Key Takeaways:
- Labeling helps with identification, organization, and maintenance tracking.
- Durable label materials ensure readability and longevity in harsh environments.
- Integrating labels with asset management software improves efficiency.
Properly labeling your equipment is important for a number of reasons.
Clear labels make it easy to identify equipment and help with inventory management, tracking maintenance, and overall organization.
But if you intend to do this practice right, there’s much to consider. It’s not as simple as putting a sticker on your tools.
This article will cover some of the most important aspects of equipment labeling, including the materials used, different types of labels, and some common mistakes you’ll want to avoid.
So, if you’re looking for a thorough guide to help you create an effective equipment labeling system, you’ve come to the right place.
In this article...
Why Effective Equipment Identification Matters?
The most important thing to consider when improving your labeling practices is proper equipment identification.
Equipment identification is the process of giving each piece of equipment a unique identifier so you can easily distinguish it from others.
This might seem basic, but it’s the foundation of efficient operations.
In fact, identifying your equipment quickly and accurately has a ripple effect, benefiting multiple aspects of your operations down the line.
As Mike Sondalini, a senior asset management consultant, explains, proper equipment identification can save significant time and resources.
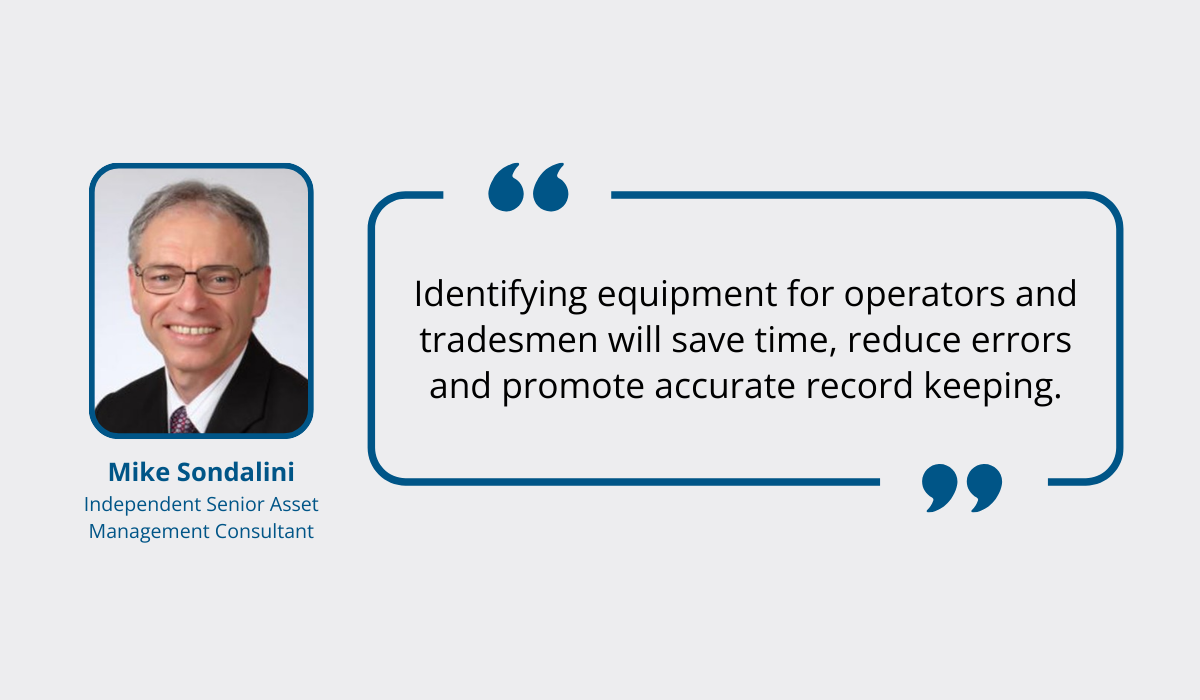
He recalls a site where equipment was identified not through labels, but through drawings.
This practice led to misidentification and errors in work orders, resulting in project delays and incorrect record-keeping.
However, once clear, durable labels were implemented, these mistakes dropped significantly.
The takeaway?
This change likely happened because readily visible labels provided immediate and accurate identification.
That, in turn, eliminated the need for time-consuming searches through drawings or reliance on potentially inaccurate memory.
Identification is also worth considering due to the unfortunate possibility of equipment theft.
In fact, the National Equipment Register (NER) reported 542 heavy equipment thefts in 2024, with the most frequently stolen equipment types shown below.
