As a construction company owner or manager, you know that managing inventory, whether consumable or durable, across various job sites can be demanding.
However, navigating the complexities of inventory management is paramount to ensuring smooth operations and maximizing profitability.
That’s why this article will explore six essential tips you can leverage to master construction inventory management, streamline processes, and enhance productivity, security, and safety on your construction sites.
In this article...
Centralize Your Storage
In the world of construction, companies employ diverse strategies to organize the transportation and storage of inventory across their job sites.
For example, some contractors may utilize offsite storage facilities, such as rented warehouses or secure yards, and regularly transport materials and equipment to and from the construction sites as needed.
This inventory management method comes with its own set of challenges, such as losing time and spending money on constantly traveling between storage and job sites.
As opposed to this, centralizing storage directly onsite can be a great way to optimize inventory management and bolster overall operational efficiency.
More precisely, here’s a breakdown of the advantages gained by consolidating construction inventory within one or a few easily accessible onsite storage locations.
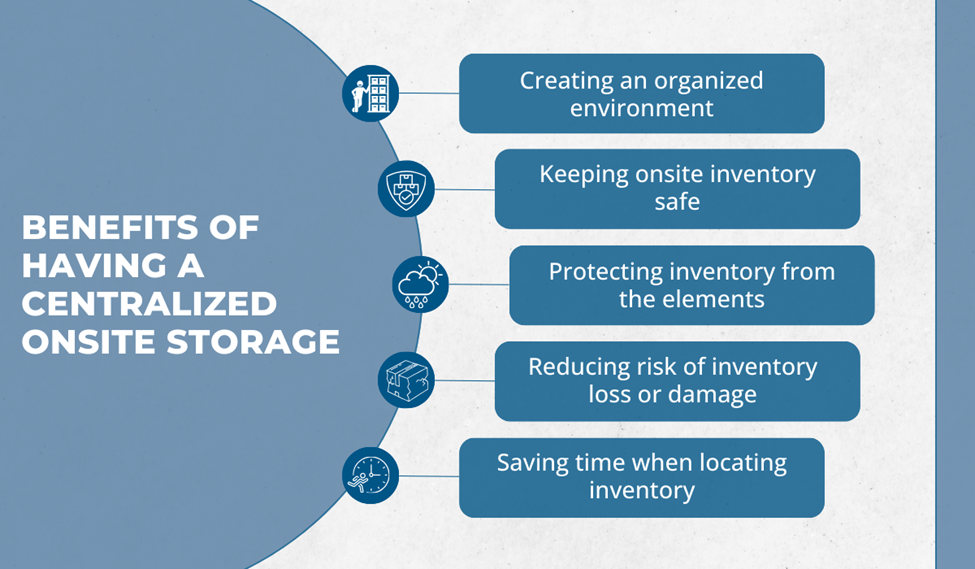
As illustrated, opting to keep your inventory onsite brings about many benefits, among which better organization, immediate accessibility, and minimized search time stand out as the most significant productivity drivers.
Additionally, when your storage is a secure area protected from the elements, you’re ensuring materials, tools, and equipment are better protected from theft while minimizing the chances they’ll get lost or damaged.
Although protective covers, like tarps, canopies, and tents, can be efficient in protecting your inventory from adverse weather conditions, they provide a less secure environment than onsite storage containers such as the one depicted below.
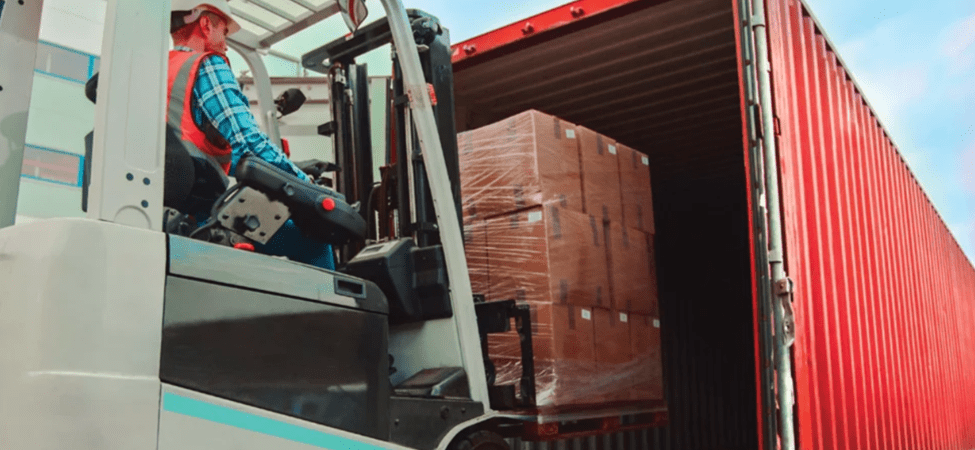
Moreover, such containers can be fitted with the necessary cabinets or shelves for inventory in advance.
