Just like with any rental business, companies supplying construction equipment to others are reliant on their assets to stay operational.
After all, it is a key aspect of the service they provide, and, in some cases, the sole source of their earnings.
Therefore, they need to make sure that their equipment stays in optimal working condition for as long as possible, and that it is utilized enough to overset its operational and owning costs.
For owners or managers looking for improvements in these areas, this article contains five crucial reasons why equipment tracking could be the solution they’ve been searching for.
To start, let’s go over how equipment tracking benefits a business by providing insight into equipment utilization.
In this article...
Provides Accurate Insight Into Equipment Utilization
One of the key advantages of tracking rental equipment is the ability to gain insights into how the equipment is used, based on a variety of collected data.
To make sure you are getting the most out of your assets, you can use this data to determine your equipment utilization rates and adjust your management strategy accordingly.
In a paper discussing the optimal equipment utilization calculations, researchers Sessions, Berry and Han explain that:
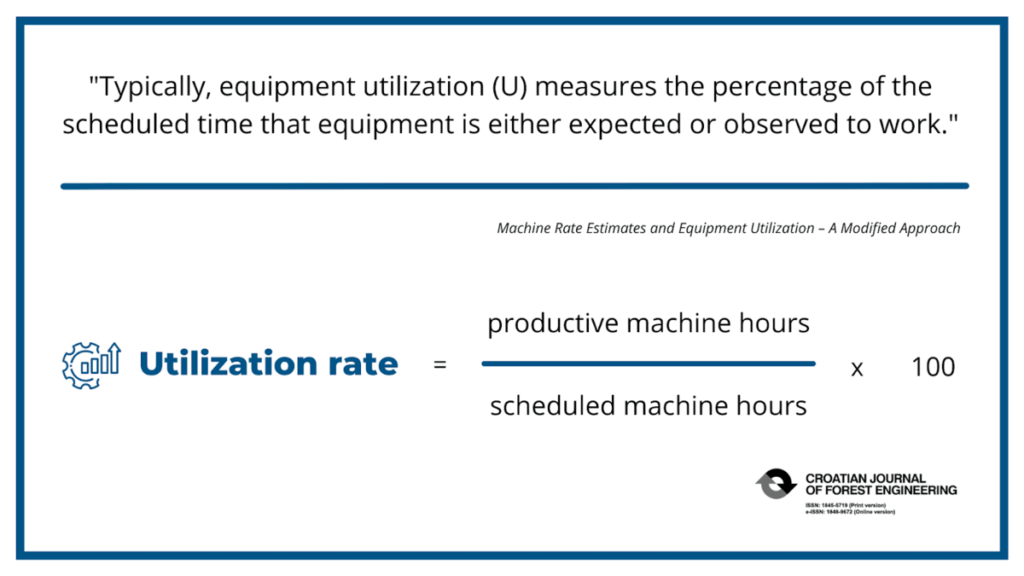
If we assume the scheduled machine hours to be the highest achievable productivity, utilization is calculated by dividing productive machine hours by scheduled machine hours, and then multiplying by 100 to get a percentage utilization rate.
While simple on the surface, there are a lot of factors that go into determining the maximum operating hours of an asset.
As it says in the paper quoted above:
Often, equipment works less than the scheduled operating hours for a variety of reasons, including weather, lack of available work, machine breakdowns, and repair and maintenance.
Following this logic, to gain an accurate insight into your assets’ productivity, you need to take into account a lot of data. This is where equipment tracking proves highly useful.
Any tracking system worth its salt has a central database of equipment containing pertinent information on each entry, such as manufacturing date, purchase date, maintenance history, and productive hours, among others.
It also allows you to track equipment usage patterns, such as the frequency of rentals, duration of each rental, and idle periods.
This will paint a clearer picture of what equipment is being underutilized, allowing you to take timely steps to address the issue.
After all, as one former student concluded in his graduate thesis for Oregon University,
the cost of construction equipment is usually presented in terms of cost per operating hour of equipment.
