Key Takeaways:
- Overstocking and understocking are two of the most common inventory control challenges, but there are ways to minimize them.
- Inventory documentation is integral to successful stock control.
- To establish efficient inventory control workflows, construction companies should standardize their processes by using a QR code-based inventory control system.
Construction inventory control is very important. That’s something anyone can agree on.
Yet, as we delve deeper into this complex process, it becomes easy to get lost in a maze of questions.
How do you exactly ensure optimal stock levels throughout entire projects? How do you tackle the many challenges of inventory control? What tools are best suited for optimizing this process?
If you find yourself grappling with questions like these, worry not: you’re definitely not alone.
In fact, you just might be in luck, because this article is dedicated precisely to answering common questions regarding inventory control.
We explore the why-to and the how-to, as well as provide some interesting statistics and practical tips to take your inventory control process to the next level.
Without further ado, let’s dive in.
In this article...
How to Establish Effective Inventory Control Procedures on Construction Sites?
The way you handle your materials, tools, equipment, and consumables has a great impact on the overall operational efficiency across the construction site.
Therefore, without standardized procedures for inventory receiving, storing, issuing, and monitoring, the quality of your stock control suffers, resulting in a major drop in productivity.
Michael McGowan, region head and CEO of Hilti North America drives this point home, revealing that improper tool handling alone costs job sites approximately one day per month.
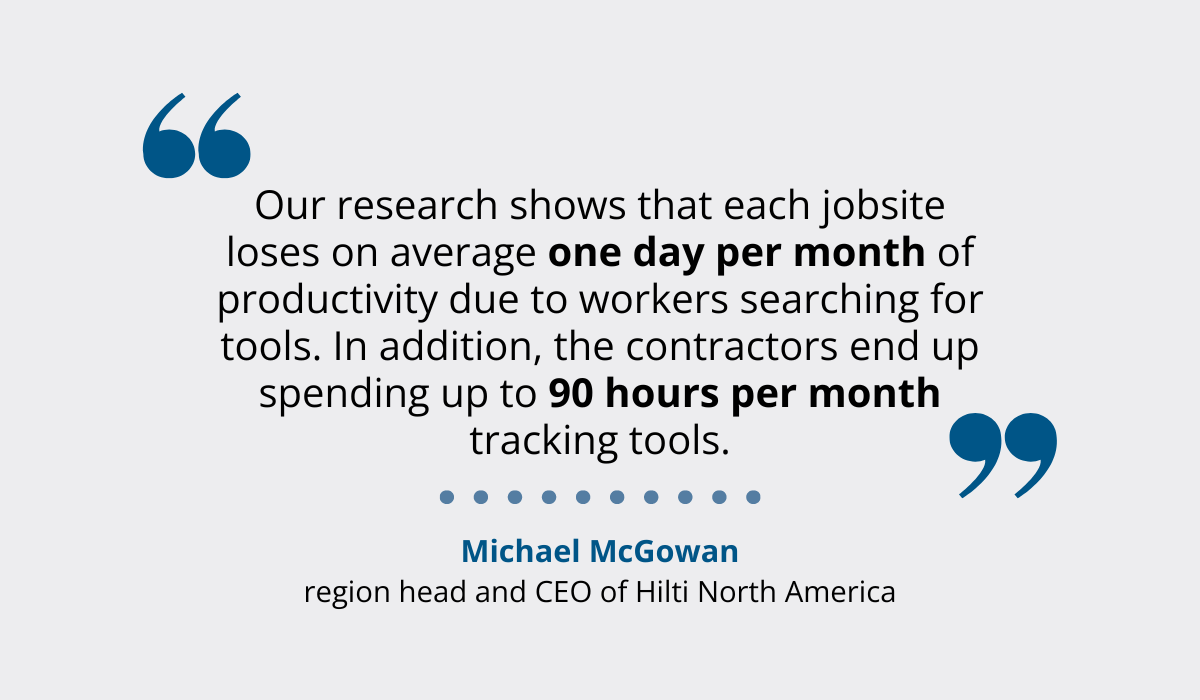
If the mishandling of small tools can have such serious consequences, imagine the chaos that the mismanagement of entire inventories can unleash.
Now, you may argue that developing and training the team on these complex procedures is equally, if not even more, time-consuming.
But, we’re here to tell you it doesn’t have to be that way.
The easiest and most effective way to standardize your inventory control processes is through automation.
Dedicated software solutions offer predefined workflows and procedures for various aspects of stock control.
They guide users through each step, thereby eliminating confusion, reducing errors, and ensuring thorough tracking of inventory-related activities.
