Construction material takeoffs serve as the primary roadmap for project success.
Their purpose is to systematically quantify and itemize all the materials and components needed to complete a construction project.
As such, material takeoffs are a crucial tool in project planning and beyond, extracting essential information from design drawings, specifications, and other project documents.
In this article, we’ll delve into three different types and two distinct methods of performing material takeoffs, offering valuable insights into these fundamental processes.
So, read on to enhance your understanding of this critical aspect of construction project management.
In this article...
Preliminary Material Takeoff
As its name suggests, a preliminary material takeoff is an initial, approximate assessment of materials required to build an office building, house, bridge, warehouse, or any other construction project.
This early-stage estimation provides a broad overview of the project’s material needs and serves as a foundation for initial cost estimates, feasibility studies, and securing project financing.
Therefore, it’s done in the early project development stages, usually after the project’s conceptual design is finalized but before any detailed material specifications are determined.
As for who performs a preliminary material takeoff, that depends on the project delivery method, the stakeholders involved, and contractual arrangements between them.
To illustrate, let’s look at two typical project delivery methods, Design-Bid-Build (DBB) and Design-Build (DB).
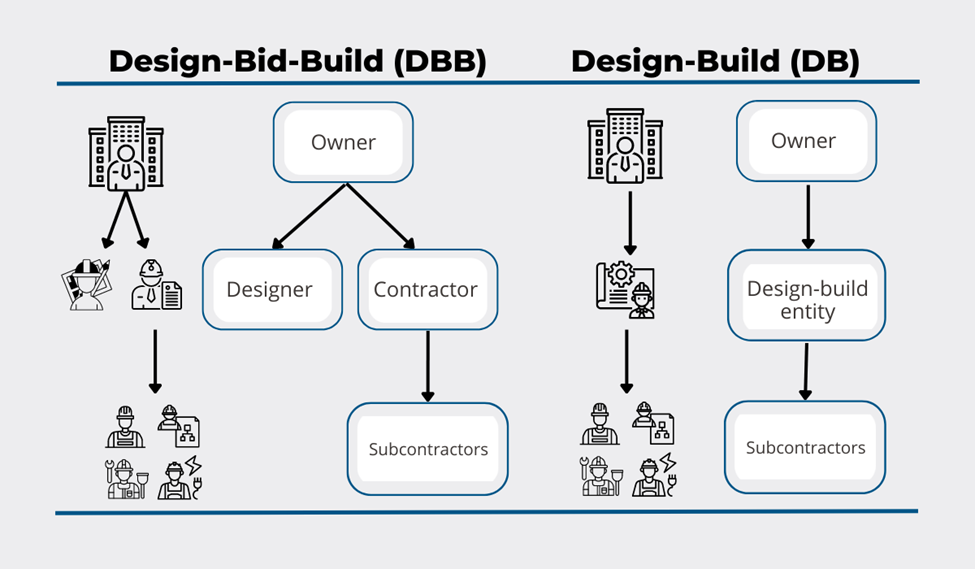
As you can see, in the still prevalent DBB method, the project owner will first hire an architect to draw up the conceptual design.
Following this, a preliminary takeoff will be performed, usually by an estimator and any other construction professionals, whether they’re part of the design team or hired separately by the project owner.
The purpose is to create a preliminary list of building materials and their approximate quantities, which helps the project owner/developer make an initial cost estimation and determine the project’s feasibility.
As the project design progresses, the preliminary material takeoff may be revisited one or more times to refine and add additional details to the initial material assessment.
The primary reason for this is to prepare project specifications for the bidding process.
In other words, the aim is to provide potential contractors with a clearer understanding of the project’s material requirements, enabling them to produce more accurate and competitive bids.
As we’ll see in the next section, each bidding contractor will typically use the provided high-level material specifications to conduct a detailed takeoff, accurately estimate total project costs, and submit a bid with an appropriately priced proposal.
