Many construction businesses rent out or lease equipment and machinery.
So if you also deal with equipment rentals, then this article is for you.
Managing your rentals becomes much easier with certain technologies.
Knowing the location, usage, and condition of your rented equipment makes all the difference.
So join us as we explore five technologies that can bring your rental business to the next level!
In this article...
QR Code Tracking
Quick response (QR) codes provide insights into the location and usage of various assets.
You need a QR code label, a smartphone with a QR reader, and connected software. Scanning the label on an asset allows the software to read the data encoded in the QR code.
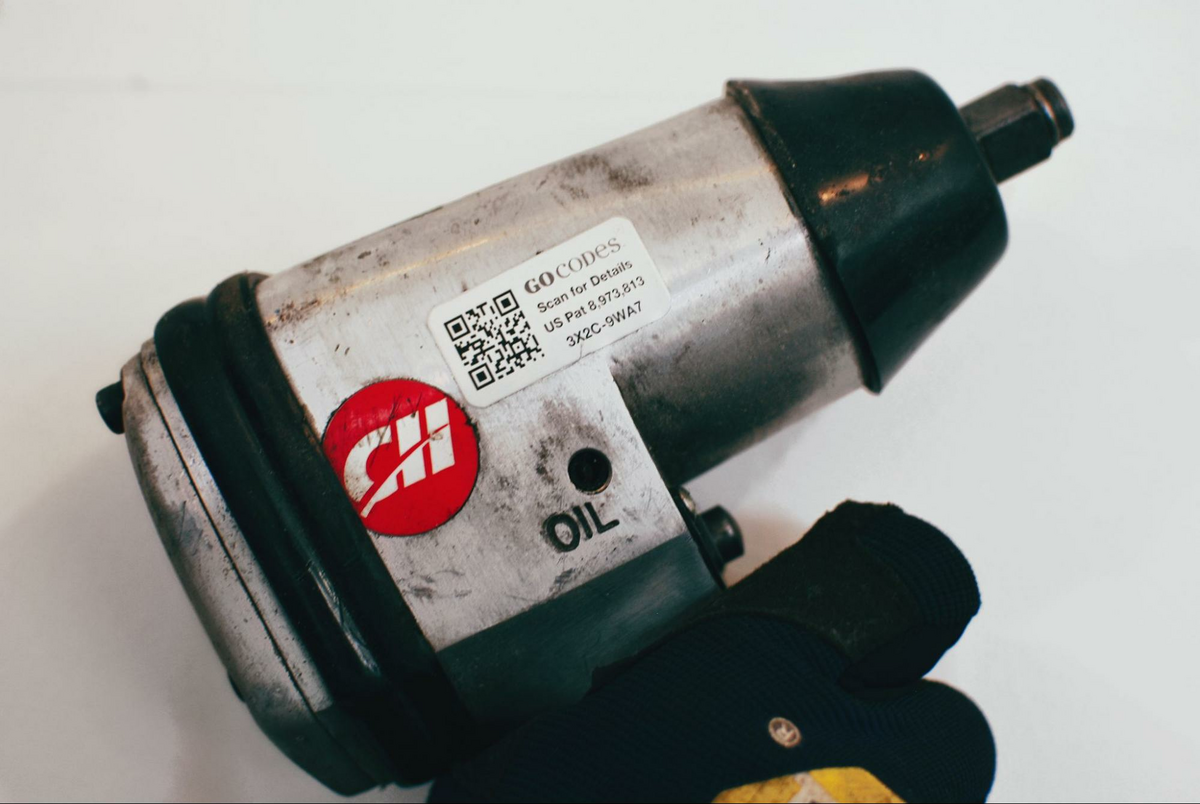
This technology tracks the current location and facilitates easy check-in/check-out of equipment, making it ideal for rental companies with large inventories.
Those managing plenty of equipment understand the importance of inventory visibility.
For equipment rental companies managing dozens or hundreds of assets, check-in/check-out software is a game-changer.