This, in turn, results in:
- consistent workflow across the board,
- unified data entry that ensures data integrity,
- audit trails of all changes made to inventory records, and
- easier monitoring of inventory performance metrics, which reveals areas for improvement.
In short, technology brings order to the chaos of construction sites, enforcing consistency, transparency, and accountability.
Recognizing the complexity of stock control processes, we developed GoCodes Asset Tracking.
This QR code-based inventory control system enables workers to check machines and tools in or out, update inventory levels, track asset location, view maintenance history, request field service, and more, all through a simple yet efficient process.
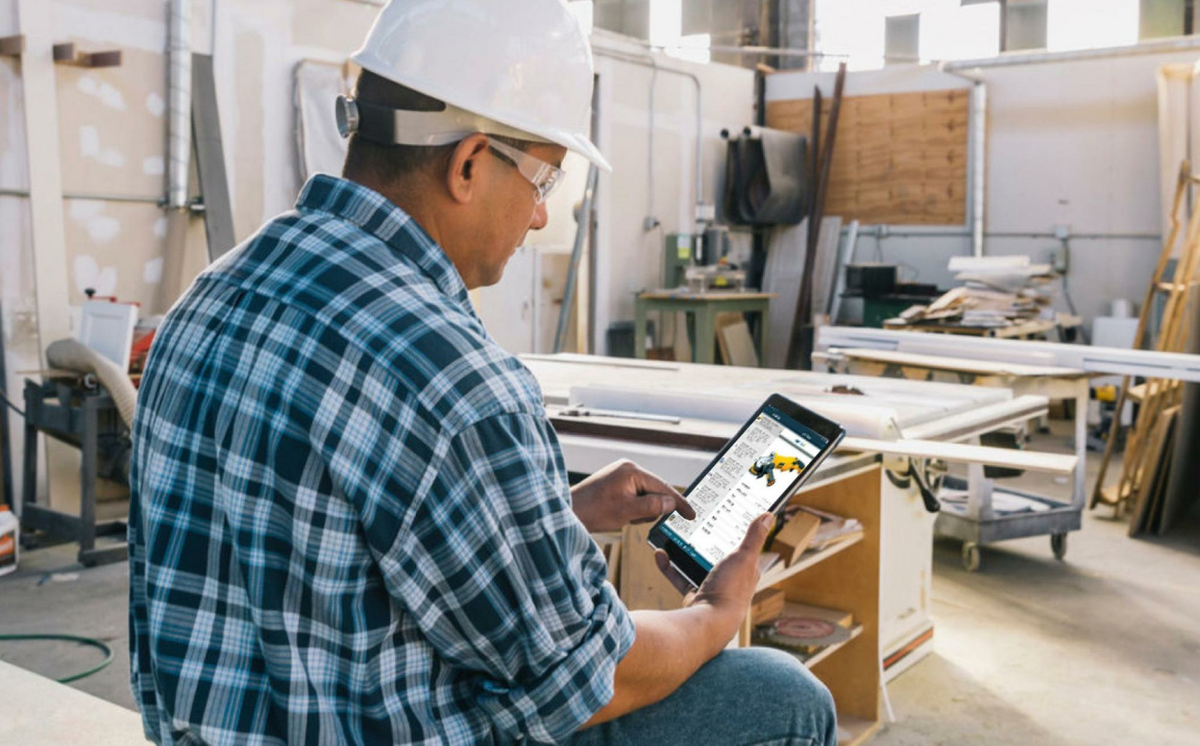
To use our solution, attach QR code labels to your assets and scan them with our app to update or view asset data.
Quick, easy, dependable, and consistent—a perfect fit for bustling job sites.
Workers quickly adapt to our user-friendly system, gradually building comprehensive stock records that centralize vital data, from quantities and conditions to salvage value and warranty information.
Plus, the software sends notifications for low stock levels, overdue equipment, and upcoming scheduled service, making sure that nothing falls through the cracks and that essential inventory control procedures remain on track.
