For construction companies, losing tools can feel like a perpetual itch they can’t quite scratch.
Although the number of lost tools is not a metric that can make or break a business, for many it is still a constant annoyance to contend with.
And not an insignificant one at that. Every minute spent searching for tools means that much less work is being done, which affects productivity and workflow.
The cost of the replacements is not insignificant, either.
Moreover, it is a problem that can’t be solved on a case-to-case basis.
No matter how many tools you find or clumsy workers you replace, it will keep happening—unless you approach it on a systemic level.
That is why, in this article, we provide site operators with several actionable measures to reduce the number of missing tools and improve workflows on their construction sites.
Let’s dig right in.
In this article...
Label or Tag All Construction Tools
So, how do you start securing the tools on your site?
This Reddit user stumbled upon a pretty good idea:
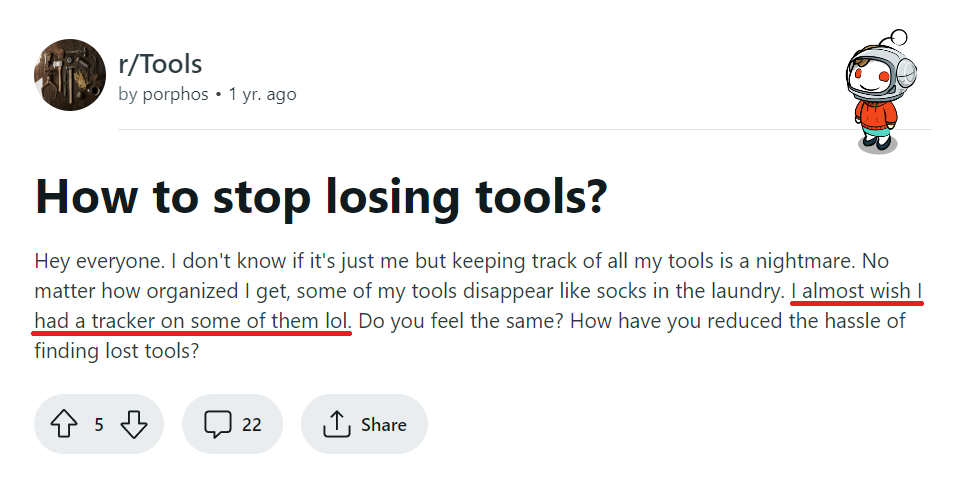
While tracking the tools inside of your own home might be a step too far, doing so is only logical for construction sites.
After all, we’re talking about hundreds of tools used by dozens of workers across different sections of the site.
With no tracking or labeling system, you would have a hard time noticing when a tool goes missing, let alone finding it.
Simply color-coding the equipment for different teams or areas would already be a step in the right direction.
In that case, if a blue-coded drill were missing, at least you would know it was used by the “blue team” or in the “blue section”.
However, for a professional environment, it’s best to go with a more sophisticated labeling solution. And the one we’re proposing is also quite affordable.
Barcode labels are a tried-and-true way of keeping track of large quantities of items.
They have been widely utilized in retail since the ’70s, when the Universal Product Code (UPC) first went into use.
Today, barcodes are slowly being replaced by their more advanced counterparts—QR codes.
