Equipment is a crucial part of doing business in the construction industry.
Of course, workers come first, as they are the ones who use the tools or operate machines and vehicles.
However, to a large extent, the success or failure of a construction project depends on the performance of the equipment.
If your company owns assets that are underperforming or often suffer failures, you can be facing project delays and cost overruns, not to mention reputational damage.
Luckily, good maintenance practices are all you need to avoid that outcome, and equipment inspections are a big part of effective maintenance.
Read on to learn about the importance of equipment inspections and the reasons they make a solid addition to your equipment management strategy.
In this article...
Lower Risk of Equipment Failure
Firstly, performing regular equipment inspections can help you lower the risk of equipment failure.
Unexpected breakdowns are the worst-case scenario for any piece of equipment, particularly heavy machinery.
When a critical failure occurs, the machine has to be hauled off the site, which requires time and manpower.
Then, maintenance workers have to take time off their regular tasks and do a thorough check to see which parts were affected by the breakdown.
In most cases of critical damage, parts have to be replaced. Until the new parts arrive, the machine stays out of order.
MacAllister Machinery, Indiana’s leading construction and heavy equipment dealer, lists these as the top reasons for heavy equipment breaking down:
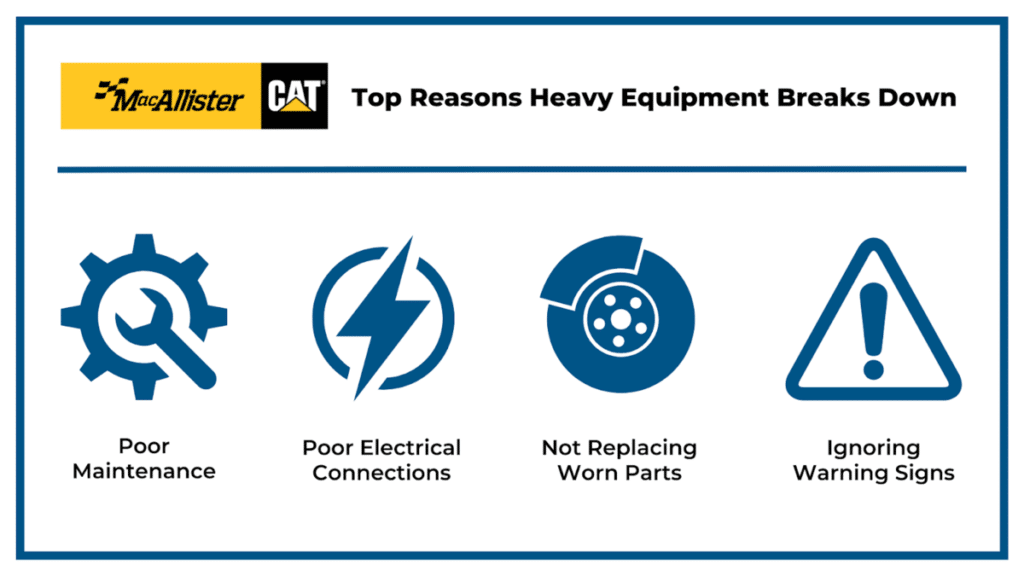
The good news is that most of these can be prevented by regularly inspecting equipment for signs of potential issues.
After all, construction equipment is very durable and made to work in tough conditions.
That means that most of it has a failure developing period (FDP), or the time before the breakdown when problems can be spotted and fixed without them causing critical harm to the machine.
Effective inspection routines are developed with FDP in mind, so that equipment is ideally always kept in working condition.
Therefore, the parts that allow for the shortest FDP—in other words, that can lead to a breakdown the fastest—are inspected most often, with some requiring daily attention.