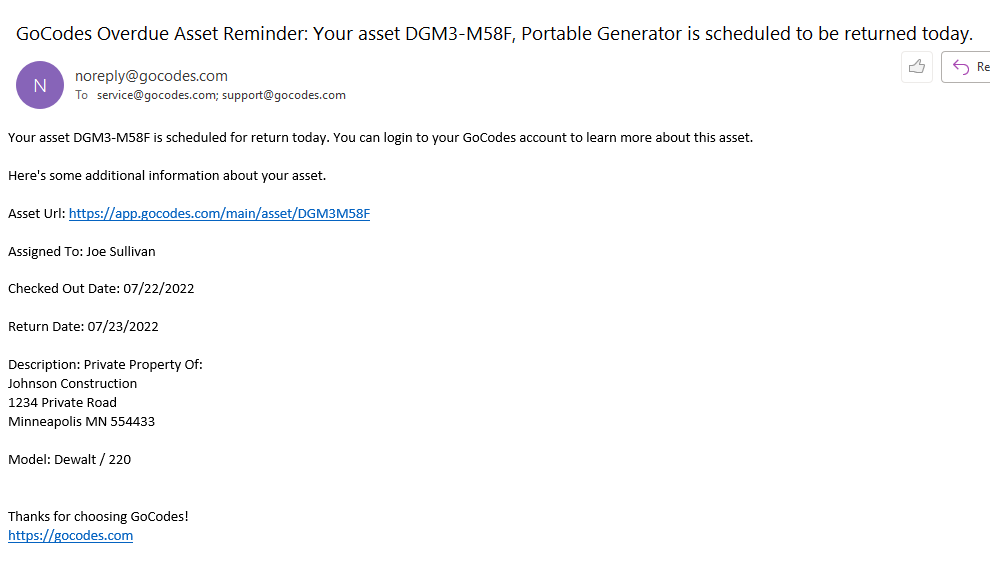
The bottom line is this: standardization of inventory control processes doesn’t have to be labor-intensive, complex, or time-consuming.
Nowadays, there are so many different software options aimed at making this important part of project management a breeze.
So, if you’re grappling with bringing structure to your operations, give these systems a thought.
They just might prove to be a real game-changer.
What Are the Challenges of Construction Inventory Control?
Keeping construction inventory in check is no walk in the park, that’s for sure.
Numerous challenges, both internal, like inefficient tracking methods, and external, such as unreliable suppliers, can seriously undermine stock control efforts and, consequently, project outcomes.
Think about it: your assets already cost you a lot of money as is.
According to a McKinsey survey, inventory procurement typically represents 40-70% of total expenditure for construction companies.
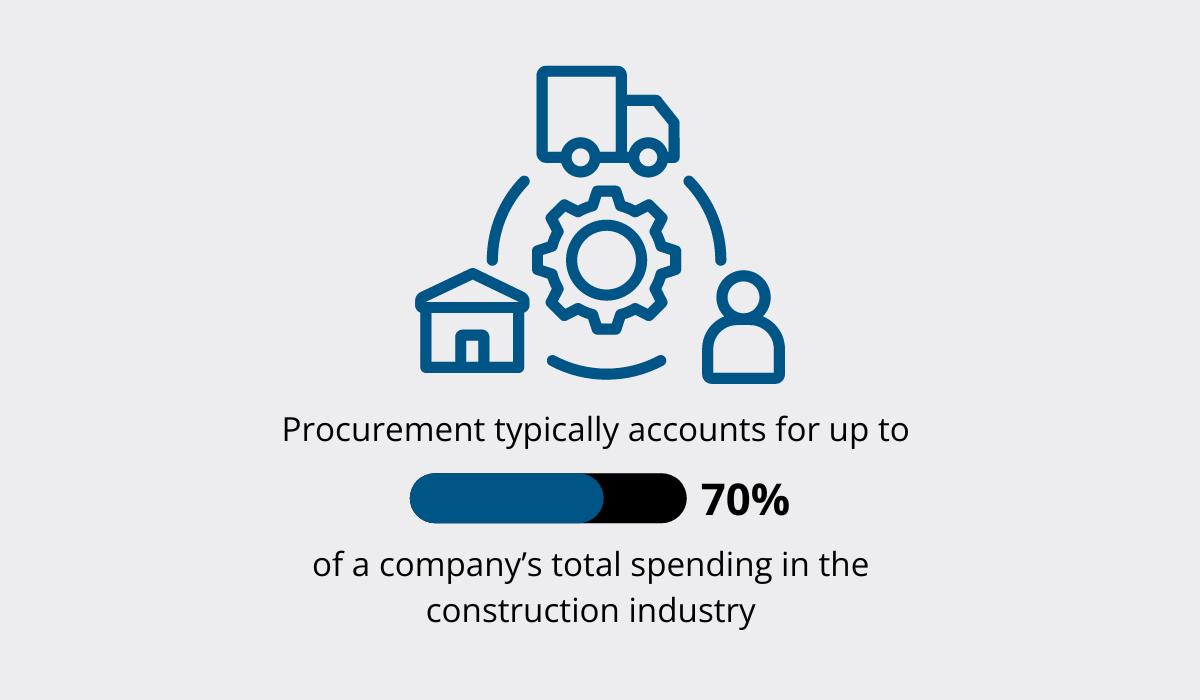
Do you really want to be adding to the financial strain?
Because that’s precisely what happens if you ignore inventory problems and don’t address them proactively.
