Asset management helps construction companies maximize the use of their equipment and tools while mitigating the risk of unplanned downtime and financial losses.
Businesses that successfully manage their assets reap the benefits of streamlined workflows and extended asset lifespan, leading to increased cost savings and profitability.
Building an effective asset plan lies at the heart of these efforts.
This article is for all construction professionals eager to create new or improve their existing asset management plans.
If that checks all your boxes, here are the seven steps to building an effective plan for your assets.
In this article...
1. Defining Your Objectives
Formulating an effective asset plan requires clear objectives.
Companies are often tempted to cast their net wide and address as many different issues as they can, but this can create the opposite effect.
When it comes to asset management, it’s important to base your plan on reaching specific goals, such as:
- Cost reduction
- Enhanced efficiency
- Regulatory compliance
- Improved asset lifespan
The goal you choose will vary depending on your company’s current priorities and overall vision.
Translating these objectives into an actionable plan ensures alignment and brings you closer to where you want to be.
In fact, the International Organization for Standardization’s ISO 55000 document illustrates that this is one of the cornerstones of effective and standardized asset management practices.
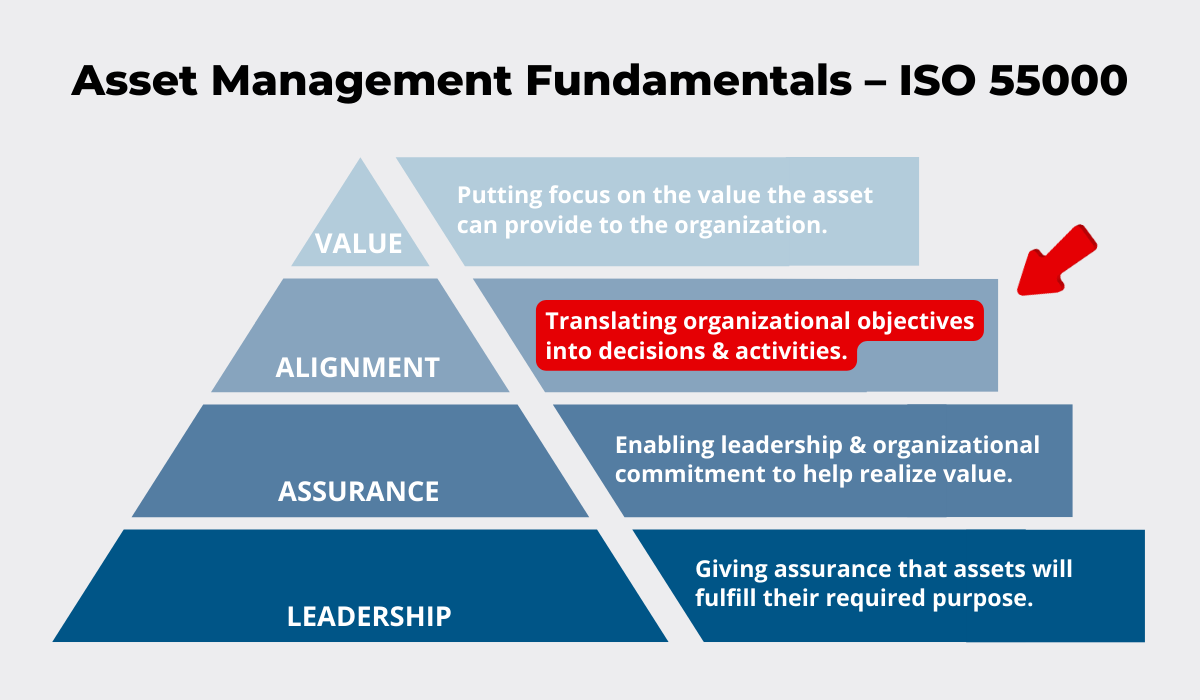
In other words, your construction asset plan needs to reflect the wider context and stay in line with the project goals, financial constraints, and operational priorities.
At the same time, it’s essential to define the mechanisms and metrics you can use to measure the plan’s effectiveness over time.
That way, you’ll have data-backed insights on what’s working and what you need to tweak.
There are many asset management KPIs, so make sure you use the most relevant ones.
