Construction material or quantity takeoffs are one of the key steps in winning project bids, ensuring a smooth construction phase, and completing projects on time, within budget, and with a healthy profit margin.
When done properly, a takeoff will provide precise quantities of construction materials needed for a project, empowering contractors to reap the benefits beyond accurate cost estimation for bidding purposes.
In this article, we’ll explore the intricacies of construction material takeoffs and their critical role in successful project management.
In this article...
Accurate Project Cost Estimation
As indicated, the primary purpose of construction material takeoffs is to provide a granular breakdown of material requirements and costs, facilitating precise budgeting for the entire project.
Before we delve deeper, a little background.
The term “takeoff” originated from the practice of builders manually taking off measurements from construction blueprints to identify the materials required for a project and calculate their quantities.
Traditionally, this process involved the use of tracing paper, rulers, and pens.
In contemporary construction practices, however, most companies now rely on partially or fully automated takeoff software solutions.
Additionally, some contractors prefer to outsource this process to specialized takeoff and estimating service providers, such as the one shown below.
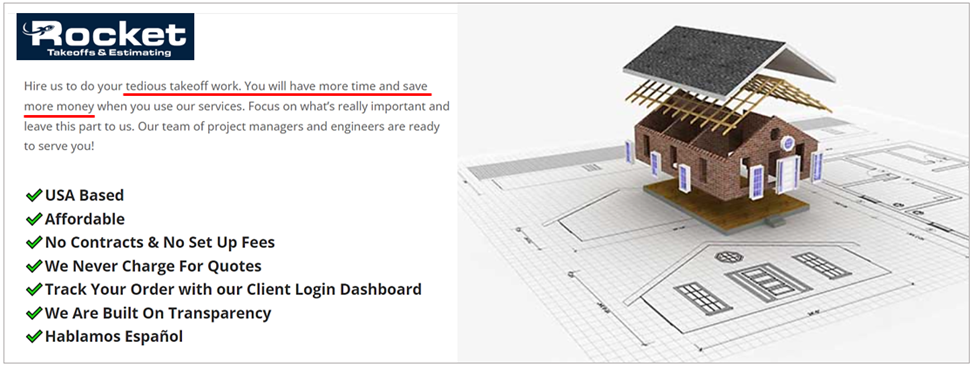
Regardless of how a material takeoff is performed, the process leading up to cost estimation involves:
- consulting project plans and specifications to determine which types of construction materials are referenced,
- creating an itemized list of all those materials (and other required components),
- going through the list and, by studying design drawings, calculating quantities for each item on the list.
This meticulous process will result in a Bill of Materials (BOM).
As illustrated below, BOM lists the types, measuring units, total quantities, and any other relevant details of all construction materials needed for the project.
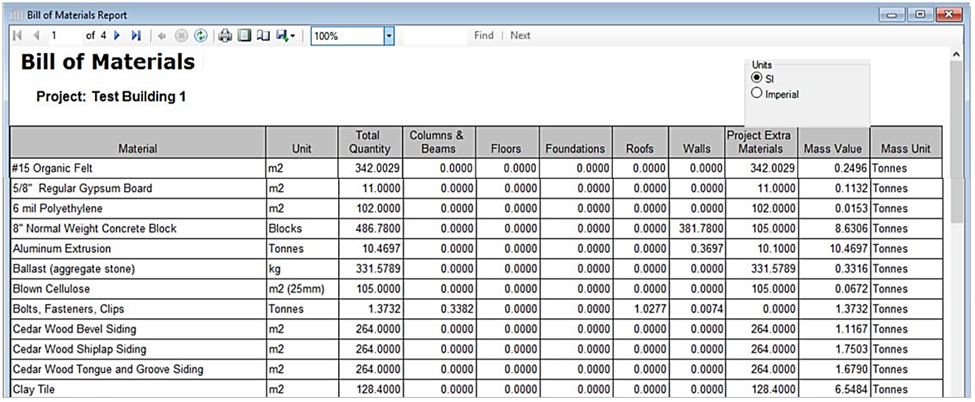
Regardless of many possible BOM formats and variations, this document serves as the foundation for accurate cost estimation.
