Key Takeaways
- Manually checking out equipment can cause mistakes, delays, and extra costs for construction managers.
- Real-time tracking shows where each tool is, helping workers find what they need quickly.
- The system tracks who checked out equipment, making workers more responsible for the equipment and increasing accountability.
Manually checking out equipment is often a hassle for construction managers.
You might have stacks of paper forms or endless rows in a spreadsheet, and each entry is a potential point for errors.
Moreover, workers may forget to record when they take a tool or equipment or return it late, which causes delays and confusion.
Fortunately, that’s where an equipment checkout system steps in.
By automating the equipment checkout process, it gives you full control over your tools, making it easier to manage and monitor all your equipment.
Today, we’ll explore what an equipment checkout system is, its benefits, and how to adopt it.
Let’s dive in.
In this article...
What Is an Equipment Checkout System?
An equipment checkout system is like a digital library—but instead of books, you’re lending out tools and machinery.
Just like a library tracks when a book has been lent, to whom, and when it’s due back, this system helps businesses manage their equipment—from checking it out to tracking its usage and ensuring it’s returned on time.
The software works hand in hand with the asset tracking solution by assigning each tool or piece of equipment a unique identifier, like a QR code or barcode.
When a worker needs to use an asset, they scan the code to check it out, and the system automatically updates its location and status.
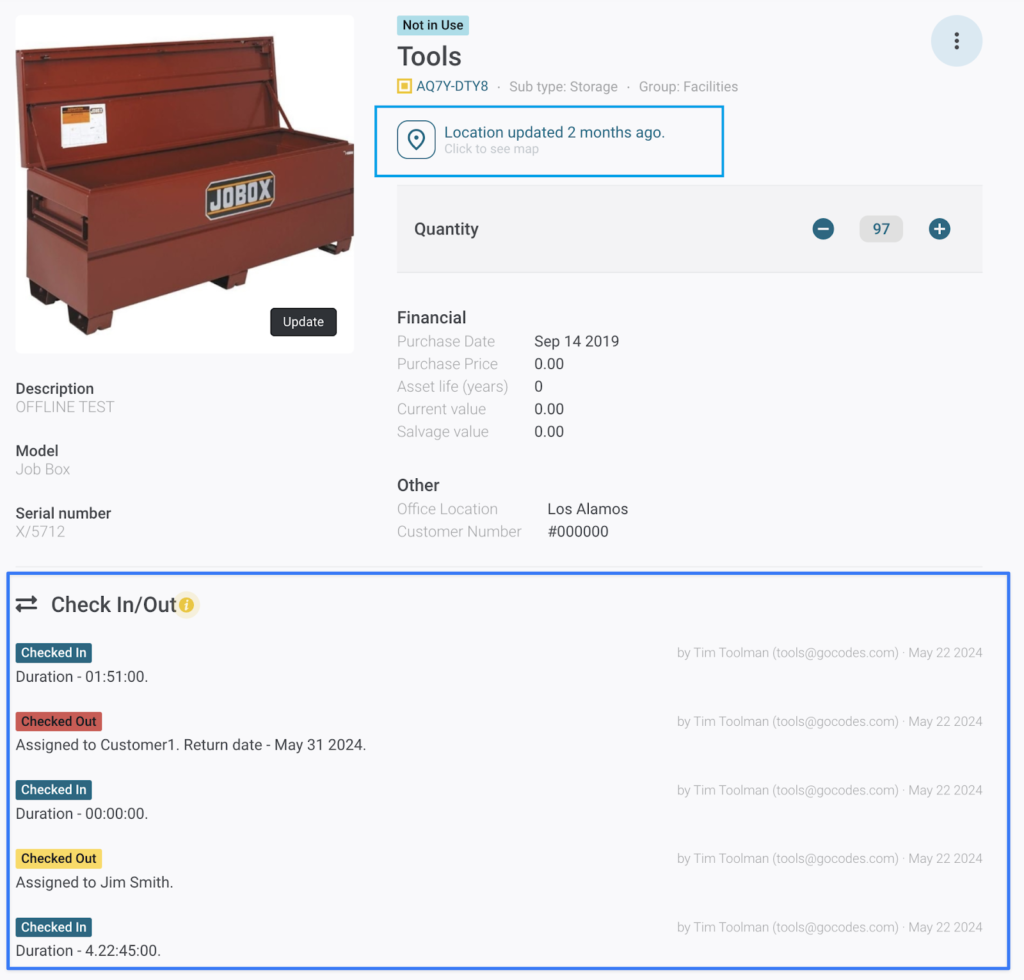
This way, everyone in the company knows where each tool is, who has it, and when it will be available again.