Two main challenges in stock control are overstocking and stockouts, both of which can wreak havoc on budgets, schedules, and profitability in their own way.
Stockouts, for instance, can result in substantial project delays, dissatisfied clients, and even reputational damage.
Overstocking is just as harmful, leading to increased inventory-related costs, like storage, handling, and transportation expenses, thereby straining cash flow and causing budget overruns.
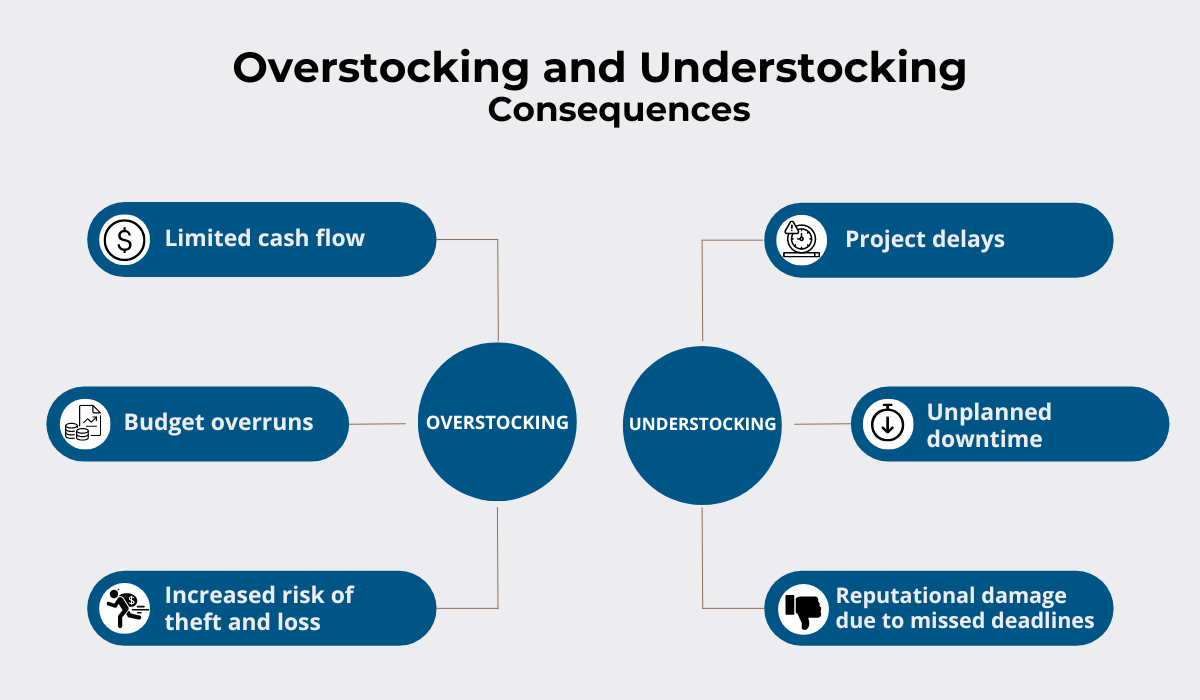
However, these problems don’t just pop up out of nowhere.
Instead, they usually stem from some underlying issues, such as lack of inventory visibility, theft problems, supply chain issues, and changes in project scope.
What does that mean?
Unfortunately, it means there’s no single solution that can solve all stock control problems with 100% efficiency and success.
An effective inventory control strategy needs to be multifaceted, involving vigilant monitoring of asset performance and movement, inventory forecasting, and diversifying suppliers to mitigate supply chain risks.
The most crucial thing to keep in mind, though, is to stay flexible and adaptable.
Being prepared to face unforeseen difficulties head-on is key, not just in inventory control, but in construction project management as a whole.
Remember, not everything will always go your way, but anticipating and preparing for potential trouble definitely puts you on the path to success.
How Does Inventory Control Minimize Stockouts of Key Materials?
Among all the challenges we’ve explored in the previous section, stockouts remain a top priority in inventory control.
The rationale behind this is clear: you can still keep on working if you have too many materials, but if you run out of something crucial midway through a project, you’re stuck.