Here is a daily heavy machinery inspection checklist suggested by MacAllister Machinery:
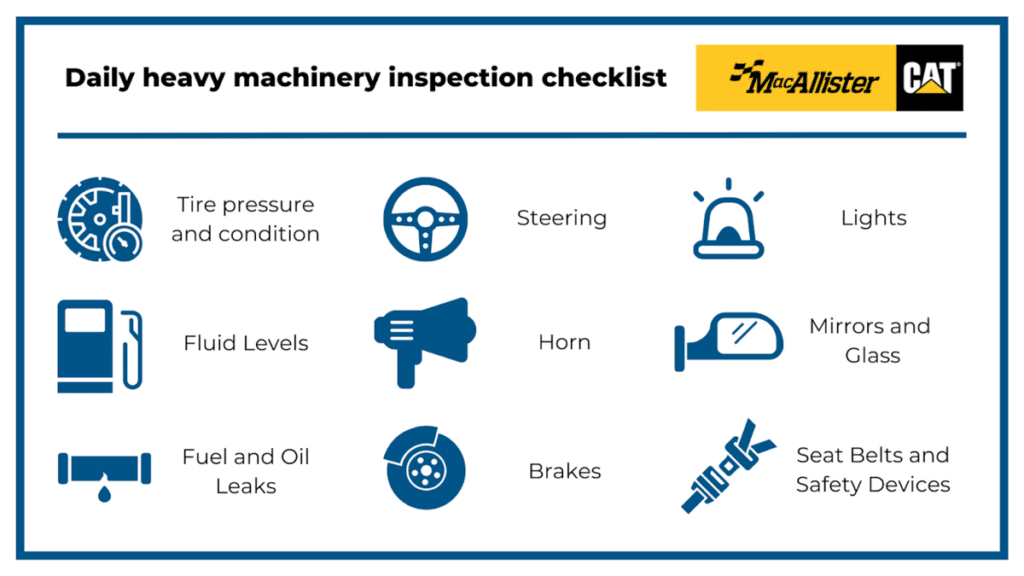
Some of these checks, such as lights and mirrors, are done mainly for safety reasons.
Others, like fluid levels, can have a significant impact on how the machine operates.
For example, a machine that isn’t lubricated properly can have parts of it jam up, causing the machine to strain and eventually break down.
In conclusion, regular inspections provide a chance to detect and remedy problems with the equipment before they escalate, which decreases the risk of breakdowns in the field.
Reduced Unplanned Downtime
By lowering the risk of unexpected failure, equipment inspections also reduce unplanned downtime.
In construction, downtime can be defined as a period of ongoing production during which a piece of equipment is not working.
Scheduled repairs or preventive maintenance fall under planned downtime, which is part of regular proceedings and does not negatively affect the workflow.
On the other hand, unplanned downtime occurs when a piece of equipment breaks down unexpectedly.
Because construction projects depend on large machinery, this can end up in production shutting down until a replacement has been found.
Equipment repairs after a critical failure are expensive and time-consuming, but this indirect impact on production can be even more damaging.
Here’s what Dan Corbett, equipment manager at Lancaster Development, who manages a fleet of over 500 assets, has to say about it:
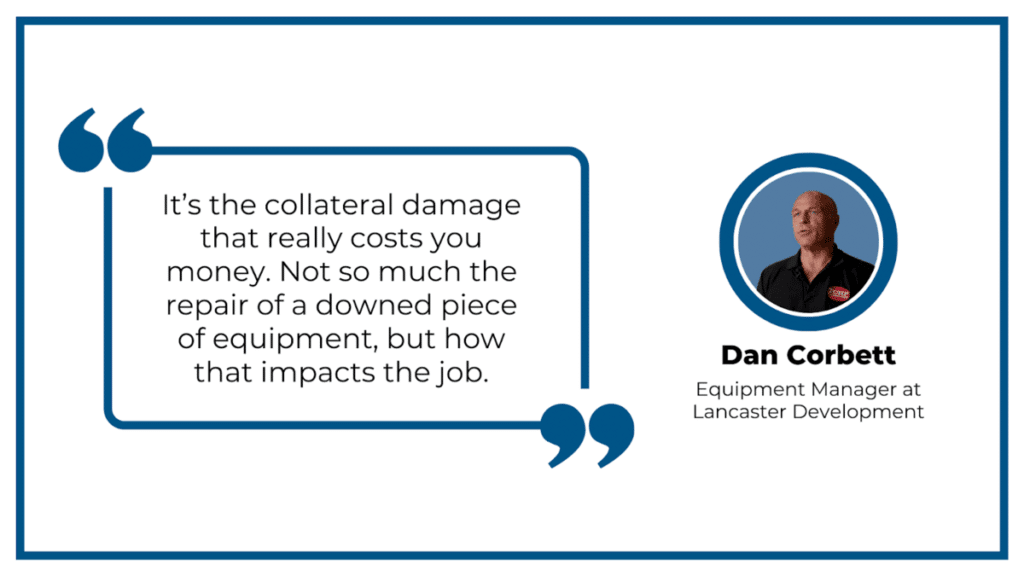
He considers production stoppages, idle employees and the costs of renting equipment replacements as the collateral damage in question.
