Poor inventory management can lead to chaos on construction sites: materials running out unexpectedly, tools misplaced, and projects delayed due to last-minute rushes.
Imagine the frustration and added costs of these scenarios.
However, with the right materials, tools, and equipment readily available when needed, projects run smoothly, timelines are met, and budgets stay on track.
But for that, you need your construction inventory management to be as effective as possible.
Today, we’ll explore why prioritizing inventory management is so essential for construction companies by uncovering six key benefits it brings.
Let’s jump right into the first one.
In this article...
Enhanced Project Planning
We can all agree that great planning depends on how organized you are.
Luckily, effective inventory management helps you organize your construction inventory to always know what materials, tools, and equipment you have, and where.
With such real-time visibility and accurate inventory data at your fingertips, you can plan your projects with more precision and confidence.
In other words, you can see what materials you have left and allocate them to upcoming projects.
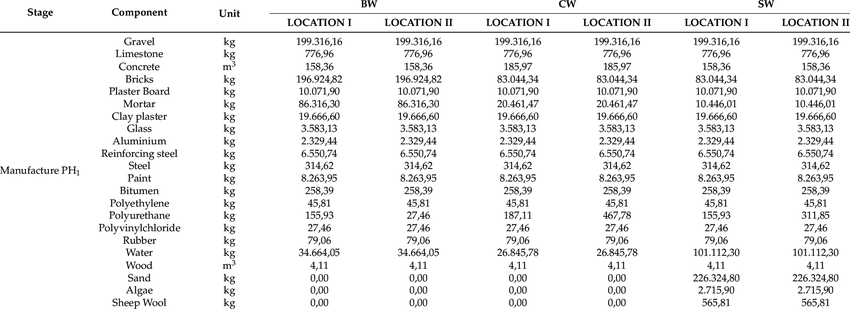
Moreover, if you leverage inventory management systems and track your inventory, you will also have old inventory data that you can rely on for more accurate resource planning.
For example, you can compare current project requirements with similar past projects and predict how much material you need.
Then, you can take these insights and your current stock levels to calculate what you need to order more accurately.
The ability to access inventory analytics equips you with the tools to refine project planning and scheduling even further.
When you, through inventory data analysis, analyze patterns and trends in material usage, you can fine-tune your project timelines for maximum efficiency.
For instance, if certain materials have longer lead times (which is now a reality, as you can see in the table below) or are prone to fluctuations in availability, you can adjust your schedule accordingly to minimize disruptions.
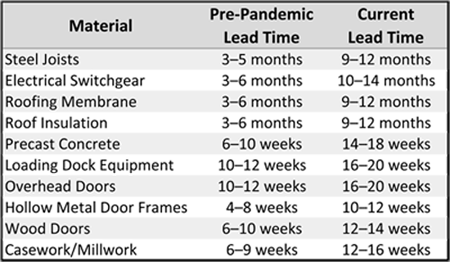
Let’s say you are building a commercial office building, and one of the critical materials required for this project is specialized glass panels for the exterior facades.
Based on data analysis, you observe that these glass panels have longer lead times due to their custom specifications and are also prone to availability fluctuations due to the supplier’s limited production capacity.
Considering this, you (or your project manager) can decide to adjust the project timeline accordingly.
So, instead of scheduling the installation of the glass panels immediately after the completion of the structural framework, you add a buffer period of 4 weeks to the timeline to account for potential delays in procurement.
This example shows how insights into material availability and lead times enable you to plan project timelines more accurately—not just in terms of resources but overall project efficiency.
All in all, better project planning, facilitated by effective inventory management, means that you can optimize resource utilization and minimize project delays, which leads to completing projects on time, within budget, and to everyone’s satisfaction.
Increased Efficiency On the Construction Site
Effective inventory management brings a crucial benefit to construction sites: increased efficiency.
By ensuring that equipment, tools, and materials are readily available when needed, you eliminate the risk of inventory stockouts, which can cause serious delays and downtime on construction projects.
Essentially, stockouts disrupt workflow and can even bring work to a standstill.
However, with the use of inventory management software, you gain full visibility into your inventory, allowing you to prevent stockouts and keep your projects moving forward smoothly.