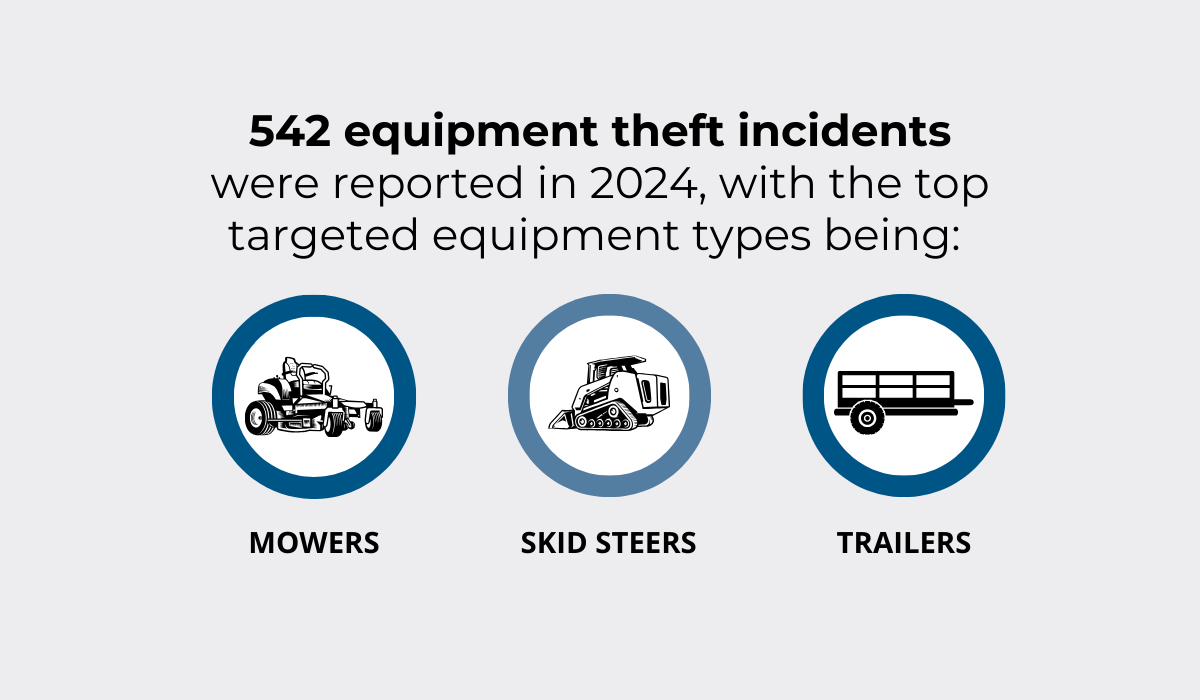
And remember, these are just the figures for heavy equipment.
When you factor in the much easier thefts of smaller, more portable equipment, you can see how significant of a problem this can be.
Fortunately, proper labeling can assist in theft retrieval.
A unique identifier on your equipment makes it much easier to track and recover if it’s stolen.
Plus, it gives law enforcement clear evidence of ownership.
All in all, effective equipment identification is crucial for daily operations and for protecting your assets.
Types Of Equipment Labels
All the benefits we’ve discussed so far only apply if you’re using the right labels.
Choosing the correct type of label is crucial as different label types serve different needs.
Also, environmental conditions and equipment types can have different labeling requirements.
In this section, we’ll talk about both the technologies used for labels and the materials they’re made of.
For a quick overview of the most common label technologies, take a look at the table below.
Label Type | Pros | Cons |
---|---|---|
Barcodes |
|
|
QR Codes |
|
|
RFID Tags |
|
|
NFC Tags |
|
|
For a more in-depth look at these technologies, we encourage you to check out our other article on the topic.
Generally speaking, though, you can choose RFID and NFC tags for greater information storage, although they come at a higher price point and with some other drawbacks.
Alternatively, you can opt for the straightforward solution of barcodes, which offer limited data storage.
Or, you could take the balanced approach with QR codes, which offer a good compromise between data capacity, cost, and ease of use.
Now, let’s talk about the materials used for equipment labels.
Take a look at the illustration below, ranking different materials by their durability.
