Although one might think being a construction equipment manager is a relatively straightforward job, this role—when done properly—involves many responsibilities that require a broad range of both technical and people skills.
So, if you’re a construction company owner or manager looking to hire a great equipment manager internally or externally, you’ll find the information in this article useful.
The same is true if you’re an experienced equipment manager looking for a technologically updated refresher, or a novice just starting on the job and eager to learn more.
Without further ado, here are the six key responsibilities of every construction equipment manager.
In this article...
Knowing Whether to Purchase or Rent
Understanding when and what construction equipment should be purchased or rented is a pivotal responsibility for an equipment manager.
Construction companies typically decide to purchase, own, and maintain core equipment and tools that will be frequently used over extended periods, ensuring operational control and long-term cost-effectiveness.
On the other hand, for specialized equipment required on a project-by-project basis, renting equipment provides flexibility and cost savings, avoiding the financial commitment of ownership.
Therefore, equipment managers should discern when it’s more cost-efficient to rent equipment and when it might be time to buy it due to, for instance, planned frequent use on future construction projects.
Moreover, when high-value heavy equipment is concerned, the manager should consider external and internal factors that might steer the company’s decision towards renting, as shown below.
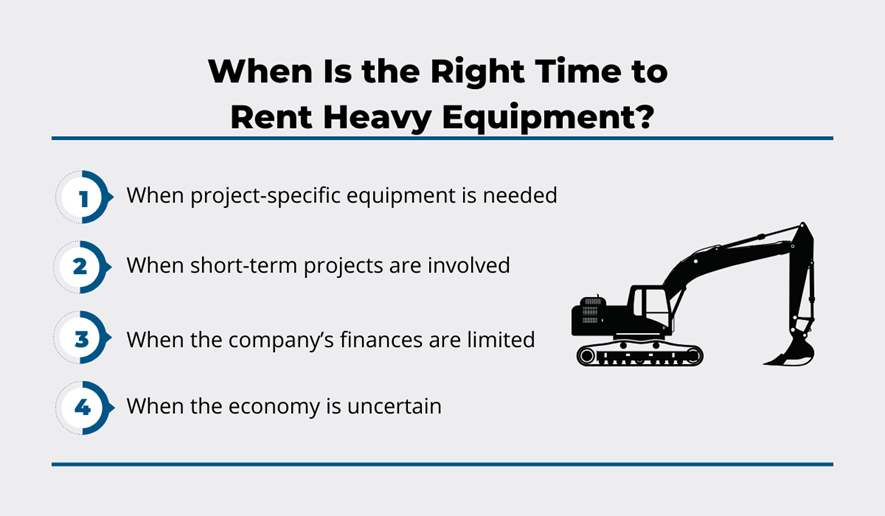
Given just these general considerations, it’s clear that the equipment manager’s role often involves a strategic balancing act to align the company’s financial goals with project demands.
For instance, a specific earthmoving machine needed for a short-term project is an ideal candidate for renting, while a specialized concrete saw might be best purchased for frequent use.
To be able to make (or more often assist company management in making) informed buy-or-rent decisions, the equipment manager should:
- keep an accurate inventory of all owned equipment, their condition, and usage,
- conduct relevant cost-benefit rent vs. buy analyses considering various factors,
- analyze project timelines and workloads to determine the optimal duration and frequency of equipment use,
- maintain relationships with equipment vendors to stay informed about purchasing and rental options, pricing structures, and industry trends,
- collaborate with project managers to forecast equipment needs for upcoming projects, and
- help management and accounting determine equipment budgets and rates for owned and potentially purchased/rented equipment.
Needless to say, these are all ongoing processes with constantly changing parameters, and the resulting decisions can significantly impact a construction company’s profitability and operational efficiency.
Considering all the other responsibilities of equipment managers, it’s clear that knowing whether to purchase or rent equipment and when to do so is just one, albeit very important, aspect of their multifaceted role in construction companies.
Keeping Track of the Equipment
Purchase-or-rent considerations aside, the equipment manager’s primary responsibility is to ensure that workers have all the equipment and tools needed to do their jobs safely and efficiently.
This includes making sure these assets are well-maintained and available, i.e., not misplaced or stolen.
Hence, one of their key duties is to keep track of what equipment a company owns, where that equipment is, and who is using it.
Moreover, they should track all equipment inspections, regular maintenance, and repairs, monitor equipment-related inventory (spare parts, accessories, and other supplies), and manage equipment availability and allocation, often in real time.
