Projects, project delays, most of the time, cost anywhere from 10% to 30% of the original estimated build cost.
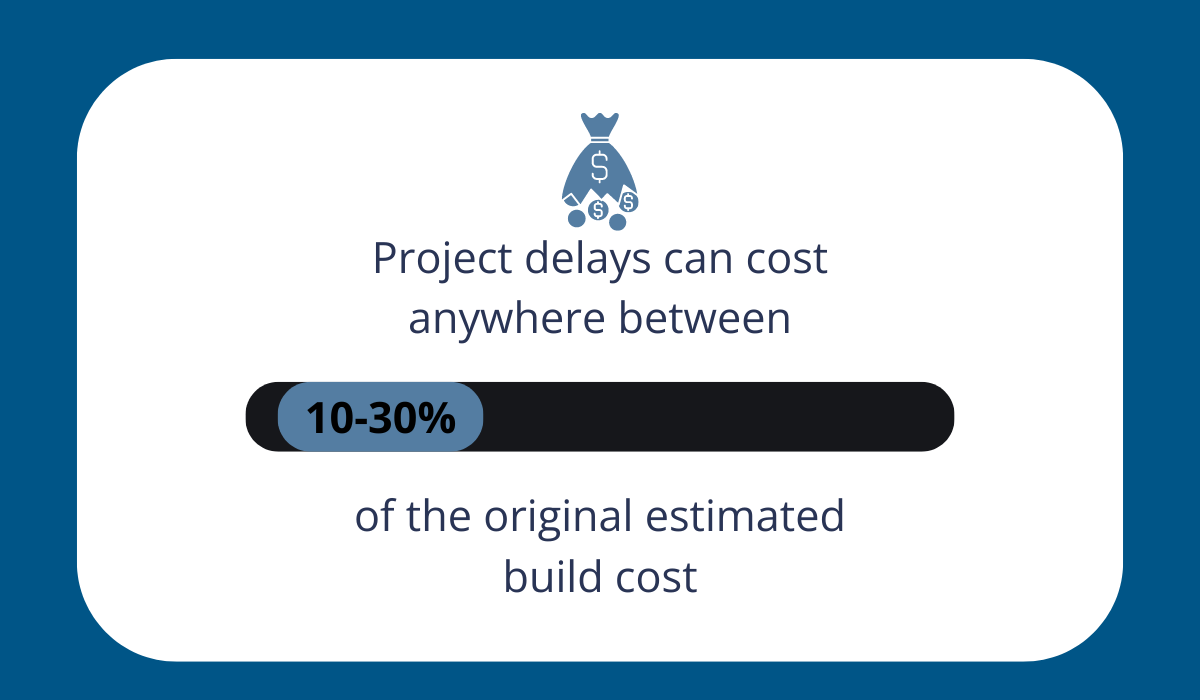
In some rare cases, they can be even costlier—over 50%.
In construction, any hit to productivity directly impacts the budget, plain and simple.
And neglecting small tool tracking is bound to cause operational disruptions, seriously harming your profitability in the process.
Costs of Tool Replacements
And what if the tool is never found?
What if it, for example, gets stolen?
Then your workers aren’t just wasting time looking for something that’s gone for good—now you also have to replace these assets, and that costs both time and money.
Many people mistakenly believe it’s the heavy, expensive machinery that gets stolen the most often, but that’s simply not the case.
According to Bauwatch’s 2024 Construction Crime Index, thefts involving stolen goods valued over £10,000 account for only 6% of all construction robberies in the UK.
In the majority of cases (64%), the cost of stolen items ranges between £500 and £4,000, demonstrating that smaller assets are actually the criminals’ target far more often.
After all, they’re much easier to take and sell discreetly.
