Managing construction inventory is no easy feat by any means.
A lot can go wrong in the process, harming project deadlines and budgets—definitely something nobody wants.
But here’s the biggest problem: you might be making some serious mistakes and relying on poor inventory management practices without even realizing it.
Luckily, you’ve stumbled upon this article.
In it, we won’t just list the common inventory errors. Instead, we dissect their repercussions and offer proactive solutions, too.
By the time you’re done reading, you won’t just be aware of these prevalent pitfalls; you’ll be ready to tackle any inventory-related challenge head-on, like a pro.
Let’s get started.
In this article...
Lacking an Inventory Strategy
An inventory strategy’s role is to guide day-to-day operations and shape your decision-making processes related to the procurement, management, and handling of various inventory items, including machinery, tools, materials, and consumables.
The truth is, without a coherent plan of action in place, you are, essentially, operating blindfolded.
You get no real-time insights into stock levels or conditions and have no efficient procedures to manage your valuable assets effectively.
What usually happens in such scenarios is that you get cornered into prioritizing immediate needs over long-term objectives, and start solving issues reactively instead of proactively.
In other words, you end up constantly putting out fires and tackling problems as they pop up, rather than nipping them in the bud.
The absence of an effective inventory control strategy typically manifests in two common problems: overstocking and understocking, both of which can severely impact project budgets and timelines.
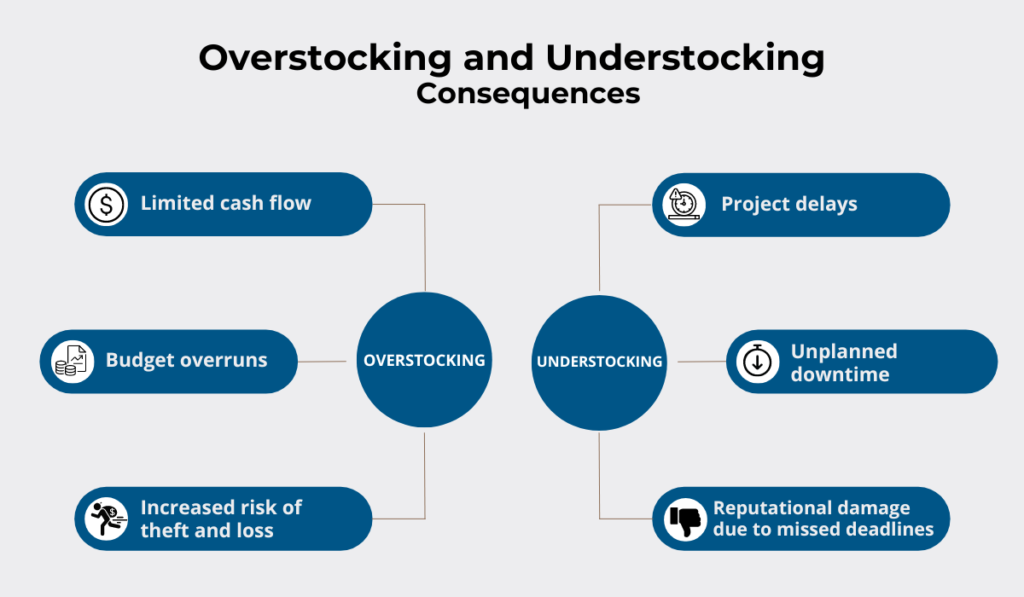
In construction, every material, tool, and machine counts.
And that’s why your strategy has to be as finely tuned as the machines you’re managing.
If done correctly, it standardizes your processes and procedures for handling stock across multiple warehouses, job sites, or departments, ensuring consistency, coherence, better coordination, and increased efficiency.
However, keep in mind that there’s no one-size-fits-all approach to crafting an ideal inventory strategy.
It must be customized to meet the unique requirements of your company.
Nevertheless, there are some universal principles to consider when developing your own inventory game plan:
Establish Clear Goals and Objectives | To align your stock control strategy with broader business objectives |
Prioritize Data | To analyze current market conditions and forecast future needs |
Embrace Inventory Control Technology | To ensure alignment with different departments |
Foster Communication with Stakeholders | To automate processes and boost accuracy |
Continuously Adapt | To stay agile and be able to address evolving challenges and changes |
All in all, you can’t have effective stock control without a well-crafted inventory strategy.