So, how does an equipment manager track and document all these processes without being overwhelmed?
In today’s world, the answer is technology, specifically equipment management software like GoCodes Asset Tracking.
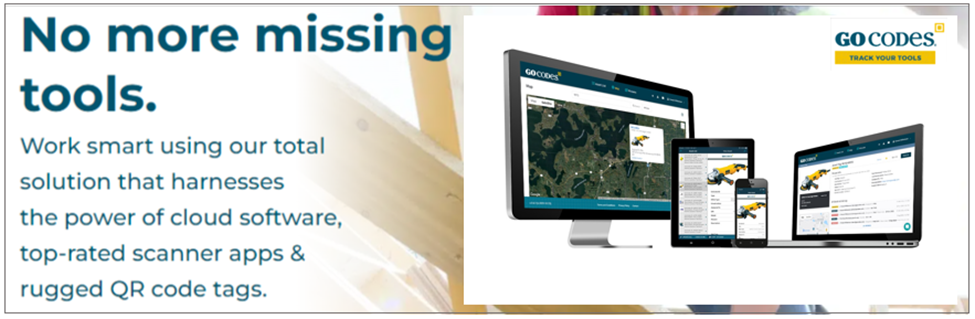
As listed above, the GoCodes Asset Tracking package includes:
- customizable QR code labels attached to equipment and tools,
- cloud software available on any internet-connected device, and
- an in-app scanner to scan QR code labels/tags with smartphones or tablets.
After a quick system setup, (labels attached to assets and the software’s database populated with initial data), equipment managers can access the central list of all tracked equipment and tools on their phone or computer at any time.
At the same time, workers can scan the equipment’s QR code with their smartphone or tablet to quickly access that equipment’s info page and the central database.
This simple and quick process is shown below.
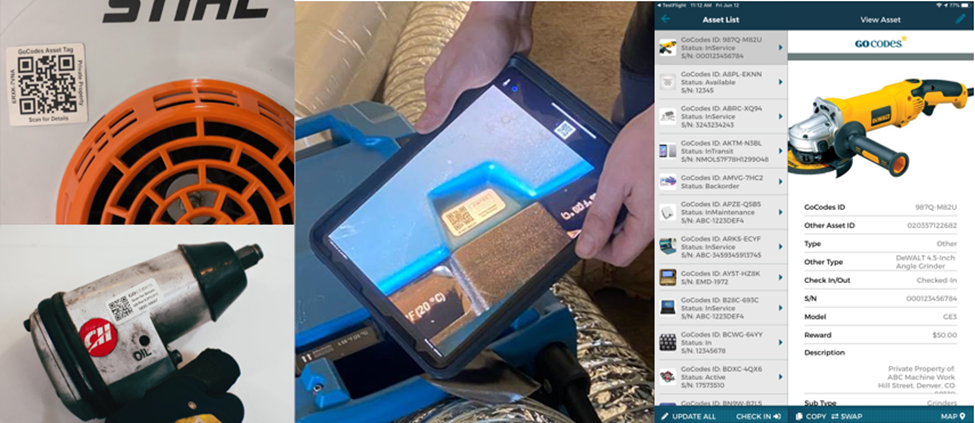
In other words, the system enables both workers and managers to easily view and update all the data we mentioned, such as recording details of performed equipment inspections, maintenance, and repairs, or checking equipment availability.
Best of all, every time a QR code is scanned, the software automatically records who scanned it and uses the scanning device’s GPS function to capture the equipment’s current location and show it on a map.
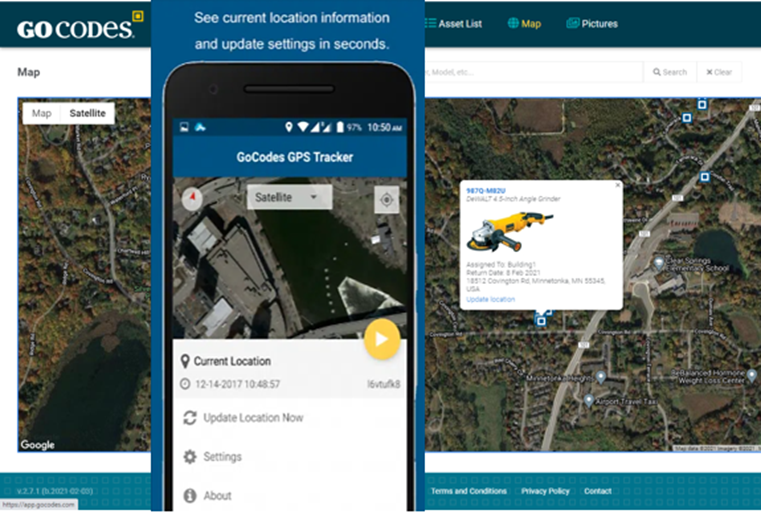
That way, the equipment manager can track who is using the equipment and where that equipment is (based on the last-scanned location), thus benefiting from real-time insights.
