Every business that relies on equipment to complete projects and turn a profit has to engage in some form of equipment tracking.
This process involves tracking the location, usage, and maintenance schedules of the items in question, and there are different methods you can rely on to conduct it.
However, no matter the method, if done correctly, equipment tracking offers numerous benefits to your business.
On the other hand, equipment tracking does come with an occasional bump in the road as well, so in this article, we’ll cover its drawbacks as well as its advantages.
Let’s start with the positives.
In this article...
The Pros
Equipment tracking is an important component of asset management and a necessary practice for any company looking to boost its productivity.
Let’s get into some of the ways equipment tracking can improve your business.
Increases the Utilization of Construction Equipment
Your equipment is a significant investment, so it’s only natural you want to maximize its value by keeping it as active as possible.
Seeing that the total cost of ownership (TCO) does not include only the price you paid for a piece of equipment, but also the maintenance, storage, transport, fuel, and labor costs, it does make sense to use the piece frequently to drive down its cost.
Still, equipment idle time cannot always be avoided. Sometimes, equipment is no longer needed for a project, or it requires significant repairs before it can be used again.
In other instances, workers simply forget about a particular piece among a great deal of other machinery at their disposal.
Although sometimes unavoidable, you should always look for ways to reduce idle time because it negatively affects your equipment and overall profitability in many ways.
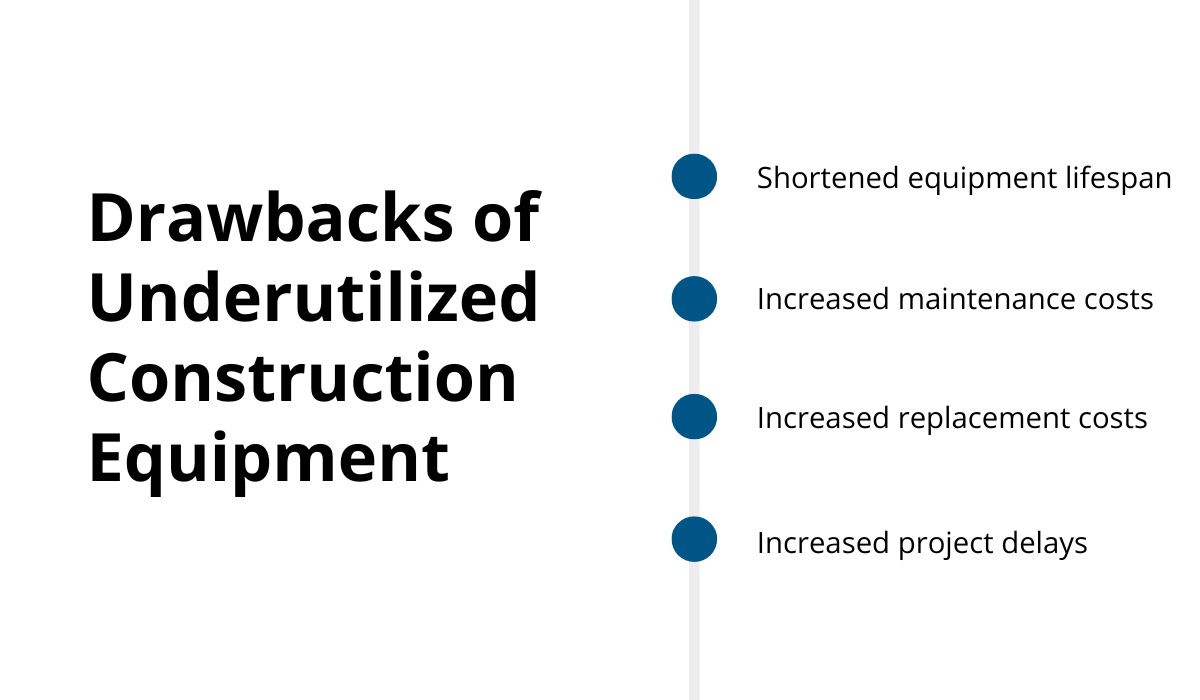
In essence, underutilized equipment generates more costs than profit.