It’s not just a set of unnecessary rules and procedures, but a system that can help you transform your inventory management game, make the most out of your assets, and ultimately, achieve better project outcomes.
Ignoring Demand Forecasting
Relying solely on gut feeling for stock control in the construction industry doesn’t really cut it anymore.
With material shortages and volatile price fluctuations becoming commonplace, it’s time to start paying closer attention to project requirements and timelines to forecast inventory demand more accurately.
According to Gordian, in 2023, a staggering 82.5% of construction materials saw significant cost increases.
Equipment costs were no different, experiencing an average increase of 5.3%.
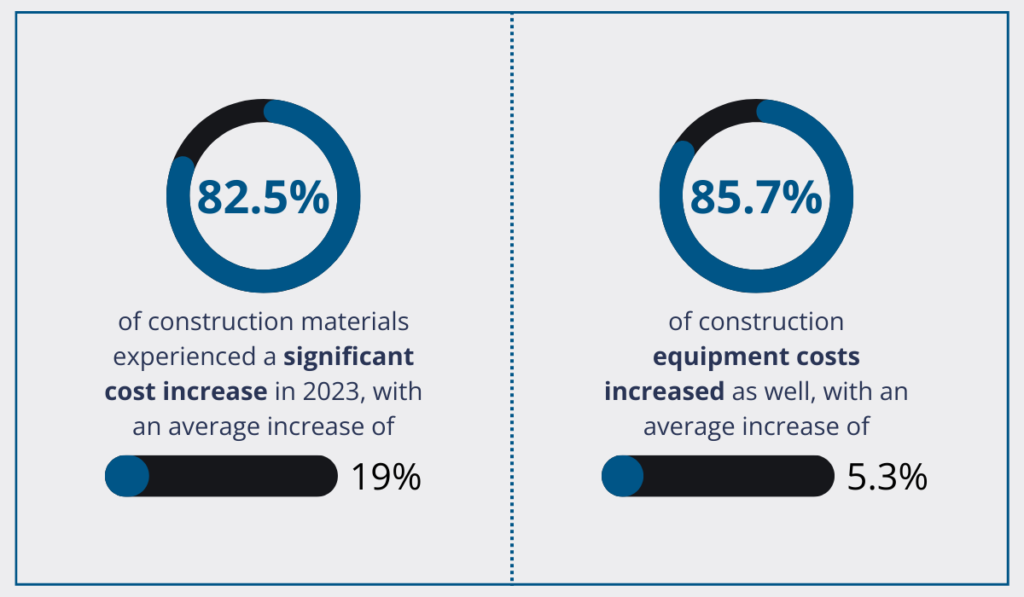
Overordering construction supplies was never a good idea, but now, in light of these soaring prices, it’s downright financially disastrous.
These statistics are almost like a wake-up call, urging construction professionals to reform their inventory management processes and try to refine their predictive capabilities.
But here’s the best part about inventory demand forecasting: it doesn’t just protect you from overspending on equipment and materials.
It also:
- Prevents delays caused by material shortages
- Streamlines the reordering process
- Maintains healthy cash flow
- Enhances responsiveness to potential risks
To unlock these benefits, and to be able to address both current and future inventory needs, you need to leverage the power of data.
And what’s the most reliable source of data today?
Technology.
Almost any construction software nowadays, from takeoff tools to asset management systems, offers robust reporting and analytics features.
This allows you to monitor asset utilization and costs, analyze market trends, and make better-informed, data-driven predictions.