Concurrently, the scan-based GPS tracking and QR codes themselves act as additional theft prevention measures, boosting job site security and minimizing theft or loss.
Compared to manual, spreadsheet-based tracking methods, this simple and easy-to-use system revolutionizes the equipment manager’s job, allowing them to digitize, automate, organize, and track all equipment management workflows.
Implementing a Check-In and Check-Out System
The next key task on the equipment manager’s list of responsibilities is to implement an equipment check-in/check-out system.
In other words, to be able to efficiently manage equipment and tools spread across multiple work crews and job sites, they need to keep track of who is using them and when.
Before equipment management software, this typically involved cumbersome pen-and-paper logs or intricate spreadsheets prone to errors, delays, and inefficiencies.
Conversely, adopting a cloud-based asset tracking software solution such as the one we described above enables equipment managers to establish an automated check-in/check-out system, thus relieving them from the above manual and time-consuming duties.
For instance, workers can now access the app on their phone or another device, and search the database to find out if a specific equipment or tool is available with no involvement by the equipment manager.
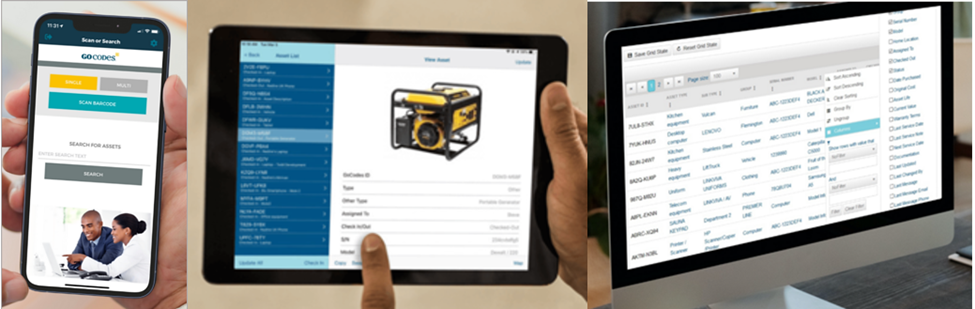
Using the app, they can reserve the equipment they need, and pick it up when it’s time to use it.
Likewise, when checking out the equipment, the worker—alone or supervised—simply needs to scan the QR code and repeat the process when checking it back in, and the system will record it.
Similarly, the manager can assign equipment to specific workers or work crews in advance and add a return date that will trigger an email reminder notifying them it’s time to return it.
Suffice it to say, when properly implemented, this automated system generates many benefits that make the equipment manager’s job much easier, such as the following:
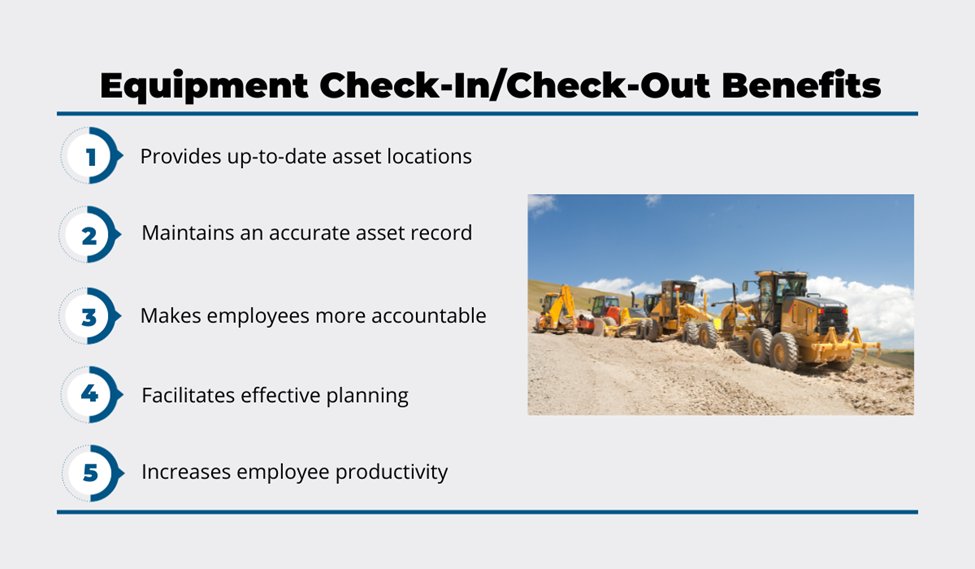
For example, such a system increases worker accountability, thus minimizing theft, misplacement, and negligent handling of tools and equipment.
