Key Takeaways
- Financial data helps improve the bottom line, win more bids, and maximize ROI
- Insider theft can be prevented with the help of ownership data
- Certain data helps you demonstrate compliance, and avoid legal issues and penalties
So, you’re interested in asset tracking, but not sure what to expect?
What kind of data can these systems track anyway?
Those are the questions we’ll answer in this article.
We’ll break down the types of data you get from tracking your assets and show you how to put those insights to good use, all backed up with real-life examples and statistics.
Let’s get started.
In this article...
Location Data
Location data is the foundation of efficient asset tracking.
It shows you where your assets are either in real-time or near real-time, depending on the system you use.
On a large, bustling construction site packed with expensive equipment and tools, this kind of information is extremely valuable, for several reasons.
For starters, it helps prevent theft or at least aid in the recovery of stolen assets.
A recent incident in Howard County, Maryland is a good example of the latter.
Namely, $5 million worth of stolen tools was successfully recovered thanks to a Sterling contractor who had installed GPS trackers on his assets prior to the robbery.
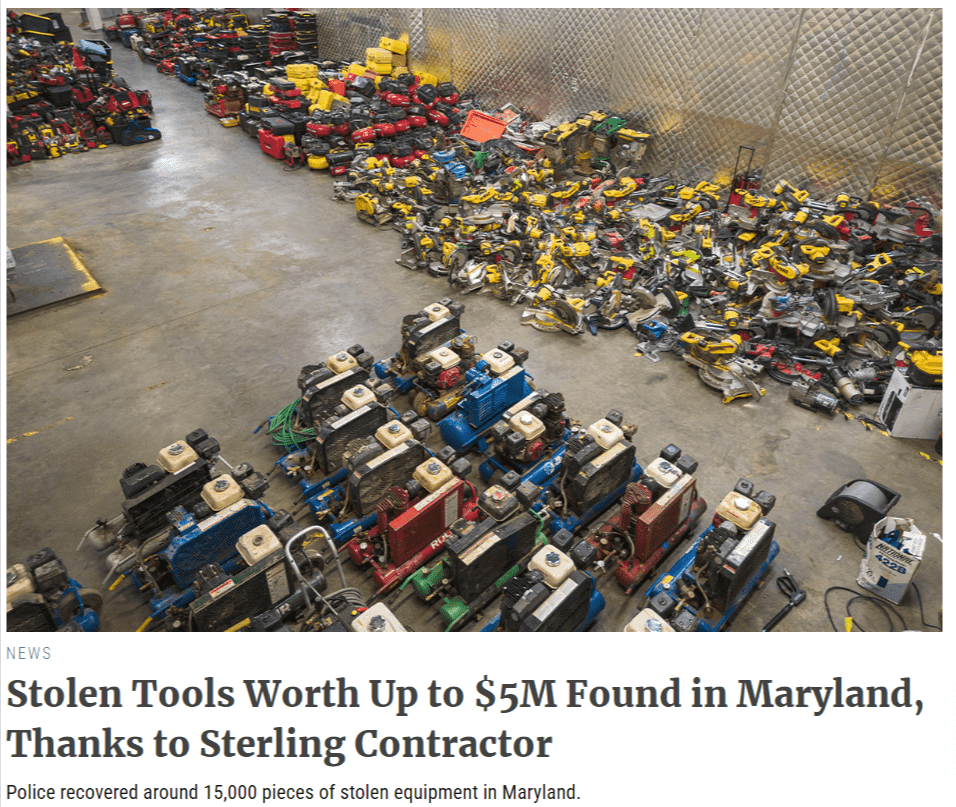
When tools went missing, he shared their location data with the police, who then obtained a warrant and quickly found them, as well as those belonging to numerous other victims.
It was a perfect demonstration of how much of a game-changer this type of information can be.
But location data isn’t just for after the fact. It can be a powerful tool that prevents unauthorized use or movement in the first place.
That’s because it powers a feature known as geofencing, which enables you to set virtual boundaries that your assets aren’t allowed to cross.
