As technology progresses, construction companies use increasingly sophisticated and valuable assets, such as vehicles, heavy equipment, and tools, to complete their construction projects on time, within budget, and to the client’s satisfaction.
However, this also presents them with the challenge of tracking and managing these construction assets to ensure their optimal use, reduce costs, and improve their overall construction operations.
Luckily, as technology evolves, so do asset-tracking methods, and we’ll explore six of them in this article.
So, if you want to find out which asset-tracking methods are available and how to choose which would best fit your specific needs and budget, keep reading.
In this article...
Using Barcodes
Despite some limitations, barcodes can be a simple and low-cost way for construction companies to track their assets.
Before we look at barcodes more closely, it should be noted that, nowadays, all the asset-tracking technologies described in this article typically include tracking devices that are attached to assets, along with readers or scanners for data collection, and tracking software for asset management.
When combined, these elements enable companies to track (often in real time) and manage their construction assets, analyze data, generate reports, set alerts, and access the data remotely.
In the case of barcodes, asset labels can be scanned with dedicated handheld scanners or a scanner app downloaded to workers’ smartphones and other compatible devices.
Now, let’s first quickly cover what barcodes are and then discuss how construction companies use them.
Barcodes, those parallel vertical black lines scanned at checkout counters, have been with us for almost 50 years.
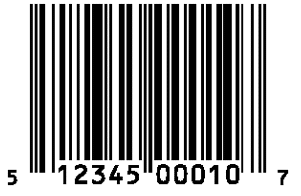
In fact, barcodes were invented even earlier, but the first barcode scanner was used in 1974.
Since then, barcodes have taken over the world, as companies started printing them on products as a means of quick identification that accelerates the purchasing process, tracks inventory, and assists in accounting.
As for construction companies, they would attach barcode labels to assets they want to track and would scan them using barcode readers connected to an inventory list of equipment, tools, and materials.
In their basic form, barcodes have some downsides, like being easily damaged, requiring a direct line of sight for scanning, and having limited data capacity.
Additionally, before the internet and mobile devices came along, the system could be operated only by workers with a barcode reader and connection to the database, such as warehouse/equipment managers and staff.
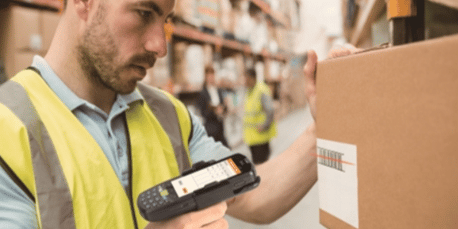
However, this is no longer the case.
Most of the aforementioned limitations can be overcome when barcodes are combined with cloud software and a barcode scanner on your smartphone or tablet.
Likewise, more durable label materials can help barcodes stay intact and readable in harsh jobsite conditions.
Still, construction companies mostly use them in warehousing operations or tracking small tools and stationary or seldom-moved equipment.
Overall, using barcodes can be a simple and cost-efficient way to track construction assets, especially when coupled with more advanced features such as an online database and scanner apps on mobile devices.
Using Quick Response Codes
Quick response (QR) codes are a two-dimensional form of barcodes that can store more information and be instantly read by smartphones and other mobile devices.
Similar to barcodes, QR code tags are attached to assets and, when scanned, enable the user to access information about the asset stored in the tracking software’s database.
However, compared to barcodes, QR codes are more easily read by devices and can also store more complex and detailed information (even offline) than barcodes, making them more versatile and interactive.
QR codes were invented in 1994 in Japan and were primarily used in the automotive industry.
Since then, they have crossed over to many different industries, including marketing and retail, providing customers instant access to various information such as website links, product details, and contact information.
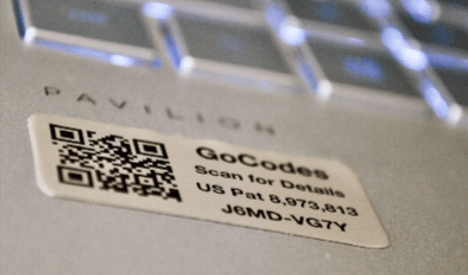
In construction, companies usually use them to track the usage and maintenance of assets like power tools, mid-sized equipment, and other items of value.
However, when QR code tags on assets are scanned with a device that knows its own GPS location (e.g., a smartphone), the asset-tracking software can automatically update their location and show it on a map.
This allows construction companies to track their assets in near real time, i.e., see where the asset was when it was last scanned.
For example, our asset-tracking solution, GoCodes, offers customizable QR code asset tags made from durable materials that companies can use to track the location, usage, and maintenance of their tools and equipment.