Considering you pay for the costs of owning construction equipment anyway, every hour your equipment is underutilized raises its cost per operating hour, increasing your overall business expenses.
Therefore, if you notice that a particular piece of equipment is underused, you can sell it and stock the most looked-after equipment, or explore alternative rental options.
For example, you could subcontract it to other companies or promote it through equipment rental marketplaces like DOZR or United Rentals.
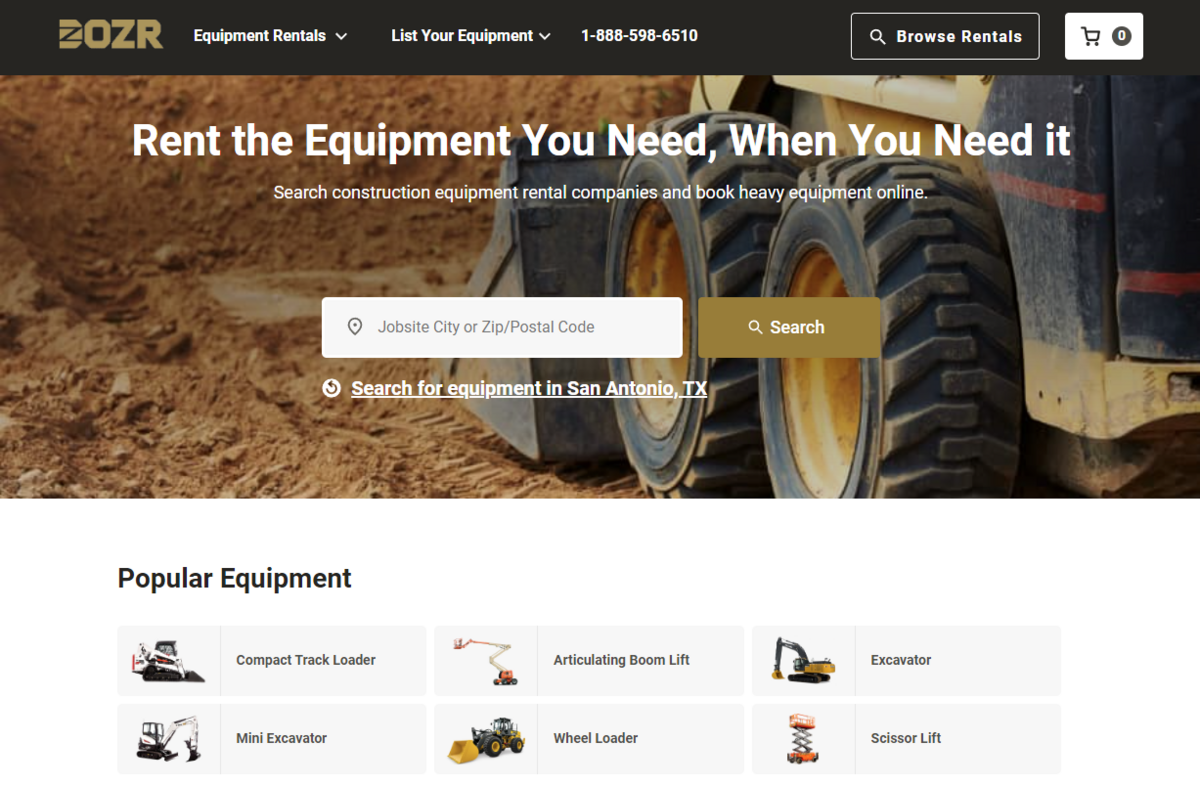
In any case, by leveraging the power of data, you can ensure that every piece of equipment is contributing to your bottom line.
In the next section, we’ll explore how to use tracking data to enhance maintenance planning, ensuring equipment longevity and reducing unexpected breakdowns.
Makes It Easier to Keep Rental Equipment Maintained
Other than utilizing equipment to the best of its potential, it is also essential to keep your business’s assets in good condition.
That requires an effective maintenance strategy.