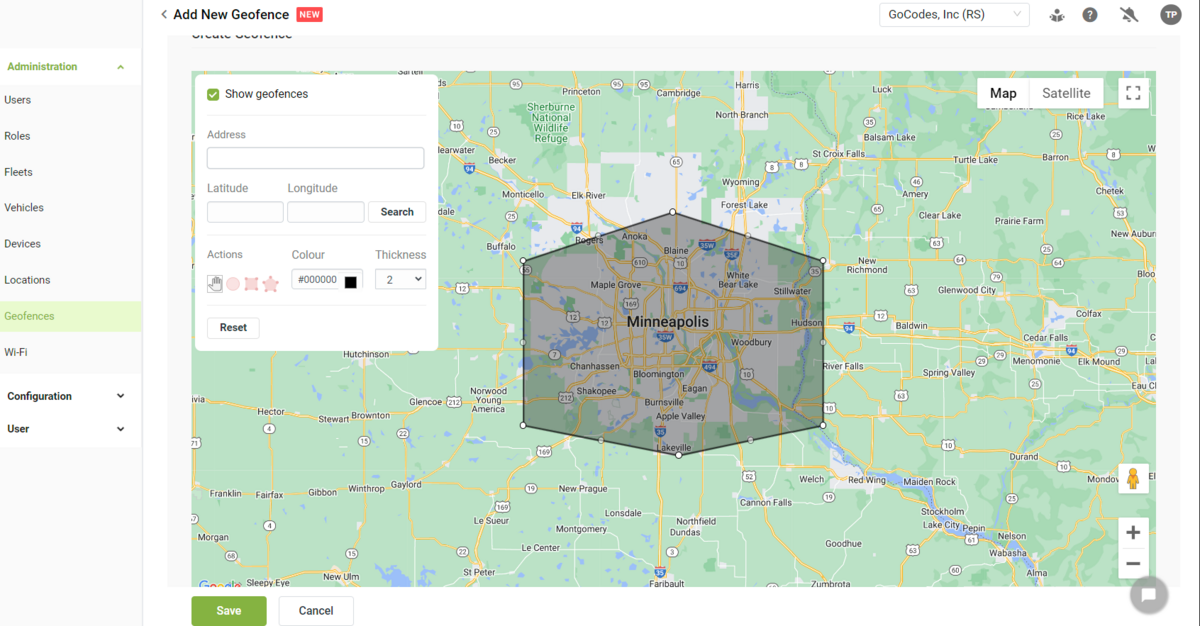
And if they do enter or exit these boundaries, the software immediately notifies you.
This means if someone attempts to steal your equipment, you’ll be alerted right away.
Besides theft, location data also helps tackle on-site productivity challenges, as it minimizes the time wasted searching for tools and equipment.
How many hours do you think are lost on such operational inefficiencies each month?
More than you might imagine.
Michael McGowan, Region Head and CEO of Hilti North America, a construction technology provider, breaks it down:
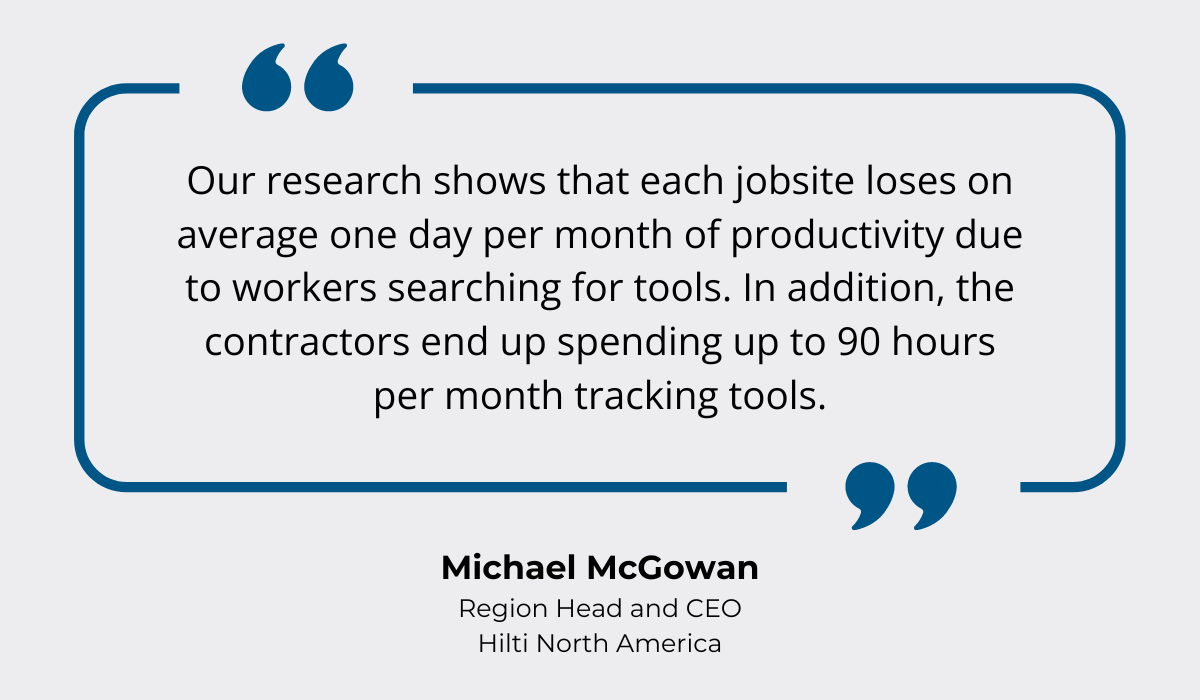
However, with an asset tracking solution, those days of wandering around a job site, and trying to find a tool are over.
Workers can simply check the asset’s exact GPS location in the system and go straight to what they need, saving precious time and keeping the project moving smoothly.
This is why location data is such an asset-tracking staple.
It not only keeps your materials, tools, and equipment safe from thieves but also maximizes your team’s efficiency, preventing costly downtime and project delays.
