The construction industry is notorious for its slow implementation of new technology. As a result, any small improvement seems like a giant leap forward.
But as new trends and technologies emerge, construction companies will no longer have a choice in whether to adopt certain trends or not.
Utilizing these trends will become essential if they want to remain competitive, win more bids, and increase profit margins.
So, let’s look at the top construction industry trends that will become invaluable to any savvy construction company aiming to improve its business processes.
In this article...
Virtual Design in Construction
What if you could see your project’s drawings and plans as 3D models to better understand structural issues or change the design faster?
Well, that’s been a reality for decades.
Virtual Design and Construction (VDC) has been in use for at least 15 years, with the first methods created in 2001 by the Center for Integrated Facility Engineering CIFE) at the Stanford University of California.
The basic purpose of this technology is to create digital models of buildings to help different stakeholders visualize and understand a project’s design, processes, and schedules to enable better decision-making.
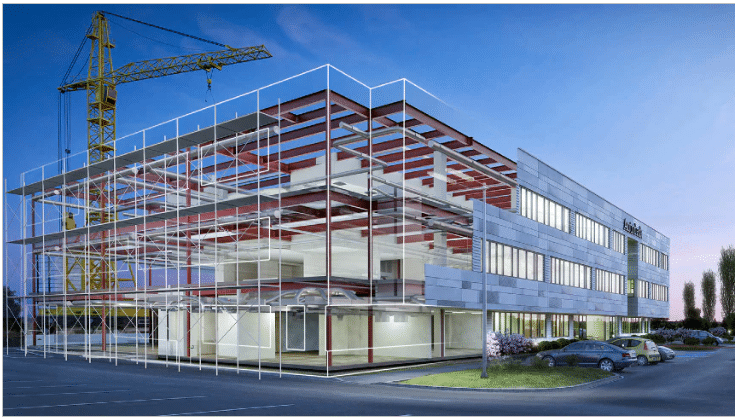
With this type of technology, everyone involved in the project should be able to see what a building will look like without prior knowledge about blueprints or technical drawings.
Because construction projects are extremely collaborative, ensuring everyone is on the same page when it comes to project requirements, risks, and final outcomes is essential.
Most importantly, in this way, the majority of potential risks and design changes can be addressed beforehand.
This requires fewer costly reworks and better control of the project’s schedule and budgets.
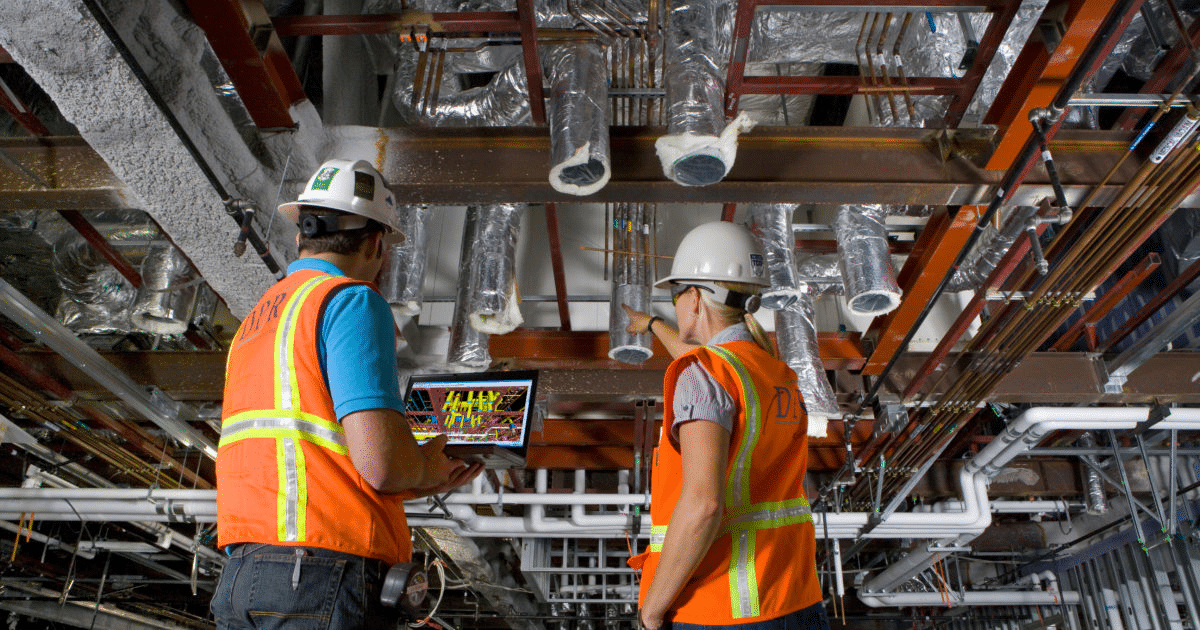
VDC is often compared to Building Information Modeling (BIM) technology, but while BIM is typically used for one aspect of a project, namely creating 3D physical renderings, VDC takes 3D models and integrates them with other data.
This enables the creation of a full digital plan of a construction project that can include estimating, scheduling, and risk management.
In a nutshell, if you want to save time and money, and deliver high-quality projects with better bids and estimations, join your peers that are already using VDC technology.