It requires more frequent maintenance, thus increasing maintenance costs and shortening the equipment’s lifespan.
In turn, the equipment needs to be replaced more often, meaning that the replacement costs also rise.
And while you spend time on equipment maintenance and replacement, workers struggle to meet the deadlines since now there aren’t enough resources at hand for timely project completion.
Needless to say, such a decrease in productivity impacts your profits and reputation.
Equipment tracking is a perfect remedy for this kind of problem.
Why?
Because it provides you with the data necessary for effective equipment allocation.
In other words, you get an insight into which equipment performs as it should, as well as the areas that might need a boost in productivity.
Here are some metrics to take into consideration when tracking equipment utilization.
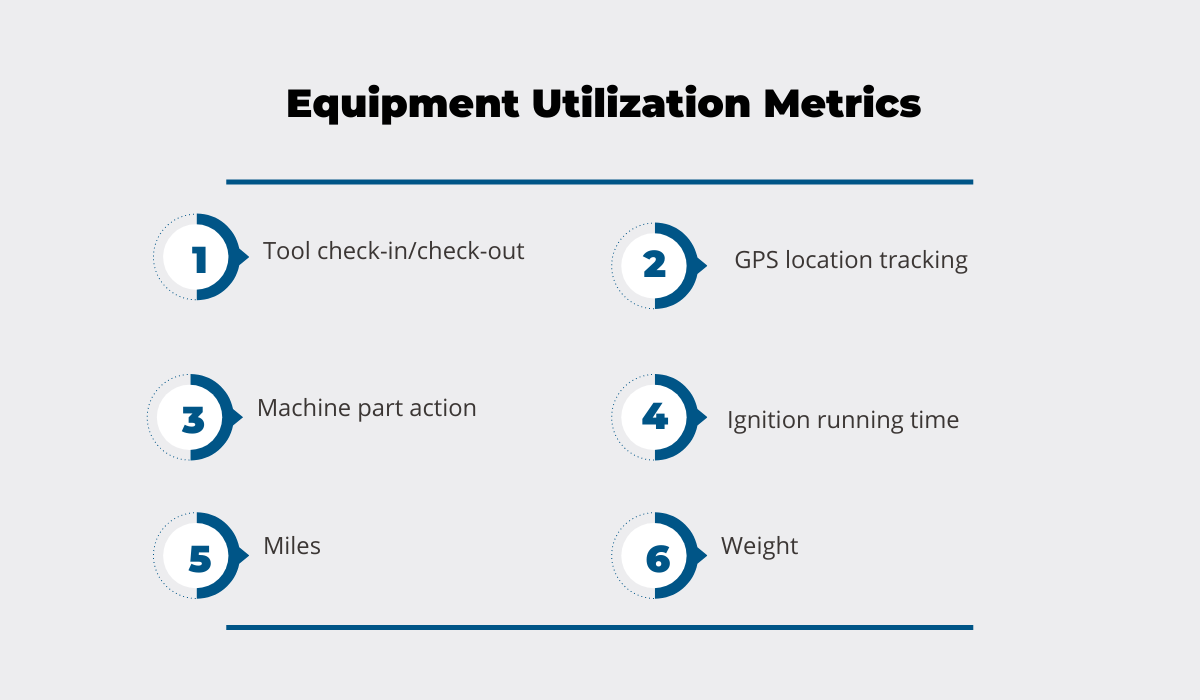
By paying attention to these utilization elements, it’s very likely you’ll start to notice that some equipment is not being adequately utilized.
Based on these observations, you can move that equipment to a job site where it might be of more use at the moment.
All in all, maximizing the utilization of your equipment is virtually impossible without equipment tracking.
You need to know how your equipment is currently performing and what can be done for it to do even better in order to make the most of it.
Reduces the Cost of Equipment Maintenance
Equipment maintenance is essential in construction, and looking for ways to improve this part of your operations could considerably boost your profitability in the long run.
What this means is that, essentially, you should be strategic about how you approach equipment maintenance instead of just fixing when something’s already broken.