That’s why significant effort is channeled into preventing or at least minimizing understocking, typically through three core processes:
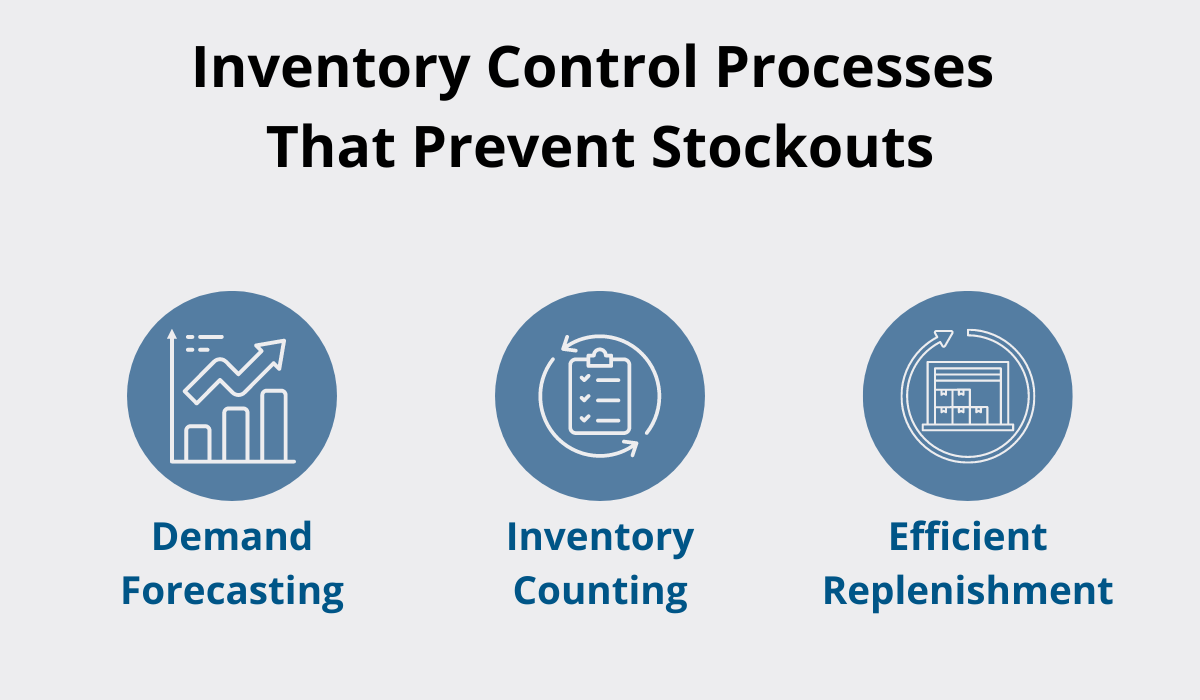
It all begins with demand forecasting.
The more accurately you can predict resource needs based on project scope and timelines, the less likely you’ll encounter problems with insufficient inventory during the project.
Software solutions like takeoff and estimating tools are typically used for this purpose.
Their robust data analytics capabilities allow them to examine data from past projects, and current project blueprints to predict the materials, tools, and equipment needed for the upcoming job.
Nevertheless, demand forecasting isn’t foolproof.
Projects evolve, clients change their minds, and that, of course, impacts your inventory needs.
That’s where the next step—regular inventory counts—swoops in.
Inventory counting helps you keep your eye on the inventory levels and identify stockouts well in advance, facilitating timely replenishment.
One effective method for inventory counting is cycle counting, which focuses on gradual inventory checks rather than a one-time exhaustive count.
According to Bill Conway, managing partner at Guide Path Consulting, this approach is great for minimizing operational disruptions and keeping productivity at an optimal level.
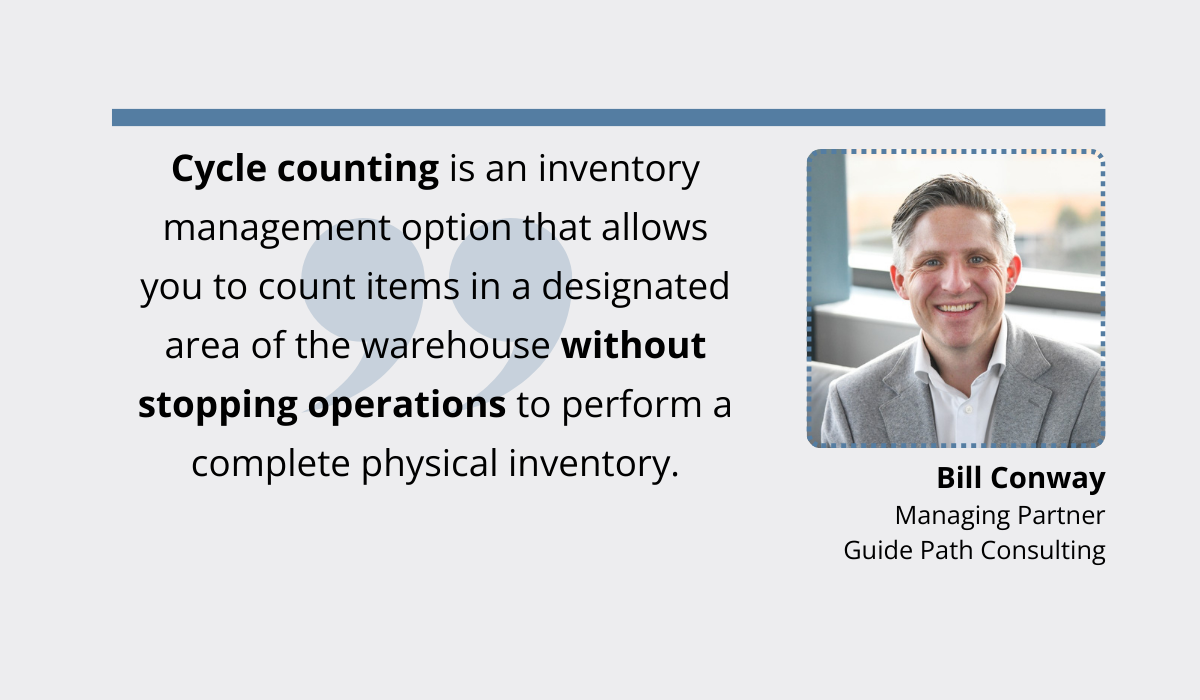
Once you identified which materials need to be reordered, it’s time to go through the replenishment processes.
