The construction industry heavily relies on equipment. To do their job effectively, workers use a variety of items, from power tools to heavy machinery, and often in less-than-ideal conditions.
Any time a piece of equipment gets damaged, displays signs of imminent failure, or stops working altogether, a work order for maintenance is created, so that the proper measures can be taken to get it up and running again.
A system for tracking those work orders will help your company manage equipment maintenance more efficiently.
The boost in efficiency will have positive effects on employee productivity and safety compliance, and result in a host of other benefits.
So, let’s take a look at some of the top reasons you should track work orders for equipment maintenance.
In this article...
Improved Planning Capabilities
Tracking work orders for equipment maintenance can improve your construction company’s planning capabilities.
Here’s how.
There are different kinds of work orders, but they generally fall into one of the following categories:
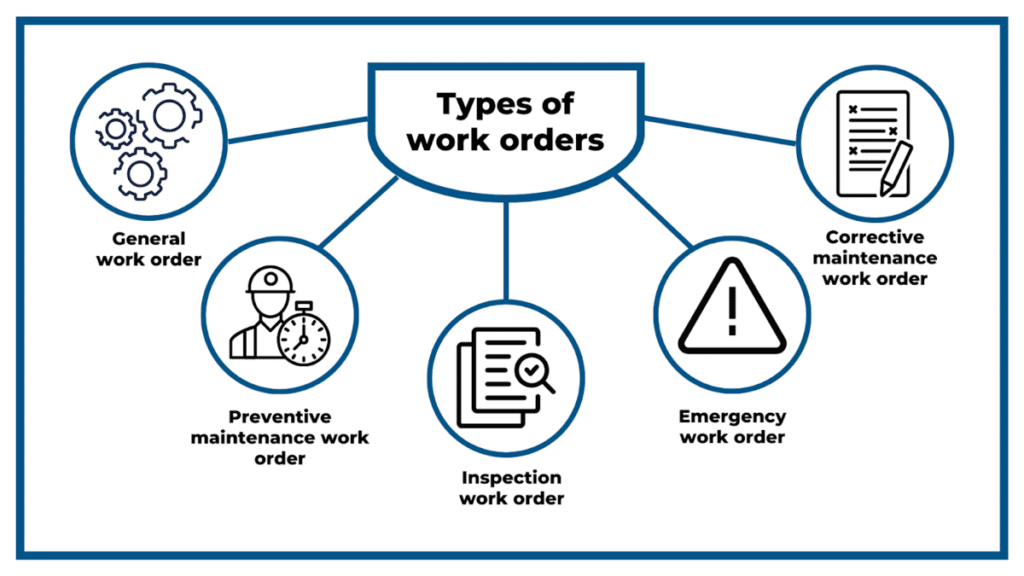
Preventive maintenance and inspection work orders are done at regular intervals, while the other three are used to resolve specific issues as they arise.
If you track all of those work orders, you will have an easier time managing and prioritizing them, as well as planning maintenance dates that are most convenient for the company.
For example, emergency work orders should take precedence over all the other types, as they ensure that construction continues smoothly after an unplanned malfunction.
On the other hand, inspection work orders should be timed for when the equipment is not being used.
After all, equipment downtime is inevitable when a piece is being maintained, so you should make sure that it is scheduled at a time that has the least impact on your work processes.
Tracking work orders also helps construction companies with budget planning and inventory control.
Without it, you may lose sight of when you are going to need certain replacement parts so you can order them in advance.
As a result, your workers may find themselves having to wait an excessive amount of time until it’s their turn to use a piece of equipment they need.
You may also have to place unplanned emergency orders for certain items, which could lead to overfilling the inventory or parts not being delivered on time.
However, with work order tracking, you will have an overview of all the parts needed for various maintenance work, as well as the dates they will be needed.
This means you can plan future maintenance-related expenses according to your budget and maintenance schedule.
By doing this, you will avoid purchasing parts you don’t need and reduce the number of unused ones that have to be returned, thereby freeing up space in your inventory.
In conclusion, tracking work orders will allow you to make a more efficient maintenance schedule, along with helping you with budget allocation and inventory management.
Lower Risk of Equipment Failure
By tracking work orders for equipment maintenance, you will minimize the risk of equipment failure.
Generally, most people understand maintenance as reactive, which means equipment being repaired after an unforeseen breakdown.
However, when equipment malfunctions suddenly, it can cause long downtimes, project delays and cost overruns.