One of the ways to do it is to schedule your maintenance during planned downtime.
This is called preventive maintenance, and it’s much cheaper and more effective than the reactive approach.
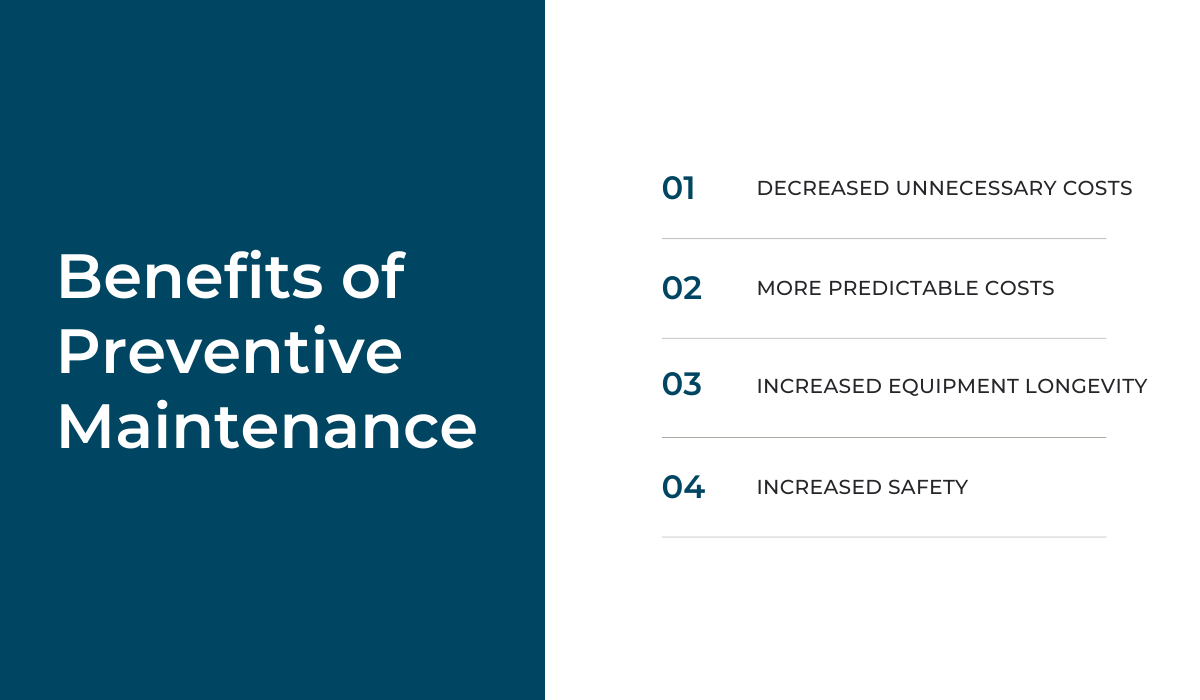
Preventive maintenance makes for more reliable equipment, which in turn results in more predictable maintenance expenses.
And since equipment breaks down less frequently, unplanned maintenance costs and downtime, as well as unnecessary project delays, are all reduced.
Well-maintained equipment also directly translates to increased equipment longevity, which contributes to reduced replacement and disposal costs.
Preventive maintenance is a great money saver all around.
In fact, according to a seminal study conducted by the researchers at the University of Nebraska, improving your preventive maintenance can reduce the costs of repairing heavy machinery by a staggering 25%.
