Procuring and monitoring construction materials constitute a fundamental part of a construction project budget. Therefore, companies need proper methods and strategies to deliver quality projects within budget.
But while people mainly associate construction material management with purchasing and delivering construction material, the reality is more complex.
Material management actually covers a wide range of activities, technologies, and processes which serve to optimize purchasing, storage, and utilization of materials.
In this short guide, you’ll learn the basics of construction material management, so you can start optimizing your company’s processes.
Let’s start!
In this article...
What Does Material Management in Construction Imply
Construction material management is the process of procuring, allocating, and disposing of construction materials.
It covers a wide variety of activities, but ultimately, its main purpose is to source materials on time and at a reasonable cost to be utilized in every construction project.
It’s safe to say that this process is vital for every construction project since it ensures meeting project goals.
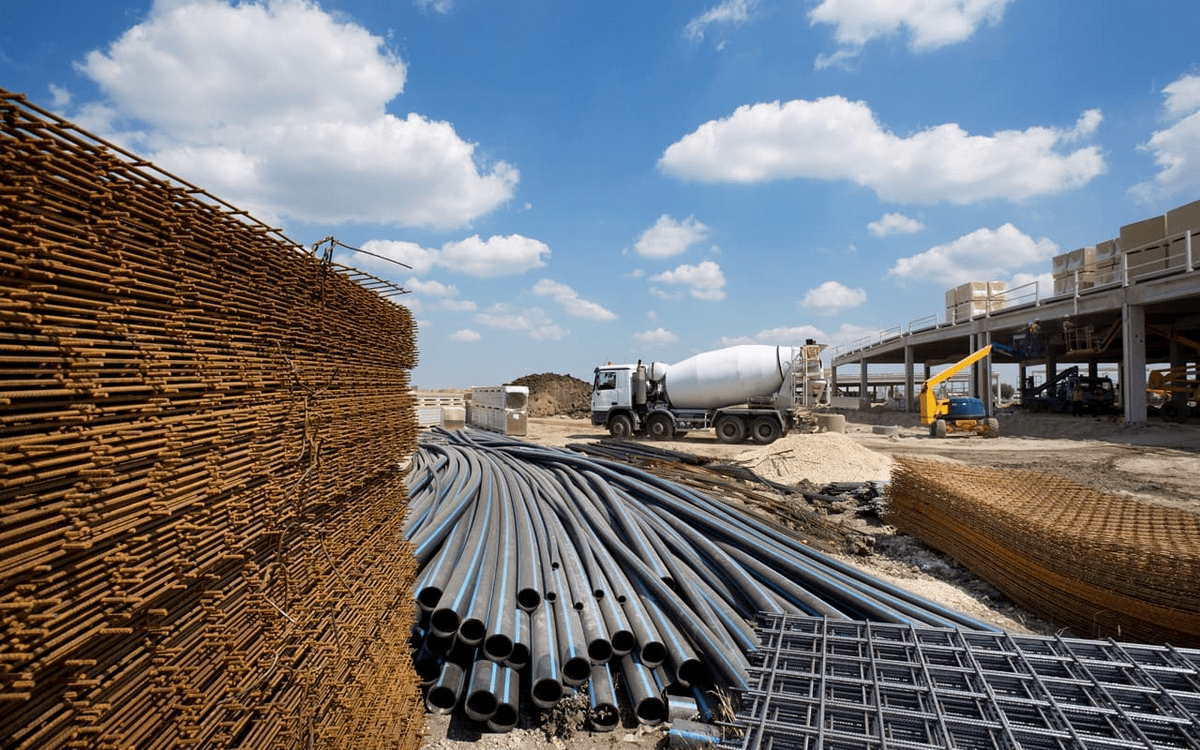
Otherwise, if you don’t have a good construction material management strategy, you’ll likely risk decreased labor productivity, material waste, and breaking the project’s budget and deadlines.
Effective construction material management usually consists of the following basic activities:
- Planning and acquisition of materials
- Scheduling and transportation
- Quality control
- Storage and inventory management
- Waste management
Remember that coordinated construction material management activities can significantly boost your company’s operational efficiency and help you grow.
Objectives of Material Management
As mentioned before, your main goals with construction material management should be ensuring the optimal supply of materials, inventory control, and improved project operations.
But how do you do that?