To ensure this goes as smoothly as possible, and to procure your goods quickly and hassle-free, you need an efficient replenishment strategy.
This includes:
- establishing reorder points,
- determining optimal order quantities,
- working towards reducing lead times as much as possible,
- maintaining a safety stock, and
- establishing efficient order processing.
If you manage to execute all of these three processes correctly, you’ll significantly minimize the risk of costly stockouts.
So, predict, count, and replenish, and you’ll surely reach new heights with your inventory control process.
The project budget and schedule will thank you for it, too.
How Can Technology Improve Construction Inventory Control?
The construction industry has undergone a significant transformation with the advent of technology, ushering in a new era of precision, speed, and efficiency across various operations.
Inventory control is no exception.
Iit’s no surprise, then, that professionals in the field have increased their investment in software solutions in 2023, as highlighted in a survey by the Association of Professional Builders.
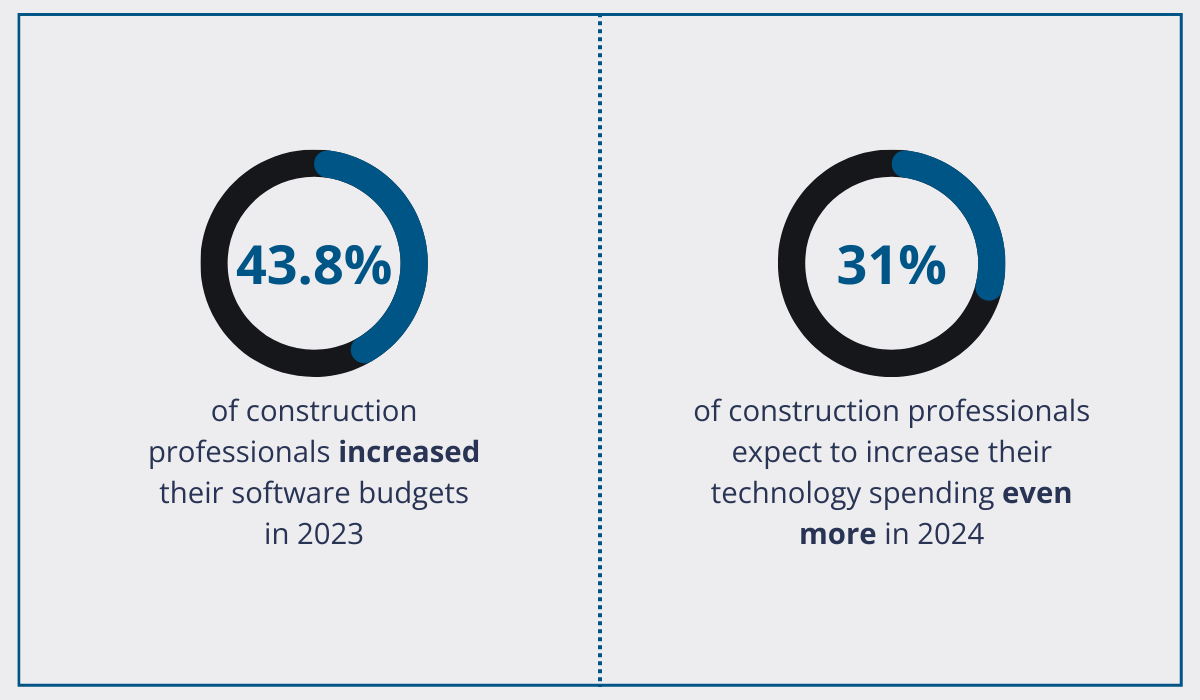
And guess what? The momentum isn’t slowing down anytime soon.
