When we’re talking about construction equipment, preventive maintenance is probably the most well-known type of maintenance—often called regular or routine maintenance—that involves routine maintenance tasks performed at regular time intervals.
The goal of preventive maintenance is to keep construction equipment running smoothly, therefore preventing breakdowns and accidents, improving its performance, extending its lifespan, and minimizing downtime and repair costs.
With all these benefits, having a preventive equipment maintenance plan is a must.
So, how does one go about creating an effective preventive maintenance plan?
Here are seven steps you can follow.
In this article...
Start by Choosing the Right Technology
Your path to creating a preventive maintenance plan for your construction equipment should start with choosing the right technology that will allow you to implement the plan with ease.
And when we say “implement,” we mean to organize, schedule, track, and document preventive maintenance activities that will be specified in your future plan.
Likewise, when we say “technology,” we mean software, as well as some “hardware” in the form of barcode tags and labels used for tracking equipment and spare parts.
As for software, getting one with an extensive list of features will allow equipment managers and service technicians to do their job more efficiently without switching between several different software solutions.
More precisely, you should be looking for software with features that will facilitate the implementation of your preventive maintenance plan, such as:
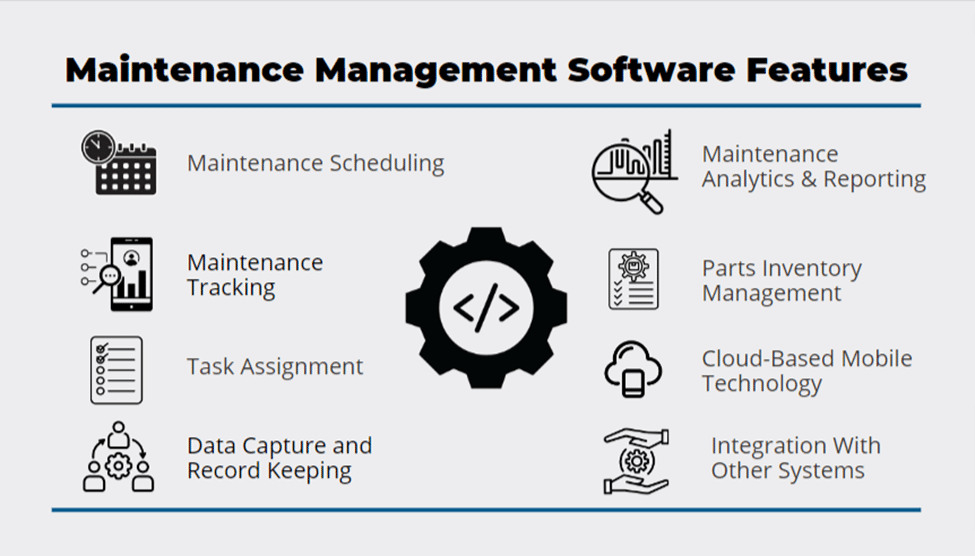
Although we called it “maintenance management software,” these features are usually part of broader equipment/tools/assets tracking and management software solutions.
Therefore, when choosing the right software, focus on whether it provides the above features in a user-friendly and affordable way.
For example, such software should enable users—depending on their role and authorization—to schedule and assign maintenance tasks in real-time, set up automated notifications for upcoming maintenance, and receive low-quantity alerts for spare parts and other consumables.
Furthermore, it should allow both managers and field technicians to track and document all maintenance activities and access and update the central database of equipment and their individual info from any mobile device with an internet connection.

It should also integrate well with other digital systems, such as construction project management and accounting software.
Finally, it should enable managers to analyze maintenance data and generate reports, allowing them to make better-informed decisions and improve the maintenance plan going forward.
And that’s critical if you want your maintenance plan to produce the benefits we mentioned, such as optimized equipment performance and reduced maintenance costs.
Given all the above, such software should automate equipment maintenance processes and make the operationalization of your maintenance plan easier, more efficient, and less error-prone.
So, when choosing the right technology, identify your needs, research, and look for the features we discussed, as they will allow you to easily implement the preventive maintenance plan.
Take Inventory of All Your Equipment
Now that you selected the technology, it’s time to take inventory of all your equipment, enter as much information about the equipment as possible into the chosen software, and create a detailed asset register.
The importance of doing this step correctly can’t be stressed enough.
Simply put, the success of your preventive maintenance plan relies on the quality of input data.
Therefore, the first step is to collect relevant data about all construction equipment, tools, accessories, and spare parts your company has.
