Key Takeaways:
- The reasons behind construction project delays are typically tied to inadequate project management.
- Construction companies that aren’t leveraging technology are missing out on opportunities to improve their construction operations.
- Experiencing resource shortages and exceeding budget estimates point to construction operations that need improvement.
Construction operations managers are experts at making sure projects run smoothly, but every construction business reaches a point where change is desperately needed.
And it isn’t just a gut feeling either.
Several clear signs point to inefficient construction operations that eat away at not only your profits but also employee and client satisfaction.
So, whether you’re already addressing these concerns or simply want to make room for future growth, join us for a deep dive into common problem areas and ways to move forward!
In this article...
You’re Consistently Experiencing Project Delays
“Project delays” counts as one of the most dreaded phrases in the construction industry.
Of course, having to keep different processes in check while juggling various stakeholders isn’t an easy task.
Plus, some delays are inevitable due to unforeseen circumstances.
The problem starts when they become too frequent.
The 2022 study by Cornerstone Projects Ltd. revealed that 91% of surveyed workers experienced delays on one of their projects.
Furthermore, nearly a third claimed that construction delays happen half the time.

When compared to the company’s 2016 study, these more recent findings also indicate that more and more projects are experiencing longer and costlier delays.
So, what are the patterns here exactly?
Firstly, it’s important to take a look at several interrelated factors that cause or prolong delays.
On the one hand, there are external factors, such as weather conditions, geopolitical changes, or legal issues, which exist beyond businesses’ immediate control.
Internal factors, on the other hand, arise from within companies, and typically fall under:
- Design changes
- Material shortages
- Labor disputes
- Inadequate project management
At first glance, the external factors seem more likely to cause unexpected delays, but the aforementioned study suggests otherwise.
The three most cited reasons behind delays point inwardly, specifically in the direction of inadequate project management.
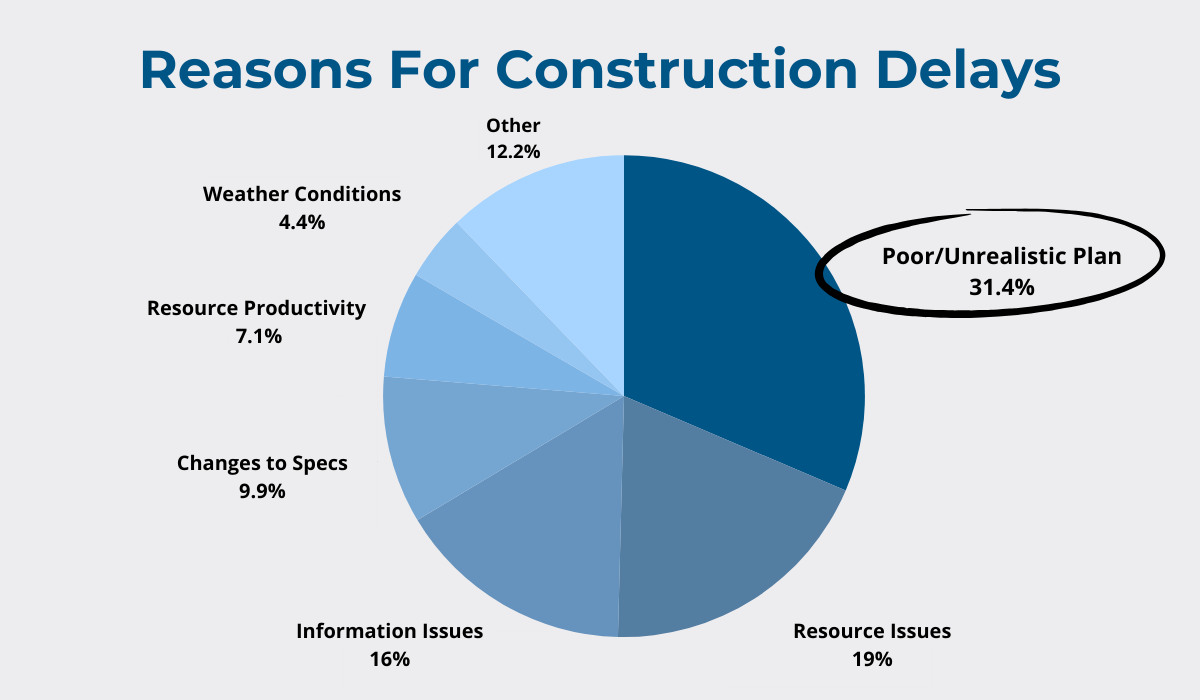
Poor planning and scheduling were identified as the top cause of delays, followed by various resource and information-related issues.
Now, keep in mind this is a good thing.
You can’t control the weather, but you can mitigate these risks immediately by conducting thorough assessments and mapping key areas for improvement.
For example, a closer look into project planning or workflow management may reveal inefficiencies that can be addressed with minimal tweaks.