As researchers Qing Fan and Hong Qin Fan state in their paper on failure prediction of construction equipment:
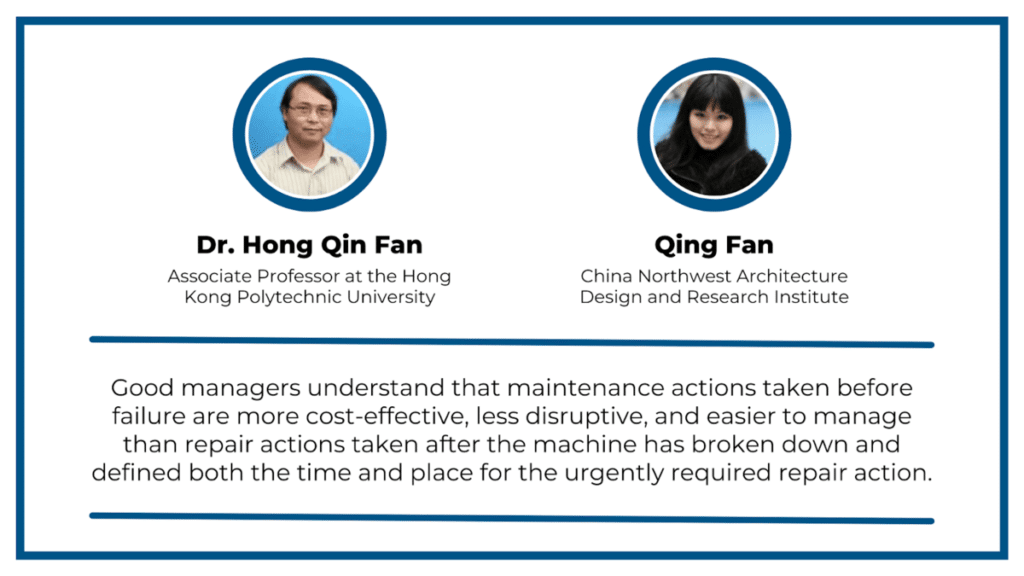
That is why the majority of maintenance is or should be arranged in advance as a preventive measure so that unexpected equipment failures do not occur in the first place.
A work order tracking system ensures that all inspections and preventive maintenance get done on schedule.
This way, if potentially critical problems with equipment exist, they are noticed in time to take corrective action.
An effective system also helps you prioritize equipment that shows warning signs of machine failure.
Waiting for other, less urgent issues to be resolved first could lead to unnecessary breakdowns in the field.
Furthermore, tracking work orders means keeping records of equipment failures, including what caused them and when.
Analyzing this data makes it easier to predict and prevent future issues with the same or similar piece of equipment, as well as decide whether to replace a particular item and when.
Keeping track of the breakdown types and frequency can also help build a more effective preventive maintenance schedule.
To sum up, a work order tracking system allows your company to perform preventive maintenance on time and keep records of past issues, thereby lowering the risk of unexpected equipment failure.
Extended Equipment Lifespan
Tracking work orders can also help extend equipment lifespan.
Every piece of equipment has an expiration date.
A widely cited life cycle study on excavators, wheel loaders and dozers conducted by the Construction Equipment Magazine found that half of them last under 10,000 hours, with only 20% surviving more than 12,000 hours.
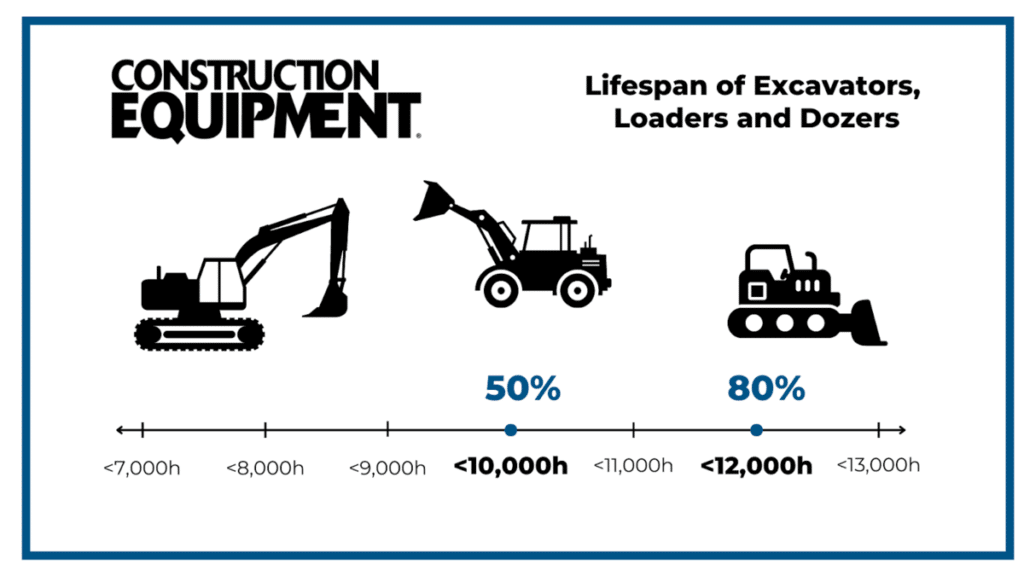
The study also found a correlation between reducing the risk of failure and rigorous maintenance.