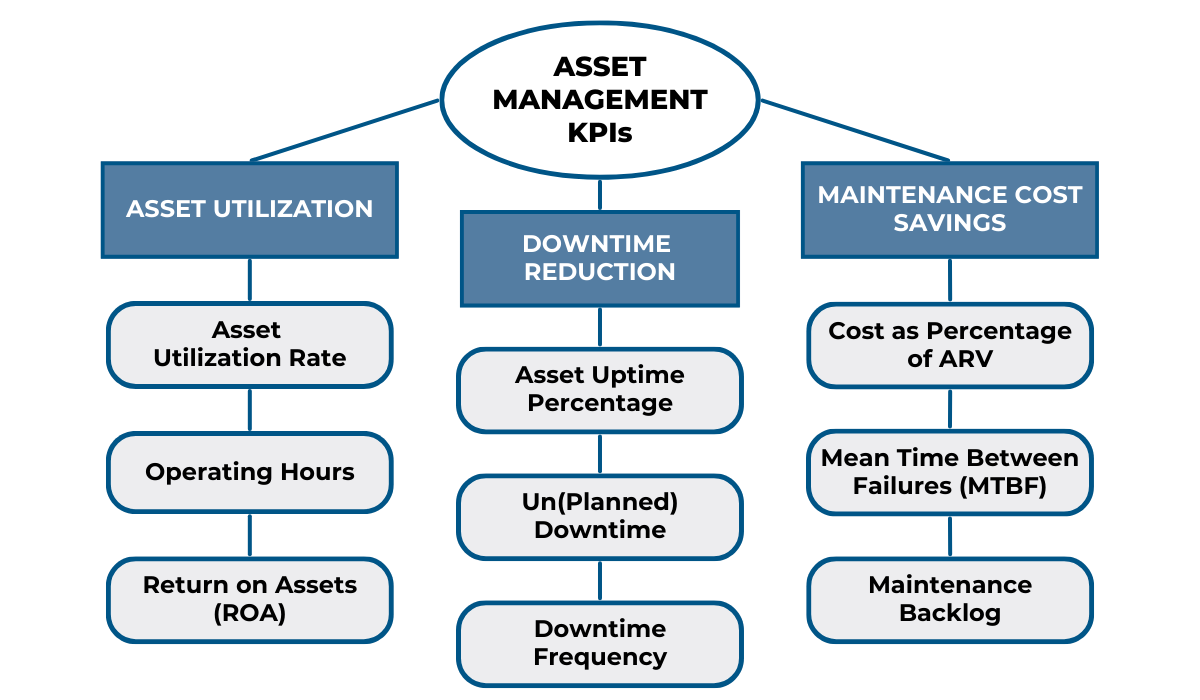
In the end, defining key goals helps you avoid false starts and paves the path to success.
2. Creating an Asset Inventory
Creating a detailed asset inventory serves as the foundation for all your future asset management efforts.
By keeping accurate records in one place, you’re enabling better tracking, budgeting, and utilization of all your assets.
You’re also avoiding unnecessary costs by keeping track of key information, such as serial numbers.
For example, if you need to service a forklift without a recorded serial number and own several of the same make, it’s easy to misidentify the equipment.
And if technicians base their repairs on incorrect data, this can lead to wasted time, ineffective fixes, and additional costly repairs.
Acquiring the necessary machinery, vehicles, and equipment is already an investment, so you should do everything to avoid additional spending.
One way to do that is by creating an asset inventory.
Construction company assets fall into these three major categories.
Consumables | Items used up throughout a construction project, including safety gear, adhesives and sealants, fasteners, etc. |
Building Materials | Raw materials needed for construction projects, such as lumber, concrete, and steel. |
Tools and Equipment | Different machinery, tools, and vehicles used for construction jobs. Knowing the availability, condition, and value of each piece of equipment enhances decision-making and enables cost savings. |
You can narrow down this division further, by organizing assets into sub-categories like machinery, vehicles, power, and hand tools, or devices.
Your inventory should include key information for each asset, such as serial numbers, purchase dates and cost, and locations, along with quantity on hand and supplier information for consumables.
Moreover, the information should be easily accessible, as shown below.
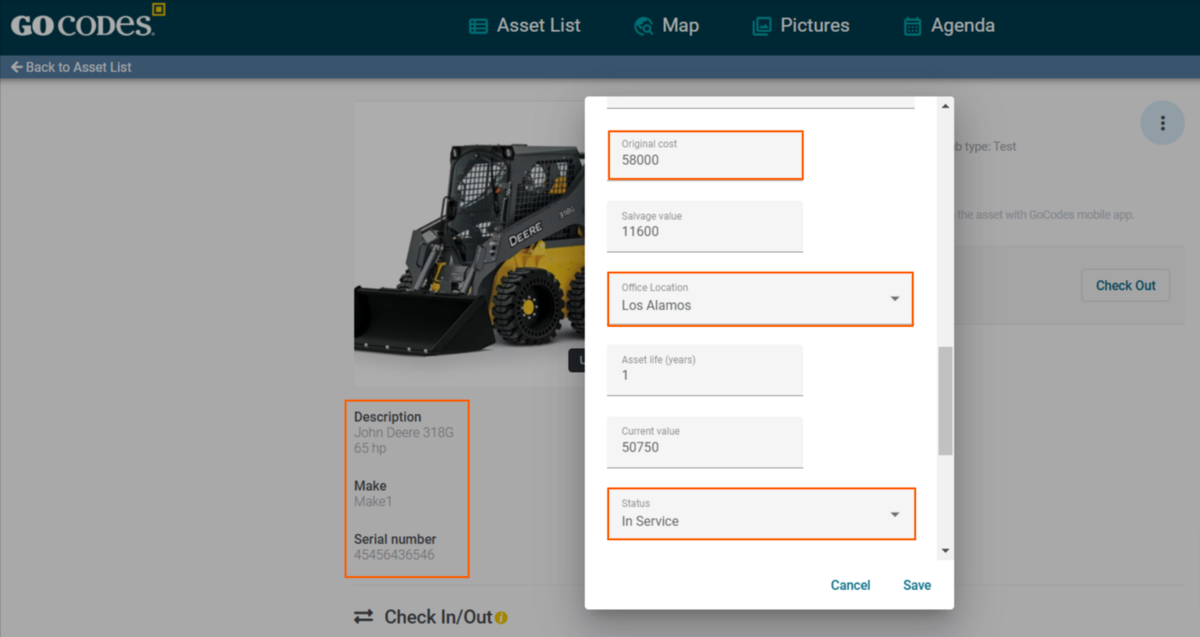
That way, you can already start mapping your inventory, ensuring:
- Increased operational efficiency
- Accurate financial reporting
- Improved risk mitigation
- A foundation for asset tracking
To sum up, knowing the availability, condition, and value of each piece of equipment enhances decision-making and leads to cost savings, which brings us to our next step.