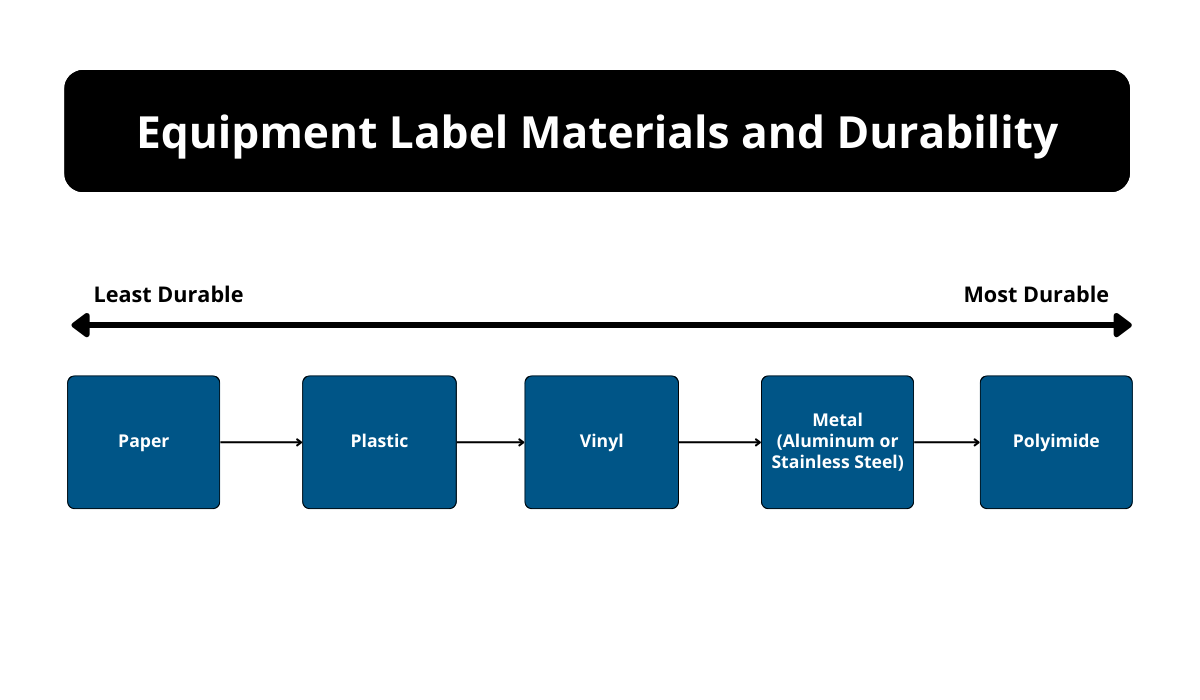
If you expect your equipment to endure rough treatment, harsh environments, or extreme temperatures, metal labels (like stainless steel or anodized aluminum) or polyimide labels are preferable to less sturdy options like paper or some plastics.
These durable materials ensure your labels remain readable and stay attached even under challenging conditions.
But, we have to mention that NFC and RFID tags rely on special electronics to function.
This means they aren’t compatible with all materials and are usually made with specific plastics and polymers.
Overall, when deciding on your labels, consider the technology you’d make the most use of and all the material options available.
Serial Numbers vs. Randomized Unique Identifiers: Which Should You Choose?
As part of your equipment labeling system, you’ll want to use an identifier number to properly track each specific asset.
Here, you have a choice to make: serial numbers or randomized unique identifiers (RUIDs).
Most people default to using serial numbers because they seem simple and are often already present on equipment.
However, there’s a key fact to consider—serial numbers are not unique.
Larry Silverman, CTO of TrackAbout, a provider of asset tracking software, provides an explanation on why that is the case.
Namely, while a single manufacturer might use unique serial numbers for a specific equipment type, there’s no guarantee you won’t encounter duplicate serial numbers on equipment from different manufacturers.
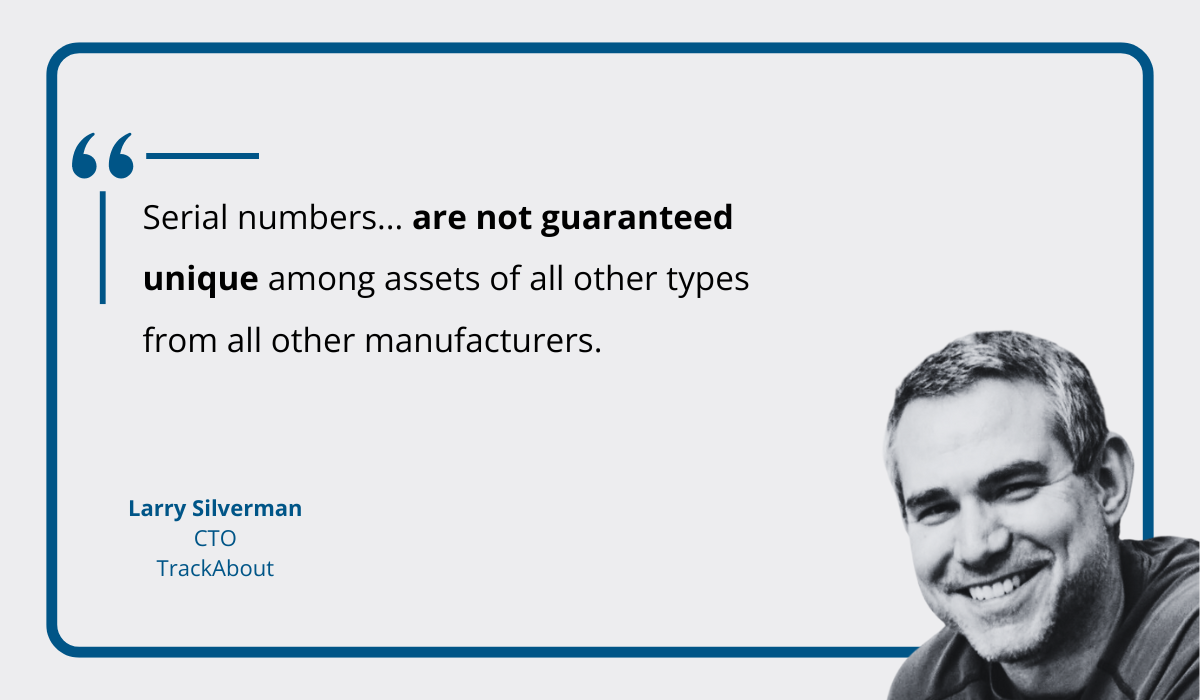
This occurs because each manufacturer maintains its own numbering system, and there’s no universal standard enforcing uniqueness across all manufacturers.