3D Printing
When it was first developed in the 1980s, 3D printing was extremely expensive to use and had few applications, but a lot has changed in the meantime.
Nowadays, 3D printing is a useful, affordable, and easy technique for many industries, including construction.
3D printing in construction (also known as additive construction) is a computer-controlled method of creating components, materials, or entire structures in a three-dimensional shape.
The design is printed by layering a printing medium (liquid, powder, sheet material, etc.).
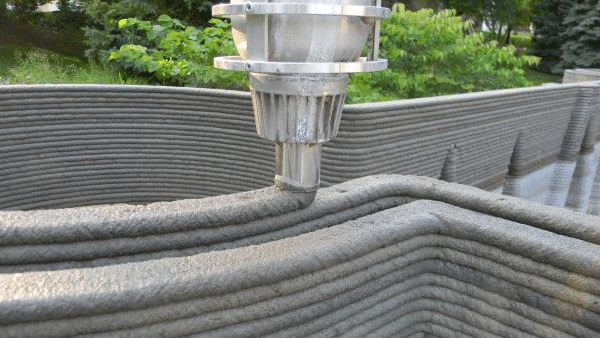
That means companies can create individual components or even entire buildings while simultaneously using fewer resources, producing less waste, and reducing human error.
This allows for increased productivity and more accurate construction of complex projects.
Also, according to Marco Vonk, Marketing Manager at Saint-Gobain Weber Beamix, 3D printing allows you to build faster than conventional construction.
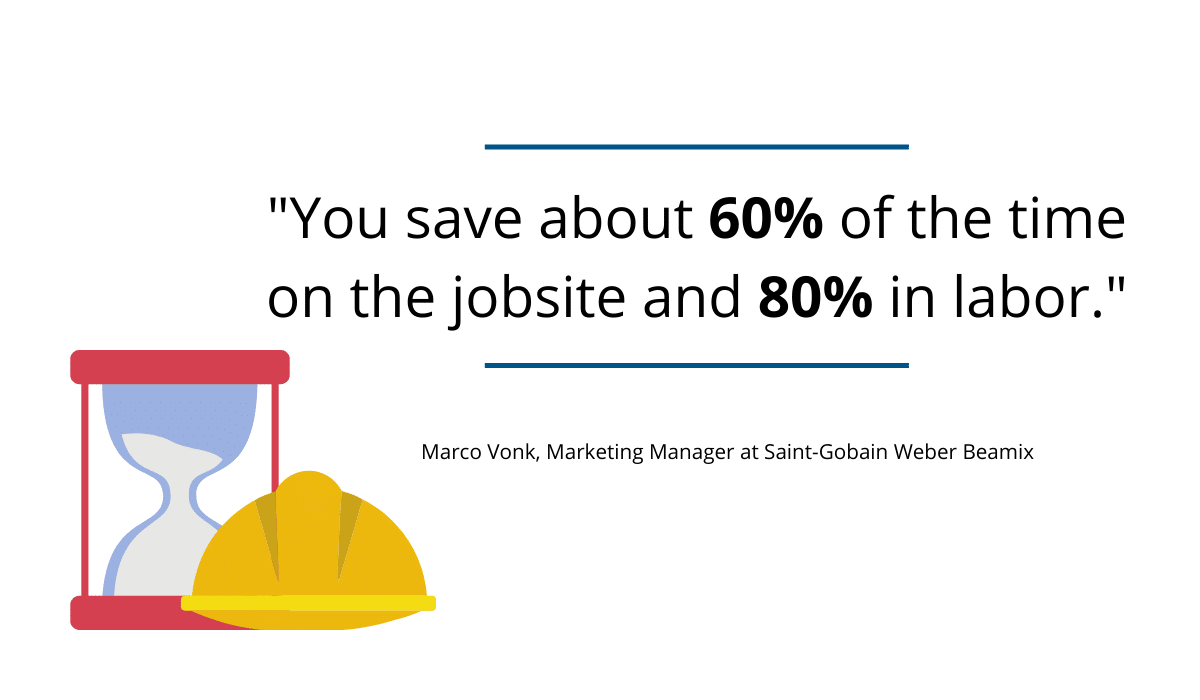
Because of this, many construction companies show an increased interest in 3D printing.
There are specialized companies working in various countries, for example, Yingchuang Building Technique in China, ICON in Texas, XtreeE in France, Monolite UK in the UK, and MX3D in the Netherlands, among others.
