You don’t need to be involved in the construction industry to see that the prices are going up.
However, the construction sector is particularly affected by rising prices of all inputs—labor, equipment, fuel, and materials.
What’s more, the rising demand for construction materials is either causing or exacerbating supply chain disruptions and materials shortages.
Against this backdrop, we’ll look at why materials prices are rising, what contractors can expect going forward, and what they can do to deal with high construction materials prices.
In this article...
Why Are Construction Prices on the Rise
The prices of construction materials are still on the rise due to supply chain issues caused by the global pandemic, labor shortages, geopolitical factors, and energy cost increases.
When the first wave of the Covid-19 pandemic hit, many factories were forced to shut down temporarily, which slowed the production of various construction materials and products and created supply disruptions across the globe.
At the same time, lockdowns created a growing demand for materials and labor, as many homeowners either started home improvement projects or looked for single-family houses that facilitated social distancing.
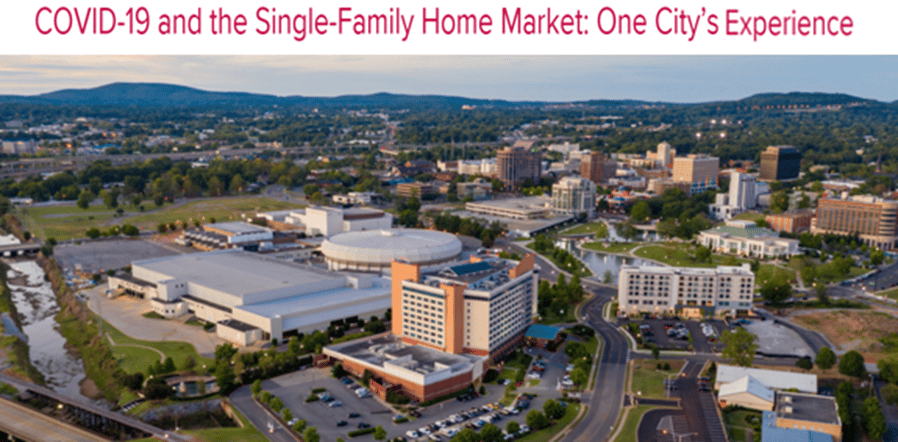
Moreover, governments around the world amped up major infrastructure projects to help their construction sectors deal with the pandemic fallout.
Naturally, this put even more pressure on supply chains.
As the higher demand clashed with lockdowns, supply issues, and movement restrictions caused by the pandemic, this drove up materials prices worldwide.
According to Oxford Economics, this mismatch between supply and demand is the primary driver of higher construction costs that increase the risks of project budget overruns and delays or even cancellations.
After the initial lockdowns subsided and the construction industry started to rebound, geopolitical factors like the war in Ukraine and China’s zero-Covid policy hindered this recovery process by exacerbating supply issues and triggering energy cost increases.
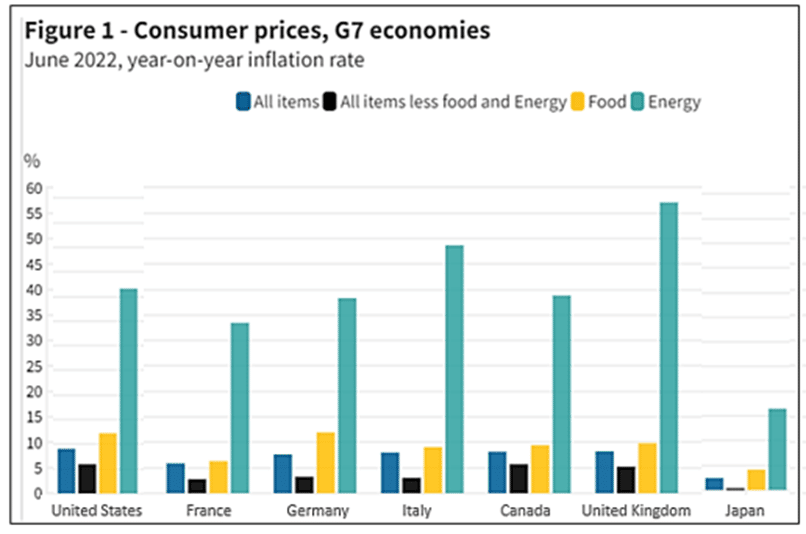
Thus, although many contractors hoped this year would bring back some stability and provide relief from rising prices, materials shortages, and transport issues, the ongoing geopolitical crises crushed their hopes, causing new supply chain disruptions and hiked-up costs.
To quote Associated Builders and Contractors (ABC) Chief Economist Anirban Basu:
“As long as you have supply chain issues, you still have price escalations.”
Overall, despite increased demand and new government spending, the global construction industry is faced with a perfect storm of issues—global pandemic, labor shortage, geopolitical factors, and energy cost increases—that are keeping construction prices on the rise.
What Materials Are Affected
A short answer to the above question would be all of them.
What’s more, although prices of some materials like timber have recently come down, they’re still higher than before the pandemic and are expected to continue to rise.