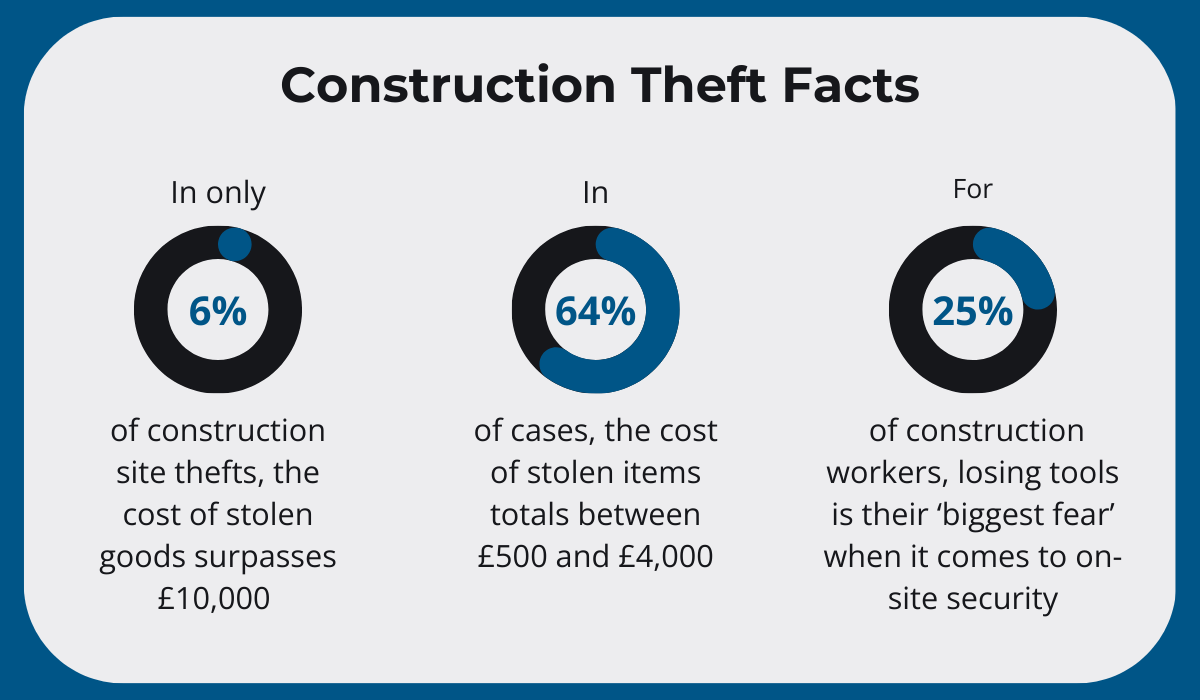
The survey also shows that, for a quarter of its respondents, losing tools is their biggest fear when it comes to on-site security.
And it’s easy to see why.
When you have to replace the missing equipment, you’re not only paying that £500 to £4,000 it originally cost.
There are a host of other factors to consider, such as:
- Time wasted sourcing replacements
- Extra costs for expedited shipping
- Time lost waiting for the replacement to show up
- Paying idle workers
- Potential project delays
See how even the smallest tools, if they’re crucial for the job at hand, can have a serious impact down the road?
And if you think it won’t happen to you—think again.
This Reddit thread is full of real-life horror stories about various tools getting stolen and the costs involved, showing just how often these things really happen.

That’s why it’s far wiser to have a proper tool tracking system in place from the get-go, rather than regretting it later.
Other Costly Consequences
The consequences of small assets going missing or getting stolen go beyond the obvious productivity and cost concerns, though.
For instance, losing tools and equipment can lead to poor worker morale, in turn resulting in higher turnover.
This is because, in situations like these, there can be a lot of blame-shifting or finger-pointing, disrupting team dynamics and creating a toxic work environment.
Add to that the fact that, without the necessary tools, workers can’t do their jobs efficiently.
This makes their work more time-consuming and exhausting.
All this leads to stress, frustration, and ultimately, valuable employees walking out the door.
With the labor shortages affecting the industry, that’s the last thing you need.
In fact, did you know that a 2022 AGC and Autodesk survey revealed that 66% of project delays were directly related to labor shortages?