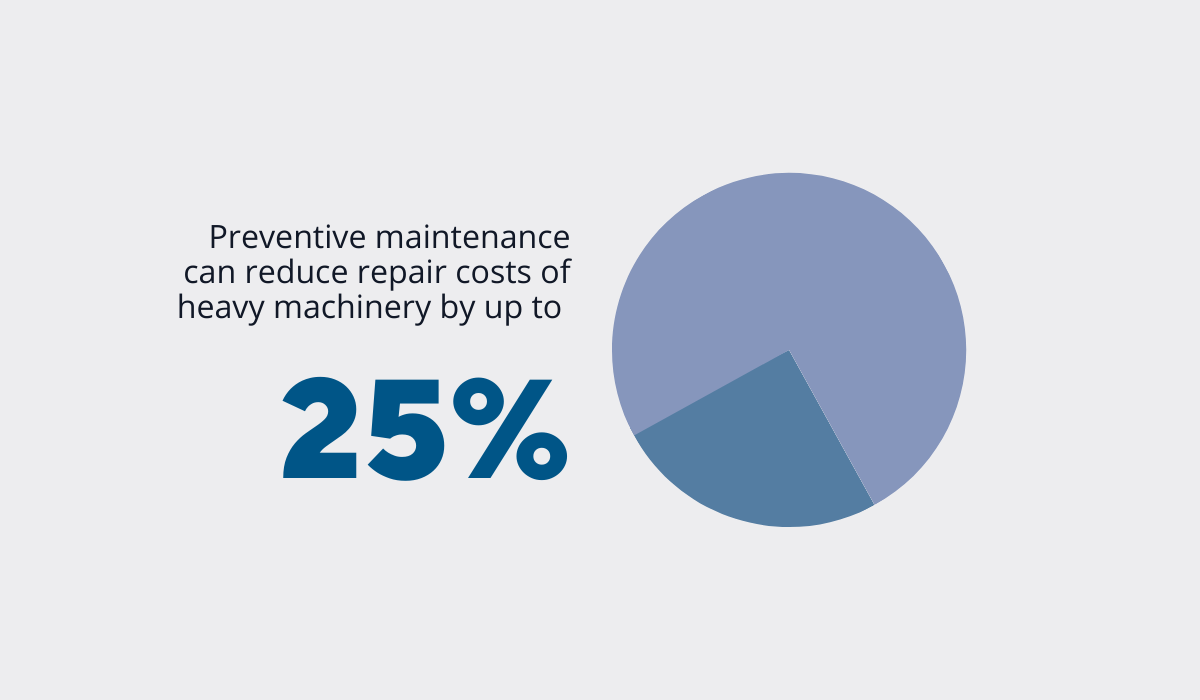
Of course, in order to know when to schedule maintenance, it’s important to track how and when your equipment is used, and monitor maintenance history so you can plan future upkeep accordingly.
Moreover, there are many equipment tracking systems that take your maintenance one step further with their many useful features.
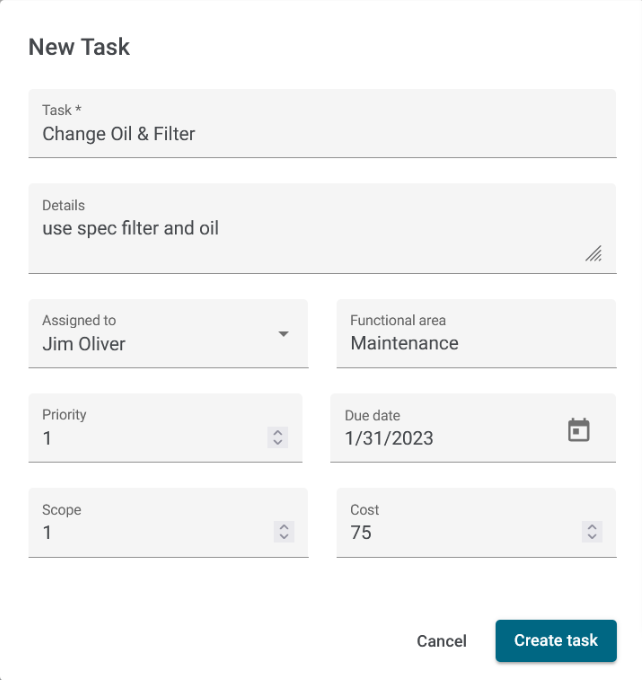
For instance, the tasks feature, which allows you to assign tasks to different employees, set due dates, and make updates, is a great tool for reducing miscommunication-related errors.
With this feature, everyone knows who’s supposed to do what, so there’s no room for confusion or unnecessary arguments.
Another useful feature to look for is the notifications feature. It will serve as a reminder for scheduled service and ensure that you’re always on top of your equipment maintenance.