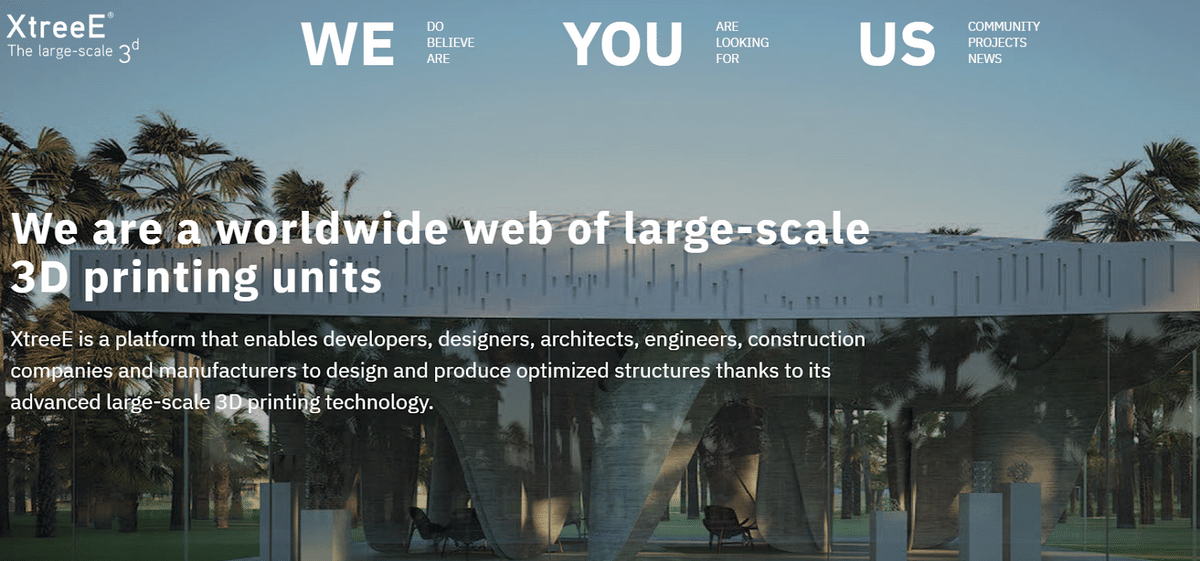
There have been numerous successful projects using 3D printing, but we’ll highlight one of the most impressive.
What makes this project special is that an entire 400-square-foot mansion was built in just 45 days.
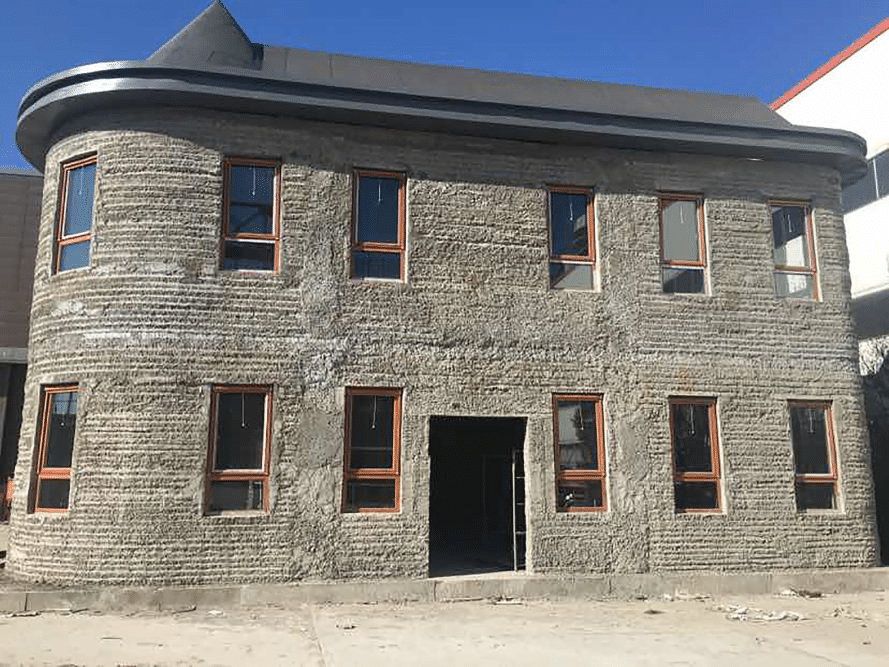
The company behind it, HuaShang Tengda from Beijing, used their own 3D printing technology to construct the entire building onsite.
Almost 20 tons of printed concrete went into the building, which is so strong the company believes the house can withstand a magnitude 8 earthquake.
In a nutshell, they were able to create a strong and safe building with modern technology in record time.
So, if you’re asking this Chinese company, the future of construction is in 3D printing.
Augmented Reality
The video games industry has dominated the augmented reality sector for years, but there’s room for the construction industry to take advantage of this technology.
As a person moves through a building, AR technology can project real-time data through a mobile device or a special helmet.
Information such as operational details and structural plans are easily accessible, and workers can make better decisions on site.
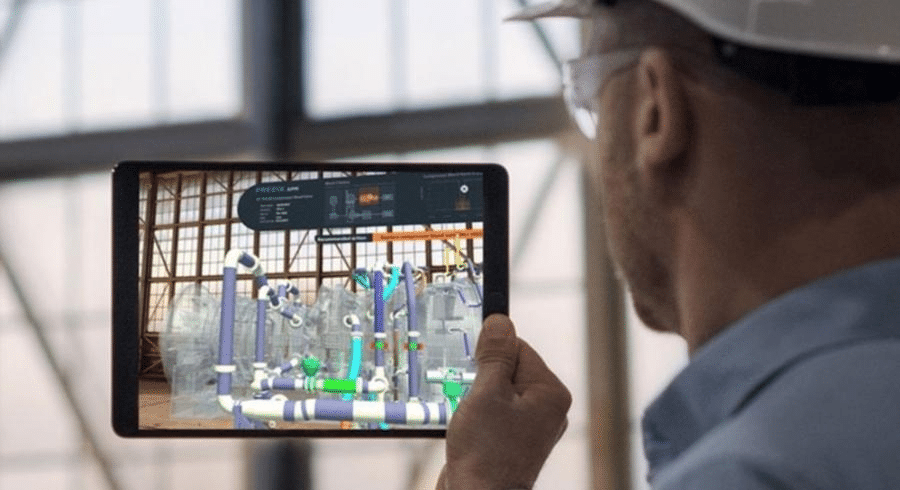
The main principle is similar to BIM (creating 3D models of a project), but AR combines the wearable technology and 360-degree video that helps engineers and developers with:
- 3D visualization of future projects in a real environment
- Fast simulation of project changes
- Safety training and hazard simulations
Furthermore, workers onsite can be instructed and assisted remotely by a supervisor to improve safety or streamline communication.
