The nature of construction projects confronts construction company owners and project managers with exceedingly complex challenges.
To address those challenges, the construction industry has developed different project management methodologies and keeps trying out new approaches that work well in other industries.
We’ll explain four construction project management methodologies you should know about, some of which are tried-and-true methods and some relative newcomers in the construction industry.
In this article...
Agile Project Management
Faced with rising project uncertainties, construction companies are increasingly applying the principles of agile project management, both in their construction projects and organizational setups.
Although agile project management can’t be simply copied onto construction projects, it can provide valuable methods to deal with ever more complex and unpredictable factors that affect the entire construction industry.
The agile management method originated in the mid-1990s in the software development industry as a reaction to traditional waterfall project management methods, which we’ll explain in later sections.
As such methods were seen as slow, inflexible, and incompatible with efficient software development, this yielded a new method—agile project management—whose principles were soon applied in other industries like manufacturing and construction.
Here are just some of the attributes associated with agile projects and organizations.
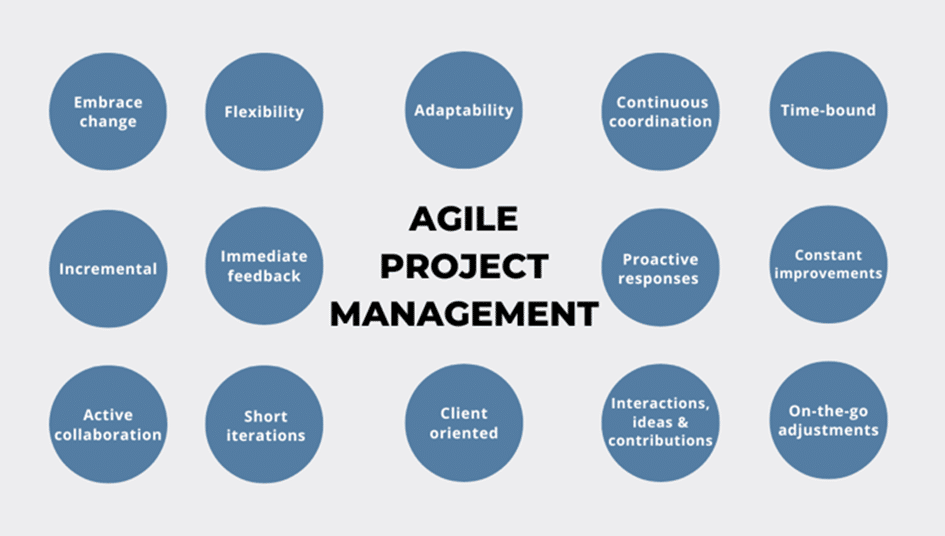
In theory, these characteristics look like the answer to many issues construction projects usually face, such as delays and budget overruns caused by, for instance, changes in project scope.
Agility is all about the ability to handle uncertainties effectively, and the construction process is full of them.
For example, inaccurate project estimates, quality issues, rework, or poor communication can shatter even the best-laid construction plans, causing delays and budget overruns.
In fact, in one survey, McKinsey found that 86% of projects break their budget and last 20% longer than expected, on average.
In another survey, they found that 82% of respondents think that a more agile organizational setup will be one of the critical factors for their successful survival of inevitable changes in the construction industry accelerated by recent health and geopolitical crises.
One study compared agile and traditional management approaches.
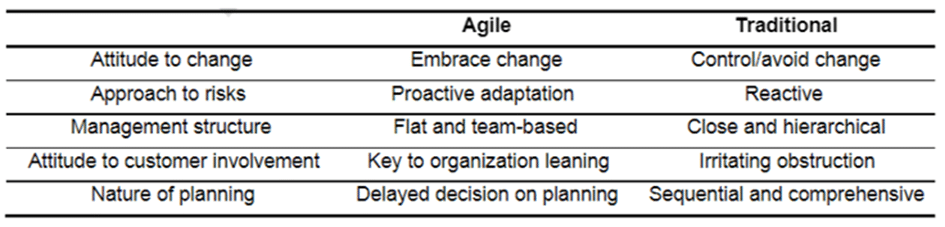
At first glance, the agile methodology looks superior to traditional management as it welcomes change, proactively adapts, and fosters collaboration and learning.
However, the above table also reveals its biggest flaw as a standalone construction project management method, at least in the context of running a large construction project based solely on agile principles.
Namely, such a project would forego extensive planning and design of all project phases to allow for ongoing changes, adaptations, and improvements.