And that is something to strive for if you’re looking to cut down on unnecessary costs.
Decreases the Risk of Equipment Theft
Theft is a serious issue in the construction industry, with a significant negative impact on both the financial and operational side of the business.
It probably goes without saying, but stolen equipment is yet another major cause of project delays and a huge profitability killer.
In fact, it’s estimated that theft costs the construction industry up to $1 billion annually.
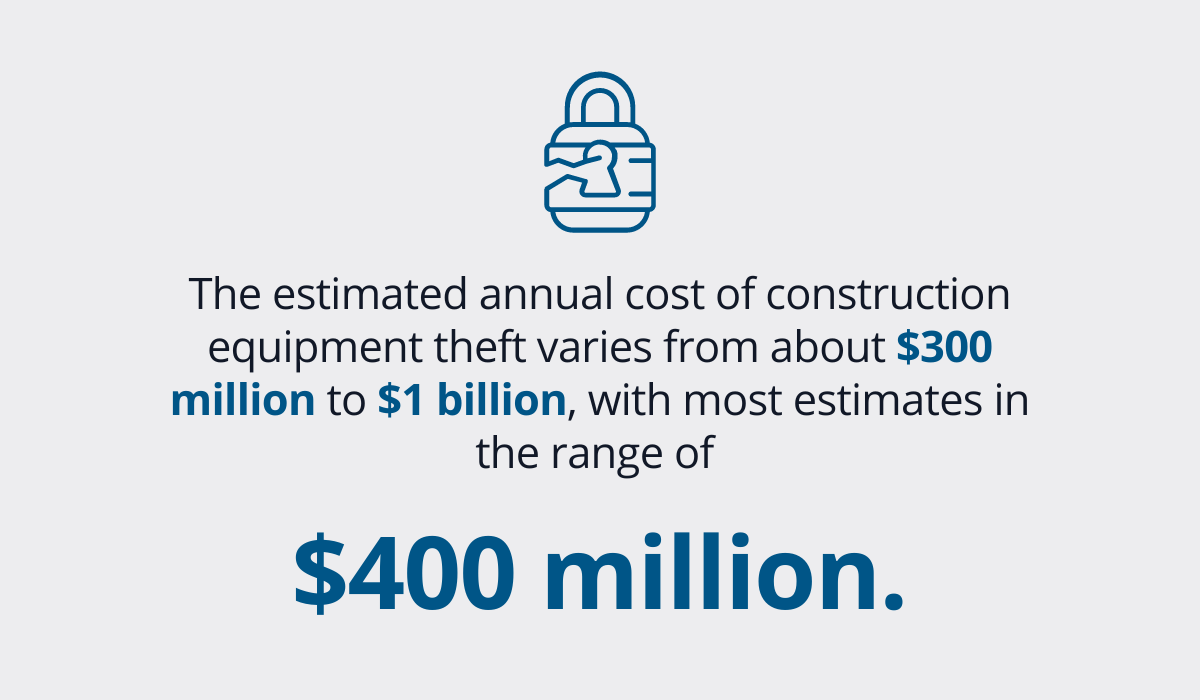
So naturally, it’s something you’ll want to avoid.
The reasons for construction equipment theft are many, but the lack of efficient equipment tracking is certainly one of them.
Therefore, give equipment tracking software a thought or two. They are super effective in decreasing the risk of theft.
Equipment tracking software like GoCodes Asset Tracking relies on QR code labels and tags.
When attached to equipment and scanned with a scanner app, they can be used to access and update different information about the equipment, including its location.

Therefore, in case of theft, you’ll have the asset’s last known location at hand, increasing the chances of retrieval.
And then, when the asset is found, asset tags and labels serve as proof of ownership.
But tags do even more than that.
They often prevent crime from happening in the first place because they indicate to the thieves that the equipment is being tracked, making them move on to easier targets.
Moreover, the newest high-tech addition to GoCodes Asset Tracking’ tracking solution—Bluetooth beacons—takes theft prevention even further by sending out alerts when the beacon is removed from within the range of the app.