Here’s what information can be collected and tracked for preventive maintenance purposes:
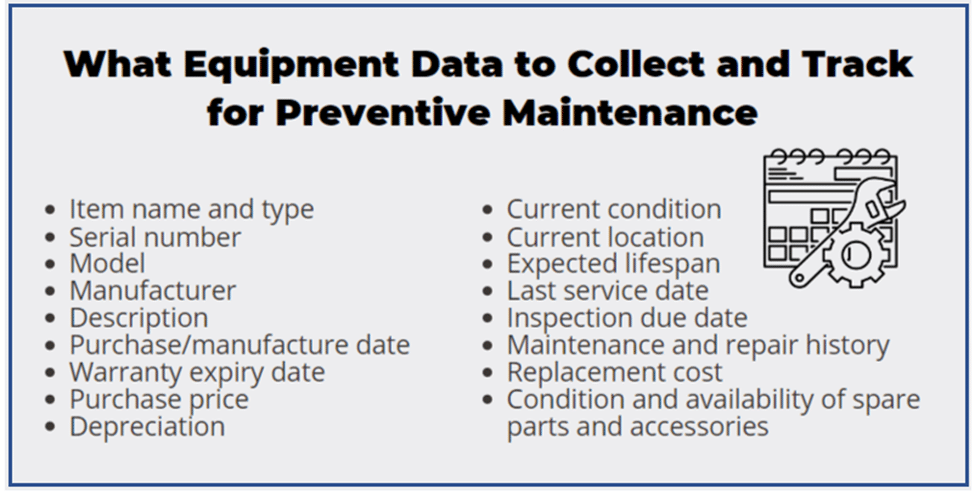
Of course, the whole point of selecting the right technology in the first place was to enable you to not only collect data efficiently, but ensure it’s stored in digital form and can be tracked and updated.
In other words, as equipment and other assets are located and their info (and documentation) collected and entered into the software, barcode tags are also attached to them for future tracking and monitoring.
For example, our maintenance tracking solution, GoCodes Asset Tracking, combines cloud-based software that makes creating a detailed asset register easy and rugged QR code tags that enable real-time tracking of equipment and maintenance.

GoCodes Asset Tracking also comes with a scanning app that enables users to scan the QR code with their smartphone or tablet to access the equipment info, which they can also do by searching the central register of assets.
Having all the features we discussed in the previous section, this mobile app can help you create a detailed register of assets and an efficient maintenance tracking system, both of which are crucial for the success of your preventive maintenance plan.
To sum up, taking inventory of all equipment is critical for creating and implementing a preventive maintenance plan, as all future decisions will be based on the quality of information gathered in this step.
Develop a Plan for Each Piece of Equipment
Now that the relevant information about your equipment is digitized and integrated into one system, you can proceed to develop a preventive maintenance plan for each piece of equipment.
This equipment-specific plan should be based on the manufacturer’s maintenance guidelines, the current condition and usage of that equipment, and its operational criticality (explained below).
Therefore, you should start with what people who created the equipment and know it best, say about its maintenance schedule, like for this Bobcat loader.
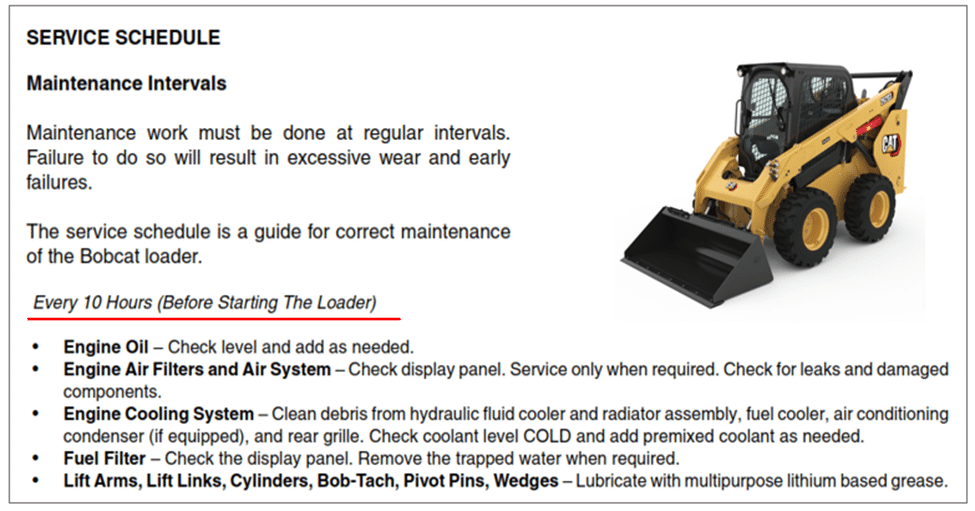
Of course, the highlighted maintenance interval of 10 operating hours, i.e., before the loader is started, is followed by other preventive maintenance actions recommended every 50 and 100 hours, and then 250, 500, and 1,000 hours (or every twelve months for each).