More precisely, costs are estimated by assigning unit costs to each material, considering factors such as market rates, supplier quotes, and historical project data.
Therefore, any mistakes during the described quantity takeoff process can result in over- or underestimation of construction material costs included in the contractor’s project bid.
If these costs were excessively overestimated, they might not get the job.
If they were underestimated, such miscalculations—depending on their magnitude—can trigger a cascade of serious consequences like budget overruns, resource shortages, project delays, and contractual disputes.
Needless to say, this can negatively affect both the contractor’s bottom line and reputation.
That’s why a meticulous material takeoff process is crucial for precise cost estimation and, as we’ll see, all the other benefits explored here, starting with planning other resources needed for successful project completion.
Effective Resource Planning
In addition to more precise cost estimation, another advantage of a material takeoff is that it enables more efficient resource planning.
Put simply, a detailed takeoff allows for better planning and scheduling of not only material orders and deliveries but also other key project resources, namely workers and equipment.
More specifically, the Bill of Materials created during takeoff will serve as the blueprint for integrating the labor and equipment requirements associated with the installation or application of each quantified material and counted component.
All the material quantities, unit costs, and associated labor and equipment requirements are combined to create a comprehensive Bill of Quantities (BOQ).
A BOQ can take many different formats, but its item descriptions should follow a logical sequence of different works/activities needed for project completion.
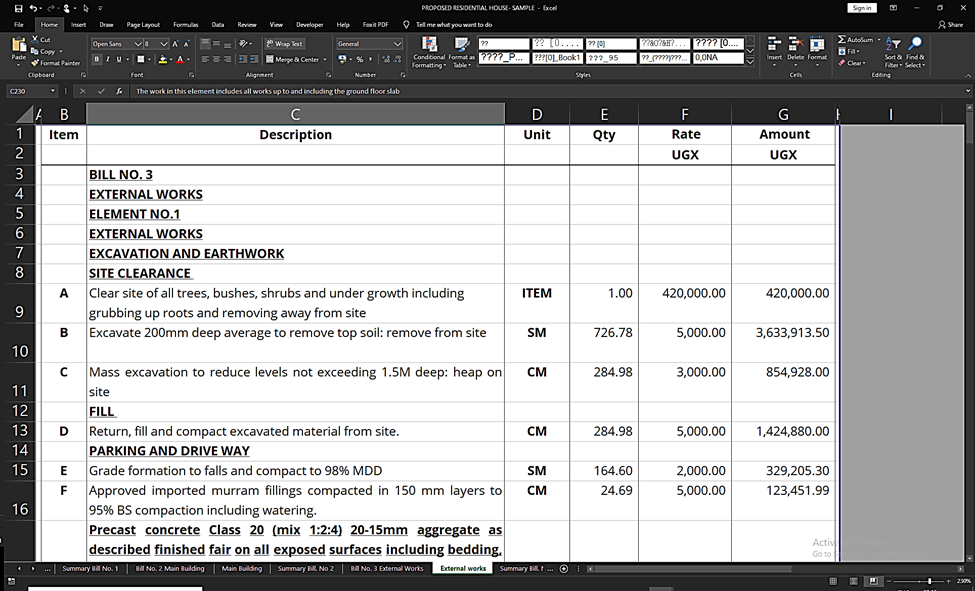
As you can see, a BOQ integrates the quantity of materials needed for a specific task with their work rates (material/labor/equipment/overhead/profit combined) and cost amounts.
By providing a detailed breakdown of the project’s resource needs, this document serves as a basis for accurate project cost estimation beyond materials.
Furthermore, this information aids in strategic resource allocation and scheduling after the bidding stage or, in other words, when planning construction.
It allows the project planning team to ensure that the necessary materials, workforce, machinery, tools, and safety gear will be available when and where needed.