As a rule of thumb, construction businesses that consistently meet project milestones keep comprehensive records and logs and search for ways to enhance cross-team communication.
One tried-and-true remedy for achieving such visibility and coordination is to introduce innovative technology, so if you’re yet to board the tech train, you’ll find the next section especially insightful.
You’re Falling Behind with Technology Adoption
Technology has helped transform the construction industry from the ground up, and lagging behind the current trends is no longer an option for growing businesses.
To put it simply, not leveraging technology means you’re likely missing out on opportunities to improve your construction operations, ensuring streamlined workflows and higher productivity.
Even before the most recent surge of advancements ushering in the Construction 4.0 Market, the industry was ready to embrace technology and reap its benefits, as indicated by Statista’s global survey on software use.
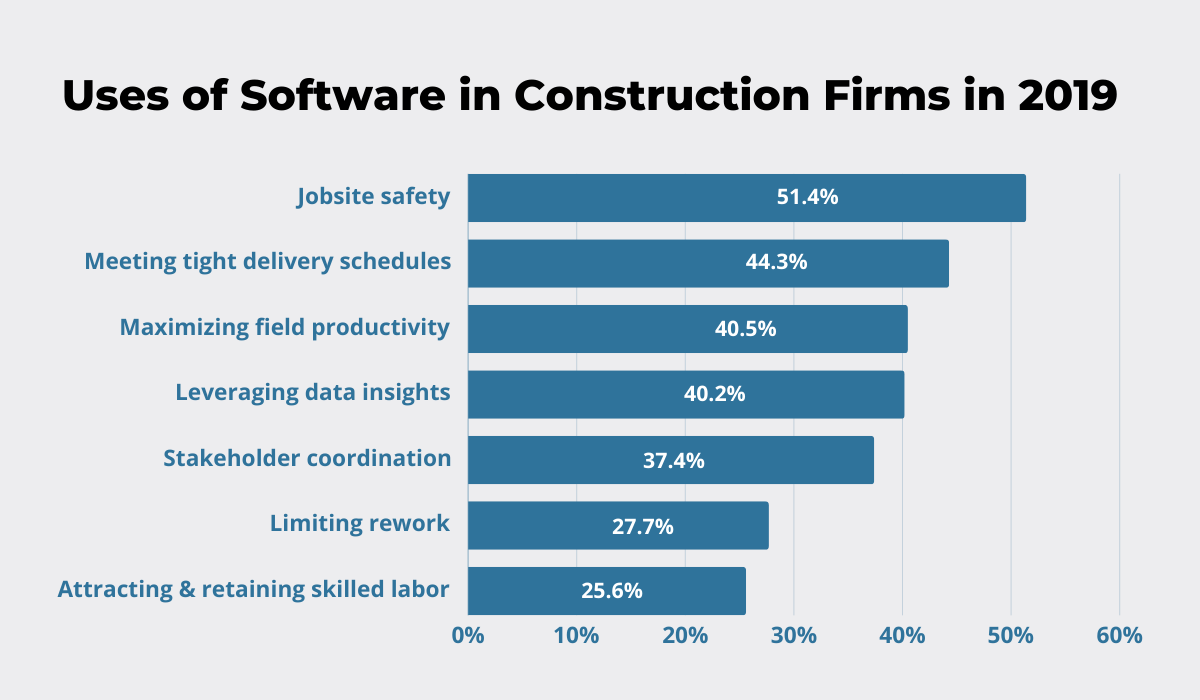
From enhancing job site safety and information sharing to maximizing productivity and efficiency, software solutions promise different benefits that businesses couldn’t pass over.
Today, KPMG’s Global Survey ranks technology such as Building Information Modeling (BIM), integrated project management information systems (PMIS), and advanced data analytics the highest based on their ROI capacity.
Several others, like artificial intelligence (AI), 3D printing, and virtual reality (VR) also hold untapped potential.
But the most important question for those who wish to navigate this rapidly changing landscape is: where do I start?
While quickly investing in the most highly praised technologies seems tempting, the most important thing is to take the time to devise a digital transformation strategy that aligns with your company goals.
As pointed out by Wilfred Obi Jr., a C-level executive in a US-based software solution company, it is essential to treat this journey and everything it entails as a long-term investment.
