When a contractor decides to buy a piece of construction equipment, be it brand new or used, there’s much more to consider than its initial purchase price.
Aside from the cost of transporting the equipment to the company’s headquarters and insurance, they should have a clear understanding of specific factors that will constitute its operating costs.
To help contractors grasp the overall cost of their construction equipment and make the right purchase and management decisions, we’ll cover six distinct operating cost categories they should know about.
In this article...
Repair Costs
As their name suggests, repair costs are expenses incurred when construction equipment breaks down or suffers a major malfunction.
As such, this is the most unpredictable and potentially the most expensive category of operating costs.
In other words, since a breakdown or malfunction is always unexpected (or would be addressed before it occurred), repair costs largely depend on what happened and how extensive the equipment damage is.
For example, each of these accidents will involve expensive repairs, but their costs can be significantly different.
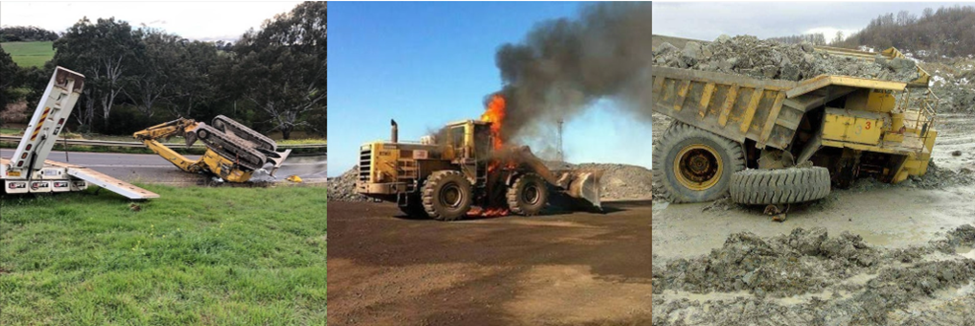
Naturally, this presents a challenge when construction teams are estimating potential future repair costs and budgeting for them.
Despite this, having a rough idea about how much repairs would cost is essential for sound financial planning and risk management in construction companies.
So, what can construction teams do to get at least a ballpark estimate of potential repair costs?
For starters, if the machine is new, they should:
- consult the manufacturer’s repair and maintenance guidelines
- find out the price of spare parts and components
- leverage their or their peers’ experience with the same or similar equipment models
If the machine is used, other factors also come into play, such as the number of operating hours, repair and maintenance history, and any records of past repair costs.
Other repair cost estimating strategies include researching industry benchmarks for repair costs of specific equipment types and models, consulting equipment specialists and mechanics, and using different cost estimation formulas.
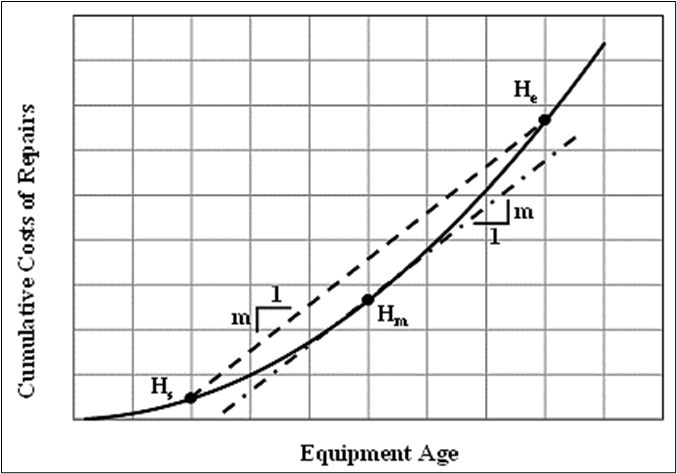
Regardless of how precise repair cost estimates are, it’s always a good idea to include a buffer in your repair budget to account for unexpected repairs.
By combining these strategies and continuously updating their estimates based on real-world data, contractors can make informed decisions about how much to budget for repair costs.
Maintenance Costs
Unlike those for unexpected repairs, the costs of performing preventive maintenance and solving minor equipment issues are typically planned and routine expenses.
As such, they’re much easier to estimate and budget for.
They cover regular maintenance activities, such as oil changes, filter replacements, lubrication, and calibrations, required to prevent major breakdowns and keep equipment operating smoothly.
Moreover, the goal of preventive maintenance is to extend the equipment’s lifespan and optimize its performance, which can significantly reduce overall operating costs during its lifecycle.
In fact, proper and timely maintenance brings a host of benefits compared to reactive, run-to-failure maintenance.
You can see them here.