Of course, more precise resource planning will prevent worker downtime caused by, for instance, not having the materials or equipment needed to perform a scheduled task.
Concurrently, the project team can optimize the procurement process, ensuring that materials are ordered in the right quantities and at the right time, reducing the risk of project delays due to material shortages.
On that note, efficient resource (equipment, tools, materials, and other physical items) planning arising from the takeoff can be further enhanced by adopting a QR code-based tracking system like GoCodes.
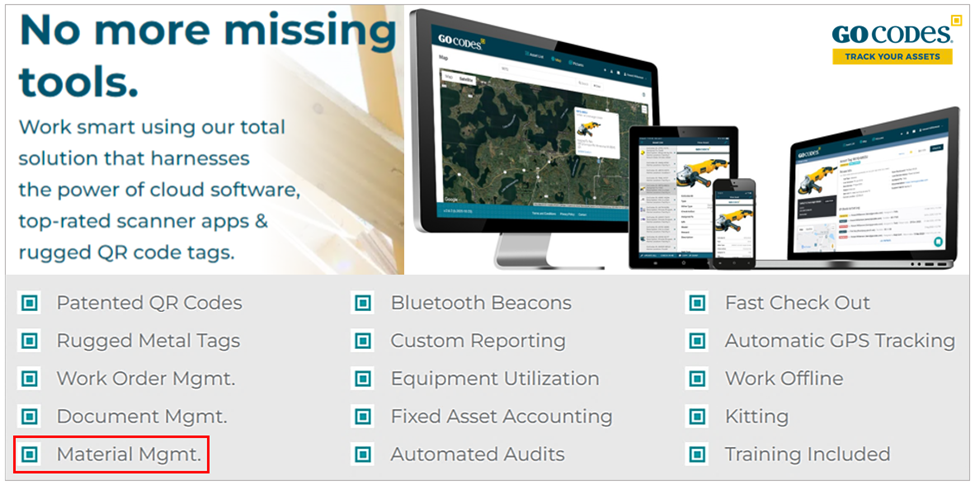
In terms of assets like equipment and tools, GoCodes enables easy access to a central database of all the company’s equipment and tools, their maintenance condition, current location, and availability.
This is extremely useful when planning equipment allocation across multiple projects, allowing managers to make informed decisions based on real-time data and maximize the utilization of valuable company assets.
As for materials, the same QR codes used for tracking assets can be utilized to track materials from their arrival to the jobsite/storage to the moment they’re used.
This provides an efficient and transparent way for monitoring on-site material usage and streamlining inventory (spare parts, other consumables) restocking processes.
Returning to takeoffs, it’s clear that a well-performed material takeoff is vital for identifying accurate labor and equipment requirements, creating the BOQ, and determining the project schedule.
By enabling effective resource planning, the project team can increase the overall efficiency of construction operations, ensuring that all the resources needed for smooth project execution are in place.
Minimized Material Wastage
As said, material takeoffs provide precise quantities of required construction materials.
With detailed material quantities in hand, the main contractor can avoid excessive purchases, which minimizes material wastage and promotes sustainable construction practices.
Therefore, reducing construction waste not only contributes to cost-efficient material management but also helps protect the environment, potentially boosting your company’s reputation.
In any case, the amount of generated material waste on a typical project can reach up to 30%, meaning there’s a lot of room for environmentally-friendly cost savings.
Again, reduced wastage will result from accurate material orders (and timely deliveries) enabled by the precise calculation of quantities during the material takeoff.
This allows you to plan ahead to minimize waste, along with other material waste minimization strategies shown below.