And proper maintenance doesn’t just mean replacing a machine’s broken or non-functional parts.
As we mentioned, inspection and preventive work orders are just as—if not more—important for your equipment’s health.
For example, for equipment to stay in optimal working order, it is crucial that it remains properly lubricated.
Hydraulic fluids, oils and coolants should be kept at the correct level and changed regularly to avoid contaminating the engine.
Also, machines should be cleaned to stop dirt and debris from entering the system, and regular inspections can identify and report any potential problems with the equipment.
Tracking working orders gives you a list of all maintenance done on a piece of equipment, as well as the condition of its many different parts.
An overview of service times and past issues of an asset makes it easy to see what kind of work is being over- or underperformed and what parts may cause problems in the future.
Addressing these issues in a timely and productive manner will help your equipment stay in working shape for longer, cutting costs and optimizing workflow.
You can also analyze how different approaches to maintenance affect your equipment’s long-term effectiveness.
If you find your equipment lasting less than expected, you can modify your strategy until you find one that produces optimal results.
All in all, work orders should be tracked to ensure equipment is regularly inspected and serviced, which keeps it in healthy working condition and extends its lifespan.
Improved Safety Compliance
You should also track work orders for equipment maintenance to improve safety compliance in the workplace.
In any business that carries the potential for serious injury, the safety of the workers should be a top priority.
This is especially true in construction.
According to the National Safety Council, a public service organization promoting health and safety in the US, the construction sector experienced the largest number of preventable deaths in both 2020 and 2021.
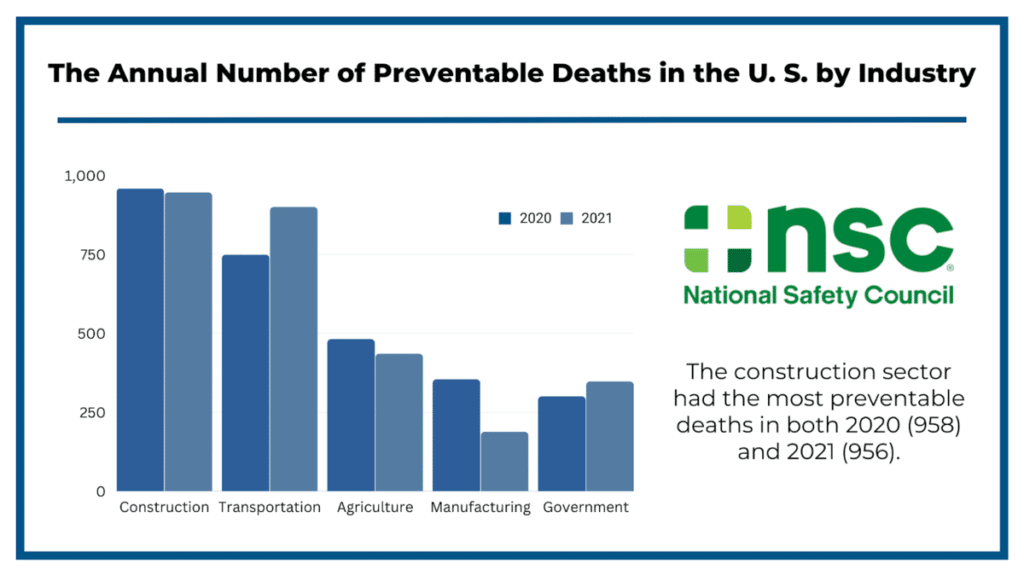
This information is hardly surprising given that construction involves a lot of large machinery that carries heavy objects in the close vicinity of other workers.
To curb the risk of injury, it is crucial to set up and abide by safety standards and protocols.