But the nature of planning complex construction projects with many different stakeholders, parameters, risks, and interdependencies is necessarily comprehensive and sequential.
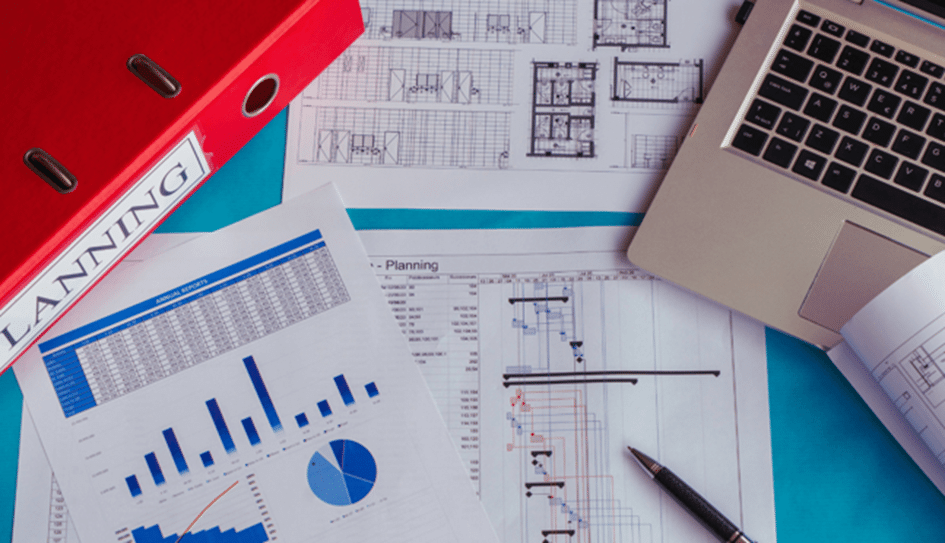
This would mean that, for example, agile principles can be applied during the pre-construction phases (project initiation, planning, and procurement) to achieve this “traditional” goal of construction project management.
With its focus on the project stakeholders’ input, collaboration, and interactions, and its responsiveness to change, agility can be used to keep everyone on the same page and “lock” the project scope, schedule, and budget before construction starts.
Further, some smaller projects (like renovations of older buildings with many uncertainties), if managed by a skilled construction manager and their team, might be run on agile principles throughout their lifecycle.
All in all, as the uncertainties are quickly rising, fueled by recent events, construction companies are looking for ways to adapt, and agile project management offers valuable strategies to do so.
However, agility doesn’t happen overnight.
Lean Project Management
Lean construction project management focuses on maximizing value for the client by minimizing wasteful activities throughout the project lifecycle.
It does so by empowering the construction team to look for improvements, apply them and transfer lessons learned, thus enhancing quality, productivity, and safety.
As a standalone project management method, lean management is more suited for construction projects than the agile approach.
Still, it usually works best in conjunction with traditional project management methods.
With its roots in the Japanese and American car manufacturing industries, lean project management is all about increasing the quality and speed of different processes by eliminating or minimizing the so-called process waste.
To define what is meant by this, we’ll use a real-life example.
When McCarthy Building Companies is engaged under a lean project delivery contract, they focus on eliminating eight types of wasteful activities:
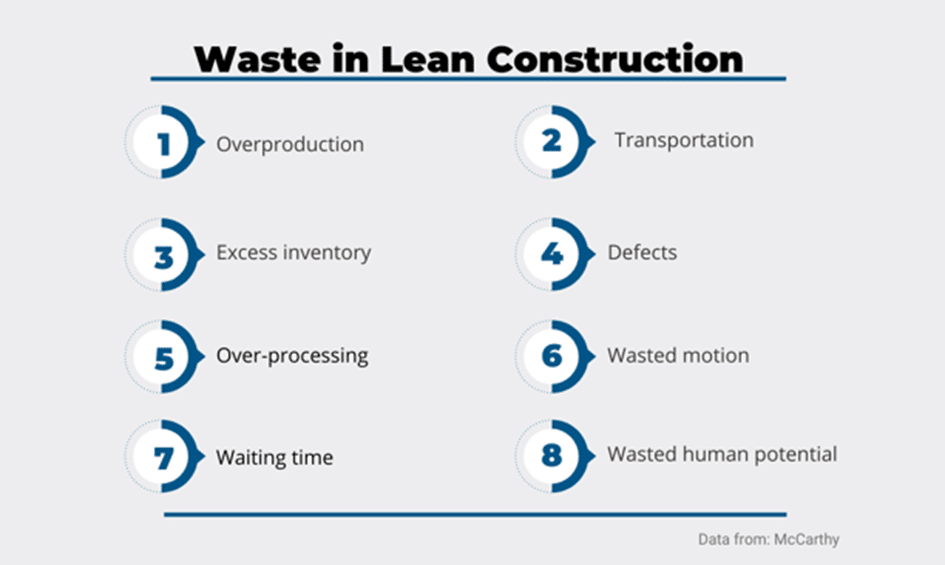
The elimination of some of these factors, such as the time workers spend waiting for the right materials or equipment to arrive on-site, is self-explanatory.