Since the pandemic started in late 2019, let’s first see how it affected the prices of construction materials and other inputs like fuel and transport between 2020 and 2021.
The following table was prepared by the Associated General Contractors of America (AGC) based on the U.S. Bureau of Labor Statistics (BLS) data:
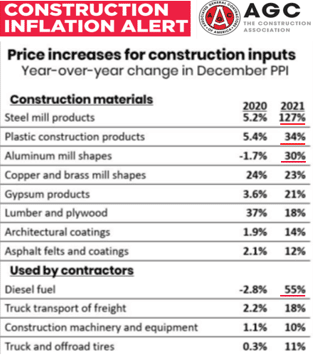
As you can see, the prices of steel mill products exploded and grew by 127% in 2021 compared to 5.2% in 2020.
Other notable price hikes include construction plastics such as insulation, pipes, doors, and windows (34%) and aluminum profiles (30%).
As for other construction inputs, the price of diesel fuel went up 55% even before the war in Ukraine.
Moreover, the pandemic-induced price increases were exacerbated by certain events that further jeopardized the availability of some construction materials.
For instance, in February 2021, Texas experienced a big freeze that damaged many petrochemical factories, which led to shortages of the resins needed for producing plastic construction products.
Another factor that drove up some prices is higher import tariffs on construction materials like softwood lumber, steel, and aluminum.
And naturally, all of these events were overshadowed by the Russian invasion of Ukraine in February 2022.
The resulting sanctions further increased the prices of aluminum and copper since Russia is among the leading producers of these metals.
Furthermore, energy prices went through the roof and led to increased prices of construction materials such as cement, concrete, steel, and plastics, which their producers transferred to final users.
To sum up, a number of health and geopolitical factors are currently causing supply chain issues and affecting the prices of most construction materials.
What to Expect Going Forward
In this section, we’ll look at what to expect in the following years in terms of construction costs for both materials and labor.
We’ll first examine the current situation with workers in construction and other related industries, as they are directly and indirectly associated with materials prices.
Labor Costs
In a nutshell, labor costs are expected to remain high in 2023 due to the serious lack of construction workers and rising living costs, which are pushing wages up.
When the pandemic hit, many contractors were forced to cut the number of employees, and many construction workers left the industry and never returned when the economy started to rebound.
This only worsened the long-standing issue of skilled labor shortages that have been plaguing the construction industry worldwide, but most notably in the U.S.

In the words of Ed Brady, president of the Home Builders Institute:
“The construction industry needs more than 61,000 new hires every month if we are to keep up with both industry growth and the loss of workers either through retirement or simply leaving the sector for good”.
This means that the U.S. will need an additional 2.2 million new construction workers from 2022 to 2024.
This very high demand, coupled with the described labor shortages, and rising living costs, are directly related to increased labor costs because skilled workers are highly sought after, and construction companies are willing to pay more to attract those workers.
When we add to this a series of new publicly funded projects planned under the Infrastructure Investment and Jobs Act, it’s clear that construction labor costs will continue rising in 2023 and beyond.
Materials Costs
Even though some construction materials are slowly becoming more available, their supply still can’t match the demand due to multiple factors that contribute to supply chain disruptions.
This means that the cost of construction materials will remain high in 2023.
However, the rising costs of labor and materials, together with the expected interest rate hikes, are causing a slowdown in demand that could bring some materials prices down, but the related supply issues will continue.
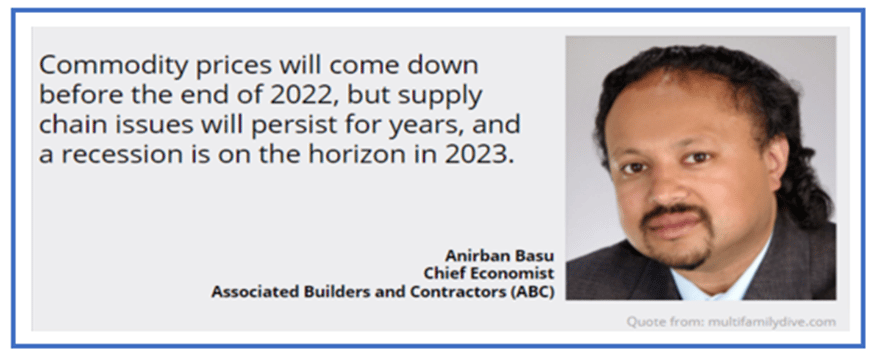
In other words, the high demand in both residential and commercial construction, on one hand, and supply chain disruptions, energy costs, and labor shortages, on the other, are the primary factors that continue to push construction costs up.
Basu emphasizes that, even if Covid disappeared and the war in Ukraine ended now, many supply chain issues would continue in 2023 and even 2024 as it takes time to build back the capacities for production and transport of construction materials and deal with all those backlog orders.
To sum up, although the prices of some construction materials should come down, the growing demand and uncertain supply imply that the prices of construction materials won’t stabilize any time soon.