Ownership Data
Ownership data shows who used which assets, when, for how long, and for what project.
Combined with location data, this information becomes a powerful tool for preventing misuse and maintaining peak productivity.
Matthew Jackson, Senior Director of Marketing at Hilti North America, agrees:
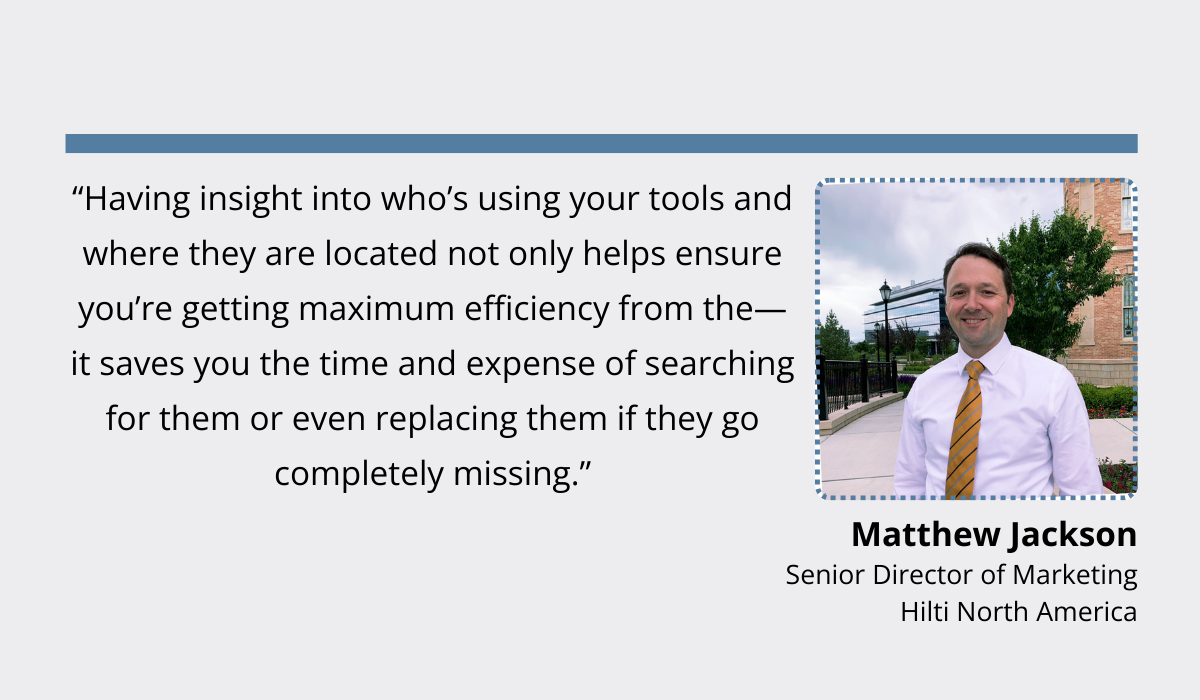
This is because, essentially, ownership data keeps everyone more accountable.
Employees know they need to handle assets carefully, return them on time, and put them back where they belong—in short, to follow proper usage protocols.
After all, if an asset gets damaged, stolen, or lost, the system will show who had it last. That kind of transparency can make a huge difference in how your team treats equipment.
In fact, sometimes, it might even help prevent crime.
While it’s not the most pleasant thought, the reality is that workers do occasionally abuse trust and steal company assets.
For instance, just this January, a construction worker in Wyoming was arrested for allegedly stealing company equipment.
And 2024 BauWatch’s Construction Crime Index further backs up the fact that these things do happen.
As it turns out, 27% of construction thefts are inside jobs.