This trend is expected to persist into 2024, with 31% of respondents expressing intentions to further increase their investments in software.
But, how does technology help inventory control specifically?
Findings from a study conducted by Samsara shed some light on this question.
In the survey, construction professionals commonly cite supply chain volatility and shortages as their biggest challenges, which are inherently tied to stock control.
Interestingly enough, the study also reveals that it’s precisely technology that helps companies weather these issues and tackle unforeseen obstacles.
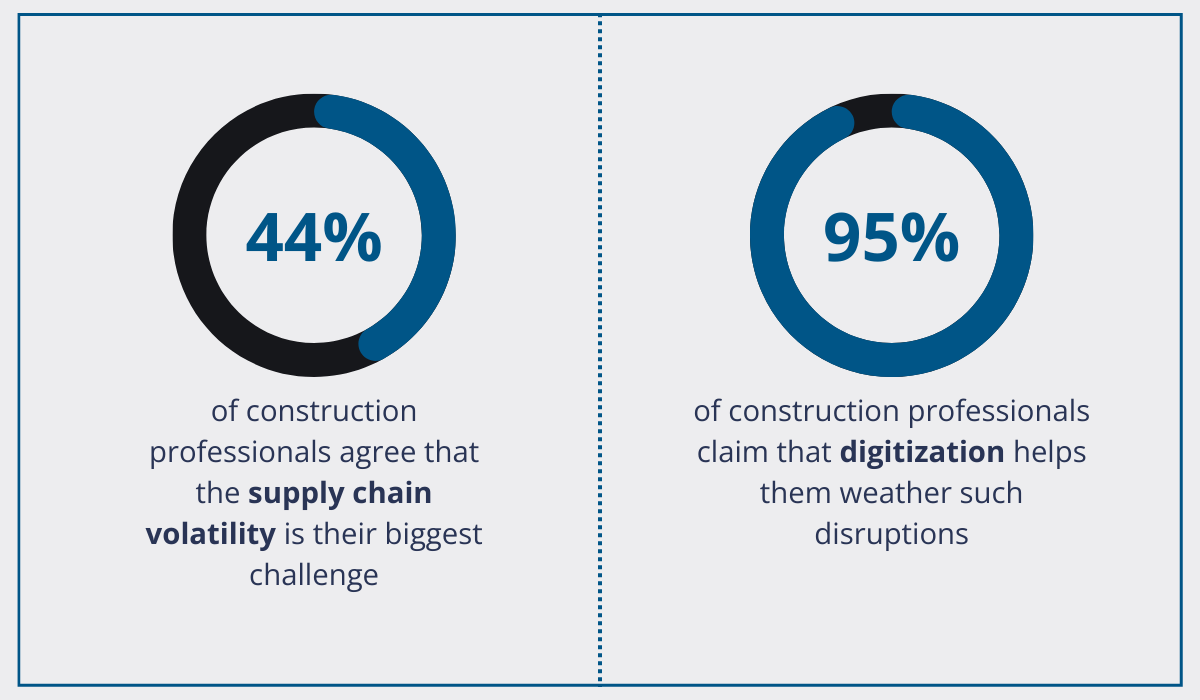
When you think about it, spreadsheets and other traditional asset-tracking methods were never explicitly designed for stock control.
Inventory management software, on the other hand, has.
These systems come equipped with many useful features, such as:
GPS location tracking | Provides real-time insights into asset whereabouts and mitigates the risk of theft |
Efficient check-out systems | Enhance accountability and minimize losses |
Automated quantity updates | Facilitate real-time monitoring of inventory levels |
Reporting and analytics | Empowers informed decision-making through data analysis |
These features were purpose-built to make stock control more accurate, simpler, faster, and better.
Tasks such as asset checkout, quantity updates, data retrieval, and more can now be accomplished within just a couple of seconds, anytime and anywhere.
With such technology at the forefront, the days of cumbersome paper records and exhaustive Excel sheets are becoming a thing of the past, paving the way for a more effective and productive construction inventory control.
What Is the Role of Documentation in Inventory Control?
Inventory documentation helps you monitor your asset-related transactions, including receipts, issuances, transfers, and disposals, all of which are integral to successful stock control.
But beyond merely ensuring that you have access to vital stock data, accurate and readily available documents also help demonstrate compliance with regulatory requirements or internal policies.
Essentially, without meticulous documentation management, not only does the precision of your inventory data suffer, but your company risks legal and financial ramifications as well.