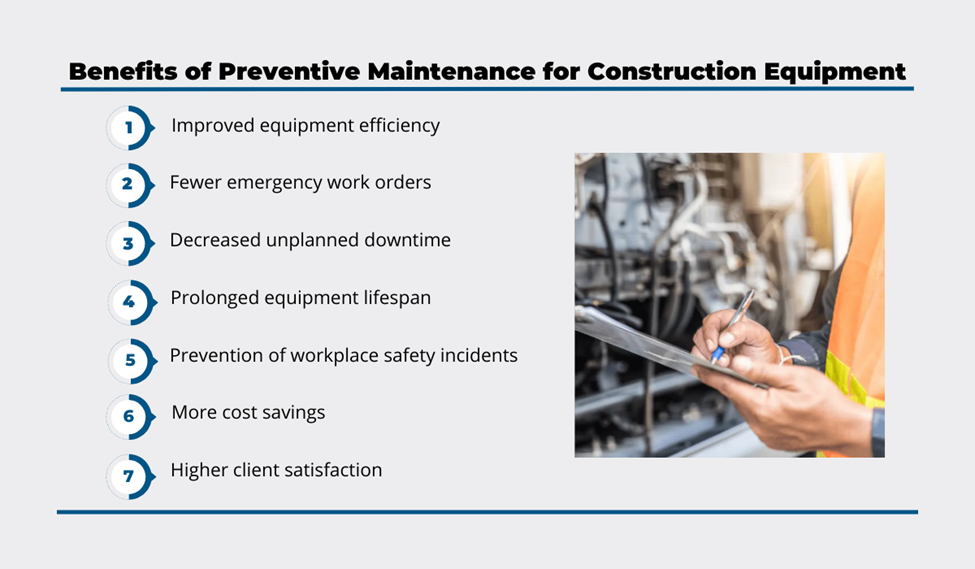
Given these advantages, it’s clear that preventive maintenance should be prioritized, and that includes estimating and budgeting for maintenance costs.
To estimate these costs correctly, contractors can refer to manufacturer guidelines detailing the type and frequency of regular maintenance tasks.
From there, they can use their own and/or others’ real-world knowledge to extrapolate how much to budget for preventive maintenance.
Naturally, if your company bought a piece of used equipment or is already using the same or similar model, records of past maintenance costs are a great source for making accurate estimates.
However, don’t forget to account for inflation, i.e., increased prices of spare parts and supplies and maintenance labor costs.
Furthermore, using maintenance management software like GoCodes Asset Tracking to track ongoing maintenance (and associated costs) and schedule routine service tasks can help you avoid those more expensive repair costs.
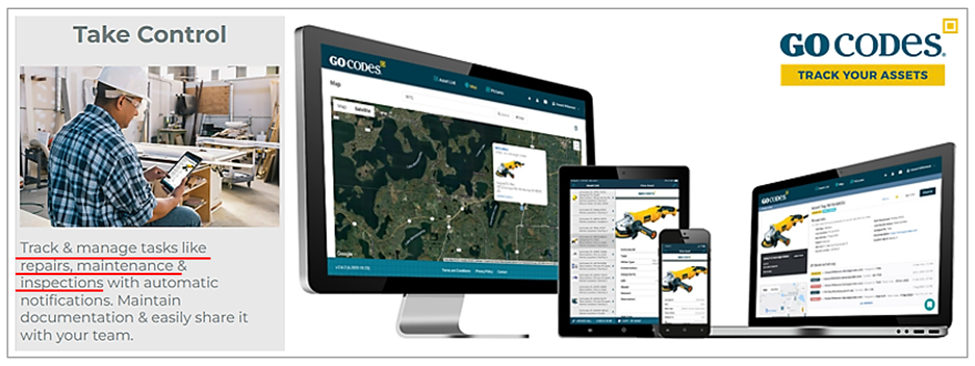
GoCodes Asset Tracking uses patented QR code labels (affixed to each piece of equipment subject to maintenance), cloud software, and an in-app scanner.
When a service technician scans the QR code with their smartphone or tablet, they’re instantly taken to the equipment’s info page, where they can access relevant data, such as maintenance and repair history, documentation, instructions, last service date, and so on.
At the same time, managers can schedule and track the performance of maintenance tasks, manage field service requests, and set up automated notifications for upcoming maintenance.
Naturally, all these functions allow construction companies to automate and streamline their maintenance operations, ensuring that equipment stays in good condition.
Overall, when properly estimated, planned, and tracked, maintenance costs can be optimized while minimizing the risk of major breakdowns and related unexpected expenses.
Costs of Replacing High Wear Parts
As you might expect, some components of construction equipment are exposed to higher levels of wear and tear than others, so you should account for the costs of replacing them.
Other than tires (covered separately below), examples of such high-wear equipment parts include tracks, bucket teeth and cutting edges, chains and sprockets, hydraulic hoses, filters, and brake pads and discs.
