It’s safe to say you understand the importance of having a solid maintenance plan for your construction equipment—after all, you’re here.
However, it’s also likely that you’re unsure how to go about making one.
Look no further. We will guide you through the process of creating a foolproof equipment maintenance plan.
But don’t expect a mere list of as many tips as we could think of. Instead, we’ll give you only the ones that work. So let’s get to work and help you create your maintenance plan.
In this article...
Consult Professionals Before Creating the Maintenance Plan
When developing a maintenance program, you should always gather the input of those who deal with construction equipment firsthand. Only then will your plan be complete and precise.
If you’re wondering which professionals to consult, start with the manufacturer.
It’s obvious why this should be the first step. The people who created the equipment know how to use, service, and inspect it the best. So, make sure you obtain that information from the instructions manufacturers provide.
The manufacturer’s instructions will provide information regarding various aspects of maintenance, including:
- cleaning equipment
- suggested spare parts
- spare part replacement schedule
- suggested maintenance schedule
So, why not use all that to your advantage?
Besides, the manufacturer’s instructions clearly state that you need to read them before using or servicing the equipment. Here’s an example:
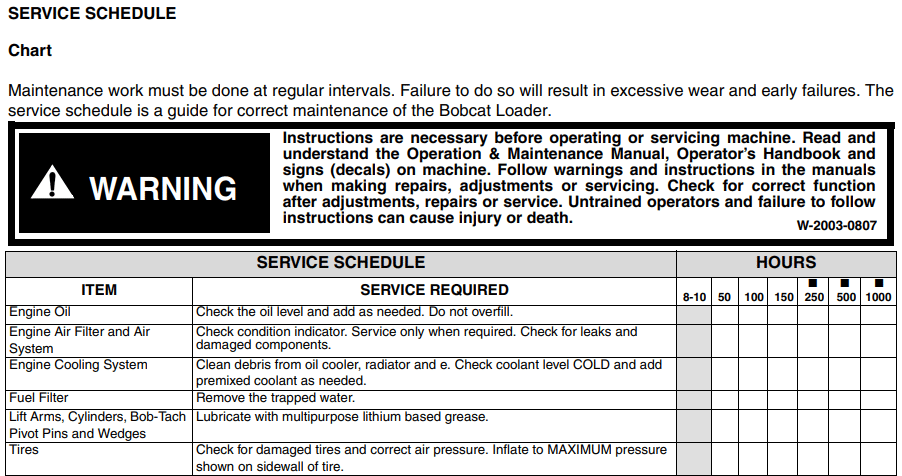
Overall, it makes little sense to go against the recommendations of someone who knows the machinery a lot better than you do.
You may be tempted to skip reading instruction manuals, eager to get right into using your new equipment. However, not abiding by the instructions can not only cause you to lose regulatory compliance but can also earn you hefty fines.
Rather learn from US Nonwovens Corporation’s example.
Occupational Safety and Health Administration (OSHA) cited them for thirteen violations, which included failing to install the equipment according to the manufacturer’s instructions.
The fine was a whopping $287,000.
Of course, not all thirteen offenses were directly related to the manufacturer’s manuals. Still, many safety and health hazards can be prevented by following the instructions, and OSHA knows that too.
Here’s an even more terrifying example. In 2015, a steel beam fall resulted in the death of a construction worker. And what was the cause? Nobody bled the air out of the clamp, which led to failure and the collapse of the steel beam.
OSHA’s problem with the unfortunate situation was that none of the workers there were familiar with this procedure, despite it being cited in the manuals.
In addition, the employees also adjusted a part of the equipment without doing a test afterward, going against the manufacturer’s instructions.
Clearly, there’s a lot at stake if you fail to consult the manufacturer’s instructions or if you fail to include them in your maintenance plan.
Besides diligently following the manufacturer’s recommendations regarding usage and maintenance, your maintenance team and equipment operators can help you come up with a perfect maintenance plan.