While this type of system is useful in many industries—such as healthcare for tracking medical devices or education for managing technology—it’s particularly important in construction thanks to its vast benefits.
Let’s explore those next.
Benefits of Equipment Checkout Software For Your Business
Equipment checkout software can bring many great benefits to your business, from increasing your asset visibility to optimizing their use.
Plus, it’s efficient both in the office and the job site.
Here are the five benefits that can make all the difference for your company.
Provides Real-Time Visibility of the Equipment
One of the greatest advantages of using equipment checkout software is that it provides real-time visibility into the status of your assets.
But how does this actually work?
Take our GoCodes Asset Tracking, for example. It is an asset-tracking solution with a built-in checkout system.
You simply attach our durable, QR-coded labels to each piece of your equipment and input vital information—like descriptions, manuals, warranties, and more—into our intuitive software.
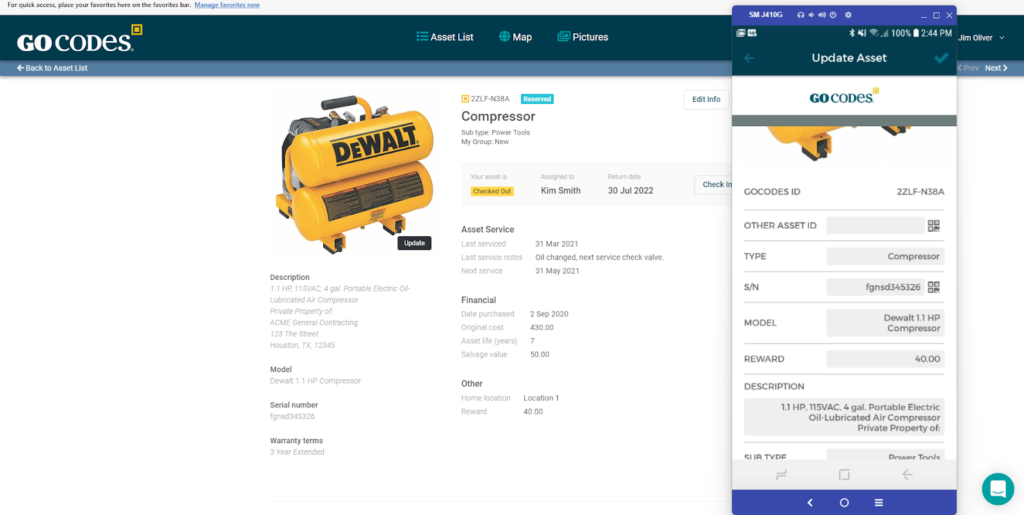
Then, you can assign an asset directly to a person or, in other words, check it out to a worker.
Optionally, you can add a return date and other notes, as you can see below:
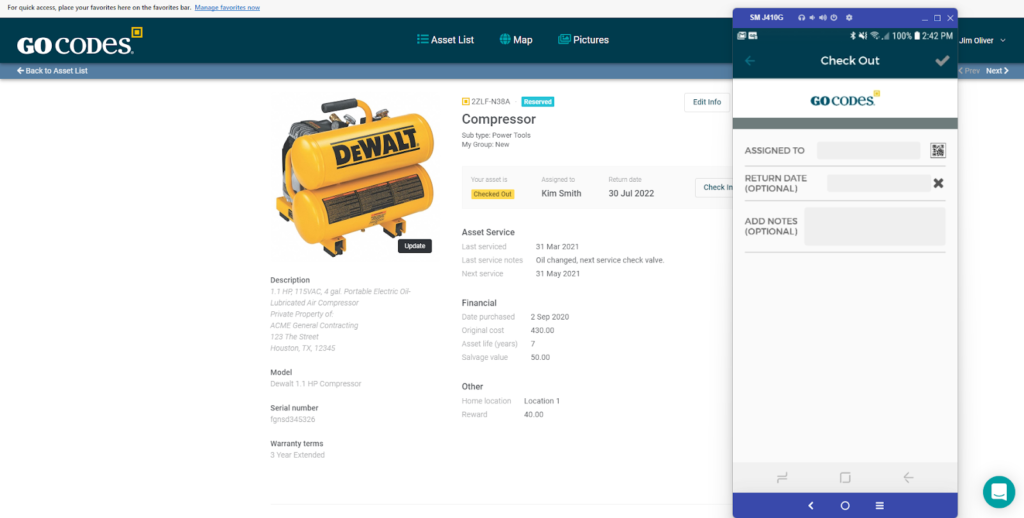
Alternatively, when a worker begins using the asset, they can check it out themselves by scanning the QR code with their smartphone.