Ultimately, this defeats the entire purpose of using a serial number for tracking, as you want a system where each piece of equipment has a truly distinct identifier.
So, instead of relying on potentially redundant serial numbers, it’s recommended to use RUIDs.
RUIDs or Randomly Generated Identifiers are designed to be globally unique, eliminating the risk of duplicates and ensuring each piece of equipment has a truly distinct identification.
GoCodes Asset Tracking, for example, offers these types of identifiers as part of our QR code labels.
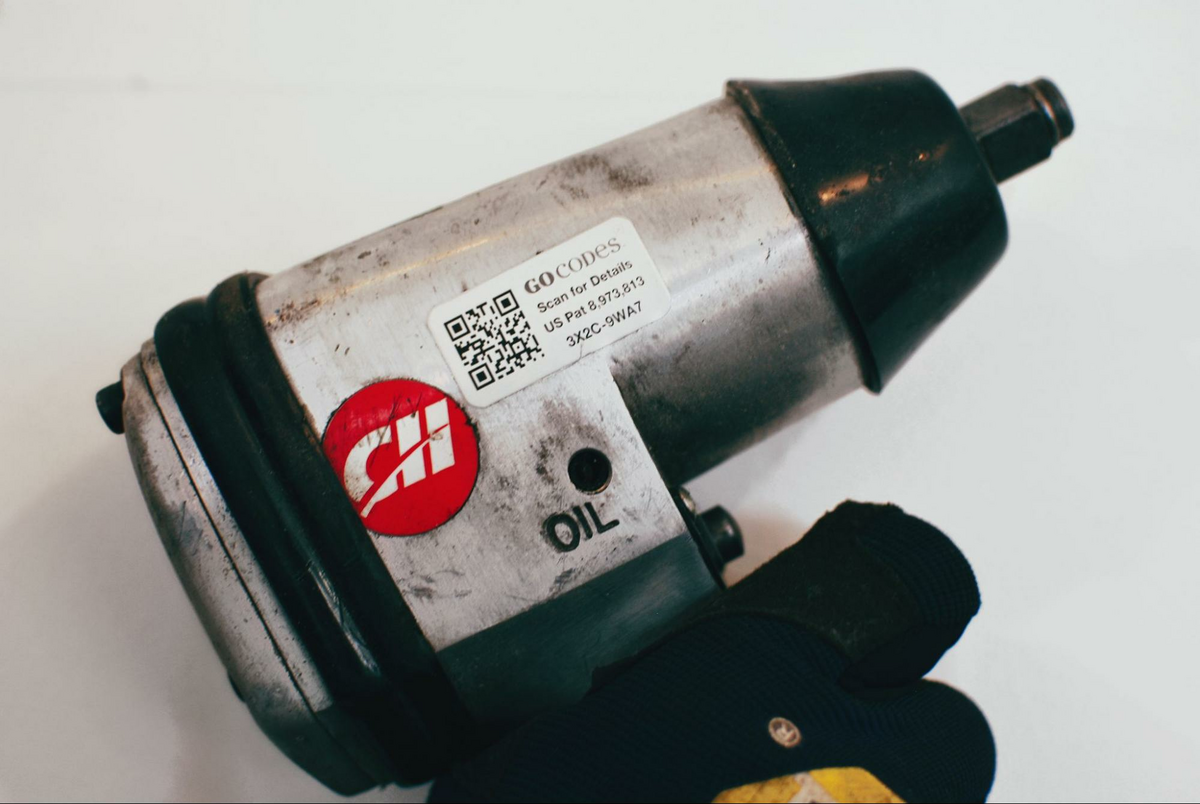
In fact, each of our asset tags or labels comes with a globally unique, randomized 8-character code.
This means that the identifier number is unique only to the specific piece of equipment you use it for.
You won’t find a duplicate among any of your other assets, even if you have hundreds or thousands of them.
This allows for accurate and reliable tracking and optimized maintenance and inventory management.
Plus, due to the nature of our RUIDs, the chance of an asset being identified when an invalid code is entered is extremely low.
To summarize, it’s clear that with unique identifiers, you can confidently track and manage your equipment throughout its lifecycle, avoiding any confusion and errors caused by serial numbers.
Mistakes to Avoid When Labeling Equipment
Finally, we’ll cover three common labeling mistakes that can significantly impact the effectiveness of your equipment identification system.
Avoiding these mistakes is crucial for ensuring your labels provide accurate and reliable information throughout their lifespan.
Let’s begin.
Not Being Careful With the Placement
An obvious practice to consider when using labels is their placement.
Unfortunately, in practice, not much thought is given to this crucial first step.