3. Evaluating Asset Conditions
Next up, it’s important to evaluate the condition of each asset.
This will be the basis for identifying replacement needs and developing a maintenance strategy afterward, enabling better financial planning.
For starters, there are three main factors you need to consider:
- Asset age
- Maintenance history
- Operational efficiency
With this key information, you can develop a standardized grading system for evaluating asset conditions.
For example, you could use a five-tier system. Here’s what that could look like:
Grade | Condition Description | Action |
---|---|---|
A | Excellent: New or nearly new, with no visible wear. Fully operational. | Routine maintenance scheduling |
B | Good: Minor wear, but fully functional. Doesn’t require immediate repairs. | Schedule preventive maintenance & monitor the condition |
C | Fair: Moderate wear. Repairs should be scheduled to maintain functionality. | Schedule minor repairs and monitor more closely. |
D | Poor: Significant wear which requires frequent repairs. Nearing end-of-life. | Maintenance priority, start planning for replacement. |
E | Non-Operational: Broken or beyond repair. Considered unsafe to use. | Decommission and replace. |
The main point of such grading is to make it easier to track assets over time.
However, keep in mind that interpreting the results of the evaluation isn’t always straightforward.
Clinton Chitwood, owner of C&C Equipment with 20+ years of experience selling used heavy equipment, explains how the wear and tear rating of an excavator’s undercarriage is rarely what it seems.
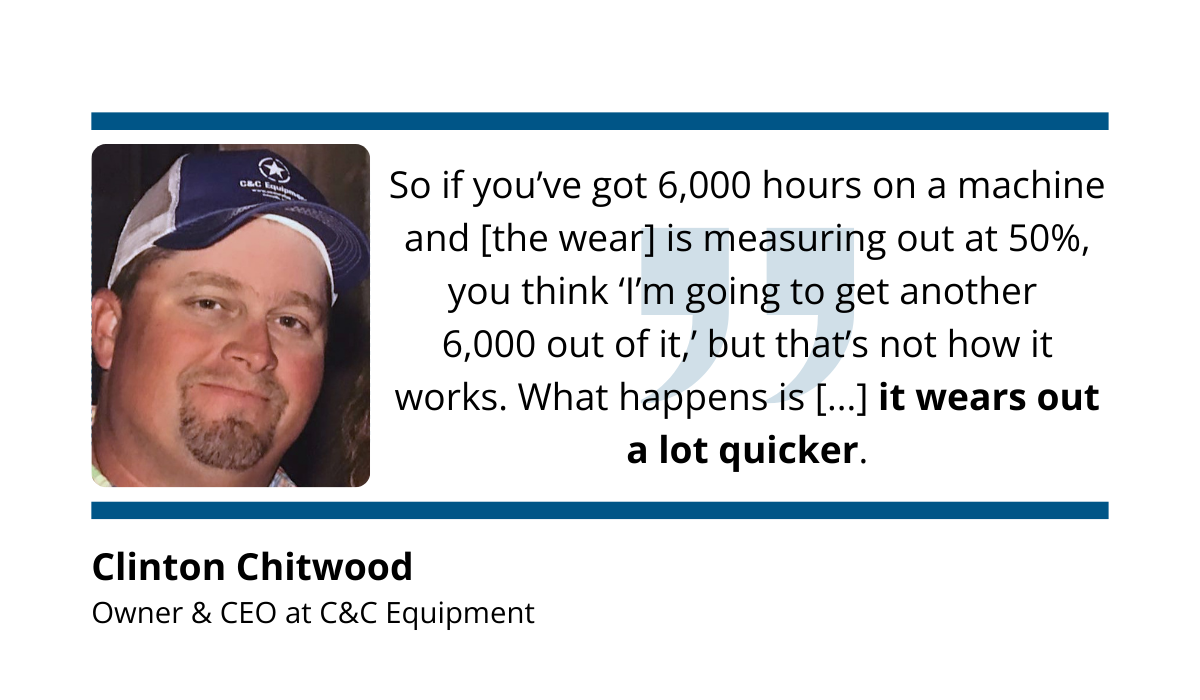
In this case, Chitwood is mainly advising potential buyers of used equipment.
However, the awareness that equipment wears down faster after a certain point in time is equally important to construction businesses evaluating their asset’s condition.
The bottom line is that without this step, you won’t be able to effectively deploy or maintain assets, let alone plan their long-term management.
4. Calculating Asset Life Cycle Costs
The previous step provided you with the outline for calculating asset costs.
To create an accurate asset plan, look beyond the initial purchase price and calculate the entire life-cycle cost of each asset.
The average asset life cycle includes various added costs, from operating expenses and (un)scheduled maintenance to eventual disposal costs.