With regular equipment inspections, issues that lead to critical failure can be identified and resolved on time.
This way, you can avoid all adverse consequences related to unplanned downtime, making for a more productive and profitable construction project.
To help with scheduling equipment inspections, consider using GoCodes Asset Tracking’ task feature.
When creating an inspection task for maintenance, you can pick the time and date a certain task needs to be performed at, as well as assign specific employees to specific pieces of equipment.
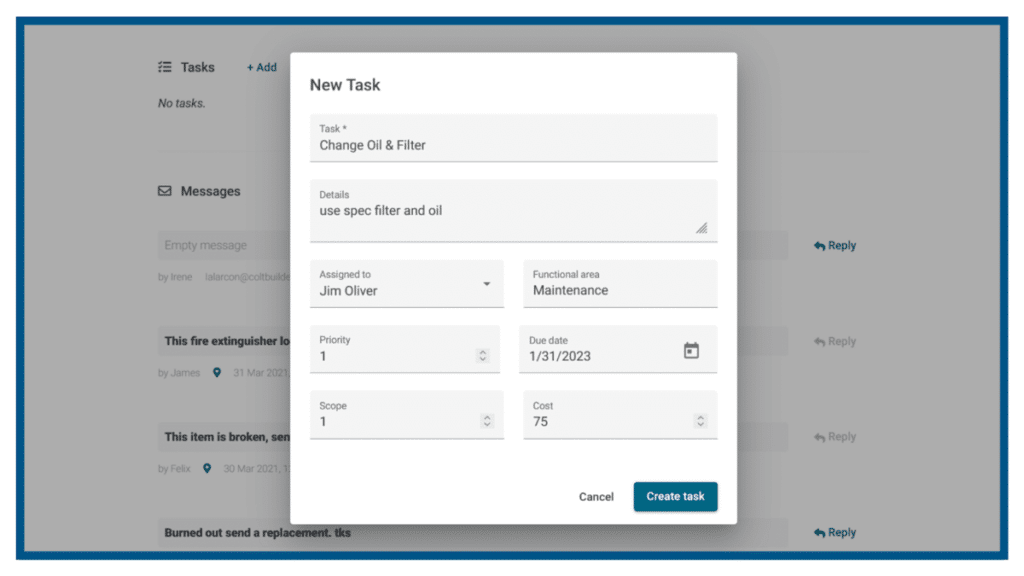
You can choose the time that will be the least disruptive to production, as well as employees that have the least to do at the time.
It also offers an overview of all scheduled and completed tasks, which ensures that no piece of equipment slips under the maintenance radar.
To sum up, planning downtime for regular inspections will keep your equipment in healthy condition, which will in turn help avoid unplanned downtime due to machine failure.
Increased Equipment Productivity
Performing regular inspections keeps equipment in optimal working order for longer, which leads to increased productivity.