Regardless of whether they’ll be holding materials or other supplies like tools and spare parts, they can be prefilled at your company’s or your supplier’s main storage facility and transported to the site as such.
Therefore, when starting construction on a new site, consider centralizing your storage for all materials, tools, and other inventory items.
In doing so, the location of your storage area on the site, as well as its inner layout, should be selected with easy retrieval and efficient inventory control in mind.
Implement Technology Solutions
Because they recognize that paper forms and digital spreadsheets are things of the past, implementing technology is a go-to solution for forward-looking construction companies.
In other words, if you’re still using manual methods to track your inventory, technology can help you automate and streamline inventory management processes, reducing manual errors and saving time.
Here are just some reasons for adopting an automated inventory management system:
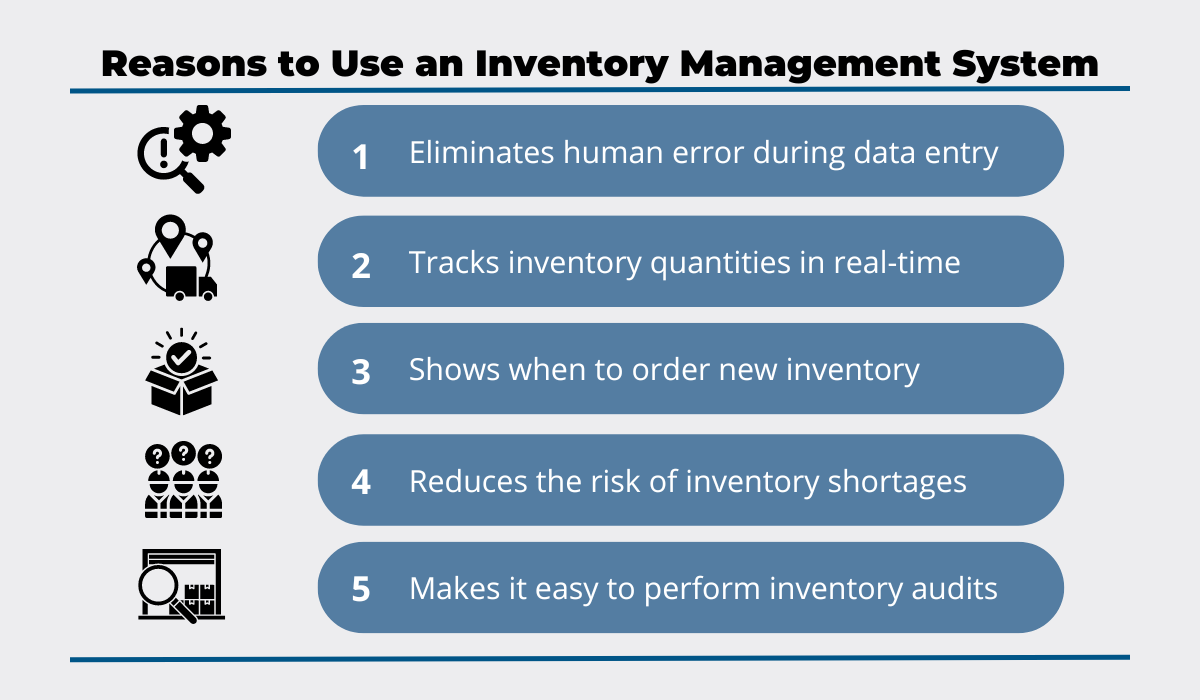
For instance, relying on traditional manual data entry and spreadsheet tracking for inventory management results in inventory changes typically being documented long after they happened.
On top of that, these changes are recorded in spreadsheets that can’t be easily shared between all stakeholders.
This makes the process inefficient, time-consuming, and error-prone, leading to discrepancies in inventory records and potential stockouts or overstocking.
Conversely, a lot of these issues are eliminated when workers can use their smartphones to quickly check the location of materials or tools and easily record what they took.