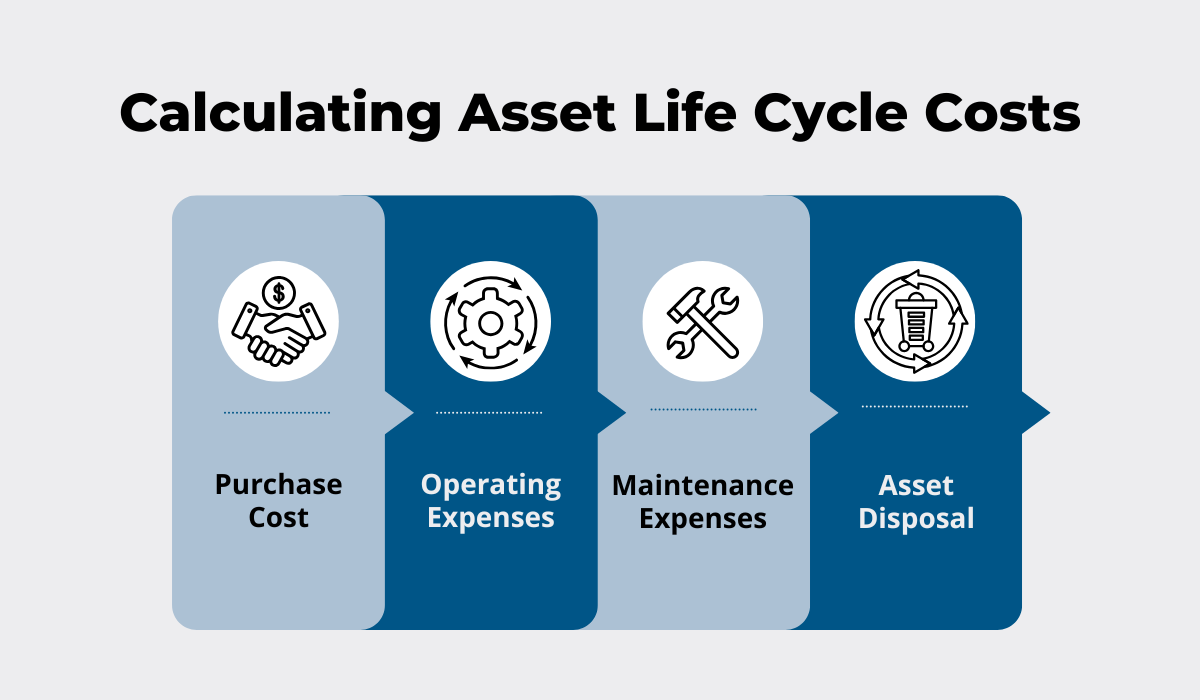
Maintenance expenses can be broken down into preventive maintenance costs, which can be estimated with reasonable accuracy, and service costs which usually fall into unplanned expenses.
Additionally, factors like new government regulations and technological advances also impact useful asset life and longevity, though they are typically harder to account for.
Nevertheless, estimating these costs as precisely as possible helps you understand how long an asset will remain functional and profitable, or otherwise beneficial to your company.
Lifecycle costing is also essential for financial and legal compliance.
Construction businesses need to calculate depreciation and salvage value of each asset to ensure they are meeting accounting standards, and maximizing their tax savings.
Implementing accounting tools like Sage or Quickbooks can help you there, offering more accurate project budgeting and effective long-term financial planning.
What’s more, most accounting solutions integrate with asset tracking software, ensuring you have all the data you need at your fingertips.
In the end, your asset management plan will only be as accurate as your life-cycle costs, so be sure to give this step enough time.
5. Implementing an Asset Tracking System
Tracking assets is an integral part of effective asset management.
That means moving away from Excel Spreadsheets toward a more proactive and efficient approach offered by specialized software.
Generally speaking, the data you get through asset tracking solutions enables more effective:
- location and usage tracking,
- maintenance, and
- reporting.
With centralized data on these key areas, construction companies gain numerous benefits, from enhanced asset visibility and safety to more employee accountability.
James Spivey, Enterprise Sales Principal at Nextworld (formerly Cloud Inventory), explains that simply having each asset marked with a unique identifier creates a world of difference.