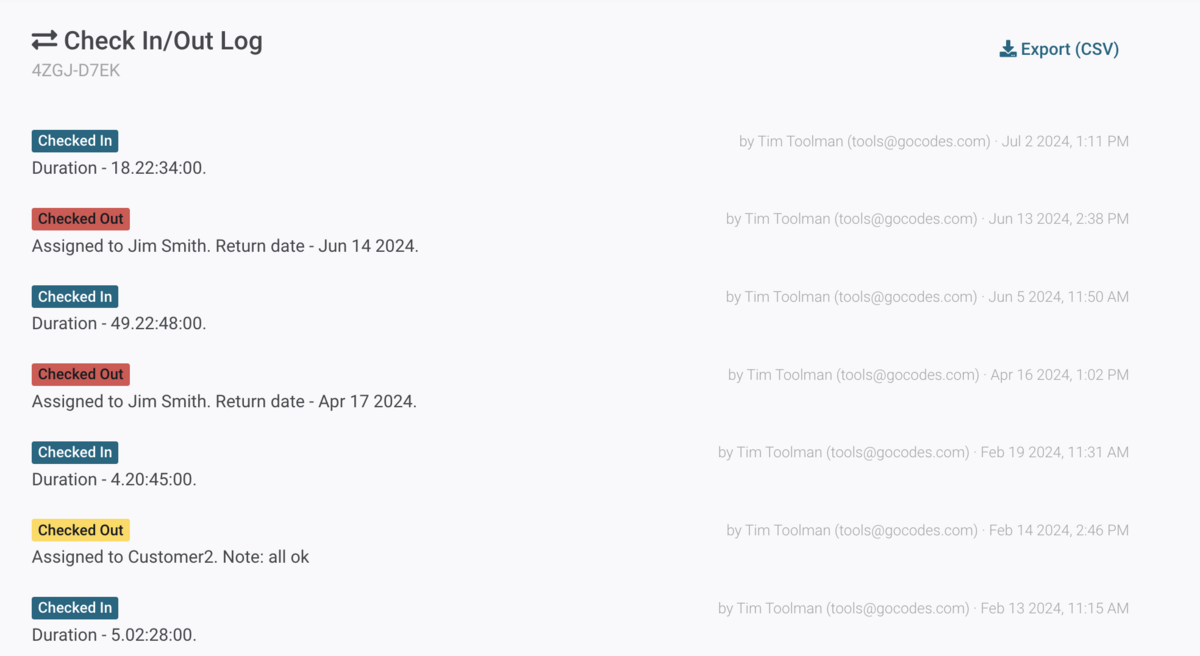
Imagine the convenience of a system where each asset has a unique QR code, simplifying the tracking of availability, location, and condition.
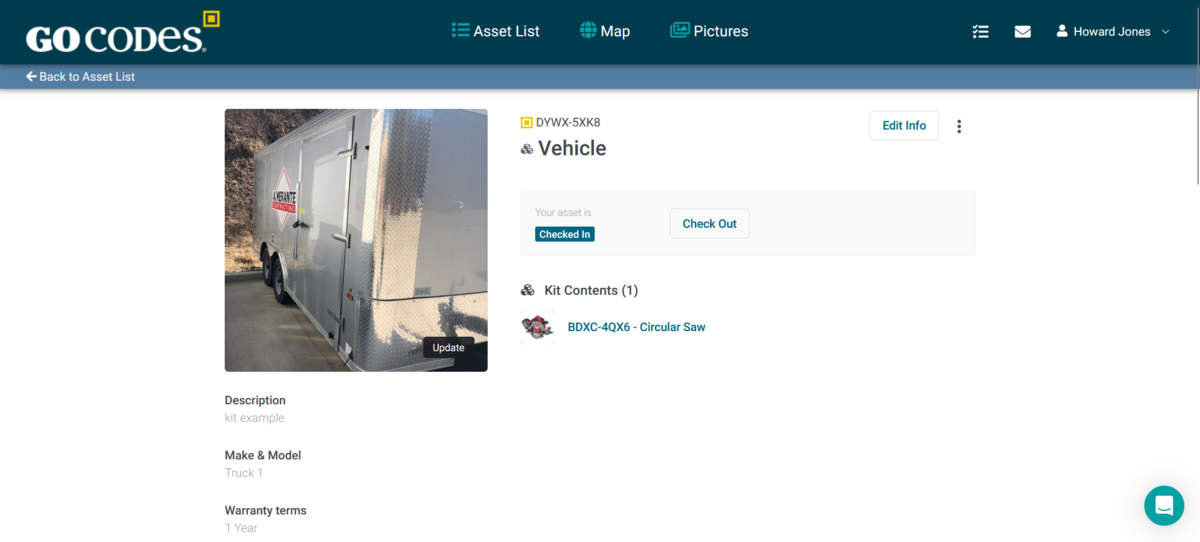
Our asset-management solution, GoCodes Asset Tracking, offers this by integrating several cutting-edge technologies into one system.
You can quickly access key information on all your rentals and manage the checkout process of one or multiple assets using a mobile or web app.