But let’s list all the benefits of AR in one handy table:
Project Planning | AR allows companies to produce detailed interactive models or walkthroughs of a project before construction even begins. With this insight, they can control delays, reduce costs and prevent mistakes better. |
Automated Measurements | AR devices can measure physical segments more accurately. This data allows for more precise material and labor estimations. |
Project Modifications | Using an AR device, workers can make virtual changes onsite, detect problems and inform the engineers before any actual changes are made to the physical structure. |
Team Collaboration | Sharing notes and reports with people who are stationed miles away from the construction site is easier. Issues can be resolved in real-time and change approval is faster. |
Companies like Akular AR provide 3D models of physical structures using smartphones or tablets.
With their technology, you can create VR/MR/XR site preparations to show your clients the projected final result of their plans or help your engineers and workers to mark issues and check progress.
Additionally, you can attach important documents to your 3D models, such as RFIs and drawings, to keep track of changes and reduce time searching for important information.
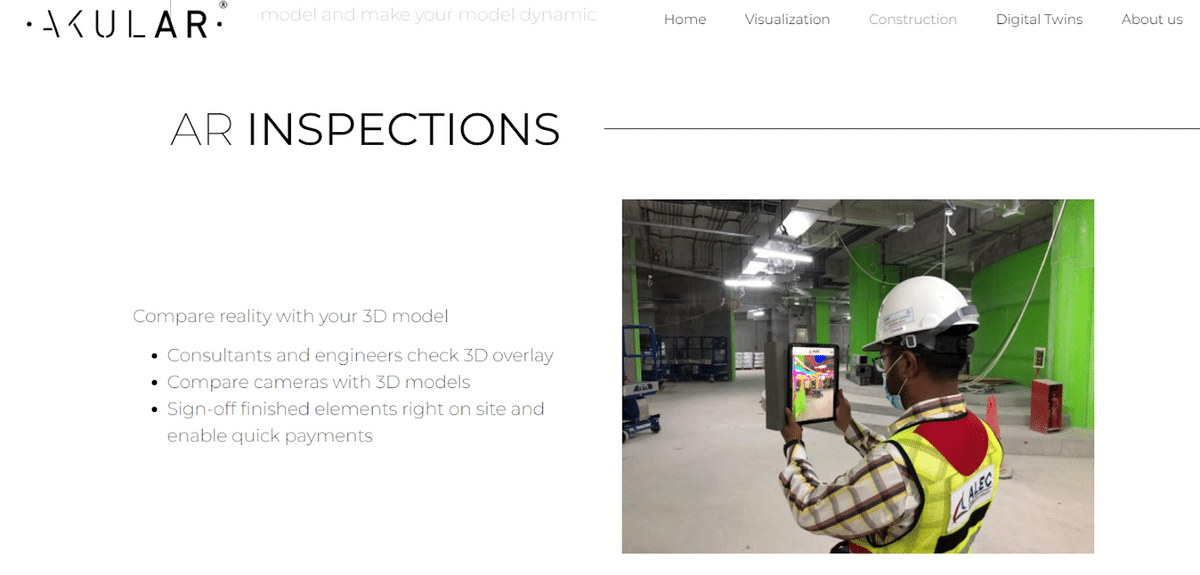
Currently, only large companies can afford to implement full-scale AR technology.
But with more competition, improvements in technology, reduced costs, and 5G expansion, it will become accessible to construction companies of all sizes.
Software Based Management
They say necessity is the mother of invention.
Or in the case of the construction industry, the need for more connected construction sites demanded an increased adoption of digital tools.
Construction companies worldwide need a better way for their teams to communicate, gather data, and make effective project decisions.
So, that’s where construction software comes in.