Others, however, require a bit more elaboration.
For example, transportation waste occurs when construction resources (labor, equipment, and materials) are misallocated, over or underused, or present on-site before they’re needed.
This is tied to wasted motion, which implies unnecessary movements of the said resources.
For example, multiple trips workers must take because materials are not located as close as possible to their point of installation, preferably in pre-packaged kits together with necessary tools.
In lean construction, excess inventory is also a source of process waste.
In other words, if materials or equipment are not needed immediately, it’s considered wasteful to let them sit idle on a construction site.
That’s where just-in-time (JIT) and other lean methodologies are used to optimize a construction project’s or company’s inventory levels.
Naturally, nowadays, the efficiency of all these methods relies heavily on utilizing different software tools and other technology.
For instance, a simple and affordable solution like GoCodes would help you apply lean principles in your company by tracking all tools, equipment, and material inventory levels, allowing you to analyze their status and utilization rate, and optimize material and equipment management.
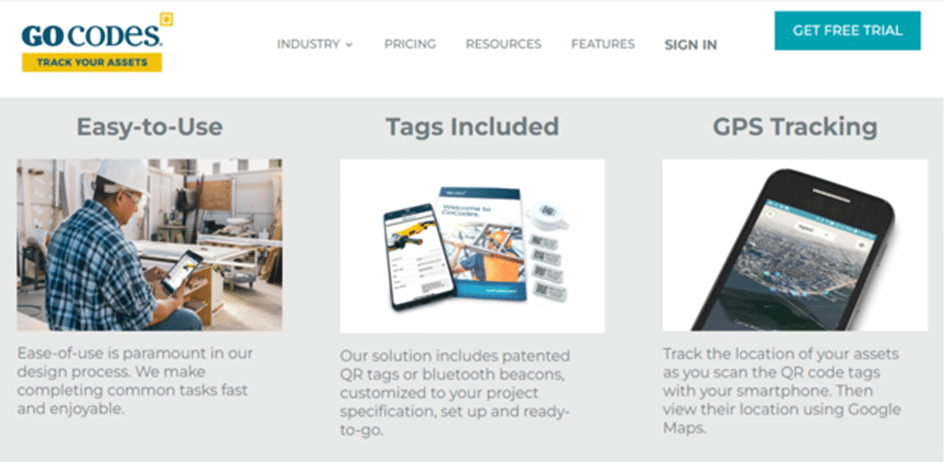
This and other construction management software can streamline the entire construction process and facilitate the uptake of lean principles in construction companies.
To see those principles in action, we can use McCarthy as an example again.
In their lean culture, after the value stream (project scope) is defined and all project stakeholders are clear on their tasks, they’re encouraged to innovate by removing from them what they consider inefficient, thus maximizing productivity and minimizing waste.
After an inefficient aspect of the process is identified and removed, the resulting fix is reviewed by the key staff and then applied on the project level, where necessary.
Of course, mistakes happen. They’re considered valuable, and stakeholders are encouraged to share the lessons they’ve learned.
In conclusion, lean thinking focuses on constant improvements and waste elimination, continuous monitoring, and adjustments by empowering individuals and team efforts to maximize value for the client by enhancing productivity and reducing lean construction waste.
Waterfall Project Management Method
Waterfall is the oldest and still most widely used construction project management method that relies on detailed planning to create a highly structured sequence of events that lead to successful project completion.
While the waterfall method is in many ways ideal for construction projects, it can be inflexible when addressing project changes and does benefit from integrating parts of other management methods discussed here.
This “traditional” project management methodology aims to capture all project requirements and mitigate risks through detailed planning and structuring of the entire project into a single sequence of tasks, where each project phase and milestone depend on the completion of the previous one.
And while various studies provide different breakdowns of the main stages of construction projects, they all have one thing in common—they flow downstream like a waterfall.
Here’s one example of the key phases of construction project management in the waterfall model.