These systems often include low stock alert features, ensuring you’re notified in time to reorder materials and avoid interruptions.
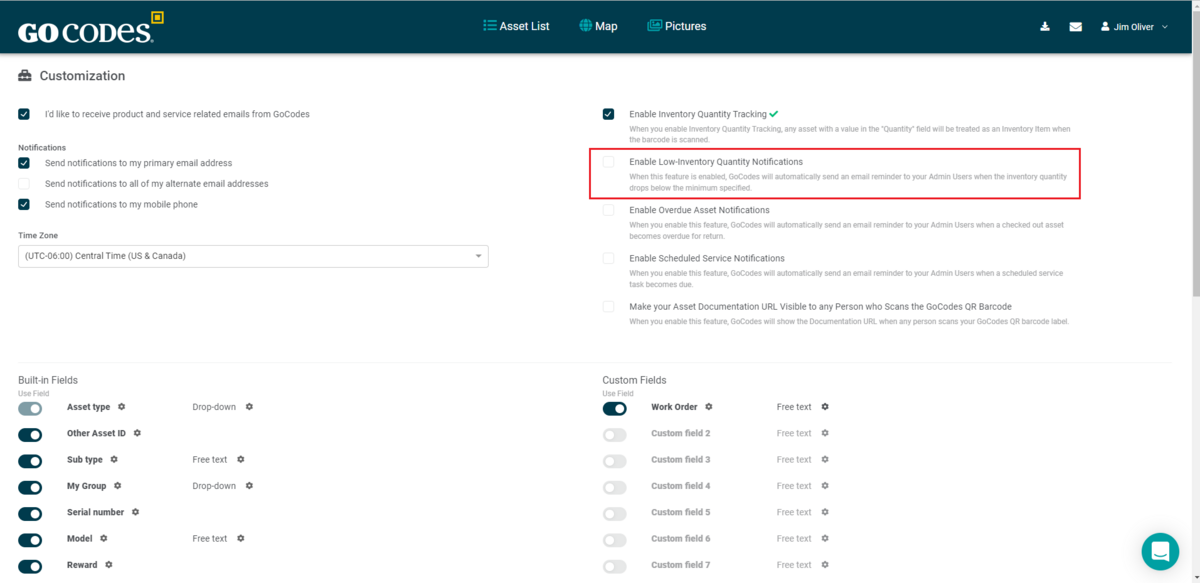
But there’s more to it than just preventing stockouts.
Effective inventory management also streamlines workflows and reduces time wasted searching for misplaced tools or materials.
Consider this: not only do workers waste time searching for tools and materials, but they also spend significant idle time on the job site due to inventory-related delays.
For example, bricklayers may waste 45 minutes, carpenters 62 minutes, roofers 75 minutes, electricians 80 minutes, and plumbers 83 minutes.
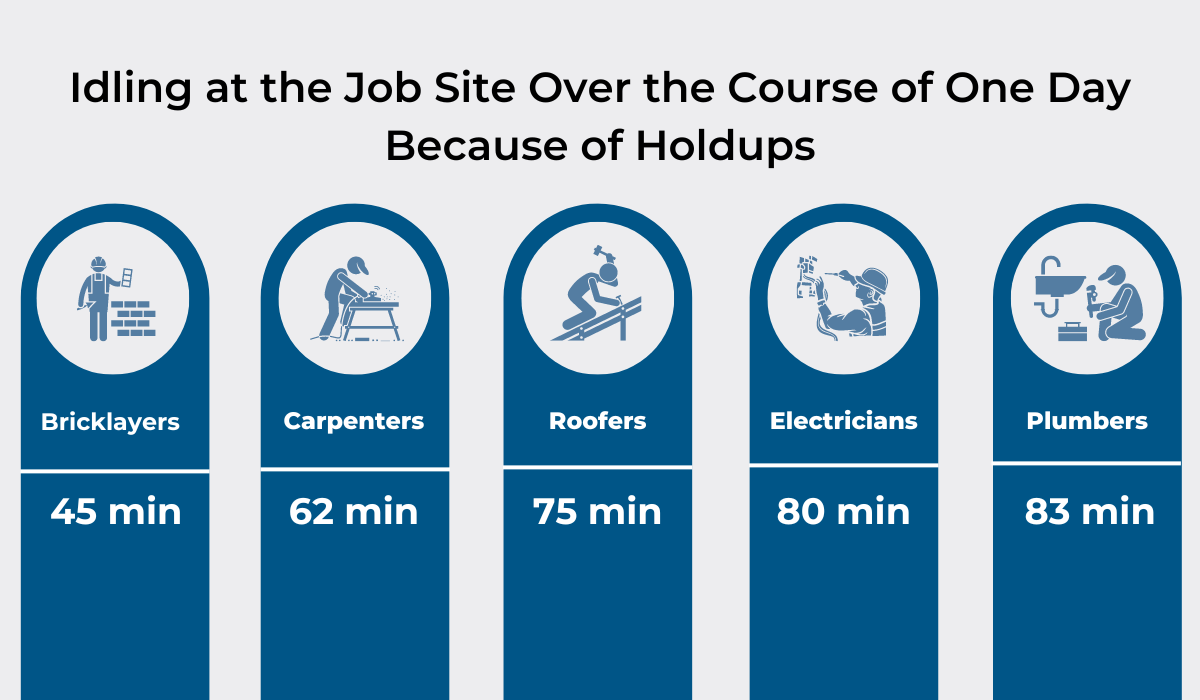
This time adds up quickly!
Moreover, effective inventory management allows for better coordination and resource allocation across multiple construction sites.
For instance, if there’s a material stockout at one site, but you have an overview of all your inventory, you can potentially transfer materials from another site where they are not immediately needed.