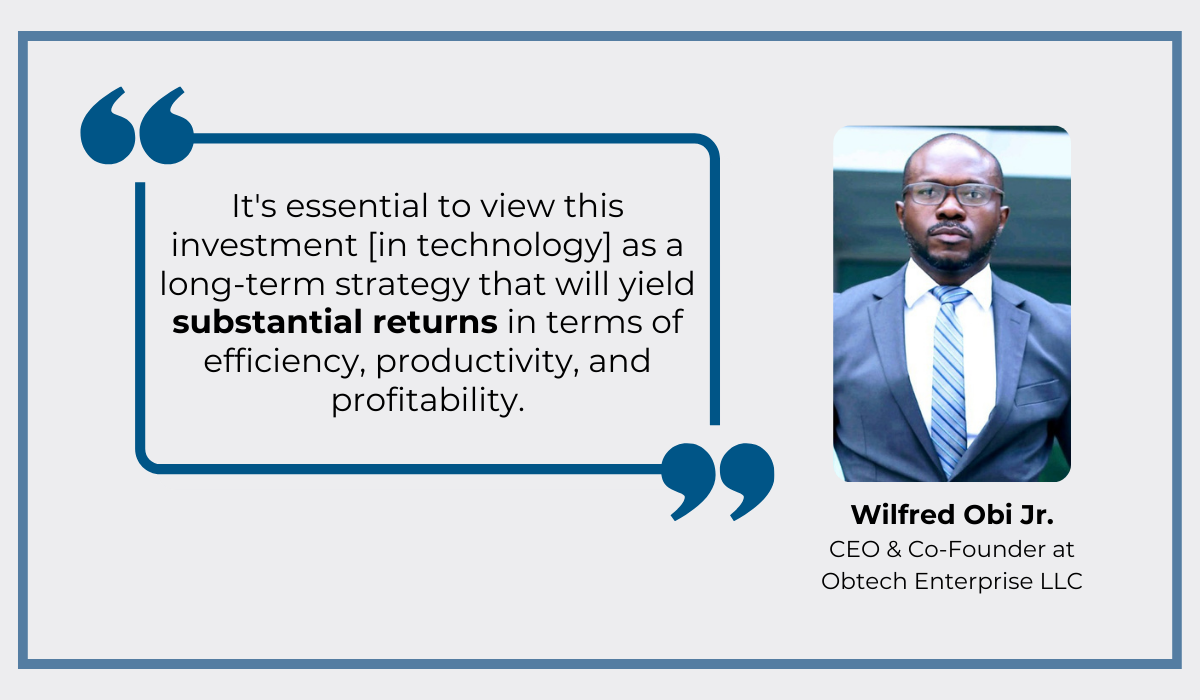
Besides identifying different pain points and areas for improvement, managers need to take into account both the existing infrastructure and the employees.
For example, providing comprehensive training and support for workers implementing the chosen solution is an essential step in every successful digital transformation.
Nevertheless, choosing technology that feels intuitive to use and actually helps automate or eliminate more burdensome aspects of construction operations is equally important.
Take our own asset management solution GoCodes, for example.
By relying on QR code asset labels and tags, employees can effortlessly check assets in and out, keep track of them in real time, perform audits, or schedule maintenance, all while ensuring high productivity levels.
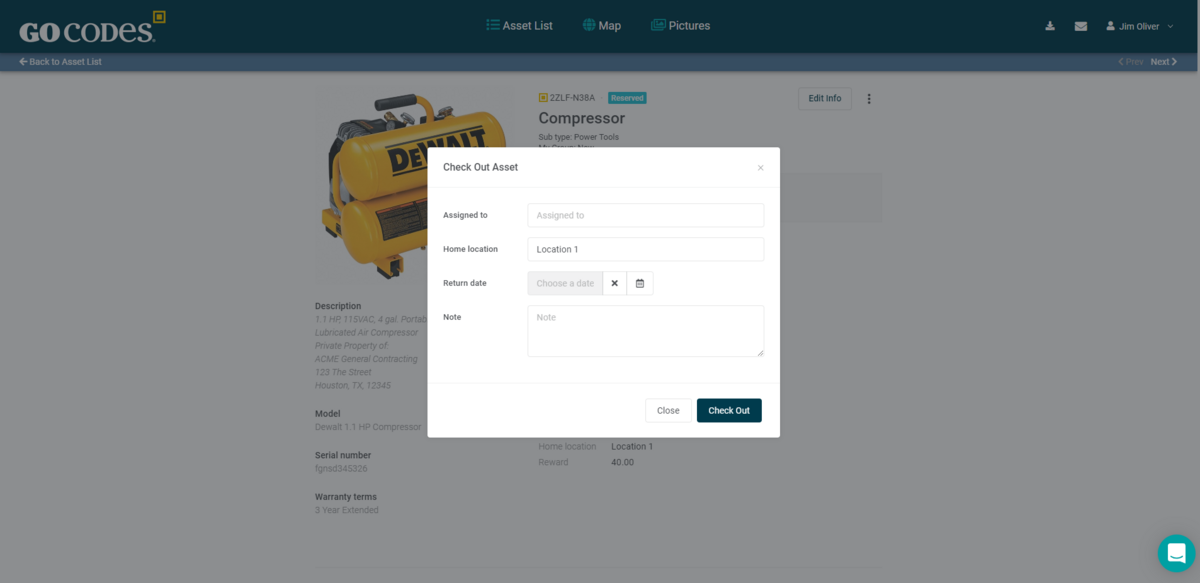
A user-friendly scanning feature coupled with one centralized information system is enough to improve the flow of construction operations across the job site.