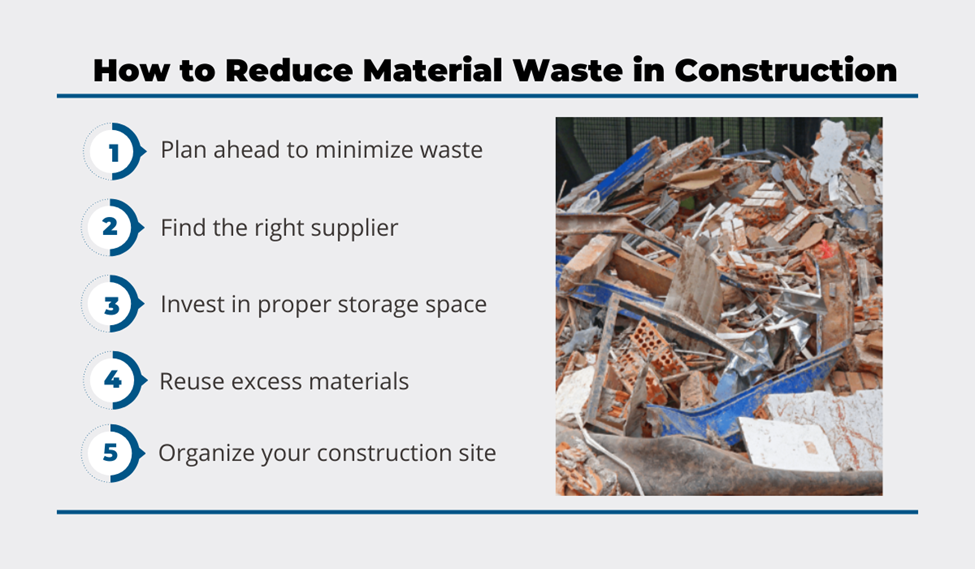
These strategies can help you implement effective project-specific and company-wide construction waste management practices.
For example, some excess materials, instead of being discarded, might be returned to the supplier (if so agreed beforehand) or strategically reused on other projects.
That said, a well-implemented takeoff remains the primary source of minimized material wastage in a construction project.
In summary, construction material takeoffs serve as the cornerstone for strategic planning, accurate ordering, and implementing effective waste reduction strategies throughout a project’s lifecycle.
Improved Accountability
Since they’re supported by documentation, material takeoffs create a tangible and accurate reference point for material requirements that ultimately enhances the accountability of all project stakeholders.
More precisely, the takeoff-derived comprehensive overview of materials facilitates the assignment and tracking of responsibilities for each project aspect.
This includes accountability for using the right materials in the right quantities and installing them in line with project specifications.
Moreover, when every material order, delivery, and movement is documented and accounted for, this also acts as a safeguard, reducing the risk of internal or external theft.
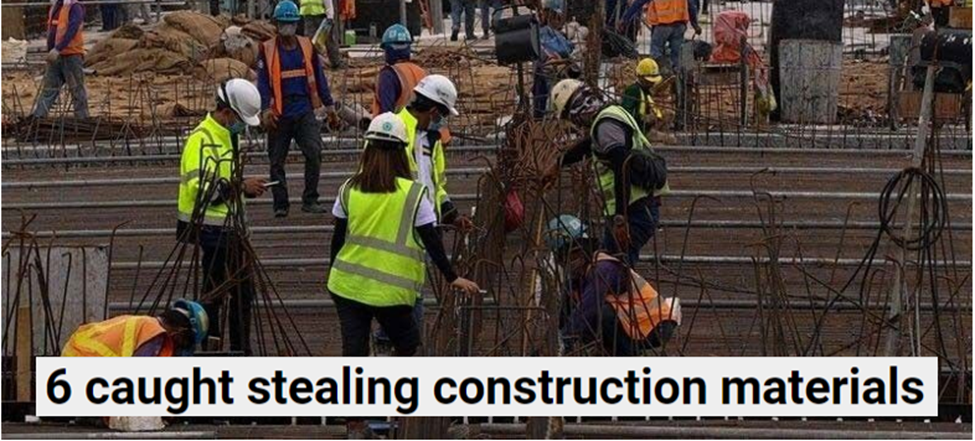
For instance, the site manager can regularly cross-reference the actual material usage on-site with the quantities specified in the material takeoff.