After all, they’re the ones who use and fix the machinery daily. Operators know to recognize a possible issue and how to address it before it leads to further damage.
Feedback from employees in the field can make a big difference. Sadly, not many employers unlock the potential that lies in getting feedback from their employees, as the following graphic shows.
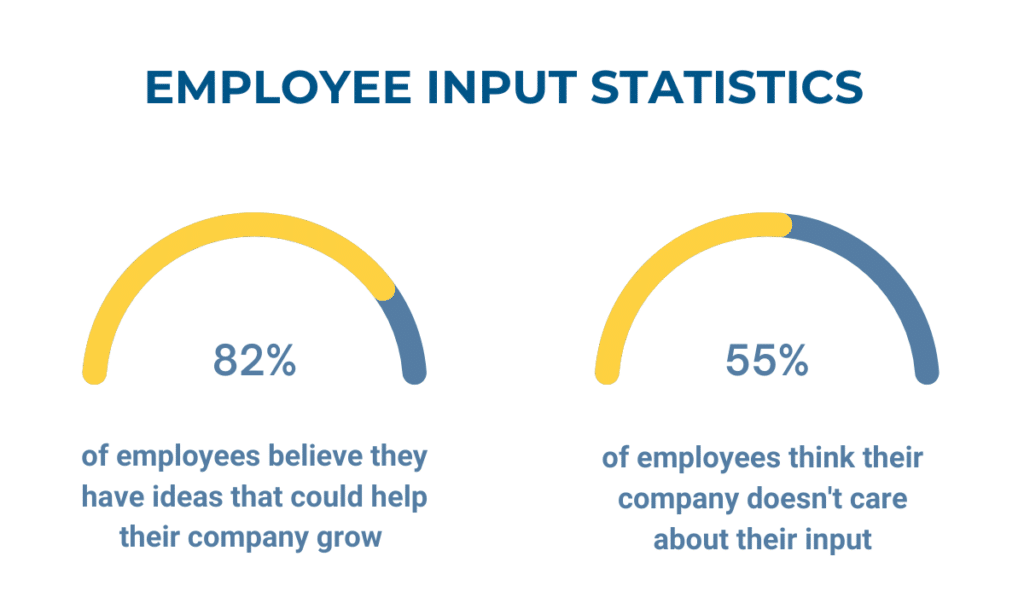
Research shows that the large majority of workers believe their ideas could help the company improve. But unfortunately, more than half of employees also feel that the company doesn’t care about their feedback.
When you take into account these numbers, along with the consequences of poor equipment maintenance plans we mentioned earlier, then it’s safe to say that taking the time to listen to your equipment specialists’ input would have multiple benefits.
First, you’d have a maintenance plan based on firsthand experience gained in the field. Your team has gathered that through years of working with the machinery, so why not use it?
Second, your employee engagement would improve. Asking employees for feedback makes them feel like their contribution is valued, directly motivating them to be more invested in the company’s success.
The following image shows additional benefits of including your employees in decision-making.