Simultaneously, repeated QR code tag scans lead to frequently updated asset locations, providing real-time asset visibility, which enables better planning and improves overall productivity.
All in all, implementing a check-in/check-out system used to be a complex and time-consuming task fraught with errors, but nowadays, any equipment manager can automate and streamline this process with the help of equipment management software.
Planning Equipment Maintenance
Naturally, one of the crucial aspects of the equipment manager’s job is maintenance.
In other words, managers are responsible for ensuring that all equipment and tools are regularly maintained and, if they break down or get damaged, timely repaired to prevent potential work disruptions, project delays, and budget overruns.
Therefore, their maintenance-related duties include a multitude of planning, scheduling, tracking, and monitoring tasks related to:
- implementing routine inspections and preventive maintenance programs,
- promptly addressing equipment breakdowns and overseeing part replacement,
- maintaining detailed records of all maintenance activities,
- ensuring equipment compliance with industry regulations and safety standards, and
- budgeting funds for planned maintenance and unforeseen repairs.
When all these processes are managed manually, performing this range of tasks efficiently is almost impossible, especially for one person.
And that’s again equipment management software provides invaluable assistance, particularly if its maintenance-related features include:
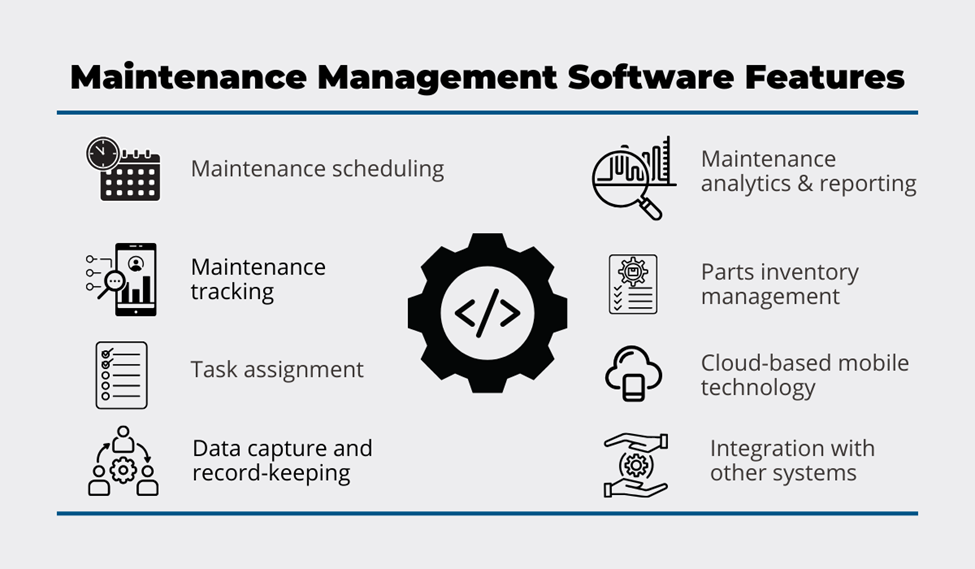
Empowered by these features, equipment managers can set up maintenance schedules based on usage, manufacturer recommendations, or specific project requirements.
Moreover, the software can be easily instructed to send timely reminders for scheduled maintenance tasks, ensuring that critical activities, such as oil or filter changes, are never overlooked.
Additionally, managers can access detailed logs of past inspections, repairs, and part replacements, enabling data-driven decisions about equipment conditions and predicting potential issues.
To recap, ensuring efficient regular and emergency maintenance of equipment and tools is another key responsibility of equipment managers that can be streamlined by leveraging software.
Providing Employee Training
The role of equipment managers extends beyond overseeing just physical assets like heavy equipment, vehicles, and tools.
In other words, equipment managers are tasked with developing and implementing training programs that educate staff on the proper operation, maintenance, and safety protocols related to the equipment they handle.