The simplest and most affordable way to do that involves using barcodes or QR codes attached to inventory items, cloud-based software with a mobile app, and an in-app scanner.
These components are essential parts of GoCodes, our inventory tracking app, and you can see them in action here.
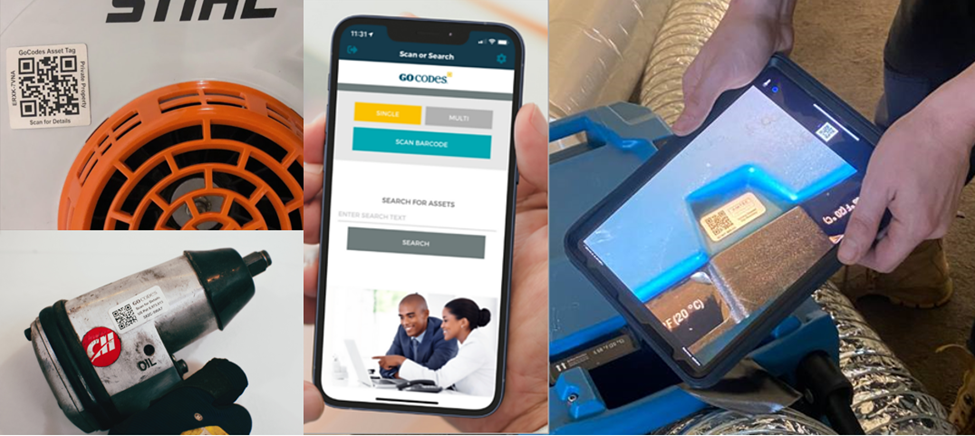
Implementing our technology solution is simple.
Once you have the GoCodes software and our mobile app installed, you order or self-print our barcodes or QR codes.
After they’re affixed to inventory items, they will serve as their unique identifiers.
These tags are then connected to the software’s cloud database, and specific data about each item is added.
For consumable materials, spare parts, and supplies, you can instruct the software to track the quantity of the items stored in a container or a pallet, and then alert you when the inventory count hits a predefined number.
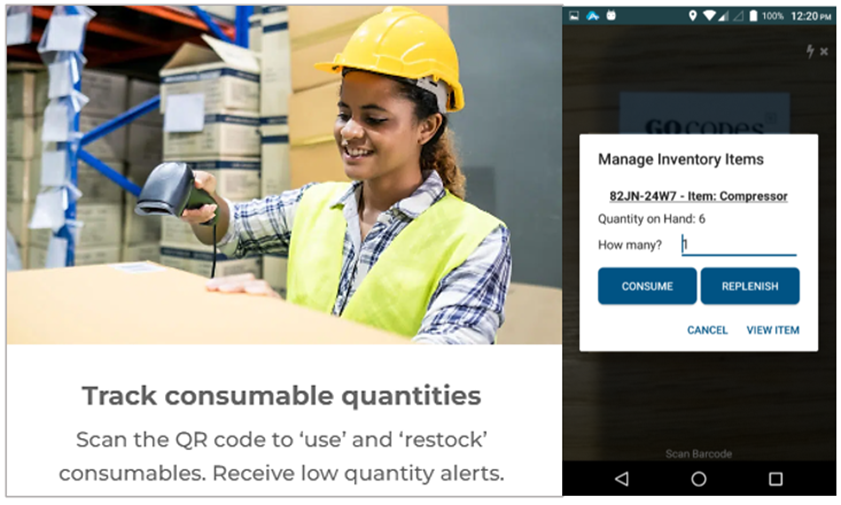
For more durable assets, such as tools and equipment, you can use the same software system to track many relevant data points, such as past and upcoming maintenance tasks and inspections.
Moreover, whatever items are labeled with asset tags, their location will automatically be recorded every time someone scans their tag.