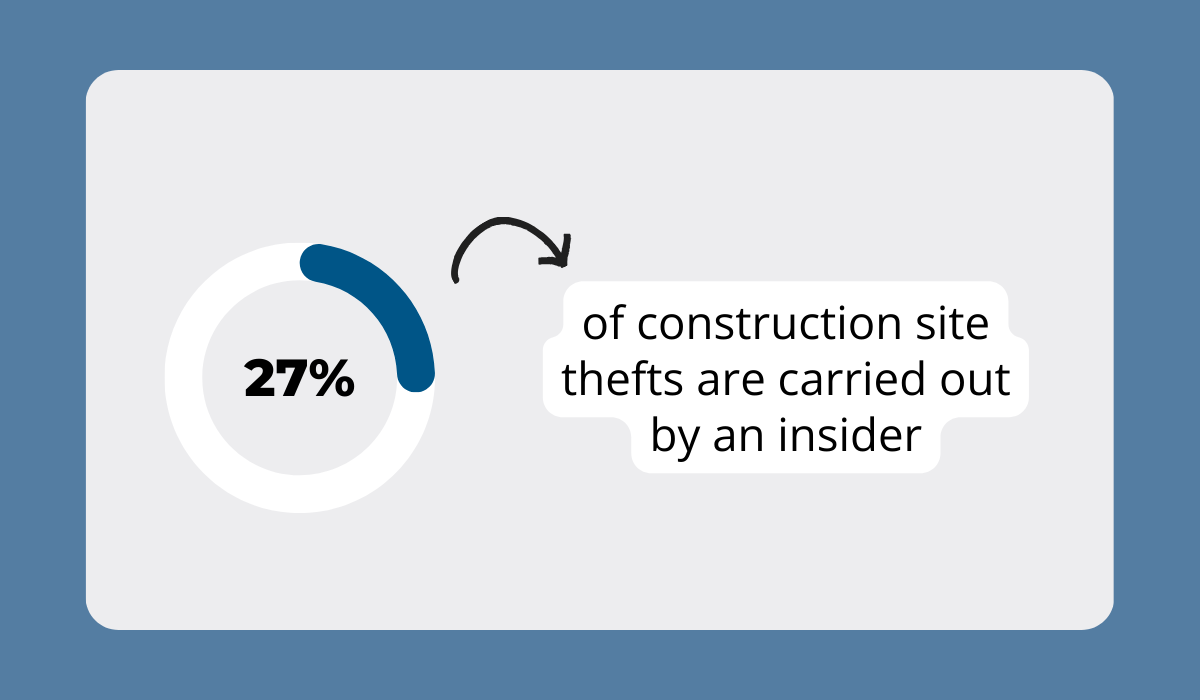
Those “insider thieves” are tricky because they blend in as regular employees and don’t arouse suspicion, which makes them hard to catch.
But with ownership information, you have a way to track who had access to what, which can help identify the culprit.
Even better, it might stop them from trying in the first place.
Now, this doesn’t mean you should suspect all your workers of wrongdoing; far from it.
Ownership data is more about creating a clear chain of custody and building a culture of fairness and visibility.
It ensures everybody is held to the same standard and clears up any confusion or disputes over equipment handling and use.
Equipment Utilization Data
Generally speaking, equipment utilization data provides insight into how assets are being used, for how long, and how frequently.
Metrics like idle time, fuel consumption, or unplanned downtime rates also fall into this category.
Plus, some more advanced systems can even capture specific details such as speed, engine hours, and instances of hard braking for vehicles and heavy machinery.
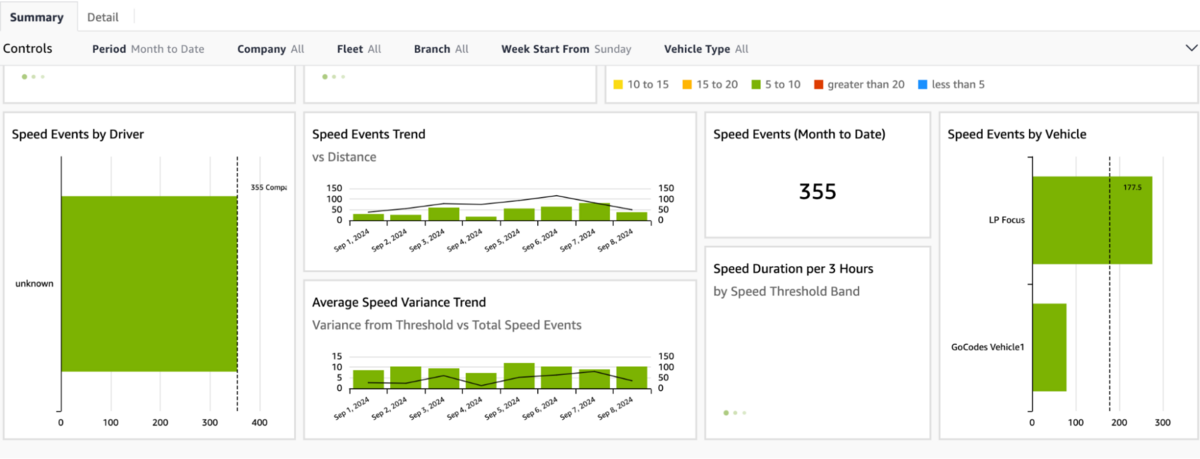
With this kind of information at your fingertips, you can easily spot over- or underutilized assets and reallocate them more strategically for safer and more efficient operations.
Joseph Micheletti, Equipment Controller at Loenbro, a company that delivers various industrial services, gives an example of how this might work on a real-life job site:
“If one of our field engineers or project managers is done utilizing the majority of their sidebooms and another field engineer says, ‘I could really use another one or two sidebooms,’ he has the resources to see, ‘It doesn’t look like this one is being used too much over on Frank’s job; let me call Frank.’”
So, with this type of data, you don’t have to worry about equipment sitting unused or someone hoarding the machines and tools they don’t need at the moment.
You can ensure you make the most out of each asset, but without pushing them past their limits.
Besides, utilization data also makes for more well-informed maintenance plans and schedules.
Knowing how often and how hard your assets are working enables you to predict when each piece will require a tune-up or an inspection, and schedule those activities more accurately.