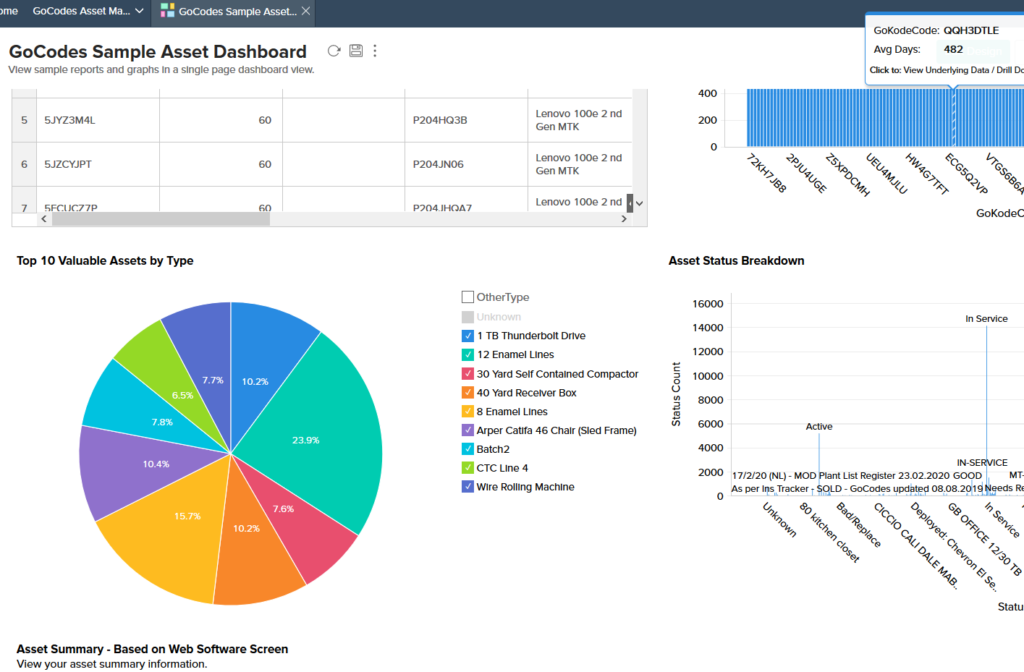
Essentially, these tools give you insight into your inventory’s past, present, and future.
So use them to ensure you always have just enough resources to finish projects successfully, without breaking the bank and going over budget.
Failing to Consider Inventory Costs
Neglecting inventory costs means failing to understand the significant impact inventory has on your cash flow and profitability.
Say you order an excess of construction materials. Since there’s no need for them at the moment, they end up idle in your warehouse.
Seemingly harmless, right?
However, without vigilant cost tracking, these surplus items begin to accumulate storage and other types of expenses without anyone noticing.
The risk of them being stolen or lost increases as well.
Essentially, they become a drain on finances, rather than an asset.
Now imagine you keep overordering materials.
All those unnecessary expenses gradually start to build up, eventually resulting in considerable budget overruns and disgruntled clients looking for an explanation.
As you can see, overlooking this one aspect of stock control can lead to a colossal mess.
That’s why it’s crucial to monitor all aspects of inventory costs, not just the purchase price.
This entails:
- Storage
- Asset management
- Handling
- Transportation
- Depreciation
- Wastage and spillage
- Insurance
Once you have your eye on all these cost components, it becomes much easier to keep your inventory expenses under control.
One efficient method used precisely for this purpose is checkpoint cost monitoring.
It’s a simple, yet effective preventive measure against excessive spending.
Here’s how it works: you establish checkpoints throughout the entire project and allocate inventory budgets for each stage.
When you arrive at each specific checkpoint, you compare actual costs to the allocated budget.
If the expenses are higher than anticipated, it’s time to investigate and determine the cause.