To start, you can follow the Five Rights (Rs) in construction material management. This formula covers the main objectives of material management and can help you plan and execute your material management strategies.
Here’s what they are:
Right Materials | Find materials that fit the project requirements in terms of quality, type, and purpose. |
Right Quantities | Ensure you order materials in sufficient amounts to meet the project demands. |
Right Time | Ensure you order your materials on time, so they arrive right before you need them on the construction site. |
Right Place | Avoid double handling and ensure the right materials are delivered to the right construction site. Furthermore, if the job site is large, have a dedicated delivery point where the workers will collect the materials. |
Right Price | Get multiple quotes and compare prices when purchasing building material. Ensure you get competitive and affordable prices to maximize profitability for your construction company. |
All in all, these objectives should ensure that you lay down the basic guidelines for managing construction material.
Examples of Construction Site Materials That Need to Be Managed
Which materials you need to manage will depend on the type of construction business you’re running.
For example, it might be more important for a painting business to stock adequate levels of paint and related supplies, whereas a carpentry business will need to keep different types of wood in its inventory.
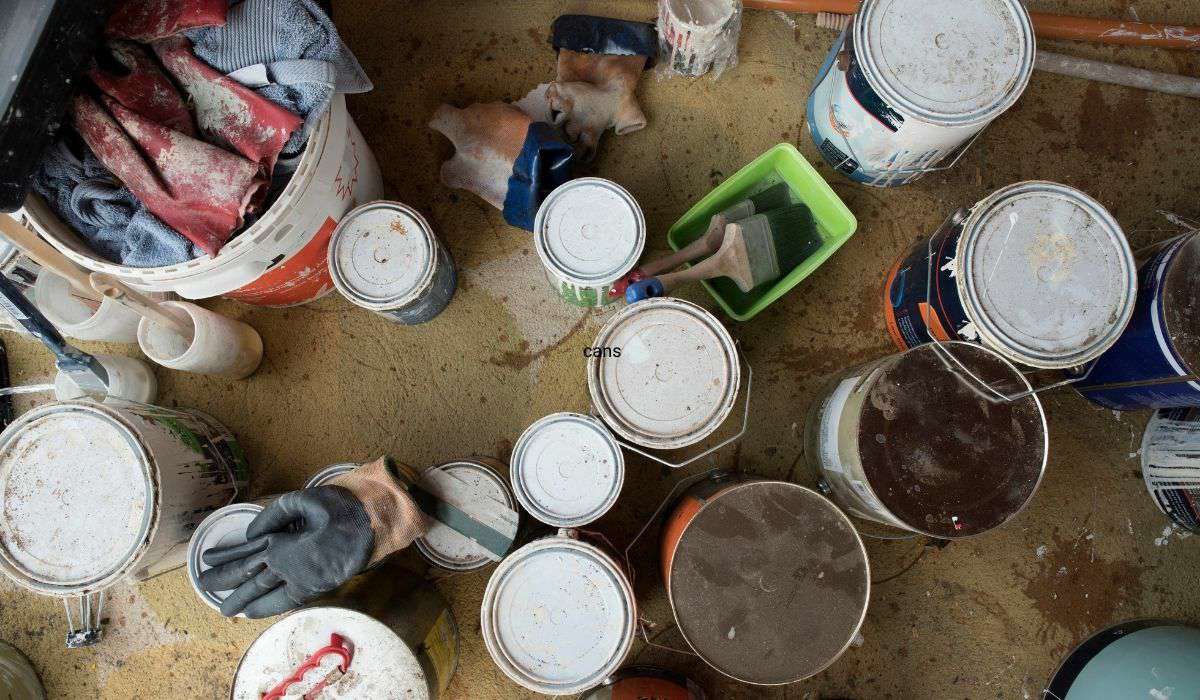
But generally, there are materials commonly used in the construction industry that need special attention from managers to prevent shortages and ensure effective distribution.
For example:
- Cement
- Timber
- Stone
- Bricks
- Steel
In recent times, high levels of demand for these materials have caused severe shortages in the industry. So it’s necessary to streamline the management of your construction materials to avoid the same troubles.
It all boils down to selecting the right materials and replenishing your inventory on time to meet the construction project’s deadlines.
Benefits of Proper Material Management in Construction
If you’re wondering how exactly construction material management can help you, the following sections will describe its most important benefits.