This often leads to labels being difficult to scan, read, or outright unusable.
Not to mention situations where a label is placed in such an unsuitable location that it quickly gets worn out, damaged, or even destroyed.
Here are some common label placements you’ll want to avoid.
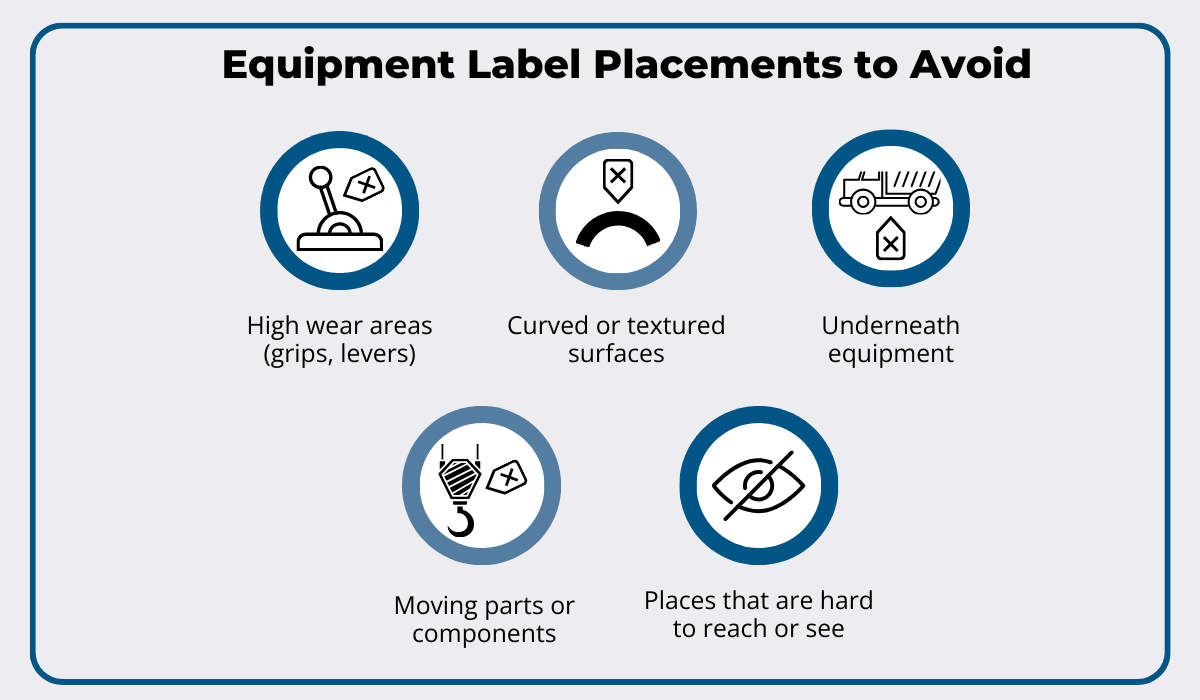
Of course, no one plans on sticking a label in a place that isn’t visible or accessible.
However, what might initially seem like a perfectly visible location can later become blocked by various equipment attachments or other obstructions.
Also, depending on the type of label, placing it on rough, curved, or uneven surfaces can make it less likely to adhere properly or cause it to become easily removed or damaged.
Proper label placement involves choosing smooth, clean surfaces that are readily visible and easily accessible for scanning or reading.
The ideal location will depend on the specific piece of equipment and its use, but generally, a flat, visible surface that is unlikely to be obstructed is best.
And, when defining these good placement practices for your organization, John Sewell, a consultant for IDCON INC, a reliability and maintenance organization, suggests enforcing consistency.