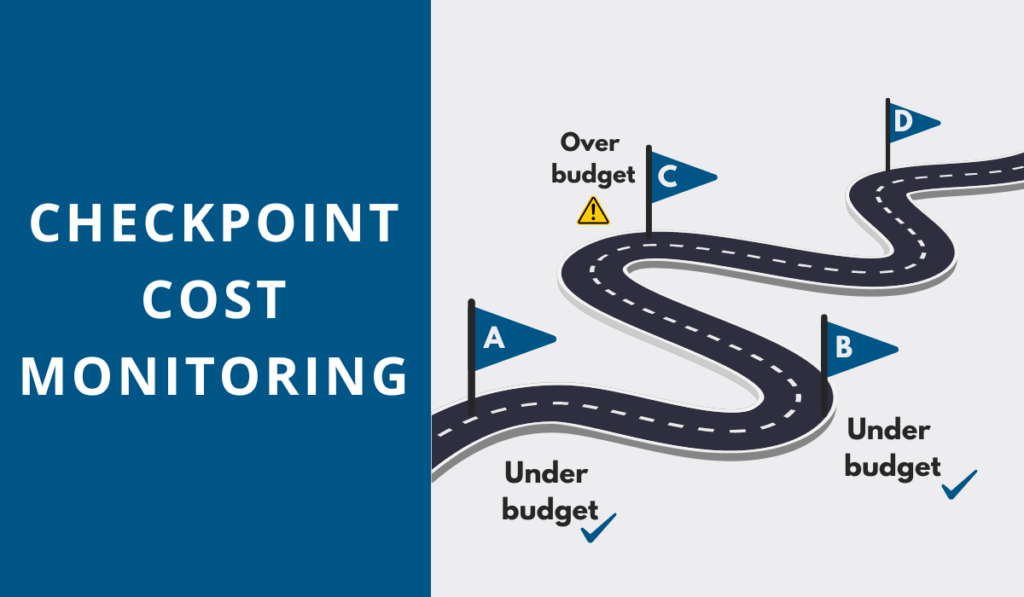
Are you overordering? Are the supplies being improperly stored? Is there a theft problem?
Once you figure out the root cause, you can steer your project back on track before it’s too late.
The bottom line is this: paying close attention to inventory costs can help you solve a surprisingly large number of problems.
From improving cash flow to preventing budget overruns or even theft, inventory cost management can be a real game-changer for your bottom line.
Relying on Outdated Inventory Control Methods
You can’t do construction work without the right tools, that much is apparent to everyone.
So, why should construction inventory control be any different?
While they may seem convenient, cost-efficient, and familiar, outdated methods like pen and paper or Excel spreadsheets simply don’t cut it anymore.
This is especially true when dealing with large inventories spread across multiple locations, which is typically the case in the construction industry.
Relying on these antiquated methods then becomes labor-intensive, time-consuming, and prone to errors.
This often results in what Autodesk refers to as “bad data”—information that’s inaccurate, incomplete, inaccessible, inconsistent, or untimely.
And guess what?
Bad data leads to bad decisions, which often means unnecessary costs, project delays, and rework.
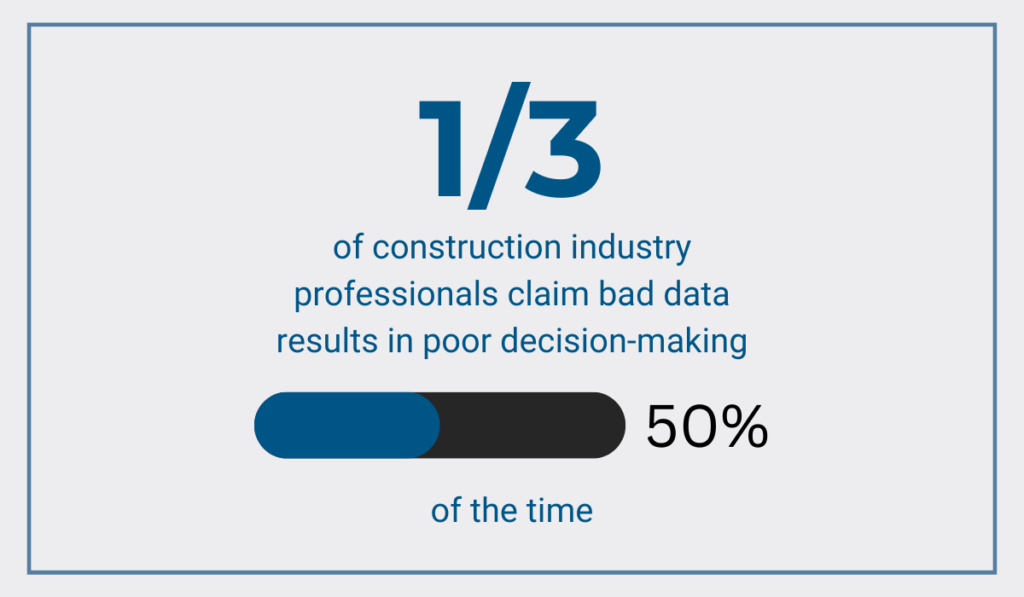
This brings us to the question: what is the right tool for the job?
