Fleet owners are often conflicted about whether heavy equipment tires should be regarded as assets or expenses.
While buying a set of high-quality tires can set you back a few thousand dollars, the fact is that tires affect the performance of your vehicles and, consequently, the quality of your services.
To ensure that you’re getting the most out of your tires, you have to know how to care for them. This article will help you learn more about tire maintenance for heavy equipment.
All the effort you put into it will be visible in reduced fuel and tire replacement costs. So, let’s see what maintenance tips you can start applying right away.
In this article...
Understand Your Tire Type
The starting point of your tire maintenance should be ensuring you’re using the correct tire type.
The right tire promotes heavy machine stability and worksite safety.
On the other hand, choosing an unsuitable kind of tire is associated with an increased risk of overheating, puncturing, and tread separation.
A construction worksite is already a dangerous place, so you should select the appropriate tire type to prevent any additional hazards.
To choose the right type of tire, it’s helpful to first understand the classification of heavy equipment tires.
All heavy equipment tires come with a code consisting of a letter and a number. You can use that information to determine the intended usage of a tire.
The tire company Tony Pneus lists four basic tire categories, which you can identify by the letter in the tire code:
C | Compactors |
E | Earth-mover equipment |
L | Loaders and bulldozers |
G | Graders |
Letters in the code are accompanied by a number, which indicates thread depths and patterns. Note that a smooth thread is not indicated by a number, but instead by the letter S.
1 | Ribbed (smooth surfaces) |
2 | Traction (regular) |
3 | Rock (regular) |
4 | Rock (deep thread) |
5 | Rock (extra deep thread) |
7 | Flotation (for yielding surfaces) |
S | Smooth (mine, hard ground) |
So, if you have a tire with the code L3, you can safely install it on a bulldozer working on rocky terrain.
If you have any doubts about the kind of tire you should choose, it’s a good idea to check the manufacturer’s handbook.
Another way to prolong your heavy equipment life cycle is to avoid using tires of different types at the same time on your vehicle, especially across an axle.
Heavy equipment tires can get costly, which makes the idea of mixing and matching tires or buying used ones sound tempting.
However, two different tires don’t provide the same traction and handling performance, so mixing them can damage the vehicle’s internal components.
Still, investing in the correct tire type will save you money in the long run because you won’t have to spend as much on repairs and equipment maintenance.
Perform Regular Tire Inspections
Regular inspections are a crucial component of heavy equipment tire maintenance because they help prevent accidents and prolong your equipment’s useful life.
All heavy equipment requires routine inspections, especially the equipment that operates on uneven or rough terrain.
Tires are usually the equipment element that bears the brunt of a harsh environment, so you have to check them regularly. Weekly inspections are mandatory, but daily inspections are ideal.
So, check the tire pressure at the start of each workday, because underinflation and overinflation can lead to tire blowouts.
Here is how the VP of the tire company Aperia Technologies sees the problem of underinflated tires:
“Driving on underinflated tires causes excessive heating, which is a tire’s biggest enemy, and causes most tire-related emergency road service events.”
Underinflation builds up the heat, which expands the tire and can lead to the tire exploding.
On the other hand, overinflation makes tires more vulnerable to impact and accelerates wear. Only the proper tire pressure can ensure optimal traction and braking capability.
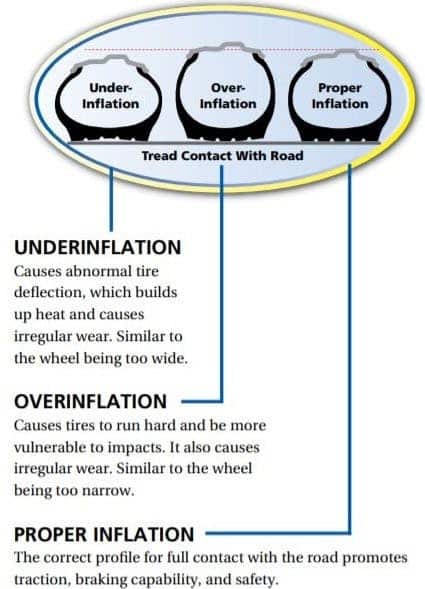
Kicking a tire to check the inflation won’t do; use a tire pressure gauge instead.
The next item on your tire inspection checklist should be tread depth.