At the Gregory Poole Machine Company, they put it like this:
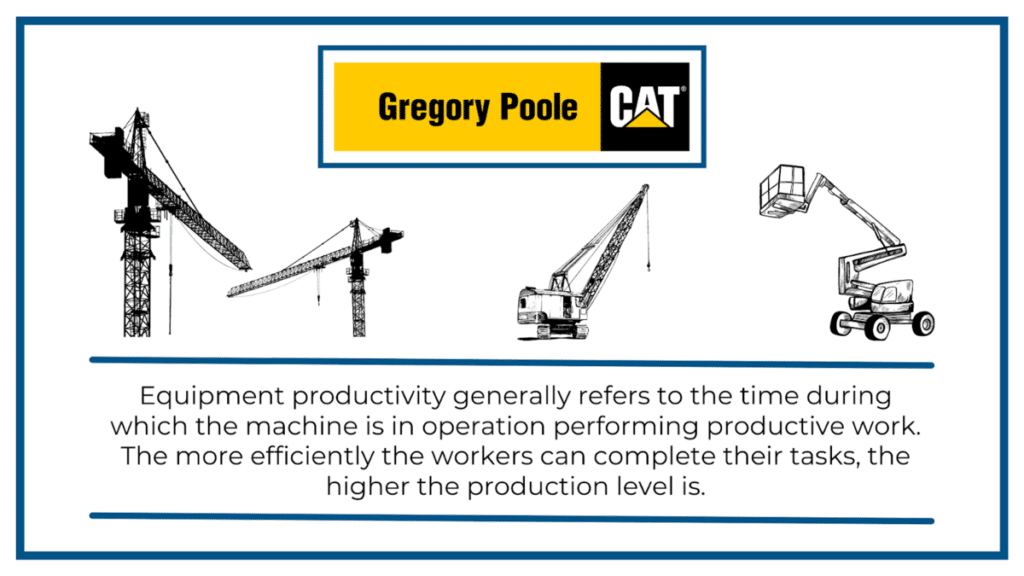
They go on to state that a typical piece of equipment is estimated to be productive around 800-900 hours annually, or about 62% of the time.
So, how can equipment inspections help increase that number?
For a start, we already described how inspections help with avoiding machine breakdowns and unplanned downtime.
Obviously, the less time a piece of equipment spends out of order waiting for replacement parts, the more productive it can be.
The same is true with employees. When a failure occurs, operators are left wasting precious time until a new machine arrives, hindering their productivity.
Additionally, maintenance workers have to dedicate work hours to fixing the machine in question instead of focusing on their scheduled tasks.
However, productivity does not depend only on bypassing these extreme cases.
Just because a piece of equipment is functional, it does not mean it is giving its optimum performance.
A bulldozer can still work with underinflated tires, but it will move at a slower pace and do less work than one with tires in perfect condition.
Regular equipment inspections include checking for damage and misalignments that impact performance.
Maintenance deals with any problems that are spotted, allowing operators to make the most out of their equipment.
Ultimately, inspections will provide equipment with the care it needs to run smoothly, maximizing its productive potential.
Extended Equipment Lifespan
Keeping equipment in the best possible shape will increase productivity, but it will also extend the equipment’s lifespan.
In their book on construction equipment management, Douglas D. Gransberg and Jorge Rueda-Benavides mention the importance of proper maintenance practices for prolonging the useful life of the equipment:
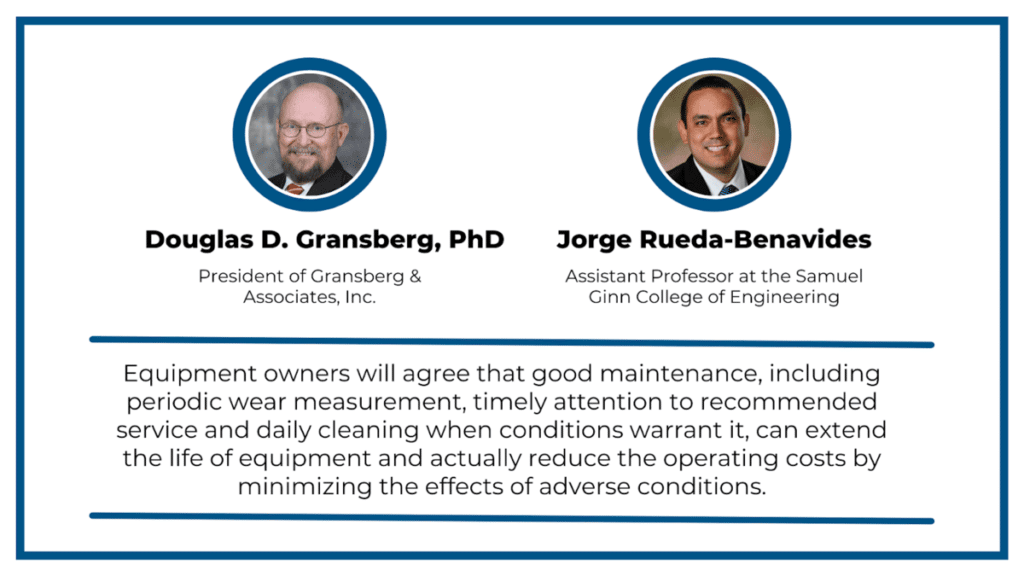
The actions they describe mostly fall under the territory of equipment inspections, and they are right to point them out.