Overall, there are so many modern location tracking solutions available today that there’s really no excuse for having an inefficient theft prevention system in place.
If you’re having problems with theft, or missing equipment in general, consider tagging your equipment and tracking its locations with equipment tracking software.
Hardly anything can be hidden from it.
The Cons
Naturally, equipment tracking doesn’t come without some challenges.
In the following sections, we’ll be explaining what these are, but also how to prevent, or at least mitigate, the drawbacks inherent to equipment tracking.
Might Cause Resistance From Employees
When a company relies on a lot of assets for project completion, equipment tracking can increase overall productivity and profitability and help solve many of the issues a company faces in its day-to-day operations.
However, you won’t be able to enjoy any of the benefits of the equipment tracking software if your team is not on board with it.
Workers resisting new technology is a big problem across all industries, but especially the construction industry.
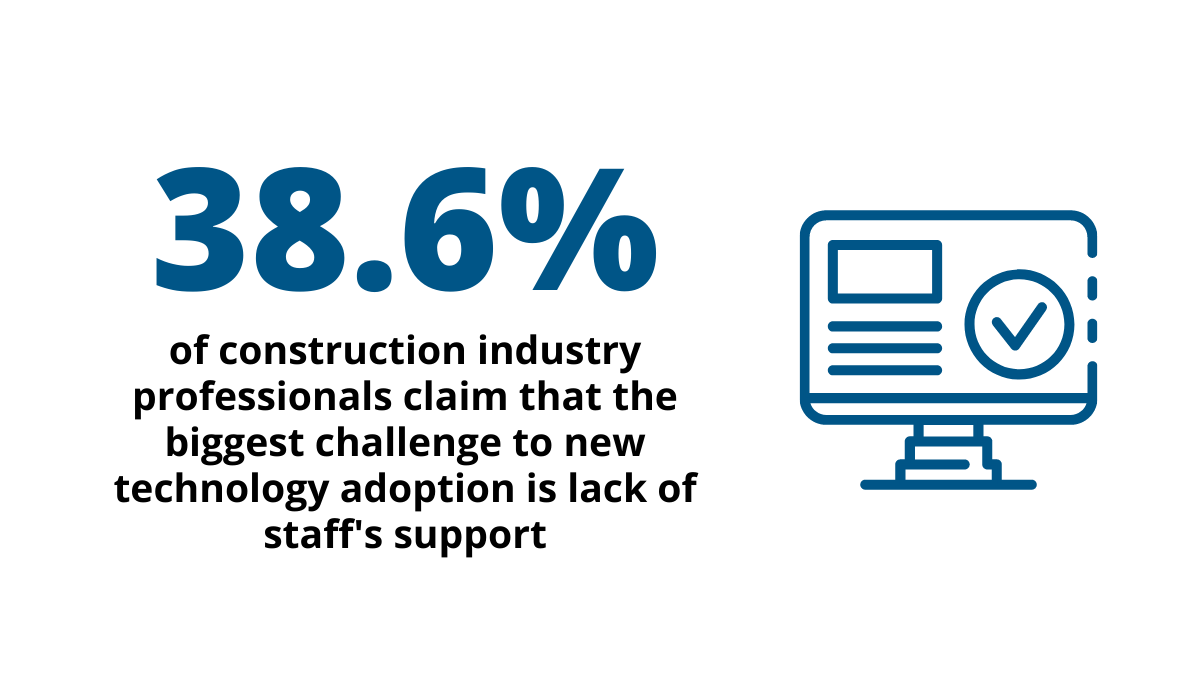
Whether it’s due to a lack of curiosity, trust, or skill, workers often tend to resist the new and the unknown.
Therefore, it’s up to you to show them that technology is not here to take away their jobs or complicate their lives but, on the contrary, to help.
The best way to do that is, of course, by choosing software that is easy to use, even for less tech-savvy employees.
But how can you know what software is like before you purchase it and start using it yourself?
One way to find out whether the software is worth buying or not is to read other people’s reviews, especially from professionals in your industry, or a similar one.

Check out websites like G2 and Capterra, where you can find great and detailed reviews. They’ll surely be of help to you during your research.