To develop it, you need to take into account multiple data points tracked across different time periods.
As the authors of a paper going over recent construction equipment research concluded:
A condition-based strategy which integrates machine data, prognostics, and remote diagnostic tools represents the future of maintenance.
Your approach to maintenance is crucial to the success of your business, as the longer your assets remain in optimal working condition, the longer they keep producing value for your company.
That’s why it’s a good idea to use equipment tracking software.
Our own solution, GoCodes, offers a comprehensive database and tracking feature that can reveal the condition of your equipment, allowing you to develop more effective maintenance strategies that prevent machine breakdowns and prolong their lifespan.
In fact, the US Department of Energy reported that a predictive maintenance plan reduces unexpected failure rates by a staggering 70% to 75%, and brings an additional reduction in maintenance costs.
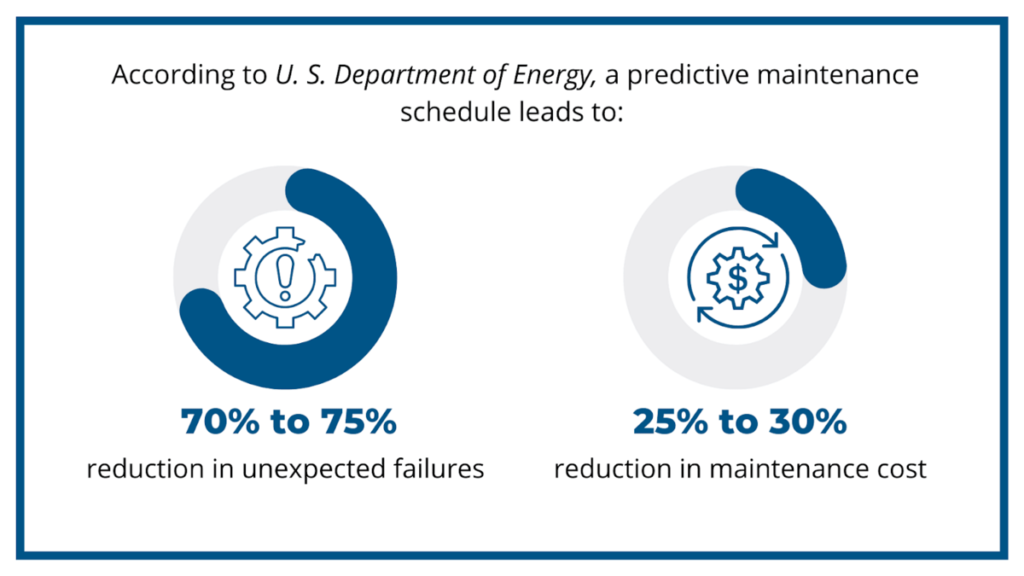
Implementing equipment tracking software will provide insight into exactly how much and for what purposes a piece of equipment is being used, informing your maintenance strategy.
GoCodes even has a utilization dashboard you can use to figure out the numbers you need.