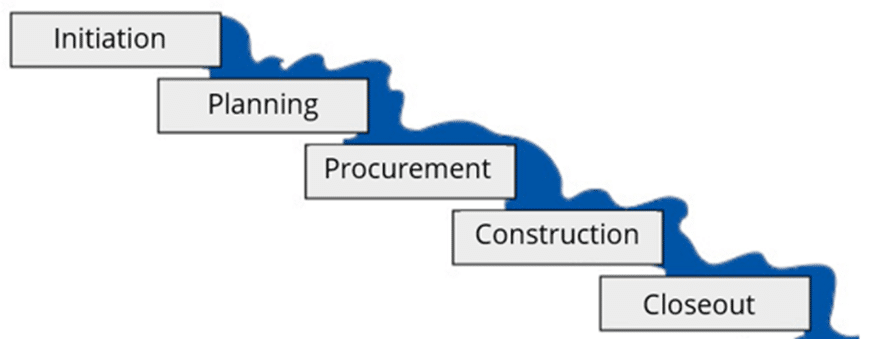
This method originated from construction and production processes where once a task is completed, you can’t go back and make changes or correct mistakes (at least not without great cost and effort).
For example, if the project milestone is to lay the foundations of a building, changes to the floor plan after the foundations are poured would be highly impractical and expensive.
Likewise, if substandard concrete was poured into the foundations by mistake, this can be undone by costly rework, but only if the error is caught early enough.
Otherwise, such miscalculations can cause exuberant costs, like in the case of San Francisco’s leaning Millennium Tower, described in The Architect’s Newspaper.
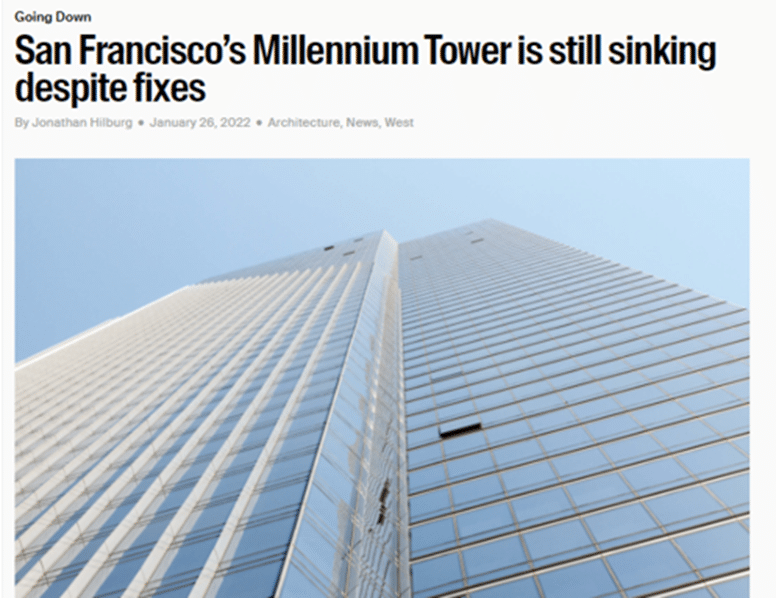
That’s why, considering the increasing complexity of construction projects and the need to avoid mistakes that are difficult to fix, this highly structured method is in many ways ideal for construction projects.
When you’re dealing with complex and specific high-value, time-restricted, and mission-based construction projects that involve many different stakeholders and face even more risks, this methodology is often the best way to successfully complete the project in terms of time, cost, and quality.
However, despite comprehensive planning and risk assessment, the structure (i.e., schedule and budget) created by using this methodology is often inflexible, and not conducive to larger project changes.
Still, they need to be incorporated into the project (change order management), which too often results in delays and budget overruns.
Thus, the waterfall model (i.e., all or some project phases) can and should be augmented with parts of other project management methodologies to enhance its performance.
For example, the causes of construction delays, as complex as they are, call for proactive, flexible, and adaptive solutions, i.e., agile project management.
All in all, waterfall is a time-tested approach to project management, with deep roots in the construction industry.
With it, you will be able to deliver projects on time, within budget, and with sufficient quality.
When enhanced by other methods, it’s still the best option for most construction projects.
Critical Path Method
This old-school method creates a sequence of interdependent tasks in a schedule that will lead the project from initiation to completion along its critical path.
It’s often used as an extension of the waterfall method and combines well with agile and lean approaches.
The critical path method (CPM) was developed in the 1950s by two DuPont mathematicians looking to avoid costs caused by inadequate scheduling.