Another way to get a feel of particular software is by requesting a free demo or trial to try out the software for yourself. After all, nothing beats first-hand experience.
Employees Need to Be Properly Trained
Still, no matter how intuitive your software is, it will still require some degree of employee training. After all, this is a brand new system that’ll cause changes in everyone’s day-to-day.
So, let’s take a look at some tips for new software training.
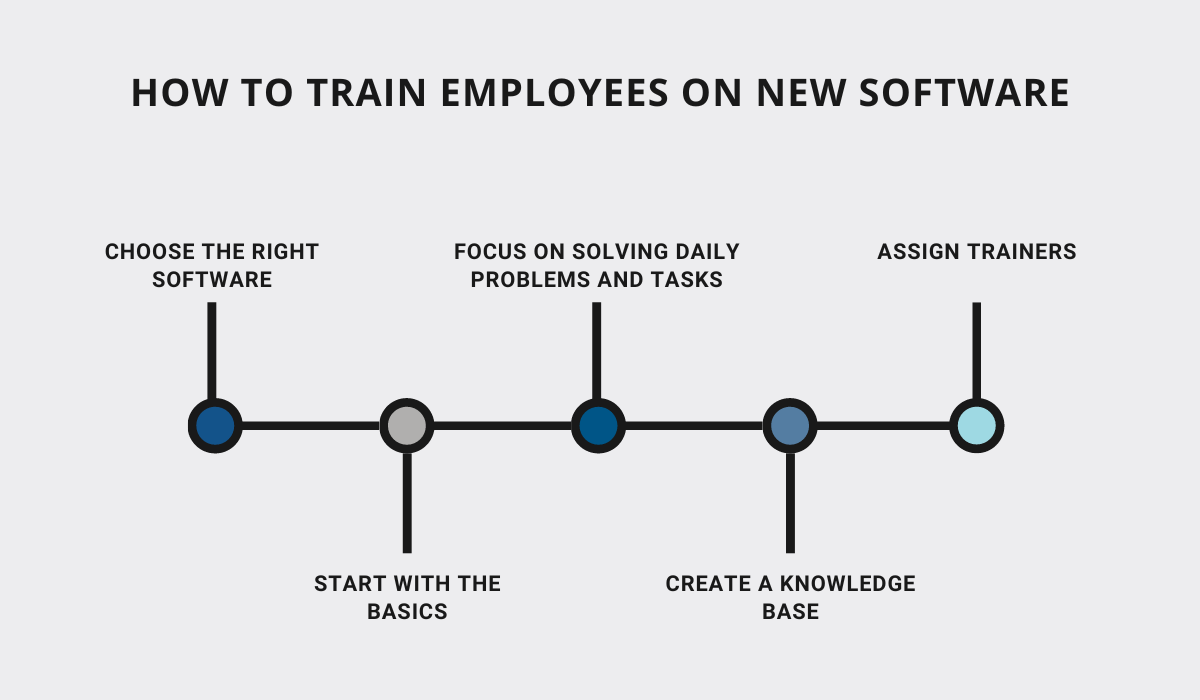
As you can see, we’ve already covered the first step in the previous section. However, picking the right software doesn’t only mean choosing the most user-friendly one.
The ideal software will also provide good customer support and include learning materials, such as, for example, how-to videos.
Moreover, definitely avoid trying to teach your team everything in a single day. Instead, ease into it and focus on solving the problems they deal with most frequently.
Show the employees, for instance, how to check in and check out a tool they need by using the app scanner on the equipment tags. Then you can move on to more advanced features.
And even if the software vendor does provide learning materials, consider creating a knowledge base of your own and centering it around your own specific daily tasks.
This will be a reliable source of data workers can go back to at any time.
Finally, provide employees who are struggling with the right mentors. These can be other team members who are more well-versed in technology.
However, keep in mind that, along with proficiency, those providing the information need to be armed with patience too.
Equipment Tracking Software Might Crash
Depending on what kind of software you use, the technology itself can represent another challenge of equipment tracking.