For instance, Tyler Smith, Product Manager at Volvo Construction Equipment, points out that their excavator undercarriages need an inspection every 40 operating hours, but other machines might have different maintenance timelines.
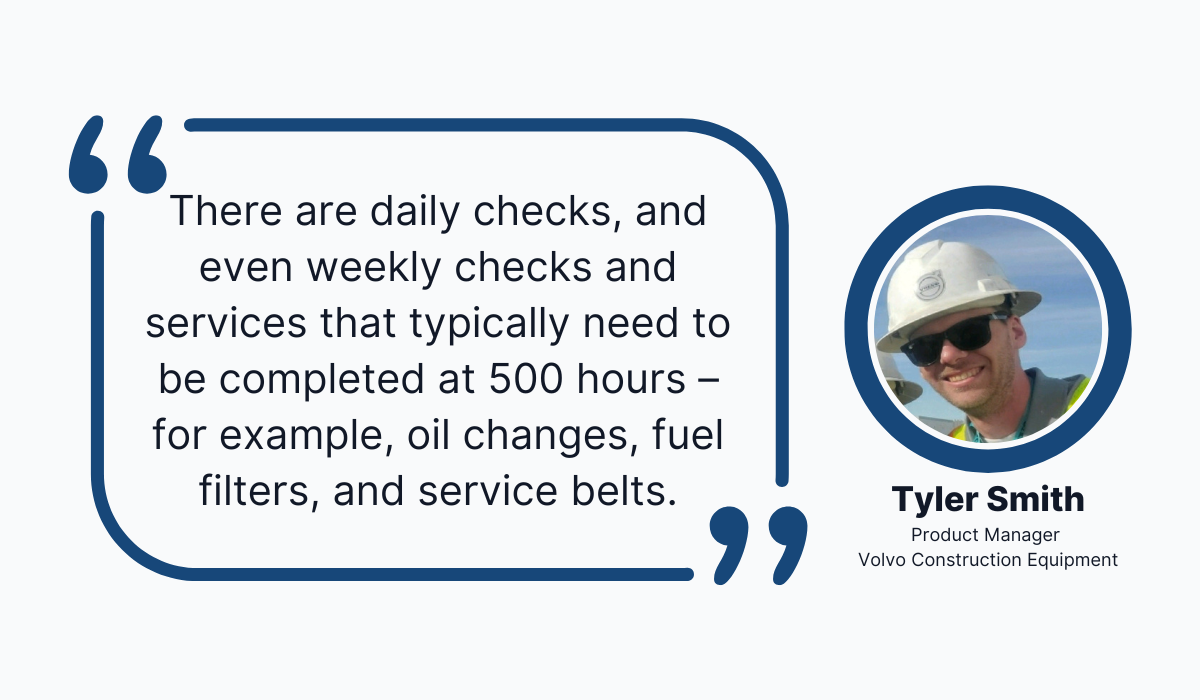
Essentially, by syncing maintenance with real-world usage, you keep your equipment in top shape without wasting time and money on unnecessary service.
And in the end, that’s what utilization data is all about.
It helps you understand your assets so that you can maintain and use them more effectively, ensuring they last longer and perform better.
Inventory Data
Inventory data refers to the information about levels of consumables, materials, tools, and equipment at your disposal, as you see in the example below.
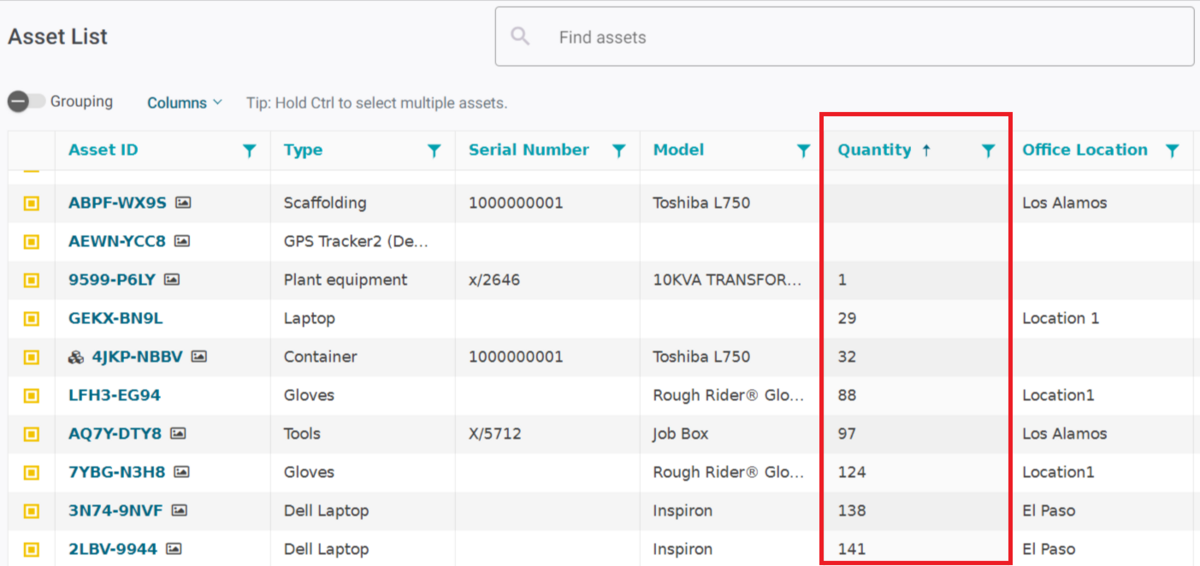
Put simply, it’s a real-time snapshot of what you have on hand.