According to Ty Campbell, director of customer success at United Rentals, a digital tool.
“In today’s world, harnessing the power of digital technology to manage construction equipment just makes sense. There is plenty to worry about on the jobsite and digital tools should be an important part of managing complexity. This approach can help contractors streamline processes, save time and gain greater control so they can deliver better results and have fewer safety incidents.”
Unlike traditional methods, specialized inventory control software solutions were made specifically to make inventory control easier, faster, and more accurate.
Recognizing just how important precise and detailed inventory data is, but not wanting to sacrifice the user-friendliness of those old-school methods, we’ve decided to develop our own solution—GoCodes Asset Tracking.
With GoCodes Asset Tracking, tracking inventory levels and asset locations becomes effortless, even for less tech-savvy workers.
Simply attach our QR code labels to your assets and install our app on your smartphone to get started.
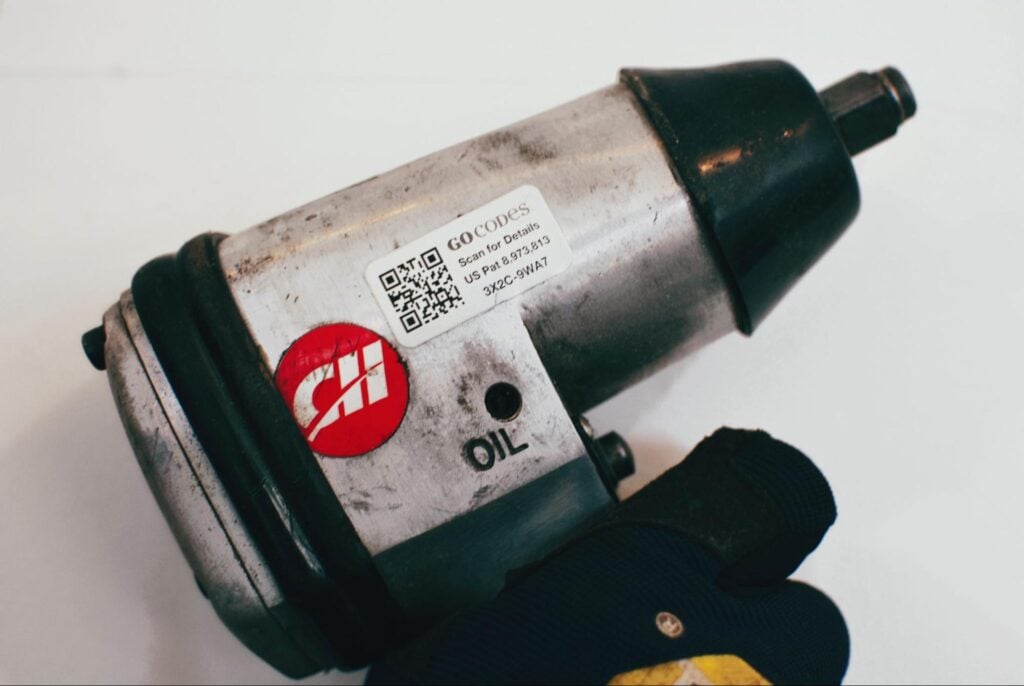
By scanning the labels using the in-app scanner, you can check machines and tools in or out, update quantities for consumables and stock items, assign assets to particular users or projects, and so much more.
Our system also has GPS tracking capabilities, updating asset location every time you scan the labels.
No more wasting time trying to hunt down materials and tools.