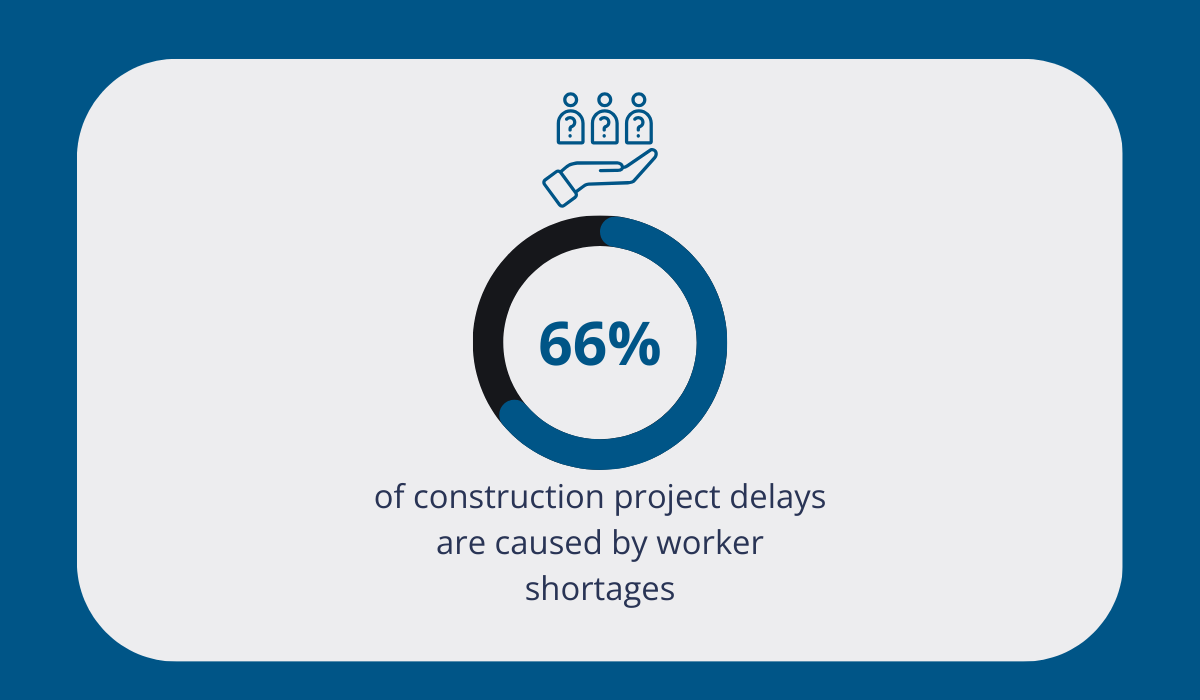
It’s clear that your workers are vital to your operations.
So why risk putting them (and yourself) in these situations by neglecting proper asset management?
This brings us to another issue: project delays caused by lost equipment can result in reputational damage.
The impact of this problem can be more immediate, like in the example below.
In that case, the client’s trust was undermined, driving them to consider hiring another contractor.
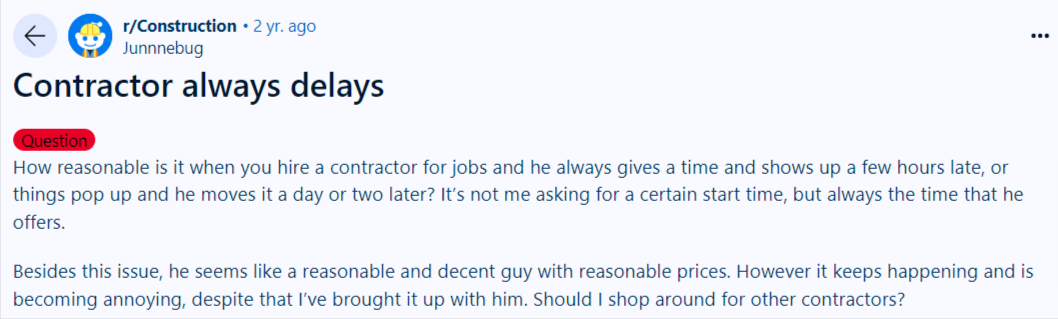
But, it can also have a long-term effect.
Becoming widely known as an inefficient organization can put you at a competitive disadvantage when competing for new contracts and cost you future business opportunities.
All in all, a lack of effective tool tracking clearly spells trouble, no matter how you look at it.
It affects profitability, operational efficiency, and overall company success.
So, what’s the solution?
How to Mark Small Tools to Prevent Theft & Loss
Effective small equipment tracking starts with one simple yet powerful step: properly marking your assets.
This alone can go a long way in minimizing instances of lost tools by preventing theft.
Gabe Marquez, Special Agent at the National Insurance Crime Bureau, elaborates.