To elaborate, equipment tracking solutions can either be on-premise or cloud-based.
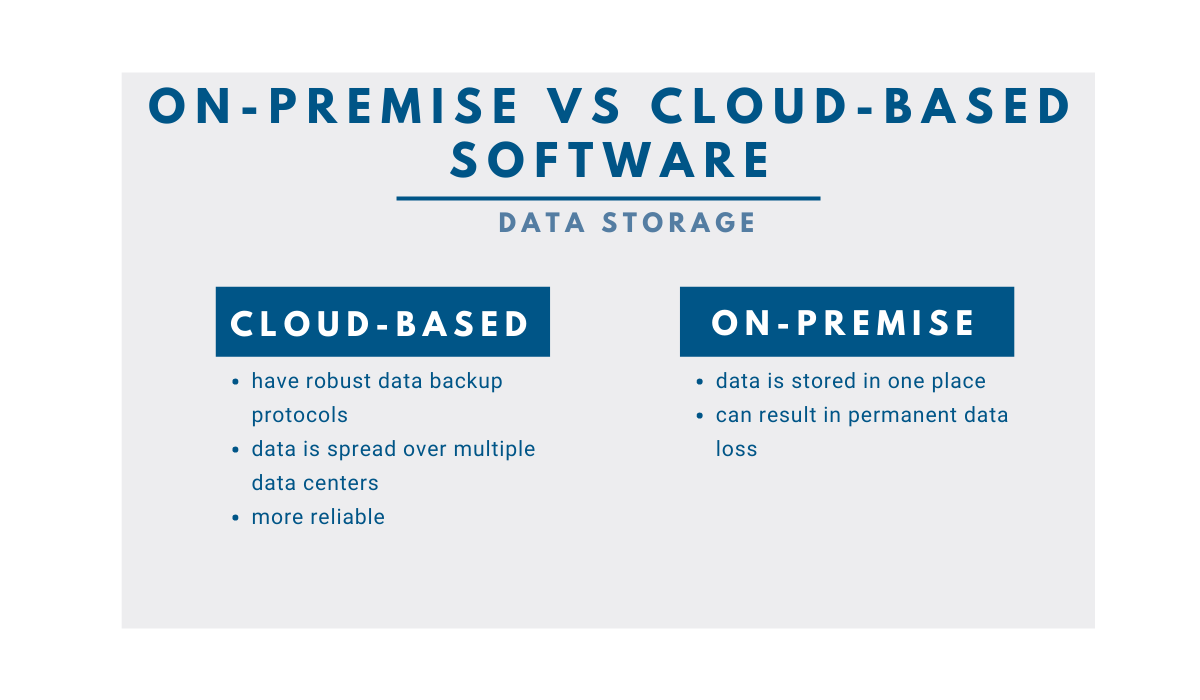
The main difference between the two is their location.
On-premise software runs on your hardware infrastructure and is hosted locally, while cloud-based systems are on the software provider’s system and are accessed via a web browser or other interface.
What does that mean in terms of reliability and data loss?
Cloud-based software relies on servers in multiple locations, which means if one of these servers goes down, another can replace it with little to no downtime.
On-premise software, on the other hand, stores all of the data in one place.
Therefore, in case of hardware failure of any kind, theft, fire, or any other calamity, you can potentially lose all your data, at least if you don’t have any backup.
Meanwhile, with cloud-based software, your data is safely stored in the cloud and can be accessed by you or your team anyplace and anytime.
Therefore, while browsing for equipment tracking solutions, make sure to pay attention to whether particular software is cloud-based.
This is a much more reliable solution in terms of data storage.
Conclusion
In conclusion, equipment tracking is an indispensable tool for improving business operations on different fronts.
It ensures your assets are properly utilized and protected while simultaneously reducing unnecessary costs.
On the other hand, there’s no denying that this process can be challenging at times.
It does take time for employees to get used to a new solution, and starting to implement it carries some risk of data loss.
Luckily, with the right equipment tracking software, many, if not all, of these issues can be prevented.
Therefore, make sure you do proper research and choose the right option for you. You’ll see results in no time.