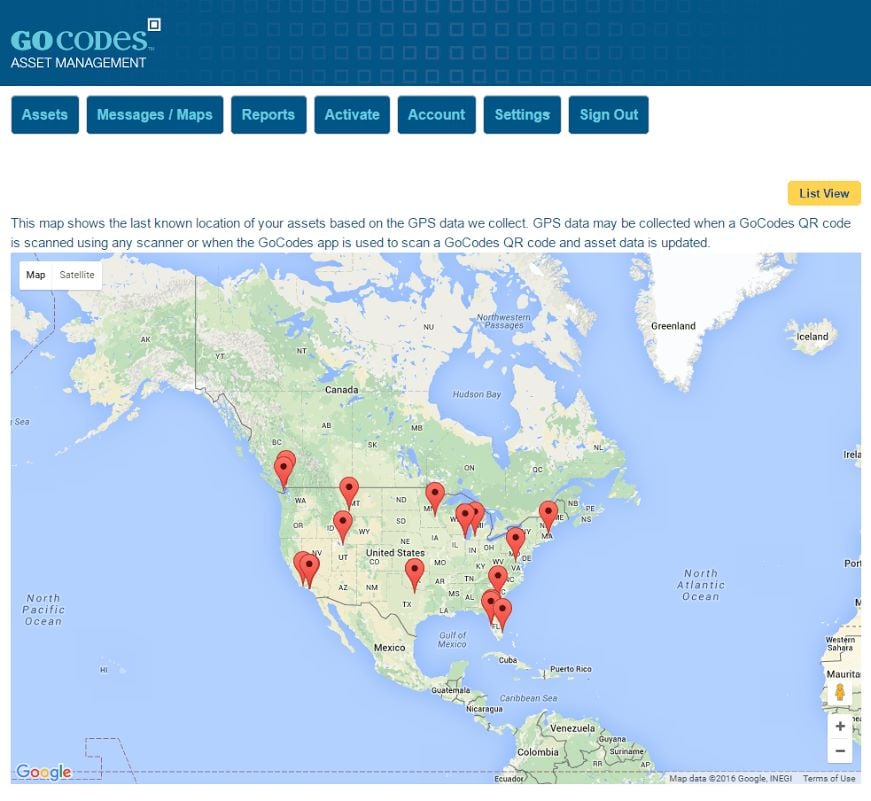
At the end of the day, you can’t expect to make good business decisions if you don’t have reliable data at your disposal.
Sure, you’ve used spreadsheets for a long time now, and you’ve gotten used to them, but they were never specifically designed for inventory control.
You wouldn’t use a stone axe to cut a tree today, right?
Neglecting Physical Inventory Checks
That being said, you shouldn’t rely solely on technology to manage your assets.
Regular physical checks to reconcile actual inventory with recorded stock levels are a must.
They can help you catch discrepancies, inaccuracies, or even theft, adding an extra layer of accuracy to your inventory database.
Don’t let your inventory management software create a false sense of security.
Be vigilant, establish a routine for physical checks, and make sure to stick to it.
Now, we can’t ignore the fact that performing these checks can be quite daunting, considering the sheer size of typical construction company asset portfolios.
Counting all those items at once may seem impractical or even downright impossible.
So, to streamline this process, consider implementing inventory cycle counting.
Rather than tackling the entire inventory at once, this method focuses on auditing smaller sets of items periodically.
Bill Conway, managing partner at Guidepath Consulting, advocates for this approach, too, highlighting its time effectiveness:
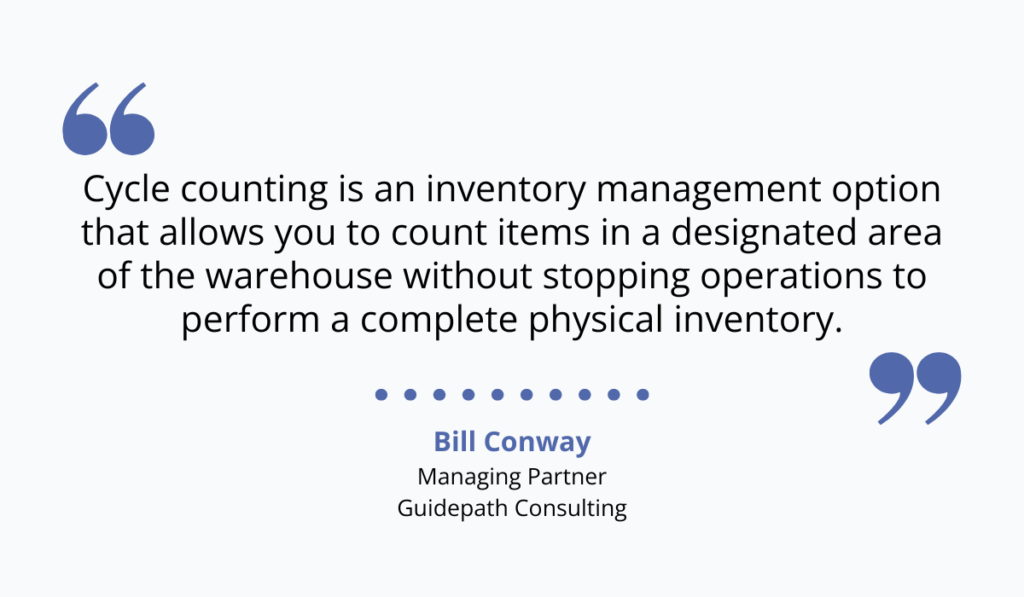
With cycle counting, there’s no need to halt operations entirely.