When they finish, they simply check it back in.
Each time a worker scans the code, the system automatically updates the equipment’s location and status.
This means you always know exactly where your assets are and who’s using them.
Why does this matter so much?
For starters, this real-time visibility allows project managers to allocate resources more efficiently.
When you know exactly where your tools are and who’s using them, you can plan tasks better and avoid unnecessary delays or overlaps.
This visibility becomes especially important on busy construction sites.
Without it, workers often waste valuable time hunting for tools that might be sitting unused at another site, which leads to non-productive working.
Andy Jenkins, an operations team leader at Schlumberger, a global technology company, knows this frustration firsthand:
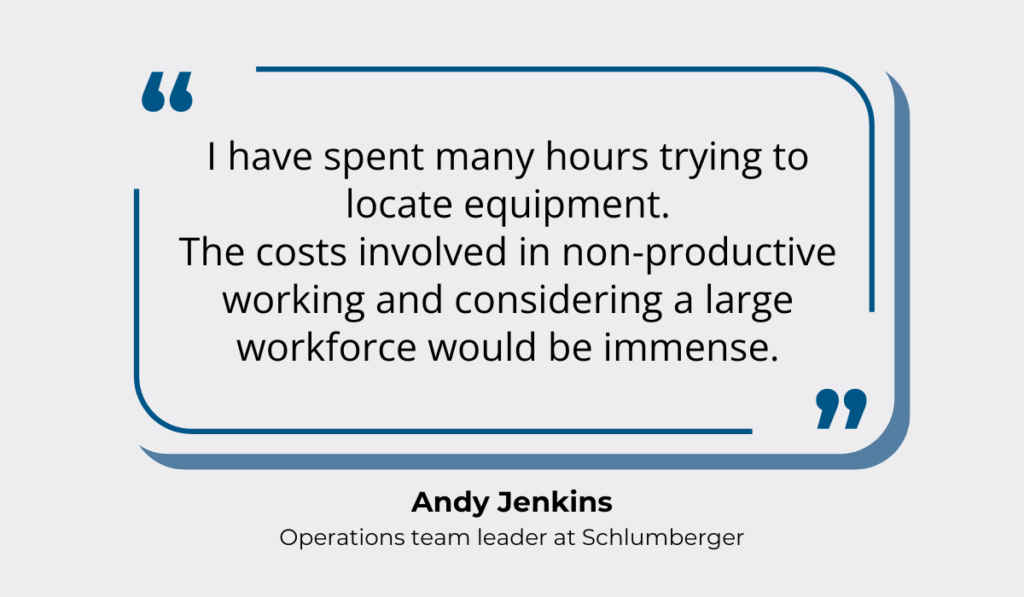
Although Jenkins doesn’t come strictly from the construction field, his experience echoes a common issue across the construction industry.
In fact, research shows that construction professionals keep wasting their time looking for lost or misplaced equipment.
Michael McGowan, region head and CEO of Hilti North America, confirms this:
“Our research shows that each job site loses on average one day per month of productivity due to workers searching for tools. In addition, the contractors end up spending up to 90 hours per month tracking tools: in essence, productivity loss for both workers and contractors due to lack of an effective asset/tool management platform.”
All this wasted time could be spent getting the job done.
Fortunately, real-time tracking with the help of equipment checkout systems can bring you one step closer to reducing non-productive time.
Instead of wasting time searching, your workers can find the tools they need right when needed, which leads to a more streamlined workflow and saves your business both time and money.
Promotes Employee Accountability
When an employee checks out a tool, the software assigns that piece of equipment to them.
The system logs details such as who checked it out, when, and for how long.