This flexibility minimizes disruptions and ensures optimal resource utilization across projects.
Every minute saved on the construction site translates into increased productivity and cost savings.
With better inventory management, ensuring that workers have the materials, tools, and equipment they need when they need them becomes achievable.
Plus, it prevents unnecessary delays and ensures that the construction site operates at its highest efficiency.
Cost Savings
Cost savings are a significant advantage stemming from efficient inventory management practices.
They materialize in various ways, such as by preventing stockouts or overstocking.
Stockouts, aside from causing delays and downtime, also incur increased costs.
Rush orders, expedited shipping, or emergency procurement of materials all come with a heftier price tag, leading to budget overruns and decreased profitability.
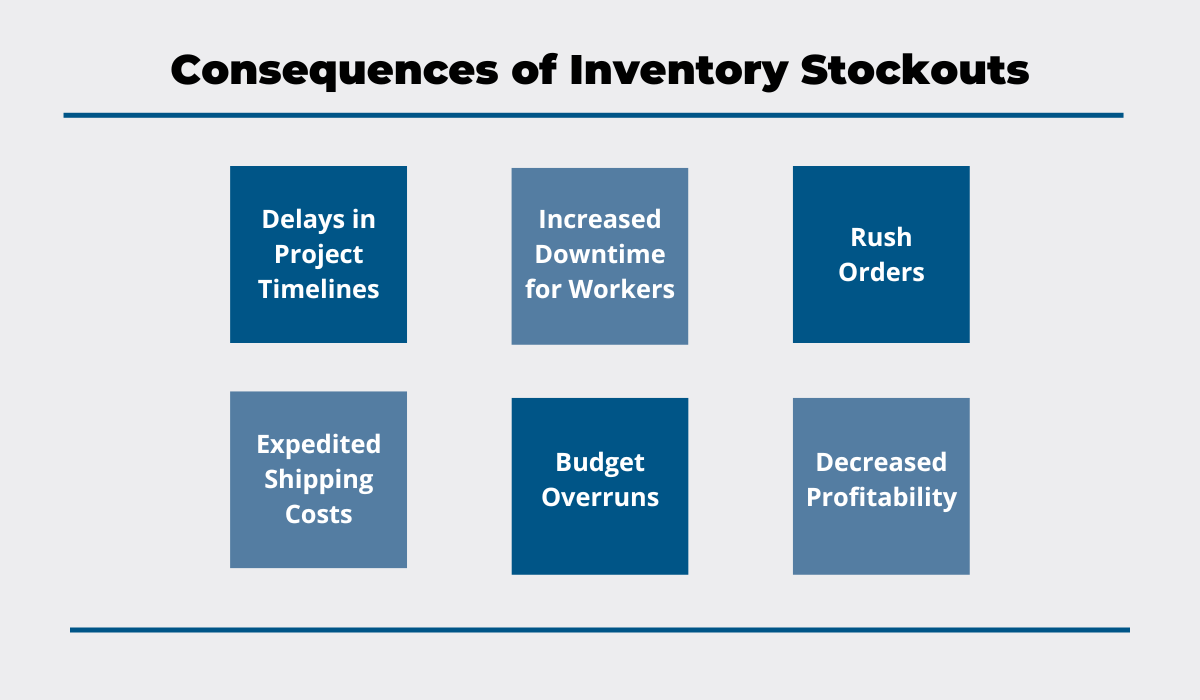
Fortunately, efficient inventory management helps avoid these issues and ensures that construction projects stay on schedule and within budget, ultimately contributing to the company’s bottom line.