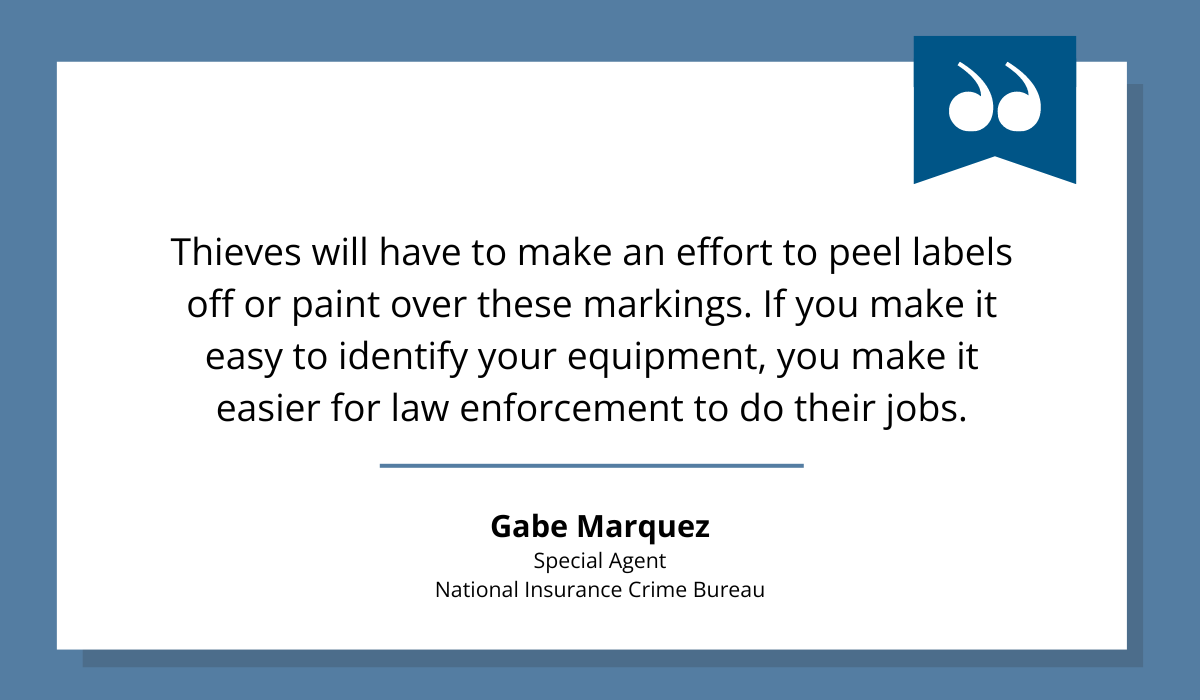
Essentially, the moment thieves see a marked asset, they know that the item is being tracked.
This could lead them to either abandon their plan or try to remove/cover the tag—something that’s not so easy to do.
Besides, as Marquez points out, even in the event of theft, these markings can be of great help in the identification and recovery of stolen items.
In any case, it’s very important to choose an asset tag or label that won’t get easily damaged or removed.
To make the best choice, consult our brief overview of common asset label materials and their attributes below:
Material | Cost/500 | Durability | Graphics | Flexibility | Adhesion |
---|---|---|---|---|---|
Paper(print your own) | $30 | Indoor, light-duty office applications | High-resolution, color | Yes, 1 dimension | Poor |
Poly | $400 | Mostly indoor, medium-duty, office and equipment | High-resolution, color | Yes, 2 dimensions | Good |
Foil | $650 | Outdoor or indoors | Medium resolution, B&W | Yes, 1 dimension | Good |
Metal | $650 | Outdoors, heavy duty, long life | Medium resolution, B&W | No | Excellent |
When it comes to tool tracking technology, QR code labels are an excellent option for smaller assets.
QR codes can be printed on any of these materials and are less invasive than other asset tagging techniques like pressing, engraving, or etching—you just simply attach them to your equipment.
This makes them versatile, cost-effective, and easy to use.
Plus, as you can see below, they can be very small, making them ideal for tracking even the smallest assets.