Plus, the system can remind you that a worker has to return an asset through email or in-app notification, like this one:
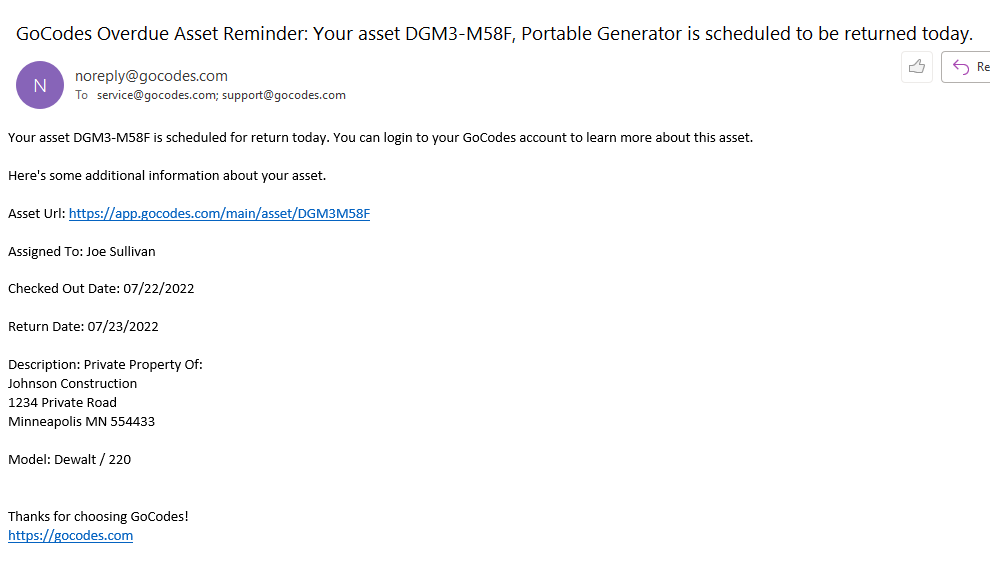
All of the above creates a clear trail of responsibility.
Why is this important?
Well, when workers know their tool use is being monitored, they’re more likely to take better care of the equipment.
It also discourages misuse or theft, because there’s a clear record of the last person who used the tool.
And theft is no small problem in the construction industry.
A recent survey by BauWatch revealed that 62% of construction professionals reported an increase in equipment theft in 2023.
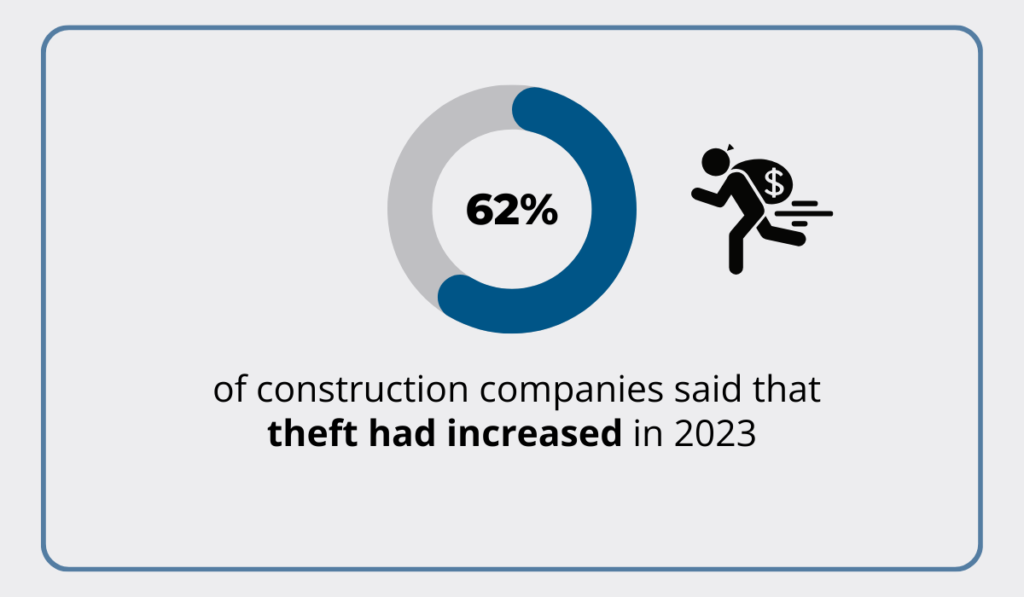
Unfortunately, theft has far-reaching consequences.
It can lead to project delays and higher costs, as Annabel Hiatt, Senior Category Manager at Travis Perkins, UK’s largest builders’ merchant, points out in the same survey:
“When viewed in isolation, it’s easy to underestimate crime’s impact. Yet, when we look at the data in the round, we see that the costs and delays add up, and this has the potential to make it harder to meet project deadlines. Construction projects always operate on paper-thin margins – and a small incident can have an outsized impact.”
However, by keeping track of who last used each tool, you have a better chance of recovering stolen or lost items.
The added accountability also improves overall productivity.
Your workers are more mindful of equipment use, and your business avoids the costly setbacks caused by theft and misuse.
Optimizes Equipment Utilization
Maximizing the use of every tool and machine is critical to keeping costs down and ensuring projects stay on schedule.
But how can you tell if your equipment is being used efficiently or sitting idle?
This is yet another area in which equipment checkout systems excel.
By tracking check-ins and checkouts, you gather valuable data on how each piece of equipment is being used.