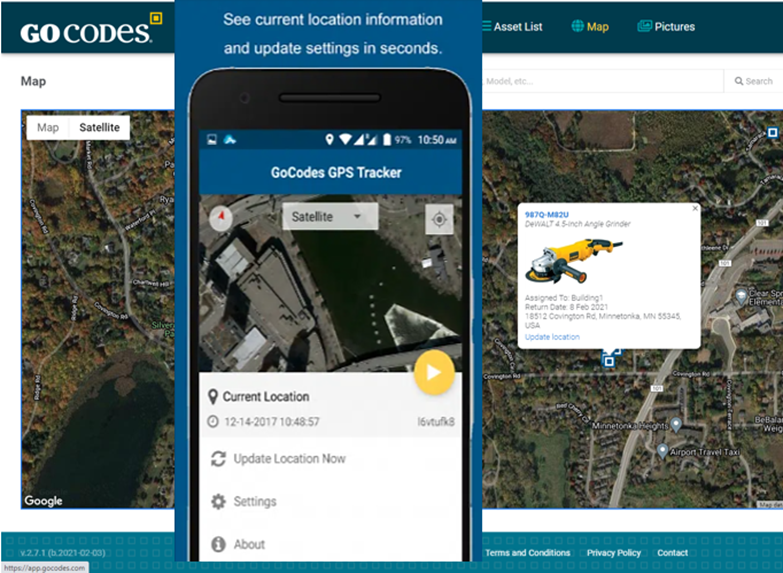
Since placing active GPS trackers on all inventory items would be impractical and too expensive, these GPS-enabled QR code tags are an ideal alternative for cost-efficiently keeping track of your construction inventory.
With the help of this technology, you get:
- real-time visibility into inventory levels and usage,
- increased accuracy in inventory tracking and forecasting, and
- seamless integration with other construction management software tools.
Overall, implementing an inventory tracking solution tailored to the construction industry is the most effective and cost-efficient way to revolutionize your inventory management processes, get full visibility, enhance worker accountability, and minimize theft.
Conduct Regular Inventory Audits
Conducting regular inventory audits is a fundamental practice that contractors should prioritize to ensure inventory accuracy and minimize the risk of discrepancies.
Regardless of how frequently they’re performed, each inventory audit involves physically counting inventory on-site and comparing those numbers with the recorded inventory levels in the system.
This implies you’ve already established a digital inventory control system, i.e., conducted an initial audit of your company’s complete inventory where all items were counted, categorized, and tagged, and the collected data entered into the system’s database.
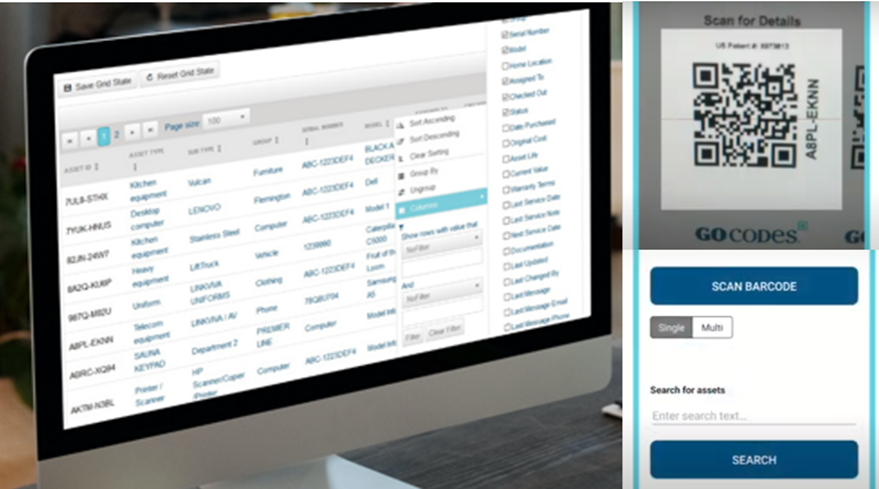
Once this initial step is done, it will be much easier to efficiently conduct regular inventory audits, whether they cover one specific job site or several of them.
In any case, the auditing process will help you identify any discrepancies between the physical inventory and the recorded inventory, enabling you to take corrective action promptly.
For instance, you might find that some inventory items on-site were miscounted, some are missing, and some have expired.
By conducting regular audits, your team can detect and rectify such errors in inventory records.
This not only ensures the availability of materials and equipment when needed but also helps prevent unnecessary expenses associated with carrying excess inventory or ordering duplicate items.
Moreover, regular audits contribute to improved decision-making on inventory levels and usage, enabling you to:
- optimize inventory management processes,
- minimize waste, and
- allocate resources across projects more effectively.
Simply put, conducting regular inventory audits is a proactive measure that contractors should adopt to maintain inventory accuracy and enhance operational efficiency.
Standardize Inventory-Related Processes
Whether your company is still relying on paper and spreadsheets, or it has introduced an inventory management app with scanning technology, your inventory-related processes should be standardized.
In a manual, paper-based system, this would imply standardized forms that should be filled out when on-site inventory is received, stored, and issued.