One of them is regularly servicing potentially hazardous equipment, like heavy machinery and vehicles.
As mentioned, tracking work orders goes a long way in helping you keep a tight and well-rounded service schedule.
If structured correctly, it should minimize the possibility of equipment malfunctioning in situations that could prove to be dangerous for employees on the construction site.
Furthermore, to stay compliant, construction companies have to pass safety audits, which are performed by a third party on a semi-regular basis.
When work orders are tracked, it creates a detailed backlog of maintenance activities across all of the company’s assets.
That means auditors won’t have to go through a ton of paperwork, making their job a lot easier.
Your company will also benefit from this, as audits will take much less time from your work schedule.
To sum up, work order tracking helps keep equipment from malfunctioning and injuring workers, and it makes safety audits easier, all of which leads to improved safety compliance in your company.
Increased Employee Productivity
Lastly, you should track work orders for equipment maintenance because doing so helps boost employee productivity.
Construction companies usually have several maintenance workers who work on more than one piece of equipment simultaneously.
If their workload isn’t properly managed, some workers could end up underutilized, with no equipment to maintain, or with more than they can handle, leading to delays.
In any case, your company would effectively be losing money.
With a centralized system in place, all work orders are categorized based on priority. Every task is assigned to a particular employee and tracked in real time.
Workers will know exactly what kind of work is required of them, and when they are expected to perform it.
This means you will have a more productive workplace.
As the global management consulting firm McKinsey & Company says in an article outlining the effect of new technologies on businesses:
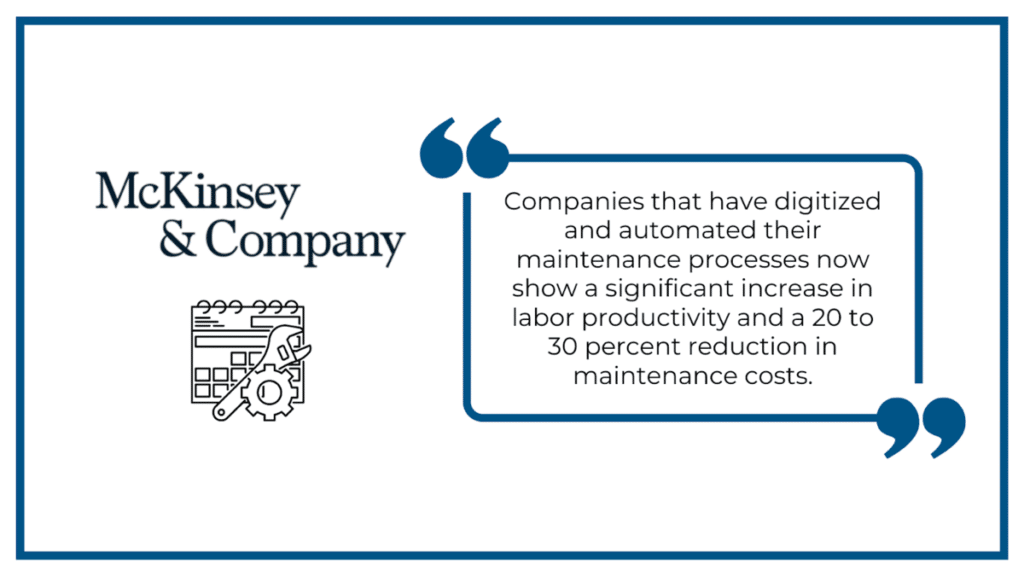
One of the ways to automate maintenance processes for employees is to use the GoCodes Asset Tracking task feature.
Companies can use the intuitive interface to allocate specific tasks, in this case, maintenance work orders, to specific employees.
By logging into their GoCodes Asset Tracking account and checking under “My Tasks”, workers can view all working orders that have been assigned to them.
This will include pertinent information like the type of maintenance, a list of required parts, and due dates for completion.
When the task is finished, employees can simply mark it as complete and move on to the next one.
Ultimately, tracking work orders will provide your employees with a clearer picture of their work schedule, allowing them to spend less time idling and more time being productive.
Conclusion
Construction companies have to balance many moving parts, all of which are important for them to stay operational and profitable.
Because of this momentum, it is sometimes difficult to decide when to slow down to make changes to the system, as well as determine which components need upgrading.
However, as shown in this article, tracking work orders is a simple adjustment that will take a short time to execute and offer many long-lasting benefits, which is why you should consider implementing it in your business.