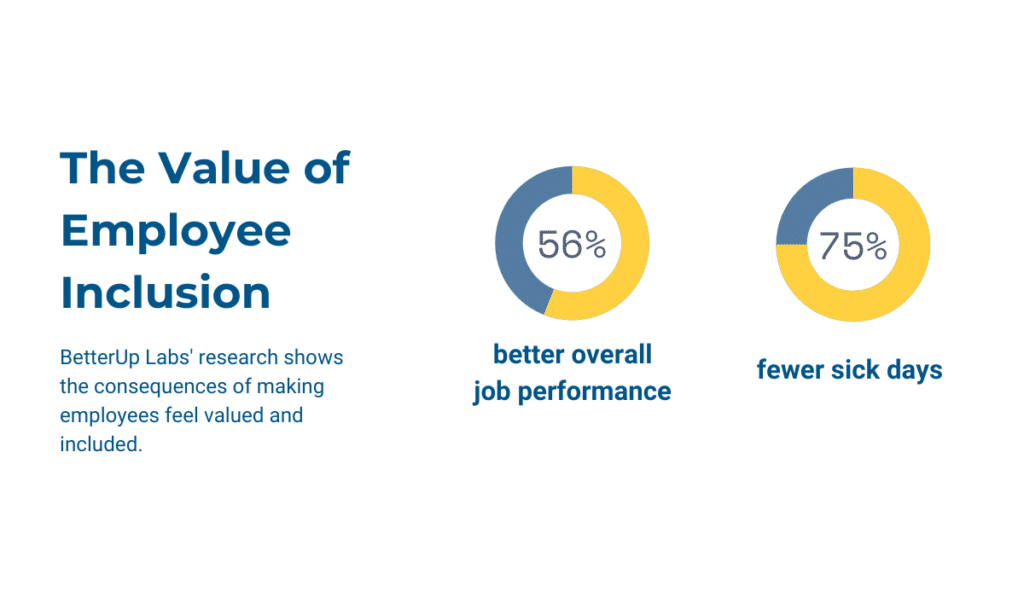
As you can see, individuals that feel appreciated perform at a higher level, achieve better results, and take fewer sick days.
So, when you include your employees in decision-making processes, not only do you ensure that your team is performing at the highest level, but their improved efforts also save you money.
Cover the Maintenance Process from Start to Finish
It’s important to map out the entire process in detail before you start implementing it as it ensures consistency.
The task is a bit tedious at first because it includes activities like compiling an inventory, listing equipment specifications, and setting up a servicing schedule.
Luckily, your team’s input and the manufacturer’s instructions will come in handy at this stage.
If you’re not sure whether it’s entirely necessary to write down your maintenance plan in such detail, let us present you with some data.
For instance, planning maintenance can double your wrench time, which is the time your maintenance team spends working on repairing the equipment (tools in hand), instead of waiting for replacement parts, etc.
The typical wrench time ranges from 25% to 35%. When a company introduces scheduled maintenance, it can increase to over 50%.
Basically, if you plan your maintenance well, you can get twice the work from your employees.
Here’s what Tim Newman, a maintenance manager at Simmons Feed Ingredients, had to say about introducing planned servicing:
We went from a six-month backlog of work to running out of jobs for the craftsmen to do, and from 10 percent planned work to 88 percent planned work. Additionally, the techs’ morale has never been higher, and they are striving to meet all the schedules. It helps for them to know what they are doing each day without any surprises.
Clearly, maintenance planning helped Tim’s company. Providing his team with a schedule that they adhere to has increased their wrench time and prevented the work from piling up. Why not do the same for your company?
Now that we’ve convinced you to detail each maintenance step and develop a schedule, we’ll suggest things you can add to the plan.
