Life as a general contractor can prove professionally and financially rewarding, but it doesn’t come without its frustrations.
The best contractors learn not only from their own mistakes but from those of others as well.
They apply sound business principles while respecting the exceptional nature of the construction industry.
In this article, we will go over some of the most common mistakes contractors make.
Keep reading to find out how you can avoid falling into the same pitfalls.
In this article...
Winning Bids by Offering the Lowest Price
To make a long-lasting and successful career as an effective contractor, it is important to understand that well-built buildings do not come without price or without many elements working together.
Sloppy contractors simply seeking to win a job do not understand, or simply disregard, the fact that construction bidding is a structured, multifaceted process that requires research and the ability to project how your business might meet and exceed the client’s expectations.
As this visual aid shows, submitting the bid is only a part of the process:
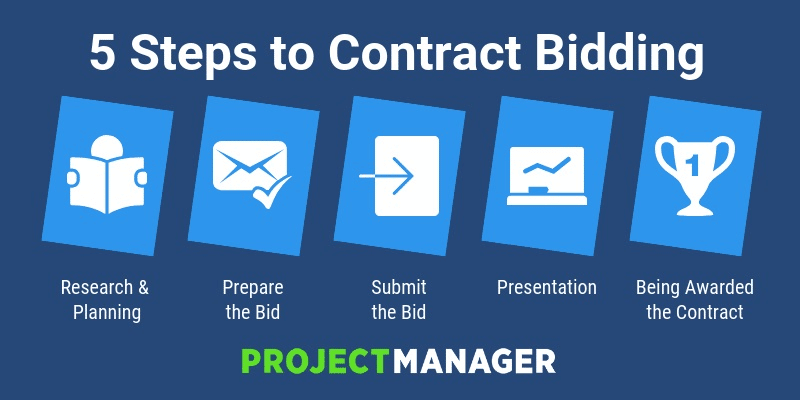
Research, logistical planning, comprehension, networking, and bid preparation all come before estimating a realistic price for the bid.
Failing to understand the final cost and/or deliberately undercutting the project’s basic costs are both massive mistakes that could adversely impact your construction company, even into bankruptcy.
You can avoid this damaging mistake by bidding strategically. Take the time to build an educated estimate.
Experienced contractors understand that bids don’t always go to the lowest bidder, but to the one who is responsive and responsible.
According to The Institute for Public Procurement (NIGP), that means the winning bidder often isn’t the one offering cut rates.
Instead, clients and public entities might study the bidders’ qualifications, reputation, past projects, and budgets while making a selection.
The entire project, then, is won or lost not at this stage, but with every relationship, reputation-building job, and daily safety record.
All these can become factors contributing to which bids are compiled and awarded.
Making Incorrect Construction Project Estimates
It’s easy to miss soft costs when putting together a construction estimate. Construction jobs are so much more than raw material and labor costs.
Other factors to consider include:
- Specialized equipment necessary to complete the project
- Insurance
- Temporary office quarters
- Marketing
- Wi-Fi on the site
- Accurate costs per square foot
- Updating licenses and renewing permits
- Relief facilities for crews
- Safety training courses
- Technology, such as mobile devices
- Taxes
- Contingencies
- Market fluctuations in raw materials
Incorrect estimates can cause unnecessary delays and cost overruns.
Autodesk states that 30% of construction companies find that over half of their data is bad, which can rapidly compound when compiling a complex estimate.
Most catastrophically, a string of underestimations can financially sink smaller or more unstable construction companies that are unable to absorb the loss.
Bad estimates can quickly erode cash flow during a project.
A study from TSheets and Quickbooks indicates that 29% of contractors earn less than expected on a job and that 60% feel very confident in the accuracy of their costs.
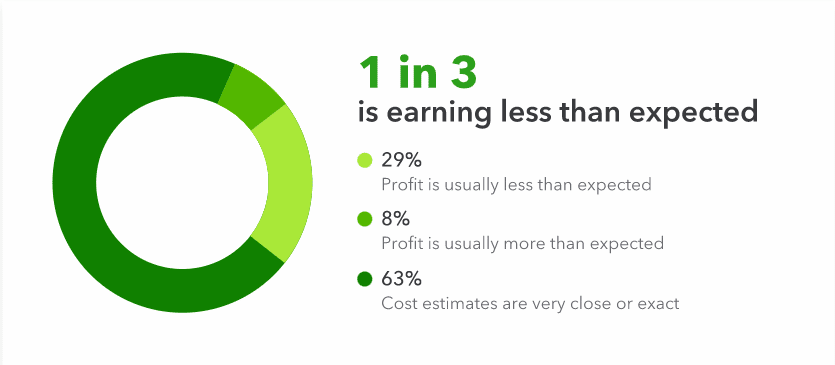
Making a correct construction estimate is a multifaceted process. In order to achieve success, it’s important to visit the site while you conduct it.