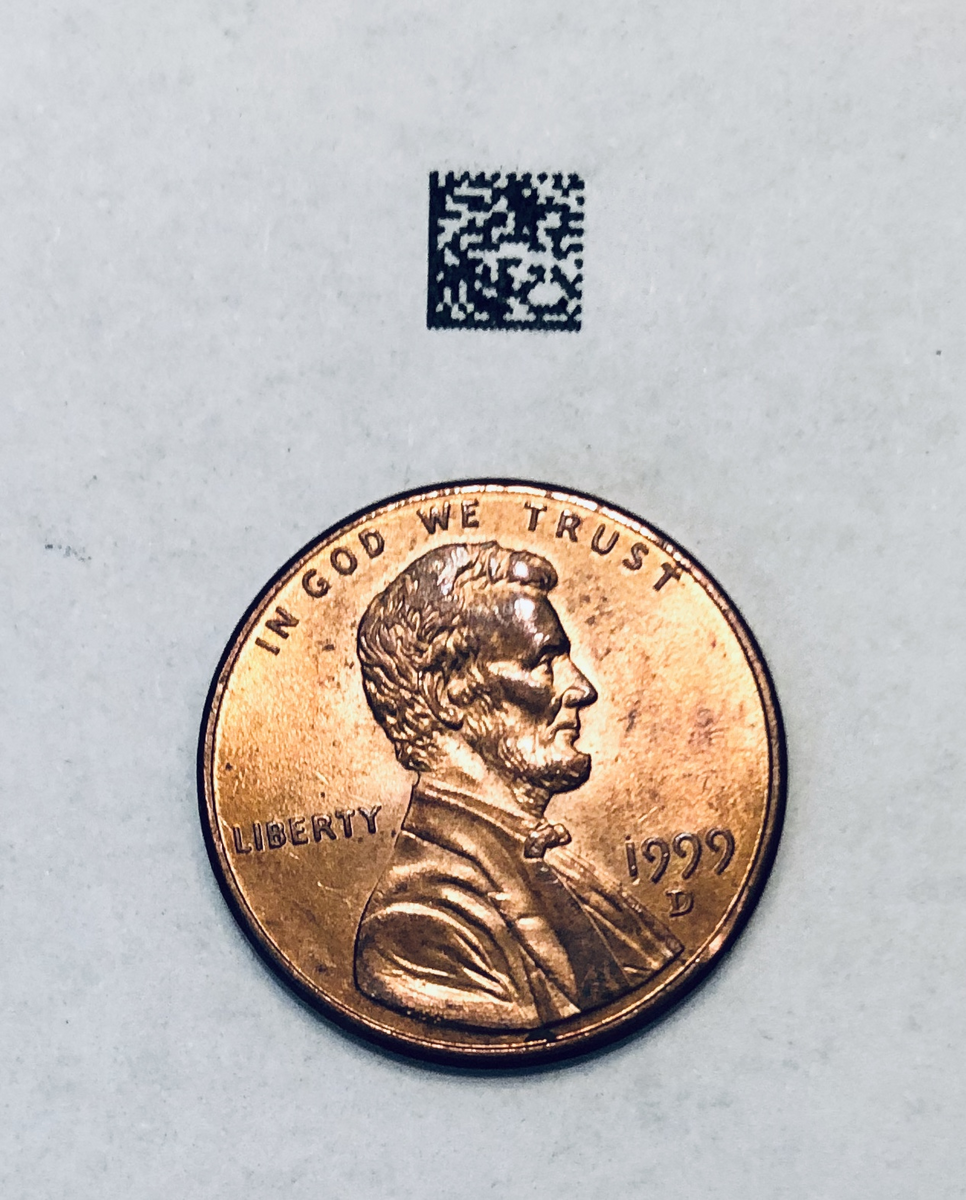
However, don’t let the size fool you.
QR code labels can hold much more information compared to many other marking methods, which gives them a range of uses beyond just theft prevention—but more on that later.
Benefits of Tool Kitting
Tool kitting involves grouping multiple tools necessary for a day’s work or a particular task into a single unit.
For example, if you have 15 tools stored in a truck for an extended period, this collection can be considered a kit.
In the context of small asset tracking, kitting can be very useful.
A kit typically includes items that are frequently used together, ensuring that everything your team needs is always on hand. No need to waste time looking around for tools.
They are also easier to manage overall.
Instead of keeping an eye on many different items, you only need to monitor that one consolidated kit.
This makes the process of tool tracking far simpler and more practical, significantly minimizing the chance of losing valuable assets.
Now, kitting can happen both physically and digitally.
On-site, you might have a toolbox or a storage unit where tools are grouped together.
Digitally, you can use asset management software to create and manage kits from anywhere.
Today, both are commonly used together for best results: physical kitting ensures practicality on-site, while digital kitting provides more transparent and accurate tracking across all of your kits and projects.
Below, you can see a kitting feature in action.