Selecting the appropriate tread and pattern takes time. When you find a tire with the right tread for your equipment, you should regularly check the state it is in to ensure vehicle safety.
Otherwise, you could be risking accidents with severe consequences. For instance, in 2018, a worn-out tire tread caused an accident with eight fatalities.
The semi-truck driver hadn’t noticed the thinning tread on the front left tire, and the tire blew while he was driving, forcing the semi to veer off course and into a bus.
To prevent such accidents, you should always instruct your equipment operators to inspect the tires before driving.
We compiled a checklist to help you cover all areas of your heavy equipment tires.
You should check the tires daily for:
- Air pressure
- Tread depth
- Dirt or substance buildups
- Tire valve caps
- Sidewalls
Asking your employees to arrive half an hour earlier to perform a tire inspection may sound like a nuisance, but that’s a small price to pay for accident prevention.
Train Employees on Tire Maintenance
Heavy equipment tires are expensive. If you want to get more mileage out of them, train your employees to look after the tires efficiently.
These tires are also massive, so teach the employees to use safety tools and equipment when doing maintenance.
Each of your employees can probably change car tires with one hand tied behind their back, but heavy equipment tires are more demanding.
Before you assign your employees with tire maintenance, you have to equip them with theoretical and practical knowledge. You could write a manual or demonstrate the procedure yourself.
Either way, you should enhance the importance of maintenance safety.
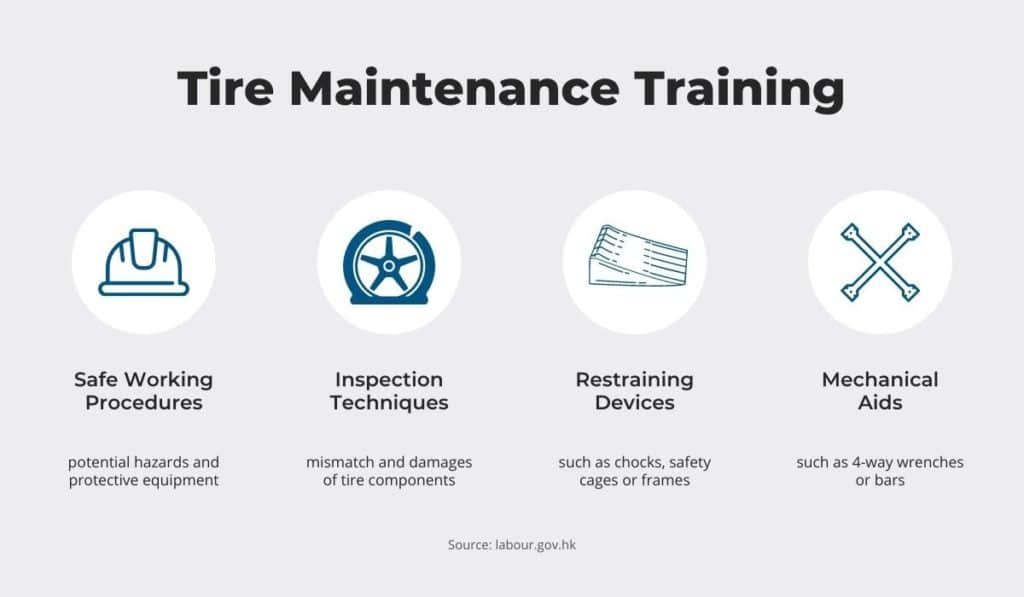
Your tire maintenance training should also cover inspection techniques so that the employees know what to look for and how to implement repair procedures.
Safe demounting practices should be included as well. Due to the size of heavy equipment tires, you can work on accident prevention by encouraging employees to restrain tire movement with safety cages or chocks.
Finally, your training should cover all tools used in tire maintenance and repair.
Since adjusting air pressure is the most common tire maintenance procedure, you should ensure each employee knows how to do it properly.
Keep in mind that tires can burst out with explosive force during inflation. To lower the chance of injuries, instruct your employees to assume a safe position for inflation outside of the trajectory danger zone.