You Have High Rates of Rework
Construction rework is essentially an expensive do-over.
It drains your budget while disrupting project timelines and lowering overall productivity.
So, if you find yourself correcting production errors time and time again, that’s a strong signal of inefficient project execution, but also inadequate quality control and stakeholder coordination.
Unfortunately, rework issues are very familiar to operations managers, and often stem from one of the following reasons.
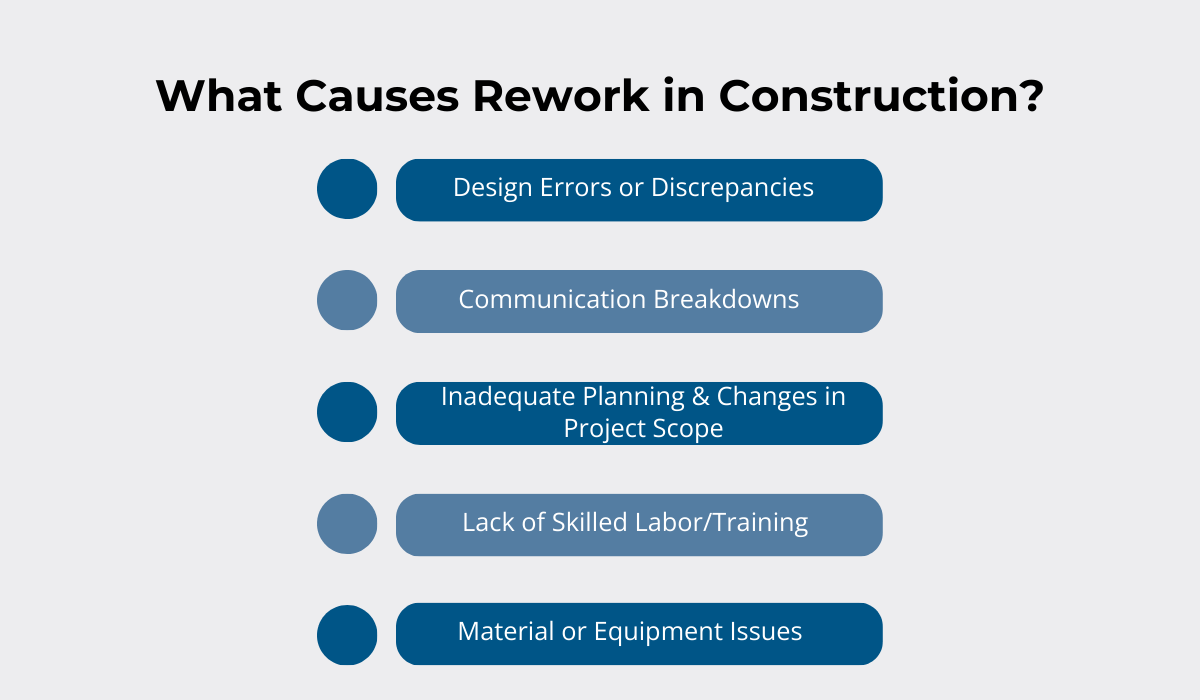
As businesses most likely experience rework due to several related factors, a careful analysis is the necessary first step for formulating a plan of action.
To gain a better sense of the root causes behind frequent reworks, start by measuring actual performance and putting greater emphasis on regular quality control inspections.
Whether your projects slow down due to design errors or lack of skilled labor, you’ll be ready to implement countermeasures only once you’ve identified the underlying reasons.
However, it’s worth paying special attention to addressing the lack of coordination among project stakeholders.
Namely, a study published in the Journal of Building Engineering revealed that complex and clogged communication channels between principal stakeholders greatly contribute to major reworks.