If there’s a significant and unexplained variance between the documented material quantities and the actual on-site usage, this will raise a red flag, indicating site security issues caused by internal or external actors.
This can be further improved by leveraging different inventory/asset tracking methods, such as GPS-enabled QR codes.
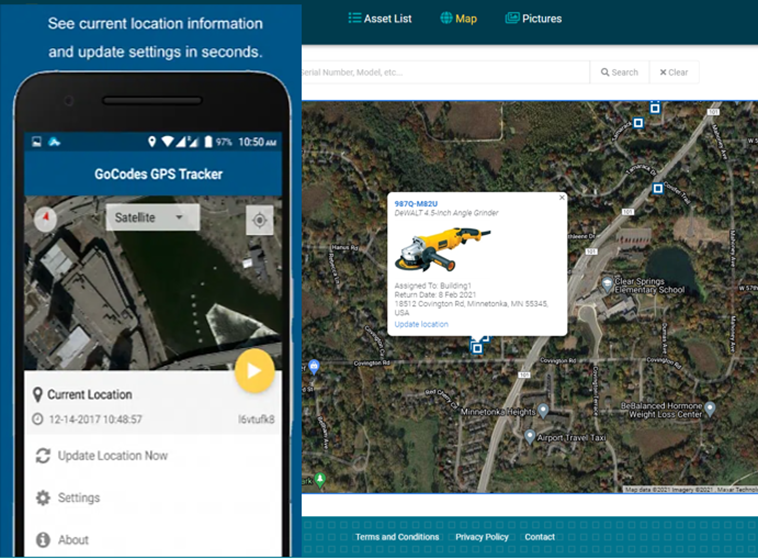
Beyond safeguarding against theft and malversations, material takeoffs also contribute to budget accountability.
They establish a framework for adherence to budget constraints, ensuring that project team members are acutely aware of the material cost implications at every stage of construction.
In conclusion, material takeoffs not only provide a precise roadmap for construction materials but also instill a culture of accountability, minimizing security risks and promoting financial responsibility throughout the project lifecycle.
Risk Mitigation
Construction material takeoffs play a pivotal role in proactive risk management by identifying potential challenges related to material delays, shortages, or cost fluctuations during project planning and throughout construction.
The detailed material specifications serve as a foundation for foreseeing and addressing these risks before they escalate.
In the planning stage, the project team can use the material takeoff data to identify any materials whose procurement might pose challenges, whether in terms of availability or long delivery times.
For example, in 2023, the below material pricing/availability trends could have been discussed during material-specific risk assessments:
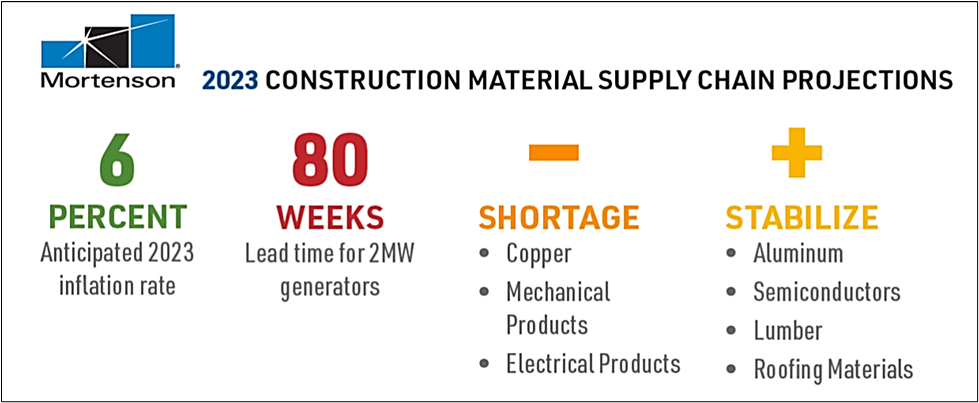
Such early identification of potential material supply issues allows for the implementation of effective risk management strategies, such as finding and proposing alternative materials with similar specifications but better availability and lead times.