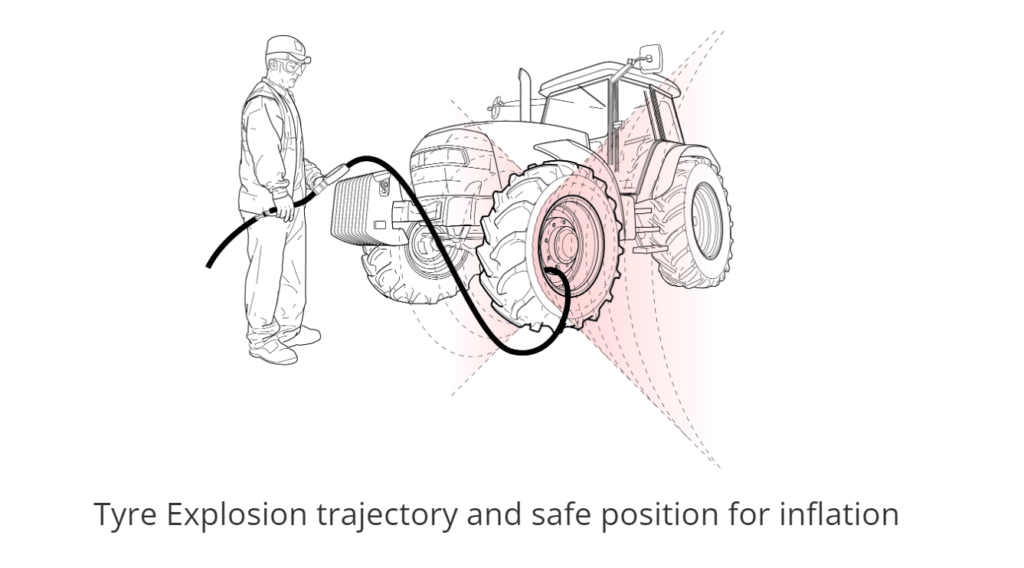
It’s worth noting that even though reinflating tires is a standard procedure, it still takes some preparation, especially if a tire has been damaged.
To sum up, when a tire is seriously underinflated or run flat, its components can be damaged or dislocated. Inflating the tire can make the loose parts explode, so make sure to inspect the damaged tire before reinflating it.
Promote Good Driving Habits
The way your employees drive their vehicles can prolong or shorten their tires’ useful life. To maximize the return on investment you get from your tires, you should promote good driving habits among your fleet drivers.
Heavy equipment tires are built to last. They are more expensive than passenger tires because they contain a higher percentage of natural rubber, a material suitable for heavy vehicles due to its heat-reducing properties.
Still, there is a limit to the abuse any tire will take, regardless of the price or materials used. Too many end up discarded sooner than necessary because employees ignore driving and operational best practices.
Sometimes you don’t need complex analyses to see what a tire has been through; the exterior surface can tell you a lot.
For instance, flat spots indicate that there was excessive sharp braking. Center wear can mean that the tire was overinflated.
You can take a look at the following chart to see some additional wear types and their causes.
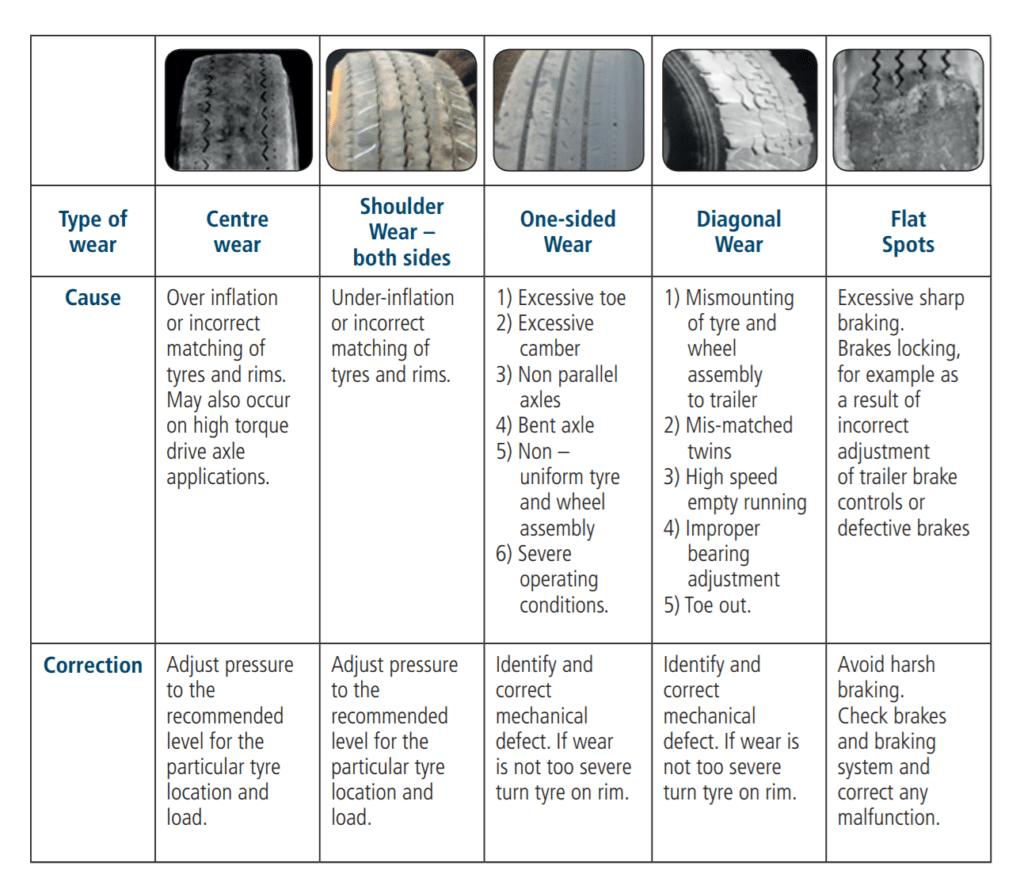
As you can see, driving and operating the equipment improperly accounts for a fair share of tire wear.
To keep your tires functional for as long as possible, advise your drivers to avoid the following habits:
- Driving at top speed
- Neglecting tire pressure
- Cornering and braking harshly
- Carrying excessive loads
- Driving haphazardly or on uneven surfaces
- Dry steering
- Ignoring maintenance
Good driving and operating habits will result in more than protecting your tires longer. You will also be able to spend less fuel per mile and enhance vehicle safety.
The Fleet Equipment Magazine offers several ways you can promote good driving habits among your staff. They suggest giving cash bonuses to those drivers with the lowest tire removal rates, or those with the fewest tire-related service calls.
In addition to financial incentives, make sure to go beyond explaining the how of the preferred driving practices.
You should strive to also explain why a specific practice is encouraged so that the drivers can understand and carry it out better.