Construction equipment, especially heavy machinery like bulldozers and excavators, is made to operate in rough environments.
Over time, exposure to mud, debris and all types of adverse weather conditions will naturally lead to wear and tear.
Nuts, bolts and gear will weaken, tires will wear down, and lubricants will dry out.
At that point, even if a machine undergoes maintenance, parts of it will not perform as well as before.
This compounds to more troubles down the road, each of which can affect its life expectancy.
Equipment inspections offer a proactive approach which springs to action at the first sign of trouble, not letting them accumulate to have a significant negative impact on the system.
Similarly, if a machine comes to a point of unexpected failure, replacing the component that primarily caused it will not remedy all the damage done.
Before it breaks down, a machine will utilize every working part to keep going, straining them and potentially inflicting further damage.
This can shorten the useful life of impacted machine components, which will also result in a reduced lifespan for the entire system.
By doing regular equipment inspections, you can recognize which pieces are malfunctioning, allowing you to fix or substitute them before the damage spreads to parts that are still unaffected.
Overall, equipment inspections will help avoid both critical damage and wear and tear, thereby keeping it in top condition and extending its lifespan.
Improved Employee Safety
Using equipment that has been thoroughly inspected will also improve employee safety.
Construction is one of the most dangerous industries to work in.
Considering it includes a lot of heavy machinery that lifts and moves tons and tons of cargo every day, that fact is hardly surprising.
In fact, around one-fifth of the total workplace fatalities in the US come from the construction industry.
Of those, a majority fall under what the Occupational Safety and Health Administration (OSHA) defined as the “Construction Focus Four”, meaning the four leading causes of fatal injuries.
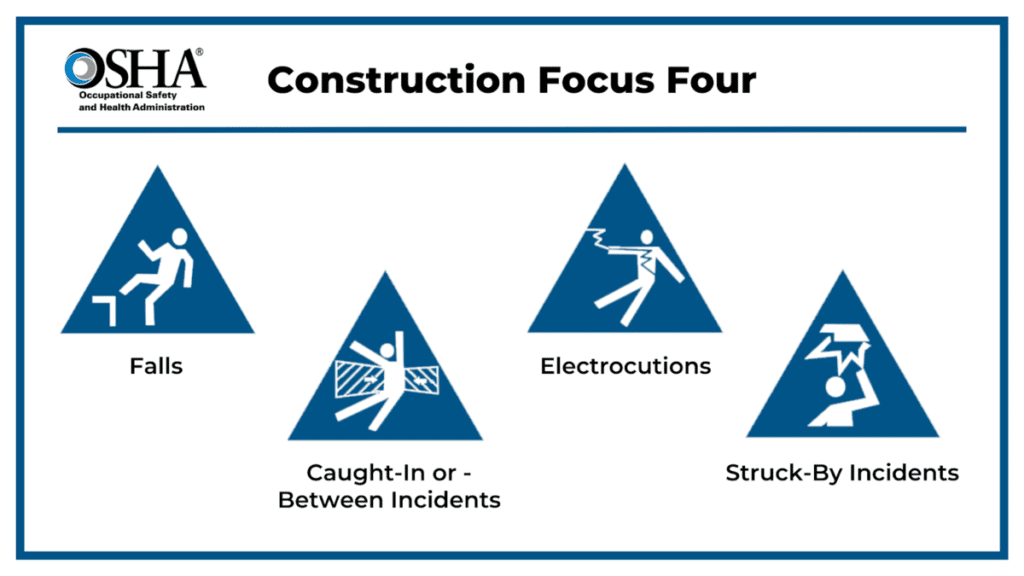
In 2019 alone, a total of 229 deaths occurred in the struck-by and caught-in-or-between incidents category, which can be caused by malfunctioning equipment.
As an example, if the brakes on a bulldozer fail while on a slope, it can slide downhill and even turn over, injuring the operator.