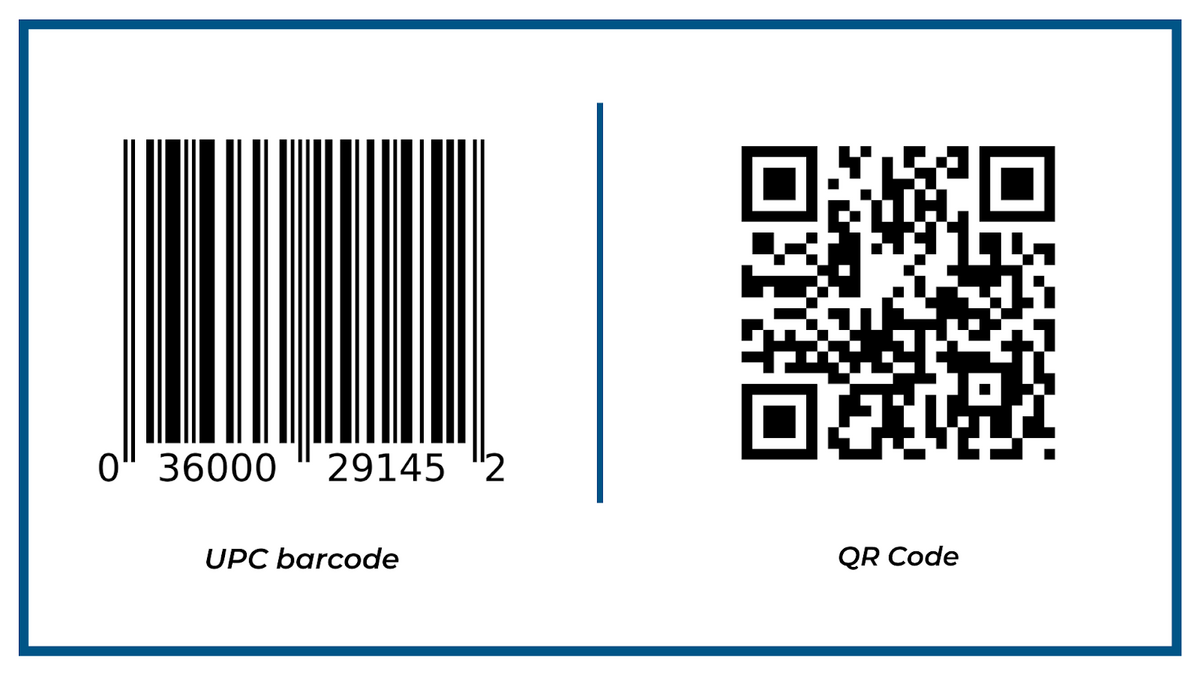
QR code labels can hold a lot more information than barcodes. Plus, they are small, durable, and inexpensive to make, making them perfect for tagging tools of any size.
Using QR codes for tracking is straightforward.
For a start, customize the data fields you want your asset labels to contain—like the manufacturing date, your company’s details, last user and time used, and the item’s identifying number.
QR codes even have enough space for images if you need them for reference.
Next, print the tags or order a more durable polyester/polycarbonate version. Then, all there is left to do is affix the labels to the tools.
Simply scanning the labels with a smartphone will reveal all the pertinent details about the tool in question.
If you want to track your tools as well, you can use spreadsheets to gather and analyze the scanned data.
But the best bet is going for a complete tracking system, which automatically updates with each scan, provides a map of your assets and tracks use times and users.
All in all, labeling your tools will help you identify found items and recover missing ones more easily, thus reducing the overall number of tools lost on the job site.
Create a Site-Specific Tool Inventory
A tagging system is extremely helpful in pinpointing the location of lost assets. But in order to start the search, you first have to notice something is missing.
This is where inventory comes in handy.
A general inventory of all the assets your construction company owns will not do you much good.
That way, you would only notice lost items after a job has been completed, and equipment returned to the storage.
Even then, it would probably take a comprehensive internal audit to figure out how much is actually missing.
What you need is a site-specific inventory.
Every time your team starts work on a new site, there needs to be an exhaustive inventory of tools taken out for that job.
