Asset management is a challenge for many construction companies, mainly because construction isn’t exactly data-driven. To manage equipment properly, you have to rely on data and find a way to gather it in real time.
We will do a quick dive into the six main challenges construction businesses face when managing their assets, including real-time visibility and sharing information, which are pretty straightforward.
However, we will also look into how managing your equipment can help your overall business goals and improve asset condition.
Let’s dig into it!
In this article...
Ensuring Sufficient Asset Visibility
If you were asked to produce a final list of all the available assets you own, would you be able to?
When you don’t manage your equipment correctly, it is likely that you simply don’t know what you have or how functional it is.
It probably also takes you a long time to even notice that a piece of equipment has gone missing, and you can never pinpoint exactly when or who last had it.
This type of practice might keep you afloat for a while, but eventually, you’re going to crack under pressure.
You’ll be wasting money on the depreciation of assets you don’t own anymore, repairing equipment you’re better off selling, underservicing machinery, and thus lowering its expected lifespan.
Conversely, let’s look at an example of what happens when you manage your assets effectively.
Once the Department of Defense (DoD) adopted asset tracking for their 16K vehicles, they achieved impressive results, conducting their inventory in a day where it once took them a year to complete it.
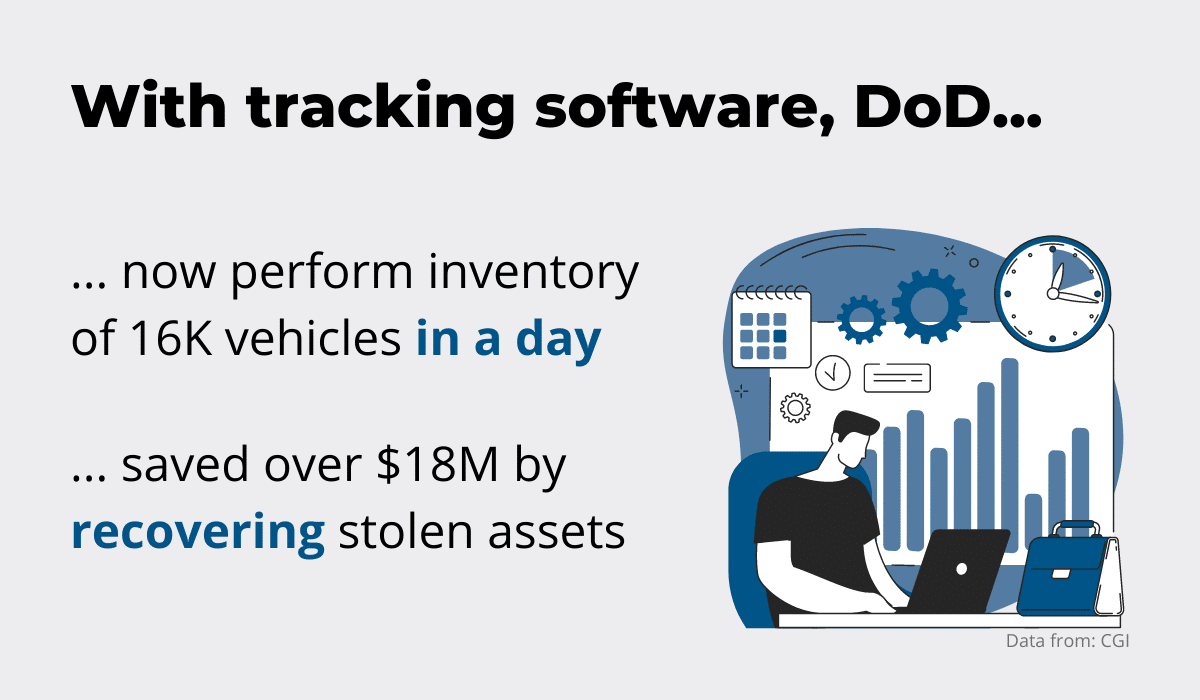
Imagine the cost savings on that alone!
The software also helped DoD recover more than 150 stolen or lost vehicles which had cost over $18 million.
Therefore, an insight into your machinery’s whereabouts helps you quickly spot a lost asset and promptly react, increasing your chances of getting your equipment back.
Sharing Asset Information Efficiently
The lack of information sharing is a pain point in construction asset management.
Many companies still don’t tag and track equipment, which stops them from accessing relevant data such as maintenance stats, availability, and utilization on time.