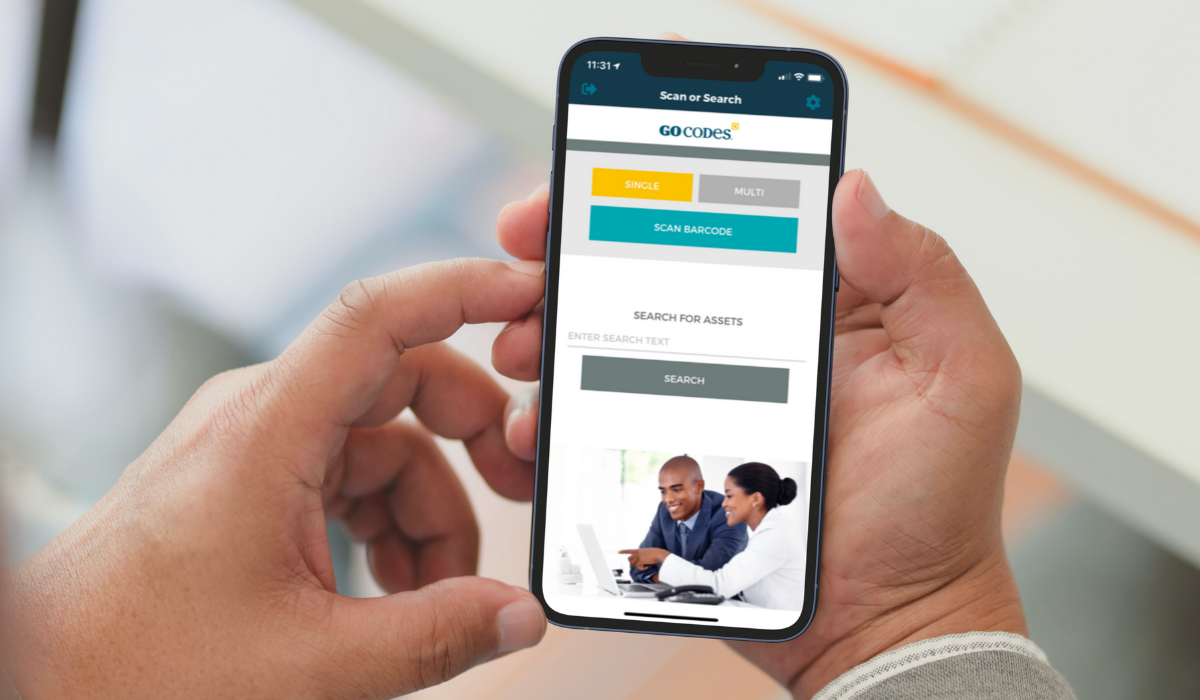
This solution works for managing large assets, but also different specialty parts, reducing the overall risk of theft and loss.
QR codes are a staple of inventory management because they allow businesses to easily enter and track changes in equipment status, quantity, and maintenance.
This technology provides you with a swift and accurate overview of all your rental equipment, ensuring the right assets reach their intended users.
Telematics
Telematics offers a more advanced option, providing detailed information on your rental equipment’s location, usage, condition, and performance.
Combined with GPS tracking, sensors, and telemetry, telematics provides rental companies with real-time equipment monitoring, resulting in:
- integration of asset data into the company’s database
- an accurate operational picture, including areas of concern
- more informed decision-making
James Morley, Senior Vice-President of Global Product Management at the Point of Rental, one of the leading rental software companies, explains how IoT enables telematics and adds value for businesses.
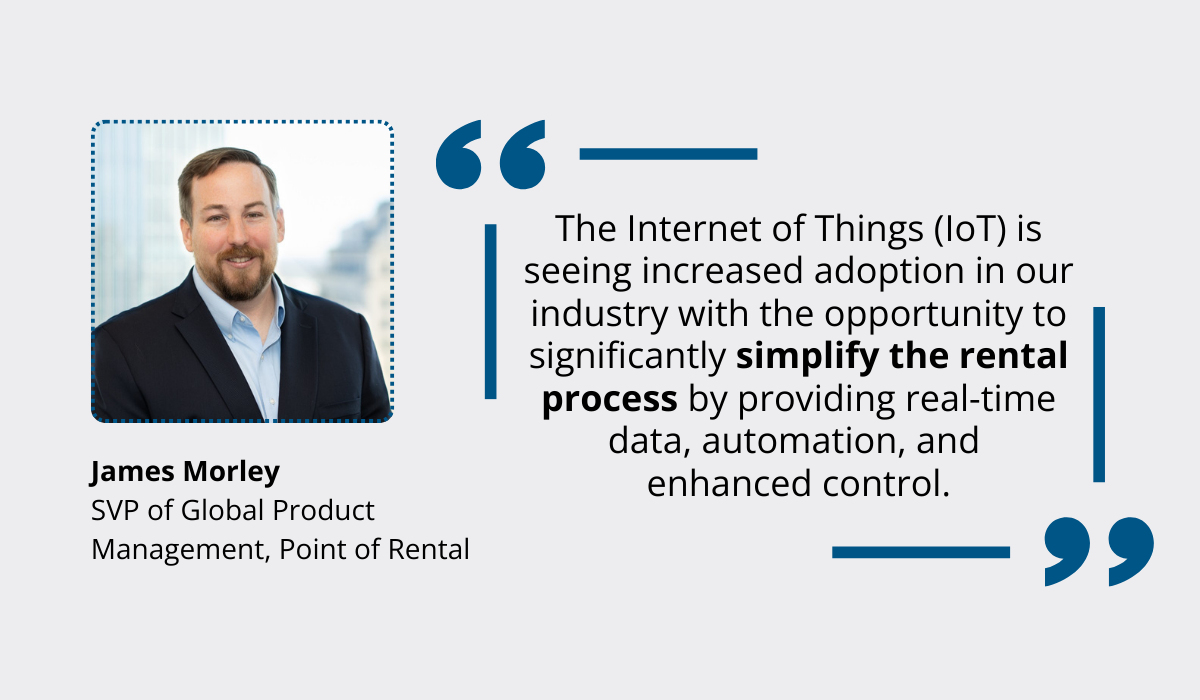
Fleet telematics systems reveal the exact location of rented machinery, its runtime, and other key usage details.