Improved Productivity
When workers are compelled to sit around waiting for construction materials to arrive, it kills worksite productivity. Every minute they’re not working is a minute that unnecessarily extends the duration of the project.
Furthermore, you’re wasting money on unproductive labor. That way, you’re not just jeopardizing the project schedule, but your costs are going up as well because those idle minutes will extend into overtime you’ll eventually have to compensate for.
But effective material management can mitigate this problem. Essentially, when workers have materials and supplies at the right time, they will finish their tasks faster and keep up with the project goals.
The way you store your equipment and materials is also an important factor.
You don’t want to waste your workers’ time and energy by storing your materials too far from the construction site, so they take too long to get what they need.
Maximizing worksite productivity is one of the best ways to finish projects on time and within budget. Therefore, material availability and efficient management are crucial to minimizing disruptions.
Lower Project Costs
Logically, once you maximize onsite productivity and coordinate material delivery, your overall project costs decrease.
A good material management strategy includes active communication and proper scheduling. The right people need to be informed about the deliveries to receive the materials and inspect their quality.
That way, if something goes wrong, they can send them back and reorder the right ones as soon as possible.
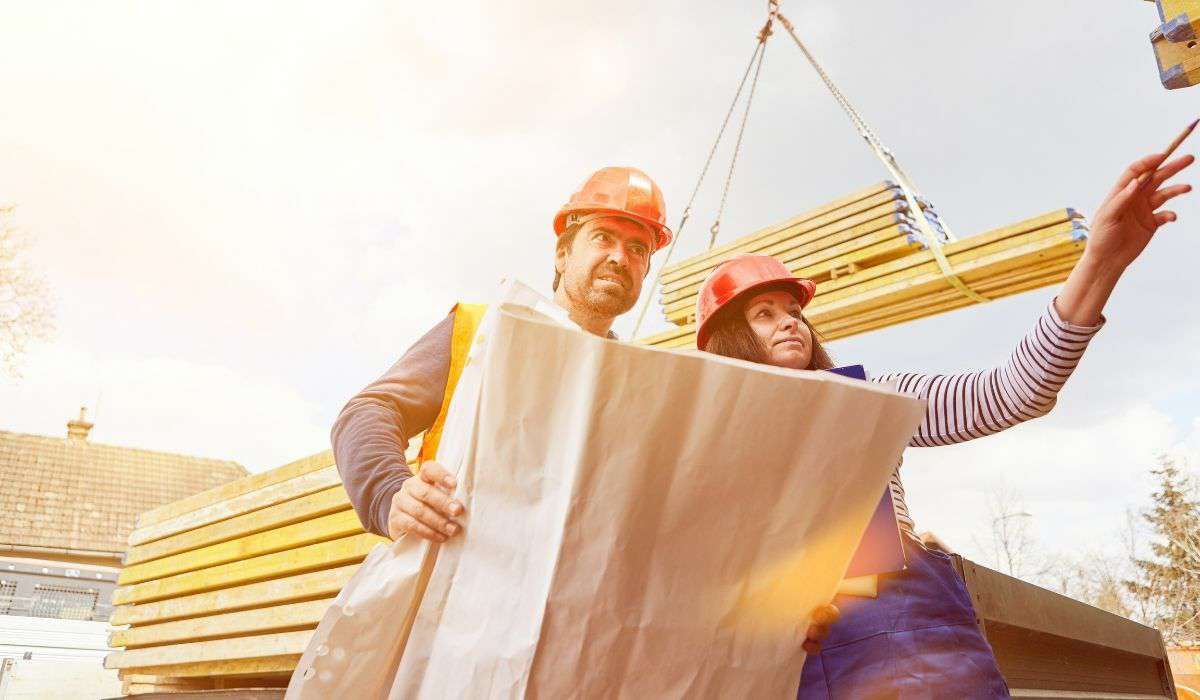
Also, the less materials have to travel, the better. With an appropriate storage facility, you’ll avoid duplicate handling and minimize the risk of damaging valuable goods by moving them too much.
Remember that timely delivery, as well as minimizing errors and disruptions, will positively impact the overall project costs.
Better Budgeting
Working within a predetermined budget is vital for contractors. It means that you’re able to utilize the resources you’re given and deliver a quality project simultaneously.