If you don’t know who, if anyone, is using a machine, you’re wasting money.
This type of visibility is necessary if your team shares tools and equipment, so it’s no wonder almost a quarter of companies plan to invest in software for better scheduling.
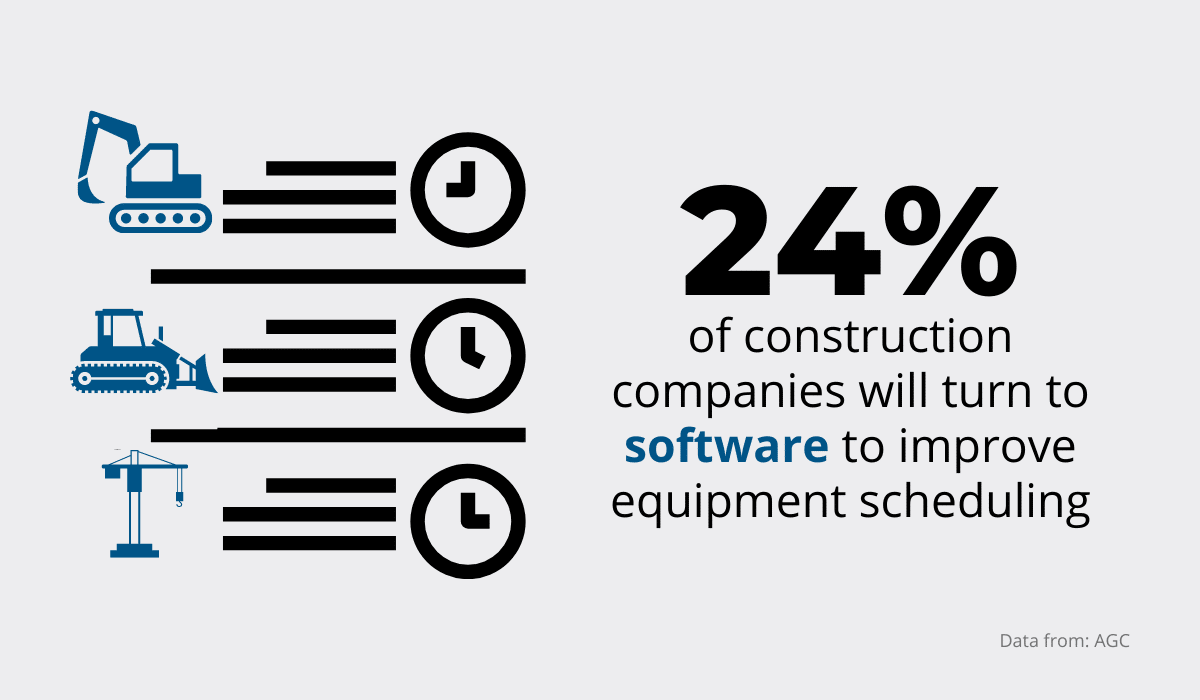
Let’s imagine your project manager needs two cranes at the construction site as soon as possible, at the same time as another manager needs one too.
If you don’t track your assets in real time, you will probably check some spreadsheets to see how many cranes your company owns. If it’s three, you will let the project managers know they can use the cranes.
However, with this approach, you’d still be missing essential information.
Without insight into the cranes’ location, condition, and safety, you’d be setting the managers up for failure.
You and your team need access to a single data source about the equipment.
With tracking software, you’d simply use the keyword ‘crane’ in your app to see how many you have, which ones are currently available, and when the remaining ones will be available next.
You could also reserve these cranes for the managers in question so nobody else could check them out on those dates.
Making the Most of Warranties
When you’re not managing your assets right, you lose sight of warranties, which is bad for business.
This guarantee comes in handy whenever your machinery doesn’t perform like it’s supposed to, as it ensures that the seller or manufacturer will assist you.
When a machine breaks down while it’s still under warranty, you may be entitled to a repair and a replacement item at the expense of the seller.
That way, you can have a new machine running while yours is in maintenance, ensuring that your project stays on track.
Of course, if you don’t keep up with warranties, you will have to fix everything at your own expense, thus wasting money you could have saved otherwise.
In fact, most companies lose more than a third of potential savings by paying for repairs the warranty should have covered or by assuming it covers something it doesn’t, which is also called warranty leakage.