Such data is incredibly useful as it enables timely, informed decisions regarding ordering and reordering and prevents mid-job equipment shortages.
This is crucial for on-site productivity as it helps you ensure workers have just enough resources to do their jobs properly and without significant delays.
Deepak Tiwari, COO at KSH Logistics, a company setting up multi-client warehouses across India, goes a bit deeper into the benefits of inventory tracking:
“Proper inventory tracking helps to reduce stock-outs and overstocks, which in turn helps to maximize customer satisfaction through timely product delivery. […] It is, therefore, crucial for businesses to carefully control and manage their inventory in order to ensure continued success and survival of the company.”
While Tiwari discusses inventory management in terms of logistics and warehousing, the same can be applied to almost any industry, including construction.
Monitoring and maintaining optimal stock levels is an absolute must to avoid cost overruns from over-purchasing and operational setbacks caused by understocking.
That’s where inventory data plays a huge role. It gives you an accurate and complete picture of your material and equipment levels.
As a result, you can easily ensure the right assets are always available right when and where they’re needed, minimize waste, and completely avoid expensive, last-minute orders.
It’s the ultimate formula for running smooth, cost-effective operations.
Compliance and Regulatory Data
Compliance and regulatory data entail all sorts of information that demonstrates your assets are being used safely, sustainably, and following relevant laws and regulations.
Some examples include:
- Maintenance and inspection histories
- Certifications
- Audit trails
- Environmental data (e.g., emissions)
- Hazardous material storage and handling procedures
When the inspection time rolls around, this is the kind of data auditors will be looking for.
If you don’t have it, or if it’s inaccurate and outdated, you could face serious legal trouble and all kinds of costly fines.
One quick look at OSHA’s penalties is enough to realize just how important it is to stay compliant with industry rules and regulations.

And keeping track of relevant asset data is part of ensuring compliance.
In 2023, a New Jersey contractor learned firsthand how serious these fines can be.
They were fined over $1 million due to “lack of fall protection and failure to ensure the use of eye protection and four serious violations for unsafe scaffolds and failure to provide hard hats for overhead hazards.”
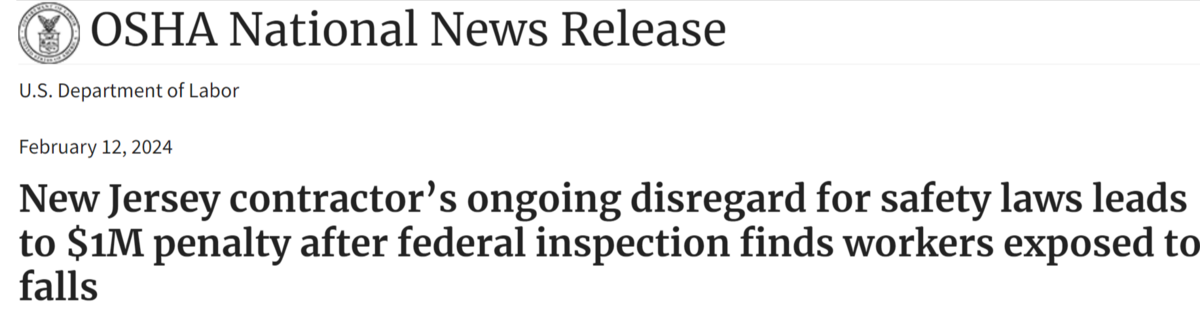
Had they used asset tracking software, they could have attached safety checklists to equipment-related tasks, and they might’ve noticed these areas for improvement much sooner.
In addition, their internal audits would’ve been much more streamlined, and when the inspectors came, they would’ve simply shown them all the relevant information and reports.
No fines. No problem.
Remember, these external audits can happen at any time, without prior notice.
And inspectors won’t have much patience if you can’t find proof of protective equipment use or the heavy machinery maintenance log.
But with asset tracking, you can have all that information in one, easily accessible place.
Financial Equipment Data
This type of data provides a financial overview of your assets, detailing their initial acquisition costs, operating expenses, as well as depreciation.
Some asset tracking systems, like our GoCodes Asset Tracking, even offer advanced reporting features that transform this raw, complex data into visually compelling, easy-to-understand insights.
For example, the pie chart below breaks down purchase costs for different equipment types.