Following that, once you establish project requirements and material needs, budgeting becomes more accurate. You can find better discounts and purchase in bulk, thus lowering material costs.
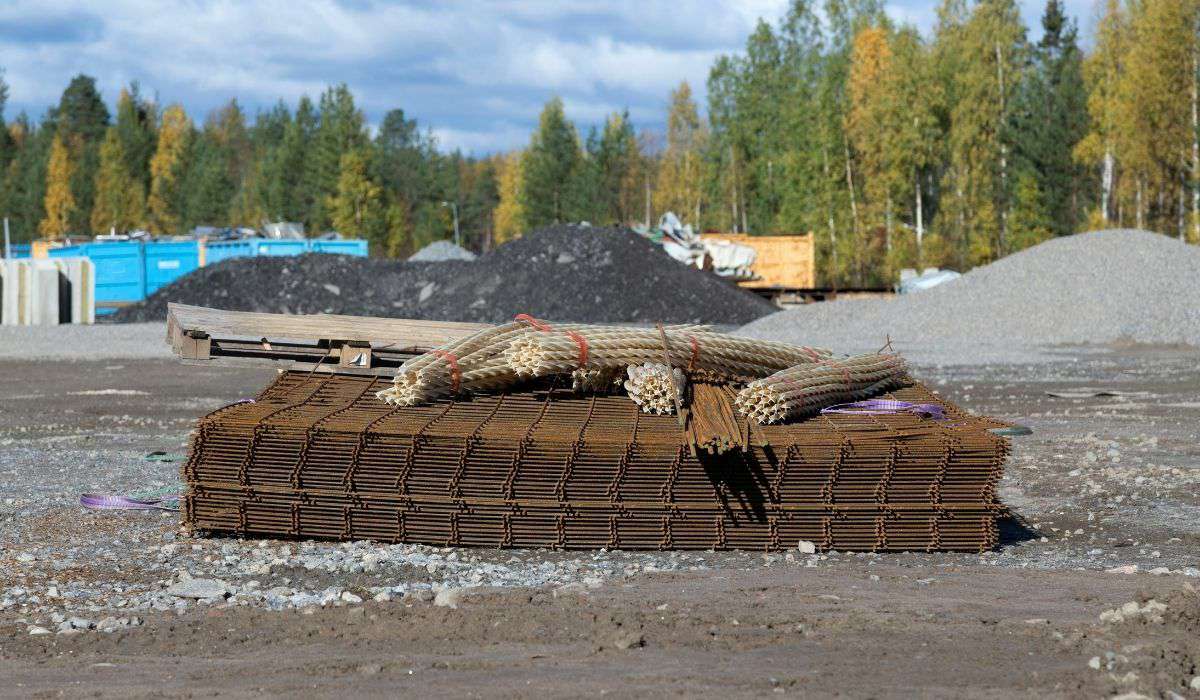
If you don’t have a good grasp of the kind and the amount of the materials you need, you’re likely to overspend.
With comprehensive construction material management, you’ll be able to forecast future project material needs better and maximize profitability for your company.
Construction Material Management Tips for Best ROI
Here are some of the best practices you can adopt to reap the benefits we’ve outlined previously.
Regularly Monitor Your Inventory
Finding out you don’t have enough resources to finish a crucial construction task you’re in the middle of is the worst that can happen to a contractor.
So, regularly updating your inventory records is necessary.
One way to do that is by utilizing technology. Most companies use asset tracking software to have a comprehensive overview of their inventory so they can order materials on time.