Other people can be injured as well. If a vehicle has a broken mirror, it can hit a passing worker while backing up because they were out of the operator’s sight.
Even if the injuries they sustain do not turn out to be fatal, the accident can still have serious consequences for the workers and the company alike.
For this reason, regular inspections have to follow safety protocols and include examining parts of equipment that have the most potential to cause an accident or an injury.
After all, with a daily routine of checking brakes and mirrors before use, the probability of failure lessens significantly, as does the chance of accidents that endanger employees.
All in all, equipment inspections that align with safety protocols will go a long way in increasing the safety of employees and creating a more stable work environment.
Higher Cost Savings
In light of all of the above, it isn’t difficult to conclude that equipment inspections save money in the long run.
However, it might not appear that way at first glance. Adopting a regular maintenance strategy also costs money and takes time, while keeping employees off production.
Furthermore, it includes inspecting equipment that is by all accounts in perfect working order, which can seem unnecessary.
But these objections fail to account for the big picture.
As mentioned, one of the biggest advantages of regular inspections is the ability to prevent unexpected breakdowns of equipment, which come at a price much greater than that of inspections.
Firstly, just like construction equipment itself, replacement parts are very expensive, with prices going up to thousands of dollars.
Additionally, unplanned production downtime can cause project delays and weighty cost overruns, jeopardizing the entire production.
Compared to these large expenses, investing time and money in regular inspection protocols is affordable enough to seriously consider.
And the US Department of Energy agrees. In their Operations and Best Practices Guide, they compare different maintenance approaches and conclude that a preventive maintenance strategy comes with a cost reduction of 12% to 18% over reactive maintenance.
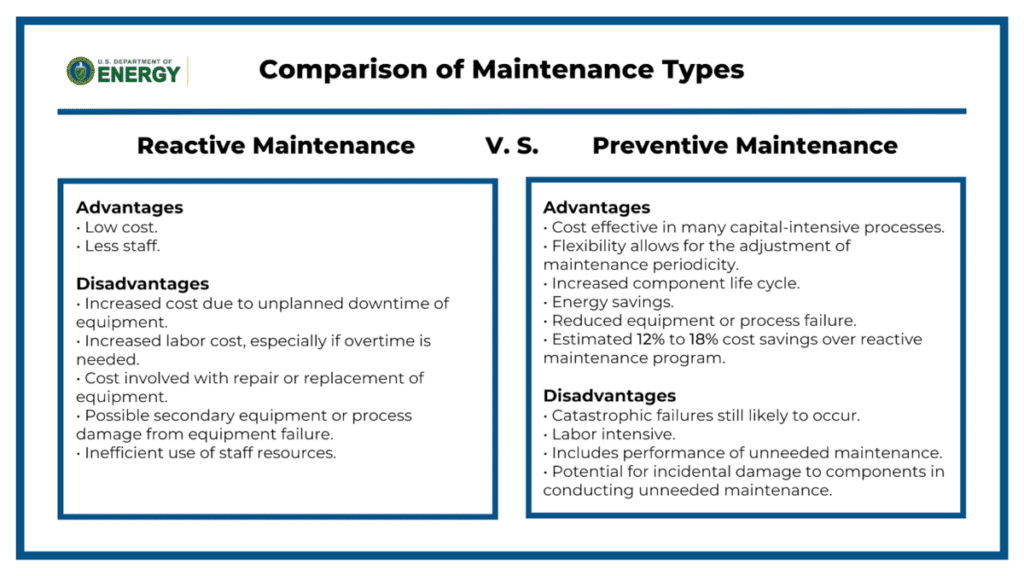
According to them, predictive and reliability-centered maintenance offer even more savings, but these also include different amounts of regular inspection, making it a surefire investment.
In general, regular inspections may seem like a major expense, but they will lead to fewer equipment failures and expensive parts purchases, project delays and cost overruns that come with it.
Conclusion
If you own or manage a construction company, you are probably aware of how important your assets are.
Without vehicles and machinery, there would be no one able to do the heavy lifting of steel and concrete usually required to build buildings, roads and other large structures.
In this article, we have outlined the importance of performing regular inspections, most of which can greatly benefit your business.
If you agree and want your equipment to keep on doing the work it does best, you should think about prioritizing equipment inspections in your management strategy.