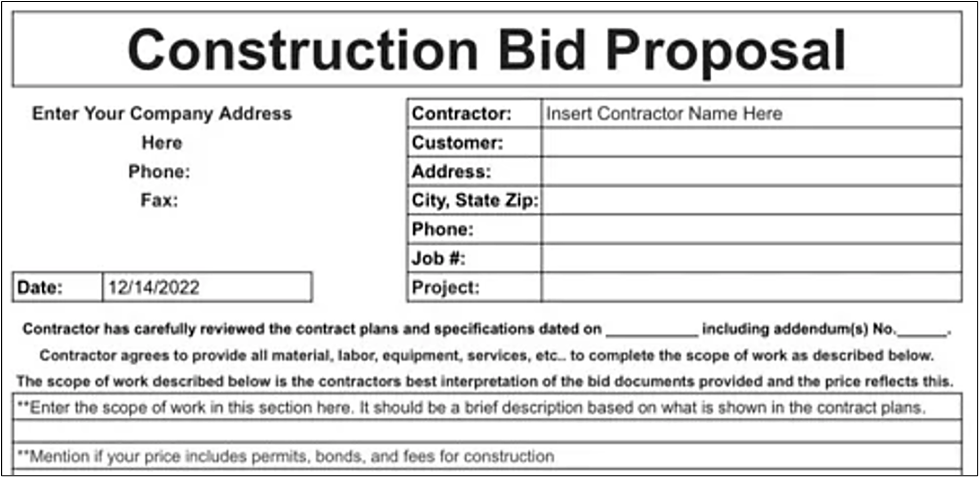
Now, let’s look at who would perform a preliminary takeoff in the other project delivery model we illustrated, Design-Build (DB).
This method involves the project owner hiring a design/build entity, i.e., an integrated team consisting of both designers and contractors (including cost estimators).
Therefore, they usually collaboratively conduct a preliminary material assessment to estimate costs and determine whether the project is feasible (fits the client’s goals and budget).
As the project concept evolves, other preliminary takeoffs with varying detail levels can be performed, allowing the design-build entity to remain aligned with the client’s requirements, design intentions, and cost considerations.
When the project reaches the advanced stages of design and planning, a detailed preliminary takeoff will typically be conducted.
Of course, there are other project delivery methods we haven’t covered, such as Construction Management at Risk and Integrated Project Delivery (IPD), each with its own nuances in preliminary takeoff processes.
In conclusion, this initial estimation of material quantities plays a crucial role in shaping early decisions, considering costs, and determining the overall feasibility of a construction project.
Detailed Material Takeoff
A detailed material takeoff can be conducted by a prospective contractor submitting their bid or by an already established design/build team.
Regardless, this process involves an in-depth analysis of materials needed for construction, resulting in a comprehensive list with quantities, sizes, and specifications.
This aids in the precise estimation of overall project costs and project planning.
When this is done by a prospective contractor to prepare an accurate bid, the detailed material takeoff is usually preceded by that contractor:
- conducting an initial assessment of the received project documentation to understand the scope, complexity, and specific requirements of the project, and
- thoroughly reviewing project specifications to identify which types of construction materials and components are referenced.
These preparatory steps help the contractor determine the level of detail needed for the upcoming material takeoff.
After the detailed takeoff, the contractor needs to go through a few more steps to finalize their bid, as shown below.
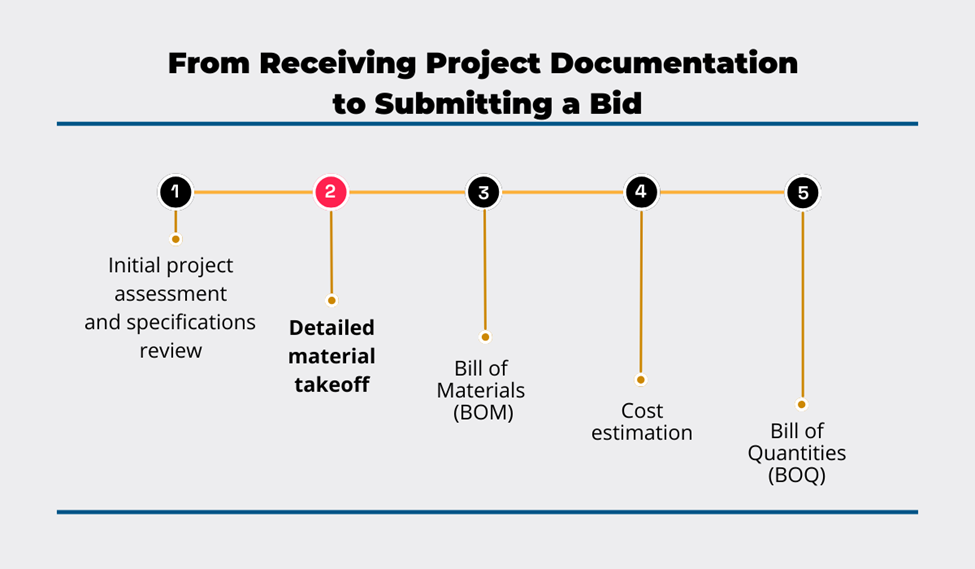
As illustrated, the detailed takeoff will result in a Bill of Materials (BOM), which will then be used as the basis for total project cost estimation, typically resulting in a comprehensive Bill of Quantities (BOQ).