Here’s what we recommend:
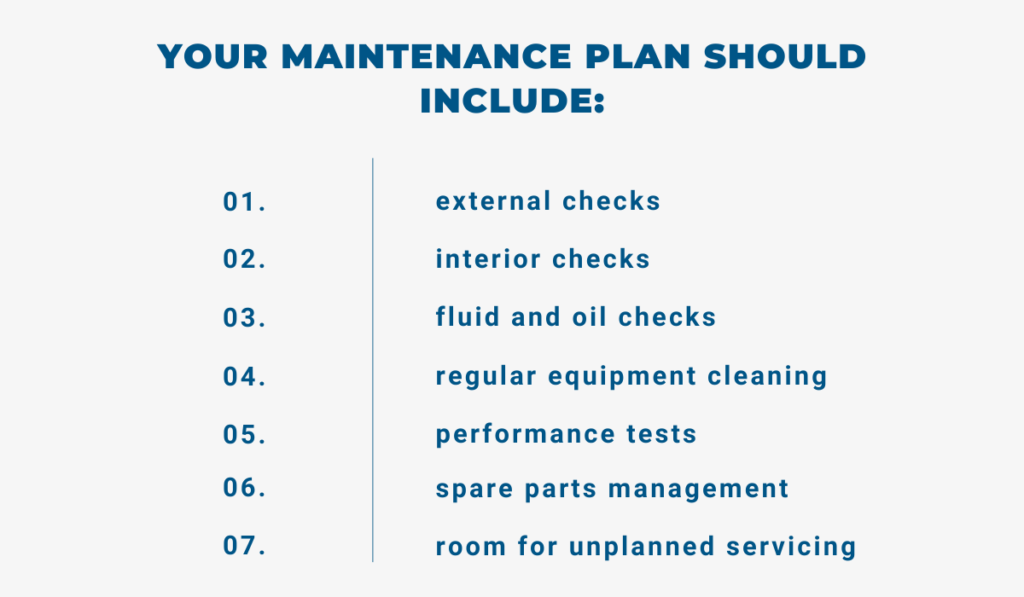
To sum up the list in the image, when a piece of equipment is due for maintenance, your team should know exactly what to check and how.
On top of that, they should know what amount of wear-and-tear is considered acceptable and what damage is critical.
If you add the suggested details to your servicing plan, you’re making sure that your staff never misses a step.
Such oversights can cost you a lot in the construction industry. Even forgetting something as simple as oil analysis can lead to expensive engine failure. So why risk it?
Finally, you might be wondering how to decide how often you need to perform specific tasks for equipment groups.
Look are some suggestions from maintenance experts:
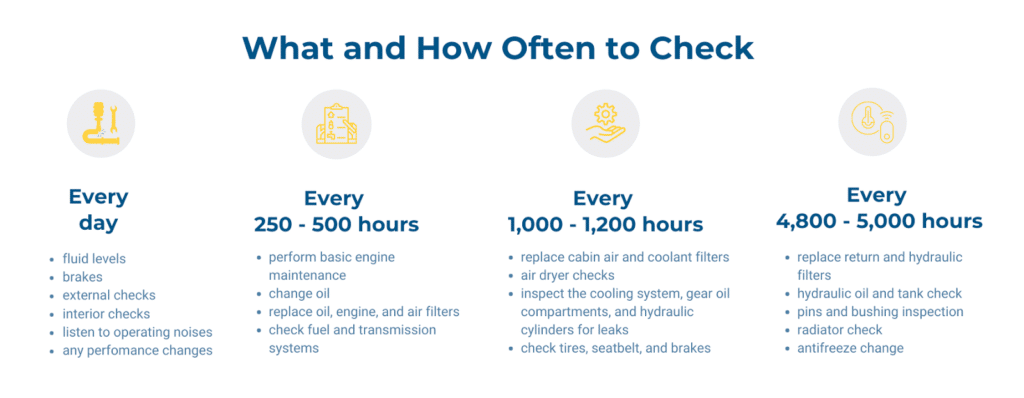
So, if you want to stay on top of all these checks, you have to find a way to seamlessly schedule maintenance tasks.
The best way to do this is to digitize this part of your plan, by opting for software like GoCodes.
It gives you the option of service scheduling for every single piece of equipment you add to the database.
On top of that, the maintenance team can leave comments regarding the condition of each item for you and other staff members to see.