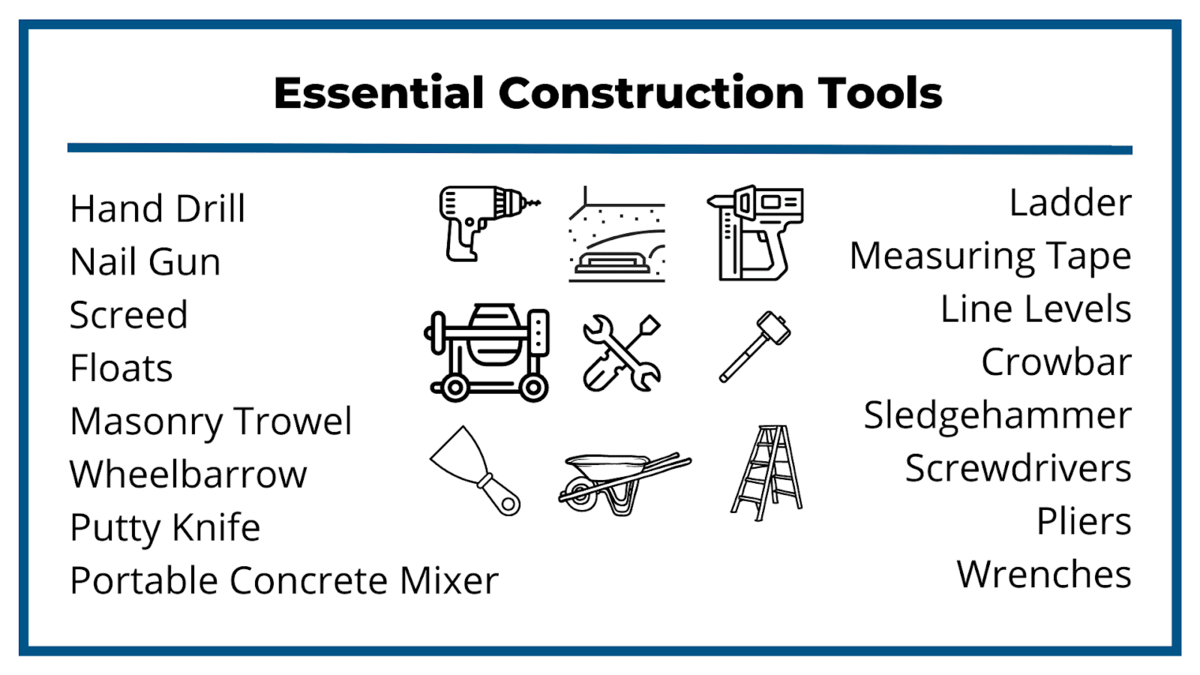
This should include everything but the larger vehicles and machinery, which form a separate category.
Diligently and regularly checking the tool inventory against the list will reveal which tools are missing in an accurate and timely fashion.
That way, all instances of lost tools can be immediately investigated and quickly resolved.
Of course, for this system to work, rigorous supervision is mandatory.
At the beginning and end of a work day, site supervisors have to carry out thorough inspections using the inventory checklist to confirm each tool is accounted for.
If you have already implemented tags or labels, the process will be much shorter. All it takes is scanning the tools available on the site and comparing the results to the inventory list.
However, it’s even easier with dedicated tracking software. You can check items in a list just by scanning asset tags on your tools.
At the end of the process, if there are any unchecked entries left, you will know which tools to search for.
Ultimately, providing a reasonably up-to-date overview of all assets makes a site-specific inventory a useful, if not an indispensable addition to your asset-tracking toolkit.
Implement a Tool Sign-Out Sheet
Checking the inventory on a daily basis is a useful technique for identifying and recovering lost tools, but it still doesn’t address the root of the problem, which is them going missing in the first place.
With a tool check-out sheet—like the one you see below—you will put the onus on the workers to take more care of the equipment they’re using.
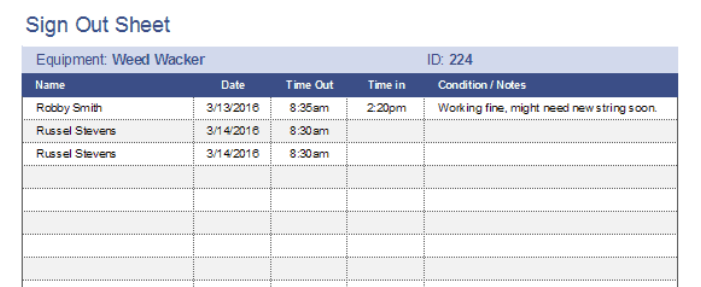
The procedure is simple.
Employees are required to check out each tool they plan to use that day. At the end of the day, or when they’re done using it, they have to check the tool back in.
That way, you will make the workers accountable for the equipment they use on the job site.
Knowing they are personally responsible for the tools in their care, employees will pay more attention to not leaving them behind or carelessly lending them to others.
Also, have we mentioned equipment theft yet?