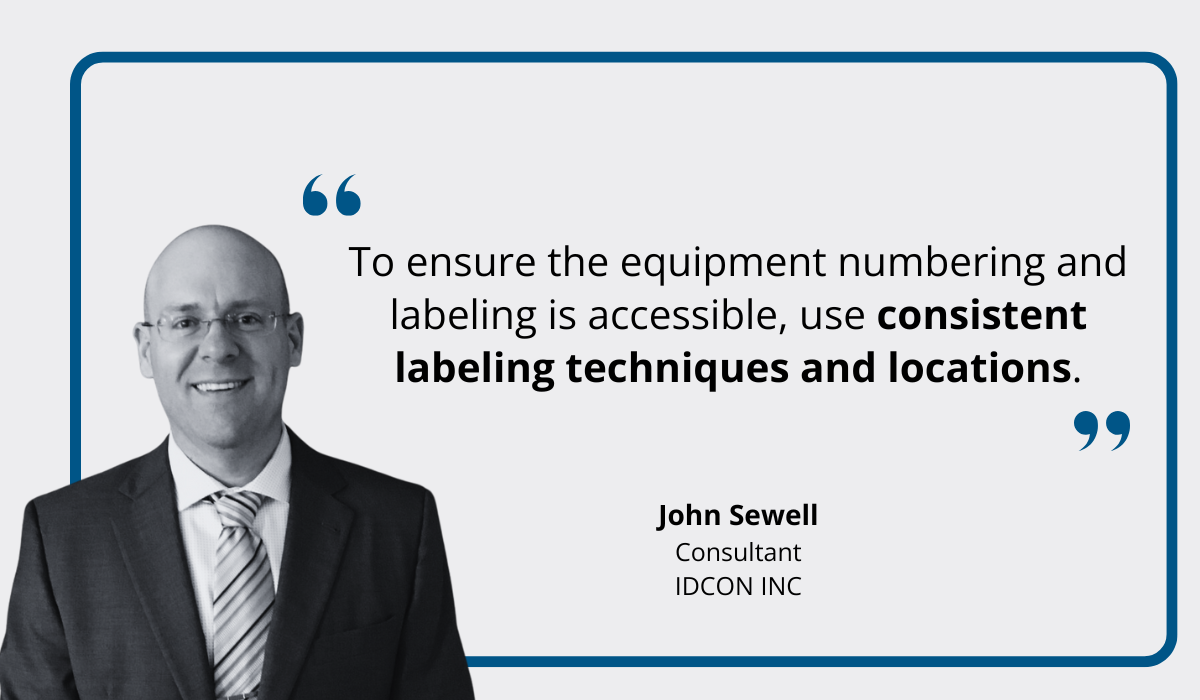
He recommends standardizing the types of labels used and where those labels are placed.
After all, consistent equipment numbering and labeling methods will make missing or damaged labels more noticeable, ensuring your system remains accurate and effective.
So, take the time to plan your label placement carefully, and you’ll avoid many headaches down the line.
Ignoring Environmental Conditions
Since different label materials offer varying levels of durability, it’s crucial to consider the environmental conditions your equipment will be exposed to.
As Chris Carter, OEM Market Leader explains, you need to carefully evaluate the environment in which your equipment operates.
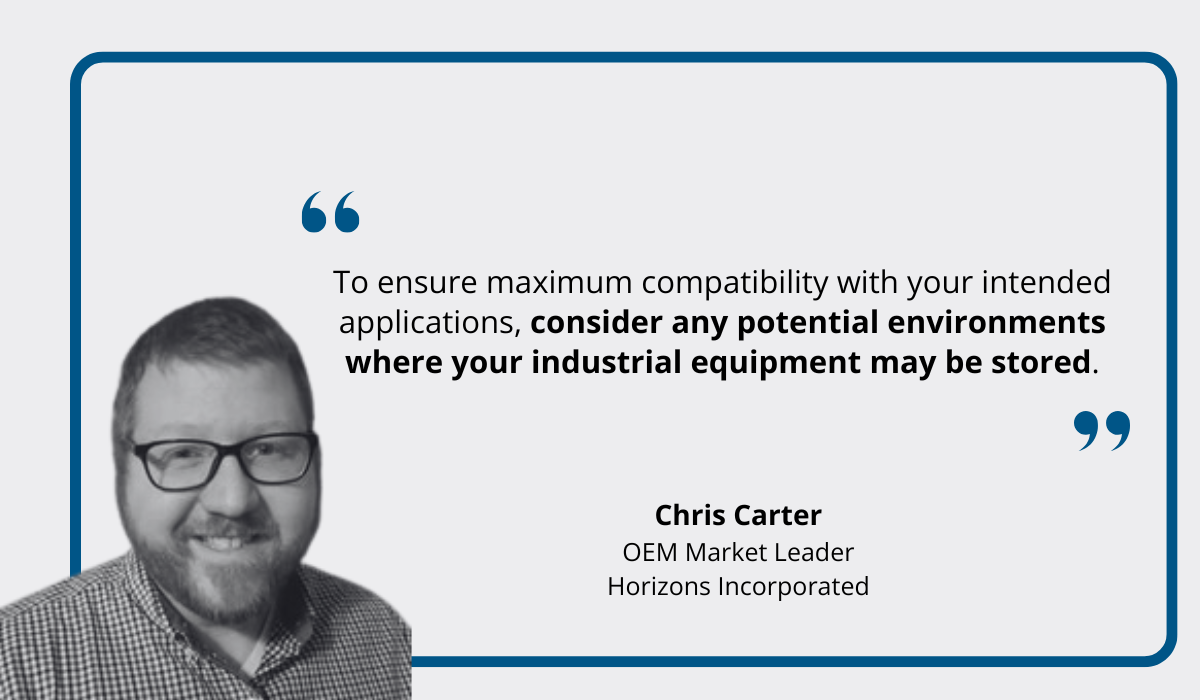
Whether your equipment is in storage or actively being used, any label you place on your assets must withstand the environmental conditions it’s subjected to.
Failing to account for these conditions can lead to labels that easily fade, smudge, peel, or become completely destroyed.
This, in turn, necessitates re-labeling the equipment, increasing maintenance costs, and raising the risk of misidentification and inaccurate tracking.
So, what conditions do you need to consider?