The software logs:
- which equipment is checked out,
- who is using it and for how long,
- the location and specific project where it’s being used, and
- the important details like run hours, mileage, or any reported issues.
All of this data is automatically logged into the system and can be analyzed through detailed reports.
For example, in our GoCodes Asset Tracking, you can generate customized reports showing how often each piece of equipment is used across different projects.
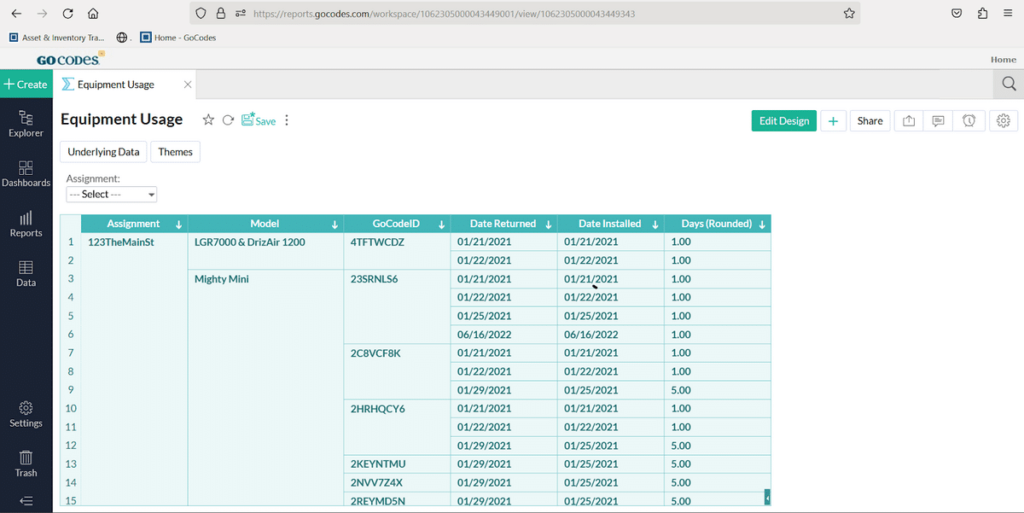
This way, you can quickly identify underutilized or overused equipment and make better decisions about redistributing resources.
For example, if a machine is barely being used on one site, it can be moved to another project where it’s actually needed.
Conversely, if a tool is nearing overuse, you can schedule timely maintenance to prevent unplanned downtime.
Optimizing utilization through accurate data means you save money by avoiding unnecessary rentals or purchases.
Instead, you can more easily ensure you’re getting the most out of every asset on your job sites.
Streamlines Maintenance Scheduling
Equipment downtime can seriously disrupt a project’s workflow, especially when it’s due to missed or delayed maintenance.
Luckily, an equipment checkout system can help you stay on top of maintenance needs by streamlining the scheduling process.
When employees check in a tool or machine, they can log any damage or issues they’ve noticed.
In the example below, Jim did this for an electric wrench that needed repair by simply adding a note into the system:

This creates a real-time record of maintenance needs.
When problems are logged immediately, they can be addressed before they turn into more significant (and more expensive) repairs.
Such a proactive approach to maintenance keeps your tools and machinery in good working order, reducing the likelihood of unplanned downtime.
And, with a system like this, you can quickly schedule maintenance and check out an asset to a technician.
As soon as they see they’ve been assigned a task, they can start with work.
In essence, equipment checkout software helps keep your machines running longer and avoids costly inefficiencies that arise from neglecting maintenance—all by streamlining maintenance scheduling.
Reduces Administrative Burden
One of the most immediate and noticeable benefits of an equipment checkout system is how much it reduces the administrative burden on your team.
If you’re still using manual processes—whether through spreadsheets, paper forms, or outdated methods—to check out equipment, you’re tying up valuable resources that could be better spent elsewhere.
Statistics confirm this.
According to research from Smartsheet, over 40% of workers spend at least a quarter of their workweek on manual, repetitive tasks like data entry and email management.