Because construction sites are often not properly secured, they make attractive targets for thieves.
While heavy construction machinery promises the highest monetary gain, tools are actually connected to the majority of theft incidents:
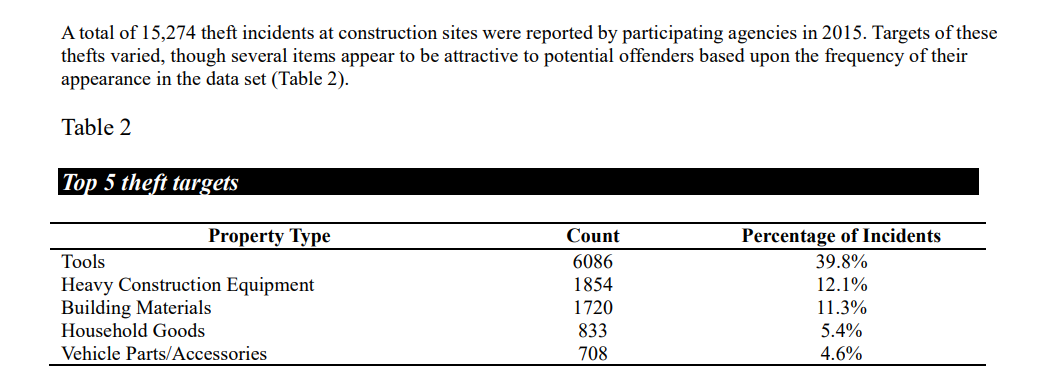
Whatever the number of those may be, a tool sign-out sheet would bring it as close to zero as possible, and it would be particularly effective at preventing theft and loss within your company.
When employees know they are personally accountable for a particular piece, they won’t let it go missing.
Ultimately, if employees have to put their name under the tools they are using, the overall number of lost tools on your construction sites tends to go down.
Instruct Employees to Use Toolboxes
Even with everything mentioned so far, workers can easily forget about the tools they signed out or the place they used them last.
To avoid mix-ups and accidental misplacements, you should instruct employees to use a tool organization system.
What we’re referring to are methods for storing, organizing, and transporting construction tools around the site.
As the founders of the organizing and decluttering business Done & Done Home point out, there are different types of tool organization solutions to choose from:
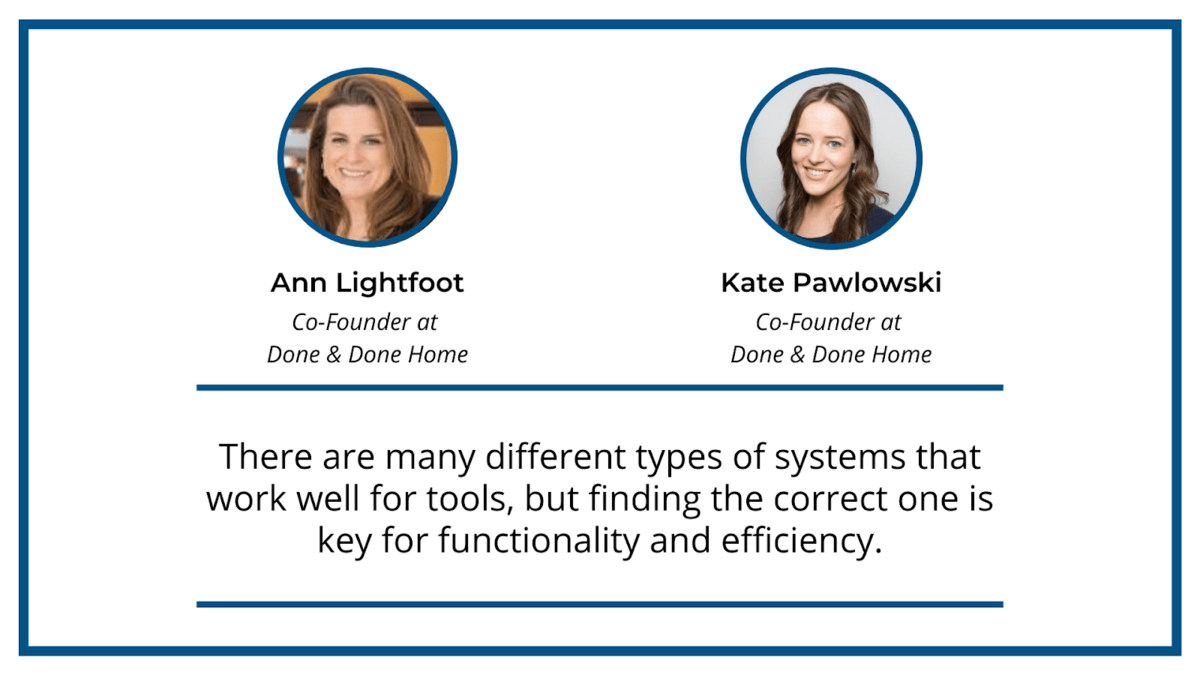
Their suggestions include toolboxes, cases, vests and tool belts of different shapes and sizes.