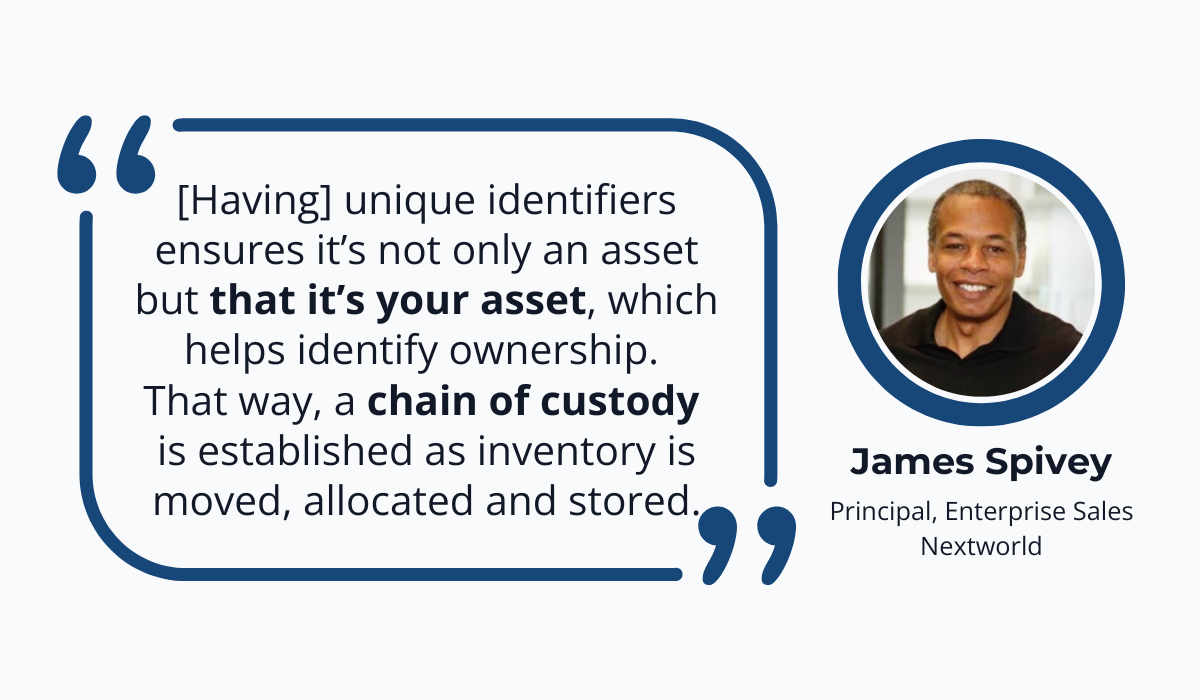
However, your choice of asset tracking systems and asset tagging methods will depend on individual needs.
Best asset management software offers different tracking devices, from QR codes and RFID tags to Bluetooth beacons and real-time GPS trackers.
Our GoCodes Asset Tracking is one such software.
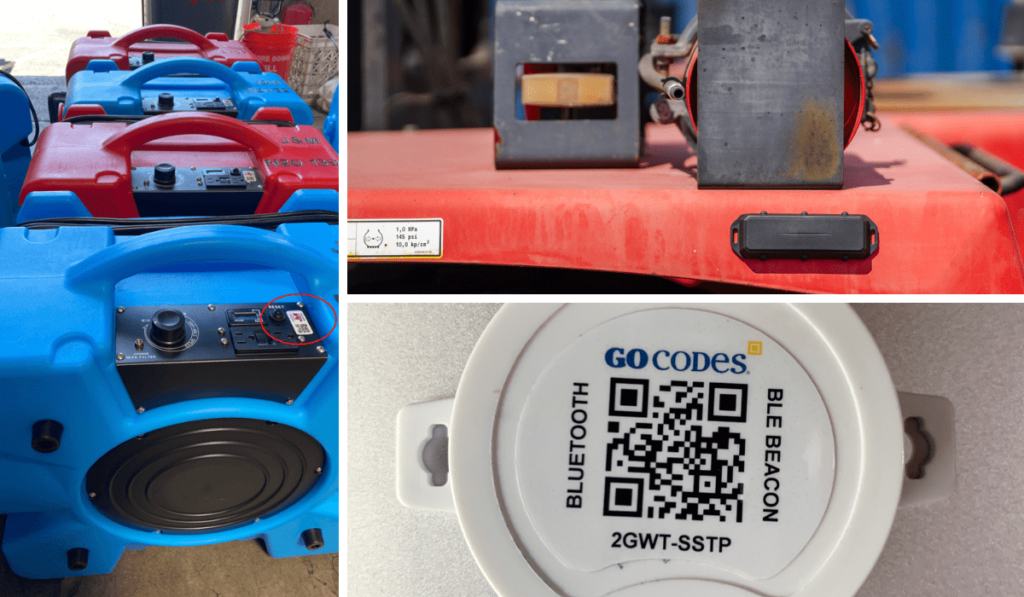
Customizable, GPS-enabled QR code labels are available in all sizes and different materials, making them ideal for smaller tools and equipment.
Besides seamless check-in and check-out experience for on-site workers, the tags allow both field and office employees to easily access the latest asset information from a single source of truth.