Most clients or public entities hold opportunities to visit job sites so that potential bidders can begin soil studies, take measurements, and look for unusual topographic challenges.
Potential subcontractors should visit the site as well; their specialties might require added costs, and a general contractor might not consider those at first glance.
Hiring Subcontractors Who Are Not a Good Fit
With the cost of raw materials and skilled construction workers spiraling, it’s tempting to add the lowest-costing subcontractor to a bid.
However, poor subcontractor performance can reflect negatively upon your company.
Clients often won’t care who put the crooked wall in place; they’ll just know it’s crooked, and that the name of your construction company is on the contract.
Sometimes subcontractors are well-meaning, but are poorly equipped or have sudden difficulty in securing the right labor force for the job.
Failing to hire the right subcontractors can end up negatively affecting the contractors in more ways than one.
Legal issues might come to the fore, and that always adds to the costs.
Project managers might have to find replacement subcontractors to conduct repairs or rebuild parts of the project, and purchase replacement materials.
Overtime pay is potentially necessary to avoid missing timeline milestones, and if a deadline is missed, penalties or loss of bonus pay could occur as a result.
Your company might have hired the right subcontractors, but managed them poorly, leading to scheduling conflicts, personality clashes, or territorial disputes.
Clear communication and establishing a web of respect between teammates are essential to avoiding subcontractor nightmares.
Ignoring the Importance of Construction Site Safety
Construction site safety is paramount.
It might take longer to conduct a job according to established safety codes and best practices, but doing so can avoid accidents, costly lawsuits, frustrating rework, or crippling fines.
The inherent danger of construction means that taking all necessary precautions to secure the site is common sense.
Every build is different, and the high turnover rate of construction forces can often mean that not every member of your team is working with current information.
Regulations can change as well.
Regular safety meetings, daily site walk-throughs, and ensuring that your labor force is outfitted with proper equipment might seem like annoyances, but ensuring these are in place can help to avoid severe consequences.
The Occupational Safety and Health Administration (OSHA) has established that the most common safety violations are related to the following:
- Protection from falls
- Respiratory protection (masks, etc.)
- Ladders and scaffolding
- Communication of hazards
- Training related to fall protection
- Hazardous energy control
- Protection for the face and the eyes
- Trucks
- Machinery and guarding of machinery
Knowing that these are common points of failure can help you understand what to emphasize in team safety meetings and training.
Note that citations related to falls appear twice in the list above.
That means you must seek out quality fall-related safety equipment and keep it in good repair, along with ensuring your workforce understands how to use it.
These two acts alone can strongly contribute to a safer construction site.
Consider the secondary impacts of failing to prioritize safety during your build:
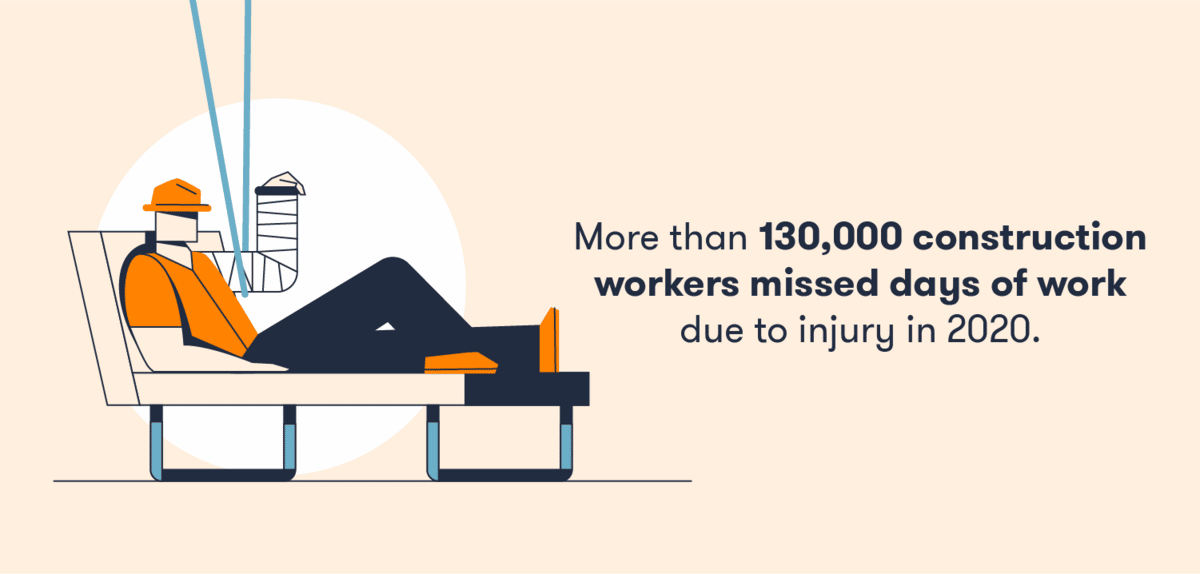
When construction workers must miss shifts due to injury, a ripple effect begins that can affect the entire job.