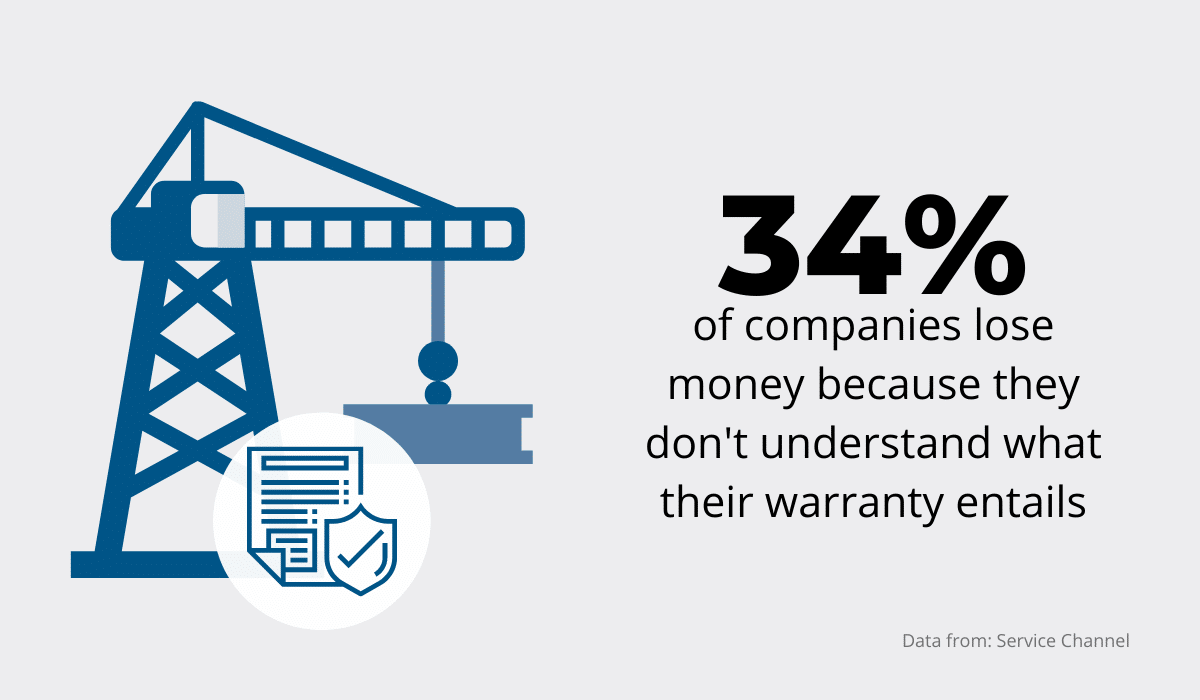
According to Patrice Eberline, vice president of global customer transformation at ServiceMax, the leading cause of warranty leakage is the lack of data visibility.
Eberline notes that “most organizations have no idea what warranty is costing them because they don’t have visibility into that data.”
In other words, because businesses don’t keep an eye on warranties, they end up wasting money.
If you don’t want to make the same mistake, invest in tracking software that lets you track the equipment’s documentation, too.
That way, a quick search in the app will lead you to valid warranties and insurances.
Making Correct Replacement Decisions
It’s often tricky to pinpoint the best time to replace an older asset with a new one.
No rule covers all scenarios, so you will have to rely on data to make an informed decision about this. In many cases, it’s easier and cheaper to invest in maintenance than to buy a new piece of machinery altogether.
However, after years of wear and tear, some machines cost more to fix than they are worth.
Maintenance logs can help you determine how often you service equipment and spot a pattern of breakdowns.
When an asset is often out of service, especially in comparison to other similar machines, it might be time to dispose of it.
By streamlining your asset management process, you will get an overview of crucial information, like utilization, repair and care costs, and frequency of malfunctions. These aspects will help you decide between keeping or getting rid of the asset.
You can easily upload service data to your asset tracking software, ensuring you never lose sight of it.
When you have this data, you can calculate what is more viable for your company. You can do this by comparing an asset’s current value with the cost of its repair.
Here’s a formula that can help you, but remember you’ll need to calculate depreciation beforehand!