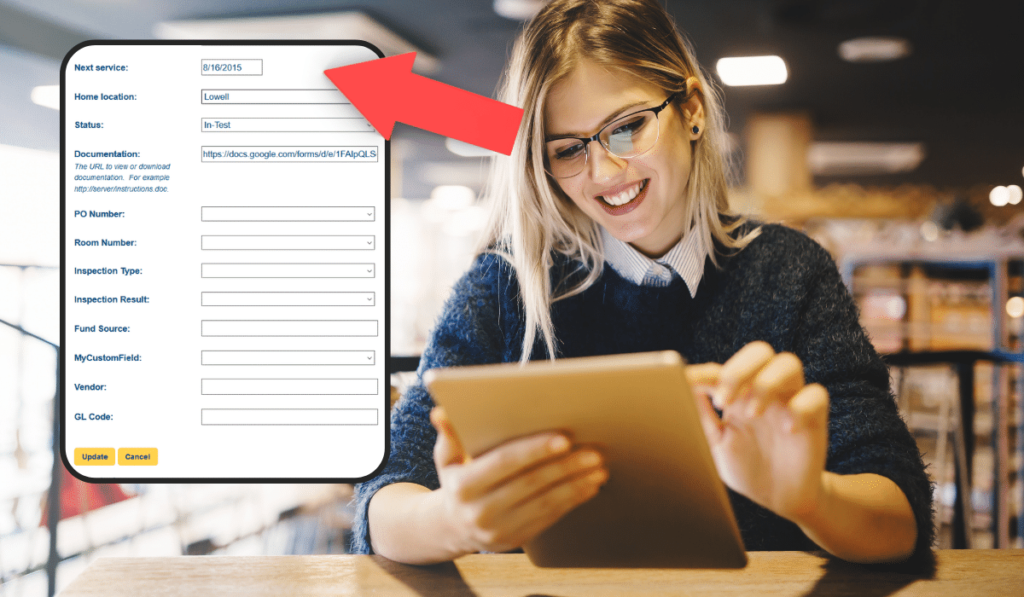
What you should take from this section is that the perfect maintenance plan is the one that covers all details, from start to finish.
Ensure Maintenance Plan Implementation
Once your plan is good to go, how will you implement it?
The four pillars of putting a servicing plan into action are:
- assigning responsibilities for the plan and individual tasks
- training the staff
- monitoring the maintenance process
- promoting communication regarding equipment servicing
Let’s dissect each one so you can see the bigger picture.
When you finally have your plan written down, you should first decide who is responsible for implementing it. Will you be in charge of it yourself, or will you assign this duty to a seasoned maintenance team member?
While someone has to be in charge of the plan as a whole, the team should have the responsibility to follow through with each stage. That means each team member should know what their individual tasks include.
But, before your employees can tackle those tasks, they need to get proper training.
If you remember the tragic case we’ve mentioned earlier, where a falling steel beam caused the death of an employee, you’ll remember that the staff hadn’t read the manuals.
However, OSHA didn’t think it was the team’s fault. Instead, they held the company accountable. After all, it’s up to the employer to train the staff and teach them how to operate and repair equipment.
So, besides showing your team the maintenance plan and teaching them how to use and repair the machinery, you should also instruct them to use the manuals that came with it.
Now that you know what to teach your team, here’s what you should avoid when doing so.
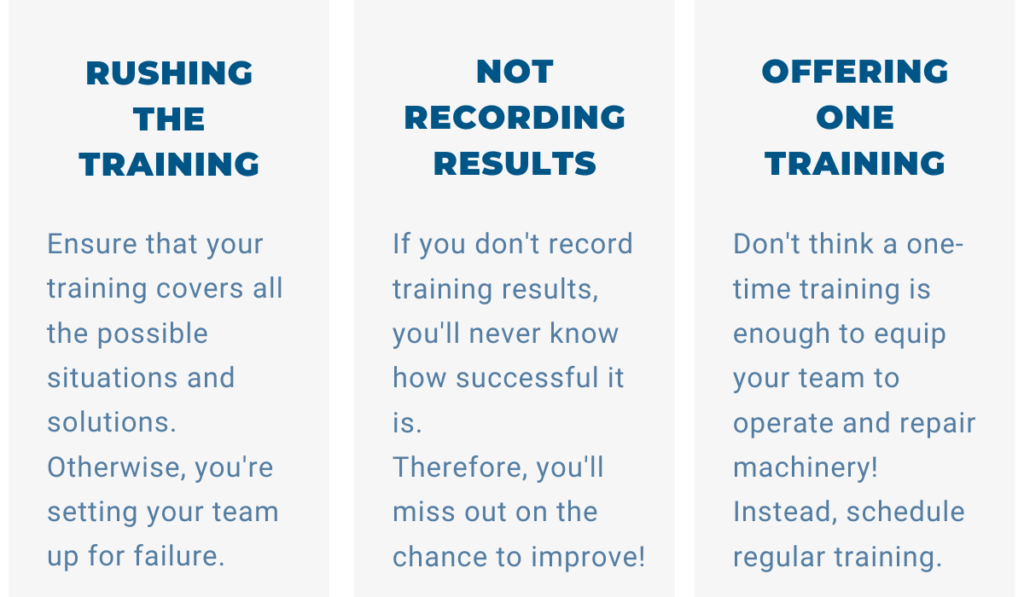
If you follow this advice, you’ll have a well-trained maintenance team!