Temporary workers, usually secured at a premium, must join the team. Union or worker compensation rules might dictate pay for the injured employee while he or she is recovering.
Machine repairs or rework stemming from the incident may be necessary as well.
These costs aren’t always reflected in the job estimate, and running an unnecessarily dangerous site with shoddy equipment can lower worker morale.
Not Taking Proper Care of Tools and Equipment
Preventive maintenance also plays a major role in maintaining a successful construction company.
Contractors who fail to undertake simple preventive maintenance can needlessly keep repair costs high:
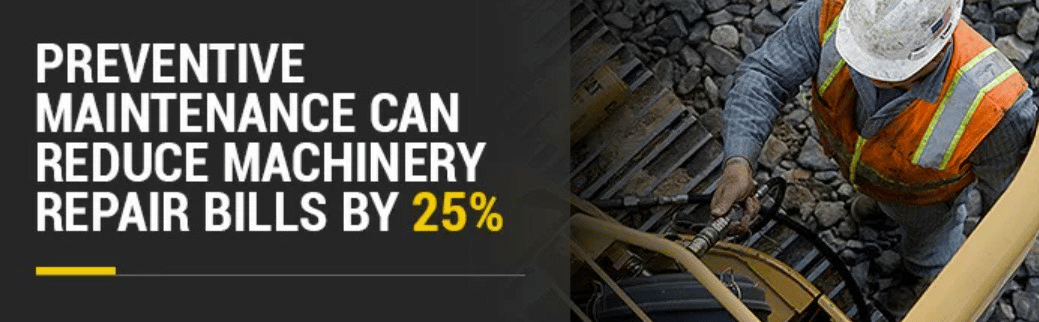
Good machine maintenance can help to stave off catastrophic machine failure, which is often a flashpoint for cascading costs.
Losing an important piece of heavy equipment can bring an entire team, and sometimes an entire site, to a standstill.
This in itself is costly, but that doesn’t address the expense of renting or even buying replacement machinery, often at high costs.
Training operators in effective maintenance practices, keeping to OEM (original equipment manufacturer) suggestions, and accurately documenting machine actions and regular services all constitute proper care for your equipment, which often represents a hefty investment for your company.
One way to easily and automatically keep track of machine maintenance is to invest in asset tracking.
Automating this process with a robust and flexible system like GoCodes can provide instant and secure access to maintenance records, warranty tracking, and other data necessary for repair.
The GoCodes system enables you to see when each of your tools or items in your fleet were last serviced, along with any notes about their quirks and characteristics to monitor.
The easy-to-scan QR app embedded in the GoCodes tag– which can attach to almost any material and weather all sorts of conditions–will also reveal the item’s chain of custody, serial number, and GPS location.
The system stores information in the cloud, which means it’s accessible to whoever is authorized to see it on a 24-hour basis.
This data, which is easily tailored to your company or current project, can help to prove compliance, establish ownership, and boost efficiency.
Conclusion
Everyone makes mistakes, and learning from them can help make you a better contractor.
Avoiding underbids or making incorrect construction project estimates are key to establishing a strong economic foundation for your project, as well as your company.
Finding quality subcontractors might prove more expensive initially, but this is preferable to harming your reputation or conducting expensive rework.
Additionally, contractors should not ignore the importance of their construction site.
And finally, the daily task of taking care of tools and equipment is a must to prevent any number of mistakes as a contractor or a business owner.