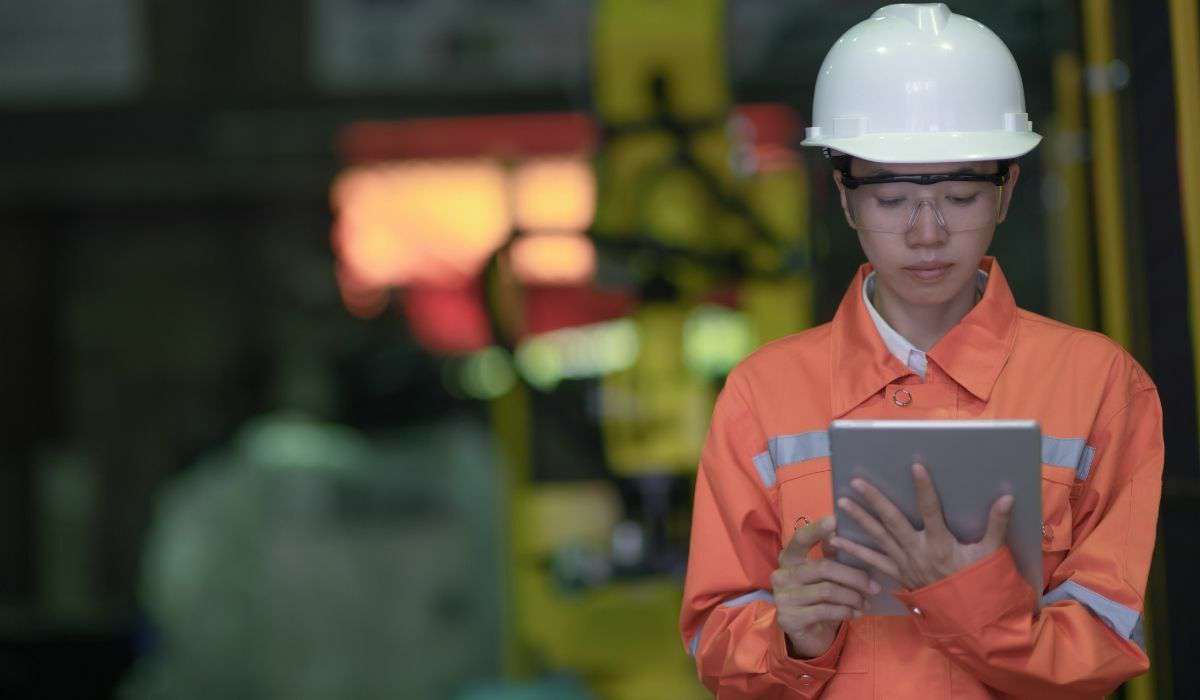
When it comes to material inventory management, if you can’t find something, you can’t use it. Then you’ll probably make a duplicate order and waste money.
Therefore, regularly check your inventory levels to get accurate information about materials, so you can replenish your stock levels on time and avoid overordering.
Find a Strategic Supplier
According to Atillo Rivetti, vice president at Turner Construction, the best way to ensure you have the materials you need is to have a good working relationship with manufacturers and suppliers from the start of the project.
So, what should you look for in a construction material supplier?
First, it might be tempting to choose a low-cost supplier because you want to minimize your costs. But low cost doesn’t necessarily equal good material quality and timely service.
Sometimes it’s better to find a reputable supplier even if it costs you more, if it means they’ll deliver your materials on schedule and in the right quality and quantity.
The extra cost is unimportant if you’re able to deliver your projects on time and within budget.
Therefore, create good relationships with your suppliers. This means having open and transparent communication and resolving issues professionally.
Once you establish that, it’ll be easier to negotiate discounts, organize flexible deliveries and get insider knowledge on material shortages.
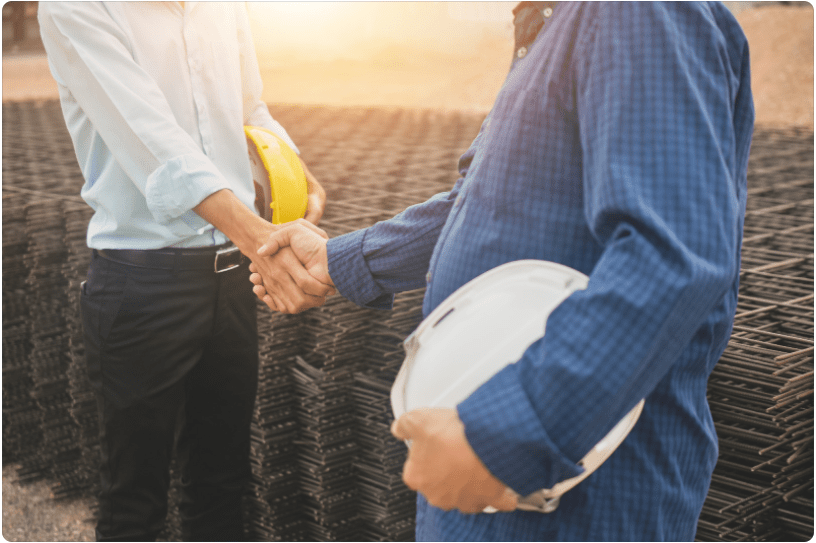
Of course, don’t forget about expertise. A good supplier will give you recommendations and advice about the most suitable materials for your projects if you’re unsure about the differences in quality or how to handle them correctly.