At the same time, the U.S. Navy independently developed a very similar method called Project Evaluation and Review Technique (PERT).
Although slightly different, both methods were predicated on the assumption that a project can be broken down into a chain of manageable tasks while identifying which of them depend on the timely completion of preceding tasks (critical path) and which don’t (usually only for a specific period called the float, or slack).
To do this, CPM uses the work breakdown structure like this Level 1 phase-based plan for constructing a house.
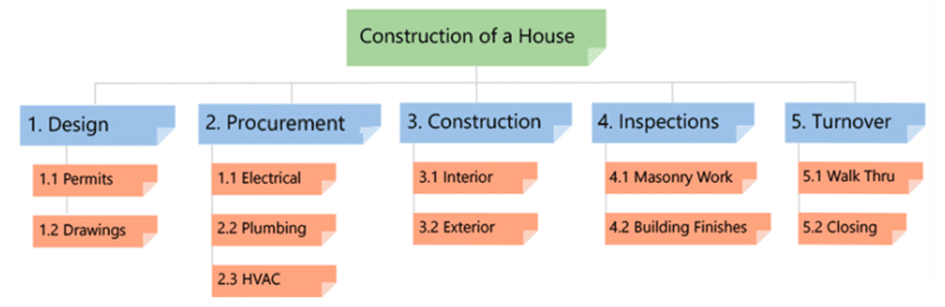
When all these tasks are taken in sequence, they create the total project duration or the project’s critical path, along with identifying a chain of critical activities to be performed for successful project completion.
Non-critical activities whose beginning or end can be delayed for a particular period without moving the project completion date are then assigned specific times (usually in days), i.e., their floats are calculated.
After all, activities are defined, prioritized, and sequenced, this project management method gives you a clear picture of all the tasks necessary to finish a project, i.e., the schedule.
Moreover, it allows you to manage interdependent tasks, mitigate risks and handle unexpected events more efficiently as the construction unfolds.
In fact, the project schedule opens itself to finding different ways to shorten the critical path.
This table, courtesy of Ten Six Consulting, shows seven path-shortening methods and their effects on the project quality, scope, and time.
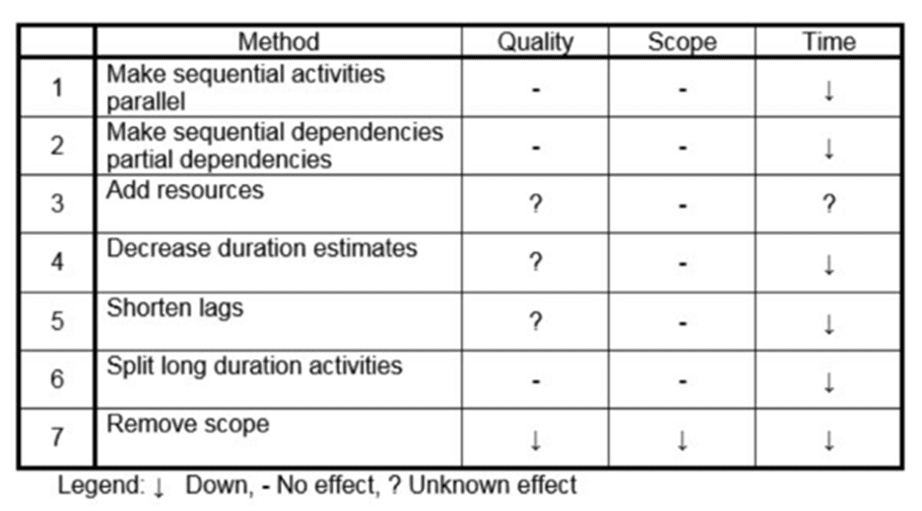
Mind you, some of these methods, like adding resources, might cause cost overruns.
As said, the critical path method allows you to establish a sequence of events that will ensure the project is finished on time and within budget.
When CPM is coupled with powerful features of construction management software, it enables you to monitor and manage a multitude of factors affecting the project schedule, from design errors to unknown site conditions.
When this method is imbued with other project management approaches, it can be the best tool for guaranteeing productivity throughout the project lifecycle.
Conclusion
After we’ve covered four popular project management methodologies used in construction projects, just keep in mind that construction projects seldom have one-size-fits-all solutions.
Thus, evaluate your project, select one method that best fits your project management needs, or opt for a hybrid approach where you combine some aspects of these methods to specific construction project phases and processes.
Thank you for reading!