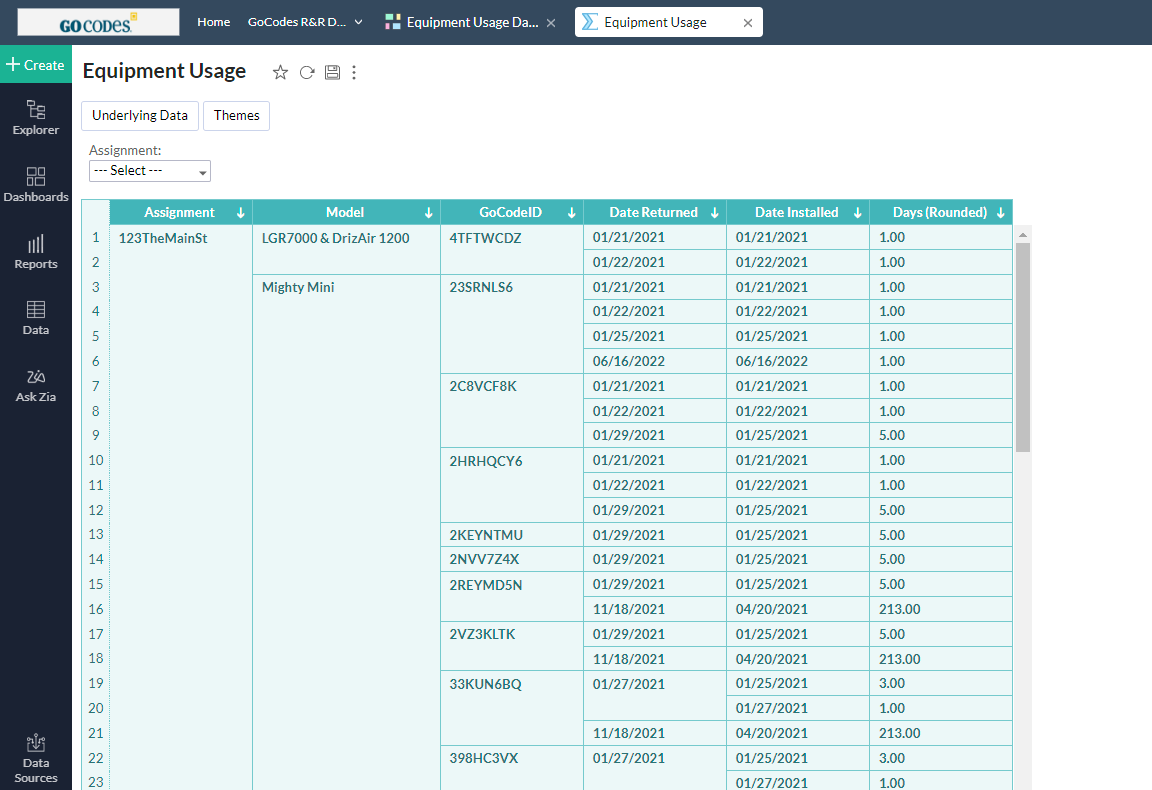
Furthermore, every asset has a profile with information about its condition at various points in time, with possible detailed descriptions and images.
GoCodes also allows you to access the asset’s comprehensive maintenance history to see the progress, or regress that it has made during specific time periods.
Taken as a whole, this information allows you to deduct an optimal maintenance plan according to equipment’s usage patterns and actual state, instead of relying on guesswork and ill-informed predictions.
Once you come up with a strategy, you can schedule maintenance dates for each asset by going into the profile and clicking a few buttons.
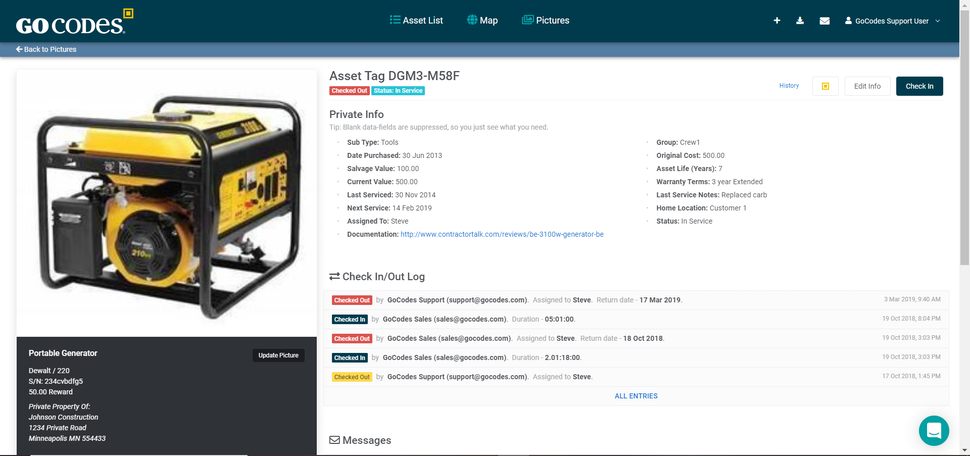
If you turn on the notification feature, the system will automatically remind you of upcoming maintenance dates by email, ensuring you don’t miss any by chance.