While you can utilize several of these solutions depending on the number of tools a worker needs, it’s best everyone has at least one personal medium-sized toolbox, such as the one in the example below:
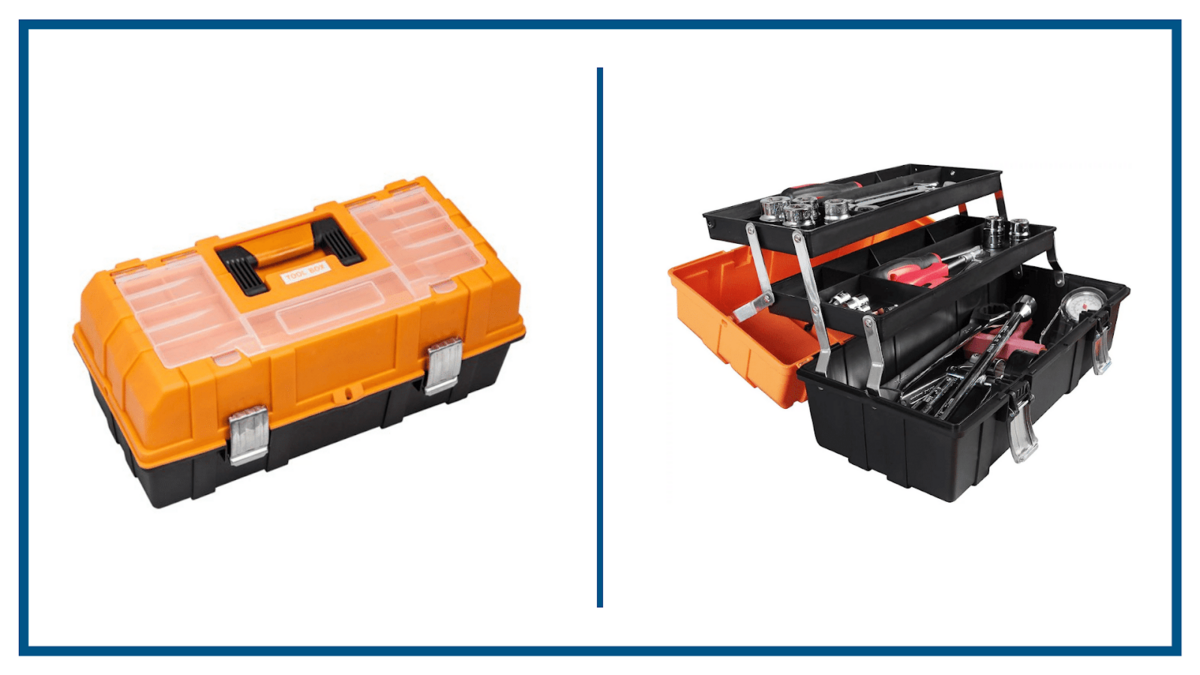
Workers should be instructed to store tools in their toolboxes as soon as they are signed out.
Additionally, employees should only take items out of the toolbox when intending to use them. In the same vein, they should return the tools to the toolbox as soon as they are done with them.
After a short while, workers will get so used to the system that it will become second nature.