Different companies prioritize different telematics insights; some aim to boost productivity, while others focus on monitoring emissions.
Telematics technology is also invaluable for availability planning. You can quickly provide potential renters with information on equipment availability by checking the equipment map in the software.
Another crucial benefit is the increased visibility and control over managing rental agreements.
Telematics allows you to instantly detect equipment misuse or any deviations from agreed-upon rental terms.
For instance, some technologies offer digital keys to prevent unauthorized use.
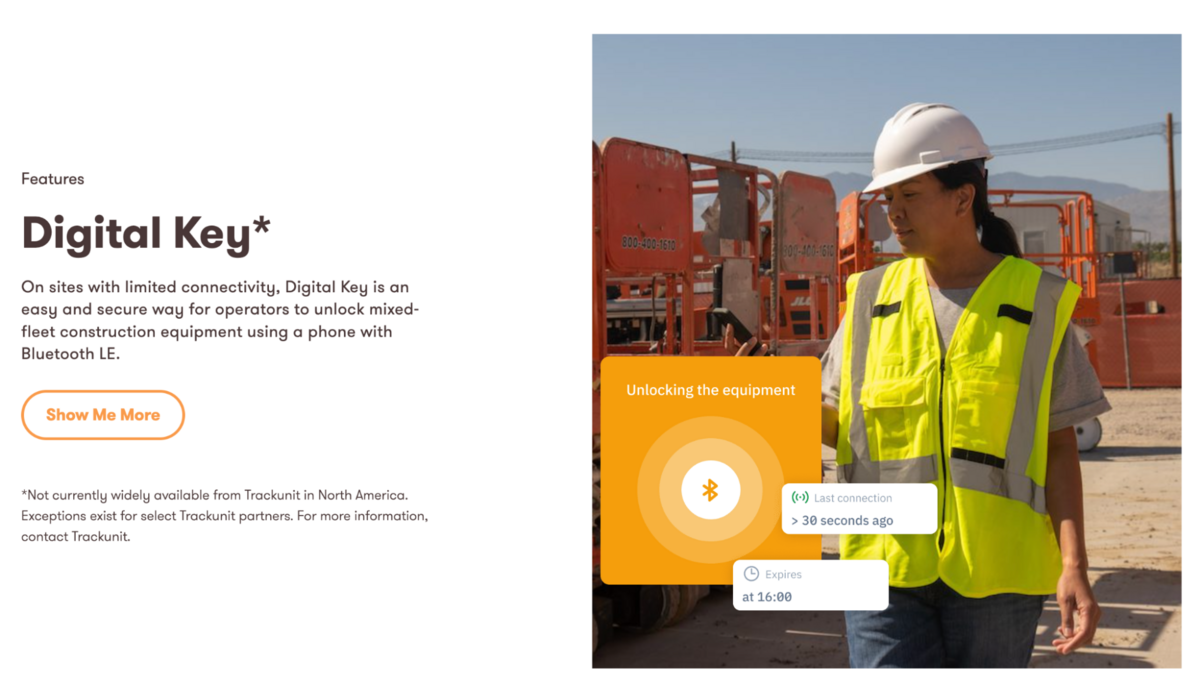
In this way, even if the renter knowingly or unknowingly disregards the agreement, you can have peace of mind because only authorized operators can access the equipment.
Telematics can also track other types of equipment misuse, such as hard braking, speeding, or engine idling.
The collected data helps you decide how to handle these situations as they arise. Keeping a record of use is also useful when issuing or handling claims.
With current technological advances, being unaware of what’s happening to your equipment is no longer an option.
Artificial Intelligence
The AI boom hasn’t missed the equipment rental sector.
AI can quickly analyze large data sets, accelerating current processes and helping your business prepare for the future in several ways.

Though effective way beyond the equipment rental context, AI technology offers versatile benefits such as demand forecasting and predictive maintenance, which your rental company can use effectively.
AI can analyze historical rental data, customer behavior, and market trends, indicating which equipment to sell and which to acquire more of, and soon.