However, before we get there, let’s see what a detailed material takeoff actually entails.
Essentially, the first step can, depending on project scope, setup, and professional preferences, overlap with the specifications review.
The point is to create a detailed itemized list of all materials and components required for the project.
After that, quantities for each item on that list should be measured and calculated by studying architectural and engineering drawings, design plans, and any other relevant documents outlining the project requirements.
As we’ll see in the last two sections, this can be done can be done manually or digitally using specialized takeoff software.
In any case, using the data from the material takeoff, the contractor will create a Bill of Materials (BOM) or a similar document.
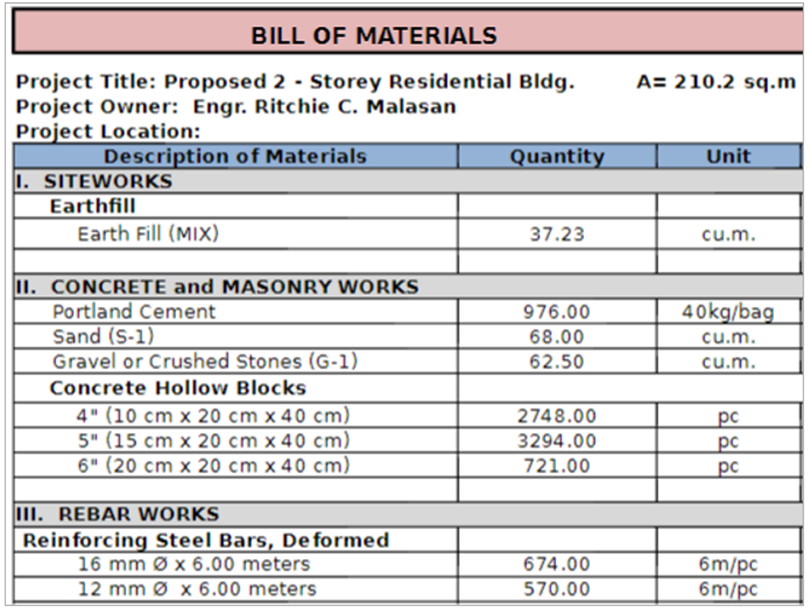
The BOM is a comprehensive list of all the materials needed for the project, including their specifications, quantities, and measuring units.
With this detailed inventory in hand, the contractor proceeds to estimate the costs associated with each material.
Cost estimation includes:
- accounting for labor and equipment requirements and overhead costs,
- assigning unit costs by factoring in market prices,
- considering any project-specific conditions,
- determining a suitable profit margin.
By incorporating these and other elements (contingencies, cost indexing, risk assessment) into the cost estimation process, the contractor develops a comprehensive Bill of Quantities (BOQ).
The BOQ shows the detailed breakdown of costs associated with every aspect of the construction project.
Now, the contractor can finalize their bid proposal and submit it to the project owner.
Bottom line, all these key processes and documents are based on a detailed material takeoff, making it an indispensable foundation for accurate cost estimation, thorough project planning, and the successful execution of construction projects.
As-Built Material Takeoff
As “as-built” implies, this material takeoff is a meticulous process undertaken post-construction that focuses on documenting the actual materials utilized in a project upon completion.
This examination involves a comprehensive field verification and comparison between the initially estimated quantities specified in the detailed takeoff and the real quantities incorporated during construction.
However, to do that, all the changes made to the initial design during construction need to first be recorded in as-built drawings and other construction documents.
Here’s a brief overview of what modifications should be documented to enable an effective as-built material takeoff.