Therefore, there will be a much smaller chance they will leave their personal tools lying around the site to be forgotten or picked up by others.
Overall, toolboxes are extremely practical because they provide workers with a single place to keep all of their tools, making it easier to keep track of them.
Let’s try to apply the same principle to individual construction sites.
Store All Tools in a Single Location
Remember that Reddit post from earlier? Turns out, there is some solid advice hidden in the responses:
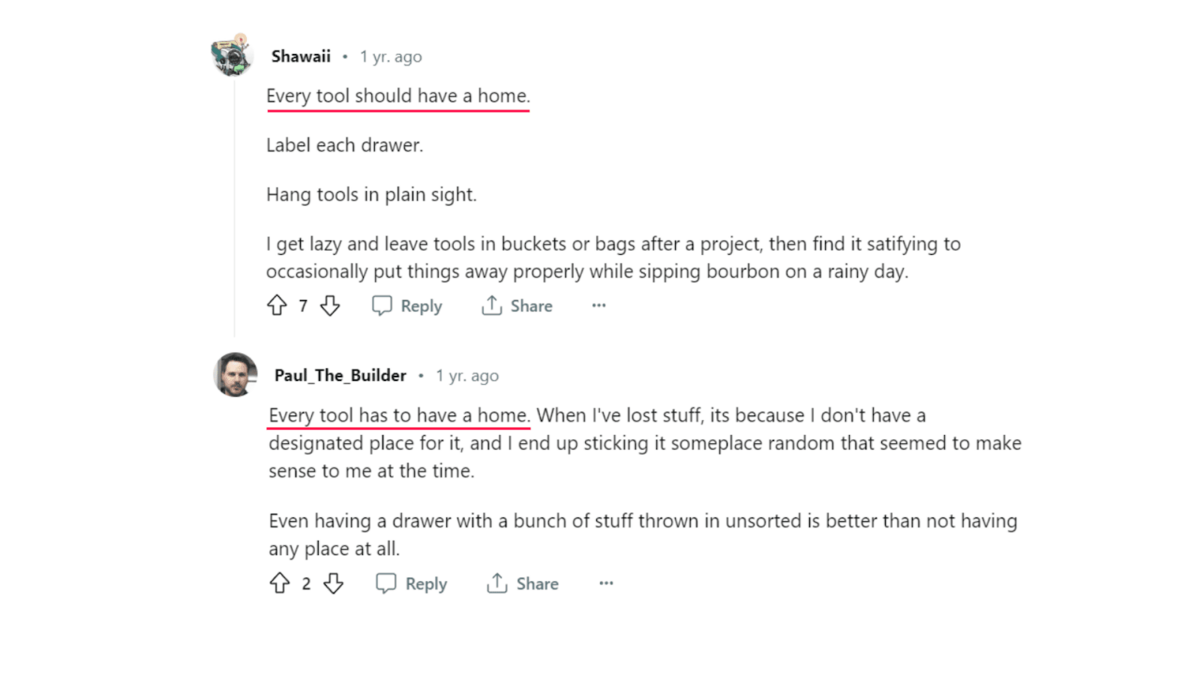
So, what does making a home for tools represent in the context of construction sites?
It means designating a single location where all tools are stored and managed, as opposed to having them scattered in several places around the site.
This provides a much better overview of all your assets. When a tool goes missing, you won’t have to check if it somehow ended up in the wrong storage space first.
Having a centralized tool repository also makes it easier to carry out some of the other measures for preventing tool loss mentioned above.
For example, inventory control can be done much faster if the person running it doesn’t have to waste time going around the site to visit multiple storage units.
Furthermore, you can avoid unnecessary mix-ups with checking the tools in or out of storage.
Without a centralized repository, you are certain to end up with cases of workers signing out tools at one location and signing them in at another.
All in all, having one location for storing all tools on the site streamlines other tool management so that it takes less time and effort.
The only way you could further improve upon everything we’ve discussed so far is to implement tool management software.
Use Tool Management Software
The last piece of the tool safeguarding puzzle is possibly also the most impactful.
Putting in place a dedicated tool management solution will both simplify and enhance every other measure for preventing tool loss, making for a more efficient workflow across the board.