It boils down to having a clear, data-driven sense of where you should be heading, rather than relying on intuition.
By relying on insights derived from AI-powered technology, you can quickly optimize your inventory levels, and allocate resources accordingly.
AI can also help you adjust your rental equipment recommendations based on previous purchases and customer preferences.
Combined with AI-powered chatbots providing consultation in real-time, this sort of personalization increases the chances for repeat business.
And since AI technology considers all your equipment insights, from utilization rates to overall condition, it can enable significant cost savings on repairs.
How?
You’ll transition from reactive to predictive maintenance, anticipating and preventing machine failures.
In an interview with the American Rental Association, Achille Ettorre, Managing Partner of GTA Equipment Rentals, explained how AI integrates equipment maintenance schedules with GPS and its resulting impact.
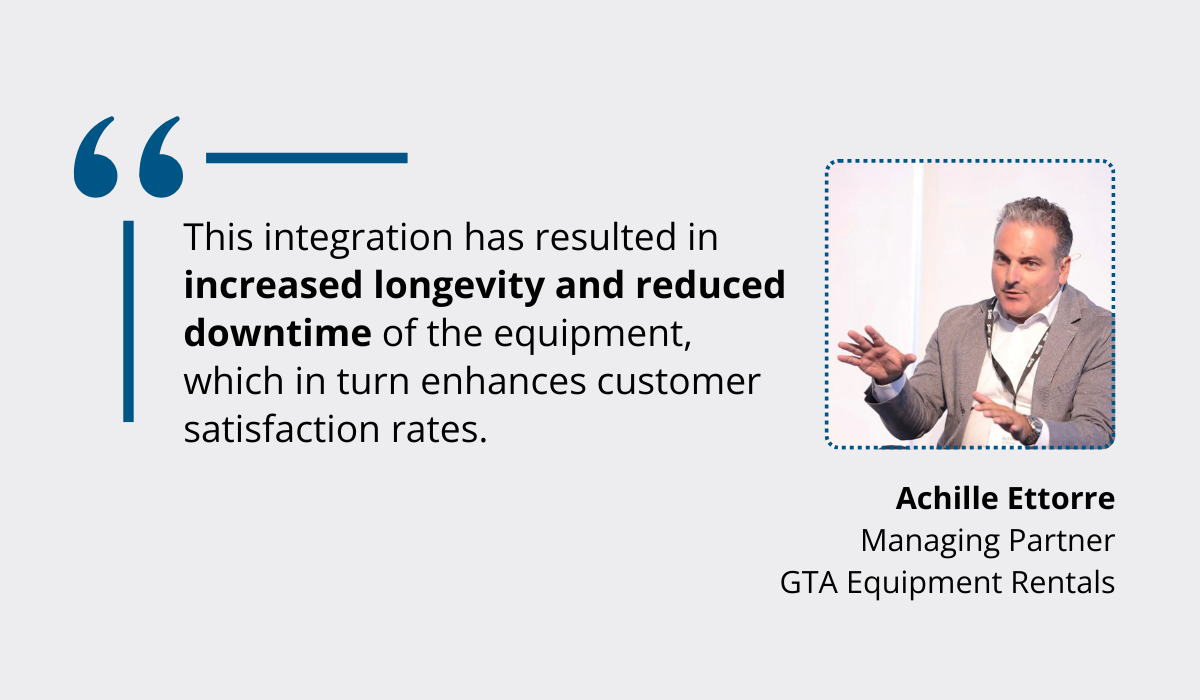
Ettore compared AI to a ‘traffic light report system for equipment,’ where red indicates a need for attention.
Major machine breakdowns are preventable with effective maintenance scheduling and up-to-date insights.
AI lays the groundwork for a predictive maintenance plan, helping you reduce costs, minimize downtime, and optimize operations.
Data Analytics
Equipment rental businesses track and store vast amounts of data about assets, customers, and more. And managing data from numerous sources can be challenging.
This is where data analytics excels.
Analytics have huge implications for the construction rental industry, from promoting customer-driven digital transformation to providing insights for anticipating and addressing issues.
Some immediate benefits include:
- improving rental forecasting and planning
- enhancing equipment maintenance and service
- strengthening customer relationships
Enhancing decision-making and boosting profitability is a priority for every organization, and many companies believe data analytics will help achieve this.
In fact, the 2024 Data and AI Leadership Executive Survey by European consultancy Wavestone indicates that most executives trust data and analytics.