When material shortages or delivery delays occur during the construction phase, exploring risk mitigation strategies is again more efficient with a well-executed material takeoff.
Whether it involves sourcing substitute materials, adjusting project timelines, or revising procurement strategies, the insights derived from the takeoff process facilitate informed decision-making.
To recap, construction material takeoffs not only unveil potential risks but also empower project teams to proactively manage and mitigate these challenges, contributing to the overall success and resilience of construction projects.
Client Satisfaction
Meeting or exceeding client expectations is a cornerstone of successful construction projects, and accurate material takeoffs play an important role in achieving this goal.
By providing a precise roadmap for material requirements, takeoffs contribute to all aspects of client satisfaction, namely completing the project on time, within budget, and with the agreed quality of the materials used and the works performed.
For instance, during project planning, the material takeoff specifics can be used to point out more cost-efficient (or more accessible or sustainable) materials to the client, allowing them to make informed decisions aligned with their goals and budget.
Along with on-time project delivery, this can increase client satisfaction, as well as build a positive reputation for your construction company.
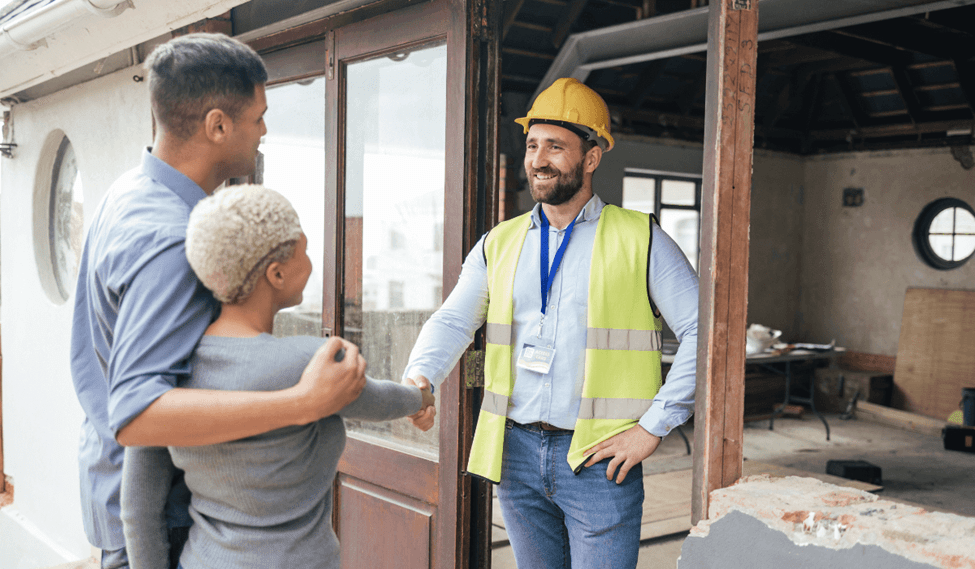
Simply put, a satisfied client is more likely to recommend you as a contractor to others, leading to potential referrals and additional business opportunities.
This ripple effect of client satisfaction establishes a foundation for your business’s long-term success and growth in the competitive construction industry.
Remember, a material takeoff underpins all other construction planning activities and documents essential for smooth project execution.
Therefore, accurate construction material takeoffs contribute directly to overall client satisfaction, improved business reputation, and the positive trajectory of your construction company.
Conclusion
In summary, construction material takeoffs are the linchpin for successful project outcomes.
As we’ve seen, they ensure more accurate cost estimates, better resource planning, and increased accountability of project stakeholders.
Likewise, they help mitigate risks and minimize material wastage, all of which contribute to smooth project completion and enhanced client satisfaction.
Leveraging advanced takeoff software and other construction management tools can significantly enhance the takeoff process, saving time, providing real-time data, and minimizing errors.
Therefore, when adopting technology, aim to streamline not only material quantification to reap the benefits we covered, but also other construction management processes crucial for project success, as well as your business’s reputation and profitability.