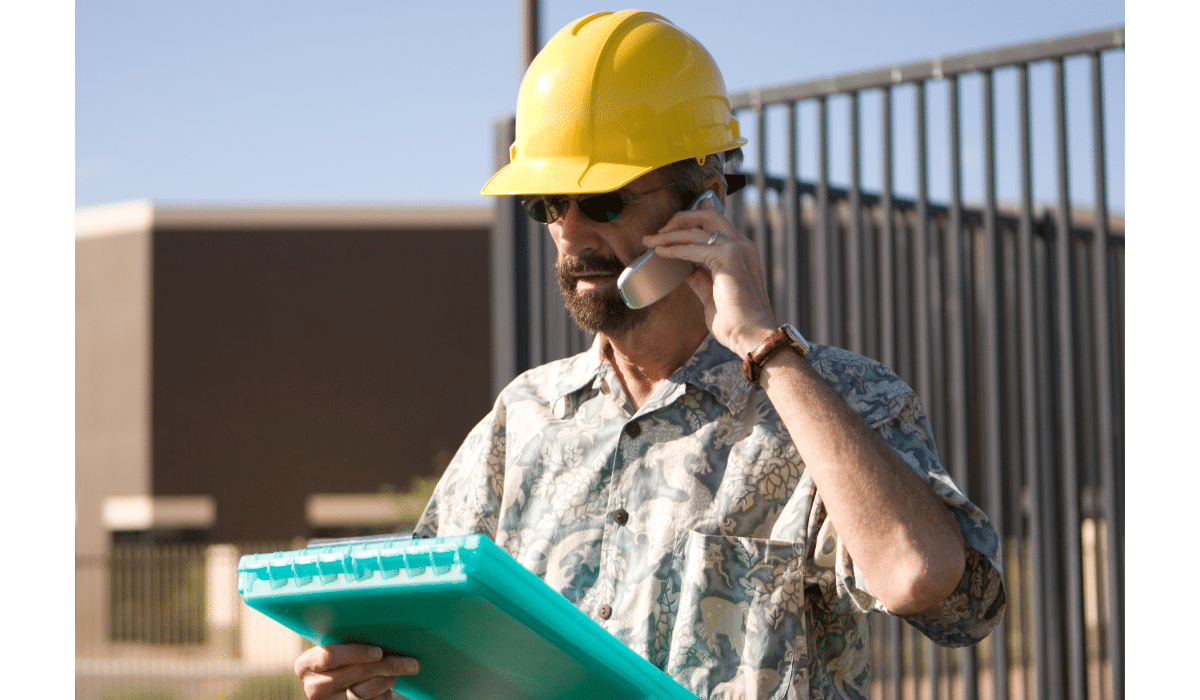
Essentially, construction software entails numerous digital tools that enable construction businesses to oversee their projects better.
There are comprehensive solutions that can take care of every aspect of the project, from bidding to billing.
Also, there’s more specialized software dedicated to particular segments, like asset tracking.
Here are some features of different construction software:
- Project management
- Takeoff
- Estimating
- Bidding
- Accounting
Moreover, according to Alex Turner, Group BIM Manager at Oktra, having construction software is a primary reason to remain competitive in this industry.
Those who utilize construction software to gather data have more insights into their project performance, analyze their KPIs better, and shift towards more sustainable practices faster.
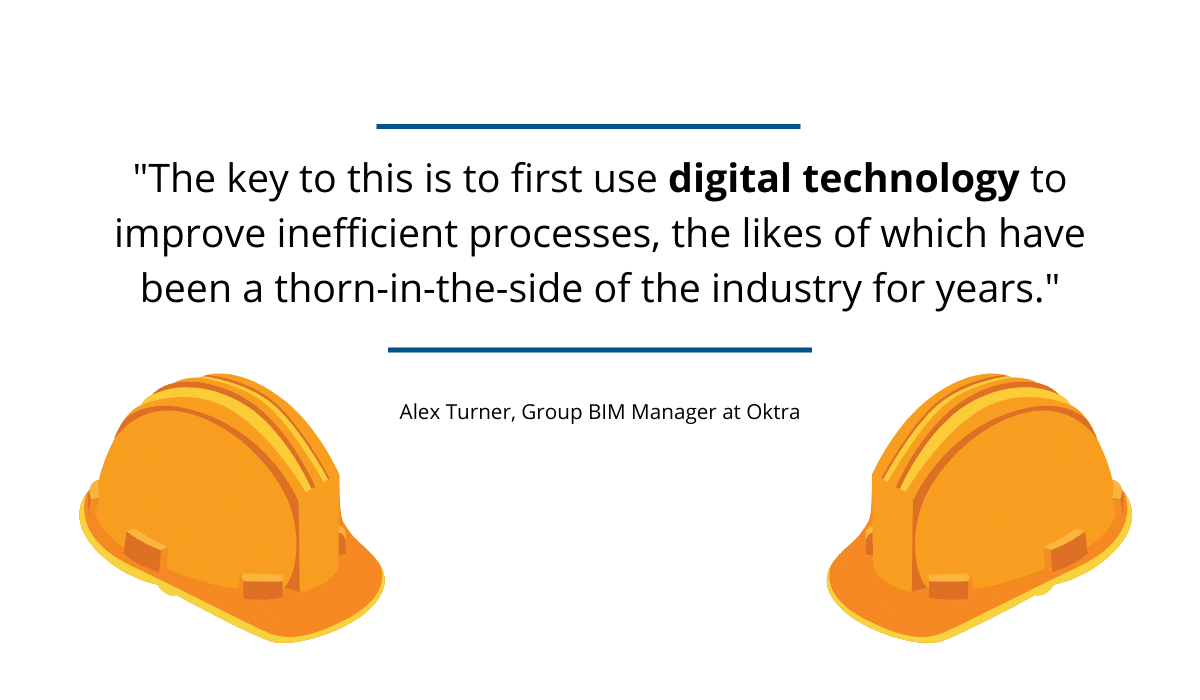
While using construction software is beneficial for any construction company, the most important thing is to find digital tools that will address your specific needs.
So, suppose one of your main problems is monitoring your assets.