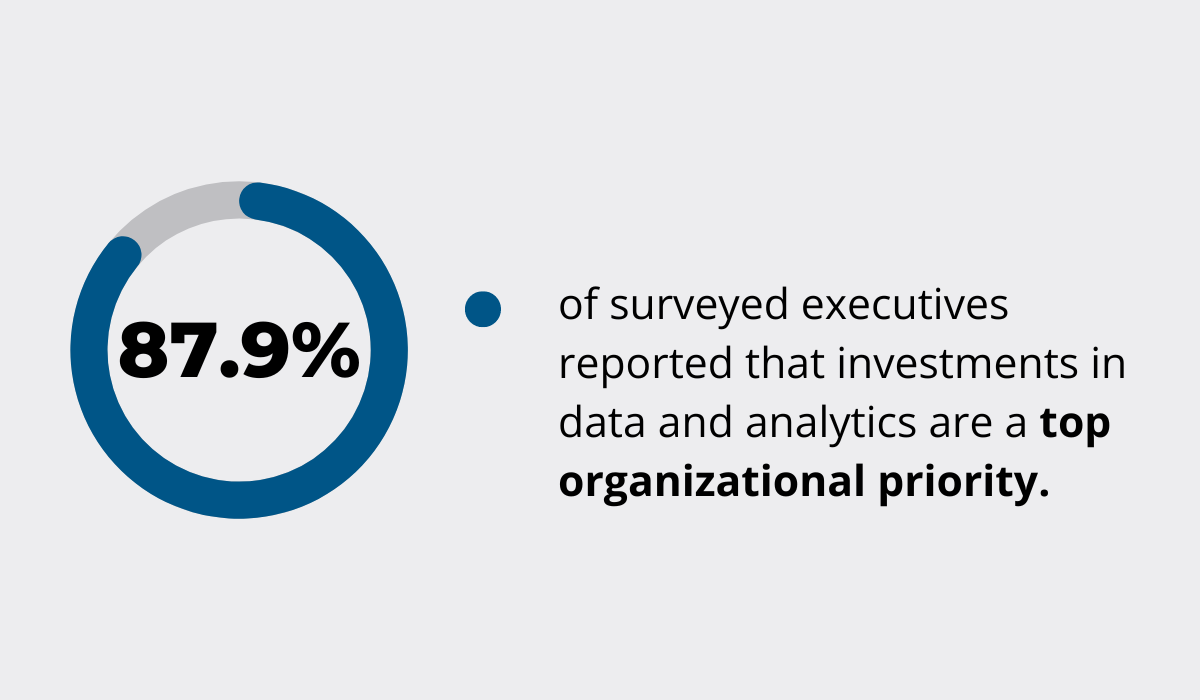
The outcome? Companies that embrace data and analytics gain a competitive advantage in the saturated equipment rental market.
The ability to collect, store, and analyze large amounts of data translates into insights about your business systems.
Identifying weak spots through analytics enables rental companies to continuously improve operations.
These insights can be complemented by information on rival companies, forming the basis for best practices that propel you ahead.
Various tools can be used for data analytics.
François Jacob, Co-Founder and CFO of a data infrastructure platform Hiboo, explains how their platform transforms vast amounts of equipment data into actionable insights.
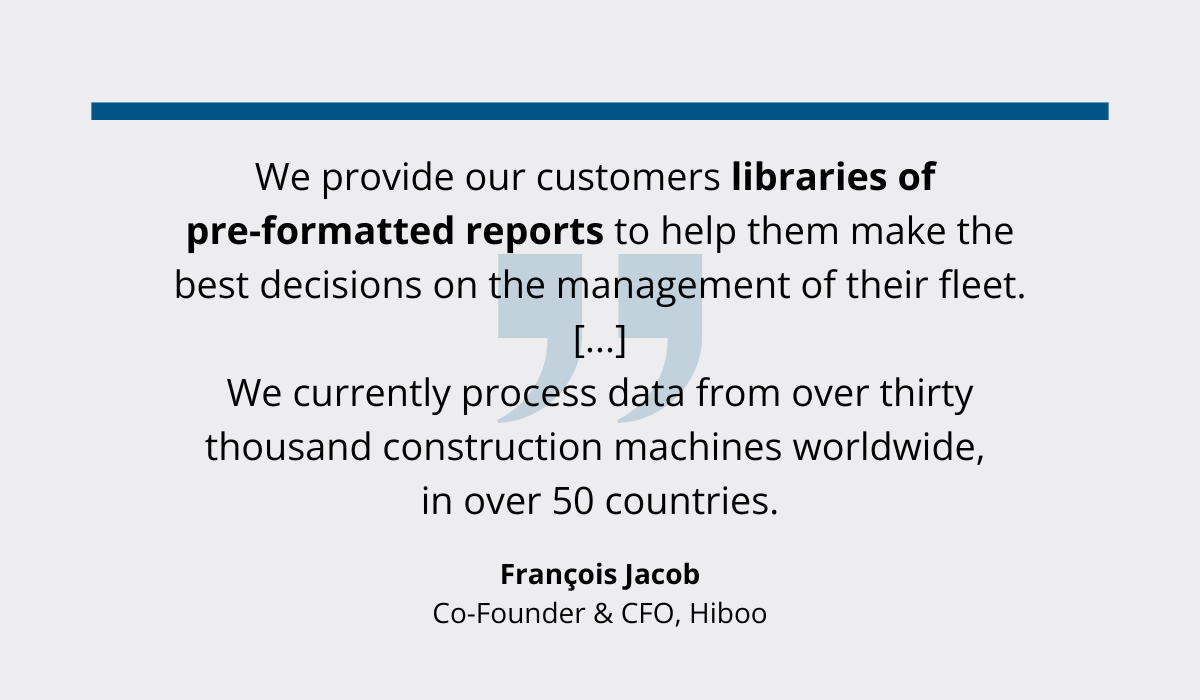
Data sources include major construction equipment manufacturers, telematic companies, and external sensors.