Overall, if you want to provide top-quality rental service, you need top-quality rentals.
An equipment tracking system like GoCodes can provide you with the tools to develop maintenance strategies that provide your equipment with the best care it can get, ensuring fewer failures and a longer lifespan.
Protects Rental Equipment Against Loss and Theft
Just like a GPS helps you keep track of your car’s whereabouts, an asset management system equipped with real-time equipment tracking acts as a recovery tool for your rental equipment.
By monitoring the precise location of your valuable assets at all times, you can significantly reduce the risk of loss or theft—which is not a minor issue by any means.
According to the National Equipment Register’s latest report, the construction industry has an average annual loss of $400 million due to equipment theft.
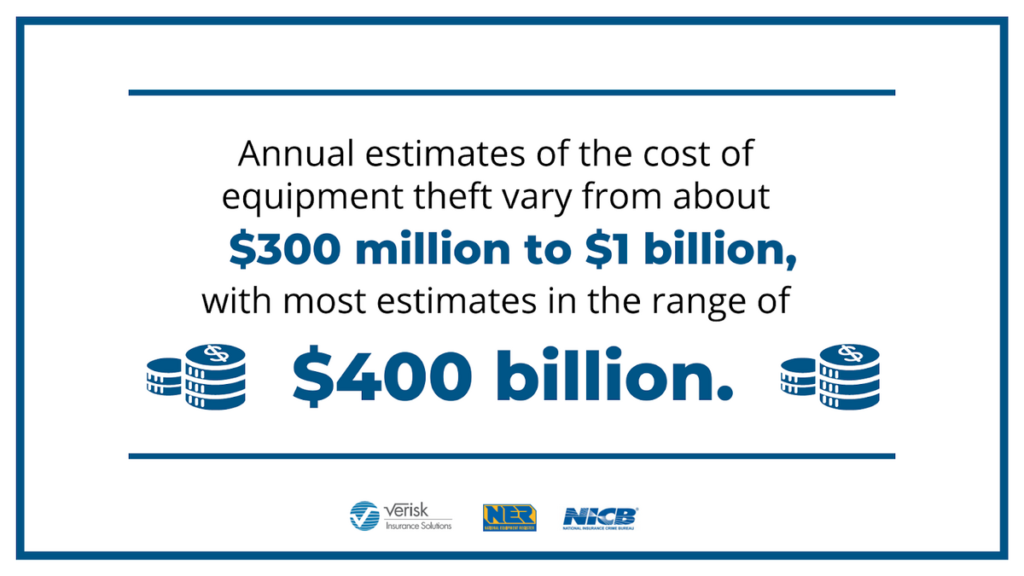
Moreover, according to their research of over 11,000 cases, only 21% of stolen equipment ever gets recovered.
To protect your rental equipment from becoming a part of this unfavorable statistic, you need to equip it with as much security as you can, which is where asset tracking comes in.
An equipment tracking system allows you to actively monitor the real-time location of your rented assets with GPS or Bluetooth locating devices.
This way, you can react promptly when you notice a piece of equipment missing or moved to a location it shouldn’t be in, which significantly increases the chances of recovering lost or stolen assets.
For example, in January of this year, there was a case of an equipment owner using GPS tracking technology to recover $100,000 worth of his stolen items.
He simply used a GPS tracker to follow the criminals, who destroyed the fake one the owner had installed as misdirection.