In that case, GoCodes has user-friendly asset tracking software that gives you real-time information about your assets using a mobile device or laptop.
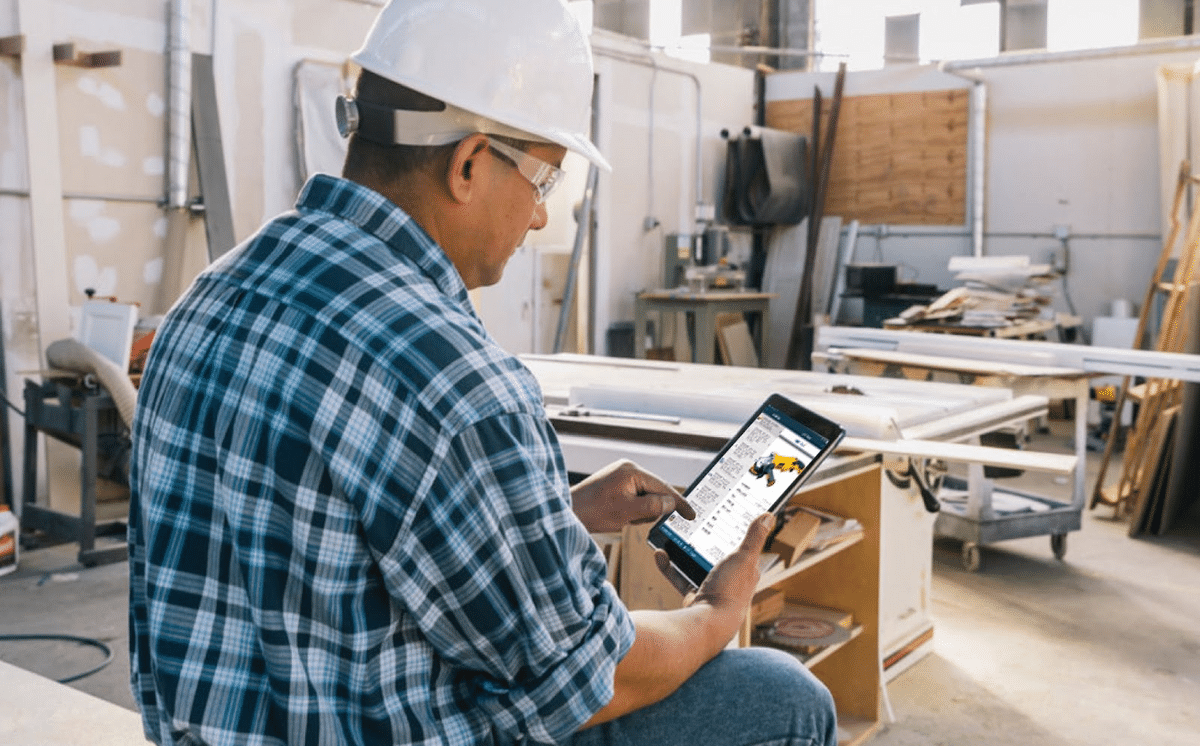
It all boils down to the fact construction software allows construction companies more agility and flexibility, especially regarding faster response to changing market trends.
Only those willing to invest in the right construction software for their company will emerge as leaders in the industry.
Green Building
According to a report by McKinsey, the new driving force in construction is the increased demand for more sustainable and eco-friendly structures.
Creating smart buildings with better energy savings and operational efficiency is slowly becoming more mainstream.
This is better known as green building or green construction.
The term covers sustainable practices from the pre-planning process to the final construction, like relying on the right technology to reduce the carbon footprint or using environmentally friendly materials.
A great example is the Bank of America Tower in New York, which some have called “the greenest office building in the US.”
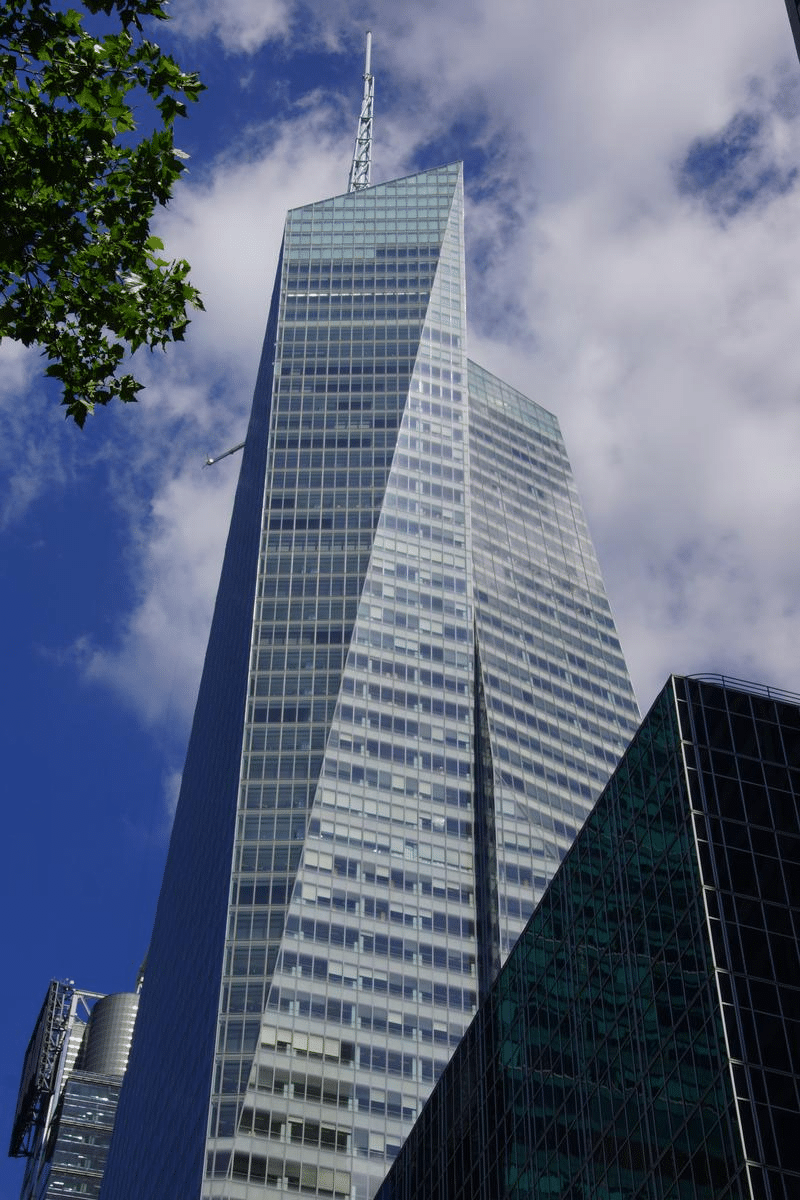
The very design of the building implemented sustainable principles.