Now, consider the implications of overstocking materials on your construction sites.
Not only does it tie up valuable capital in excess inventory, but it also incurs additional costs for storage and handling.
However, with effective inventory management systems in place, you can accurately track material usage and consumption patterns to maintain optimal inventory levels and avoid overstocking scenarios.
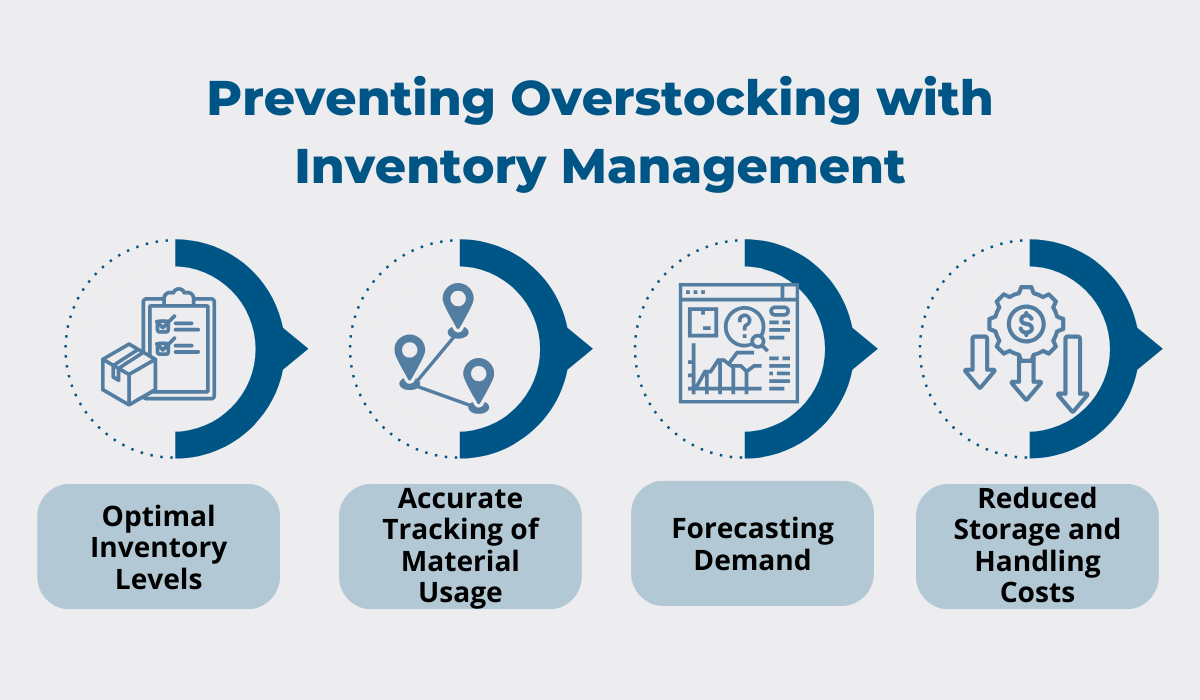
Moreover, by preventing unnecessary purchases through better inventory visibility and forecasting, you can eliminate the costs associated with redundant inventory.