Naturally, this also helps ensure that construction equipment and tools comply with health and safety regulations issued by the U.S. Occupational Safety and Health Administration (OSHA):
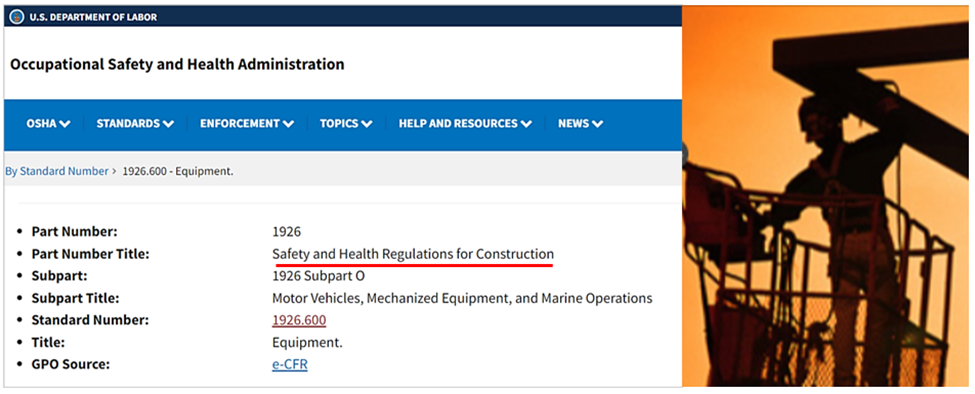
Therefore, the equipment manager’s duties may involve conducting regular training sessions, creating informative materials, and integrating new equipment models and technologies into training modules.
Additionally, equipment managers are responsible for fostering a safety-first culture within the company and emphasizing adherence to protocols, thereby minimizing the risk of accidents and injuries, and enhancing operational efficiency.
In summary, employee training is another important aspect of the equipment manager’s job that shouldn’t be neglected and also requires good presentation and communication skills.
Ensuring Team Communication
Given their diverse responsibilities, a pivotal aspect of the equipment manager’s role is to ensure effective team communication, at least in matters related to equipment management.
For example, they regularly communicate with:
- project managers to forecast equipment needs,
- executive and accounting teams to inform their operational and budgeting decisions,
- various work crews and subcontractors to track equipment usage, and
- equipment and parts suppliers to stay informed about availability and prices.
These communication channels are crucial for effective equipment management, ensuring that all stakeholders are properly and timely informed.
Naturally, today’s equipment managers should be able to utilize different communication methods and technologies to streamline and document their interactions, such as those automated notifications we mentioned.
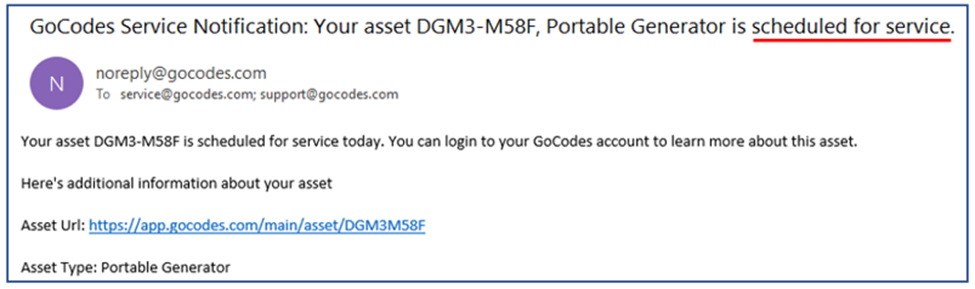
These e-mail reminders are a great example of how equipment managers can utilize software to automate and document their communication, which saves them time and ensures a digital trail in case of mix-ups.
The same applies to communication involving equipment scheduling and allocation, maintenance requests and ensuing work orders, and other equipment-related task assignments.
In essence, by ensuring effective team communication, the equipment manager can help synchronize construction operations, optimize resource allocation, and foster a cohesive workflow across different facets of equipment management.
Conclusion
So, we covered the six key responsibilities of every equipment manager, ranging from knowing when to purchase or rent equipment and tracking equipment locations, users, utilization, and maintenance to ensuring proper employee training and enhancing team communication.
Given the broad range of tasks under their responsibility, it’s clear that a great equipment manager should have relevant technical expertise and experience, while also being adept at using new technologies and providing efficient training and communication.
Ultimately, finding the right person (and software) for the job can bring order and efficiency to your construction equipment management, allowing you to minimize equipment theft and loss, improve maintenance, increase productivity, and reduce costs.