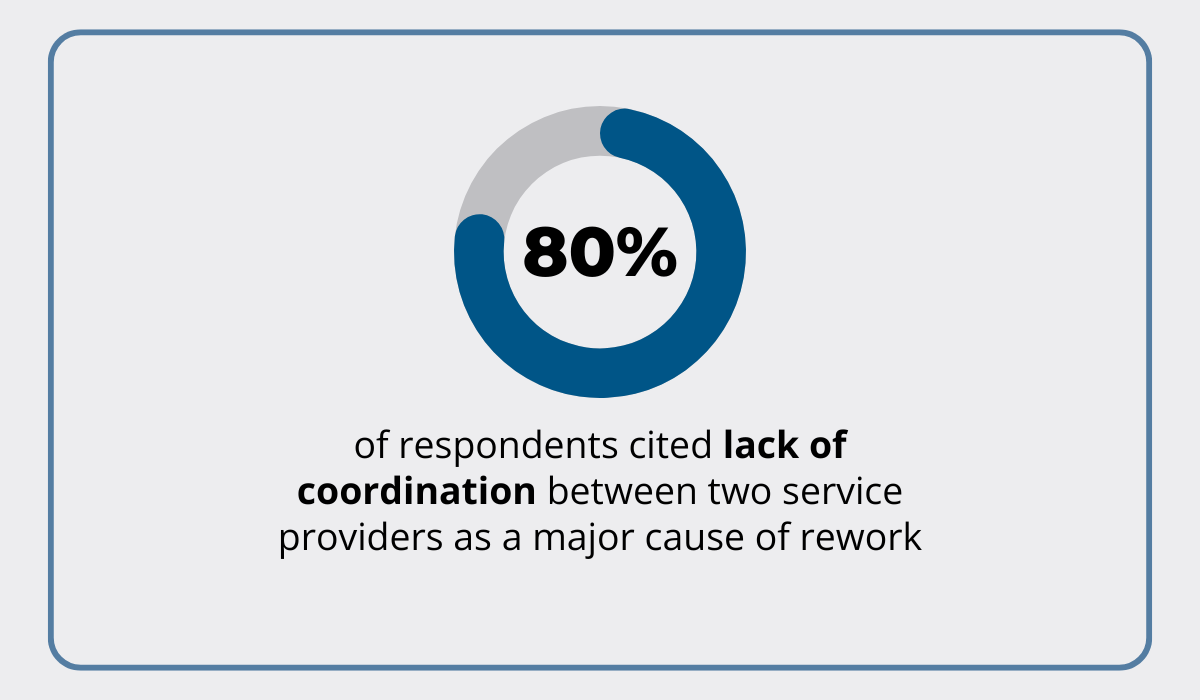
In some cases, poor scheduling and discrepancies meant having to dismantle an already finished structure, while a lack of agile communication channels led to frequent delays in receiving updated schematics and, consequently, rework.
But how can you avoid these disaster scenarios?
More easily than you think, thanks to centralized communication systems.
Robust project management and communication solutions facilitate quicker exchange of information, and by keeping everything in one place, the stakeholders can stay in the loop well after the initial planning.
Furthermore, this means enhanced internal communication, better task flow, and any changes to the scope of the project communicated instantly across the entire job site.
On the other hand, the lack of visibility and communication often leads to additional operations problems, including resource shortages.
You’re Experiencing Resource Shortages
Constraints on vital resources are among the biggest threats to the timely wrap-up of construction projects.
Although in some cases directly related to global shifts, such as the one brought upon by the COVID-19 pandemic, experiencing persistent shortages of resources like skilled labor, materials, and equipment is a tell-tale sign of operational inefficiency.
And even if some inefficiency doesn’t sound too bad on its own, just consider how resource shortages translate to delays impacting total costs and project outcomes.
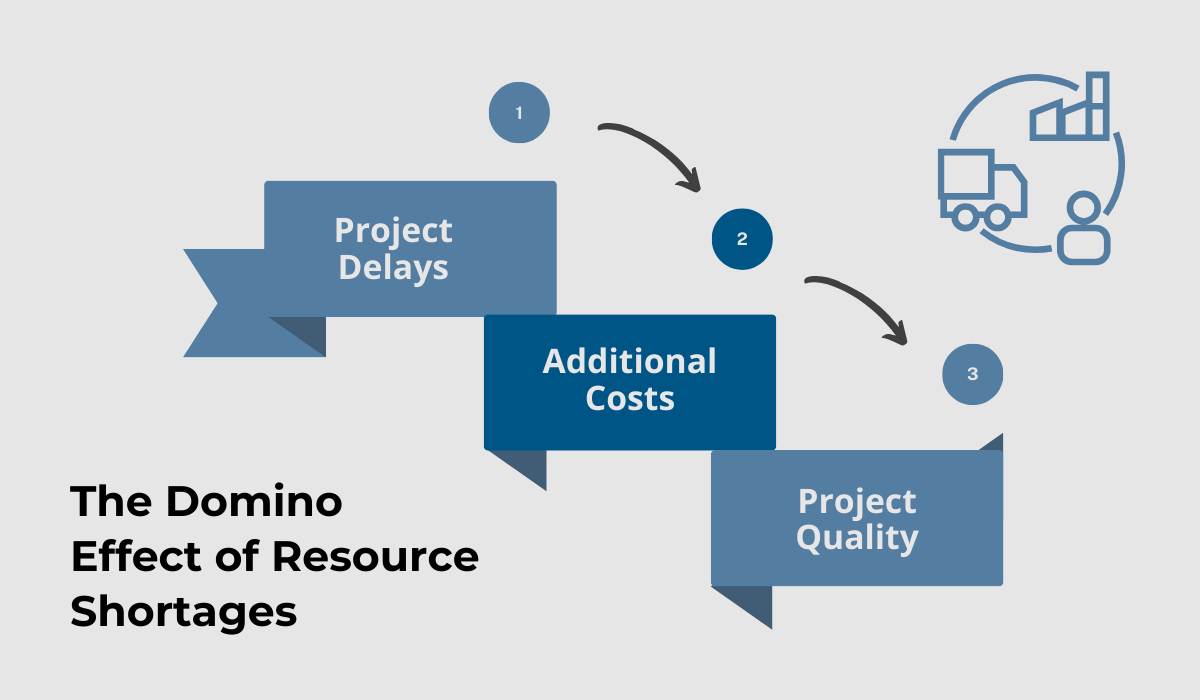
The additional costs are often a result of attempts to mitigate delays, which usually means sourcing materials at a higher price or paying workers overtime, but can also include penalties due to missed deadlines.