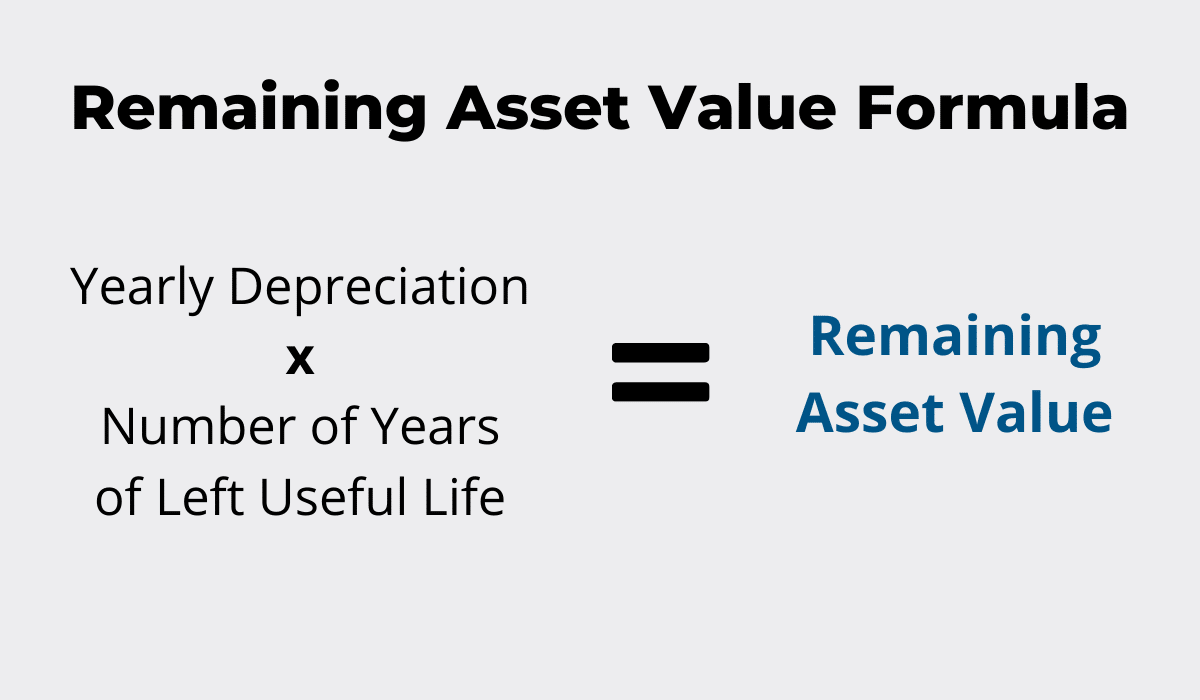
Start by multiplying the asset’s yearly depreciation cost with the remaining years of its useful life. For example, if you pay $500 yearly in depreciation for equipment with three more years of useful life, its remaining value is $1,500.
Once you know the amount, you can compare it with the yearly maintenance costs and decide whether it would be more prudent to replace the asset instead.
Avoiding Maintenance Errors
Proper asset management helps decrease the number of equipment service issues.
For one, having all the manuals and specifications listed in the same place ensures that all of your maintenance specialists, no matter how inexperienced, know what to check.
The manufacturer’s instructions usually list possible problems you might encounter with the machine, along with the possible causes and solutions to each issue.
Therefore, the manuals are an indispensable part of your maintenance plan and help your team immensely.
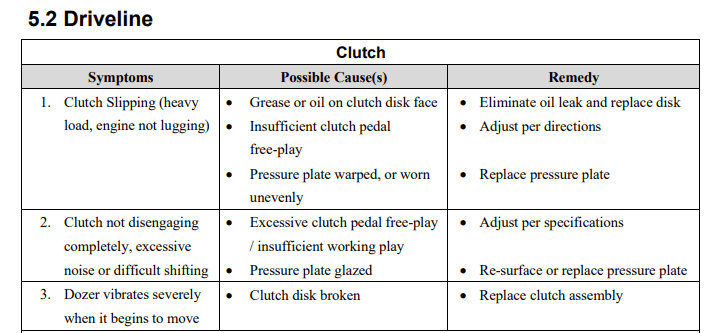
On top of that, having access to equipment manuals also decreases safety risks associated with maintenance. Each manual comes with instructions on how to perform repairs safely, as this often differs from machine to machine.
So, allowing your team access to all manufacturer’s documentation means you’re helping them stay safe, too.
In their manual, Northern Tool has different safety sections, from basic service instructions to asset-specific ones, like in the image below.

Then, the manuals also list the necessary replacement parts.
If you’re keeping track of all your assets, you’ll know how many replacement parts you have and where, which means your team will quickly get the pieces they need to fix the machine in question.
This option will speed your team up and save you money.