Consider the substantial fines imposed for violating OSHA regulations as an example.
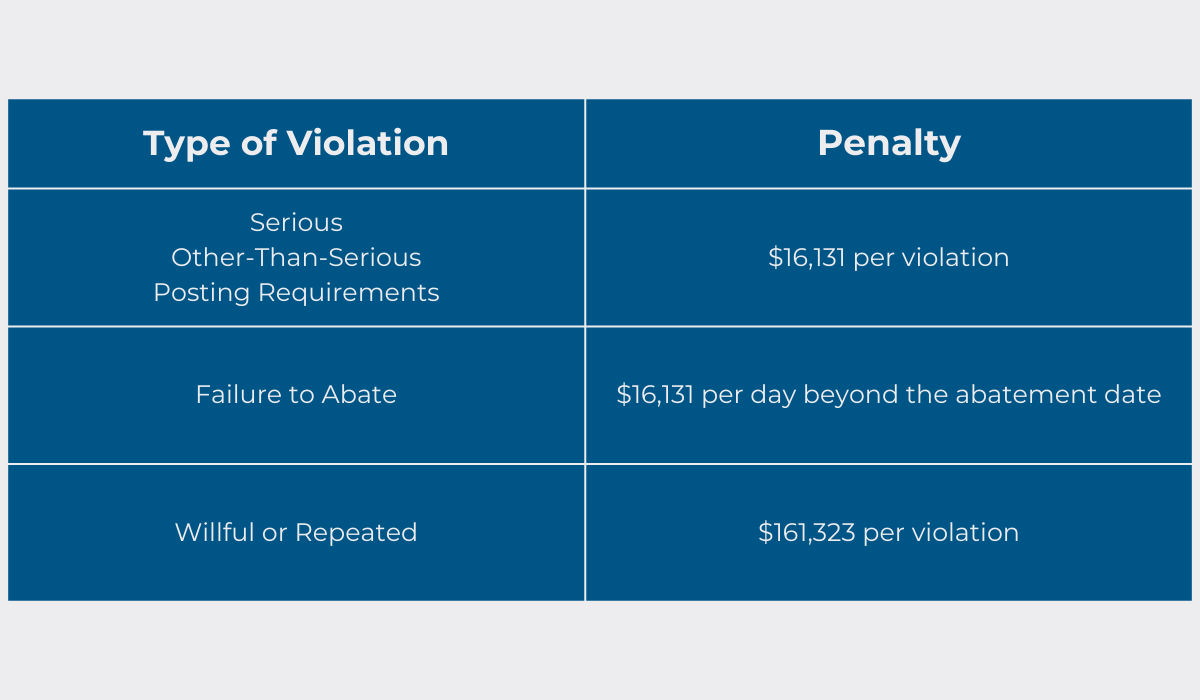
Compliance with these guidelines, particularly those concerning the handling of materials, tools, and equipment, falls under the purview of stock control.
In other words, inventory managers shoulder the responsibility of maintaining thorough documentation to prove adherence to these rules and mitigate potential liabilities.
So, what constitutes comprehensive stock records?
As you might expect, it’s not just about recording inventory levels for each item.
Instead, it involves detailing:
- quantity of each asset at the SKU level,
- quantity of stock used up, sold, and reordered,
- total value of each asset,
- location of each item, and
- other business-related information, such as work-in-progress inventory data.
This information can be compiled and managed either manually or digitally, depending on your specific needs, asset portfolio size, and budget.
However, it’s worth noting that digital solutions, especially cloud-based ones, offer greater efficiency.
Cloud-based software centralizes all the important data and enables remote access, making sure you and your team stay ready for inspections or audits, even if conducted unexpectedly.
These systems are also much more scalable, accommodating your business’s growth and allowing you to expand your asset base seamlessly.
In contrast, paper documents require physical storage space.
This means that, with the growing documentation volume, managing an extensive paper trail becomes increasingly challenging and prone to human error.
Overall, contrary to popular belief, documentation isn’t just a necessary evil.
It is, in fact, your golden ticket to better-informed decision-making, guaranteed regulatory compliance, and ultimately, better project and business outcomes.
Conclusion
As we near the conclusion of this article, we hope you were able to find the answers about inventory control you were looking for.
As you can see, there’s more to this process than first meets the eye.
However, no matter the size of your inventory, or the scope of the project you’re working on, some universal truths can always be applied in your workflow.
Picture them as the three pillars: data, precision, and technology.
With the rich inventory data that helps you forecast resource needs and the right software solution that streamlines processes, your inventory control game is bound to go to the next level.
Add a dash of thoroughness and attention to detail, and you’ll become an unstoppable force in the world of inventory control.