For instance, leveraging historical data and demand forecasting tools allows you to anticipate future material requirements and procure only what is necessary, thereby reducing excess inventory and minimizing waste.
On top of that, effective inventory management can lead to cost savings through strategic supplier negotiations and consolidation of purchases.
By clearly understanding your inventory needs and usage patterns, you can negotiate better deals with suppliers, take advantage of bulk purchasing discounts, and streamline procurement processes, further reducing costs and enhancing profitability.
Minimized Risk of Inventory Loss
Effective inventory management is essential for minimizing the risk of inventory loss within the construction industry.
Instances of theft, damage, or misplacement of inventory items, particularly equipment, can significantly disrupt project timelines and strain budgetary constraints, which is a big challenge for construction operations.
According to Soeren Brogaard, CEO of fleet management solution Trackunit, approximately 20% or more of equipment is susceptible to theft.
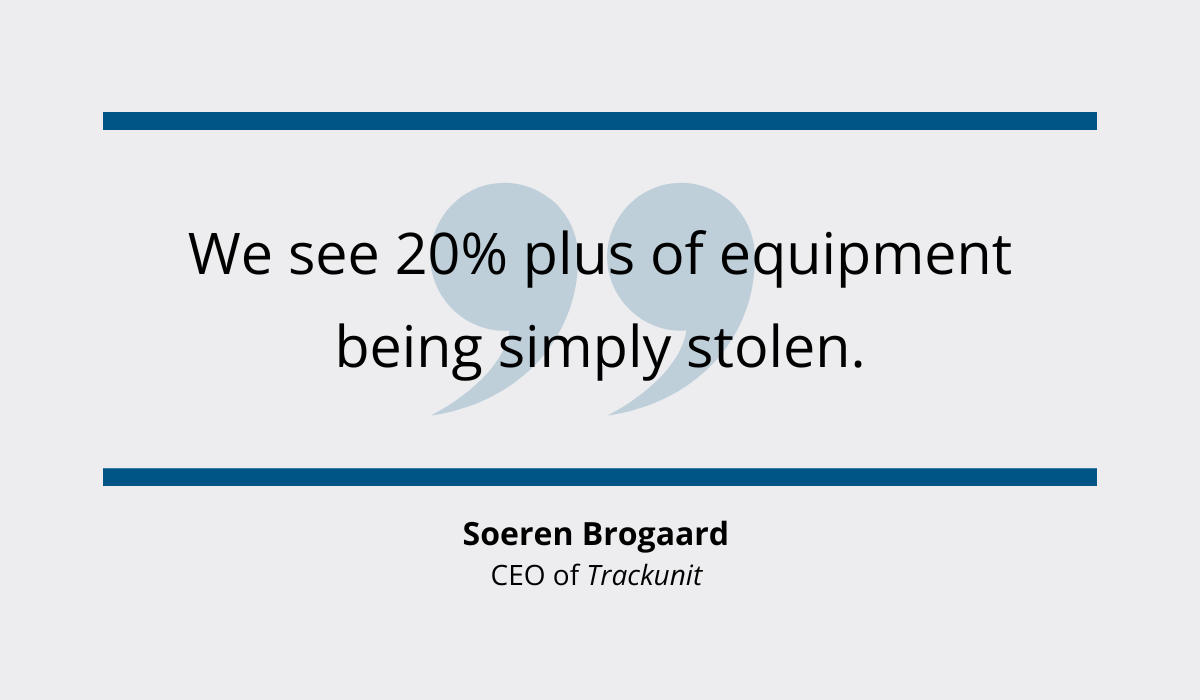
Up to one-third of all annual tool purchases result directly from theft, loss, or damage, with only a fraction of lost equipment ever recovered.
Adopting better inventory management practices, including inventory tracking solutions, is the way to mitigate these risks.
For example, with our asset tracking software, GoCodes, you can use GPS trackers to monitor your equipment in real time.
These trackers show you exactly where your equipment is, even if it’s on the move.
Also, you can set up a geo-fence or boundary around that location that your equipment should not cross, like your project site.