If you make sure your team uses the software not only to check the instructions and manuals but also to update their servicing logs with correct data, your maintenance will be smooth sailing.
Aligning Asset Management With Strategic Business Goals
Proper asset management can help you achieve company goals faster.
Despite this, many businesses don’t invest in managing their assets. Instead, they put all their money towards goals and wonder why it is not working out for them.
As a construction company, one of your main goals is to decrease your delay time and stay on track with your projects.
Since reports show that a typical delay costs up to 20% of the original cost of the project, it’s no surprise that companies find this so important.
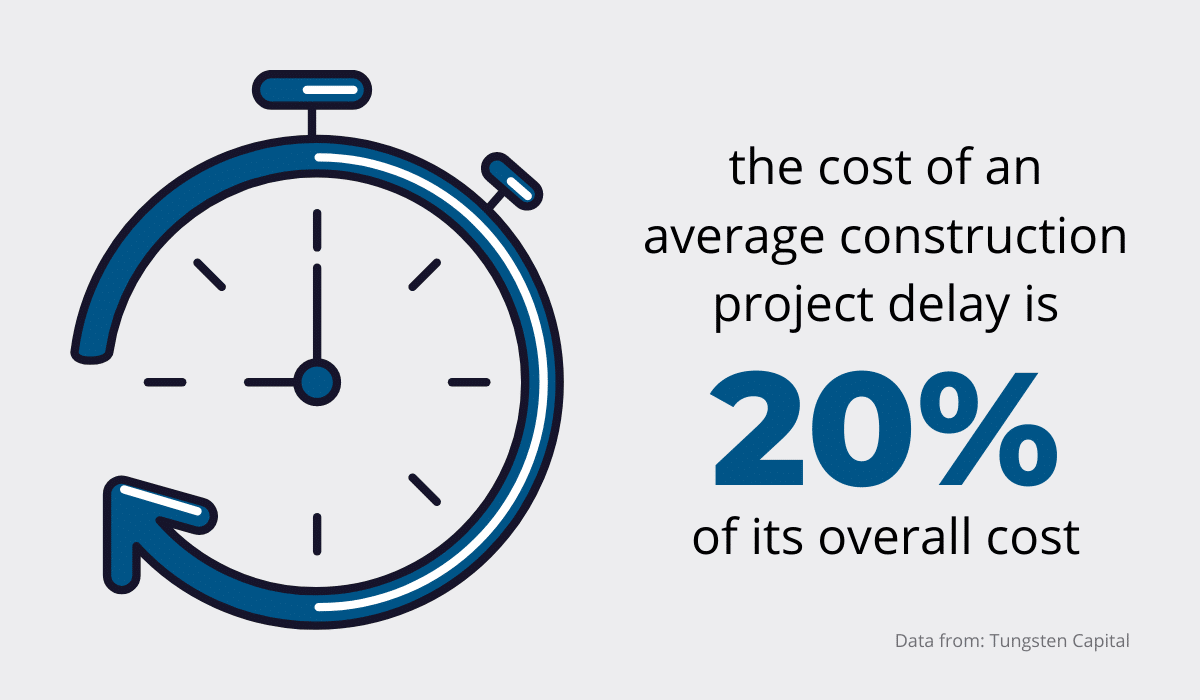
As already explained, when you manage your assets well and are informed of their current conditions, utilization, and worth, it’s easy for you to stay on top of your schedule.
Asset tracking helps keep your projects on track, thus saving you money and affecting customer satisfaction.
Safety should also be a top business priority in construction, considering construction workers have a 75% chance of getting a disabling injury during a 45-year career.
One out of 200 workers will die at the workplace during the same timespan. Clearly, construction companies need to do more to improve safety, and managing their assets correctly is an important aspect of that.
You can use equipment tracking software, such as GoCodes, to always be aware of the current condition of your machinery, as well as for easier reporting of safety problems, and to deliver operating and maintenance manuals to your teams.
Conclusion
Construction companies aren’t always known for prioritizing digitization, but that doesn’t mean you should neglect giving your daily operations a boost in the form of some effective technological solutions.
Otherwise, you’ll start lagging, especially in terms of asset management, which can transform so many of your daily construction activities. Managing your equipment allows you to have a clear and detailed overview of all related data.
The best way companies can do this is to look into software that helps them manage all their assets and related documentation, such as maintenance logs, warranties, and operator manuals.
Keeping all this data in the same centralized location allows for better equipment management, and therefore, quicker goal achievement. What’s stopping you?