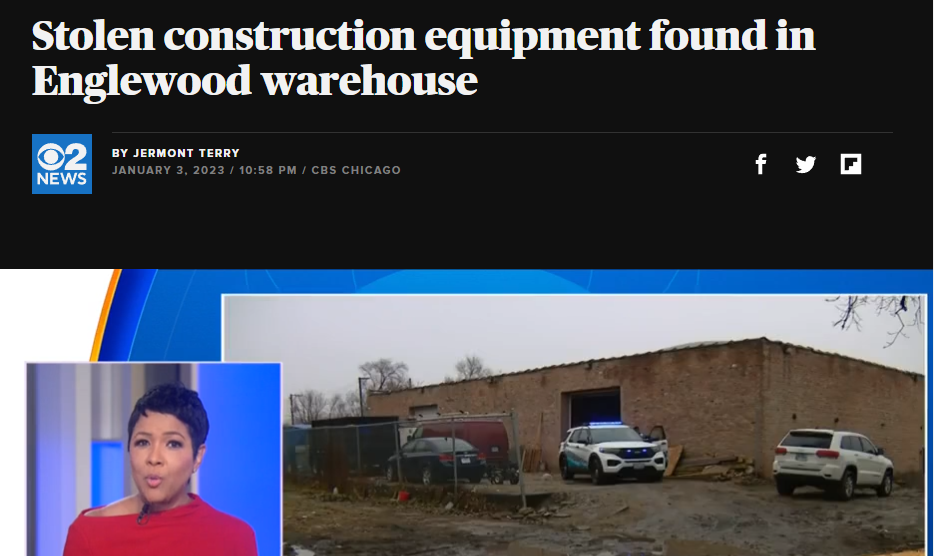
Not only that, but the warehouse he tracked the thieves to contained an additional $200,000 to $400,000 of equipment, showing the amount of stolen property which would have been lost if not for the tracking system of this one owner.
Now, in most cases, you won’t get to catch the criminals yourself. However, your reaction time can be crucial for the police’s investigation.
This is confirmed by research from the Associated Schools of Construction, which shows that over 50% of recoveries for single-item thefts occur in the first 24 hours of reporting.
With equipment tracking, any suspicious activity or deviation from the predetermined route will be immediately recorded in the system.
Not only will this make for a more rapid response in reporting the crime, but the report will also have more weight to it.
Detailed descriptions, photographs, and unique characteristics can go a long way in helping recover or identify lost equipment, especially if it appears sometime down the road as a part of a larger find.
All in all, with real-time equipment tracking, you can enhance the security of your rental equipment, minimize losses due to theft, and expedite recovery efforts in case of any unfortunate mishaps.
Improves Contract Enforcement for Rental Equipment
When renting out valuable equipment to construction companies, especially for extended periods, there is only so much trust you can put in the client.
That’s the primary reason rental agreements exist—to protect your business from unauthorized or non-agreed-upon use of your assets.
So, how does equipment tracking help in this regard?
Firstly, it gives you the ability to detect the aforementioned unauthorized use of your equipment.
By equipping your assets with GPS tracking devices, you can monitor their location in real time and receive notifications whenever they are used outside of designated areas or during prohibited times.
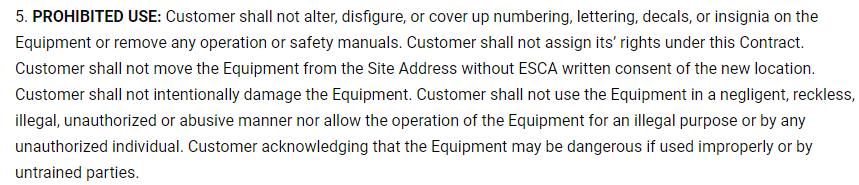
If your contract stipulates against this behavior, like in the example above, this allows you to take appropriate action, holding renters accountable for any breaches of the contract.
Secondly, an equipment tracking system keeps comprehensive and accurate records of dates, times, locations, and use time of your business assets.