What’s worse is that companies facing shortages often feel forced to take shortcuts, such as using lower-quality materials as replacements.
Besides compromising the quality standards of the final product, in this way, businesses also risk reputational damage.
This is why it’s crucial to address these issues and find ways to manage disruptions effectively.
For starters, having a good understanding of resource requirements and potential constraints requires you to take a closer look at different areas, such as resource assessment, procurement, and utilization.
After you’ve identified focus areas, there are some additional strategies you can incorporate.
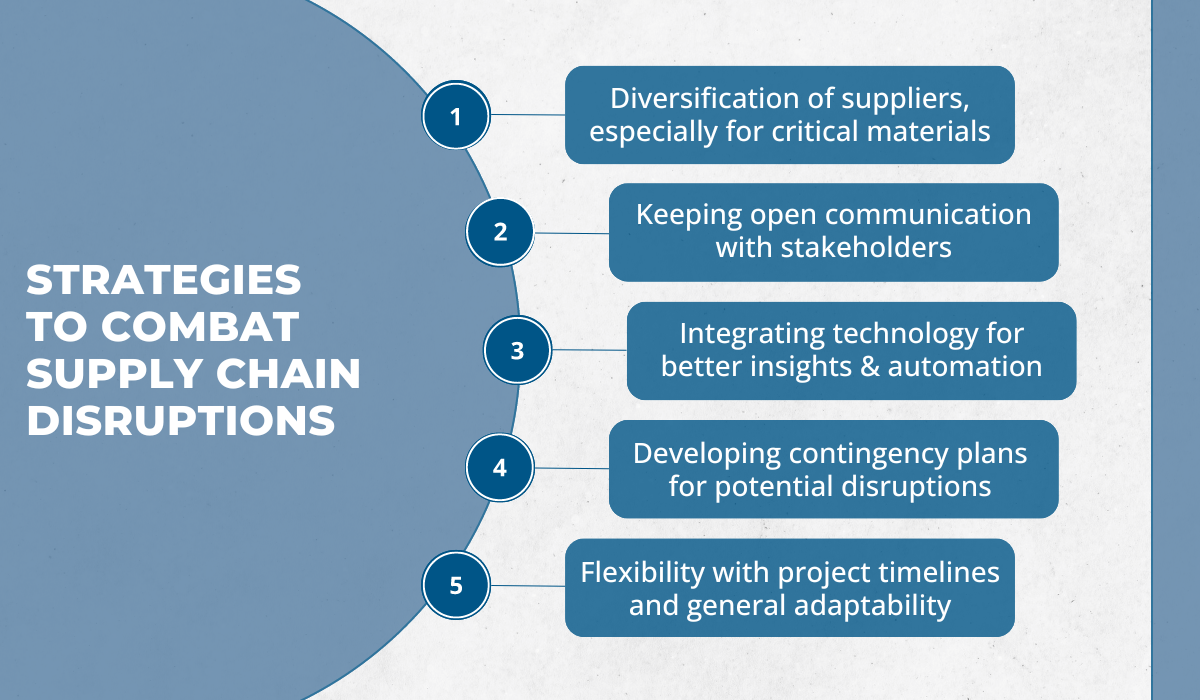
These five strategies tend to overlap and have common elements, so let’s take a closer look at two of them.
Firstly, contingency planning is invaluable because it promotes regular assessment of supply chain risks and creates a safety net of alternative suppliers and materials.
By taking the time to devise contingency plans, you’ll have greater adaptability and won’t be caught off guard even when unexpected situations do arise.
Secondly, construction technology can be leveraged to help you track and manage resources more effectively.
For example, using geofencing software for real-time tracking of shipments and inventory levels can provide crucial insights allowing you to anticipate disruptions and improve operations on several levels.