For instance, the building has sloped walls because they take in more sunlight and collect more rainwater that’s later used for cooling.
This shape even allows more sunlight and air circulation for the neighborhood around it.
When it comes to construction materials, the skyscraper was created from regionally sourced and recycled materials.
To reduce the amount of concrete, the developer used fly-ash.
All in all, 83% of materials were recycled, which significantly reduced the amount of pollution during construction.
All these practices resulted in the Bank of America Tower receiving the LEED Platinum certification, as the first skyscraper to achieve this.
But building sustainably isn’t just about bragging rights.
There are great business benefits in switching to green building, based on a recent Dodge’s World Green Building Report.
Their respondents highlighted the following as the essential reasons to start building green:
- Lower operating costs
- Improved user health and well-being
- Future-proofing assets
- Education about sustainability
- Certification quality assurance
And there were some significant outcomes for Dodge’s respondents regarding green building, specifically in better finances.
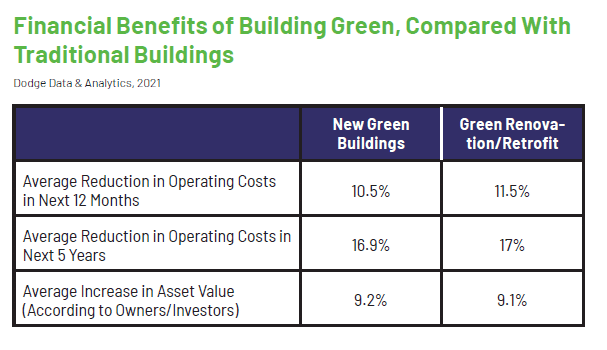
Keep in mind that clients worldwide want healthier living spaces that will last them for a long time with fewer maintenance costs.
Using sustainable construction methods, implementing renewable energy sources, and upcycling materials will produce such results.
Furthermore, such an approach will become a standard in construction.
The Dodge survey we’ve mentioned earlier shows that 42% of construction companies will have 60% of green buildings in their portfolio by 2024.
That’s nearly double what the companies were doing in 2018.
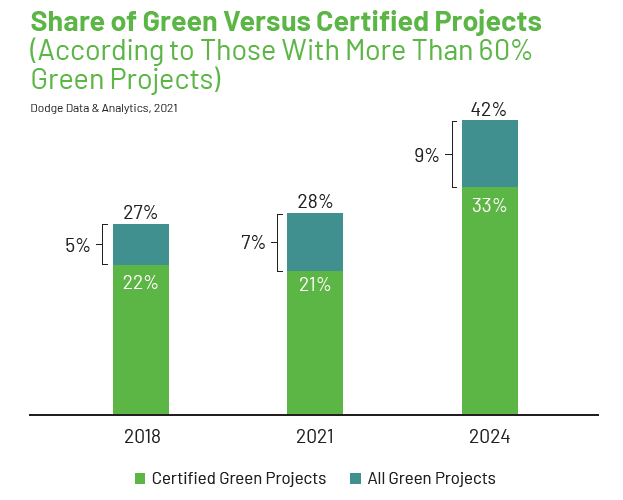
Based on these survey results and expert projections, we can safely say that green building is going to revolutionize the way we approach construction in the upcoming years.
Modular Construction
The global modular construction market is expected to reach $196 billion by 2026, with an annual growth rate of 7.1%.
These predictions are further supported by another Dodge’s report, where 90% of contractors see improvements in their projects when using prefabrication and modular construction.
Obviously, contractors find modular construction more beneficial than traditional construction.
Why?
To classify as modular construction, at least 60-90% of a building needs to be manufactured or assembled offsite.
These components are then transported and constructed onsite.