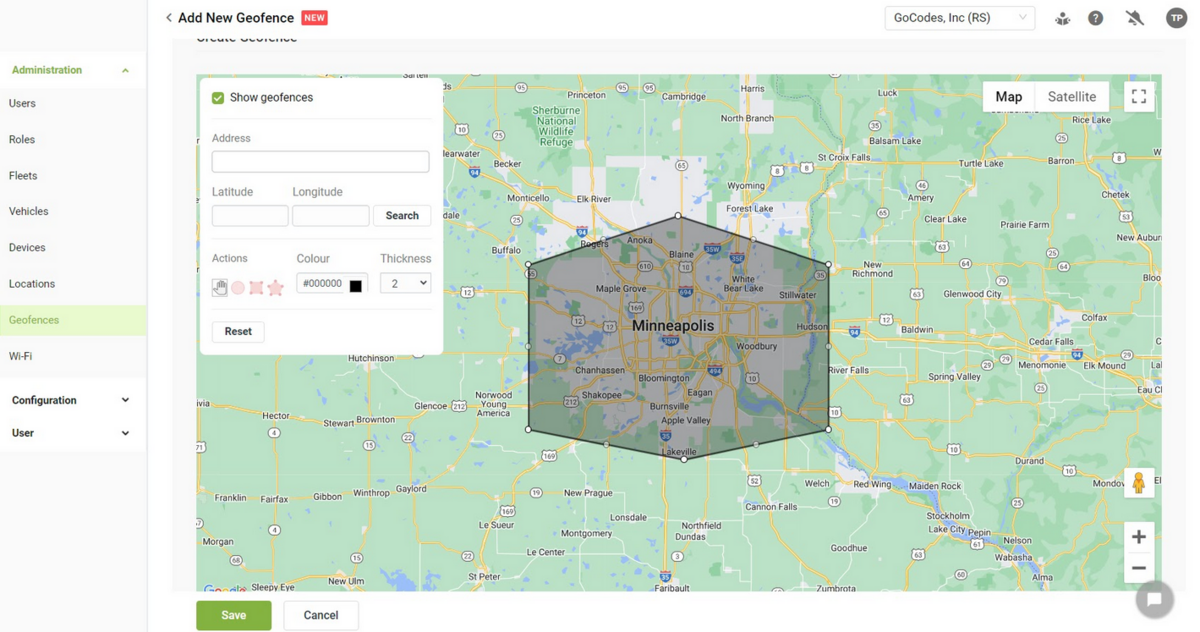
Then, if your equipment leaves a designated area, you get notified.
So, if something does go missing, you can quickly share its location with law enforcement to help get it back.
Another way to minimize the risk of inventory loss is with regular inventory audits.
During an audit, physical counts of inventory items are compared against the recorded inventory levels to identify any discrepancies.
This, too, helps to detect instances of theft, damage, or misplacement of inventory items.
All in all, by leveraging technology for effective inventory management, you can mitigate the risk of inventory loss and safeguard your assets against theft, damage, or misplacement, making this benefit significant for any construction company.
Better Supplier Relationships
When you excel at managing your inventory, it’s not just your company that reaps the benefits.
Your suppliers benefit, too, leading to stronger relationships overall.
This translates into improved collaboration, better terms negotiation, and ensuring suppliers deliver on time and honor contracts.