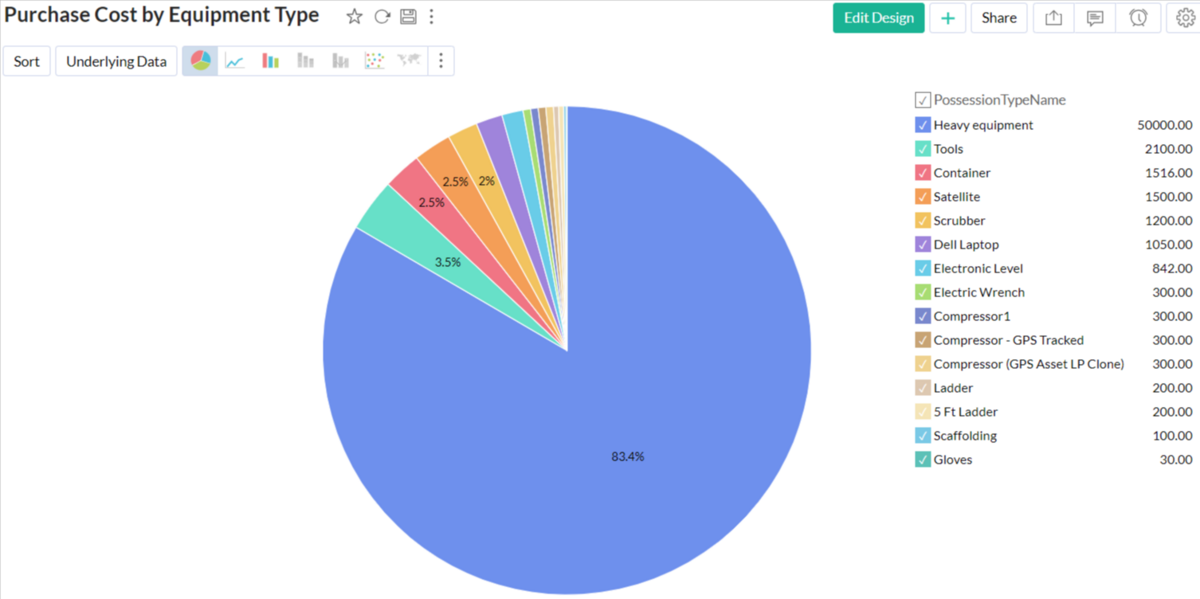
This allows you to quickly see which asset is costing you the most and what percentage it contributes to your total equipment expenses.
GoCodes Asset Tracking can also calculate depreciation for you.
You just need to input some basic information—such as an asset’s cost, purchase date, and lifespan—and the software calculates depreciation using a range of common IRS MACRS schemes.
It generates a Microsoft Excel-compatible .csv file that includes each item’s depreciation details, like:
- Annual depreciation
- Current year depreciation
- Prior year depreciation
- Total depreciation to date
- Balance remaining to be depreciated
Having access to all this financial data simplifies planning for the future.
For instance, Cristian Sebastian Fernandez, Superintendent at Linbeck Group, a Texas-based construction firm, explains how those insights help prepare for upcoming projects.
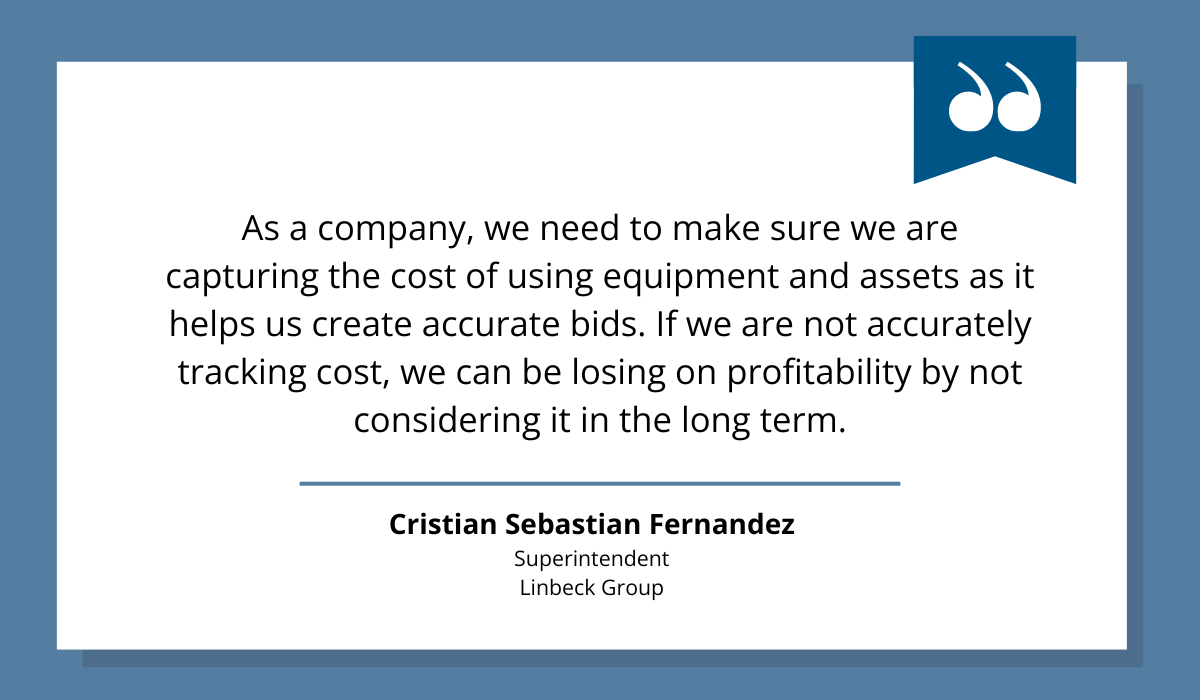
That’s right. By understanding past equipment, tools, and material costs, you can create bids that are both competitive and accurately reflect the true expenses of project execution.