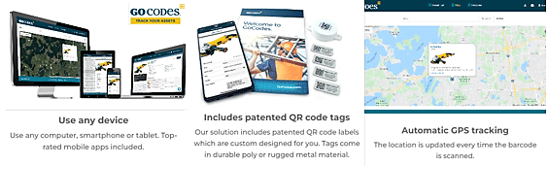
As you can see, this easy-to-use and affordable solution comes with patented QR code tags and a mobile app, allowing workers to view and update the asset’s information as needed.
Compared to barcodes, QR codes can be printed/etched directly onto an asset for enhanced durability, read by the scanning device even when damaged, and also provide much more information when offline (for instance, on remote jobsites with no reception).
Overall, QR codes are an advanced form of barcodes that can, in conjunction with tracking software, be used to cost-effectively track construction assets, including their GPS location.
Using Radio Frequency Identification
As its name suggests, radio frequency identification (RFID) is a technology that uses radio signals to track all tagged assets on a construction site (or at a warehouse).
RFID tracking systems consist of passive or active RFID tags with antennas and handheld or fixed RFID readers.
Generally smaller in size, passive RFID tags do not have their own power source, meaning they need to be activated (powered) by a radio signal sent by the RFID reader to transmit the data stored on them.
Conversely, somewhat larger active RFID tags are usually battery-powered and can transmit their signal to the RFID reader at a greater distance.
Therefore, the reading range of this tracking technology will depend on the type and frequency of the RFID system used, the size of a tag’s antenna, and the range of a specific reader model.
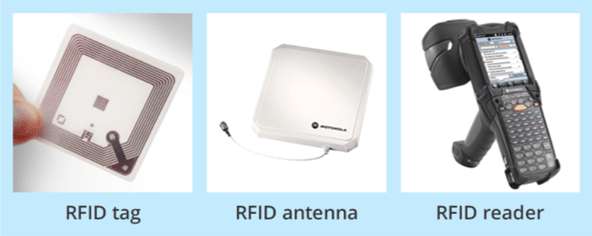
Generally, passive tags can be read from a distance of several feet, while active tags can have a range of several hundred feet, depending on the environment in which they’re used.
As for the advantages of this technology, RFID readers require no line of sight for reading tags and provide data in real time and at longer distances than barcodes and QR codes.
The downsides of using RFID for asset tracking include interference with radio signals (for example, the presence of metal in the working environment), limited read range, and cost.
In other words, the price for RFID tags and readers can quickly add up, and the cost of replacing lost or damaged tags can also be a factor.
To quote ScienceSoft:
Prices for RFID tags range from 5 cents to $10 per item. The price of RFID readers (together with installation and configuration) can go to as much as $3,000 to $20,000 depending on the reader type.
Therefore, construction companies should carefully consider their specific needs and weigh the benefits and costs of using RFID as an asset-tracking solution.
Overall, RFID tracking does have several advantages compared to barcodes and QR codes, such as requiring no direct line of sight and having extended range, but it also has several downsides, such as high cost, limited read range, and interference.
Using Near-Field Communication
Although near-field communication (NFC) can be used for tracking construction assets, it’s still not as commonly used for asset tracking as other technologies listed here, but it can be used for access control and information purposes.
This RFID-derived technology allows wireless two-way communication between an NFC tag and reader at a very short range, typically a few inches.
The most well-known examples of NFC use are contactless payments made by credit cards or different apps, such as Apple Pay and Google Pay, and access control, such as unlocking doors with an NFC-enabled key card or phone.
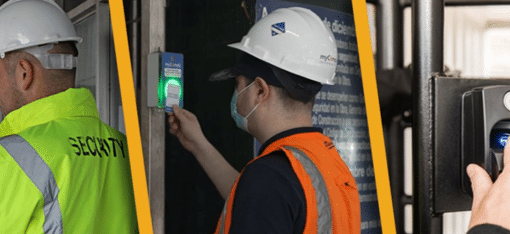
NFC tags can also take the user to an online asset-tracking platform where they can access more information about the asset, such as its usage and maintenance records.
Moreover, when an NFC tag is scanned with a device that is both NFC and GPS-enabled (usually a smartphone), the tracking software can update the asset’s GPS location, thus enabling construction managers to track the movement of assets on-site.
However, as we noted, NFC tags are still not commonly used for tracking construction assets, mainly due to their much shorter range.
Nevertheless, some tool manufacturers use them to complement their asset-tracking technology.
For instance, Milwaukee uses NFC tags on their trackers that allow users to rapidly scan and easily log an asset into the digital inventory, which is then tracked by their solution, One-Key, which uses Bluetooth technology.
We discuss that technology in the following section.
Overall, although NFC can be used for tracking construction assets, its extremely short read range makes it better suited for other purposes, such as jobsite entry control and accessing asset information.