Training will also help you with the next step, which is maintenance monitoring. Obviously, you have to track your servicing to understand whether your current process works well. If not, it’s time to make changes.
But, even if your servicing plan functions well, for now, don’t get too comfortable.
Instead, continuously monitor the entire process to find weak spots or flaws. That way, you’ll be able to optimize it and achieve even better results. After all, there’s always room for improvement!
So, how can you monitor your maintenance? Here’s what you can do:
- tag all your machinery to be able to track the usage and maintenance dates of each piece
- offer an easy way to report equipment issues to the service staff
Luckily, you can use one software for both.
Solutions like GoCodes let you have an equipment database, where you can enter items in a couple of clicks, and find or add information on the machinery’s condition.
The last step is just as important as the prior three, mainly because it deals with communication.
If you’re not sure why promoting communication about equipment maintenance is vital, keep in mind that inadequate communication can cost smaller companies (with up to 100 people) up to $420,000 a year.
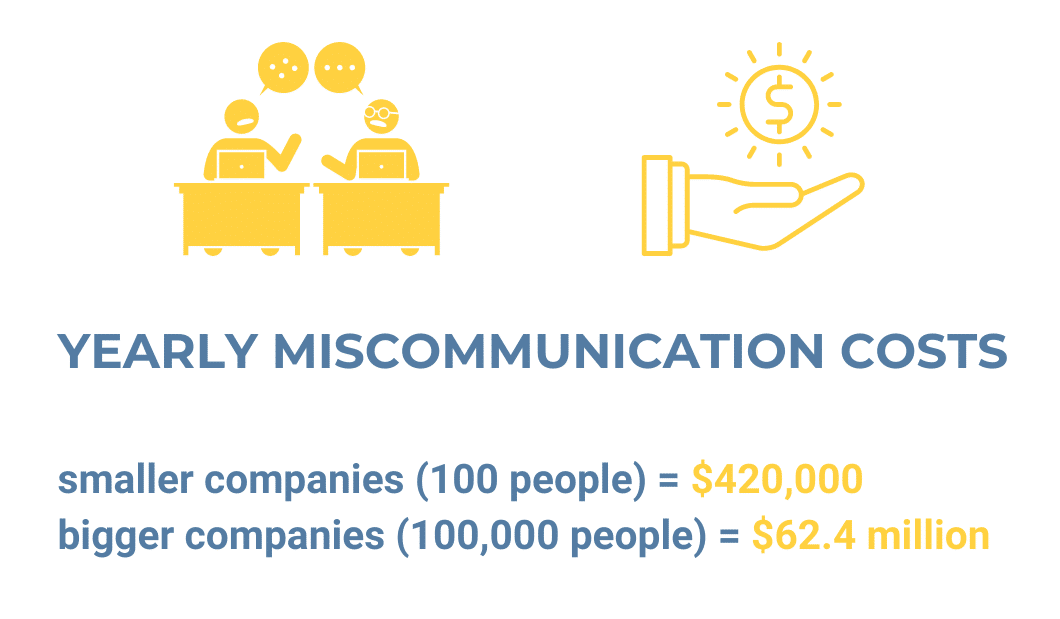
In short, miscommunication is something you cannot afford, not unless you have money to waste. Therefore, you should invest in creating and promoting a way for your team in the field to communicate with your maintenance staff.