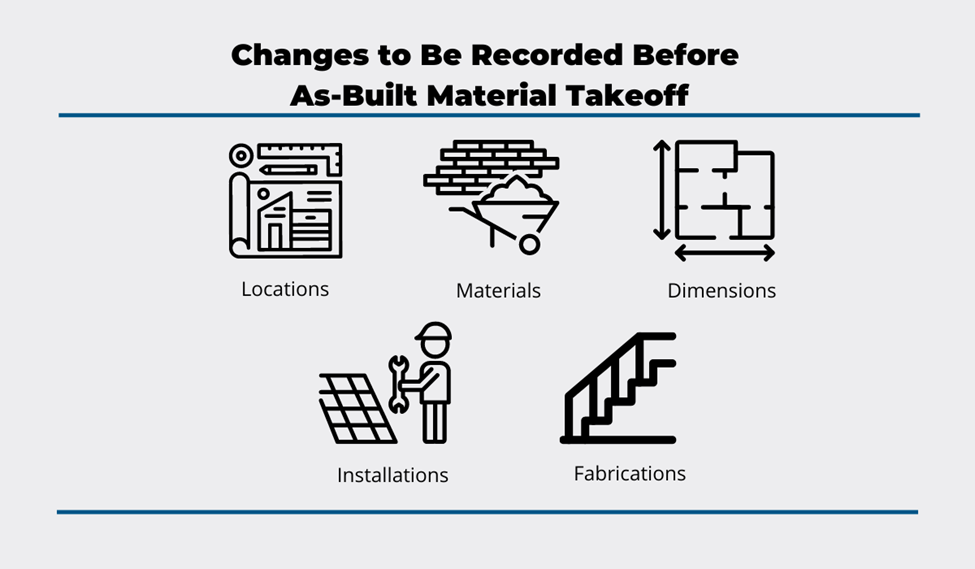
As you can see, this involves recording changes in locations of, for example, doors and windows, other installations, and fabrications (columns, beams, handrails).
Naturally, these changes can also result in different dimensions from the original plan, as well as different material types or, more often, quantities.
With updated as-built drawings, you can proceed to compare the estimated and actual quantities of materials used in a project.
The purpose of an as-built material takeoff is to establish an accurate record of the construction’s material reality, which can then be used for:
- accurate project billing (under some contractual arrangements),
- providing project cost transparency,
- making informed decisions on future maintenance or renovations.
Moreover, it’s a great tool that informs decision-making for future projects, offering contractors valuable insights into the efficiency of their material management strategies, potential discrepancies, and usage patterns.
Overall, the as-built material takeoff provides not only an accurate record of a completed project but also guides material-related decisions for future endeavors.
Manual Takeoff
Having covered the three types of material takeoff, let’s explore the two methods—manual and digital—that can be used to perform them.
These methods are not mutually exclusive, meaning that, depending on the tools used, your takeoffs can be a combination of both.
A manual takeoff is a traditional method of quantifying materials by physically measuring and counting materials and components needed for construction.
As said, it involves analyzing and interpreting construction drawings and material specifications to determine quantities using a variety of tools, most of which are illustrated below.
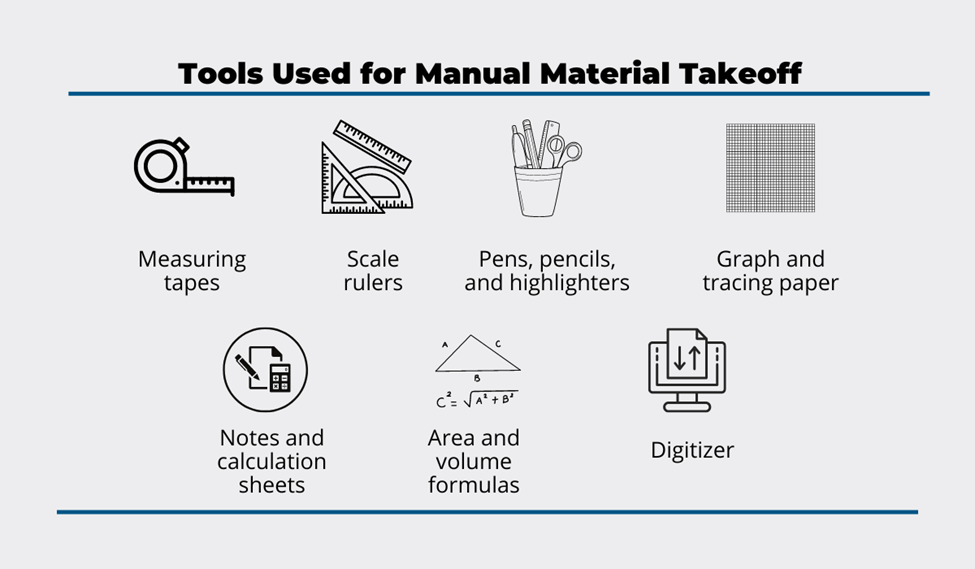
While these tools are largely self-explanatory, let’s just clarify what digitizers are.
In essence, digitizers are tablet or board-like devices that allow estimators to use physical drawings for takeoff to extract digital information.
As such, they stand halfway between purely manual and completely digital takeoffs, but their use has declined due to the rise of faster and more accurate software solutions we’ll discuss next.
In any case, manual takeoffs can be extremely time-consuming and prone to errors, especially when dealing with large and complex construction projects.