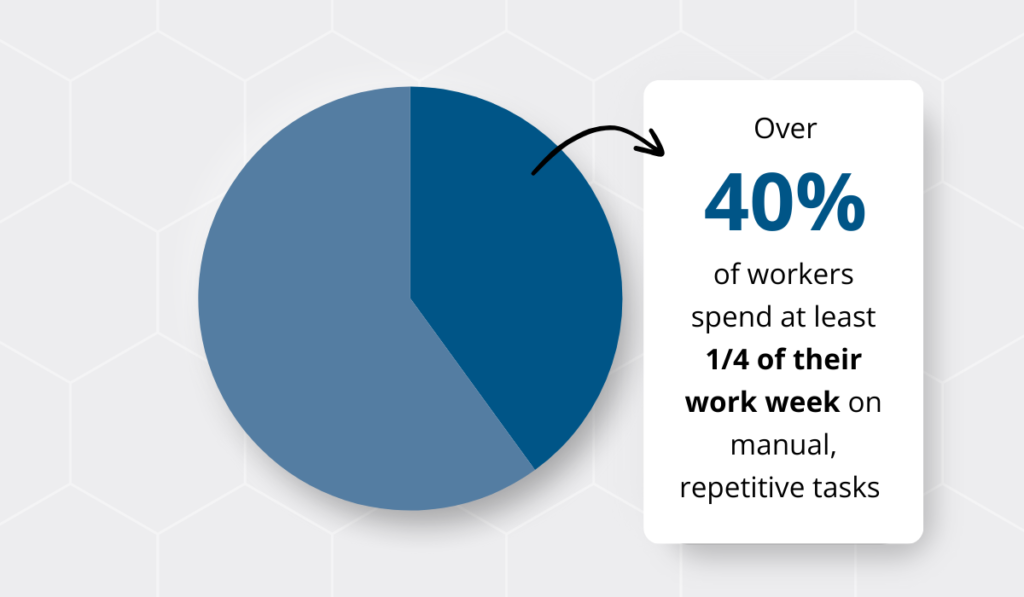
In construction, this problem is compounded by the complexity of managing multiple job sites and checking equipment in and out for all of them.
This is where equipment checkout software transforms operations.
Instead of chasing down who has which tool or updating spreadsheets, the system does it all for you.
Employees simply check out or return equipment using a mobile app, and the system logs the transaction, updates the tool’s status, and even tracks its location in real time.
This saves countless hours of administrative work.
And the benefits don’t stop at the office.
On the job site, poor coordination is one of the biggest hurdles to efficient work.
In a study by Levelset and Fieldwire, 40% of contractors reported that poor coordination was slowing down their projects.
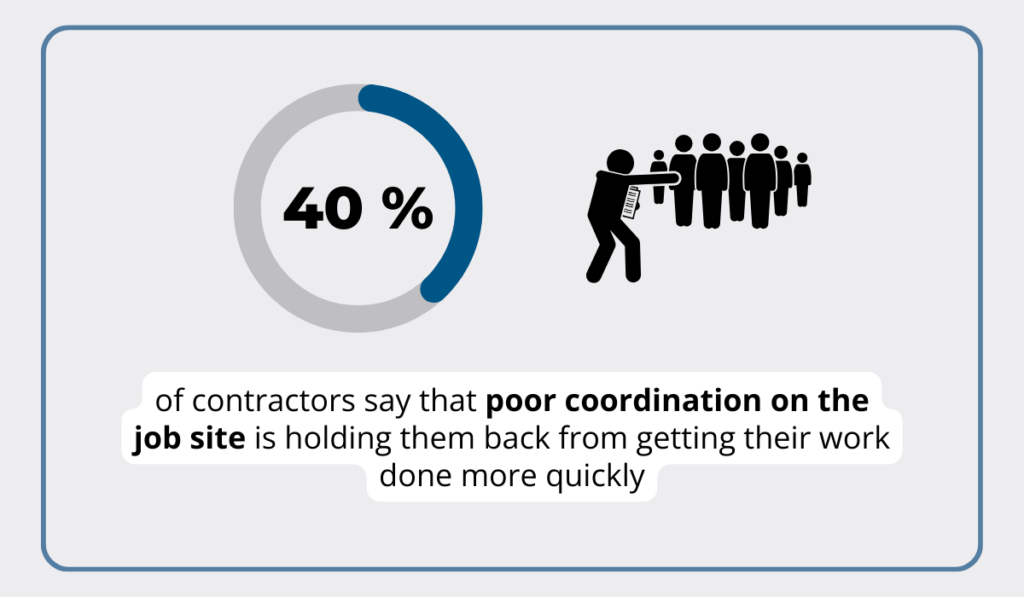
Illustration: GoCodes Asset Tracking / Data: Levelset
And this often comes from not knowing where certain equipment is and who is using it.
Equipment checkout software helps solve this by providing real-time data on tool availability and location, which further simplifies team communication and coordination.
In short, the equipment checkout system frees up valuable time for your staff and improves efficiency both in the office and on-site, reducing operational headaches and boosting productivity.
If you haven’t been convinced whether you need checkout software, this benefit alone is why you should go for it!
How to Ensure Adoption of New Checkout Software
As you can see through all these benefits, adopting equipment checkout software can truly transform your construction company’s operations.