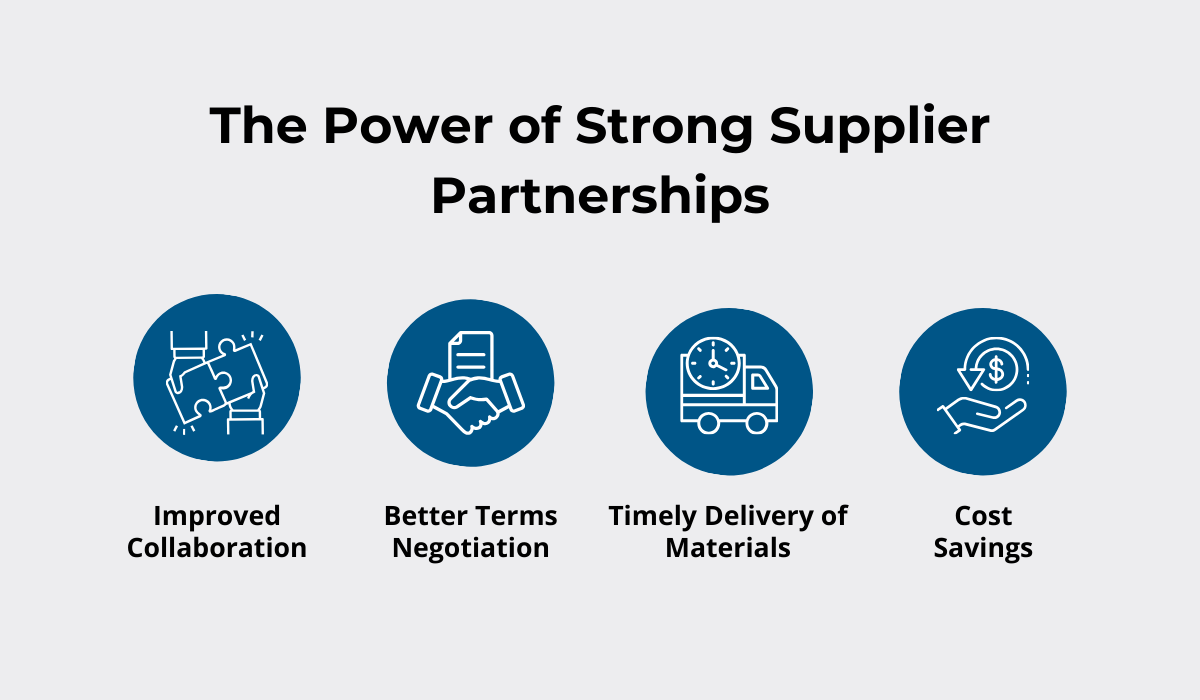
Just imagine how important it is for you to have accurate insights into your inventory levels and upcoming project demands.
With this information ready, you can give suppliers precise forecasts and timelines.
This is equally important for them, as they can plan production schedules and inventory levels more effectively, as well as reduce their stockouts or overproduction.
Minimizing returns to suppliers is another significant benefit of effective inventory management for both parties.
By efficiently managing your inventory, you are less likely to over-order or order incorrect items, resulting in fewer returns due to excess or incorrect inventory.
This not only saves suppliers from restocking, handling, and processing expenses associated with returns but also saves you time and the inconvenience of returning inventory.
When both sides benefit from improved inventory management, there’s an opportunity to negotiate better deals that further benefit both parties.
For instance, you can negotiate volume discounts with suppliers by committing to larger, consistent orders over time, while suppliers benefit from increased sales volumes and revenue.
Moreover, as relationships strengthen, you may renegotiate contracts to better reflect evolving needs and priorities, adjusting pricing structures and terms to optimize mutual benefits and long-term partnership success.
Ultimately, effective inventory management provides clear visibility into your inventory needs and requirements.
It is a foundation for building better supplier relationships and negotiating better terms.
Improved Compliance with Regulatory Requirements
Complying with regulatory requirements is essential for construction businesses, given the myriad regulations governing material and equipment handling, storage, and disposal.
Consider the diverse regulations you encounter on construction sites, from safely storing hazardous materials to adhering to environmental protection guidelines.
By implementing efficient inventory management systems, you can confidently navigate these regulations.
For instance, let’s say you’re overseeing a construction project where you need to ensure compliance with environmental regulations regarding the disposal of hazardous waste materials.
With effective inventory management tools, you can accurately track the quantities of hazardous materials used on-site, document their disposal according to regulatory guidelines, and generate reports to demonstrate compliance during inspections.
This safeguards compliance with environmental regulations and minimizes the risk of environmental harm and potential legal consequences.
Also, accurate record-keeping of material usage and disposal is essential for demonstrating compliance during regulatory inspections.
When you’re audited, inspectors can request documentation regarding material handling and disposal practices.
With comprehensive inventory records at your fingertips, you can quickly provide evidence of compliance, mitigating any potential issues.