Technical consultant Myra Sharma explains:
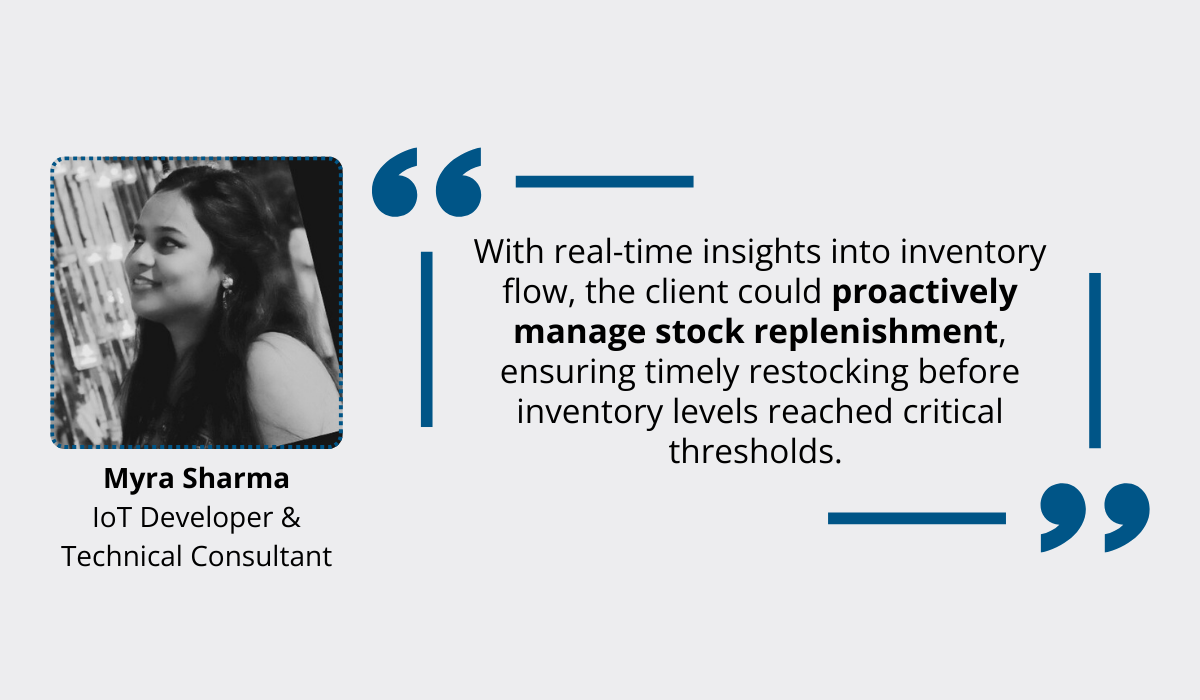
This kind of automation addresses significant pain points, but also eliminates repetitive tasks and opens up new venues for productivity.
For example, an inventory management system represents a significant upgrade compared to traditional spreadsheets through functionalities such as automated stock reordering and multi-location inventory tracking and routing.
These features help you control costs and stay within the budget, bringing us to another set of issues plaguing construction companies.
You Often Exceed Budget Estimates
Running up costs far beyond budget estimates isn’t unusual for construction companies.
In fact, frequent cost overruns have hounded the construction industry for decades, as evidenced by a comprehensive academic study on the topic.
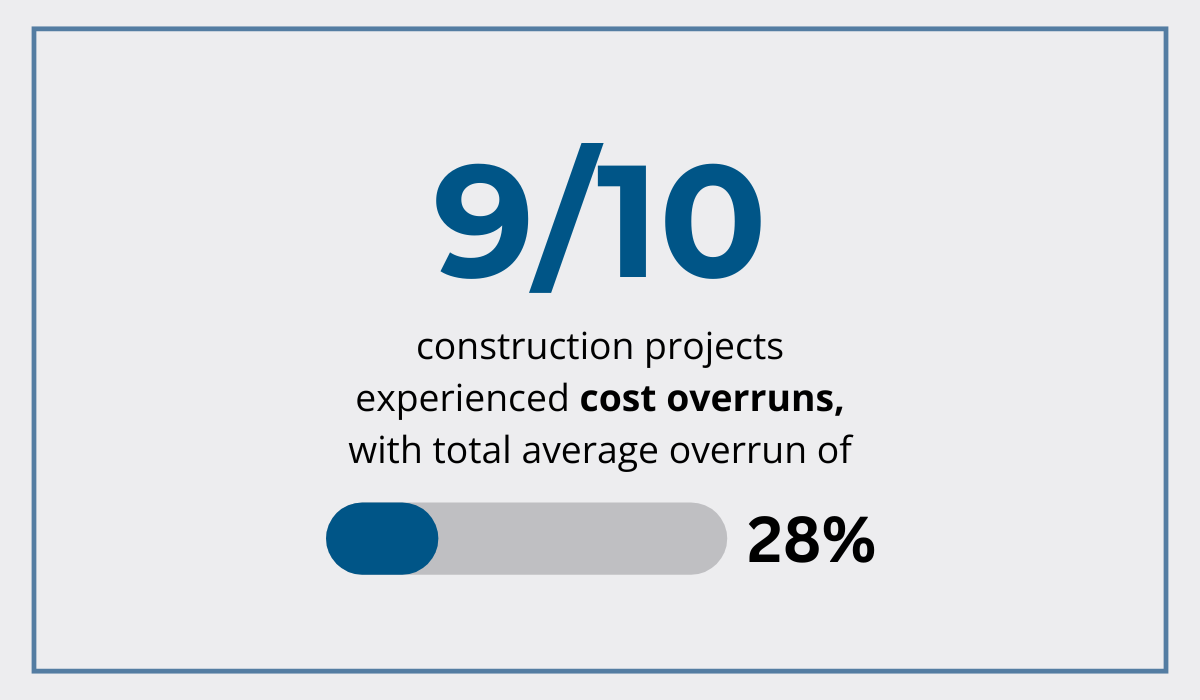
With 85% percent of businesses from 20 countries reporting cost overruns, some budgeting issues typically won’t raise alarm or will even be accepted as status quo.