Let’s use a fuel-powered generator as an example.
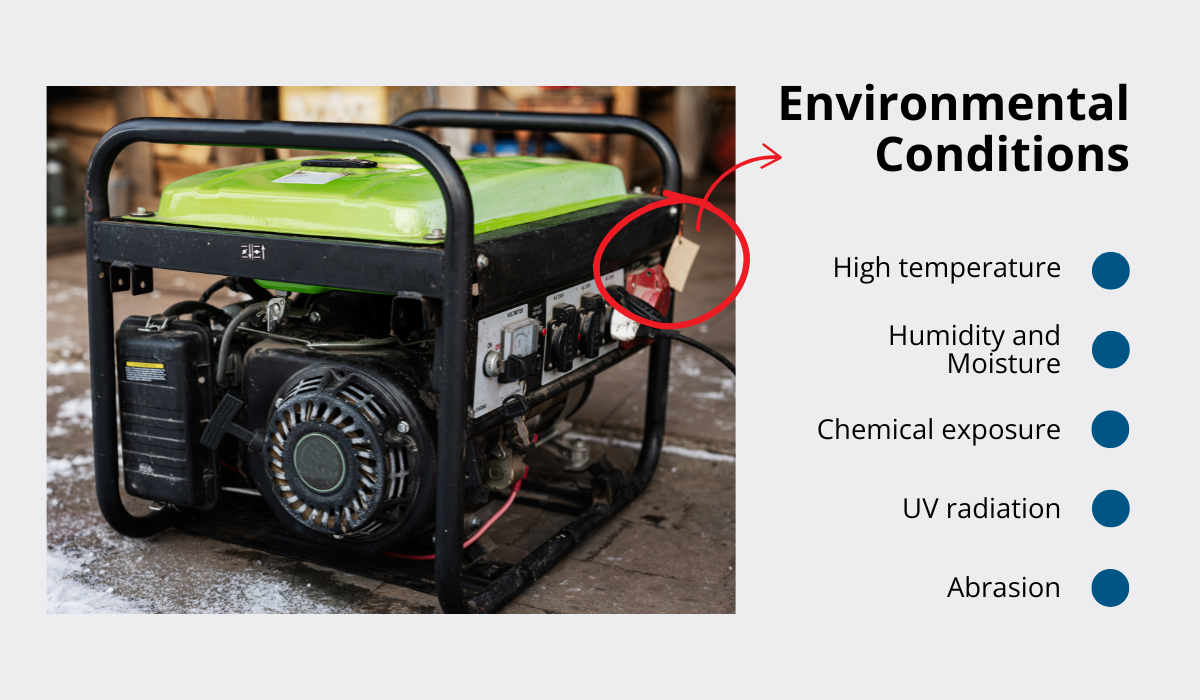
Any label placed on this piece of equipment needs to withstand the high temperatures created during the generator’s normal operation.
Additionally, the label must be resistant to:
- accidental fuel spills,
- moisture from rain or humidity,
- UV rays from sunlight, and
- potential abrasion from moving or handling the unit.
In short, any label material must be chosen strategically to ensure it can survive the specific challenges of the generator’s operating environment.
In your own operations, always assess your equipment’s operating environment before selecting your labels.
Not Connecting Labels with Asset Management Software
Lastly, a significant mistake in modern operations is not integrating your equipment labels with an asset management system.
Consider the information typically present on a standard label: you might have the equipment name, a serial number (or hopefully, a RUID), and some optional information like the equipment model and purchase date.
This is static information.
While useful, it can become outdated over time as equipment undergoes maintenance, changes locations, or gets assigned to different projects.
Now, consider the alternative.
Integrating your labels with asset management software allows you to link a wealth of dynamic information to each piece of equipment, going far beyond the basic details that are printed on.