The perfect solution might be the specialized software we’ve mentioned before.
On top of letting you track each maintenance session and equipment status, it allows users to comment on the equipment’s page. So if someone notices something strange or spots any damage on a piece of equipment, they can leave a comment for the service team.
In sum, when trying to implement your maintenance plan, don’t forget its four pillars.
Document Everything
Now for the most important part: documenting every aspect of the maintenance process. While this might seem time-consuming, trust us, it’s worth it.
Here are the main points you should document, other than the maintenance plan itself:
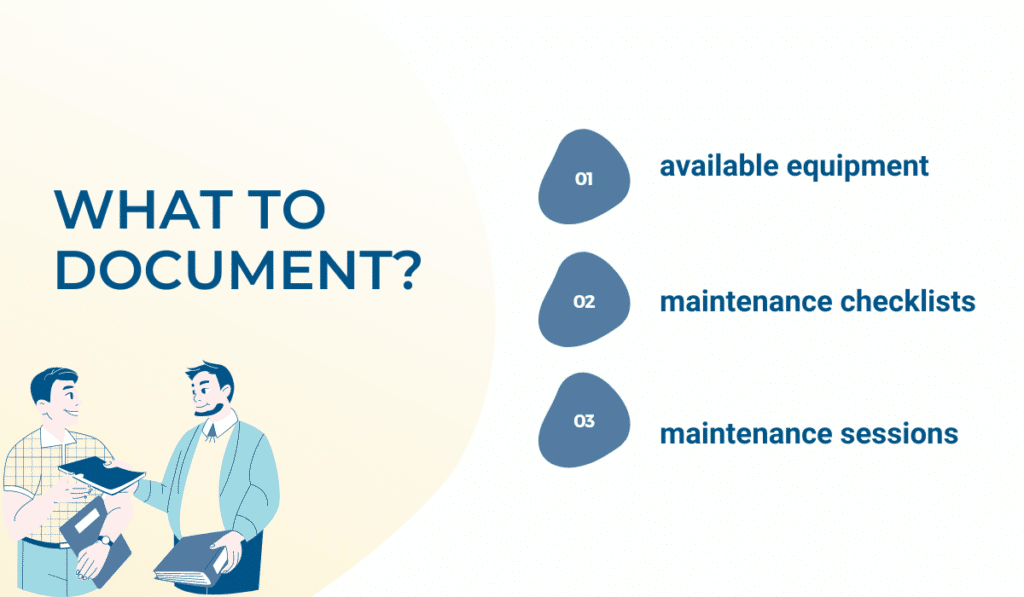
Let’s see what these three points include!
You should start documenting the maintenance by doing an inventory of all your equipment. Only with an overview of what you own, you can plan for its servicing effectively.
Another vital aspect of creating an inventory is that you’ll get to determine whether you’re wasting money on parts. Keep in mind that you have to find the fine balance between having too little and too much equipment.
If you don’t have enough equipment or lack replacement parts, you’ll cause downtime whenever you schedule maintenance. This issue happens more often than you think: as much as 50% of unplanned downtime is caused by the lack of necessary parts.
On the other hand, you don’t want to store too many pieces of equipment, either. Take into account that the carrying costs (the expense of owning machinery) equals to 12% to 20% of the purchase cost.
Therefore, you should strive to own just enough equipment to avoid downtime whenever there’s a servicing activity.
Another thing you should have on file is a maintenance checklist for each piece of equipment.