Using Bluetooth Low Energy
Bluetooth Low Energy (BLE) can be a relatively low-cost, low-maintenance solution that provides precise real-time tracking of construction assets, particularly indoors.
BLE uses radio waves to communicate via the same frequency bands as Wi-Fi and similar technologies.
The tracking system uses BLE-enabled devices (smartphone or tablet) and/or standalone BLE readers to record the information transmitted by BLE asset tags.
BLE asset tags (beacons) are small devices with built-in long-lasting batteries designed to consume less power than traditional Bluetooth (hence the “Low Energy” part of Bluetooth Low Energy).
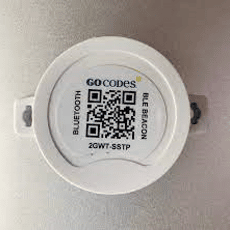
After they’re attached to assets, these beacons transmit information at regular intervals, typically every second, and BLE-enabled devices and readers can pick up that information if the asset is within about 300 feet from them.
When that happens, they automatically record the beacon’s information and signal strength, which the tracking software then uses to determine the precise location of an asset.
However, to make this information accessible to multiple users, a central (cloud-based) server is often used to collect and store the data from BLE beacons, which users then access via the asset-tracking app on their mobile devices.
The advantages of using BLE are:
- accurate tracking of assets in real time
- low power consumption
- low implementation costs
Conversely, one downside of BLE technology is its limited range.
This is usually not a problem indoors, where the range can be extended by strategically placing BLE readers or using more of them.
However, it can be a challenge outdoors, where walls, buildings, and other obstacles may prevent an optimal distribution of BLE readers.
Another BLE downside is potential interference caused by other wireless signals, such as Wi-Fi.
Despite these limitations, BLE can be a good choice for construction companies looking for a low-cost, low-maintenance, and accurate solution for tracking assets in real time.
Using the Global Positioning System
Using the Global Positioning System (GPS) for tracking assets gives construction companies the widest possible tracking range among all the asset-tracking technologies, along with a highly accurate determination of the asset’s location and real-time updates.
However, this tracking technology has some drawbacks, primarily its cost, so it’s usually used for tracking vehicles, heavy equipment, and other high-value items that are always on the move.
Simply put, GPS trackers are placed in assets to be tracked, and they use signals from satellites in the Earth’s orbit to determine their own location.
When the tracker calculates the asset’s location and time, it sends that information to the tracking software, which displays it on a map on your desktop or mobile device.
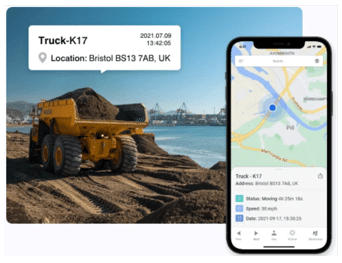
Since the GPS covers the entire globe, it allows construction companies to track their assets over long distances in real time.
This feature also makes GPS an ideal navigation system, which companies use to plan the most efficient driving routes, reduce fuel costs, and save time.
As said, the main drawback of using GPS for tracking all construction assets is its cost, i.e., the price of GPS trackers, including installation costs, and the subscription for ongoing GPS tracking service.
These costs make GPS one of the more expensive tracking options available.
Despite the cost, it’s still extensively used for tracking construction vehicles and heavy machinery, as well as some other high-value items, such as generators and air compressors.
That’s because the benefits that construction companies get from GPS tracking in terms of efficient fleet management, theft protection, and reduced insurance, fuel, and maintenance costs (to name just a few) can far outweigh the cost.
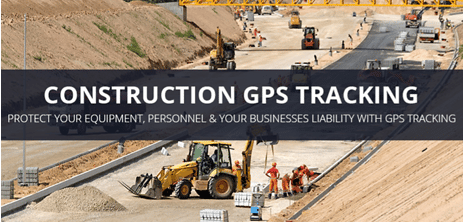
However, since it’s satellite-based, another GPS limitation is not working underground and indoors, i.e., where GPS signals are weak or blocked.
That’s where other tracking technologies we mentioned come in, such as BLE and RFID.
Outdoors, GPS signals can be obstructed by mountains, tall buildings, or even trees, resulting in less accurate location data or signal loss.
Overall, despite some limitations, GPS is the most accurate real-time tracking technology ideal for tracking large movable assets of high value over large distances.
Conclusion
Now that we’ve covered six asset-tracking technologies, it’s clear that construction companies should choose the right combination of tracking methods that best fits their specific needs and budget.
With the appropriate tracking solutions in place, construction companies can track and manage their valuable assets to ensure optimal use, reduce operating costs, and improve their overall construction management.