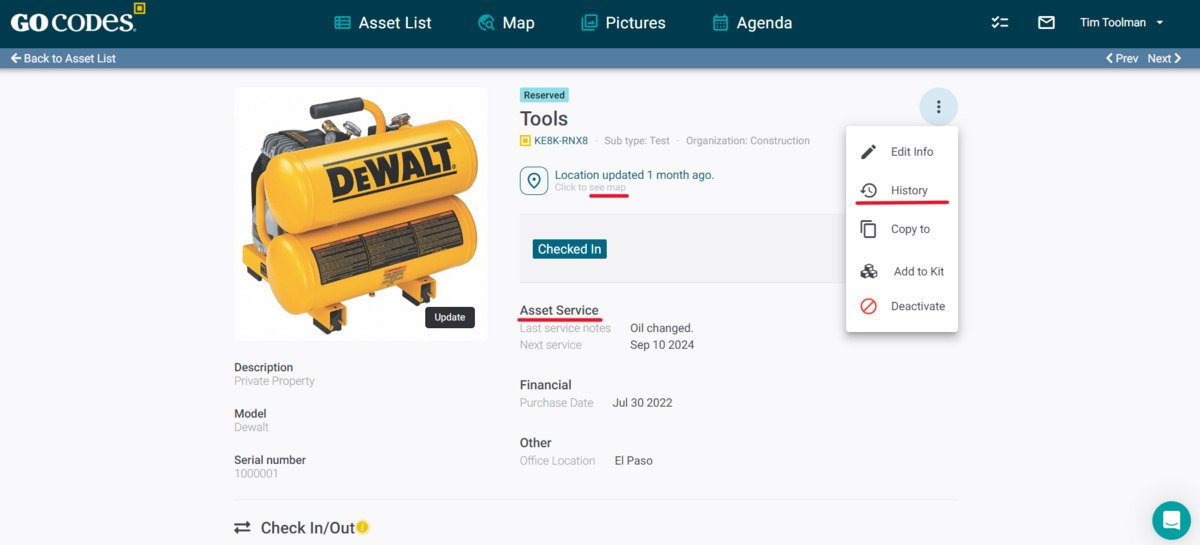
Comprehensive location history and usage records guide deployment decisions while the electronic trail also mitigates the risk of equipment loss and helps prevent theft.
GPS real-time trackers provide an additional layer of security for your most valuable assets, enabling minute-by-minute location updates and instant loss alerts in case of theft.
One thing is certain: Asset tracking is a core part of creating construction asset plans, and a vital investment for every construction business looking to bring their operations to the next level.
6. Developing a Maintenance Strategy
Maintenance is another indispensable part of asset planning.
And now, with everything else in place, you can move on to develop a comprehensive maintenance strategy for your assets.
By doing so, you will reduce the risk of unexpected breakdowns and associated expenses, which usually cost more than preventive maintenance.
In formulating your maintenance strategy and scheduling, there are two questions you need to ask yourself first:
- How cost-effective are our current maintenance processes?
- Do we have enough data to support maintenance-related decision-making?
The last question is crucial because effective scheduling combines manufacturers’ recommendations with data collected through asset-tracking software.
Official equipment manuals contain detailed information on the best practices for operating and maintaining equipment, listing the required time intervals for different maintenance processes.
Here’s an example from an operating manual for a CAT excavator.
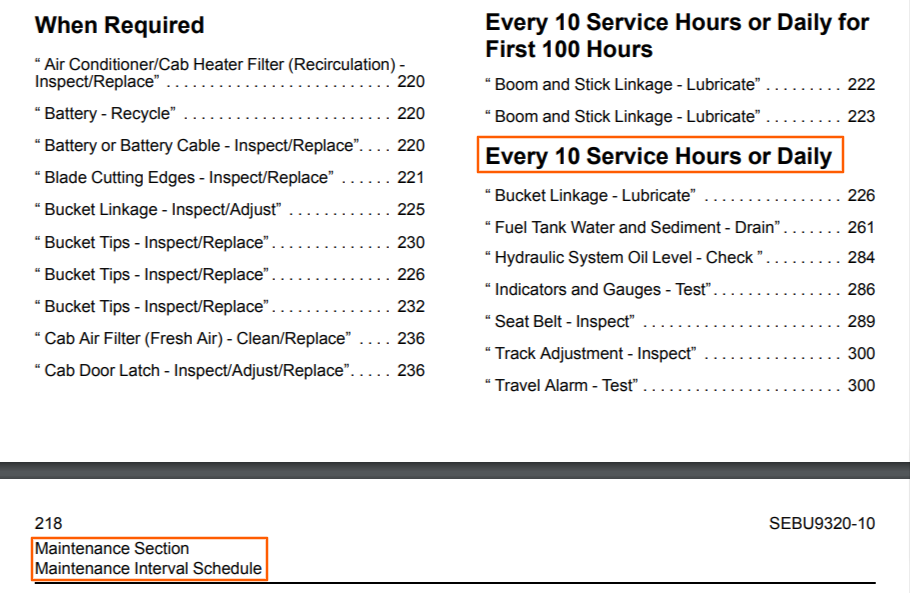
While operating manuals provide the initial framework, asset tracking systems fill it with real-world data.
It collects a bulk of data, including operating hours, locations, performance, and overall asset health and history.