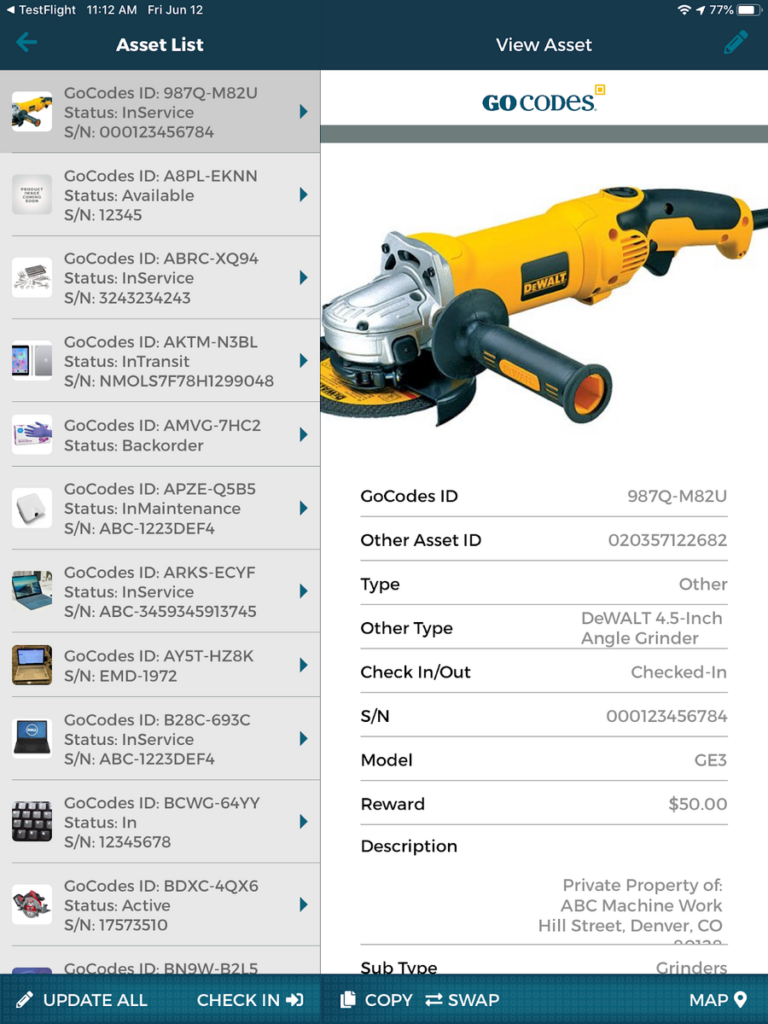
This documentation can be invaluable when disputes arise regarding the duration or condition of equipment usage.
In such cases, the detailed historical data not only serves as concrete evidence supporting your case, but it will also save a lot of time and energy you would have otherwise spent proving your side of the argument.
Overall, another notable benefit of tracking your rental equipment is protecting your business from underserved legal complications, saving you time, money, and effort in the process.
Increases Invoice Accuracy by Tracking Billable Time
With an asset management system, you can automate the tracking of billable time, leading to cleaner and more efficient operations.
Humans are prone to error, especially when doing repetitive tasks such as entering numbers and letters on a keyboard for prolonged periods of time.
In fact, research has found that even experienced typists working in good conditions record an error rate of 1.8% at the lowest.