For example, in the below image of dozer components, the high-wear parts are highlighted in bold letters:
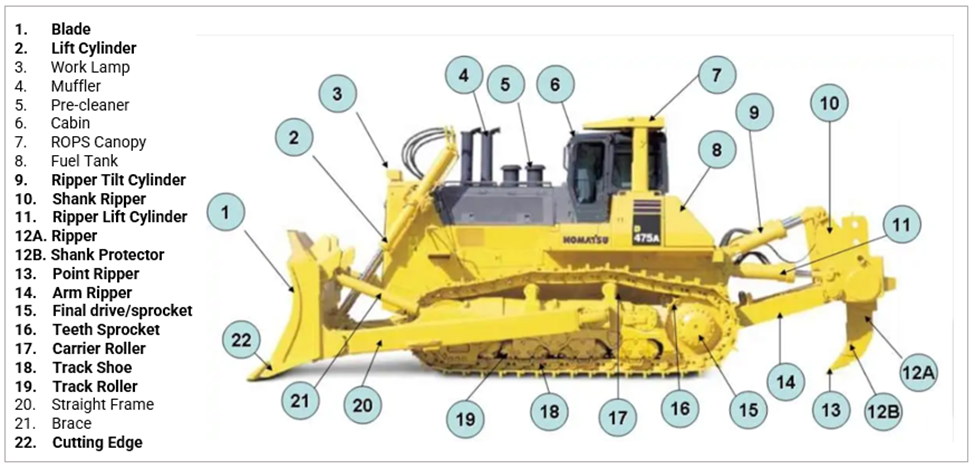
These components are subject to significant wear and tear, either due to their direct contact with abrasive materials or because of the stress they endure during operation.
As for how contractors can identify such parts on a particular machine and estimate the costs of their replacement, they can employ a number of strategies, such as:
- consulting the manufacturer’s manuals and maintenance guidelines
- reviewing historical maintenance records to gain insights into the wear patterns
- regularly inspecting key components for signs of wear, damage, or reduced performance
- tracking operating hours and comparing them to the manufacturer’s recommendations
- utilizing equipment management software to track maintenance schedules and component replacement intervals
By using these and other methods, maintenance teams can determine which high-wear parts should be replaced and when.
As for replacement cost estimates, they can consult the manufacturer’s documentation and contact equipment suppliers and dealers for information on the price, availability, and lead times of the replacement parts.
Naturally, this proactive approach will help contractors minimize equipment downtime, improve its reliability, and efficiently manage the costs of replacing high-wear parts.
Fuel Costs
Fuel typically has the largest impact on the operating costs of construction equipment.
For example, since most heavy equipment uses diesel fuel, Market Research Future estimates that diesel consumption:
…contributes more than 35% of operational costs of construction equipment, and fluctuations in the price of fuel and fuel consumption have a significant impact on the company’s profitability.
Aside from the fuel type, these costs are directly related to the equipment type and size, where larger and more powerful machines generally consume more fuel.
Other factors include the number of operating hours, the equipment’s fuel consumption rating, worksite conditions (e.g., rough terrain), and operator behavior (e.g., excessive idling).
Given the share of fuel expenses in the equipment’s operating costs, some manufacturers like Volvo offer a fuel efficiency guarantee for their machinery.
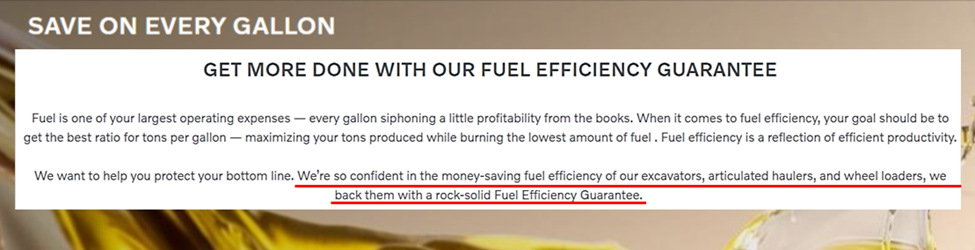
As for how to estimate future fuel consumption for budgeting purposes, we already mentioned factors like equipment type and expected operating hours, which should be used by construction companies as a baseline for calculations.
Alongside those, contractors should factor in the typical loads that equipment will carry or handle because operating near or at its maximum load capacity increases fuel consumption.
Lastly, there is a range of measures, such as route planning and idle time reduction, that can help you cut down the projected fuel costs and keep this major component of your equipment’s operating costs under control.
Tire Costs
As mentioned, many types of construction equipment have tires, and they wear and tear easily, and the costs of their maintenance and replacement represent another item to consider when estimating operating costs.