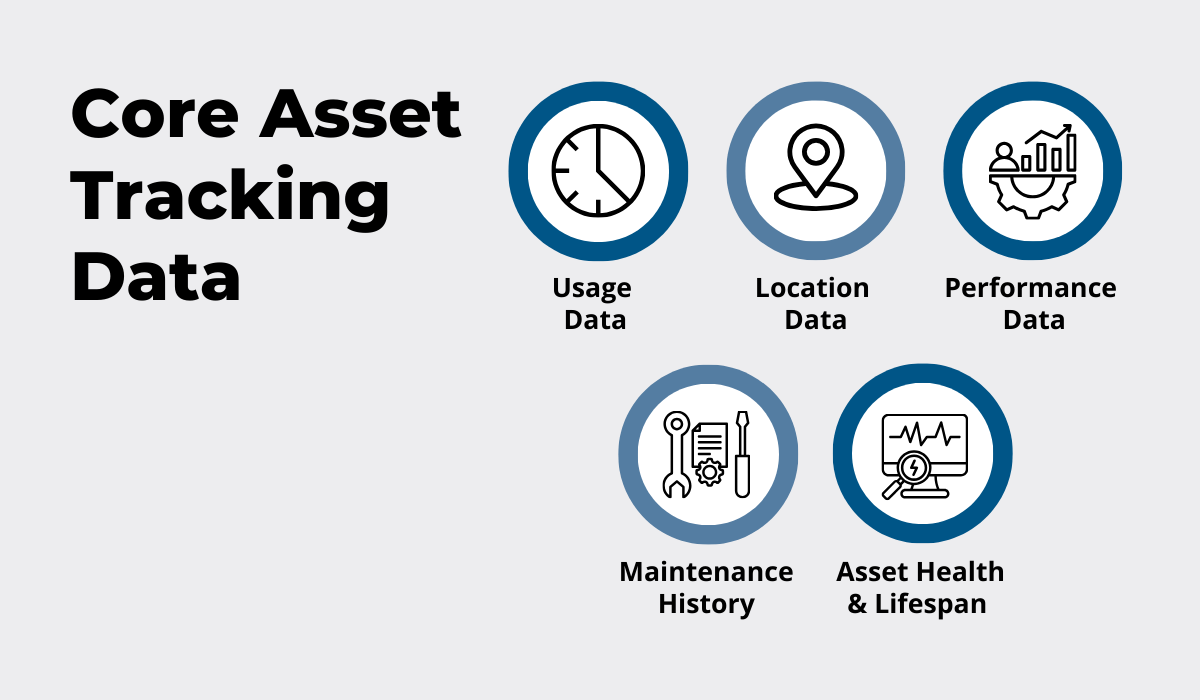
Even basic utilization insights coupled with maintenance records are invaluable for maintenance scheduling that will help prevent unexpected failures and costly repairs.
Remember: with the right maintenance strategy in place, you’re drawing a roadmap for safe and effective asset use.
7. Analyzing Asset Performance
Creating mechanisms for analyzing asset performance is the final ingredient of your construction asset plan.
While defining key objectives was our essential starting point, ongoing and thorough analysis provides the data needed to achieve them.
This way, construction businesses can make the best possible decisions on inventory management, including asset deployment, reallocation, and decommissioning.
We’ve already determined which types of data you can collect using asset tracking software, but performance analysis requires some additional considerations:
Formula | Which data inputs and calculations are needed? |
Owner | Who’s collecting and analyzing the data? |
Frequency | How often do we conduct monitoring and reporting activities? |
Format | What’s the most effective way to report and visualize the data? |
Audience | Who’s responsible for reviewing performance data? |
Defining the formulas, key roles, and reporting frequency is typically easier than deciding on the best way to sum up and present the data.
Making sense of large quantities of data can be challenging, but this is why the leading asset-tracking tools have robust reporting features.
Using our GoCodes Asset Tracking solution as an example, the reporting dashboard enables a quick, visual overview of key info on asset usage and performance.
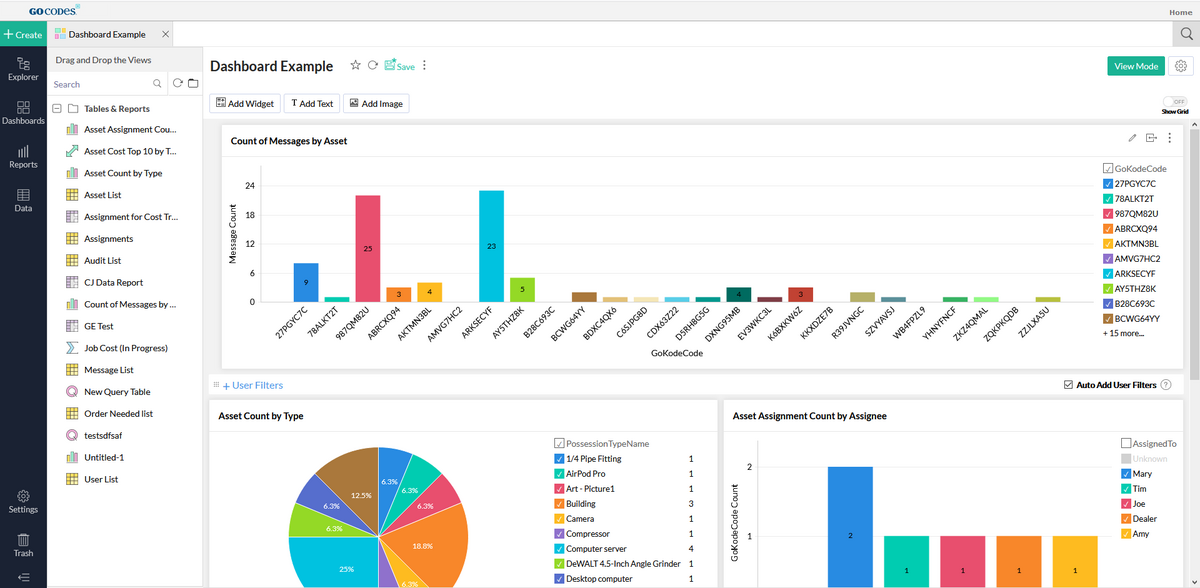
You get even more insights when using real-time trackers and the data they provide.