The same principle applies to budgeting—using data from similar projects, you can forecast future costs and develop more realistic budgets.
Financial data also aids in assessing equipment life cycles and making more informed choices about their acquisition, repair, and disposal.
Lee Lackey, Product Manager at Noregon, a company providing maintenance solutions for commercial vehicles, sums up what these decisions are about very well.
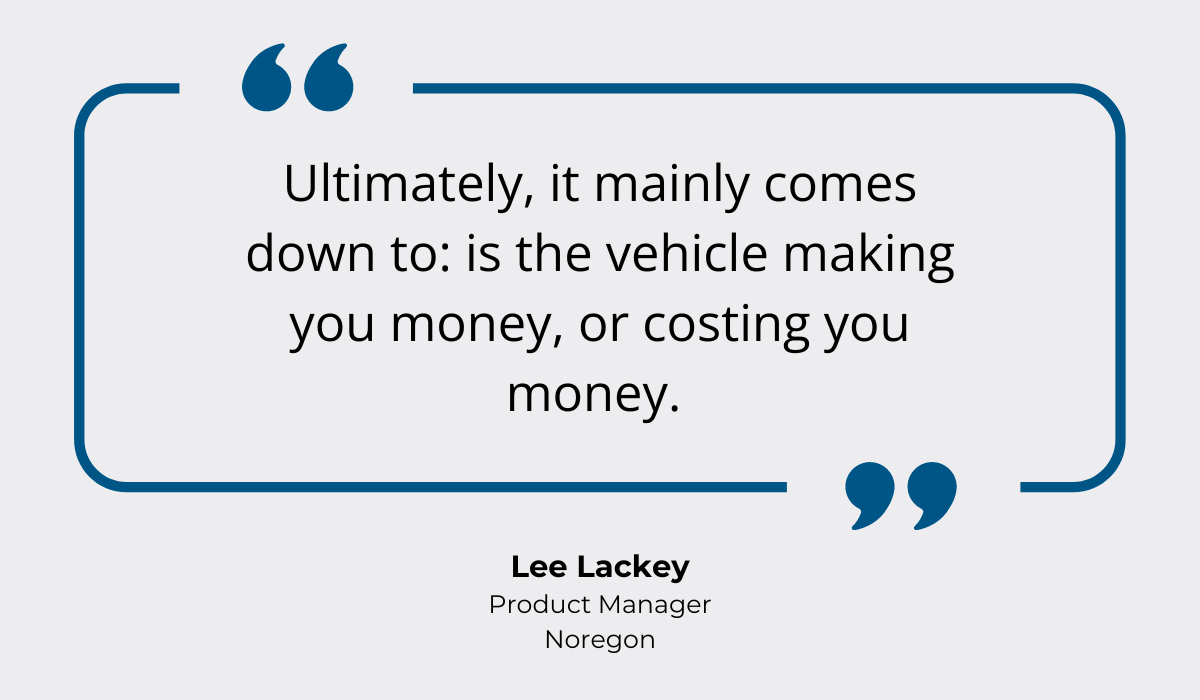
He also goes on to explain that to determine whether an asset will stay profitable, various factors must be considered, like its age, depreciation, repair costs, resale value, operating costs, and so on.
In short, you need reliable financial information to make these calls.
Thad Pirtle, VP and Equipment Manager at Traylor Bros., a heavy civil contractor, offers a specific example of how such data helps when you need to decide whether to replace or repair an asset:
“When you bought a backhoe for $80,000, and you run it for seven years, and its first life is done, you’ll look at the replacement on that and it’s, say, $200,000. If you only need a backhoe to run 400 to 500 hours a year on a small job, then you probably don’t need a $200,000 backhoe. You can probably take that $80,000 unit and refurbish it for $20,000 to $25,000 and do the job.”
Overall, financial data powers all kinds of important decisions in construction, related to both asset and project management.
As such, it’s indispensable for boosting your bottom line, winning more bids, and maximizing asset ROI.
Conclusion
As you can see, asset tracking offers so much more than just location data, as many assume.
It provides a wealth of information that can improve your decision-making across all aspects of asset management.
In fact, those who learn how to use this data strategically, manage to slash costs, boost operational efficiency, and even extend the lifespan of their assets.
After all, you can’t properly manage what you don’t track, right?