However, frequently exceeding budget estimates paints a different picture.
Experiencing cost overruns on each project casts doubts on budgeting accuracy and raises concerns about cost management in general.
So, how do you overcome this hurdle?
Having some clarity about the common causes is a good first step, so here are some major factors contributing to cost overruns:
- Inaccurate project estimates
- Major project design or administrative errors
- Not accounting for change requests
- Disregarding hidden costs of permits, delays, and labor
- Inefficient site management
Although each of these can be analyzed separately, inefficient site management deserves special attention, given the findings of Levelset’s 2020 report:
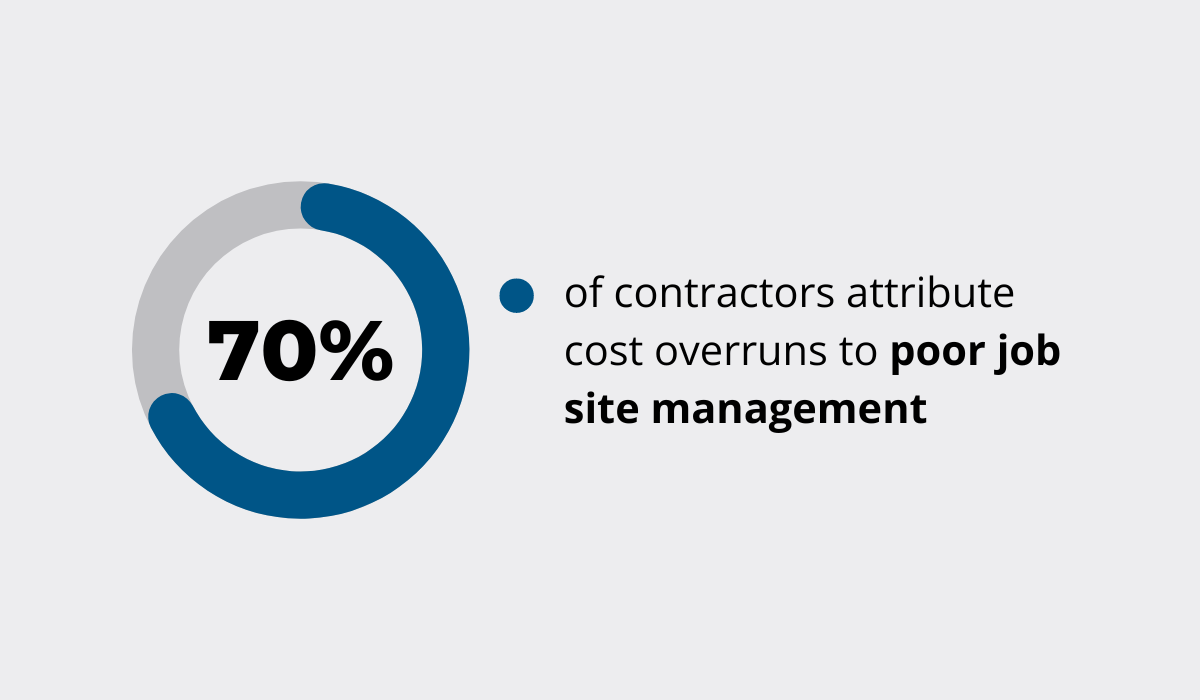
This insight is particularly valuable for businesses looking to identify negative trends and explore cost-saving opportunities by streamlining construction site processes.
For example, measures such as digitizing documentation or tracking fuel consumption through asset management solutions introduce significant improvements while reducing costs.
Although this is a good starting point, don’t stop at operations!
Take the time to analyze project costs and note which operational aspects contribute to overspending the most.
Keeping your future projects in mind is also of vital importance, as noted by Senior Quantity Surveyor, Safeerul Hug:
“Conduct post-project reviews to analyze budget performance and identify lessons learned. Document successes, challenges, and areas for improvement to inform future projects and enhance budget management practices.”
Finally, only continuous effort at implementing cost-control measures and seeking general improvement will fully address your company’s needs and yield the best results.
Conclusion
There are dozens of inefficiencies chipping away at construction companies, and you should address them sooner rather than later.
Staying on top of delays and rework or managing resource shortages is possible.
One course of action is to make use of the latest technology, but it’s even more important to plan meticulously and reduce unnecessary expenses.
Improving construction operations will enable you to navigate treacherous waters and steer your business to success, so what are you waiting for?
It’s time to carve out a path forward!