Insights gained from these data sources are shared through reports to aid the rental company’s equipment management efforts.
Virtual Reality (VR)
Virtual reality is another hot topic in the construction industry, alongside AI and data analytics.
According to Fortune Business Insights, the VR market is projected to reach $244.84 billion by 2032.
In the construction industry, VR applications typically fall into four categories:
- Improved visualization and planning
- Progress capture
- Remote collaboration
- Personnel training
For equipment rental companies, personnel training and remote collaboration are the most prominent VR applications.
Using VR tools for training helps companies avoid safety risks and reduce the chances of equipment malfunctioning due to human error.
Sanlab, a company specializing in simulation-based training technologies, aims to provide high-quality VR training for operators before they operate real equipment.
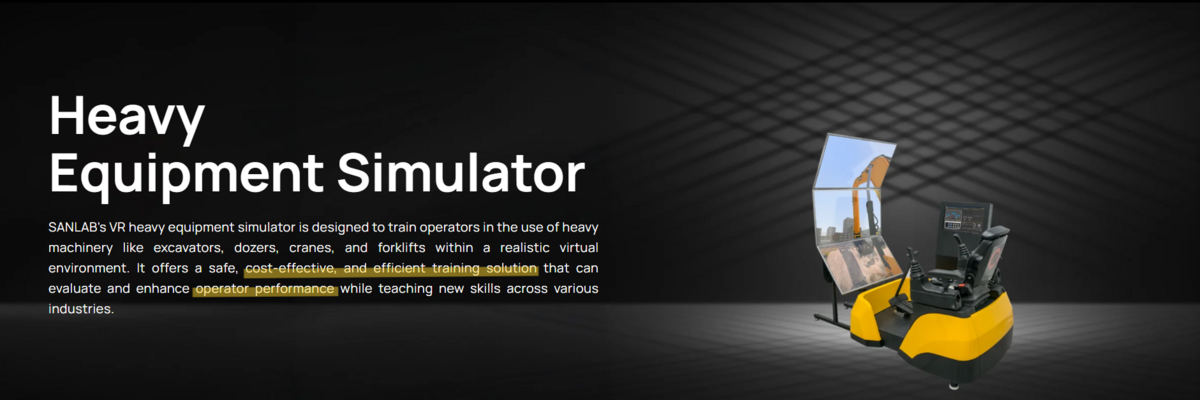
These training solutions ensure operators are well-equipped to handle unfamiliar assets, enhancing safety and efficiency.
Since minimizing safety incidents and damage to valuable assets is a priority for equipment rental services, VR technology is worth considering.
And if you’re wondering how realistic and valuable VR for construction training truly is, don’t forget that the technology is advancing at a breakneck pace.
A software development company Onix combines virtual reality (VR) with mixed-reality technology (MR) to create solutions for the construction industry.
Their products enable a simulation of realistic site conditions using specialized controllers.
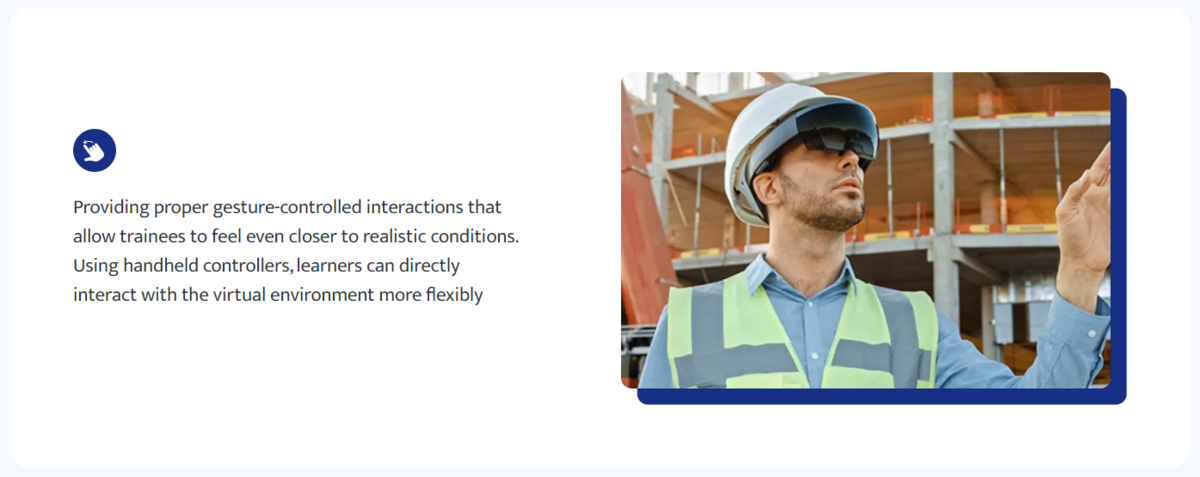
It’s important to note that the VR simulator doesn’t replace hands-on training.