Also, don’t forget that your workers need personal protective equipment (PPE) and safety gear, which is a regulatory requirement on construction sites.
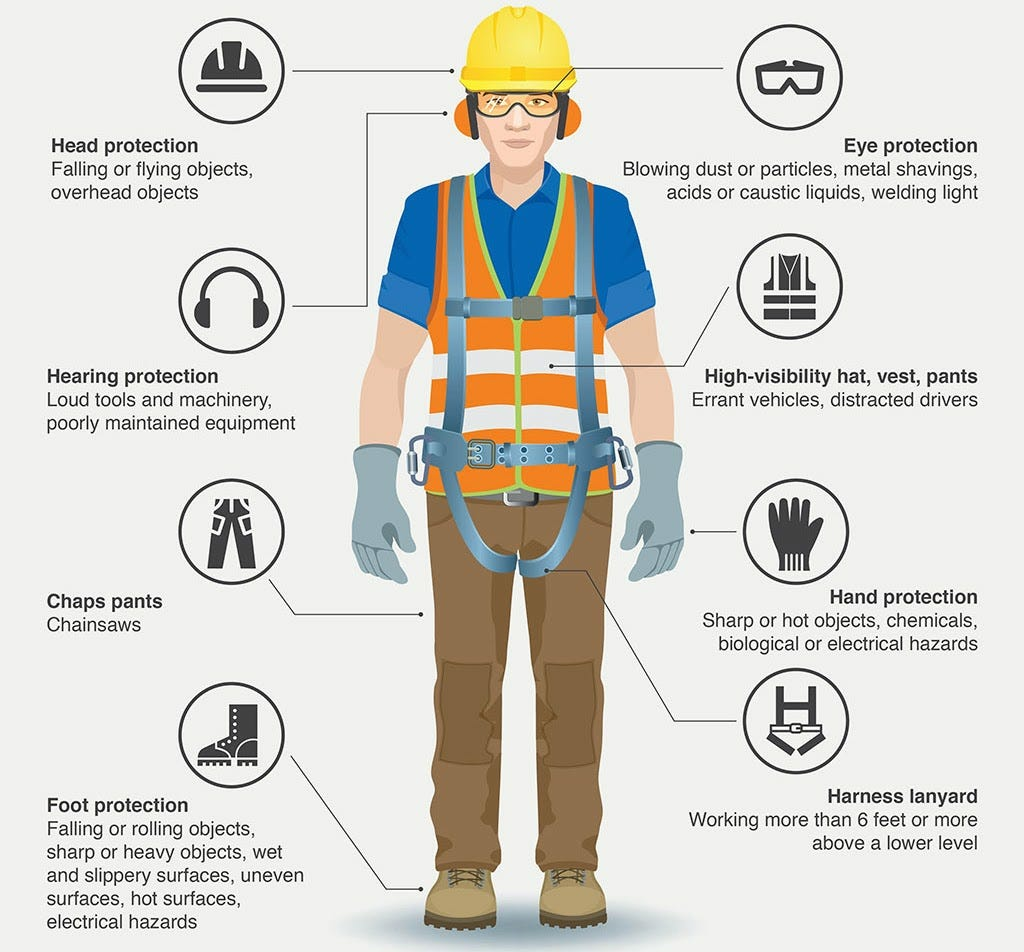
With inventory tracking, you can monitor the availability of such protective equipment, track its location, and ensure it’s allocated to the appropriate personnel.
As you can see, effective inventory management empowers you to meet regulatory requirements with more confidence—we dare say.
So, when you implement robust inventory practices, you can ensure compliance, mitigate risks, and uphold your reputation as a responsible construction professional.
Conclusion
As evident, the benefits of effective construction inventory management are indeed multifaceted and far-reaching.
By implementing robust inventory management practices, you can better plan your construction projects, increase efficiency on your construction sites, maximize cost savings, and prevent tool, material, and equipment theft.
Ultimately, effective inventory management empowers you to meet project deadlines, stay within budgetary constraints, and satisfy stakeholders’ expectations.
And perhaps most importantly, it gives you peace of mind knowing that your costly inventory is under control!