Implement Best Tire Tracking Practices
You put a lot of effort into selecting, purchasing, and maintaining tires. If you incorporate just one additional step into the process, you’ll get data on which you can base your future tire-related decisions.
We’re talking about tire tracking.
In business, information is power—for big fleets and small contractors alike. Luckily, compiling the data for tire management isn’t too demanding.
You generate potential data each time you purchase, repair, or replace a tire. Jotting down the date on a piece of paper is one option.
Still, it’s better to use a solution that allows you to easily access the information, such as our tracking solution, GoCodes.
The solution was designed with construction companies in mind, so you can easily manage your fleet.
GoCodes provides you with an overview of your assets, together with all the additional notes you enter. If you record the purchase date for a set of tires, you’ll be able to calculate when they need replacement.
You can also note down the maintenance procedures performed, so your calculations can be more precise.
Even the American Trucking Associations (ATA) has included tire tracking into their acclaimed Recommended Practices Manual.
The Recommended Practice 208, total tire cost determination, suggests that fleet managers track and analyze annual heavy-duty vehicle tire cost, durability, and fuel efficiency.
Tracking tires goes beyond noting the purchase and replacement dates. For instance, GoCodes lets you see who used a vehicle and when.
Analyzing such information combined with regular tire inspections can help you determine if you have an employee whose driving habits could be improved.
All in all, an insight into the source of tire wear can give you a solid base for tire management. You can only combat tire wear properly if you know its cause, so consider tracking for the most accurate wear predictions and replacement plans.
Conclusion
Tires that aren’t properly cared for can be a drain on your resources. However, if you approach them with care, your crew will be able to achieve great results with your heavy equipment.
Tire maintenance should start with selecting the right tires. You can prolong their useful life with regular inspection and maintenance.
In addition to applying the driving and maintenance practices that benefit the tires, don’t forget about the safety of your workers either.
To avoid unplanned tire replacements, you can use software to track tires and schedule maintenance accordingly.