It simply offers a safer alternative that can make a difference in how effectively someone handles equipment for the first time.
On the topic of familiarity, doing maintenance on newly rented equipment isn’t exactly a walk in the park either.
You’re probably already picturing the consequences of botched maintenance, but this is something that VR and MR can help with too.
Imagine being able to enter a piece of machinery virtually alongside an expert who could give you instant directions and guide you on how to check and repair the rented asset.
In 2019, Kim Nyberg, Trimble’s Technology Director and mixed reality solutions expert, pointed out that these kinds of repairs were already happening.
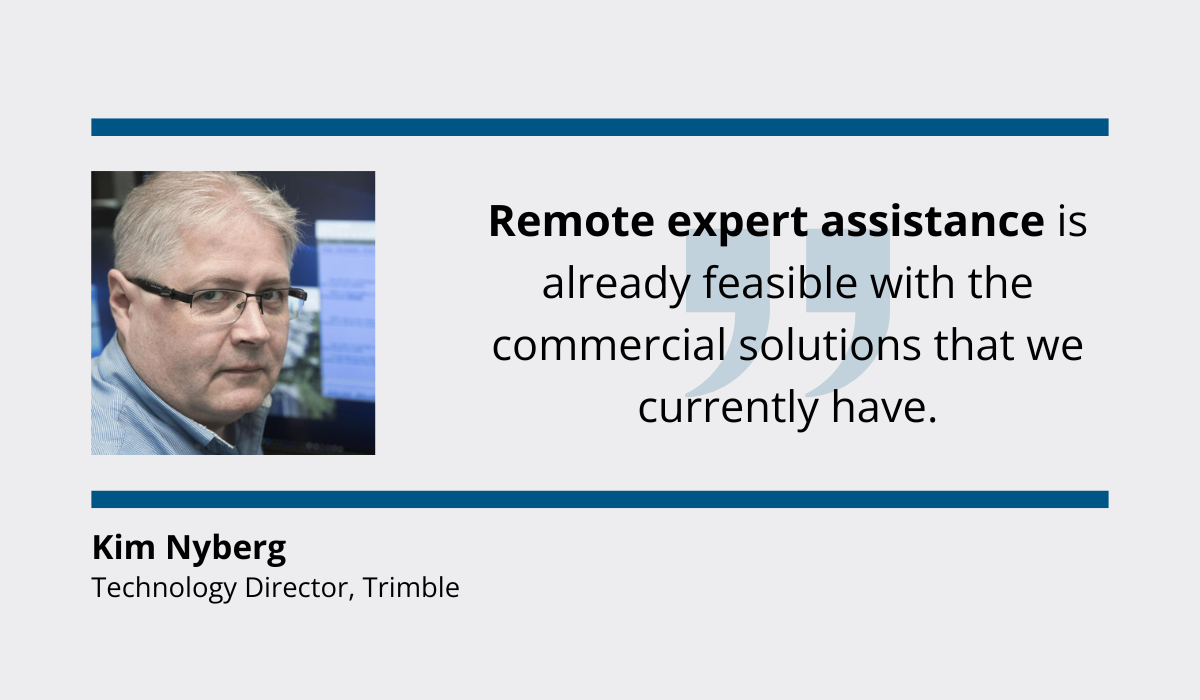
Fast-forward five years, and it’s clear that the sky’s the limit with the current tech advances.
With VR, experienced staff can remotely inspect equipment or assist in repairs, even when the equipment is elsewhere. Alternatively, they can guide on-site personnel on how to fix the problem themselves.
Whether for training or maintenance, one thing is certain: VR offers numerous benefits that can be tailored to your business needs.
Conclusion
One of these five technologies may have made a stronger impression, but their synergy is what usually delivers the best results.
Optimizing your operations requires a continuous flow of data from QR codes and telematics in tandem.
Meanwhile, AI and data analytics both generate insights that lead to better outcomes, but in slightly different ways and scope.
And VR brings its unique value to maintenance and operator training.
If you want to achieve significant improvements in efficiency and profitability, embrace these technologies without delay!