So, such manufacturer’s guidelines and servicing instructions should be used to create the basic preventive maintenance schedule for a specific piece of equipment.
This schedule and the tasks specified in it should then be adjusted according to the actual age/condition of that machine, how often it has been and will be used, and your staff’s previous experience with its maintenance.
For example, let’s say that the loader we mentioned is heavily used.
In that case, its engine oil and filter may need to be replaced more frequently than recommended (500 hours or every 12 months), and your individual asset maintenance plan should take that into account.
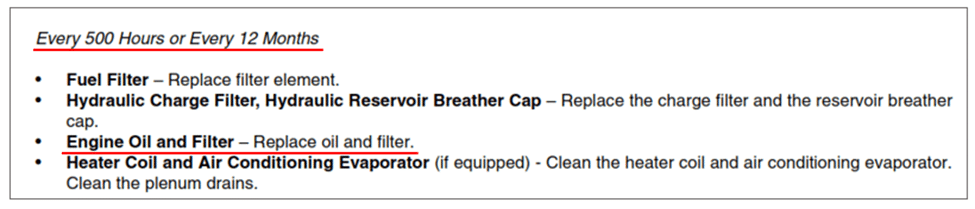
Finally, you should determine how critical each piece of equipment is for your construction operations (hence “operational criticality”) and then prioritize maintenance tasks related to such equipment in your preventive maintenance plan.
The benefits of this prioritization are:
- critical equipment is well-maintained, and its lifespan extended
- reduced risk of breakdowns and unplanned downtime
- improved allocation and budgeting of resources, including labor and parts
- increased worker safety and regulatory compliance
Of course, this doesn’t mean that maintenance of other equipment should be neglected, but it ensures that managers and service personnel know how to prioritize their tasks.
Overall, by determining the maintenance schedule and tasks required for each piece of equipment and then prioritizing them according to how indispensable they are for construction operations, you basically created the preventive maintenance plan.
Prepare the Required Documentation
Simply put, the step that involves preparing the required documentation works on two levels.
First, you should have all pre-existing equipment documentation, such as manufacturer’s manuals and warranties, as well as its previous maintenance and repair records when creating the central register of assets.
Moreover, these documents should be digitized (if they’re not already), so they can be accessed by equipment managers and field technicians alike from their phone, tablet, or computer at any time.
Second, you should prepare the documents required for future maintenance tracking and monitoring of your maintenance plan, such as preventive maintenance checklists and maintenance logs.
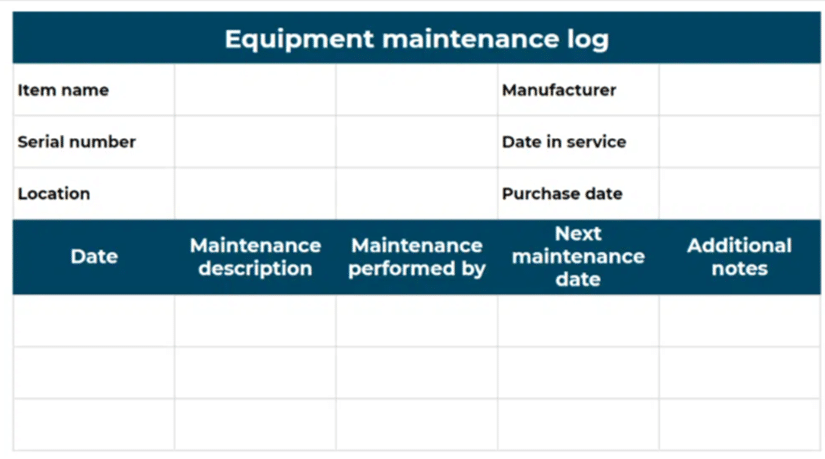
As you can see, maintenance logs are records about what servicing and repairs were done on a machine, along with standard info such as item identification, location, etc.
In other words, depending on how you set up your selected software solution, you already have or can easily create and customize a digital maintenance log for each piece of equipment.
These logs serve as a valuable source of insights about equipment maintenance and as proof if something goes wrong with the equipment, whether for warranty or insurance purposes.
On the other hand, preventive maintenance checklists contain a list of standardized procedures for each maintenance task, which helps ensure the quality and consistency of the work done by maintenance personnel.
Therefore, having the required equipment documentation and records prepared and digitized so they can be easily accessed and updated will help both implement and monitor the quality of your preventive maintenance plan.