But only if your team fully adopts it.
To make this happen, you need buy-in from leadership and active involvement from the field.
Let’s look at how you can make this a reality in your construction company.
Involve Key Stakeholders In the Software Selection Process
The first step is to involve key people—managers, supervisors, and field workers—in choosing the software.
This ensures the solution addresses everyone’s needs, from job site challenges to logistical management.
And, of course, leadership is where it starts.
Steve Schultz, Business Analyst at James G. Davis Construction, stresses that technology adoption has to be driven from the top:
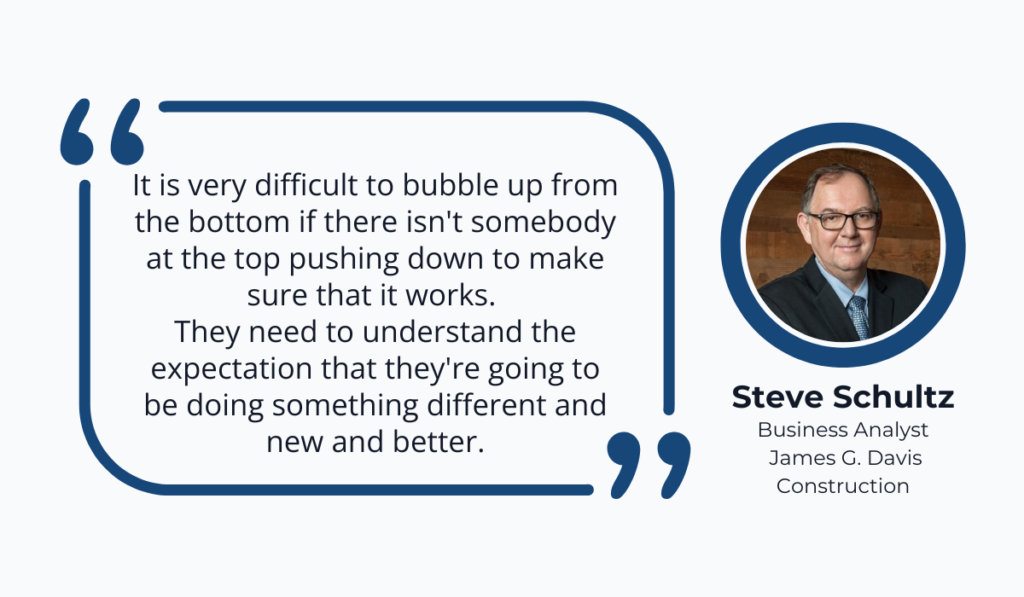
When the company’s leaders actively support the transition to new software, it sets the tone for the rest of the team.
But there’s another reason for leadership to get on board—national initiatives are backing digital transformation in construction.
For example, the Federal Highway Administration (FHWA) is offering millions in grants through its Advanced Digital Construction Management Systems (ADCMS) program to encourage the use of digital technologies in construction.
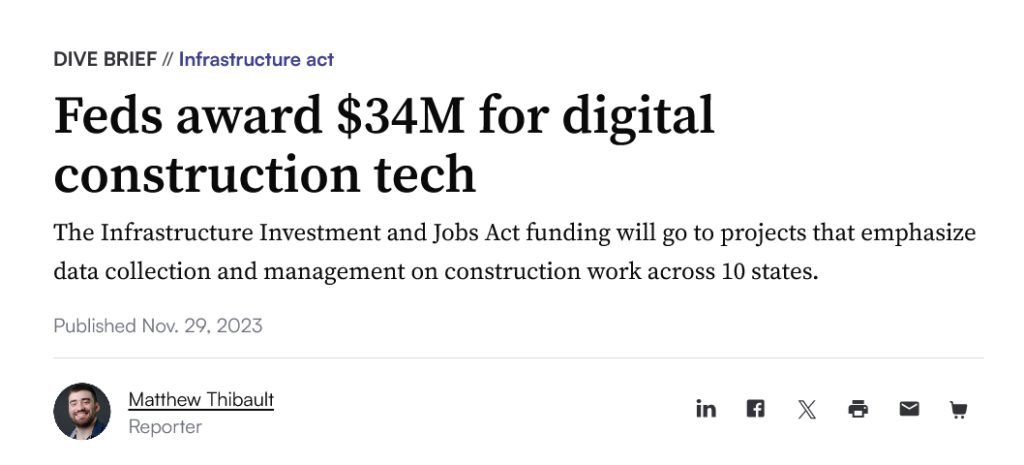
These grants aim to boost productivity, improve information-sharing, and reduce reliance on paper-based methodologies.