As for digital solutions, standardizing inventory management processes involves establishing consistent procedures for tagging, scanning, and recording inventory movements.
For instance, this can include providing training to staff on how to use the app’s scanning mode correctly, so workers can save time and scan multiple inventory items at once.
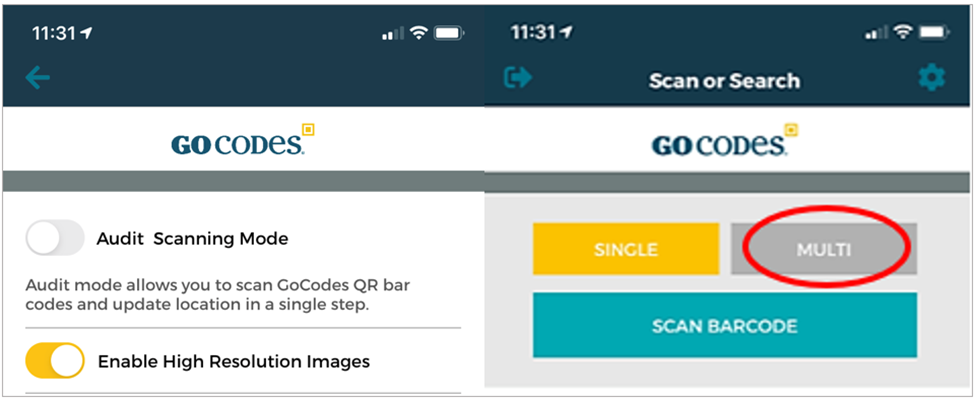
Another example involves creating standardized workflows within the app for handling different inventory-related tasks, such as receiving shipments, transferring materials between locations, and conducting inventory audits.
For example, when receiving a shipment of materials, employees would attach a QR code on each item and use the app to enter relevant information, such as quantity and location, and confirm receipt in the system.
Similarly, when these materials are used on-site, they would scan the QR code tag to record their consumption.
By standardizing these processes, i.e., clearly outlining the steps to be followed for each process, you can ensure consistency, minimize errors, and improve overall efficiency in inventory management.
Maintain Relationships with Reliable Suppliers
In addition to your internal processes, there are external factors that can be streamlined to enhance your inventory management.
Among them, maintaining good relationships with reliable suppliers and vendors stands out as a strategy that can help you ensure the timely delivery of materials and other supplies and negotiate more favorable terms to minimize lead times and costs.
Moreover, close relationships with suppliers allow you to implement a just-in-time (JIT) inventory management strategy.
This strategy can be defined in the following way:
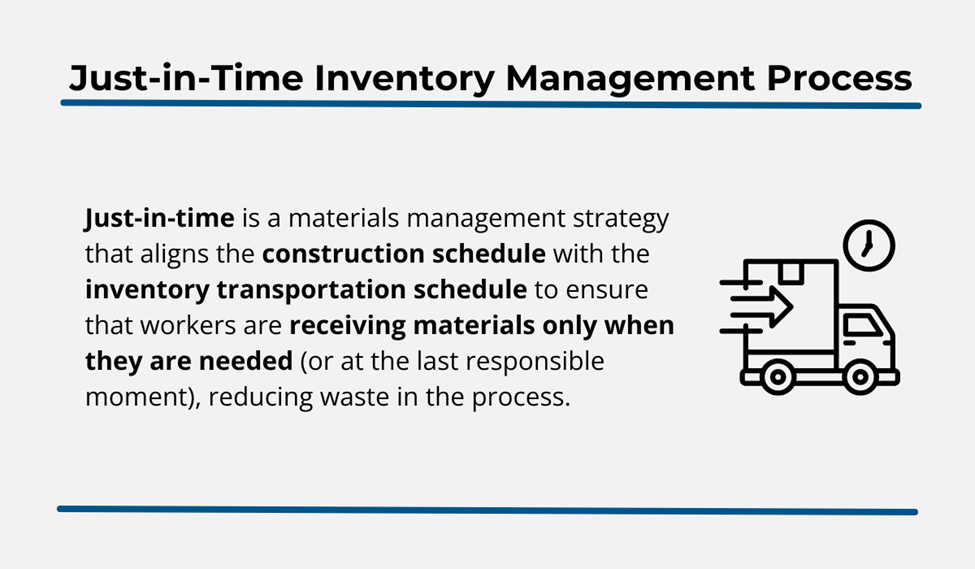
As explained, this inventory management strategy allows you to minimize inventory kept on hand by coordinating crucial material deliveries with established project timelines.