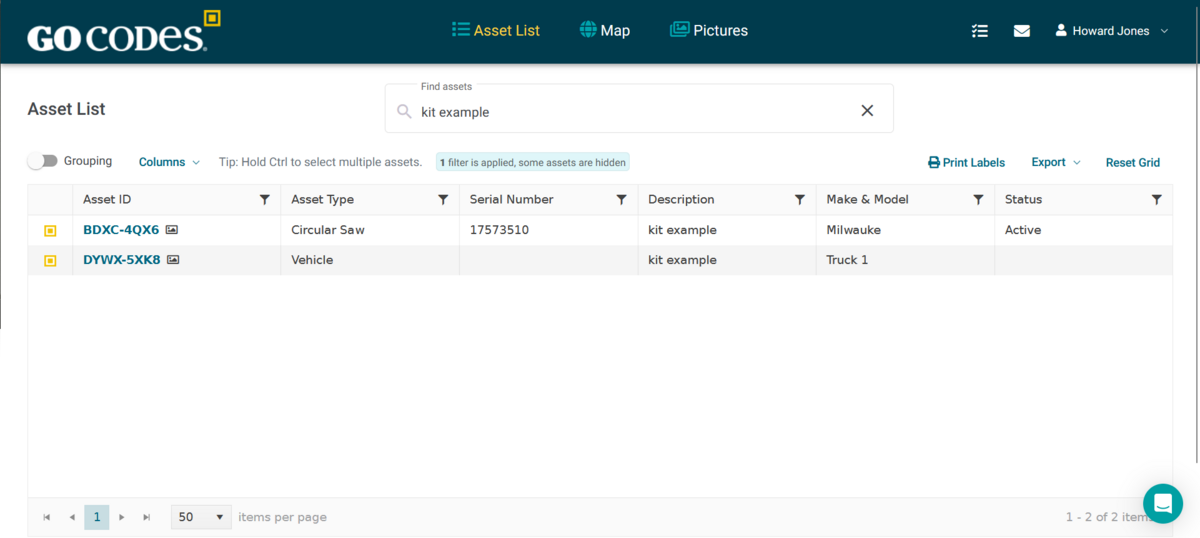
There are two items on this digital inventory list—a vehicle and a circular saw.
The saw can then be added to the vehicle’s kit with just a few clicks.
That way, anyone who accesses the asset’s data in the software can see it as part of that kit.

It’s also possible to check what other assets belong to this particular kit.
This setup not only helps keep track of where the group of items is located and who is responsible for it.
It also accounts for the tools within it without needing to track each individual asset separately.
Ways to Track Your Small Tools
There are many ways to track small equipment and tools, but they can be broadly categorized into two groups: manual and automated.
Manual tracking involves using non-digital systems like paper logs and semi-digital systems like spreadsheets to keep tabs on your assets.
With this method, inventory lists are maintained within Excel, tool checkouts are recorded on paper sign-out sheets, and maintenance or damage reports are all filled out by hand.
A great thing about this approach is that it’s straightforward as well as inexpensive, and—since most people are familiar with spreadsheets or pen and paper—training is minimal.
This isn’t to say, however, that manual tool tracking isn’t without its drawbacks.
Human error is a big risk here.
In fact, a survey by Acuity Training found that it’s quite common for workers to make costly and time-consuming mistakes while using Excel.