While they are currently focused on transportation projects, they show a growing national push toward innovation that could expand across sectors.
For owners and key stakeholders, this could be a great reason to support digital tools and drive their adoption within the company.
Besides the stakeholder buy-in, it’s equally important to gather input from those who will be using it every day—field workers and supervisors.
This way, the team feels involved, and the solution is more likely to fit their actual needs, so they will also adopt it more easily.
Emphasize the Benefits of the Equipment Checkout Software
However, employees might be hesitant to use this new equipment checkout system if they believe their current processes work just fine.
In fact, according to the 2021 Annual Construction Technology Report by JBKnowledge, hesitant employees were the biggest barrier to technology adoption for construction companies.
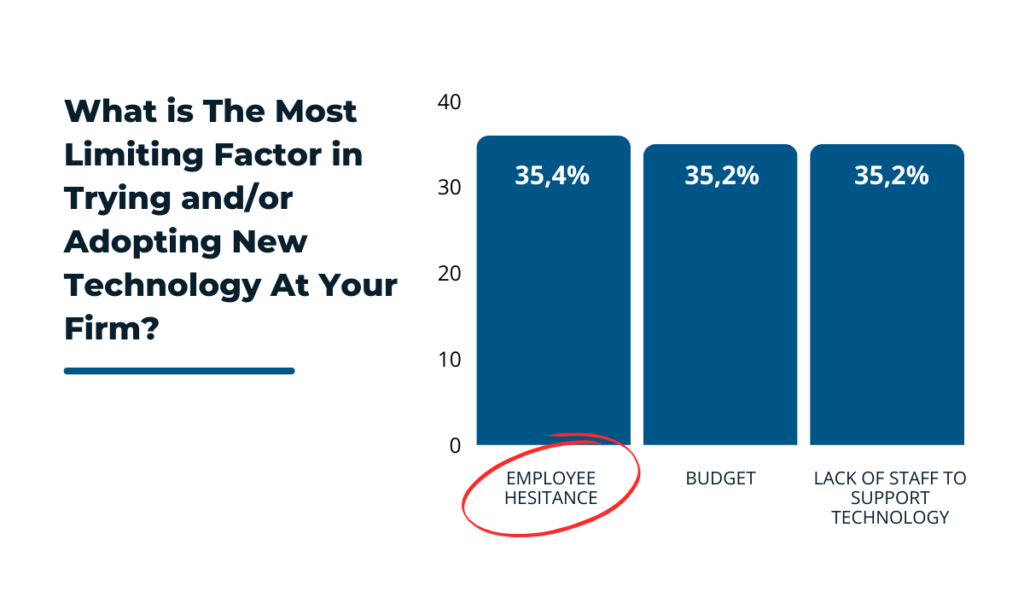
That’s why it’s important to highlight how the new software will make their jobs easier.
So, it would definitely be wise to emphasize how much manual paperwork the software will reduce for your office team.
On the other hand, job site crews won’t have to search for tools that are not there or return to the office to note down that they checked in the equipment.
When workers understand that the software can directly improve their day-to-day tasks and how, they will be more likely to get on board.
Provide Comprehensive Training
But simply explaining the benefits isn’t enough.
You also need to ensure that everyone knows how to use the software properly.
Hands-on training is key, especially for workers who may not be as tech-savvy or who might feel intimidated by the new system.
At Davis Construction, for instance, they approach training in a way that supports long-term learning, as Schultz explains:
“At Davis, we conduct monthly technology webinars that are available as lunch-and-learn programs. These sessions are recorded, shared, distributed and then cut into individual lessons. This approach focuses on training, covering what’s new, what’s hot, and our best practices. We constantly review these topics with all of our users.”
This is a great way to provide continuous support.
Recorded sessions allow your team to revisit the training whenever they need a refresher, ensuring they stay confident using the software even as updates and new features roll out.
Ultimately, the key to successful software adoption is involvement at every level—from top management to job site crews.
Equip your team with the tools and training they need, highlight the real benefits, and tap into the industry’s growing focus on digital solutions.
That’s how you ensure your company fully embraces the new technology and reaps the benefits of adopting an equipment checkout system.
Conclusion
So, are you ready to stop wasting time hunting for tools and losing money on delays?
With an equipment checkout system, you can track your assets in real time, keep everyone accountable, and reduce administrative work, among many other benefits.
It’s a simple upgrade that saves you headaches and streamlines your workflows.
Just make sure to have everyone’s buy-in and invest time and effort into training your people to use the software properly.
You will see the difference it makes in no time!