You may be thinking: why do I need checklists when I have the whole plan written down?
It’s because the more detailed your checklists are, the easier it will be to follow the maintenance plan.
Such lists usually cover every step of the maintenance process, and whoever is performing the servicing has to go through each one. The chances of skipping a segment are meager when the checklist is right in front of you.
So, create a checklist that covers everything necessary for proper machinery functioning.
And finally, the most critical step to document is the maintenance sessions.
The data gathered after servicing helps you understand just how effective your overall maintenance plan is. When you notice that certain aspects are lacking, you can easily change that part of your routine and then monitor how the changes have affected your results.
Therefore, tracking your maintenance is necessary for you to determine whether or not you’re reaching your goals.
When speaking of servicing, maintenance goals are also these:
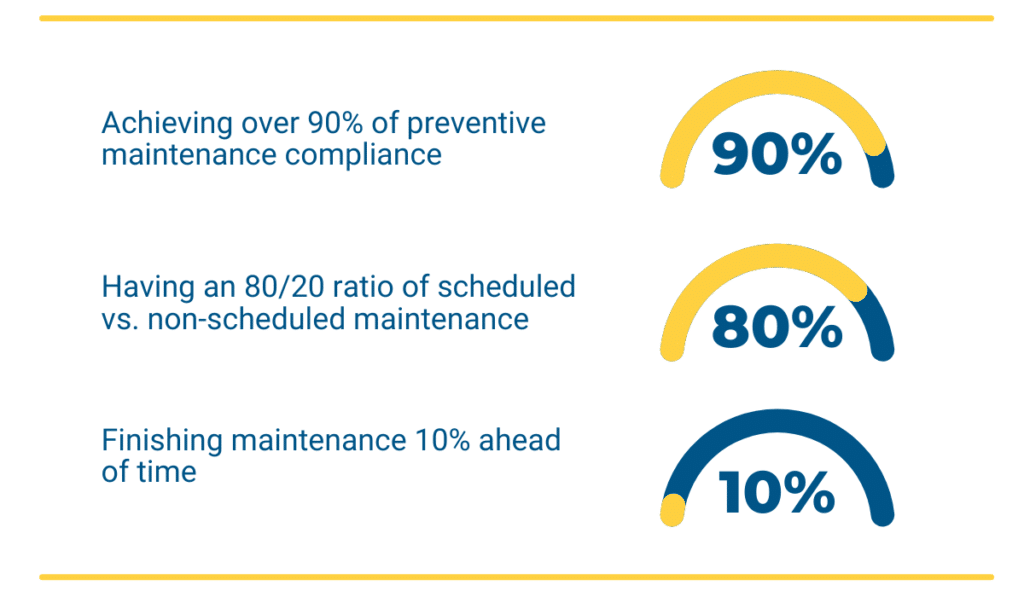
What does this mean?
The first goal, preventive maintenance compliance, lets you know how many scheduled tasks you’ve completed in a given period. The minimum goal is 90% since equipment is unpredictable, but the higher your score, the better!
The planned versus unplanned service schedule ratio should be 80/20. Your aim, of course, is for as many maintenance hours you put in to be planned. If you end up with many unexpected maintenance sessions, it means that something isn’t right with your plan.
The last aim is to finish maintenance 10% ahead of the deadline. For example, if you have 50 days to complete a maintenance work order, it should be done by day 45 at the latest. Sticking to the 10% margin makes sure you always have enough time for unplanned servicing events.
So, if you keep records on your equipment, use checklists, and track your maintenance, you’ll perfect this step in no time.
Conclusion
To have a successful maintenance plan, make sure it correlates to the needs of your team, then invest time and resources in continuously developing, and monitoring your plan.
That way, you’ll ensure that it’s constantly optimized.
When you follow the steps we’ve mentioned, your plan will be based on practical insights and experience obtained in the field, making it easy to follow.
Isn’t that the whole point of this process? Now go and make it happen.