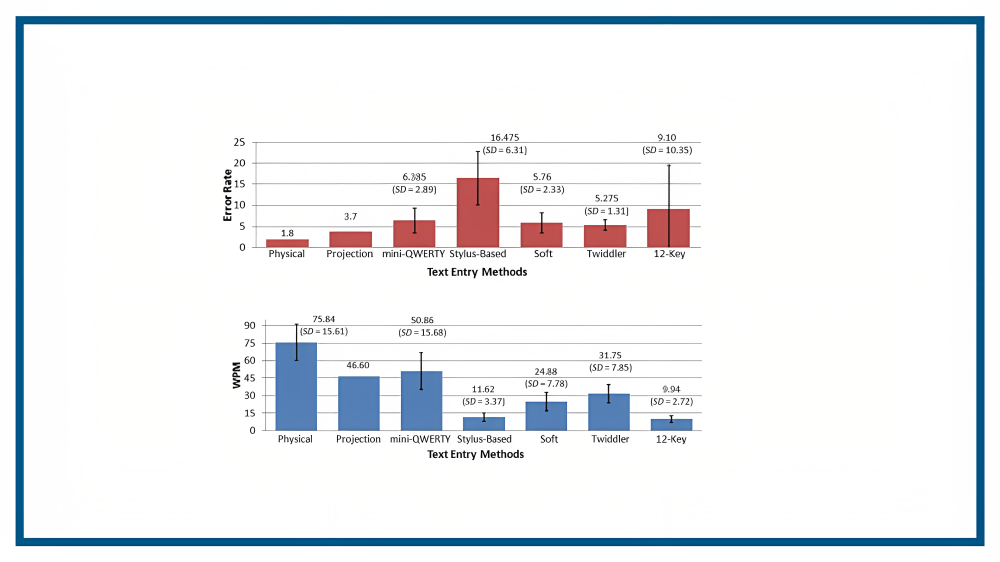
Not surprisingly, they are also faster, as humans’ best typing effort averaged around 75 words per minute, restricting the amount of potential information any one person, or several, in the case of a company, can enter.
Seeing as it involves calculations and typing, manually billing renters based on hours or days can lead to inconsistencies, miscalculations, and—in the worst-case scenario—disputes.
Conversely, equipment tracking can automatically and immediately calculate the duration of equipment usage to the hour, if not minute.
With this system, you can generate invoices based on actual utilization rather than creating them manually, leaving no room for human error.
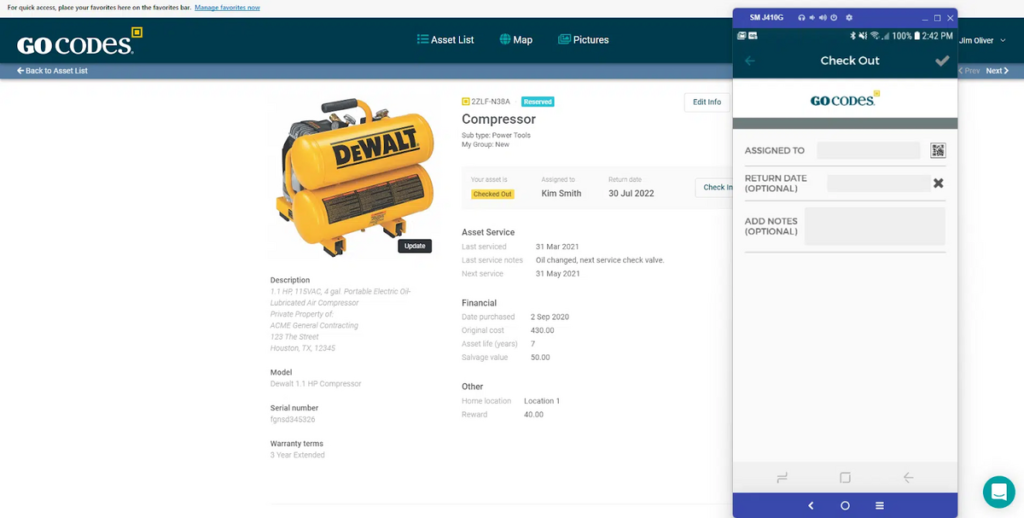
Accurate billing has an additional benefit for your business.
Relying on manual operations means you sometimes have to cut corners. For example, it’s much easier to bill daily than hourly, because it’s a less precise and calculation-intensive task.
With equipment tracking, you can offer to charge your clients by the hour, leading to a more flexible service and more satisfied customers.
Conclusion
Managing a construction equipment rental service can be a highly challenging set of tasks to manage.
You have to deal with transport, regular maintenance schedules, unforeseen breakdowns, and heavy equipment theft, which happens exceptionally often in the construction industry.
Equipment tracking can help you handle most of these tasks with a high degree of efficiency, shortening the time for various processes, securing the business against theft and legal troubles, and providing you with more managerial flexibility.