How to Deal With the High Prices of Construction Materials
Since construction materials prices are not expected to go down any time soon, contractors should plan and budget their projects accordingly, develop close working relationships with suppliers, look for alternative materials, and, above all, remain flexible and creative.
In other words, to quote Mischa Fisher, Angi’s chief economist:
“With so much uncertainty around manufacturing slowdowns, supply chain disruptions, scarce product availability, and volatile prices, building in flexibility and advance planning into your projects is more important than ever.”
Naturally, to plan ahead and pre-order the materials, you first need your project cost estimates to be as accurate as possible.
From there, you can utilize one or more of our tips on how to save money on construction materials:
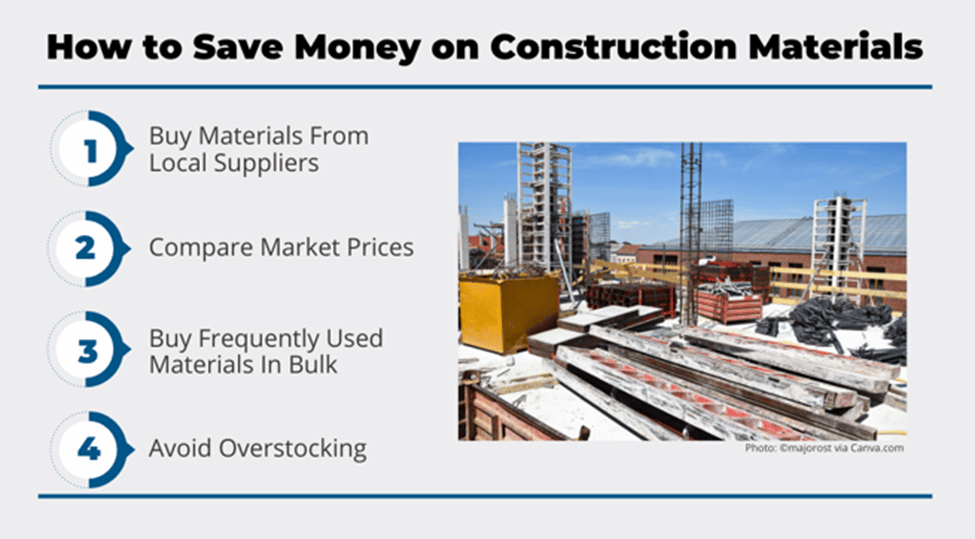
For instance, if the materials you need for a future project can be sourced locally, you can save money on supply chain costs (transport, handling, and storage).
In addition, buying locally will give you more flexibility in case the quantities of some materials were miscalculated and you need to order more.
It will also ensure a closer relationship with the supplier, which can go a long way when addressing issues or getting the best price.
Furthermore, you should ensure a reasonable stockpile of frequently used materials like concrete, drywall, framing, and siding materials, but avoid overstocking some custom materials or products that might be left unused or lose their efficacy.
However, to take advantage of the above tips, you need to keep track of your inventory of construction materials.
One way to do that is by using inventory tracking software that will give you a clear picture of your current inventory levels and provide low quantity alerts, thus ensuring you don’t run out or overstock materials.
One such cloud-based inventory and asset tracking solution is GoCodes.
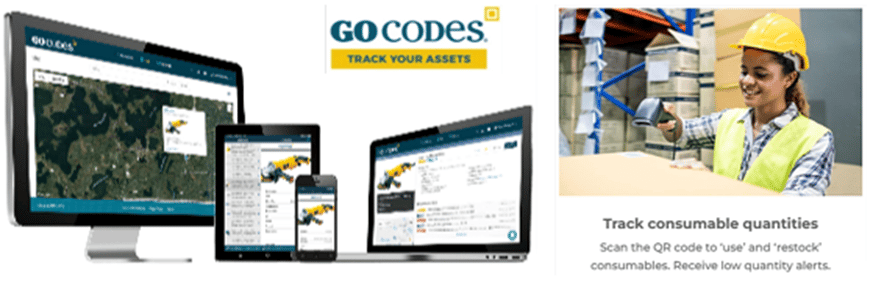
Once you know precisely what materials you have in stock and what materials you’ll need for projects down the pipeline, it allows you to plan for purchasing materials in advance.
Moreover, it allows you to be flexible and manage your clients’ expectations in the project budgeting phase.
For instance, if some project materials are unavailable or too expensive, you and the client can agree on alternative materials that are available, preferably at a reasonable price.
Other than that, maintaining solid working relationships with your suppliers can help you get the best price or give you a heads up on probable materials shortages, thus allowing you to be creative and address potential issues even before they occur.
Naturally, nobody knows when the supply of back-ordered materials will stabilize or which materials could be in short supply next.
That’s why it’s advisable to keep track of your materials inventory, plan and budget your projects in advance and take advantage of different cost-saving opportunities.
Conclusion
After taking this stroll through why construction costs are rising, what materials are affected, what to expect going forward, and how to deal with high materials prices, keep in mind that, despite many current supply challenges, most of the issues arise from high demand for construction materials and quality contractors who know how to use them efficiently.