Instead, inventory is counted bit by bit over time to maintain a smooth workflow for everyone working on a project.
One widely used variant of this system is ABC cycle counting, which assigns values to asset types based on factors such as quantity, space requirements, or dollar value.
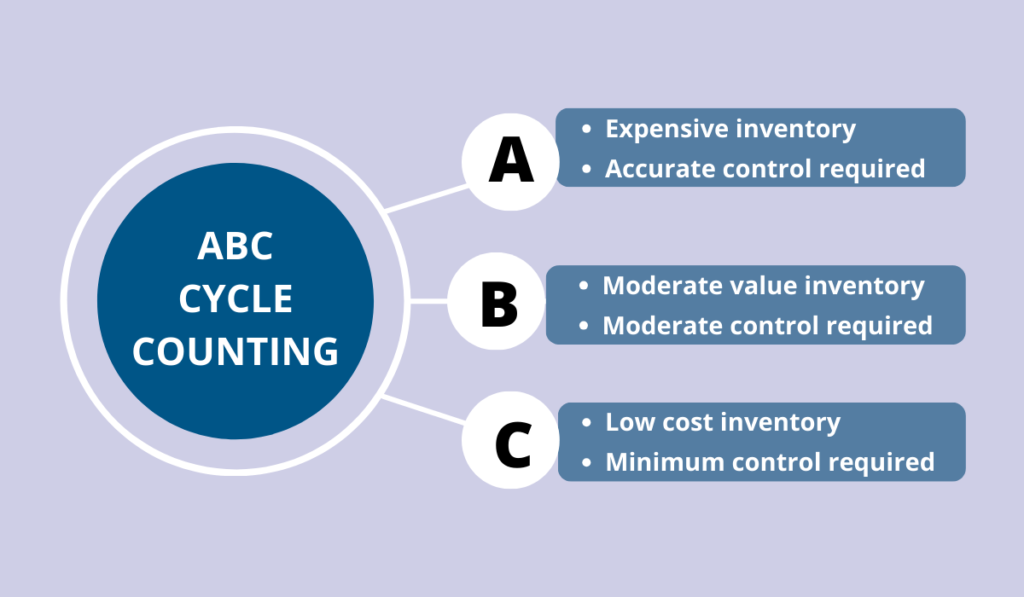
The frequency of counting is then determined for each group, with higher-value items being counted more frequently than items with a lower value.
This ensures that focus is directed towards resources with the most significant impact on business operations.
However, if you’re going to use this method, try to avoid overcounting prioritized items at the expense of neglecting others.
To prevent this imbalance, listen to suggestions from the workers responsible for counting, and be willing to make adjustments and reassign value as needed.
Conclusion
Now, our greatest hope is that you actually didn’t learn anything new from this article.
Ideally, you were already ahead of the game and these mistakes aren’t news to you at all.
However, if you identify with any of these examples, worry not. Everything can be fixed.
When it comes to inventory control success, the golden rule is to prioritize inventory data, streamline processes wherever possible, and give equal attention to future resource requirements as you do to present ones.
Stick to these principles, exercise patience, attention to detail, and vigilance, and you’ll undoubtedly see improvements in your inventory control process in no time.