First of all, equipment management platforms such as GoCodes Asset Tracking offer a centralized database of all tools in your company’s possession.
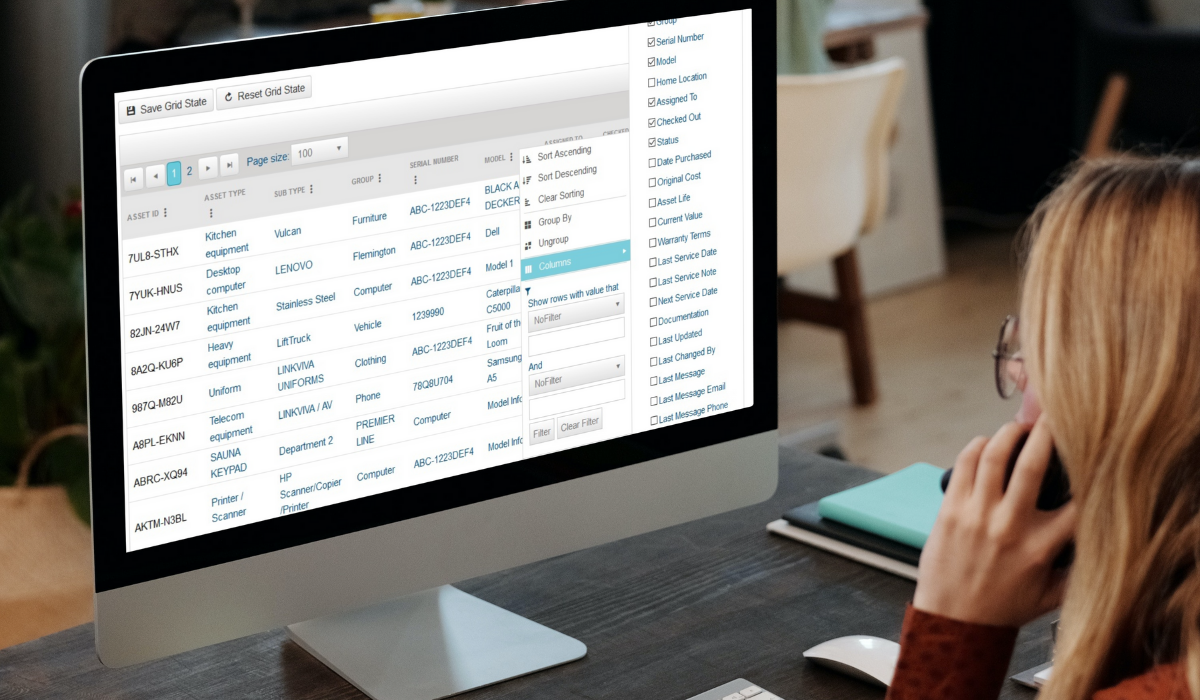
As you can see, there are a number of data fields to filter and group assets by, all of which are customizable to fit your specific situation.
This is extremely helpful in creating lists of any type, site-specific inventories included.
Secondly, it makes it much easier to check equipment in and out. Every tool has a database entry which contains all pertinent information and history related to it.
In the entry, there is a check-out option where you can assign the tool to a specific employee for a specific duration.

Of course, this also allows you to filter tools by users, or to show just the tools at the end of their life cycle.
Finally, another major benefit of digitized tool management is GPS tracking.
When you scan a QR code tag on a tool, it can automatically update the assets location to be where the scan was performed.
This way, if a tool goes missing, you will have an exact time and location as a basis for performing a search.
All in all, by offering a polished and comprehensive version of methods outlined in this article, tool management software is the best way to stop the loss of tools on your construction sites.
Conclusion
Construction site management is all about reducing the time and increasing the efficiency of processes and procedures which govern how construction sites operate.
Seeing as lost tools can have a tangible impact on workflow, it’s important to find solutions which address the problem without taking too much from other aspects of production.
For this reason, all of the advice shared in this article is practical and most can be applied at little or no cost.
However, given the affordable price and extensive number of useful features, construction companies will benefit most from investing in tool management software, which is why you should consider using one for your business.