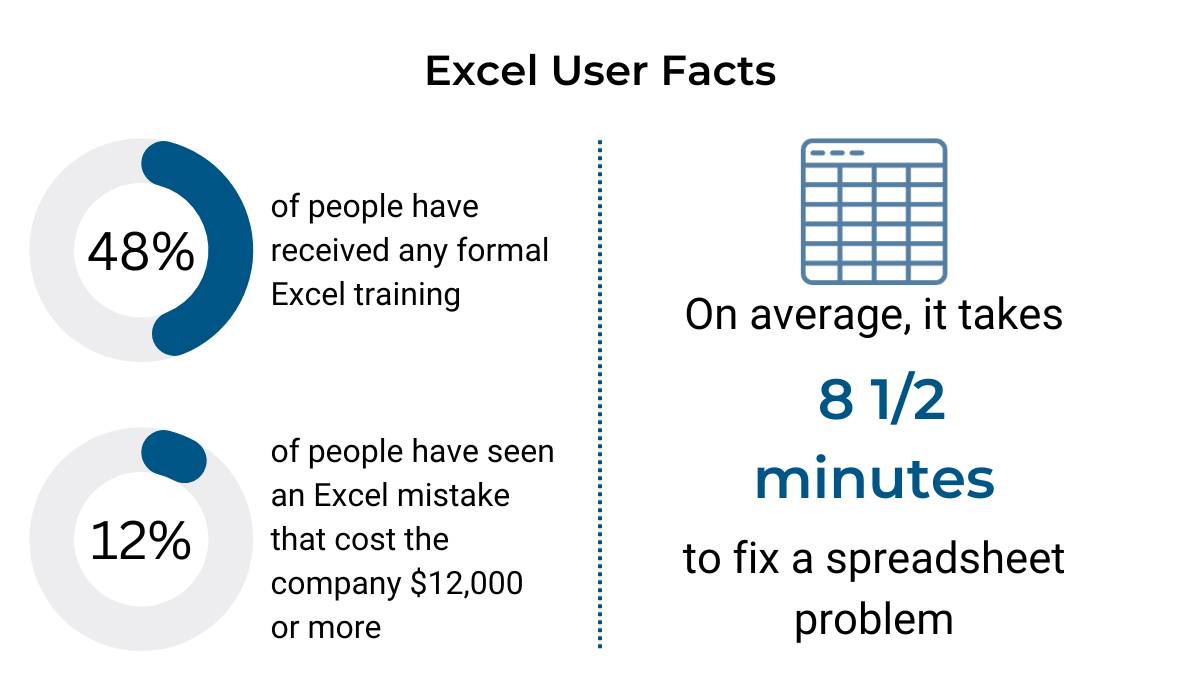
This can then result in inventory lists that are inaccurate, incomplete, and outdated, which is hardly ideal for small asset management, right?
Automated tracking, on the other hand, leverages various technologies such as asset management software and asset tags to manage small equipment data.
These digital systems automatically compile all relevant equipment information in a centralized database, which cannot be damaged or lost.
The result?
More accurate, timely, and reliable data that can be accessed from anywhere.
Ty Campbell, Director of Customer Success at United Rentals, North America’s largest equipment rental company, summarizes the benefits of such an approach:
“In today’s world, harnessing the power of digital technology to manage construction equipment just makes sense. There is plenty to worry about on the job site and digital tools should be an important part of managing complexity. This approach can help contractors streamline processes, save time, and gain greater control so they can deliver better results and have fewer safety incidents.”
Essentially, automation works wonders when it comes to streamlining unnecessarily complex tasks and takes small asset tracking to a whole new level.
But, how does it work exactly? And how tricky is it to set it up?
Let’s find out.
Automating Small Equipment Tracking
Automated small asset tracking offers capabilities that manual methods simply can’t match, saving you quite a bit of time and money in the long run.
But the best part is, it unlocks all these benefits without sacrificing user-friendliness.
Don’t believe us?
Let’s demonstrate how to set up and implement automated tracking using our own asset management solution, GoCodes Asset Tracking, as an example.
First, you attach the GoCodes Asset Tracking QR code labels to your assets.
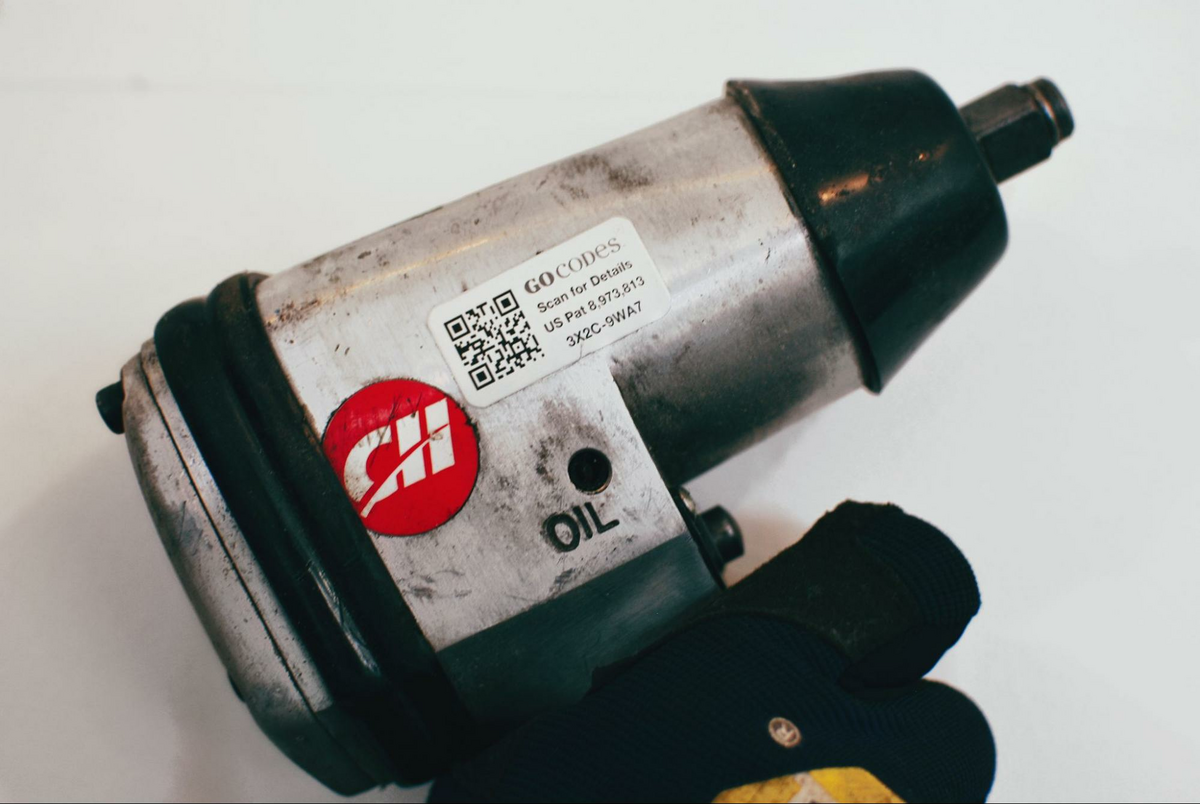
We provide these labels in a wide variety of materials, but you can also print them yourself if you’d like.