This ensures that materials are delivered to the construction site precisely when needed.
Therefore, well-planned and closely coordinated JIT deliveries can:
- reduce the need for excess inventory storage on-site,
- minimize inventory waste, and
- optimize resource allocation and utilization.
Beyond JIT, maintaining close supplier relationships provides several other benefits.
For example, it fosters collaboration and communication with trusted suppliers, which increases the likelihood they’ll be more responsive to your inventory needs in case of project changes or unforeseen challenges.
Additionally, suppliers familiar with your company’s needs and preferences can offer tailored solutions, expedited services, and preferential pricing.
Overall, prioritizing relationships with reliable suppliers facilitates timely deliveries, helps minimize inventory storage and waste, and fosters collaboration and responsiveness, leading to more successful inventory management.
Regularly Perform Demand Forecasting
Regularly forecasting the demand for materials, equipment, and supplies needed for your future construction project can help streamline your inventory management processes.
Typically, such forecasts are based on specifications and tentative schedules of projects that are already in your pipeline, meaning you won the bidding process or directly contracted the job.
These future requirements are then compared to historical data on inventory consumption for past projects and cross-referenced with market trends for each material, component, or another item on your inventory list.
Of course, this implies you have past inventory data stored in your inventory management software’s database.
If that’s the case, you can use the software’s analytics and reporting features to obtain accurate and detailed data on your historical inventory use.
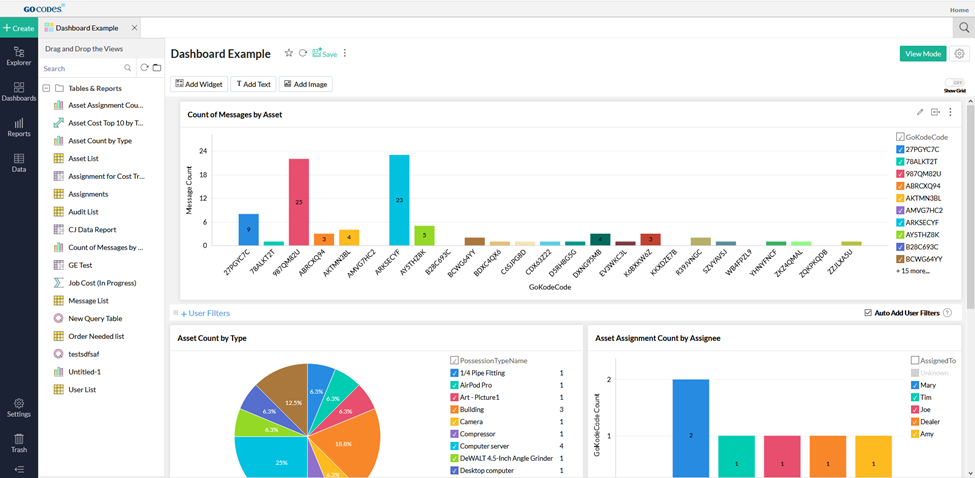
After you extract relevant inventory data using these features, you can use it to forecast future demand, i.e., anticipate the quantity and timing of inventory needed to support upcoming projects.
This proactive approach allows you to avoid stockouts and overstocking, optimize inventory levels, and reduce inventory carrying costs.
To effectively perform demand forecasting, various techniques can be utilized-
They are based on either:
- quantitative criteria (e.g., average number/quantity of inventory used on similarly sized projects) or
- qualitative criteria (e.g., expert judgment, market research).
By combining these techniques with real-time project data and insights from key stakeholders, you can develop more accurate demand forecasts and make informed decisions regarding inventory procurement, allocation, and utilization.
To recap, regularly performing demand forecasting empowers contractors to proactively manage their construction inventory, prevent shortages or overages, and optimize inventory levels.
Conclusion
In conclusion, it should be noted that four out of the six tips outlined in this article are closely related to implementing technology:
Namely, a mobile inventory management app with a built-in scanner coupled with inventory tags.
In addition to saving time, minimizing errors, and reducing inventory loss and theft, the right solution will allow you to quickly and easily conduct regular inventory audits, standardize related processes, and obtain more accurate demand predictions.
By combining these advantages with the other two tips—centralizing your on-site storage and maintaining relationships with reliable suppliers—you can significantly advance your construction inventory management practices.
Ultimately, this leads to more efficient operations, enhanced productivity, and greater profitability of your business.