In the end, working with experts, you can rely on will give you peace of mind in your construction material management process.
Store Materials With Care
What is the use of procuring materials if you’re not going to take care of them? A vital aspect in efficiently utilizing construction materials is preserving their quality before use.
So you need to keep your materials in adequate storage conditions. This means putting them in a dry and ventilated facility and properly organizing them.
For example, the heaviest materials should always be placed on lower heights while the lightest materials can be put higher.
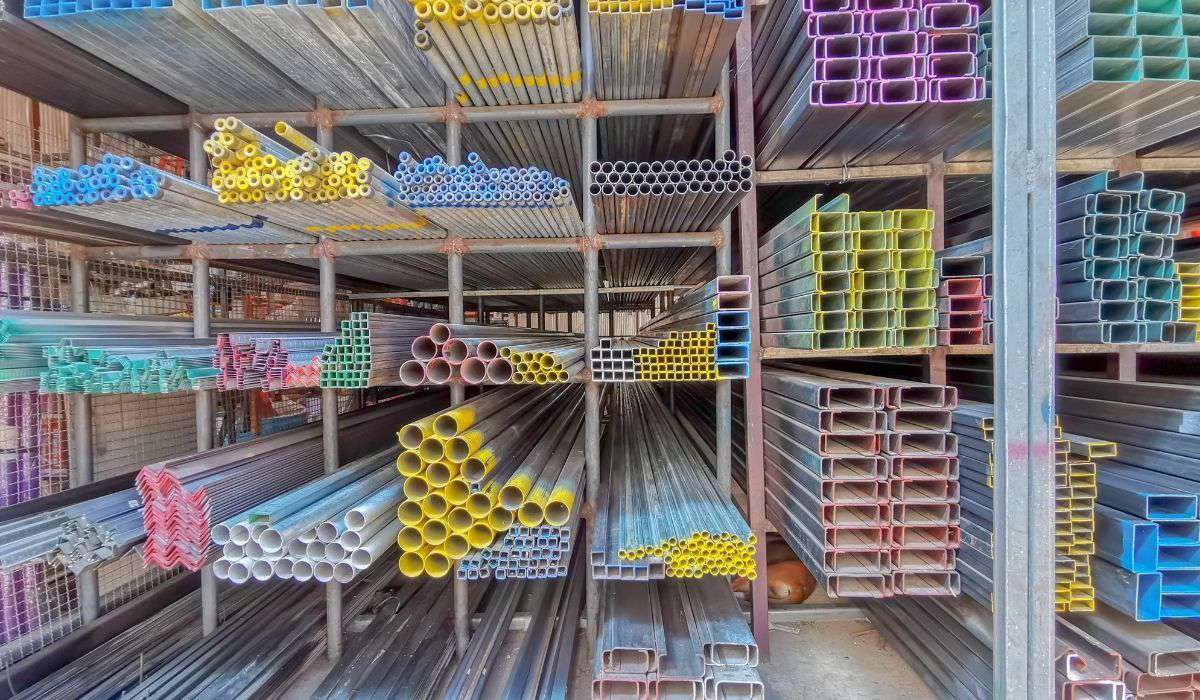
If you don’t have a storage facility, a simple but effective temporary solution is to put all your materials on a raised platform, or a pallet, so they’re not in direct contact with the ground and cover them with a tarp.
That way, they’re protected from extreme weather conditions and moisture.
Keep in mind that your storage arrangements should always serve to protect your materials, so you avoid damages and preserve their original quality.
Construction Material Management Software
Now that we’ve established why proper construction material management is beneficial for your company, the following question is: how do you simplify this process for maximum efficiency?
This is where robust construction material management software can help you.
If you want more visibility in your construction material inventory, procurement, and disposal activities, then consider GoCodes Asset Tracking’ asset management software. Here is how it works.
First, put a tracking identifier in the form of barcodes or QR codes on each material unit. These tags will have unique labels you can scan with any smartphone and get relevant information about the material.