Each label is unique and contains a specific ID that is added to the GoCodes Asset Tracking tracking system, where you can build an asset profile for individual tools.
And remember how we said QR codes can hold large amounts of data?
That’s absolutely true: those profiles contain all sorts of information, from assets’ locations and current users to warranty details and salvage value.
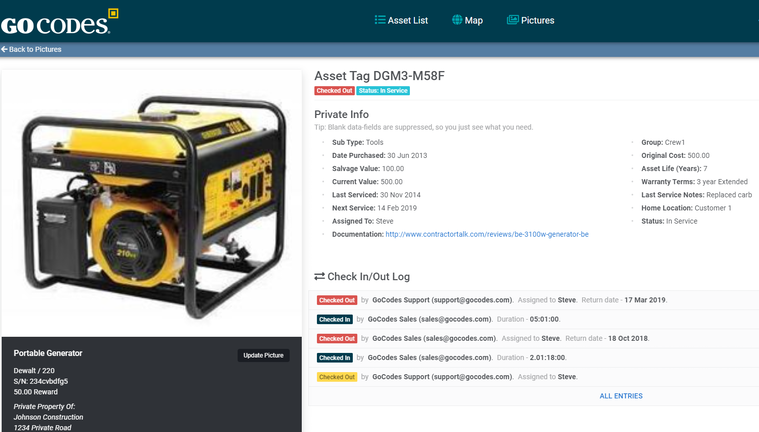
Okay, but how do you access or update these asset profiles?
Easy! With our intuitive mobile app, you can view and change equipment details on the go.
You just scan a QR code tag using the in-app scanner, and you can quickly:
- view asset information,
- check the asset in/out,
- update its location,
- assign a tool to a worker or project,
- update the asset’s maintenance log,
- request field service,
- set up automated notifications for overdue assets or upcoming maintenance,
- and so much more.
With a powerful yet user-friendly system like this, the chances of theft or misplaced tools are drastically minimized.
Just try and imagine a job site where even the smallest tools are all accounted for and where nobody has to waste hours every week looking for the equipment they need for the task at hand.
With automated asset tracking, that can definitely become a reality.
Conclusion
The bottom line?
The impact of small equipment on construction operations is not to be underestimated: neglect it, and you risk budget overruns, project delays, and even damage to your reputation.
Now, the good news is that managing small equipment and tools doesn’t have to be a headache.
Modern asset management solutions do practically all the heavy lifting for you, automatically tracking equipment’s locations, users, conditions, and utilization.
That way, it’s far easier to keep a close eye on your assets and allocate them more strategically.
So, give your tools the attention they deserve.
You’ll be rewarded with smoother operations, a more productive team, and disruption-free projects.