According to Paul Tansill, executive vice president at Affordable Structures, time and cost savings are the main benefits.
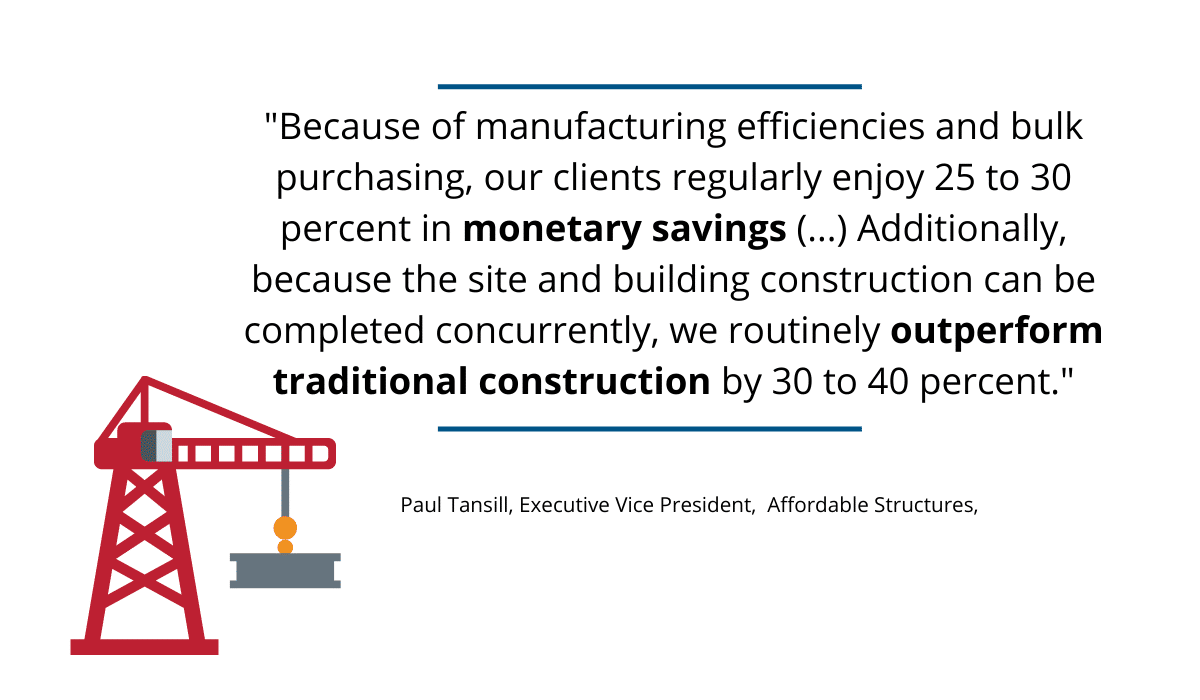
He believes offsite manufacturing to be more efficient, with better quality control resulting in 25% to 30% cost savings.
Also, because large sections of a project are completed offsite, you need less time to construct a building fully.
In some cases, modular construction can outperform traditional construction by 40%.
But here are some other things contractors have improved since starting to use modular construction:
- Productivity
- Quality
- Increased schedule certainty
- Reduced waste
- Safety performance
- Cost predictability
- Increased client satisfaction
One notable example is from Oakland, California, where PYATOK architecture firm and Cahill Contractors created a housing development with 110 units using modular construction.
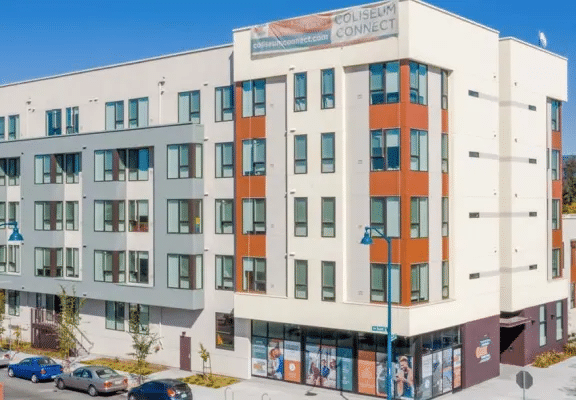
The Coliseum Connections consists of four buildings with two types.
The first is a five-story block of flats on the west side, and the second has three rows of townhouses on the east side.
Interestingly, all components for both types of units were created in a manufacturing facility Guerdon Enterprises in Idaho.
The site was completed in 2019, and the final cost was $43 million.
The team involved in the project said that the biggest challenge was coordination, planning, and finalizing decisions very early in the process, but the effort was worth it.
In the end, they were able to save $4 million compared to traditional building methods, and the completion time was 17 months (4 months less than traditional).
These savings also resulted in a very happy client who could begin collecting rent sooner than expected.
The main thing you can learn from this is that modular construction has many benefits you can take advantage of.
This will help you stay competitive and create a sustainable business.
So, keep modular construction in mind as one of the trends to look out for.
Conclusion
Judging by these trends, the future of construction is bright, both for the end-users and construction companies.
On the one hand, you might benefit from new materials, processes, and digital tools to upgrade your business practices.
On the other hand, your clients will get to monitor the project with advanced 3D and AR technology from the beginning and get the sustainable building they want.
The possibilities are endless if you watch out for these construction industry trends.