For example, you’ll be able to see the quantity, location, the time of the last scan, and additional notes about the materials your workers left.
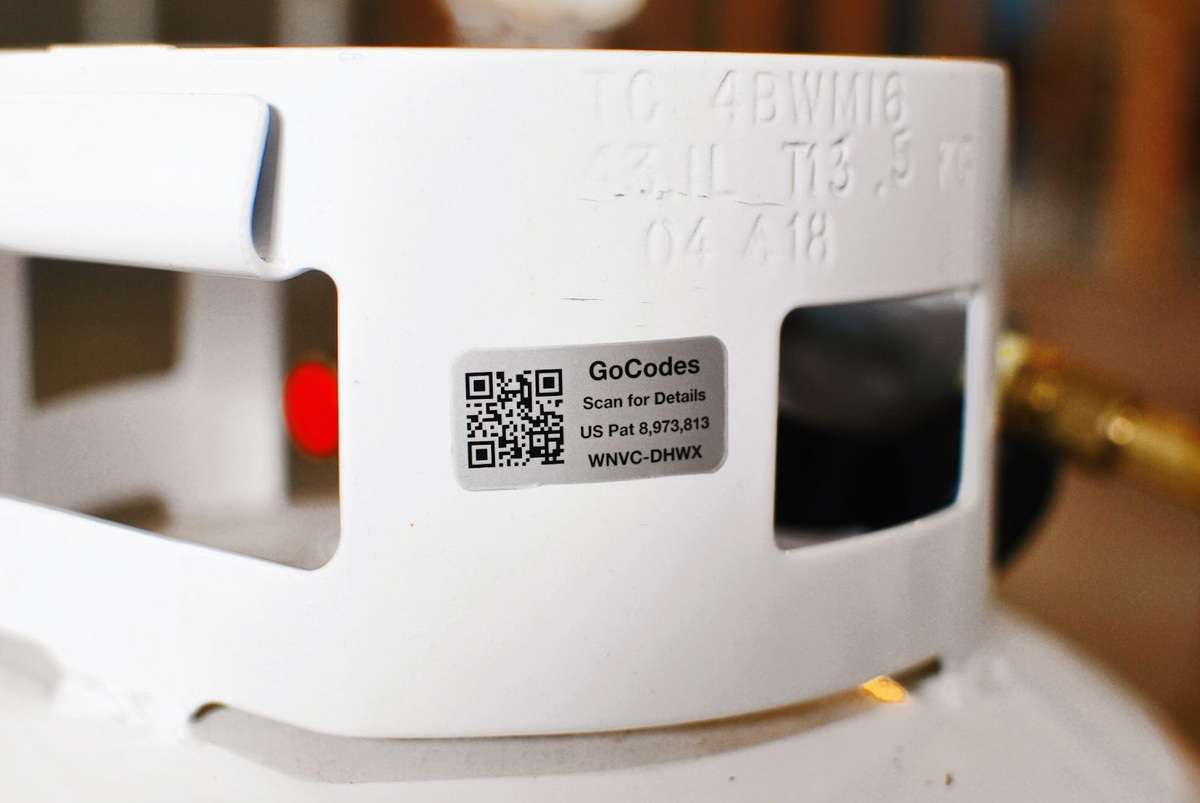
With these tags in place, checking materials in and out is easy, and the information is stored in the cloud. This allows you to see and review historical material data.
Additionally, automatic updates enable real-time visibility of your inventory, so you’re able to respond to low levels on time.
Furthermore, GoCodes Asset Tracking has a nifty feature where you can get low inventory email alerts if you set it in your account.
In other words, you’ll immediately know who used the last bag of cement and when, so you can order more if necessary.
In the end, GoCodes Asset Tracking is an excellent solution to cover the necessary tasks related to construction material management. You’ll get real-time information, streamline your operations and manage your materials more effectively.
Conclusion
Construction material management is a key process that connects different areas of successful project delivery. You’ll be able to meet project schedules, stay within budget and create a final product of desired quality.
But the first step is finding the right solutions to simplify this process and streamline core tasks. Leveraging technology is necessary to manage your inventory and have end-to-end control of your construction materials.
Hopefully, our guide has helped you realize the importance of construction material management, and you’ll use this knowledge to improve your business operations.