Access to telematics data is becoming increasingly relevant in the construction industry today, revealing more about utilization, machine health, and driver behavior.
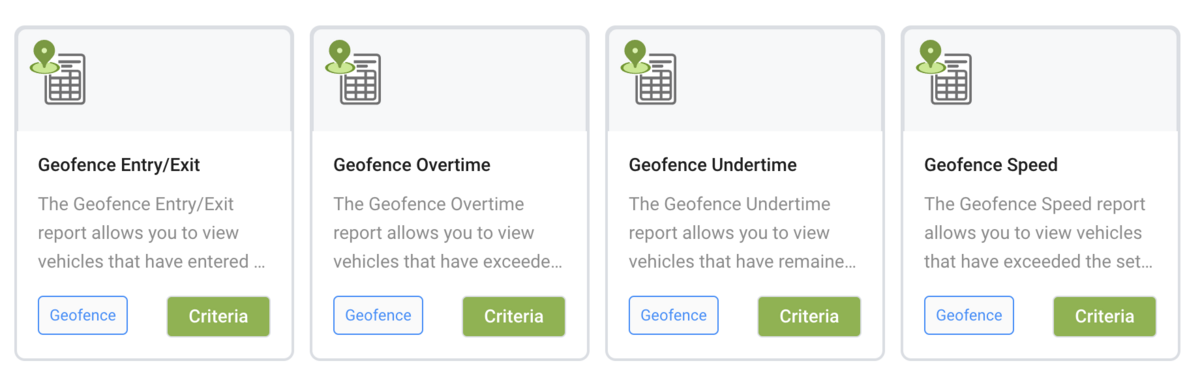
For example, you could detect events such as overspeeding.
Frequent overspeeding reduces equipment lifespan, leads to engine failure, and can suggest dangerous driver behavior, but also inefficiencies and inadequate jobsite conditions.
Access to all this data enables you to use your assets to their full potential without overworking them. However, data is just one part of the equation. Interpreting it is another.
Jason Threewitts, Site Innovation Manager at Carter Machinery agrees that context is everything when analyzing data.
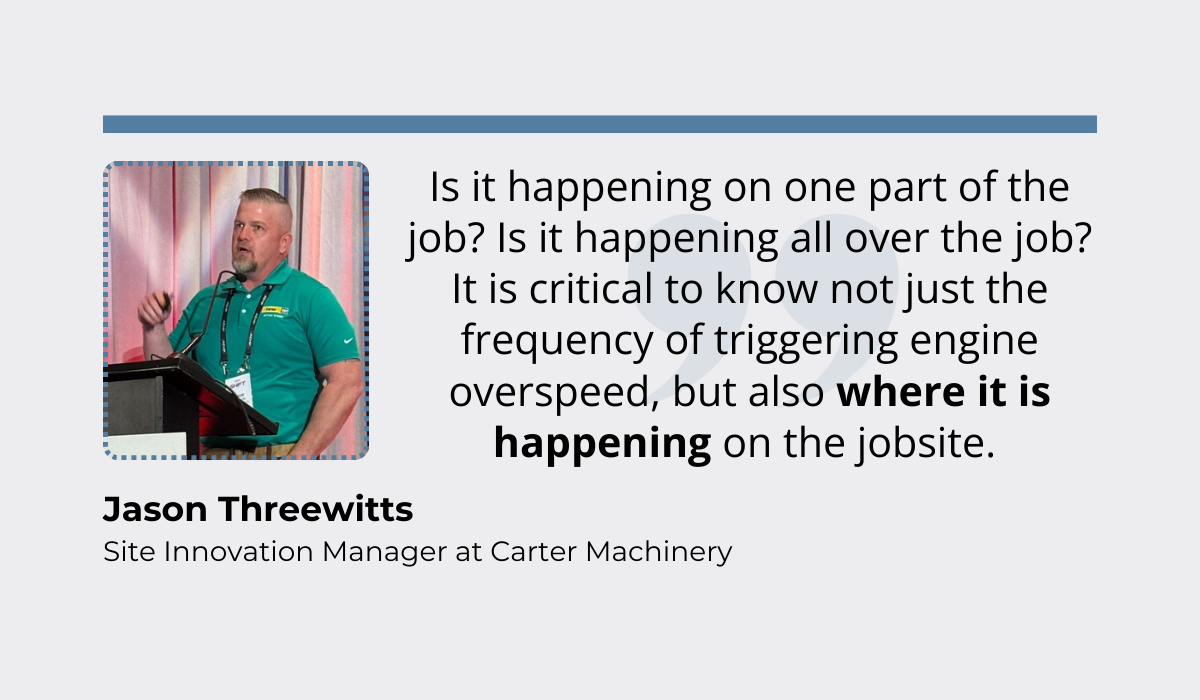
Keeping in mind the context and conducting a thorough analysis will ensure you have a comprehensive overview of asset performance.
And with that, you will have built an effective asset management plan that drives results.
Conclusion
Creating an effective construction plan delivers long-term value that goes beyond better asset or inventory management.
Gaining control over your assets’ value, usage, and longevity drives operational efficiency and profitability, leading to better project outcomes overall.
All in all, following these steps will help you craft a plan that ensures long-term success and builds your competitive advantage.
And if you get stuck along the way, feel free to revisit this article at any time!