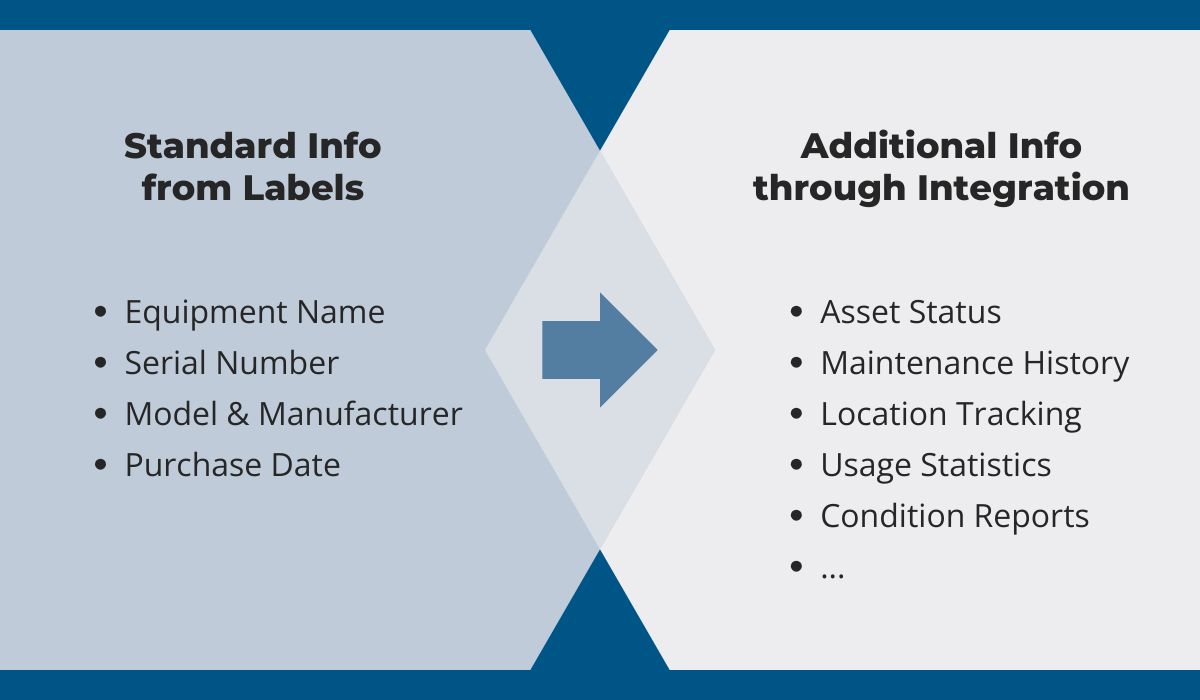
Without integration, this additional information is usually managed separately, often in spreadsheets.
This introduces the possibility of error, creates data silos, and makes accessing information a cumbersome process.
But, integrating labels with software effectively centralizes many of your asset management needs, reducing the amount of manual work required to access key information.
As an example, consider the scenario where a compressor’s label is scanned.
If that label is one of GoCodes Asset Tracking’ patented QR code labels, scanning it will instantly provide all the information illustrated below.
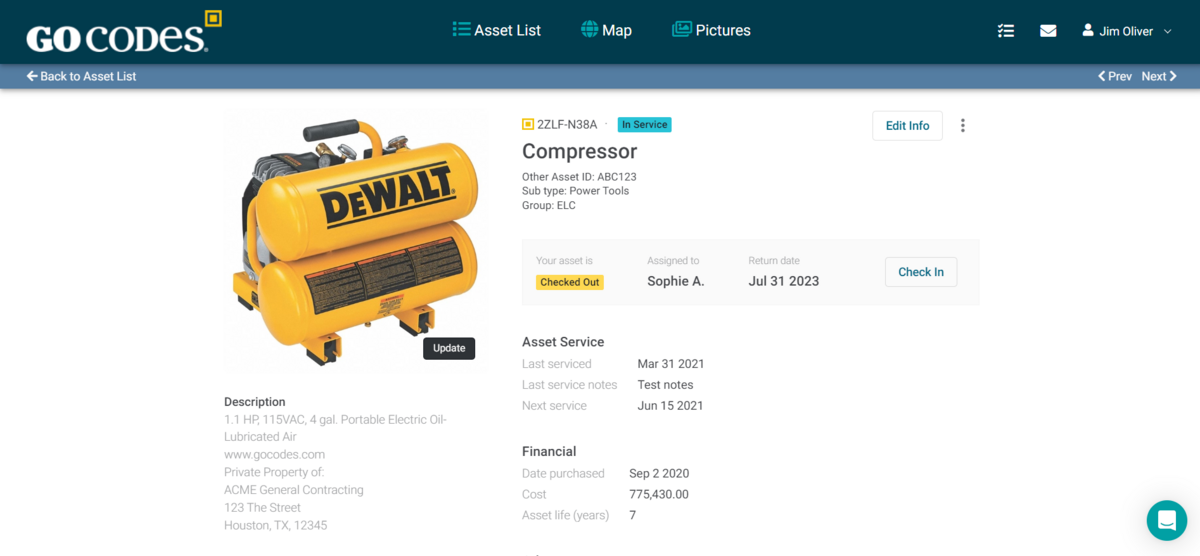
You get a clear image and description of the asset, its ID number, and its type.
More importantly, you get real-time information on whether the compressor is currently in use or checked out, helping with scheduling and resource allocation.
You also see which operator has the compressor and when it’s due back.
Plus, you have access to a complete service history, including past maintenance records, repairs, and inspections.
This is invaluable for preventive maintenance and ensuring equipment longevity.
In short, integrating your labels with an asset management system transforms your equipment tracking and management capabilities.
You gain access to dynamic, real-time information, streamline your workflows, and improve overall operational efficiency.
Conclusion
And that’s it!
We’ve covered everything you need to know to get started with effective equipment labeling.
We looked at the overall benefits of labeling, the different materials and types of labels available, and finally, some of the most common labeling mistakes.
Whether it’s implementing a new, more durable label material or integrating your labels with inventory management software, using the information in this article can transform your equipment identification workflows.
Now, take what you’ve learned and start improving your own labeling system today.