Naturally, the two major factors that affect how fast tires will degrade and have to be replaced are tire type and size.
In other words, selecting the right type of tire (all-terrain, off-road, on-road) for specific equipment and its applications is crucial for keeping tire-related costs down.
The same applies to their size, as oversized or undersized tires can lead to premature wear and tear and reduced efficiency.
Additionally, the type of terrain and equipment usage can also significantly affect tire wear, as these images illustrate.
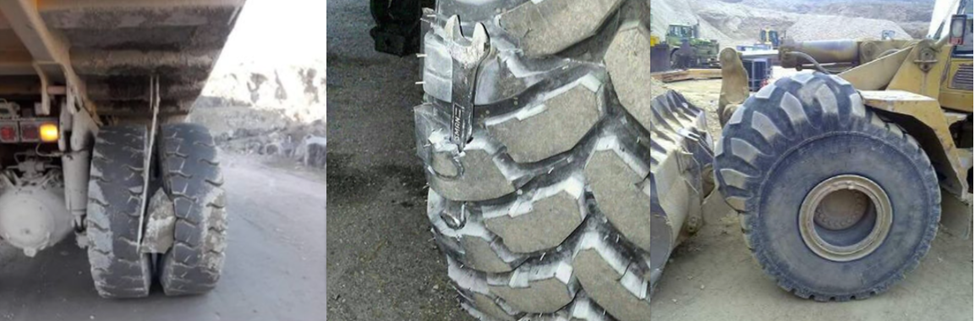
Other factors to consider and costs to budget for involve regular tire inspections and maintenance, such as proper inflation, alignment, and rotation, which can extend tire life and reduce replacement costs.
Furthermore, to keep tire costs under control, contractors should consider using equipment tracking software solutions that enable them to monitor tire conditions, detect issues early, and optimize tire replacement schedules.
To recap, construction companies should factor in the above considerations to better estimate and manage the costs associated with maintaining and replacing equipment tires.
Labor Costs
Last but not least, wages, training, benefits, and insurance for equipment operators and maintenance and repair workers constitute a significant portion of equipment-related operating costs.
Although no specific data on their share in operating expenses is available, overall labor costs in construction are estimated to be between 20% and 40% of any project’s budget.
As for available data on hourly and annual wages, in May 2022, the U.S. Bureau of Labor Statistics (BLS) provided the following figures:
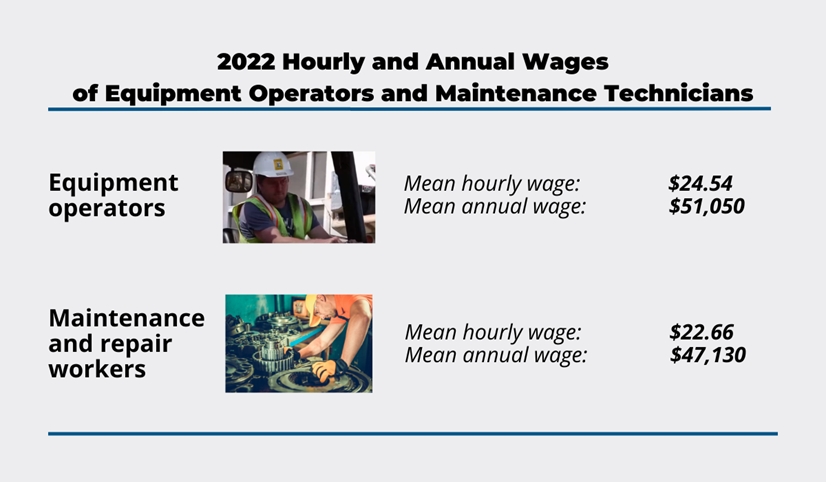
Naturally, these averages vary significantly depending on where your company is located, how well it pays its employees (or outsourced workers), their experience, and the complexity of the work they perform.
Therefore, aside from current industry wage rates and labor market conditions, when estimating labor costs for equipment operators and maintenance technicians, contractors should consult their personnel records and historical data.
For example, historical labor costs should give insights into cost variables other than salary, such as paid overtime, required training and certification, and provided benefits and insurance.
Additionally, for maintenance staff, cost estimates should account for specialized tools and equipment they need to perform their tasks effectively.
All in all, by analyzing historical data and staying in tune with industry trends, construction companies can more precisely estimate and better manage labor costs and thus their operating expenses.
Conclusion
In closing, we’ll highlight that better cost estimates of the six operating costs discussed in this article contribute to more accurate budgeting and can help improve any construction company’s overall operational efficiency.
Therefore, understanding and effectively managing these operating costs is critical if your company is looking to optimize its financial planning and achieve long-term success.