This is the primary reason why many contractors are transitioning away from manual approaches to fully digital takeoffs.
Digital Takeoff
As explained, digital takeoffs involve using software tools to perform measurements and quantify materials electronically.
These tools enhance accuracy, speed, and collaboration in the material takeoff process by leveraging technology and digital representations of construction plans.
That way, they can address most of the challenges associated with manual takeoffs.
The range of digital takeoff solutions includes a diverse array of applications, from specialized takeoff and estimating software to platforms that utilize Building Information Modeling (BIM) data for takeoffs.
The choice between them often depends on the contractor’s preferences, technical expertise, and specific project requirements.
For example, Buildxact is a cloud-based construction management solution that focuses on enabling residential contractors to streamline takeoffs and create more high-quality bids in minimum time.
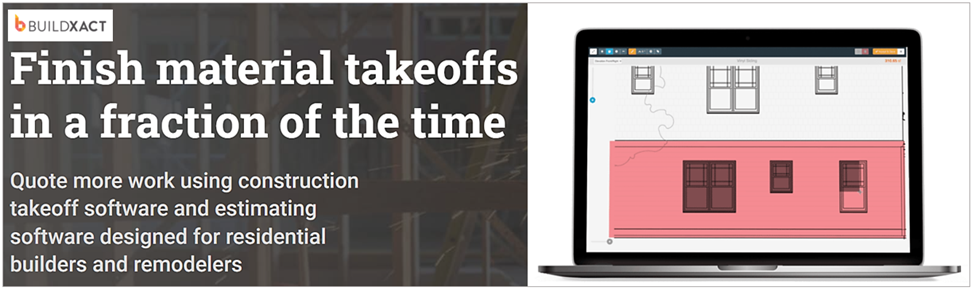
Despite potential differences between digital takeoff solutions you can choose from, such software will generally ensure:
- enhanced accuracy of takeoff measurements and streamlined documentation,
- immeasurably faster quantification and calculations of materials, and
- efficient collaboration among project stakeholders, facilitating real-time sharing and updates.
Since the detailed material takeoff is the basis for all other project planning activities, adopting an appropriate software solution can generate many advantages, including more accurate cost estimations and more efficient resource planning.
On that note, you should also consider other digital solutions that can help you streamline resource allocation for upcoming projects, such as our asset-tracking software, GoCodes Asset Tracking.
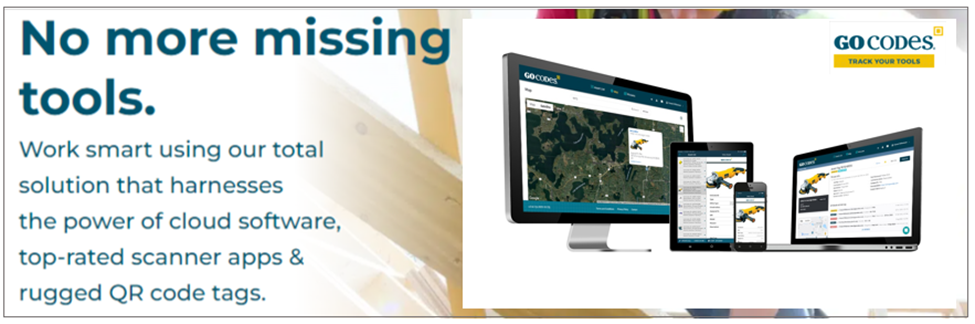
You can use GoCodes Asset Tracking to track the location, usage, and maintenance status of all your equipment and tools by leveraging cost-efficient and practical QR codes.
These QR code tags are attached to assets you want to track, and their locations and users are monitored by scanning the QR code with a smartphone or tablet.
The same principle can be applied to material management, enabling more precise allocation and real-time management of materials and components extracted from the material takeoff.
In conclusion, the adoption of digital takeoff solutions significantly enhances accuracy, speed, and collaboration in material takeoff processes.
This lays a foundation for more precise project planning, efficient resource allocation, and, ultimately, the successful execution of construction projects.
Conclusion
We’ll close this article with a few key takeaways.
First, mastering the art of material takeoffs is pivotal for precise project planning and successful execution of the construction phase.
Second, it’s evident that technology, such as advanced takeoff software and other construction management tools, is reshaping the construction landscape.
As we stride into a digital era, embracing these solutions not only streamlines the takeoff processes we described but also ensures accurate cost estimations and efficient resource management.
Therefore, you should consider integrating technology into your workflows for enhanced efficiency and superior project outcomes.