Assign Responsibilities to Your Team
Now that you have the preventive maintenance plan and monitoring mechanisms in place, it’s time to assign roles and responsibilities to your team, making them accountable for how the plan is implemented.
In other words, employees can be assigned different responsibilities based on construction site locations, equipment types, and preventive maintenance activities that need to be performed.
For example, you can assign a team of mechanics responsible for performing preventive maintenance on heavy equipment like excavators, bulldozers, and loaders, while another team is responsible for smaller equipment such as generators, compressors, and power tools.
Naturally, this will all depend on many factors, such as the size and setup of your maintenance team, as well as their qualifications and training.
Here’s an example of a large maintenance team and its responsibilities.

Again, roles and responsibilities for implementing the day-to-day activities that constitute your preventive maintenance plan will depend on how your team is organized and what budget and resources—including expertise, experience, and training—it has available.
In any case, this step is crucial for implementing your preventive maintenance plan and keeping everyone engaged and accountable.
Develop a Training Plan For Your Team
This step arises from the previous one, meaning that everyone on your team who will be involved in realizing the maintenance plan should be trained on how to use the maintenance management software you selected.
Although today’s software solutions can be easy to use, practical training shouldn’t be ignored.
Instead, it should be used as an opportunity to get everyone on the same page, make them understand the value of your preventive maintenance plan, and reduce mistakes when they’re performing and documenting their maintenance activities.

Therefore, however simple the software interface and functions are, it’s still best to explain to all team members how they will use it.
For example, they should know how and when they’ll be notified of scheduled maintenance, what safety precautions and maintenance checklists they should follow, and how to find that info in their app.
Likewise, after they finish maintaining a piece of equipment, they should know how to enter the relevant information into the software and document their actions.
So, developing a training plan for your team will strengthen their commitment and improve the implementation of your preventive maintenance plan by helping everyone understand what is expected of them.
Improve Your Plan Based on Results
Last but not least, when your preventive maintenance plan is up and running, you and your team should establish and track relevant maintenance KPIs (key performance indicators) to measure the plan’s effectiveness.
In other words, as the famous quote by Peter Drucker goes:
You can’t manage what you can’t measure.
Therefore, to know whether your preventive maintenance plan is working, you should first establish maintenance goals that your company wants to achieve.
Here are some examples:
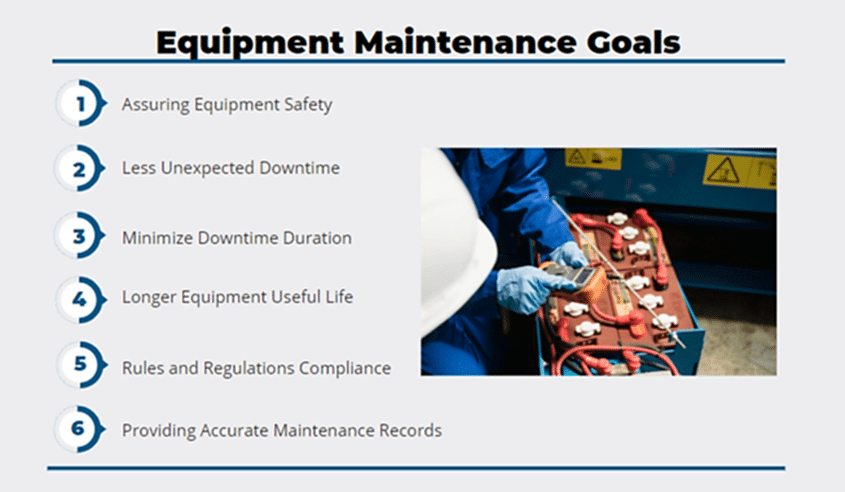
Once set, these goals need to be turned into quantifiable values, such as reduced equipment downtime by a certain percentage, improved percentage of planned vs. unplanned maintenance, increased mean time between failure, and other maintenance metrics.
Some of these KPIs related to your preventive maintenance plan can also include workforce productivity and equipment lifecycle costs.
The main takeaway is that your preventive maintenance plan should have clear goals and defined ways of measuring their achievement, as that’s the basis for regularly analyzing your plan’s results and thus gaining insight into how it can be improved.
Therefore, this final step is a continuous one—the results of implementing the maintenance plan are consistently reviewed, and the plan is improved according to the insights gained.
Conclusion
So, from choosing the right technology and creating a central register of equipment to assigning responsibilities to your team and improving your plan based on results, these seven steps will help you create an effective preventive equipment maintenance plan.
The results of its successful implementation will be seen across your company as the number of equipment breakdowns and accidents goes down, and its performance improves while extending the equipment’s lifespan and reducing maintenance costs.